Beryllium Copper
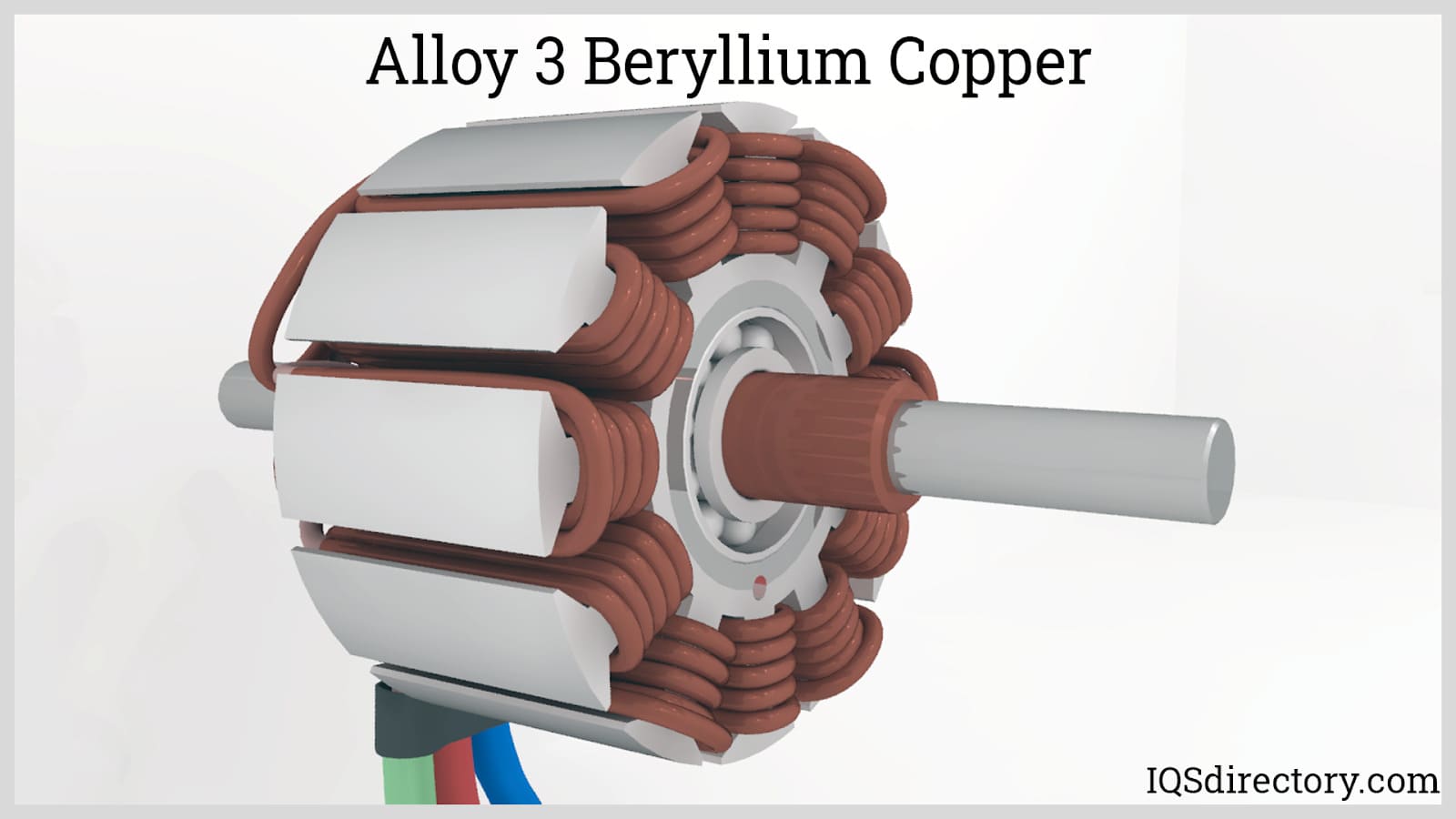
Beryllium Copper is a versatile copper alloy that is valued for its high strength and hardness, combined with good electrical and thermal conductivity. It is a non-ferrous, non-magnetic, and non-sparking metal alloy...
Please fill out the following form to submit a Request for Quote to any of the following companies listed on
This article will give detailed information about brass metal.
The article will give details on the following:
Brass is a descriptive term used to describe a wide range of copper and zinc alloys that are durable, strong, long lasting, and resistant to corrosion. Changes in the ratio of copper to zinc alters the mechanical, corrosion, and thermal properties of brass in order to meet the requirements of various applications. Generally, the percentage of copper ranges between 60% to above 80% while the percentage of zinc ranges from less than 10% up to more than 40%.
