Aluminum 1100
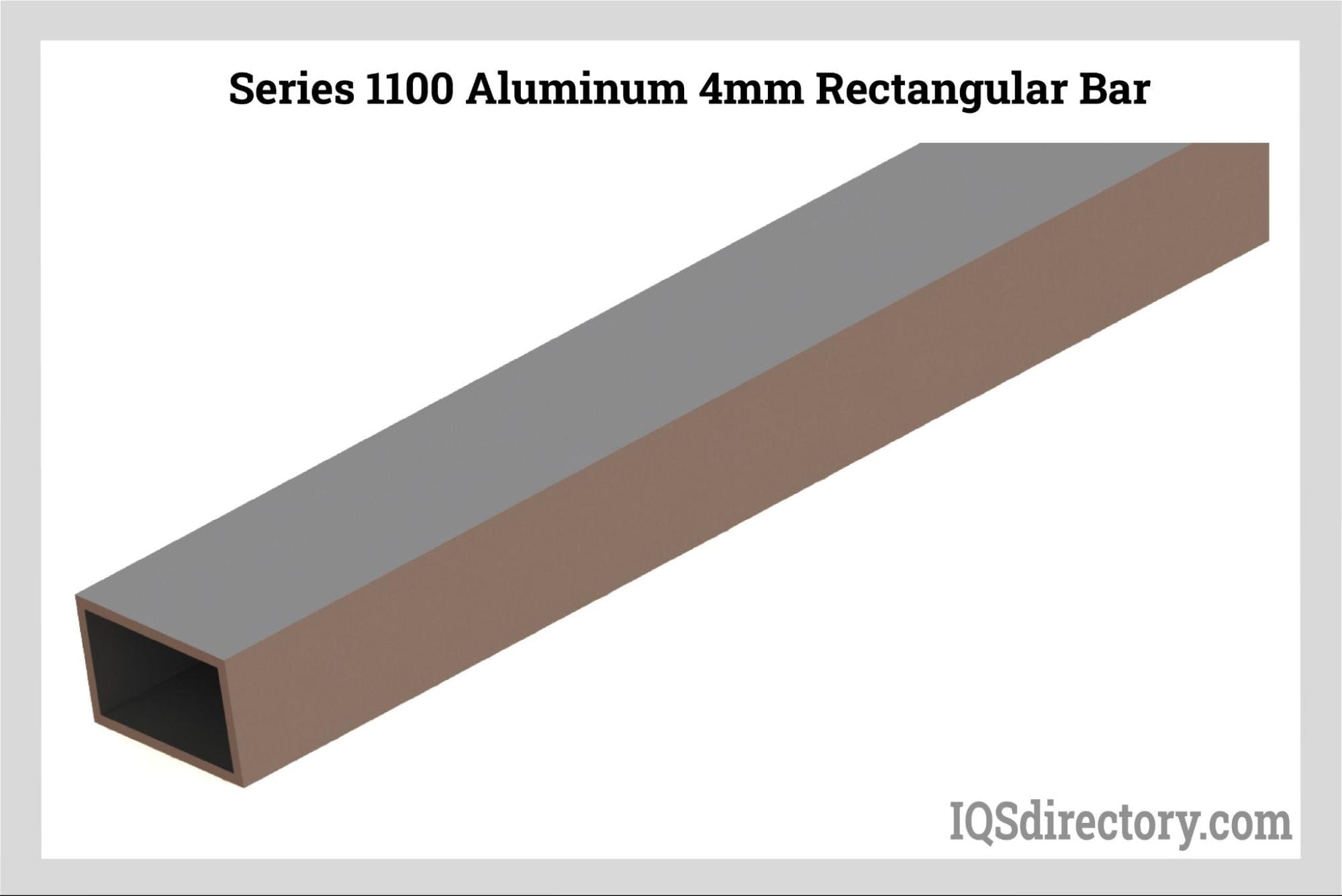
Aluminum 1100 is the softest of the aluminum alloys, which makes it easy to shape and form into a wide range of products for industrial and home use. It can be cold and hot worked but is frequently shaped by...
