Brass
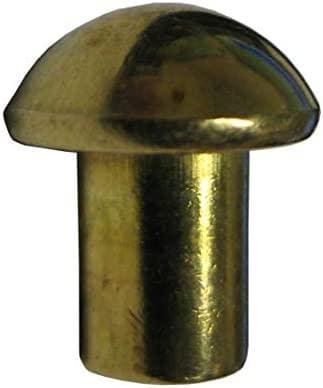
A variety of copper-zinc alloys are referred to together as brass. Different ratios of brass and zinc can be used to create alloys, which produce materials with various mechanical, corrosion, and thermal properties...
Please fill out the following form to submit a Request for Quote to any of the following companies listed on
This article presents all the information you need to know about Beryllium Copper. Read further and learn more about:
Beryllium copper (BeCu) is an age-hardened alloy with high strength and non-magnetic and non-sparking properties. It is made by combining 0.5% to 3% beryllium with copper to create a metal with the highest strength of any copper-based alloy. The amount of beryllium mixed with copper determines beryllium copper’s grade, with each grade having its own advantages and positive properties. Their strength and conductivity determine the division between the grades.
Compared to most alloys, beryllium copper is a new alloy. Unlike brass and bronze, which were discovered centuries ago, beryllium was first isolated in 1828 by reacting beryllium chloride with potassium. The first beryllium copper metal pieces, in the form of conductive springs, were created in 1920 and were used in telephone switchboard relays. In the 1970s, beryllium copper became popular in the automotive and telecommunications industry.
Nowadays, beryllium copper is widely used in industries such as energy (tools for oil and gas extraction, coal mining), power, electronics (connectors), cryogenics, automotive (valve seats and guides, anti-lock braking), and much more. Beryllium copper is a good material for musical instruments like triangles, trumpets, bells, and tambourines because it offers consistent tones and resonance. It can withstand marine environments due to its biofouling properties combined with its high strength. It is also used in Magnetic Resonance Imaging (MRI) equipment, wherein the use of magnetic ferrous metals can be detrimental.
An alloy is a mixture of a metal combined with another metal or other non-metal elements to enhance its properties. Beryllium copper, brass, and bronze are all copper base alloys. Copper is considered the "solvent" or the main alloying element of these mixtures. Corrosion, biofouling resistance, and thermal and electrical conductivity are all properties inherited from copper.
Brass: Brass is an alloy of zinc and copper. It is a metal with good strength and ductility attributed to the properties of zinc. It has better malleability than bronze. It has been used since prehistoric times but was discovered around 1,400 B.C.E., and it has historically been referred to as "yellow copper". Its color is dull yellowish to reddish depending on the amount of zinc alloyed. Applications of brass are musical instruments, plumbing materials, and ammunition components. Light-colored variations of brass are used in decorative pieces of jewelry as a substitute for gold.
Bronze This alloy is a combination of copper and additives such as tin (the main additive), manganese, and phosphorus. It was discovered earlier than brass and dates back to around 3,500 B.C.E. It is a hard and brittle metal with a higher melting point than brass. It is distinguished by its reddish-gold color. Applications of bronze are sculptures, musical instruments, electrical connectors and springs, fittings, etc.
Beryllium Copper: This alloy is made of beryllium and copper combined with small amounts of alloying elements. Beryllium is found in 30 different mineral species. It is a soft, low-density metal with a steel-gray color. When alloyed with copper, it increases its strength, hardness, and electrical and thermal conductivity. The succeeding chapters will discuss more characteristics of beryllium copper and its applications.
Beryllium copper pieces may be wrought or cast and sold in various forms such as plates, rods, strips, and wires. Wrought beryllium copper metals are commonly formed through hot or cold working. Cast beryllium copper pieces are shaped by pouring or injecting molten beryllium copper into a mold. The forming process is followed by age hardening for better modification and control of the resulting mechanical properties.
Beryllium copper alloys are divided into two categories according to their composition and the inherent physical properties they exhibit. The physical properties are mainly influenced by the beryllium content of the alloy and addition of other alloying elements, and the heat treatment conditions employed by the manufacturer.
High-strength beryllium copper alloys contain 1.6% - 2.05% beryllium and are used for heavier-duty applications. The exceptional strength of beryllium alloys is achieved by age hardening or precipitation hardening. When beryllium and copper are precipitation hardened, the results are created by the precipitation of beryllium from a supersaturated solid solution of mainly pure copper.