When brass has a percentage of zinc over 30%, it is referred to as high brass, an alloy that is brittle, less malleable, and difficult to shape. Additionally, an increase in the zinc content makes brass susceptible to corrosion because zinc reacts to exposure to air and water to form a zinc oxide layer.
Brass, with a high percentage of copper, is referred to as red brass or gunmetal. The increase in the percentage of copper, above 85%, makes brass malleable, ductile, corrosion resistant, and easy to shape and form. Red brass has excellent machinability, such that it can be easily cut, formed, and drilled. The downside to red brass is its cost, which is higher due to its high copper content.
Lead is added to brass as a stabilizer for the copper and zinc alloys. The addition of lead increases the malleability of brass and makes it more machinable. The allowable amount of lead added to brass is strictly regulated due to the health dangers in regard to inhaling lead. Lead content in brass is not to exceed 2%, with some states requiring a much lower content level.
The Unified Numbering System for Metals and Alloys (UNS) categorizes each type of metal with a letter followed by five numbers. The number for a metal or alloy defines their chemical composition and not their mechanical properties. The first three digits of a UNS number are taken from other numbering systems.
The designation for brass is the letter “C” followed by five numbers. The categories for brass are C20000 to C29999 for yellow brass, C30000 to C39999 for leaded brass, C40000 to C49999 for tin brass, and C87300 to C87900 for cast silicon brass. Red brass, with an 85% copper content, is identified by C23000.
The percentage of zinc determines how malleable brass is. When it has a zinc content of more than 45%, it is unworkable. Brazing (soldering) uses a coarse variant of these brasses, known as white brass, which are not economically significant but act as the base for die casting alloys.
Pliable brasses have a zinc content of less than 40% and can be cold worked. Alpha brass has a zinc content that is less than 37% and is named for its crystal structure. Alpha-beta brass, known as duplex and hot working brass, has a zinc content between 37% and 45% with a beta and alpha grain structure.
Although copper and zinc are the main alloys for the manufacture of brass, other alloys are added, such as lead, to enhance the physical and mechanical properties of brass and to increase its corrosion resistance. A form of alpha-beta brass is naval brass that has 59% copper, 40% zinc, 1% tin, and a small trace of lead. The tin content of naval brass increases its resistance to the effects of seawater.
The distinction between the various types of brass is their crystal structure, which can be face centered cubic (FCC) or body centered cubic (BCC). Brass with a high percentage of copper has a FCC crystal structure, while brass with more zinc has a BCC crystal structure. The FCC crystal structure of brass is similar to that of copper with copper atoms on the corners and center of each face of the unit cell with zinc atoms between the copper atoms.
Brass can appear reddish-gold, silvery-white, or dazzling gold. More zinc gives the alloy a silvery appearance, while more copper gives it a rose tone.
More malleable than either bronze or zinc is brass.
Brass alloys are preferred in metalworking due to their toughness and corrosion resistance. The properties and characteristics of brass change depending on the ratio of copper-to-zinc and the inclusion of additional alloys. Alloying elements, like tin, aluminum, iron, and lead, increase deformability, machinability, and the tensile strength of brass.
Although it is still a monophasic alloy, alpha brass differs from red brass in terms of its appearance, which is a yellowish hue. Certain environmental conditions and temperatures can cause alpha brass to decay, which does not deter from its use. It has better mechanical strength and ductility than the other brasses, factors that make it ideal for forming processes.
Alpha brass, known as "cartridge brass," is used for ammunition cartridges, heat exchanger tubes, evaporators and automotive radiators, fire extinguishers, rivets, bolts, and screws. It is named for its homogeneous alpha crystal structure and its less than 37% zinc content.
When zinc is combined with copper, a solution with a consistent composition is created that exhibits the alpha crystal structure. Alpha brasses can be easily cold worked, welded, rolled, drawn, bent, or brazed because they are soft, ductile, and malleable. They are referred to as 70/30 brass because of their 70% copper and 30% zinc content.
Alpha brass combines strength and flexibility to allow for cold drawing. Its higher zinc content gives it greater resistance to corrosion. It is frequently used to create electrical socket spring connections and fasteners like wood screws. Alpha brass can be easily shaped without losing its hardness and is less prone to dezincification, a condition where zinc disintegrates over time.