Please fill out the following form to submit a Request for Quote to any of the following companies listed on
This article takes an in-depth look at the types of aluminum.
Read further and learn more about:
Aluminum, the most abundant metal in Earth's crust, is rarely found in its pure elemental form. Its various alloys are prized for their low density, high strength-to-weight ratio, durability, and resistance to corrosion. Being 2.5 times less dense than steel, aluminum serves as an excellent alternative in applications where mobility and portability are key.
Aluminum alloys are known for their ductility and malleability, making them easy to shape and machine. They also excel as electrical and thermal conductors and possess non-sparking and non-magnetic properties. Aluminum is highly recyclable, with re-melting requiring just 5% of the energy used to produce the primary metal. Impressively, 75% of aluminum can be reclaimed for reuse without any loss of its original properties, contributing to its sustainability and environmental friendliness.
Pure aluminum is alloyed with various elements to enhance its mechanical properties, corrosion resistance, formability, and machinability, leading to different grades. The Aluminum Association developed and maintains the nomenclature for these standard aluminum grades, classifying them based on their primary alloying element and how they respond to mechanical and thermal treatments.
Aluminum alloys are primarily classified into two types: wrought and cast. These categories use distinct identification numbering systems. The key difference lies in their processing methods: cast aluminum is melted and poured into molds, whereas wrought aluminum is manipulated in its solid form.
The various manufacturing processes yield aluminum alloys with distinct properties, making it challenging to select the right grade for a project. Cast aluminum contains a higher proportion of alloying materials, whereas wrought aluminum offers greater tensile strength.
Wrought aluminum has exceptional mechanical strength and can be formed into many shapes. It is produced by smelting aluminum ingots with a measured amount of an alloying metal, resulting in the grade's composition. The smelted aluminum alloy is cast into billets or slabs and mechanically processed by rolling, forging, or extrusion. Heat treatment further improves the aluminum alloy's natural properties.
The advantages of wrought aluminum include:
Each wrought aluminum grade is identified by a four-digit code:
Here is a summary of the wrought aluminum series: Series 1000 represents the purest aluminum, featuring the lowest yield and tensile strength. In contrast, the 7000 series, which includes alloys of magnesium, zinc, and copper, offers the highest tensile and yield strength.
Temper | Composition | Tensile Strength (MPa) | Yield Strength (MPa) |
---|---|---|---|
1000 Series | 99.00%-99.99% Aluminum | 82-166 | 28-152 |
2000 Series | 2.2%-6.8% Copper | 110-283 | 41-248 |
3000 Series | 0.3%-1.5% Manganese | 110-283 | 41-248 |
4000 Series | 3.6%-13.5% Silicon | 172-414 | 45-180 |
0.1%-4.7% Copper | |||
0.05%-5.5% Magnesium | |||
5000 Series | 0.05%-5.5% Magnesium | 124-352 | 41-345 |
6000 Series | 0.2%-18% Silicon | 124-310.3 | 55.2-276 |
0.35%-1.5% Magnesium | |||
7000 Series | 0.8%-8.2% Zinc | 228-572 | 103-503 |
0.1%-3.4% Magnesium | |||
0.05%-2.6% Copper |
The following are the series of wrought aluminum grades:
The 1000 series of aluminum alloys is non-heat treatable and consists of at least 99.0% pure aluminum with minimal alloying elements. This series is known for its outstanding corrosion resistance and superior electrical and thermal conductivity. Due to its ductility and relatively soft nature, 1000 series aluminum is easily formable and hardens slowly with work. It is ideal for applications that require significant deformation. While it is weldable, it has a narrow melting range that needs to be managed. However, a notable limitation of the 1000 series is its very low yield and tensile strength.