Precipitation of the pure copper happens during the very slow cooling of the alloys due to the fact that the solubility of beryllium in copper decreases with cooling. Normally, the alloys are rapidly cooled after annealing so that the beryllium remains in a solid solution with the copper. The alloy, precipitation or age hardening treatment, lasts for an hour or more at 392 ° F to 860 ° F (200° C and 460° C). During tempering, the beryllium-containing phase, called beryllides, precipitates out of the solution.
It is during precipitation that the beryllium copper alloys have a change in their properties and an increase in their strength. The coherency strains that develop at the interface of the matrix and precipitates increase the strength of the beryllium-copper alloy. The main characteristic of beryllium copper alloys is their excellent treatment response to precipitation hardening and resistance to stress relaxation.
Some of the high strength beryllium copper alloys are:
C17200 has the highest strength and hardness of the beryllium copper alloys, with a hardness and strength that is similar to steel. It contains 2% beryllium with a tensile strength that can exceed 200 ksi and a Rockwell hardness of C45. C17200 has an electrical conductivity of a minimum of 22% IACS and exceptional stress relaxation resistance at high temperatures. It is widely used in the oil and gas industry and for springs that must be non-magnetic, electrically conductive (current-carrying springs), and corrosion-resistant.
When inserted into a plastic mold, C17200 reduces the temperature of the mold, eliminating the need for cooling water. The thermal conductivity of C17200 is four times better than the steel of the mold. This aspect of C17200 can ensure rapid and uniform cooling of plastic products, decrease product deformation, and assist in removing defects. The use of C17200 to cool molds helps increase plastic mold efficiency and shorten production cycles.
C17300 has a lead content ranging from 0.2 to 0.6%. The addition of lead reduces chipped-edges during the use cutting tools, which decreases tool wear, making C17300 suitable for manufacturing electronic, automotive, and aerospace components. C17300 is easier to machine and fabricate than other high-strength alloys with a high fatigue resistance.
The properties of C17300 are similar to C17200. It is referred to as the "leaded beryllium copper" due to the small amount of lead it contains, which makes it machinable. Its lead content increases its cutting coefficient from 20% to 50%, making it more adaptable for the production of precision parts. Included in the C17300 process performance properties are high thermal conductivity, weldability, corrosion resistance, polishability, wear and adhesion resistance, and the ability to be forged. C17300 is used to make fuse fasteners, springs, connectors, spot welding heads, seam welding rollers, die casting heads, and plastic molding die.
C17000 has lower beryllium content and slightly lower strength. It is less expensive than C17200 and is used for lighter applications. C17000 retains its strength in cryogenic conditions. It is also commercially used to manufacture tools, fasteners, bearings, and bushings. C17000 is commonly used in resistance welding equipment.
The main use of C17000 is in applications that require high strength and good conductivity. It is ductile, heat treatable, and can be mill-hardened. C17000 can be welded using soldering, brazing, arc welding, spot welding, and butt welding, although Oxy-Acetylene welding is not recommended. Threaded joints using C17000 are resistant to galling, whether connected to themselves or stainless steel.
High conductive beryllium copper alloys contain lower beryllium content that ranges from 0.2% to 0.7%, with trace amounts of cobalt and nickel. As the name implies, these alloys have high electrical and thermal conductivity. The copper alloying element contributes thermal and electrical properties. However, these properties are decreased with increasing beryllium content, resulting in a higher-strength material. The same is true for other alloy mixture systems (e.g., brass and bronze). Some of the high conductive beryllium copper alloys are:
C17510 contains 0.2 to 0.6% beryllium and 1.4% 2.2% nickel. It is used in applications requiring moderate strength and thermal fatigue resistance. In its wire form it is used for power and signal cables in offshore oil and gas operations. Its stripped form is used in switches and relays due to its high electrical conductivity.
Typical manufacturing uses for C17510 are spot and seam welding of high resistance alloys such as stainless steel. It is recommended for stressed welder structural current members and offset electrode holders. C17510 has a tensile strength of 140 ksi with a Rockwell hardness of B100 and conductivity of 45% to 60% of regular copper.
C17500 contains 0.4% to 0.27% beryllium and a higher cobalt content of 2.4 to 2.7%, wth mechanical properties that are similar to C17510. The addition of cobalt slightly lowers C17500's thermal conductivity and melting point. With high thermal resistance, C17500 has good hot working and cold working properties. It is an excellent material for casting and molding tools.