Alpha-beta brasses, known as "duplex brasses" or "hot-working brasses", have an alpha-grain structure and a beta-grain structure with a zinc content between 37% and 45%. They are atomically comparable to pure zinc with the zinc content determining the alpha-phase to beta-phase brass ratio. Alloys, such as aluminum, silicon, or tin, can enhance the quality of beta-phase brass.
Alpha-beta brass, which is more prevalent than alpha brass, is tougher and stronger and has less cold ductility. Alpha-beta brass is less expensive because it contains more zinc but is also more prone to dezincification corrosion.
Alpha-beta brasses are much more workable at high temperatures, despite being less malleable than alpha brasses at ambient temperatures. In addition, such brasses are resistant to cracking even when a lead component is present to enhance machinability. Alpha-beta brass is typically hot-worked through extrusion, stamping, or die casting.
A particular type of alpha-beta brass is Muntz metal or Muntz brass, which was developed in 1830 by George Frederick Muntz as a replacement for the hulls of wooden ships. It has a 60 to 40 copper to zinc ratio with traces of lead and is exceptionally durable. Although it is still valued as a ship building material, it is used today in the manufacture of fittings, pipes, and springs.
Beta brasses are stronger, tougher, and well suited for casting. They are the brightest and least golden of the brass alloys due to their high zinc low copper content. Beta brasses have a beta crystal structure, which makes them harder and stronger than alpha and alpha-beta brasses. They can only be hot wrought or shaped due to their beta crystal structure.
Beta brasses are the third type of brass alloy and are the least used. They have a 45% zinc content and are tougher and more powerful brass alloy because of their beta crystal structure. Types of beta brasses include machining brass, high tensile brass, naval brass, dezincification resistant brass, cold working brass, and casting brass
The addition of lead to brass enhances its machinability by acting as a chip breaker and lubricant. Since lead is insoluble in brass, it is distributed along the grain boundaries in the form of free particles. With lead as an alloy, brass becomes stronger and more resistant to corrosion. The amount of lead content can be up to 3.5% and be classified as high, medium, or low leaded brass.
The two types of lead brass are alpha (α) and alpha-beta (α+β). Alpha (α) lead brass is normally cold formed or hot extruded because of its low plasticity at high temperatures. Unlike alpha lead brass, alpha beta (α+β) lead brass has acceptable plasticity at high temperatures and can be forged.
Brass grades C34500 and C35300 are high lead grade brass while grade C38000 is low lead brass. High lead brass is used to make pinions, gears, valve stems, flare fittings, and adapters. Low lead architectural brass is used for thresholds and door and window frames.
Lead brass can be purchased as pipes, bars, or tubes and be adapted to fit the needs of an application. It is a hazardous metal due to its lead content and should be handled with extreme care.
Due to the ever increasing restrictions on the use of lead in products, brass manufacturers have had to use other alloys to get the same properties that are created with the addition of lead to brass. With the new alloys, such as silicon and bismuth, brass has the same machinability it has with lead as well as exceptional pressure tightness.
Although the lead in lead free brass has been replaced with other alloys, it still contains small, allowable trace portions of lead at 0.25%, which is the permitted amount. The 0.25% content of lead is 32 times less than that which was used in the past.
Brass grade C87600 is a lead free silicon brass that has exceptional machinability and pressure tightness with the same appearance as lead brass. Lead free brass valves and connectors are identified with an “LF”marking on their body and a plastic tag. By law, plumbers are no longer allowed to install lead brass in homes unless it has the required 0.25% content or less.
Lead free brass is composed of zinc and copper. The ratio of the metals varies in accordance with the needs of an application. A high copper content is ideal for applications where machining is necessary while a high zinc content is helpful when strength is required. Aluminum and manganese may be added when there is a need for specific or needed properties.
The addition of tin to tin brass increases the alloy's heat resistance and its resistance to corrosion caused by seawater, which is the reason it is referred to as "naval brass". Tin easily dissolves in solid copper-based solutions and strengthens the solutions.
When the percentage of tin rises, the alloy becomes brittle (CuZnSn complex) and unsuitable for plastic deformation. Tin concentrations in tin brass fall between 0.5% and 1.5% with popular types being HSn70-1, HSn62-1, and HSn60-1.
HSn70-1 is used for the manufacture of pipes and can be formed by hot and cold pressing because of its excellent plasticity. HSn62-1 and HSn60-1 have α and (α+β) two-phase structures with a trace amount of α phase. As a result, they have low plasticity at ambient temperatures and are deformed using high temperatures.
Tin brass or naval brass is used to build boats and ships and has a content of 59% copper, 40% zinc, 1% tin, and trace amounts of lead. Aside from its use in the construction of ships, it is used for components that are exposed to humidity and moisture.
