Steel Service Centers
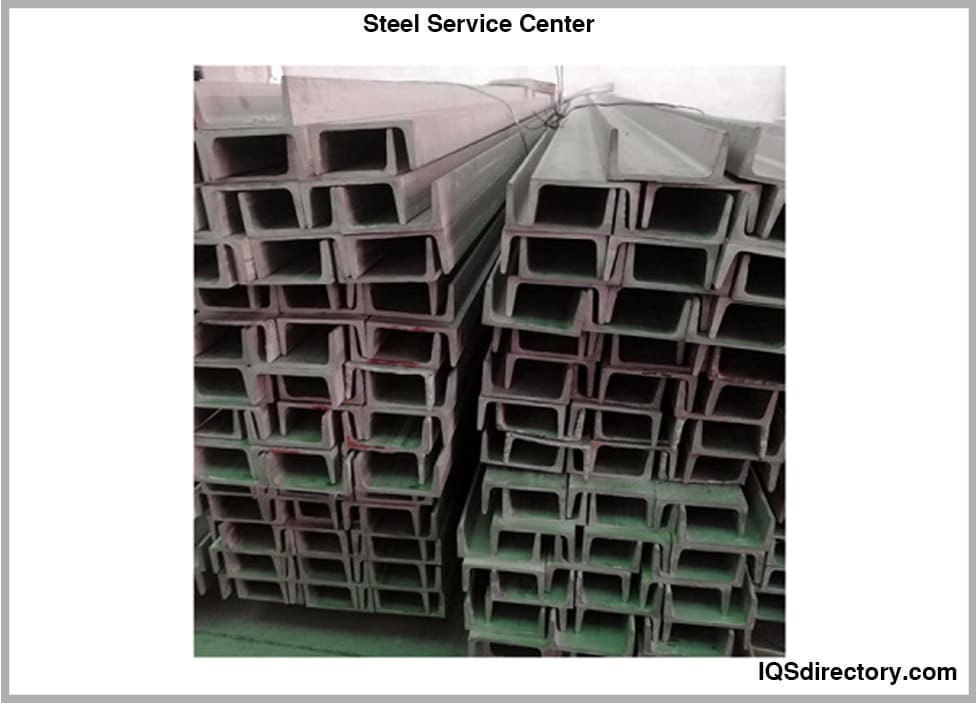
Steel service centers are companies that specialize in procuring steel directly from mills and manufacturers and supplying them to the customers. They are fundamental to the steel supply chain...
Please fill out the following form to submit a Request for Quote to any of the following companies listed on
This article will provide industry insights into aluminized steel.
Read further to learn:
Aluminized steel is a coated steel with a hot dipped coating of aluminum or aluminum silicon added to improve its properties, especially its resistance to corrosion and rust. Hot dipping, a process that involves dipping steel into a vat of aluminum, takes ordinary steel and gives it superior surface properties that significantly strengthen its performance and physical characteristics, making it comparable to stainless steel.
The process for manufacturing aluminized steel takes the structural properties of steel and the surface properties of aluminum and combines them to produce a metal with exceptional strength and appearance. Steel is a low-cost metal with strength, hardness, and good mechanical properties, while aluminum has an excellent appearance with an oxidized coating that is resistant to corrosion. The combination of the durability of steel and the corrosion resistance of aluminum creates a metal with more capabilities and broader use.
Aluminized steel is supplied by steel service centers that process from steel mills. Aluminizing, a process similar to galvanizing, is one of the surface treatments performed on ordinary steel to meet the needs of downstream manufacturing sectors such as construction, transportation, automotive, aerospace, shipbuilding industries, appliances, HVAC systems, bakeware, and fireplaces.
The concept of aluminized steel takes advantage of the best properties of both metals. When comparing them, steel has 250% the density and weight of aluminum, making it significantly stronger. However, if steel is left unprotected or uncoated, it easily rusts when exposed to the atmosphere, while aluminum has a coating that prevents it from rusting and corroding.
Aluminum is one of the most commonly used metals today. They are particularly known for their high strength-to-weight ratio, making them suitable for automobiles and aircraft parts. Aside from its lightness, aluminum has many desirable surface characteristics. Its ability to protect the material from corrosion tops the list. Other properties such as conductivity, toughness, and reflectivity are also described below.