The conductivity of C17500 is 45% to 60% of regular copper with a tensile strength of 140 ksi and a Rockwell hardness of B100. All C175 grades of beryllium copper have a cobalt alloy addition, with the variation in C17510 being alloyed with nickel. Regardless of the nickel content of C17510, C17500 and C17510 offer the same dependable performance.
The conductivity of C17500 is 45% to 60% of regular copper with a tensile strength of 140 ksi and a Rockwell hardness of B100. All C175 grades of beryllium copper have a cobalt alloy addition with the variation in C17510 being alloyed with nickel. Regardless of the nickel content of C17510, C17500 and C17510 offer the same dependable performance.
Alloy 10x is a copper, cobalt, beryllium, and zirconium alloy developed to improve beryllium copper’s high temperature strength and ductility. It has exceptional strength and ductility at temperatures of 806 ° F (430° C) with resistance to thermal cracking. One of the main uses for Alloy 10x, due to its thermal conductivity and resistance to thermal cracking, is in automotive powertrains such as exhaust valve seats and pre-ignition chamber applications.
Alloy 310 is a combination of copper, beryllium, nickel, and cobalt. Its properties are the strengths of C17500 and C17510, which are their high electrical and thermal conductivity as well as their strength and hardness factors. Additionally, Alloy 310 has high thermal fatigue resistance. The popularity of Alloy 310 is due to its lower cost compared to the other beryllium copper alloys.
The combination of unique properties of Alloy 310 makes it an ideal material for welding electrodes and components, non-ferrous casting dies, nozzles, and plungers.
Beryllium copper attains the highest strength of all copper alloys while maintaining high thermal and electrical conductivity. These are the most prominent characteristics of this alloy. The tensile strength of high-strength beryllium copper alloys can exceed 200 ksi or around 1,400 MPa. Its strength and hardness are brought by precipitating beryllium out of the alloy mixture through a heat treatment process called precipitation hardening.
Other distinguishable properties of beryllium copper that set it apart from other metals are the following:
This is the most prominent characteristic of a beryllium copper metal piece. Beryllium copper does not produce a frictional spark when struck with other metals, making it a safe material choice for tools in environments with fire and explosive hazards like oil rigs and coal mines. A hot dislodged particle of beryllium copper from tools cools rapidly and does not cause ignition of nearby flammable material.
Galling is a type of mechanical wear of a metal surface caused by adhesion and frictional forces, especially if it is not lubricated. It is commonly experienced by two metals in which their surfaces are sliding with each other under compressive forces (e.g., thread). Beryllium copper does not exhibit wear and produces minimal friction and surface damage when in contact with other metal pieces, even under overload conditions and continuous vibration. Beryllium copper is also abrasion-resistant.
Being a non-ferrous metal, beryllium copper is non-magnetic. Magnetic fields do not disrupt the normal function of a beryllium copper component. Beryllium copper does not behave like a "hot magnet" during machining and forming, unlike other metal alloys.
Beryllium copper's tensile strength and toughness are maintained at temperature extremes, even at long exposure times. Beryllium copper can be used in cryogenic conditions, wherein steels become brittle at very low temperatures. The performance of beryllium copper at elevated temperatures is above average compared to other copper alloys. This and its inherent hardness are why beryllium copper is commonly used in molding tools and welding electrodes.
Beryllium copper does not corrode in harsh environments, is resistant to biofouling, and does not tarnish easily. It is immune to chlorine-induced stress corrosion cracking, unlike stainless steel of the same value that cracks after a few hours of exposure to high chloride conditions. Hence, it is a good material selection for apparatuses and equipment in a saline environment and oil and gas plants.
Beryllium copper can be used to handle glycols, ketones, hydrocarbons, and esters routinely. However, impurities present in these solutions can accelerate the corrosion of beryllium copper. These impurities can be sulfides, acids, and salts. The curing of polyvinyl chloride and room temperature vulcanized silicone emit fumes that can corrode the beryllium copper metal piece.
Beryllium copper is machined with relative ease. It is metal-worked before the hardening process done by the fabricator. Before the hardening process, the beryllium copper has a moderate hardness level and high ductility.
In addition, beryllium copper is resistant to hydrogen embrittlement. Hydrogen embrittlement is the phenomenon where hydrogen atoms are absorbed in the beryllium copper microstructure during fabrication processes such as welding, hot forming, and electroplating. Hydrogen-embrittled beryllium copper parts are prone to cracking when stress is applied.