Architectural bronze is a form of brass due to its zinc content since traditional bronze contains tin and copper. The alloys of architectural bronze are 55% to 59% copper, 2.5% to 3.5% lead, and 0.35% iron with trace amounts of zinc. Its properties make it an ideal metal for industrial applications due to its affordability, durability, and corrosion resistance.
The methods used to shape architectural bronze include hot forming, bending, brazing, soldering, butt welding, and machining. It is hot-formed at 1150°F up to 1350°F (621°C up to 732°C) and annealed at 800°F up to 1100°F (426°C up to 593°C).
Manganese brass is an alloy of copper and zinc with a 3% manganese content and is able to handle heavy loads at high speeds. Its UNS grade is C86300 and is often referred to as manganese bronze. The strength and durability of manganese brass makes it ideal for use as heavy load bearings, hydraulic cylinder parts, and large valve stems.
The main characteristics of manganese brass are its exceptional strength and corrosion resistance. Since manganese is highly soluble in solid brass, the addition of 1% to 4% of it to brass radically improves the properties of brass. Manganese brass has an alpha and alpha beta crystal structure and can be hot or cold worked.
Manganese brass has a Rockwell hardness of B95 and is available in bars and rods. In either form, it is wear resistant and maintains its strength over time due to its excellent fatigue resistance. It is often used in applications that require corrosion resistance, anti-seizing properties, and high strength.
The uses for manganese brass include applications with heavy loads, require shaft hardness, and operate in non-abrasive conditions since abrasive applications can cause surface deformation and weakness in manganese brass. In the aerospace industry, manganese brass is used for landing gear parts, bearings, bushings, gears, and screw nuts.
Iron brass has an alpha beta crystal structure and less than 1.5% of iron content. It has a silver appearance and is a tough and strong alloy with plasticity at high temperatures. Iron brass contains 50% to 61% copper, 17% to 19% zinc, 21% to 30% nickel, and less than 1.5% iron.
In the manufacturing process, iron is precipitated into a molten mixture of copper, zinc, and nickel. Iron brass has an alpha beta (α+β) crystal structure and distorts in cold environments.
Two types of iron brass are Alloy 280 (Muntz Metal) and Alloy C360 (Free Machining Brass). Both alloys have 60% of copper and 35% to 40% of zinc. Muntz metal has slight traces of iron in its content and is used for the hulls of ships. Free machining brass includes a lead content with its iron content and is extremely easy to machine.
The addition of iron to a metal increases its hardness. In the cases of Muntz metal and free machining brass, iron adds to their hardness and makes it possible for them to be forged, which is not possible for any pure copper and most of its alloys.
Nickel brass has a gold color, which varies in accordance with the amount of nickel and does not discolor or tarnish over time. The use of nickel as an alloy increases the recrystallization temperature of brass and produces a finer grain. The nickel content of nickel brass significantly increases brass’ resistance to the effects of air and seawater corrosion.
As with all forms of brass, nickel brass begins with copper and zinc. Unlike other brass metals that are composed of 60% copper and 40% zinc, nickel brass is composed of 60% copper, 20% zinc, and 20% nickel with variations in the color determined by the amount of nickel. Nickel brass is often referred to as nickel silver or German silver due to its silver appearance.
Nickel brass has the same corrosion resistance properties as other brass metals with additional properties due to the nickel content. A high nickel content in nickel brass gives the alloy superior tarnish resistance and resistance to stress corrosion cracking.
A common use for nickel brass is as material for the production of coins since it is difficult to duplicate and has a unique electromagnetic signature, which makes it ideal for coin validators. One of the well known uses for nickel brass is as material for the manufacture of musical instruments.
Zinc dissolved in copper at less than 35% zinc content creates single-phase brass. The main method used to deform single-phase brass is cold rolling. It is highly ductile and flexible due to its low zinc content.
Double-phase brass contains alpha (α) and beta (β) phases and has a zinc content of 36% to 46%. The beta phase with high zinc content makes double-phase brass less plastic, more tensile, and is deformed using high pressure processing.
The alpha phase is a solution of copper and zinc, while the beta phase is the same solution with a higher percentage of zinc. Double-phase brass has corrosion resistance, strength, and exceptional machinability. An increase in the amount of zinc significantly influences the tensile strength and usefulness of double-phase brass.
Bolts, nuts, washers, springs, and structural components for electrical equipment use double-phase brass. Single-phase brass is cold form due to its flexibility while double-phase brass is hot formed because of its high zinc content.