Corrosion resistance is the most important property of aluminized steel. Aluminum has an inherently high corrosion resistance compared to most metals. It protects the metal from the two mechanisms of corrosion: direct chemical attack and electrochemical action.
Direct chemical attack, or pure chemical corrosion, is corrosion resulting from the direct exposure of a highly reactive agent to the bare surface of a metal. The corrosion process is spontaneous to the area in contact. Liquid and gaseous products of the reaction eventually escape or disperse from the corrosion site. However, solid products remain. These solid products are typically rust or metal oxides. The gradual buildup of metal oxides to the outer layer of the metal can hinder further corrosion.
Aluminum does not readily corrode because it forms a thin protective layer of aluminum oxide on its surface. This aluminum oxide layer is a product of a direct chemical attack that does not progress to the degradation of the material. This imperious and adherent layer forms instantaneously upon exposure to the atmosphere. Moreover, when the layer is broken, it can regenerate by forming new aluminum oxide layers on the freshly exposed surface. This gives the material an almost permanent corrosion resistance.
Another protective feature of aluminum is electrochemical. Electrochemical corrosion involves an electrolyte solution to link the metal to a corrosive agent. This corrosive agent can be acids or cations of less active metals.
In most conditions, the outer aluminum oxide layer is enough to provide corrosion resistance. But for cases where the protective layer is unable to regenerate, such as in the presence of a strongly acidic solution, the aluminum alloy underneath can still protect against electrochemical corrosion. During an electrochemical reaction, instead of consuming the steel, the highly active aluminum coating is corroded instead. Thus, aluminum provides cathode protection by acting as a sacrificial anode. Aluminum is one of the best anodic materials and is comparable to zinc.
The electrical conductivity of aluminum is around 61% that of copper. It is preferred over copper for certain applications due to its lower density and cheaper cost.
Aluminum conducts heat twice that of brass and four times that of steel. This means aluminum is extensively used in heat sink applications in electronics and electrical components.
In contrast with steel, aluminum retains its toughness at low temperatures. Low temperatures typically make metals fail under brittle fractures. The mechanical properties of aluminum are almost constant across all temperatures.
Because of its natural toughness, aluminum has high resilience and impact strength. Aluminum parts can absorb sudden forces or shocks and elastically flex from dynamic loads.
Aluminum has some of the highest reflectivity of any metal in the 200-400 nm range, better than gold and silver. As a result, aluminum coatings, rather than silver, are commonly applied to glass to make mirrors. Depending on its finish, aluminum can reflect about 90% of light across the wavelengths of the visible spectrum.
Unlike steel, aluminum is not ferromagnetic but paramagnetic. This means it does not acquire a magnetic charge when subjected to strong magnetic fields, making aluminum coatings suitable for electronic and electrical enclosures and parts that emit high electromagnetic fields. Moreover, along with its electrical conductivity, aluminum can be used to create electromagnetic field shields.
In its pure or alloyed form, aluminum does not produce sparks. This property is required for making tools used in flammable or explosive environments.
Aluminized steel offers several advantages over other materials made for the same purpose. Stainless steel and galvanized steel are two extensively used materials, particularly for purposes needing corrosion protection. Aluminized steel is now becoming a better alternative because of its unique qualities.
As mentioned in the previous chapter, aluminized steels are protected against direct chemical attack and electrochemical action. Direct chemical attack is often referred to as dry corrosion, while electrochemical action is termed wet corrosion. Both corrosion mechanisms are present in most industrial environments.
Stainless steel is a common material that competes with aluminized steel in terms of corrosion resistance. This material offers better resistance since it is homogeneously alloyed with chromium, an excellent oxide-forming metal. However, when coupled with other metals such as steel, it tends to promote a type of electrochemical reaction called galvanic corrosion. Steel that is connected to stainless steel corrodes faster by acting as an anode.
However, when coupled with other metals such as steel, it tends to promote a type of electrochemical reaction called galvanic corrosion. Steel connected to stainless steel corrodes faster by acting as an anode.
Aluminized steel presents no problem when it comes to galvanic corrosion. The aluminum coating is more anodic than steel. Thus, it is consumed by corrosion instead of the adjacent metal parts. Magnesium, beryllium, and zinc are a few metals that are more anodic than aluminum.