The 2000 series aluminum grades are composed of 0.7-6.8% copper, along with trace amounts of silicon, manganese, magnesium, and other elements. Copper serves as the primary alloying element, enhancing the strength and hardness of these grades while also improving their machinability. These alloys retain their high strength across a broad temperature range.
2000 series aluminum grades are known for their high performance and strength, making them ideal for aircraft and aerospace applications. However, the inclusion of copper in these alloys reduces their ductility and corrosion resistance.
The 2000 series consists of heat-treatable aluminum alloys that can be strengthened through precipitation hardening. This process enhances the alloy's hardness by forming the intermetallic compound Al2Cu during heat treatment. However, these intermetallic compounds can complicate welding, as some 2000 series alloys are prone to issues such as hot cracking and stress corrosion cracking, making them less suitable for arc welding.
The 3000 series aluminum grades are characterized by a manganese content ranging from 0.05% to 1.5%, which is the primary alloying element. Manganese enhances the alloy's mechanical strength compared to pure aluminum, with this strength being stable across a broad temperature range. These grades also offer excellent corrosion resistance, high ductility, and good formability. Although they cannot be heat-treated, they can be hardened through cold working. Additionally, 3000 series aluminum is well-suited for welding applications.
The 4000 series of aluminum grades include 3.6-13.5% silicon, along with minor quantities of copper and magnesium. Silicon is the primary alloying element, which reduces the alloy's melting point and enhances fluidity when molten. This characteristic makes the 4000 series particularly effective as a filler material for welding and brazing.
Certain grades within the 4000 series are heat-treatable based on the copper and magnesium content in the alloy. These additions enhance the alloy's response to heat treatment. When combined with heat-treatable aluminum grades, the heat-treatable grades can also be suitable for welding applications.
The 5000 series aluminum alloys contain 0.5-5.5% magnesium. These alloys are non-heat-treatable but can be strengthened through cold working. They offer moderate to high strength and high ductility when annealed. Additionally, 5000 series aluminum alloys are weldable and resistant to corrosion and alkaline environments.
The 5000 series grades contain 3.5% magnesium and are not ideal for high-temperature applications due to their susceptibility to stress corrosion. Known as marine grades of aluminum, the 5000 series is valued for its resistance to saltwater corrosion.
The 6000 series aluminum grades primarily include 0.2-1.8% silicon and 0.35-1.5% magnesium as their key alloying elements. These grades can undergo solution heat treatment to boost their yield strength. During aging, the precipitation of magnesium-silicide further strengthens the alloy. Higher silicon content improves precipitation hardening but may reduce ductility. This reduction can be countered by adding chromium and manganese, which help to inhibit recrystallization during heat treatment. However, welding these grades can be challenging due to their susceptibility to solidification cracking, requiring careful welding techniques.
The 7000 series aluminum alloys feature zinc as their primary alloying element, ranging from 0.8% to 8.2%. Known for their exceptional strength, these alloys are heat treatable, allowing for solution heat treatment and aging to boost yield strength. The presence of intermetallic compounds like MgZn2 and Mg3Zn3Al2t contributes to their hardness. Enhanced corrosion resistance is achieved with the inclusion of copper. However, many alloys in this series are not suitable for welding due to their vulnerability to stress corrosion cracking and hot cracking.
Cast aluminum is made from bauxite dissolved in caustic soda, causing the alumina to crystallize and settle to the bottom of the container. The alumina is broken down using an electric current that separates the aluminum from the oxygen. The aluminum from the process is sent to a casting house to remove impurities and to be formed in pure aluminum billets.
After purifying and shaping the aluminum into billets, it is melted and combined with alloying elements. The resulting mixture, consisting of aluminum and alloys in various proportions, is then poured into molds to create products or shaped for additional processing.