The appearance of brass makes it ideal for decorative applications, while its strength, durability, and corrosion resistance make it useful for mechanical purposes. The low friction of brass is one of the reasons that it is used for fasteners, connectors, tools, and ammunition components.
Due to its low friction coefficient, brass is used for the manufacture of gears, locomotive axle boxes, and marine engines. Its durability and strength gives tools a long useful life without needing to be honed, repaired, or regular maintenance. Brass is chosen for applications that have to endure constant use and stress due to its resistance to wear.
The automotive industry relies on brass components for the production of radiator cores, tubes, and tanks. Brass radiators are replacing aluminum radiators in trucks due to their low cost, easy processing, and reduced scrap. They are made of solder coated brass tubes and copper fins, which are joined by tin lead solder.
A common use for brass is as connectors and fasteners due to their resistance to corrosion and the influence of water. Brass nuts are exceptionally durable, have a pleasant appearance, and come in a wide range of sizes. Brass washers have an attractive appearance and are used by the military, airlines, and gas companies.
Brass is widely used for electrical components for its conductivity. Brass components are used to connect two lines. They are used to make a wide range of electrical parts from brass panel board accessories and wiring accessories to switch gears and light fittings. They are used to attach lamps or lights to lampshades and come as raw brass or polished and plate finished brass.
Brass has several positive properties that make it ideal for use as pipe and fittings. A necessity for plumbing is the prevention of corrosion caused by water, gas, and various fluids. Brass’ resistance to corrosion and the effects of heat and pressure make it ideal for plumbing applications.
As any plumber can testify, installing piping is a challenge that requires bending and shaping pipes to fit in hard to reach places. Brass is a malleable material that can be easily shaped to fit into any difficult or isolated space. Additionally, after being bent and shaped, brass retains its durability and resilience without cracking, breaking, or rupturing.
One of the original uses for brass, at the beginning of the 19th century, was as a replacement for the wood hulls of ships that were susceptible to rot and the infestation of worms. The corrosive resistance of brass and its strength and toughness made it an ideal replacement.
Since its initial use, brass has been replaced by more durable materials for hulls of ships but is still used for other components due to its resistance to corrosion. Ship builders use brass for valves, propellers, fittings, and pipes due its ability to endure stress and its longevity.
Brass, with its copper content, is known for its excellent conductivity for use as electrical components. Every aspect of an electrical installation includes some form of brass connector, circuit breaker, or terminal block.
Common brass electrical components include:
Brass is widely used for its aesthetic appearance and decorative qualities. It can be enhanced with a variety of finishes to further improve its eye appeal. As with other uses for brass, its decorative use is also related to its strength, durability, and longevity.
Brass can have a bright glowing finish to present a new and fresh feeling. Due to its thousands of years of use, brass can have an antiquated and aged appearance to indicate years of use for conditions that have the appearance of antiques.
Brass is used for lamps and dishwasher fittings because it is aesthetically pleasing and microbial resistant. Candle holders, sculptures, trophies, and plaques have their distinctive quality from the visual appeal of brass. The assortment of items made from brass include lighting fixtures, doorknobs, furniture, bathroom fixtures, and cabinet hardware.
Brass is a common alloy used in architecture because of its natural durability and resistance to corrosion. It is used for architectural fascias, trimmings, and hedges. Since brass has been used for centuries, brass alloys are used to renovate or restore old buildings back to their original form.
Architects choose brass as a cladding material due to its weathering abilities and lustrous appearance. Over the years, architectural brass patinates from its original gold tone to a more mellow yellow or pink. Although brass changes its color during the aging process, it never loses its durability.
Brass handrails are the first choice of many projects due its copper content being antibacterial. Since handrails are touched by so many people, having an antibacterial metal keeps them safe and protects users. In this era with so much concern for disease, handrails that provide an extra layer of protection are ideal.
A very common use of brass is as a decorative accent that highlights a feature of a building or structure. Brass has a wide range of properties that can be adjusted to fit the construct of a design or plan. The range of colors of brass include gold, dull yellow, amber brown, chocolate brown, and black. This allows architects the flexibility to dream, design, and create unique and distinct looks.
Plumbing and electrical systems, two of the most often used systems in a home contain brass as a component. Different parts of electrical sockets and switches contain brass alloys. In addition, brass is frequently used in valves and different pipe fittings like elbows, plugs, and couplings in the plumbing industry.
