Stainless Steel 304
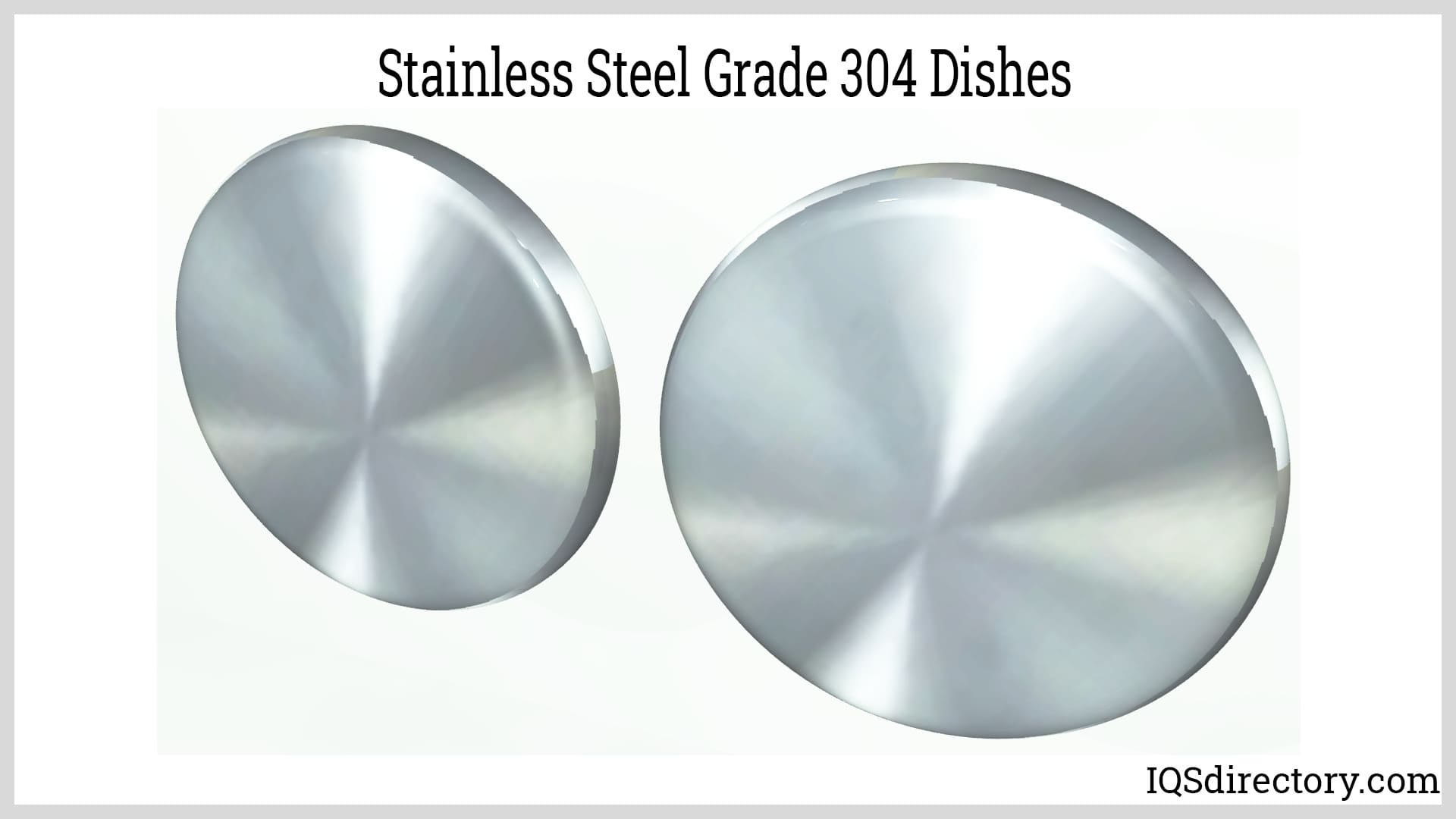
Stainless steel grade 304 is an austenite stainless steel that is the most widely used and versatile of the various grades of stainless steel. It is a part of the T300 series stainless steels with...
Please fill out the following form to submit a Request for Quote to any of the following companies listed on
This article offers detailed information about stainless steel 316.
You will learn:
Stainless Steel Grade 316 Spec Sheet | |
---|---|
316 | 316L |
ASTM A240 | ASTM A240 |
ASTM A666 | ASTM A666 |
ASME SA240 | ASME SA240 |
AMS 5524 | AMS 5507 |
Stainless steel is a steel alloy that contains at least 10% chromium, making it corrosion resistant. The addition of chromium to stainless steel creates a thin film of metal oxide over the metal's surface that protects against corrosive materials.