Aluminized steel presents no problem when it comes to galvanic corrosion. The aluminum coating is more anodic than steel. Thus, it is the one consumed by corrosion instead of the adjacent metal parts. Magnesium, beryllium, and zinc are a few metals that are more anodic than aluminum.
Aluminized steels are much cheaper than stainless steels. This is because, in aluminized steel, the main structural component of the finished part is still plain carbon steel. The aluminum alloy coating is only 30 to 270 grams per square meter or 0.10 to 0.90 ounces per square foot of surface area. Most of the cost of aluminized steel goes into the operating expenses of the hot dipping process.
The coating of steel with alloys to offer extra protection is very common and includes several different metals. Anodizing, electroplating, and powder coatings have been used for years to protect the surface of steel. Although hot dipping for aluminized steel is costly, its costs are comparable to other steel coating methods. In the galvanizing process, carbon steel is coated with zinc, which provides the same protection as aluminum. Anodizing involves the application of various types of non-ferrous metals, such as copper, lead, and tin.
Aluminized steels are suitable for applications up to 1292°F (700°C). This maximum temperature varies with the type of aluminum coating and the carbon steel base. At these temperatures, the mechanical properties of the base are maintained. Aluminized steel is an effective material for heat exchanger tubes, automotive mufflers, exhaust pipes, and structural components of furnaces, water heaters, and burners.
Compared to stainless steel, results can vary depending on the stainless steel grade. Some stainless steel alloys have stabilizing elements, namely titanium and niobium, an example of which is stainless steel 316Ti. This stainless steel variant is intended for high-temperature use. However, without stabilizers, stainless steel is prone to oxidation at high temperatures. At temperatures above 932 °F (500°C), carbide precipitation occurs, which eventually results in intergranular corrosion. This limits the application of the basic stainless steel grades to lower temperatures.
Galvanized steels can only withstand temperatures of approximately 482° F (250°C). At higher temperatures, free zinc in the coating reacts with the steel to form an iron-zinc alloy. Though the iron-zinc layer can provide protection, continued exposure to heat can cause the layer to crack and peel off.
As mentioned earlier, aluminum has a high reflectivity in the visible spectrum. The same is true for reflecting infrared radiation. Infrared radiation is the common form of thermal energy or heat in furnaces and burners. Aluminized steel can reflect up to 80% of the incoming radiation depending on the coating‘s surface quality.
There are two main types of hot-dipped aluminized steel grades classified according to their aluminum bath composition. The first type, commonly called Type 1, is composed of an aluminum-silicon alloy. The second type, Type 2, is made from pure aluminum. Aluminized steel produced from each type has unique characteristics intended for specific applications.
Type 1 aluminized steel is hot dipped to form a thin layer of aluminum with 5% to 11% silicon added to create better adhesion of the aluminum layer. Silicon helps in the formation of a brittle intermetallic layer between the thin outer aluminum coating and various types of steel base metals.
Silicon slows the growth and controls the formation of the intermetallic layer, which improves the heat resistance and workability of aluminized steel. Although the addition of silicon is beneficial in enhancing the bonding of the aluminum layer and the base steel, it does slightly deteriorate its corrosion resistance and electrical conductivity and creates black spots on the finished aluminized steel. Type 1 aluminized steel is typically used in industrial equipment and commercial products such as mufflers, furnaces, ovens, ranges, heaters, water heaters, fireplaces, and baking pans.
The molten aluminum bath of type 2 aluminized steel is composed of commercially pure aluminum. It is designed for use in conditions where the primary requirement is resistance to atmospheric corrosion. Type 2 aluminized steels are used as structural materials for enclosures, sewage piping, corrugated roofing, siding, grain bins, drying ovens, and air conditioner condenser housings.
Aside from carbon steel, several types of steel are used in the aluminizing process. The positive properties of aluminum are ideal for the protection of all steels, including commercial grade, forming, deep draw, structural, and high-strength low alloy steels, all of which are susceptible to the same negative effects as carbon steel. Applying aluminum alloy increases the longevity of the steels and the number of applications for which they can be used.