The quality of sound produced by a musical instrument is directly related to the material used to produce the instrument. Silver, bronze, plastic, and platinum have been used for years. Historically, brass has been found to be one of the most durable materials for the production of sustained vibrations, the best example being cymbals made of brass. This is due to its ductility, malleability, and the thin sheets or plates of brass that do not crack or break when being formed.
Unlike other instruments, brass instruments can be dented or impacted and still retain their sound quality. In addition, they can be repaired, which is unlike other metals that lose their sound quality when damaged.
Cartridge brass is used to produce cartridge casings. It is produced in large coils that are slit into narrow coils to be processed by a cupping press that produces thick walled wide diameter cups. The heavy walled cups are drawn several times before being pinch trimmed and formed to produce the shell casing.
Brass is used for cartridges because it has compressive strength and high melting temperature but is softer than the bore and rifling of the barrel of a gun. Its high friction coefficient acts as a lubricant that is hard enough and smooth such that it does not harm the rifling of a gun.
Brass bars are thick long rectangular or square shaped bars that are used for construction and engineering projects. As with all forms of brass, they are widely used for their superior strength and resistance to corrosion.
The different shapes and sizes of brass bars are not used for decorative or aesthetic purposes. They can be polished and finished to enhance their appearance. The ductility of brass and its malleability makes it possible to cut, shape, and form brass bars to fit any application. To fit the needs of an application, brass bars can be brazed, drilled, butt welded, and soldered.
Unlike brass bars, brass strips are flat thin sheets that are used for their electrical conductivity and corrosion resistance. Since they are thin and flexible, brass strips are used to produce electrical components, jewelry, and various decorative items.
Brass angle trim has a bright and brushed polished finish and comes in various sizes with a mill finish. It is used for edging on steps, wall corners, framework, and areas that need protection and precision trimmed edges.
Brass’ hot working temperature is between 750°C and 830°C (1382°F and 1526°F) with annealing temperatures between 520°C and 650°C (968°F and 1202°F) and low temperature annealing temperature between 260°C and 270 °C (500°F and 518°F).
Heat exchangers, pipes, equipment, and electronic parts are produced from brass due to its plasticity, high strength, good machinability, weldability, and corrosion resistance.
Standard Brass Specifications:
Brass angles, known as “L” shaped bars, are made by rolling and bending brass bars. The shape of brass angles is known for its exceptional structural support. Brass angle bars are not used for heavy construction due to their expense but are useful as supports for shelving and cabinets.
The smallest sizes of brass angles are used for edge and corner reinforcement and protection. They are used in the manufacture of side tables, chairs, and bed frames due to their strength, stability, longevity, and aesthetic appearance.
Of the various types of brass, solid brass has been used for thousands of years for a wide variety of applications including swords, guns, and other weaponry. Today, solid brass is used for door knockers, fireplace tools, cabinet hardware, light fixtures, and statues and figurines.
In many cases, the use of solid brass is appreciated as a traditional metal due to its long history. Home decor, that relishes antiques, has multiple items and accents that are highlighted by brass.
Brushed brass has abrasions and scrapes across the length of the brass that create a matte effect and reduces the shine of brass to create a subdued textured appearance. Unlike the golden shine of polished brass, brushed brass is dull and offers a quiet soft feeling. It is commonly used for faucets, light fixtures, and cabinet pulls.
Brass sheets have the same longevity, strength, and durability of solid brass and are used in several industrial applications. The types of brasses used to make brass sheets are limited to five types of brass as determined by the American Standards for Testing and Materials (ASTM), an international standards organization.
Brass used for brass sheets:
Brass sheets are lightweight, flexible, and strong and are used for architectural designs and interior highlights. Although brass sheets are easier to manipulate than solid brass and bars, they still have the same properties and characteristics of solid brass, which is the reason they are used for musical instruments and home decorations.
The corrosion resistance and tensile strength of brass sheets are two of the reasons that brass sheets are used for the manufacture of radiator cores, automotive grills, heat exchangers, and electrical components.
Brass has existed for thousands of years and has been the primary metal for many projects, applications, and components. Its resilience, longevity, and beauty have made it a popular and reliable part of human history.
Brass is a flexible metal that can take several forms each of which is designed to make it more accessible and fit the needs of applications. Much of the use of brass is due to its electrical conductivity and malleability, which gives it the ability to be used in a wide range of projects from piping to tubing to flanges. It is this adaptability, along with its strength, that has made brass a popular choice for difficult and challenging applications.