A popular grade of stainless steel is stainless steel 316 is generally composed of 16 to 18% chromium, 10 to 14% nickel, 2 to 3% molybdenum, and a small percentage of carbon. Adding molybdenum to stainless steel 316 increases its corrosion resistance compared to other grades of stainless steel. The addition of other alloys further enhances its properties.
The properties and characteristics of stainless steel 316 make it the second-most widely used stainless steel grade after stainless steel 304. It is used in corrosive environments such as chemical plants, refineries, and marine equipment.
Stainless steel 316L has a lower carbon content and is used in applications that subject the metal to risks of sensitization. The higher carbon variant is stainless steel 316H, which offers greater thermal stability and creep resistance. Another widely used grade of stainless steel 316 is the stabilized 316Ti. Stainless steel 316Ti offers better resistance to intergranular corrosion.
Stainless steel utilizes the principle of passivation, wherein metals become "passive" or unreactive to oxidation from corrosive compounds found in the atmosphere and process fluids. Passivation is done by exposing the stainless steel to air, where it builds chromium oxides on its surface.
To enhance the formation of the passive film, the alloy is introduced to a chemical treatment where it is thoroughly cleaned by submerging it in acidic passivation baths of nitric acid. Contaminants, such as exogenous iron or free iron compounds, are removed to prevent them from interfering in creating the passive layer.
After cleaning with an acidic bath, the metal is neutralized in a bath of aqueous sodium hydroxide. A descaling process removes other oxide films formed by high-temperature milling operations, such as hot-forming, welding, and heat treatment.
The predominant characteristic of stainless steel 316 is its molybdenum content, which enhances its corrosion resistance. It is the second most important of all austenitic stainless steel after stainless steel grade 304. Austenitic stainless steels are differentiated from other stainless steels by their nickel or nitrogen content, which gives austenitic stainless steel a unique crystalline structure.
Stainless steels are divided by their chemical content, physical properties, metallographic structure, and functional characteristics. Their mechanical properties are classified into four families: ferrite, martensite, austenite, and duplex, stainless steel that includes combinations of the first three families, such as martensite-ferrite or austenite-martensite. The matrix structure of the different stainless steels determines the four classifications or families.
The families of stainless steel are further divided into grades describing the properties of the alloys used to produce them. Older grades are designated by three-digit numbers established by the Society of Automotive Engineers (SAE). Although three-digit identifiers are common, many countries have their own systems, with North America using a six-digit system established by the American Society for Testing and Materials (ASTM).
Regardless of the numbering system, each grade of stainless steel must comply with its predetermined combination of alloys. Each change, adjustment, or addition to an alloy impacts the performance of a grade of stainless steel. A specific set of characteristics, properties, and performance qualities are expected when families and grades are placed together and identified.
The different grades of stainless steel have various degrees of corrosion resistance, strength, toughness, and high and low-temperature performance. The specific determining factor for the various grades is their microstructure, which is observed using a microscope set at 25 times magnification. The microstructure of any material influences its physical properties, such as strength, toughness, ductility, hardness, corrosion resistance, temperature behavior, and wear resistance.
The microstructure of stainless steel 316 has cell structures with boundaries enriched with chromium, manganese, molybdenum, and niobium elements, which enhances its corrosion resistance. The corrosion resistance is improved due to densification, the fine cellular structures, and the enrichment of chromium and molybdenum at the interfaces.
Austenitic Stainless Steels: Austenitic stainless steels are non-magnetic with high levels of chromium and nickel and low levels of carbon. They are the largest and most used group of stainless steels.
Austenitic stainless steels have a face-centered cubic (FCC) crystal structure with one atom at each corner of the cube and one in the center of each face, a grain structure formed due to nickel being added as an alloy. The microstructure of austenitic stainless steel makes it tougher and more ductile, even at cryogenic temperatures.
When subjected to high temperatures, austenitic stainless steels do not lose their strength, which gives them excellent formability and weldability. Since the austenitic structure is maintained at all temperatures, they do not respond to heat treatment. Instead, they are cold-worked to improve their toughness, strength, hardness, and stress resistance.