Cast aluminum alloys generally have lower tensile strength compared to wrought aluminum due to defects introduced during the molding process, making them more prone to cracking and shrinkage. Nevertheless, cast aluminum remains a cost-effective choice that can be molded into a wide range of shapes. When molten, cast aluminum readily conforms to the mold, filling every detail and crevice.
Each cast aluminum grade is designated by a four-digit code that includes a decimal point.
Grade | Composition (wt%) | Tensile Strength (MPa) | Yield Strength (MPa) |
---|---|---|---|
1XX.X | 99.00%-99.99% Aluminum | 131-448 | 28-152 |
2XX.X | 4.00%-460% Copper | 131-276 | 90-345 |
3XX.X | 5.00%-17.00% Silicon | 117-172 | 66-172 |
4XX.X | 5.00%-12.00% Silicon | 117-172 | 41-48 |
5XX.X | 5.00%-12.00% Magnesium | 131-448 | 62-152 |
6XX.X | Not Used | ||
7XX.X | 6.20%-7.50% Zinc | 207-379 | 117-310 |
Here are the series of cast aluminum alloys:
The 1XX.X series aluminum grades are known for their high electrical and thermal conductivity, excellent weldability, and superior corrosion resistance and finishing qualities.
The 2XX.X series aluminum grades are heat-treatable and known for their high strength and low fluidity. However, they exhibit low corrosion resistance and ductility, and are prone to hot cracking.
The 3XX.X series aluminum grades are heat-treatable, offering high strength along with excellent wear and crack resistance. However, their higher copper content can reduce their corrosion resistance, and they tend to have lower ductility.
The 4XX.X series aluminum grades are non-heat-treatable and offer moderate strength. Known for their excellent machinability, these grades feature high ductility and are also noted for their good impact resistance, corrosion resistance, and casting properties.
The 5XX.X series aluminum grades are not heat-treatable but offer excellent corrosion resistance and a pleasing appearance when anodized. Additionally, they feature moderate to high strength, good machinability, and favorable casting properties.
The 7XX.X series aluminum grades are heat-treatable, offering high strength, excellent corrosion resistance, dimensional stability, and good finishing qualities. However, they are known for their poor casting properties.
The 8XX.X series aluminum grades are non-heat-treatable. They offer excellent machinability and wear resistance because of their low coefficient of friction, but they have relatively low strength.
The temper designation system helps assess how an alloy will respond to welding and other fabrication processes, based on its strengthening and hardening treatments. This system applies to both wrought and cast aluminum alloys.
The temper designation of an aluminum alloy consists of a capital letter followed by a number or numbers, indicating whether the alloy is strain-hardened or thermally treated. This designation is separated by a hyphen from the alloy number (e.g., 5052-H32).
Letter | Treatment |
---|---|
F | As fabricated alloys, no treatment was performed. |
O | Annealed |
H | Strain-hardened or cold-worked |
W | Solution heat-treated |
T | Thermally treated |
Aluminum's widespread use stems from its abundance, versatile properties, and excellent recyclability. This metal finds application in everything from cookware to the structural framework of high-rise buildings. Its ability to be shaped, bent, formed, and welded into various configurations makes it a top choice for structural applications.
Although flat, thick pieces of aluminum are available for shipping, aluminum coils are widely used to store and ship aluminum. They have a hollow core wrapped with aluminum. Aluminum coils come in several different lengths, widths, and thicknesses. All different alloyed grades are produced in coils and shipped for manufacturing purposes.
Aluminum coils can be painted, diamond-coated, or heat-treated for enhanced durability. They are designed to endure constant use and harsh conditions. However, the main limitation of aluminum coils is their thickness; some grades may be too thick to wrap around the core.
Coiled aluminum plays a crucial role in various industrial processes, such as the production of air conditioners, automobiles, aircraft, furniture, cases, and construction materials. In metalworking, aluminum coils are positioned at the start of the process, with the aluminum material fed into progressive metal shaping machines for further processing.