Brass wire has improved corrosion resistance and lower electrical conductivity with exceptional ductility. There are a wide range of applications that depend on brass wire including scientific components and instrumentation. One of the reasons for the wide use of brass wire is its strength. Brass is an exceptionally strong metal that has the endurance to withstand hostile conditions where other metals will quickly erode.
Even though brass has only 28% of the conductivity of copper, there are applications where brasses' limited conductivity is a better choice. The different forms of brass wire include riveting, free cutting, lead free, flat, zipper, stitching, brazing, and forging brass wire. Each of these varieties of brass wire are designed for specific applications and use different grades of brass wire. Brass grade C37700 is used for forging wire due to its hot working characteristics.
The multiple grades of brass wire makes it possible to use it in a plethora of applications and conditions. Brass wire grade C36000 is free cutting wire that is used for high speed machining applications. Grades C26000 to C28000 are used for zipper wire and stitching brass wire due to their surface finish and brass color. Brass wire grade C38100 is used for brazing due to its low fuming that makes it suitable for welding.
As with many brass components and materials, brass sheets have a wide range of applications that vary according to their thickness and brass composition. For many years, brass sheets have been used as decorative panels, window frames, and cladding material. These uses are based on the gold appearance of brass.
The low electrical conductivity of brass enables it to be used as a shield for electronic equipment to prevent damage from electromagnetic interference (EMI). Brass sheets are used as shields for medical equipment, electrical contacts and connectors, relays, and RF connectors. The reasons for choosing brass sheets as shielding are its wear resistance, high temperature tolerance, and easy formability and machinability.
Brass foil is used for the production of brass type, which is used to produce books, albums, and leather products. It conducts heat evenly and rapidly to create crisp images at low temperatures. The hardness of brass foil type makes it possible to use it for many years without deformation or deterioration. It is the most expensive of the hot stamping types, which is compensated for by its long useful life.
A very common use for brass is as fasteners and connectors. Part of the reason for their use is their positive appearance, which can enhance a piece of furniture, cabinet, or installation. Although this is a beneficial aspect of brass fasteners, their greater value comes from their strength, durability, and resilience in the face of difficult and harsh conditions. This characteristic of brass fasteners is the reason for their use in mariner applications and the auto industry.
The use of brass fasteners is related to their exceptional performance as well as their easy machinability and formability with low friction. Brass fasteners are found in every part of industrial, commercial, and residential applications. They come in several forms including bolts, screws, nuts, washers, and spacers. As with all other forms of brass, brass fasteners are made from several different grades of brass such as UNS C22000, C26000, C27000, C27400, C36000, and C69400, which are high quality grades of brass.
Another common use for brass is as piping, which is mainly due to brass’ resistance to corrosion and rust. An area of plumbing where brass is widely used is in the production of fittings due to the strength of brass and its ability to withstand variations in pressure. This aspect of brass fittings is especially true in applications that involve chemicals and gases.
The different types of brass pipe fittings include couplings, adaptors, nipples, tees, gate valves, and end plugs. The only drawback to brass pipes and fittings is their cost, which is higher than PVC, cast iron, and steel. As with other brass products, the higher cost is compensated for by the long useful life of brass pipes that never need replacing.
A popular form of brass piping are brass gate valves, or sluice valves, that open and close by changing the position of a wedge or gate. They are used to control the flow of non-shock cold water, oil, or gas, and air in compressed air systems. Brass gate valves are rated for pressure up to 200 psi and come in a wide variety of sizes as well as custom designed sizes.
Brass flanges are components of piping systems that are used for secure and leak proof connections between brass pipe and brass pipe fittings. As with all forms of brass materials, brass flanges provide superior strength, durability, resistance to corrosion, and a long useful life. They are available in sizes to fit any type of pipe or can be custom made to fit unique and unusual pipe sizes.
As with all forms of brass forms, brass flanges are made from different grades of brass to fit the needs of an application. The various sizes of brass flanges are used to connect pieces of equipment that cannot be connected directly. Additionally, they are used as support for piping or tubing that are carrying heavy loads.
The key benefit of brass flanges is their ability to provide a tight seal when connecting unlike pieces of equipment. This aspect of their nature is a necessity for the prevention of leaks or any contamination. The selection of the type of flange is dependent on the application where they will be used. Brass flange types include weld neck, slip on, and threaded flanges with weld neck used for high pressure applications while slip on brass flanges are used for low pressure applications.
Brass plate is machinable and able to withstand hot and cold pressure processing. It is used for structural components like gaskets and linings for cutting and stamping applications. Brass plate is made from a variety of brass grades for uses that include marine applications and conduits for steam and oil.