The principle alloy for all austenitic stainless steels is nickel, which is used for all series 300 austenitic stainless steels, including grades 316 and 316L. When a stainless steel has a low nickel and high nitrogen content, it is no longer a 300 series stainless steel. The presence of nitrogen in stainless steels is limited since it can have very negative effects. Stainless steels with a low nickel and nitrogen content are classified as series 200 stainless steels.
Aside from its resistance to chlorides, the main difference between series 304 and series 316 is the presence of molybdenum in series 316 at percentages of 2% to 3%, which identifies series 316 as a Cr-Ni-Mo system. Adding molybdenum makes series 316 resistant to pitting caused by phosphoric acid, acetic acid, and dilute chloride solutions. The strength and toughness of molybdenum increase series 316’s heat and wear resistance.
Comparison of the Elements of Series 304 Stainless Steel and Series 316 Stainless Steel | ||
---|---|---|
Type 304 | Type 316 | |
Carbon | 0.08% Max | 0.08% Max |
Manganese | 2.00% Max | 2.00% Max |
Phophorus | 0.045% Max | 0.045% Max |
Sulfer | 0.030% Max | 0.030% Max |
Silicon | 1.00% Max | 1.00% Max |
Chromium | 18.00 - 20.00 | 16.00 - 18.00 |
Nickel | 8.00 - 10.50% | 10.00 - 14.00 |
Molybdenum | - | 2.00 - 3.00% |
Ferritic Stainless Steels: As the name suggests, these stainless steels that have a ferritic microstructure. Its ferritic microstructure is present at all temperatures due to the addition of chromium with little or no austenite forming elements such as nickel. Because of this constant microstructure, like the austenitic stainless steel, they do not respond to heat treatment. They are more difficult to weld due to excessive grain growth and intermetallic phase precipitation, especially at higher chromium content. The result is lower toughness after welding which makes them unsuitable for structural materials. Ferritic stainless steels are designated as AISI 400 series. This designation is shared with martensitic stainless steels.
Martensitic Unit Cell: These stainless steels have higher amounts of carbon that promotes a martensitic microstructure. Martensitic stainless steels are hardenable by heat treatment. When heated above its curie temperature, they have an austenitic microstructure. From an austenitic state, heating rapidly results in martensite, while cooling slowly promotes the formation of ferrites and cementite. Varying the carbon content results in a wide range of mechanical properties, making them suitable for engineering and tool steels. Increasing the carbon content makes the stainless steel harder and stronger, while decreasing it makes the alloy more ductile and formable. However, adding more carbon results in lower chromium to maintain a martensitic microstructure. Thus, higher strength is attained at the expense of corrosion resistance. They generally have lower corrosion resistance than ferritic and austenitic stainless steels.
Duplex Stainless Steels: This type of stainless steel consists of a combination of austenitic and ferritic metallurgical structures, usually in equal amounts. It is created by adding more chromium and nickel to a standard martensitic stainless steel, promoting a duplex ferritic-austenitic microstructure. Since they do not have a constant ferritic and austenitic microstructure, they respond to heat treatment. Austenitic stainless steel is far superior to ferritic in terms of corrosion resistance and mechanical properties. However, they are highly susceptible to stress corrosion cracking. Stress corrosion cracking happens when a crack propagates when the material is subjected to a highly corrosive environment. This can lead to the sudden failure of ductile materials. A ferritic microstructure is resistant to stress corrosion cracking. By combining the ferritic phase with the austenitic phase, added resistance to stress corrosion cracking is obtained. Aside from improved corrosion resistance and mechanical properties, the price of duplex stainless steels is more stable than austenitic. This is attributed to the lower nickel content. The most common grade is the standard duplex 2205. Duplex stainless steels are not covered by AISI designation.
Precipitation Hardening Stainless Steels: These are stainless steels that can further be modified by precipitation hardening. Initially, precipitation hardening stainless steels are supplied in a solution annealed condition. Manufacturers can perform an additional aging process to attain the desired mechanical properties. Note that this heat treatment has a different mechanism than hardening martensitic stainless steels. In precipitation hardening, precipitates or secondary phase particles are allowed to form at elevated temperatures usually lower than the curie temperature. The formation of these secondary phase particles is promoted by alloying elements such as copper, niobium, aluminum, and titanium. Their growth rate, size, and dispersion are controlled by temperature and time. These secondary phase particles act as dislocation sites to the crystal structure, improving the metal's overall toughness and strength. Moreover, unlike the martensitic varieties, they have comparable corrosion resistance with austenitic and ferritic stainless steels.