Aluminum 1100 is commonly used in fin stocks, heat exchangers, and heat sinks because of its excellent thermal conductivity. It is typically cold worked at or near room temperature. As one of the softest aluminum alloys, Series 1100 is easily shaped through spinning, stamping, and drawing processes, all without the need for heat. It can be formed into various shapes, including foil, plates, round bars, rods, sheets, strips, and wire.
Series 1100 aluminum is employed in the manufacturing of rivets, deep-drawn components like pots and kitchen sinks, railroad tank cars, and reflectors. Its excellent conductivity also makes it ideal for electrical applications.
Aluminum 2011 is employed in manufacturing machines, automotive components, weapons, munitions, fasteners, pipe and tube fittings, and atomizer parts. Its high mechanical strength facilitates machining, and it is classified as a free-machining alloy (FMA) that can be efficiently shaped using a lathe.
Its exceptional machining capabilities enable the creation of complex and intricate parts with precise details using Series 2011 aluminum. While it has poor corrosion resistance, this issue is effectively addressed through anodization, which offers excellent surface protection. Although aluminum 2011 cannot be welded, its ability to produce precise details through machining eliminates the need for welding.
Aluminum 2024 is the top choice for aircraft and aerospace applications due to its superior strength and fatigue resistance. As one of the most well-regarded high-strength aluminum alloys, it is ideal for manufacturing aircraft components. Its exceptional strength-to-weight ratio and smooth finish make it a preferred material for applications requiring durability and precision.
Aluminum 2024 stands out due to its unique properties, allowing it to be annealed and heat treated—features not commonly found in other aluminum alloys. However, similar to series 2011, aluminum 2024 cannot be arc or gas welded, though it can be joined using spot, seam, or flash welding methods.
Similar to Series 2011, aluminum 2024 exhibits low corrosion resistance, which can be mitigated through anodization or by cladding it with a surface layer of pure aluminum. Consequently, it is extensively used in marine equipment, wing tension members, bolts, nuts, hydraulic valve components, gears, shafts, couplings, and pistons.
Aluminum 3003 is commonly used in various applications, including heat exchangers, pressure vessels, storage tanks, and fuel tanks. It is also suitable for food-handling items like cooking utensils, pans, pots, ice cube trays, and refrigerator panels. Additionally, this versatile aluminum alloy is crafted into building products such as roofing materials, sidings, gutters, garage doors, insulation panels, and downspouts.
Aluminum 5005 is widely used in construction for applications such as roofing, siding, and furniture, and it is also an effective electrical conductor. Its adaptability makes it suitable for chemical and food handling equipment, HVAC systems, tanks, vessels, and high-strength foils. Additionally, its bright finish is perfect for decorative purposes.
Aluminum 5083 is utilized in various applications, including shipbuilding, vehicles, rail cars, pressure vessels, and drilling rigs.
Aluminum 5052 is commonly employed in a variety of applications including food processing equipment, cooking utensils, heat exchangers, and chemical storage tanks. It is also utilized in automobile and truck panels, flooring panels, rivets, wires, treadplates, and containers.
Aluminum 6061 can be crafted into tubes, beams, and angles with rounded corners. It is commonly utilized in pipelines, tank fittings, railroad cars, trucks, marine components, and furniture.
Aluminum 6063 is commonly employed in architectural applications, including stair rails, furniture, window frames, doors, and sign frames. It is also versatile enough to be fabricated into tubes, beams, angles, and channels.
Aluminum 6262 is utilized in a variety of applications, including screw machine products, hinge pins, knobs, nuts, couplings, valves, marine fittings, pipeline fittings, and decorative hardware.
Aluminum 7075 is highly favored for aerospace and aircraft applications due to its exceptional strength. Additionally, it finds applications in bicycle components, high-performance sporting gear, molds, and industrial tooling.
The 1XX.X series is used in the production of electrical rotors.