Commercial steel is often referred to as mild steel or commercial quality steel. It is used for general purpose applications and is ductile, soft, and malleable enough to be bent flat in any direction without cracking. Commercial steels have a carbon content of around 0.10%.
Forming steel has a lower carbon content than commercial steel, making them more ductile and malleable. Forming steels contain 0.02 to 0.10% carbon.
These steels are used in steel fabrication processes where the stock is radially drawn from a forming die. They contain approximately 0.06% carbon.
EDDS is similar to DDS. However, these steels have a smaller carbon content of around 0.02%, which makes them more ductile.
Structural steel is industrial-grade steel composed of 0.20% to 0.25% carbon, which makes it harder than commercial steel due to the high carbon content. The exceptional tensile strength of structural steel makes it the preferred choice for construction and building. Its wide varieties include carbon steel, high-strength carbon steel, weathering steel, and fire-resistant steel.
These steels are made according to a set of mechanical properties and not by specific chemical composition. They have yield strengths of around 250 to 590 MPa.
Ferritic stainless steel, an alternative to austenitic stainless steel, has its properties further enhanced by the aluminizing process. It is a low-carbon, high chromium stainless steel with little to no nickel content. Ferritic stainless steel is known for its ductility, corrosion resistance, and magnetic properties. It is classified as part of the 400 series of stainless steels, which are divided by their composition and applications.
Hot dipping is the main process employed for producing aluminized steel. It is a widely used method since its operation is the least expensive and requires the simplest equipment. However, aside from hot dipping, other aluminum coating methods exist. These are summarized and explained briefly below.
Calorizing is a surface modification process used to place aluminum coatings on steel to add exceptional heat and corrosion resistance. During the calorizing process, steel is immersed in a mixture of aluminum powders that are sealed to the steel in a furnace. The extreme temperatures of the furnace cause the aluminum mixture to diffuse over the surface of the steel. Two methods used in calorizing are pack diffusion and the slurry method.
Electroplating is a process designed to deposit a thin layer of metal onto an electrically conductive surface using two electrodes or conductors positioned apart from one another. The electrically charged anode electrode causes positively charged ions to move to the negatively charged cathode electrode while negatively charged ions move back to the anode.
The metal coating is placed at the anode, while the metal to be plated is positioned at the cathode. As ions move from the anode to the cathode, they plate and cover the steel workpiece. Direct current is sent to the anode, which oxidizes its metal atoms and dissolves them. When they make contact with the cathode, they are reduced, causing them to plate the metal piece. The applied current rate is such that the rate of dissolving by the anode matches the rate of the plating of the cathode.
Electroplating, also known as electrodeposition, is used to increase the strength and durability of steel by placing a coating of aluminum on its surface. It is used to coat steels for aerospace, automobiles, medical and dental tools, and microwave products.
Metal spray coating, also known as metalizing and thermal spraying, melts aluminum wire into a molten material and injects it into a compressed air stream, where the molten aluminum is atomized into fine droplets and sprayed onto the surface of the steel workpiece. The fine droplets quickly cool, fuse, and solidify to form a protective metallic layer or film with a thickness of 0.47 to 0.59 inches (12 mm to 15 mm).
The aluminum feedstock for the metal spray coating process is 85/15 wire. The process is designed to cover the surface of steel and does not create an intermetallic layer as is produced by hot dipping. The surface of steel coated using metal spray coating does not have the same smooth finish as other coating processes and tends to be mottled, rough, and uneven.
Aluminum coating through the cladding process is achieved by rolling, extruding, or drawing steel together with an aluminum sheet or film. The process is done at elevated temperatures to facilitate the bonding of the aluminum coating to the steel part.
Hot dipping is a straightforward process involving three main operations: surface preparation, immersion, and finishing. Additional steps may be added to improve the process, such as flux coating and heat treatment. These series of operations are explained in detail below.
Fluxing: This process serves two purposes. The first is to prevent the oxidation of the surface of the workpiece after cleaning. Metals oxidize is faster at elevated temperatures. Since hot dipping occurs at the melting point temperature of aluminum alloy, the oxidation of the workpiece is accelerated. The newly created oxides can interact with the intermetallic layer and can decrease the bonding strength of the coating.