Source 21 is a supplier of stainless in coils and strips in all grades including grades 316 and 316L. Processing of stainless steel coils includes cutting to length, polishing, masking, and tempering rolls, which are custom boxed, export crated, or specialty skid mounted. Source 21 supplies stainless steel to several industries including aerospace, roll forming, automobile manufacturing, and food processing. The company’s goal is to supply stainless steel to meet the needs of their customers, whether it is regular grades stainless steel or exotic ones.
Cleveland-Cliffs is one of the largest producers of flat rolled stainless steel in North America with operations for mining iron ore in Michigan and Minnesota. The company provides stainless steel to the auto industry and is dedicated to steel recycling and sustainability. Cleveland-Cliffs produces all five types of stainless steel including grades 304 and 304L and provides steel for the auto industry and other manufacturing industries.
Allegheny Technologies is a producer of a wide range of metals and specialty metals including various grades of stainless steel. The company offers a complete line of stainless steels as well as specialty forms of stainless steel such as superaustenitic and superferritic stainless steels. ATI produces stainless steel using hot rolling in a wide range of product sizes and thicknesses. The company is capable of fulfilling customer orders quickly with short lead times.
Acerinox is a Spanish company that manufactures all forms of stainless steel for the transportation industry, industrial equipment manufacturing, food processing, and environmental technology industry. The company produces stainless steel plates, hot and cold coils, hot and cold sheets, strips, and discs. With locations around the world, Acerinox supplies its various forms of stainless steel to a wide range of industries and customers.
Aperam is located in Luxemburg and supplies all forms of stainless steel to 40 countries with a production capacity of 2.5 tons at five production facilities around the world. The company supplies stainless steel iron coils, sheets, tubes, discs, flat bars, strips, and heavy plates with a service center in Sterling Heights, Michigan that provides flat stainless steel. Aperam prides itself on its innovative and high performance solutions to technological and manufacturing problems. All of its stainless steel products are recyclable, which are produced with an exceptionally low CO2 footprint.
As mentioned in the previous chapter, stainless steel 316 belongs to the austenitic group in which nickel is added as the austenite stabilizer. The standard composition of stainless steel is 16–18% chromium, 10–14% nickel, 2–3% molybdenum, 2% manganese (maximum), 0.75% silicon (maximum), 0.10% nitrogen (maximum), 0.08% carbon (maximum), 0.045% phosphorus (maximum), 0.03% sulfur (maximum), and iron as the balance. Other alloying elements, such as titanium and niobium, are added to make other grades. The compositions of different stainless steel grades are summarized below.
Grade | Alloying Elements (Percent) | |||||||||
---|---|---|---|---|---|---|---|---|---|---|
C | Cr | Ni | Mo | Mn | Si | N | P | S | Others | |
316 | 0.08 | 16-18 | 10-14 | 2-3 | 2.0 | 0.75 | 0.10 | 0.045 | 0.03 | |
316L | 0.03 | 16-18 | 10-14 | 2-3 | 2.0 | 0.75 | 0.10 | 0.045 | 0.03 | |
316H | 0.04 - 0.10 | 16-18 | 10-14 | 2-3 | 2.0 | 0.75 | 0.045 | 0.03 | ||
316Ti | 0.08 | 16-18 | 10-14 | 2-3 | 2.0 | 0.75 | 0.10 | 0.045 | 0.03 | Ti¹ |
316Cb | 0.08 | 16-18 | 10-14 | 2-3 | 2.0 | 0.75 | 0.10 | 0.045 | 0.03 | Cb² |
316N | 0.03 | 16-18 | 10-14 | 2-3 | 2.0 | 0.75 | 0.10 - 0.16 | 0.045 | 0.03 | |
316LN | 0.03 | 16-18 | 10-14 | 2-3 | 2.0 | 0.75 | 0.10 - 0.16 | 0.045 | 0.03 |
Notes:
Enumerated below are the alloying elements of stainless steel 316 and their effects on the alloy‘s properties.
Carbon: This is the main alloying element of steel. Iron alone has poor mechanical properties, but when alloyed with varying amounts of carbon imparts a wide range of hardness and strength. Adding carbon makes the steel harder and stronger but more brittle. Decreasing it improves ductility. Also, adding sufficient amounts of carbon allows the steel to respond to heat treatment. However, there is a certain limit to how much carbon can be added. For austenitic stainless steels, adding too much carbon promotes sensitization. Sensitization is the precipitation of chromium carbides at the grain boundaries that consumes the chromium from the adjacent regions. This makes the stainless steel susceptible to intergranular corrosion.