The 2XX.X series is utilized in manufacturing automotive and aircraft engine cylinder heads, diesel engine pistons, bearings, and components for exhaust systems.
The 3XX.X series is used in various applications, including compressor and pump components, automotive cylinder blocks and heads, motor parts, and castings for marine and aircraft use.
The 4XX.X series is utilized in pump casings, pots, pans, and dental equipment.
The 5XX.X series is designed for decorative architectural applications and sand casting components.
The 7XX.X series is utilized in automotive components and mining machinery.
The 8XX.X series is used in slide bearings and bushings.
Aluminum products are available in the following forms:
Aluminum foils are produced by flattening and thinning aluminum sheets through a rolling mill. Their thickness varies between 0.006 and 0.2 mm (6 to 200 microns). Known for their malleability and pliability, aluminum foils can be easily bent and wrapped around objects. They are commonly used in packaging, electromagnetic shielding, and various other industrial applications.
Aluminum foil serves various purposes, including thermal insulation, decoration, and mold creation. It is available in different tempers, each with its own processing characteristics. The tempering of aluminum foil is denoted by the HXX designation, where "H" indicates the work hardening process used to enhance the foil's strength. The following two or three numbers specify the type of tempering applied.
The second digit of the HXX code is the degree of strain hardening.
Temper | Type |
---|---|
Hx2 | Quarter Hard |
Hx4 | Half Hard |
Hx6 | Three Quarters Hard |
Hx8 | Full Hard |
Hx9 | Extra Hard |
A third digit might be used for wrought products, where H111, H311, and H321 indicate that the aluminum foil has been strain hardened to a lesser degree than usual.
Aluminum bars come in various shapes—including round, flat, hexagonal, and square—and are offered in a range of thicknesses, widths, and diameters. When selecting aluminum bars, it's important to choose the grade that best meets the requirements of the application, as each grade differs in strength, machinability, and corrosion resistance.
Minimum Strength in KSI | ||||
---|---|---|---|---|
Alloy | Machinability | Ultimate | Yield | Corrosion Resistance |
2011-T3 | A++ | 45 | 38 | C |
6262-T6511 | B | 42 | 35 | A |
2017-T4, T451 | A | 55 | 32 | C |
2024-T4, T351 | A | 62 | 42 | C |
6061-T6-T651 | B | 42 | 35 | A |
7075-T6, T651 | A | 77 | 66 | C |
6063-T6 | C | 30 | 25 | A |
063-T5 | D | 21 | 15 | A |
Aluminum bars are manufactured through an extrusion process, where an annealed aluminum billet is pressed through a die using compressive force. As the billet is forced through the die, it assumes the shape of the die's profile. This extrusion method produces aluminum bars in round, rectangular, square, and hexagonal shapes.
Aluminum pipe, with its tubular shape, is designed for the movement and flow of liquids and gases. Like other aluminum products, it is lightweight, corrosion-resistant, and produced through an extrusion process that results in seamless pipe. Aluminum pipes typically come in round and square shapes, with custom designs available to suit specific applications.
The aluminum used for producing aluminum pipe is high-strength, heat-treated hard aluminum, which is strengthened through heat treatment. This type of aluminum exhibits medium plasticity in its annealed, quenched, and thermal states, and has good spot welding characteristics. Aluminum pipe can be machined through cold working and quenching, and its corrosion resistance can be further enhanced through anodizing and coating.
Aluminum pipe has a vast range of applications, including aviation, the automotive industry, chemical processing, agriculture, and shipbuilding. Its lightweight nature, strength, and conductivity make it well-suited for heavy-duty industrial uses. The properties of aluminum pipe can vary depending on the grade of aluminum used in its production.
While aluminum tubes resemble aluminum pipes in appearance, they serve different purposes and functions. Both aluminum pipes and tubes are long, hollow, and can be either rectangular or round in shape. However, aluminum tubing is defined by its outer diameter (OD) and wall thickness (WT), which are measured in inches or millimeters.