The manufacture of several brass parts begins with brass plates that can be configured into pins, bolts, washers, nuts, and radiator parts. Its popularity is due to its plasticity in a cold or hot state and how easily it can be brazed or welded. UNS C26000 is a brass grade that is used as brass plate due to its strength and low thermal conductivity.
Brass plate is produced in several sizes and can be custom made to fit unique applications. The variations in brass plate are in regard to the size of plates, which can be standard preformed sizes or custom sizes. UNS C28000 brass plate is used for its low friction coefficient that reduces wear on moving parts.
As with brass plates, brass rods are the raw materials for the manufacture of brass tools, fasteners, and other products. Brass rods with a high melting point are used in place of solder to join pieces of metal. For production processes, brass rods are cut to specific or custom lengths to be transformed into other products. They come with round, triangular, square, hexagonal, round hollow, D stock, and rectangular cross sections that are created by extrusion.
At the completion of the extrusion process, the extruded brass rods are cooled and subjected to an acid bath to remove oxidation. They are then cold drawn to accommodate the dimensions of the application for which they were produced and to create the desired mechanical properties. Brass rods are selected for the manufacture of components and products such that the shape of the brass rods are as close as possible to the shape of the product, a factor that assists in reducing waste.
Brass rods are used to make the components for valves, fasteners, gears, connectors, and handles. An essential part of metalworking are brass brazing rods that have a higher melting point than solder due to their copper content, which makes them a viable material for the joining of pieces of metal that may be subjected to stress or pressure.
Beryllium Copper is a versatile copper alloy that is valued for its high strength and hardness, combined with good electrical and thermal conductivity. It is a non-ferrous, non-magnetic, and non-sparking metal alloy...
Copper is a ductile, malleable, and reddish-gold metal with the capacity to effectively conduct heat and electricity. Brass and bronze, two commonly used alloys, are created when copper is combined with...
The copper sheet is a highly malleable and workable metal with outstanding electrical and thermal conductivity and corrosion resistance. Copper (Cu) is a reddish, very ductile metal that belongs to Group 11 of the periodic table...
Aluminized steels are steels that have been hot-dip coated with pure aluminum or aluminum-silicon alloys. This hot-dip coating process is termed hot-dip aluminizing (HAD)...
Aluminum 1100 is the softest of the aluminum alloys, which makes it easy to shape and form into a wide range of products for industrial and home use. It can be cold and hot worked but is frequently shaped by...
The term "aluminum coil" describes aluminum that has been flattened into sheets where their width is significantly higher than their thickness and then "coiled" into a roll. Stacks of individual aluminum sheets are difficult to...
Aluminum piping and tubing is silvery-white, soft, and ductile. The metal belongs to the boron group. Aluminum is the third most abundant element present on earth. Aluminum has low density. When exposed...
Metals are a group of substances that are malleable, ductile, and have high heat and electrical conductivity. They can be grouped into five categories with nickel falling in the category known as transition metals...
Stainless steel grade 304 is an austenite stainless steel that is the most widely used and versatile of the various grades of stainless steel. It is a part of the T300 series stainless steels with...
Stainless steel is a type of steel alloy containing a minimum of 10.5% chromium. Chromium imparts corrosion resistance to the metal. Corrosion resistance is achieved by creating a thin film of metal...
Stainless steel grades each consist of carbon, iron, 10.5%-30% chromium, nickel, molybdenum, and other alloying elements. It is a popular metal used in various products, tools, equipment, and structures that serve in many industrial, commercial, and domestic applications...
Steel service centers are companies that specialize in procuring steel directly from mills and manufacturers and supplying them to the customers. They are fundamental to the steel supply chain...
Stainless steel can be fabricated using any of the traditional forming and shaping methods. Austenitic stainless steel can be rolled, spun, deep drawn, cold forged, hot forged, or stippled using force and stress...
Stainless steel tubing is a multifaceted product that is commonly utilized in structural applications. Stainless steel tubing diameters and variations vary greatly based on the application requirements and are...
Titanium metal, with the symbol Ti, is the ninth most abundant element in the earth‘s crust. It does not occur in large deposits, yet small amounts of titanium are found in almost every rock...
Tungsten is a rare naturally occurring chemical element on earth. It is known to be one of the toughest metals on the earth. It is usually a tin white or a steel gray metal. Tungsten is common for its high tensile...
Aluminum is the most abundant metal on the Earth’s crust, but it rarely exists as an elemental form. Aluminum and its alloys are valued because of their low density and high strength-to-weight ratio, durability, and corrosion resistance...