Nickel: Nickel is added to stainless steel to form or retain an austenitic microstructure at room and low temperatures. The minimum amount required to stabilize an austenitic microstructure is around 8 to 9%. In austenitic stainless steels, 10 to 14% is required due to the addition of molybdenum, another ferrite former aside from chromium.
Titanium: Titanium is a stabilizer added to standard or straight 316 stainless steels to form the 316Ti variant. Titanium is a stronger carbide-former than chromium. At high temperatures, chromium tends to react with carbon and precipitate at grain boundaries. In stainless steel 316Ti, titanium reacts with carbon instead of chromium. This maintains the amount of chromium present within the austenite, resulting in the high-temperature stability of 316Ti. By lessening the formation of precipitates, intergranular corrosion resistance is improved.
Stainless steel 316 is the second most widely used stainless steel grade next to 304. 316 is preferred due to the presence of molybdenum, which makes it suitable for applications with is a higher risk of a chemical attack, especially from chloride solutions. Aside from the alloying of molybdenum, most of its desirable properties are attributed to its austenitic microstructure.
Summarized below are the general properties of stainless steel 316 and its variants. Most of these properties describe their advantages over other types of stainless steel.
Corrosion Resistance: All stainless steel 316 grades have molybdenum as an alloying element that further improves corrosion resistance, particularly pitting corrosion. Pitting is a highly localized type of corrosion that creates shallow holes on the surface of the metal. This takes place in the presence of solutions containing chloride ions, such as seawater. High resistance to pitting corrosion makes stainless steel 316 recommended for marine applications. Molybdenum, together with chromium and nitrogen, is one of the factors in determining the pitting index or pitting resistance equivalence number.
Weldability: Austenitic stainless steels experience fewer negative effects from welding. They can retain their toughness and impact strength since they do not transform to martensite. They are less susceptible to cold cracking as encountered in martensitic stainless steels. Because of these, they are suitable for welding fillers even in welding different stainless steel groups.
Below are the different grades of stainless steel 316. These are modifications of the standard 316 composition wherein the amount of carbon is decreased or alloying elements called stabilizers are added. This is to improve or retain its mechanical properties and corrosion resistance after welding. The high carbon and high nitrogen variants are used for their increased hardness and creep resistance.
316L: As of now, this is perhaps the most widely used variant compared to the standard and the 316Ti grade. Originally, low carbon grades were more expensive and difficult to produce until the introduction of the production process known as Argon Oxygen Decarburization (AOD). This grade of stainless steel 316 has a lower carbon content to reduce the effects of sensitization.
Lower carbon content means less formation of chromium carbide precipitates and less depletion of chromium in regions near the grain boundaries. This improves the retention of toughness and corrosion resistance of the stainless steel after welding.
316H: This grade contains higher amounts of carbon, improving its thermal stability and creep resistance. Its corrosion resistance is comparable to 316L. However, due to the high carbon content, it is prone to sensitization which makes welding joints vulnerable to corrosion.
Stainless steel grade 304 is an austenite stainless steel that is the most widely used and versatile of the various grades of stainless steel. It is a part of the T300 series stainless steels with...
Stainless steel grades each consist of carbon, iron, 10.5%-30% chromium, nickel, molybdenum, and other alloying elements. It is a popular metal used in various products, tools, equipment, and structures that serve in many industrial, commercial, and domestic applications...
Stainless steel can be fabricated using any of the traditional forming and shaping methods. Austenitic stainless steel can be rolled, spun, deep drawn, cold forged, hot forged, or stippled using force and stress...
Stainless steel tubing is a multifaceted product that is commonly utilized in structural applications. Stainless steel tubing diameters and variations vary greatly based on the application requirements and are...
Perforated stainless steel is cut, punched, or stamped to produce a precise pattern of holes or apertures. It is used for functional reasons, such as filtration or ventilation, and aesthetic ones, such as architectural accents...
Stainless steel hinges connect two components while allowing them to move in relation to one another. They can have various leafs shaped like rectangles and other forms depending on the type of stainless steel hinge. Stainless steel hinge leafs are...
Stainless steel tanks are widely used in food, beverage, dairy, medicine, cosmetics, and other manufacturing processes where cleanliness and purity are important. These are also used in industrial plants for storing chemicals and gases where strong resistance from chemical degradation is required...
Titanium metal, with the symbol Ti, is the ninth most abundant element in the earth‘s crust. It does not occur in large deposits, yet small amounts of titanium are found in almost every rock...