Aluminum tubing is lightweight with good heat conductivity and is used for hydraulic systems, airplane fuselages, HVAC equipment, and appliances. Each of the various types of aluminum tubing are custom designed to fit the needs of specialized applications. Square tubing is used for machine parts while rectangular tubing is used for interior and exterior molding. Round tubing is ideal for structural supports and framework.
Aluminum grades 6061 and 6063 are commonly used for manufacturing aluminum tubing. Grade 6061 is known for its high strength and can be heat treated to enhance its corrosion resistance. In contrast, grade 6063 is a lower-strength aluminum, making it ideal for architectural details and applications where high strength is not required.
Aluminum sheets are created by repeatedly rolling aluminum slabs under high pressure until they become thin and flat. The thickness of the sheets varies based on the gauge of the aluminum.
Gauge | Thickness | Thinckness Tolerance |
---|---|---|
(0.250" | 6.35mm) | ±0.014" | |
(0.118" | 4.78mm) | ±0.009" | |
8 gauge | (0.1285" | 3.26mm) | ±0.007 | ±0.18mm |
10 gauge | (0.102" | 2.59mm) | ±0.006 | ±0.15mm |
11 gauge | (0.091" | 2.31mm) | ±0.0045" |
12 gauge | (0.081" | 2.06mm) | ±0.0045" |
14 gauge | (0.064" | 1.63mm) | ±0.0040" |
16 gauge | (0.051" | 1.30mm) | ±0.0035" |
18 gauge | (0.040" | 1.02mm) | ±0.0035" |
20 gauge | (0.032" | 0.81mm) | ±0.0030" |
Aluminum sheets are favored for their lightweight, impressive strength, and ability to withstand demanding conditions. Despite their ease of handling, these sheets are highly durable, making them an ideal choice for industries that need to reduce weight without compromising on resilience.
Aluminum sheets are primarily used in the production of cans and packaging materials. Their formability and corrosion resistance make them ideal for beverage cans, food containers, and various packaging solutions. The tight seal provided by aluminum helps preserve the freshness and quality of the contents. Additionally, aluminum's recyclability enhances its popularity in the packaging industry.
The automotive industry leverages the strength-to-weight ratio of aluminum sheets to improve fuel efficiency and vehicle performance. These sheets are used in body panels, hoods, doors, and structural components, offering a lightweight option that maintains safety and durability. Additionally, aluminum sheets are widely used in cookware manufacturing and construction applications, including roofing, siding, and gutters.
Aluminum plates are manufactured using a rolling process similar to that used for sheets but are thicker and available in various thicknesses depending on the gauge and grade of aluminum. Their increased thickness provides greater strength and rigidity, making them ideal for heavy-duty applications.
The characteristics of aluminum plates make them well-suited for use in the transportation, aerospace, aircraft, marine, and military industries, where they serve as structural supports, body panels, wings, and fuselage sections. Their favorable strength-to-weight ratio enhances fuel efficiency and performance. Additionally, the corrosion resistance and durability of aluminum plates make them ideal for demanding environments, including storage tanks, fuel tanks, railcars, trailers, and truck beds.
Aluminum wires are produced through a process known as wire drawing, where aluminum ingots are pulled through a die to decrease their diameter while increasing their length. Aluminum wire's electrical conductivity and strength-to-weight ratio make it a viable alternative to copper in certain electrical applications. However, a drawback of aluminum wire is its susceptibility to oxidation, which can lead to wiring deterioration and potential fire hazards.
To reduce the risks associated with aluminum wire oxidation, several precautions can be taken. One effective method is using aluminum alloy wires, which are specifically engineered to enhance resistance to oxidation and improve overall performance. Compared to pure aluminum wires, aluminum alloys offer better corrosion resistance and a longer lifespan.