The second benefit of fluxing is to improve the wettingcharacteristics of the metal, ensuring that the whole surface is covered and free from voids or discontinuities. This further enhances the bonding strength of the intermetallic layer.
Aside from directly applying the flux coating onto the workpiece, fluxing can also be done by covering the molten aluminum bath with a flux solution. This is known as wet fluxing. Through wet fluxing, a layer of molten flux is applied to the surface of the aluminum bath. This not only prevents the workpiece from oxidizing upon contact with the molten bath but also prevents the bath from oxidizing.
Immersion: This is the main aluminizing process in which the workpiece is dipped into the molten aluminum bath. At first glance, this is a fairly easy process. However, certain difficulties arise, which can result in problems such as peeling of the aluminum coating, poor mechanical properties of the finished part, surface discontinuities, and workpiece deformation. To correct these, a few requirements must be followed.
The first and second requirements are easily met when steel is used as the base metal. Steel has a much higher melting point than aluminum. Also, both metals readily form alloys. The third requirement is based on the best practices of the manufacturer. Some variables that affect immersion time are the composition of the aluminum alloy, the target thickness of the intermetallic layer, and the molten bath temperature.
Steel service centers are companies that specialize in procuring steel directly from mills and manufacturers and supplying them to the customers. They are fundamental to the steel supply chain...
Aluminum 1100 is the softest of the aluminum alloys, which makes it easy to shape and form into a wide range of products for industrial and home use. It can be cold and hot worked but is frequently shaped by...
The term "aluminum coil" describes aluminum that has been flattened into sheets where their width is significantly higher than their thickness and then "coiled" into a roll. Stacks of individual aluminum sheets are difficult to...
Aluminum piping and tubing is silvery-white, soft, and ductile. The metal belongs to the boron group. Aluminum is the third most abundant element present on earth. Aluminum has low density. When exposed...
Beryllium Copper is a versatile copper alloy that is valued for its high strength and hardness, combined with good electrical and thermal conductivity. It is a non-ferrous, non-magnetic, and non-sparking metal alloy...
A variety of copper-zinc alloys are referred to together as brass. Different ratios of brass and zinc can be used to create alloys, which produce materials with various mechanical, corrosion, and thermal properties...
Copper is a ductile, malleable, and reddish-gold metal with the capacity to effectively conduct heat and electricity. Brass and bronze, two commonly used alloys, are created when copper is combined with...
The copper sheet is a highly malleable and workable metal with outstanding electrical and thermal conductivity and corrosion resistance. Copper (Cu) is a reddish, very ductile metal that belongs to Group 11 of the periodic table...
Metals are a group of substances that are malleable, ductile, and have high heat and electrical conductivity. They can be grouped into five categories with nickel falling in the category known as transition metals...
Stainless steel grade 304 is an austenite stainless steel that is the most widely used and versatile of the various grades of stainless steel. It is a part of the T300 series stainless steels with...
Stainless steel is a type of steel alloy containing a minimum of 10.5% chromium. Chromium imparts corrosion resistance to the metal. Corrosion resistance is achieved by creating a thin film of metal...
Stainless steel grades each consist of carbon, iron, 10.5%-30% chromium, nickel, molybdenum, and other alloying elements. It is a popular metal used in various products, tools, equipment, and structures that serve in many industrial, commercial, and domestic applications...
Stainless steel can be fabricated using any of the traditional forming and shaping methods. Austenitic stainless steel can be rolled, spun, deep drawn, cold forged, hot forged, or stippled using force and stress...
Stainless steel tubing is a multifaceted product that is commonly utilized in structural applications. Stainless steel tubing diameters and variations vary greatly based on the application requirements and are...
Titanium metal, with the symbol Ti, is the ninth most abundant element in the earth‘s crust. It does not occur in large deposits, yet small amounts of titanium are found in almost every rock...
Tungsten is a rare naturally occurring chemical element on earth. It is known to be one of the toughest metals on the earth. It is usually a tin white or a steel gray metal. Tungsten is common for its high tensile...
Aluminum is the most abundant metal on the Earth’s crust, but it rarely exists as an elemental form. Aluminum and its alloys are valued because of their low density and high strength-to-weight ratio, durability, and corrosion resistance...