As with any type of wiring, choosing the proper installation method is crucial for the effective use of aluminum wire. This involves using connectors specifically designed for aluminum wires and employing appropriate insulation to protect against moisture and environmental factors.
Brazing is a metal joining technique where aluminum brazing rods or fillers are used to join base metals by heating. When the aluminum reaches its melting point, it bonds metal pieces together or fills cracks, holes, and gaps. Brazing is favored for its exceptional strength and durability.
There are four main methods of brazing: torch, dip, fluxless vacuum, and furnace. Torch brazing uses a propane or gas torch to heat the metal. In dip brazing, the filler metal is poured around the joint area and then dipped into a molten bath. Fluxless vacuum brazing removes flux from the process using water or a chemical bath. Finally, furnace brazing involves placing the metals in a furnace, a process that requires careful monitoring.
Brazing forms robust, solid joints at lower temperatures compared to welding, allowing the base metal to retain its original properties. This method facilitates the joining of dissimilar metals while producing a smooth and visually appealing finish. In manufacturing, brazing is often fully automated and generally faster than welding.
Aluminum 1100 is the softest of the aluminum alloys, which makes it easy to shape and form into a wide range of products for industrial and home use. It can be cold and hot worked but is frequently shaped by...
The term "aluminum coil" describes aluminum that has been flattened into sheets where their width is significantly higher than their thickness and then "coiled" into a roll. Stacks of individual aluminum sheets are difficult to...
Aluminum piping and tubing is silvery-white, soft, and ductile. The metal belongs to the boron group. Aluminum is the third most abundant element present on earth. Aluminum has low density. When exposed...
Aluminized steels are steels that have been hot-dip coated with pure aluminum or aluminum-silicon alloys. This hot-dip coating process is termed hot-dip aluminizing (HAD)...
Beryllium Copper is a versatile copper alloy that is valued for its high strength and hardness, combined with good electrical and thermal conductivity. It is a non-ferrous, non-magnetic, and non-sparking metal alloy...
A variety of copper-zinc alloys are referred to together as brass. Different ratios of brass and zinc can be used to create alloys, which produce materials with various mechanical, corrosion, and thermal properties...
Copper is a ductile, malleable, and reddish-gold metal with the capacity to effectively conduct heat and electricity. Brass and bronze, two commonly used alloys, are created when copper is combined with...
The copper sheet is a highly malleable and workable metal with outstanding electrical and thermal conductivity and corrosion resistance. Copper (Cu) is a reddish, very ductile metal that belongs to Group 11 of the periodic table...
Metals are a group of substances that are malleable, ductile, and have high heat and electrical conductivity. They can be grouped into five categories with nickel falling in the category known as transition metals...
Stainless steel grade 304 is an austenite stainless steel that is the most widely used and versatile of the various grades of stainless steel. It is a part of the T300 series stainless steels with...
Stainless steel is a type of steel alloy containing a minimum of 10.5% chromium. Chromium imparts corrosion resistance to the metal. Corrosion resistance is achieved by creating a thin film of metal...
Stainless steel grades each consist of carbon, iron, 10.5%-30% chromium, nickel, molybdenum, and other alloying elements. It is a popular metal used in various products, tools, equipment, and structures that serve in many industrial, commercial, and domestic applications...
Steel service centers are companies that specialize in procuring steel directly from mills and manufacturers and supplying them to the customers. They are fundamental to the steel supply chain...
Stainless steel can be fabricated using any of the traditional forming and shaping methods. Austenitic stainless steel can be rolled, spun, deep drawn, cold forged, hot forged, or stippled using force and stress...
Stainless steel tubing is a multifaceted product that is commonly utilized in structural applications. Stainless steel tubing diameters and variations vary greatly based on the application requirements and are...
Titanium metal, with the symbol Ti, is the ninth most abundant element in the earth‘s crust. It does not occur in large deposits, yet small amounts of titanium are found in almost every rock...