Age precipitation of beryllium copper relieves stress and imparts exponential strength and hardness, resulting in high dimensional stability of the metal piece during stamping and cutting processes.
Heat treatment of beryllium copper requires a series of controlled heating and cooling, which gives it desirable mechanical properties. The benefits of heat treatment of beryllium copper are a significant increase in strength, durability, and machinability. This process applies to all wrought and cast beryllium copper alloys.
The physical states of the beryllium copper solution are illustrated as a function of temperature and concentration in the binary phase diagram shown below. A phase diagram is a useful tool for understanding the heat treatment process. Thermal properties of beryllium copper, such as boiling point and melting point, vary with beryllium content.
Heat treatment of beryllium copper occurs in two stages: solution annealing and age precipitation.
Solution annealing is usually done at the supplier‘s side and prepares the beryllium copper piece for age hardening. At this stage, the beryllium precipitates are dissolved in the copper matrix to form a supersaturated beryllium copper solution, through the diffusion of beryllium atoms in the alpha phase. It also ensures a uniform concentration of beryllium on the alloy system and regulates its grain size. Depending on the alloy composition, the beryllium copper is heated slightly below the solidus temperature, which varies around 1450⁰F (790⁰C) for high strength alloys and 1652⁰F (900⁰C) for high conductivity alloys until a solid homogeneous mixture is present. At the solidus curve (curve BC) in the binary phase diagram, the solid and liquid phases of beryllium copper coexist. The solidus temperature decreases with increased beryllium concentration. The annealing temperature and time are controlled to prevent undesirable grain growth and melting.
To maintain the resulting structure (in a supersaturated solution) from the annealing step at room temperature, the beryllium copper piece is rapidly quenched in cooling water. The result is a soft and ductile beryllium copper metal piece that is readily cold worked by forming, drawing, or rolling.
Age hardening, or precipitation hardening, involves heating below the solvus temperature and slow cooling of the annealed piece. In a furnace, heating lasts for an hour or more at around 392-752⁰F (200-400⁰C in a furnace). Below the solvus region in the binary phase diagram, beryllium and copper exist as two distinct solid microstructures. The solvus temperature also increases with increased beryllium concentration. Age hardening is performed after the forming and shaping process.
The strengthening and hardening of the beryllium copper piece are attributed to the precipitation of beryllium out of the solution. Precipitation is brought by slow cooling. In general, the solubility of the solute decreases as the temperature of the solution decreases. The beryllium-rich (gamma) phase comes out in the copper matrix as beryllides along the grain boundaries.
Heating temperature and time are the critical parameters in age hardening, in which physical properties such as strength and conductivity are the responses. The age hardening condition is arbitrary to the customer, depending on the end application of the beryllium copper piece. The common age-hardening conditions are:
During age hardening, oxides of beryllium and copper are developed on the surface of the metal piece. The development of oxides is inevitable even in pure hydrogen atmospheres or in vacuum conditions, but its effect is not detrimental to the properties of the parts. However, it is important to remove the surface oxides if the parts are to be plated or soldered.
Beryllium copper can pose health hazards like other metal alloys. The mechanisms of its entry into the human body and its effects on health are:
Beryllium is known to be a human carcinogen. Workers involved in beryllium copper production have a high risk of developing lung cancer.
The following are industry practices to minimize the health risks involved when handling beryllium copper, particularly to protect workers from toxic dust and fumes:
The many positive properties of beryllium copper have expanded its use to a wide array of industrial and commercial applications. Through research, testing, and experimentation, the number and scope of potential uses have gradually grown beyond that of a highly resilient conductive material. A key factor in the use of beryllium copper is its elasticity with twice the strength of other copper alloys.
Increasingly, engineers and designers are finding new and innovative ways to make use of the characteristics and properties of beryllium copper. Its reliability, durability, strength, and consistently positive performance have made it the ideal choice for sustainable and dependable application use.
A variety of copper-zinc alloys are referred to together as brass. Different ratios of brass and zinc can be used to create alloys, which produce materials with various mechanical, corrosion, and thermal properties...
Copper is a ductile, malleable, and reddish-gold metal with the capacity to effectively conduct heat and electricity. Brass and bronze, two commonly used alloys, are created when copper is combined with...
The copper sheet is a highly malleable and workable metal with outstanding electrical and thermal conductivity and corrosion resistance. Copper (Cu) is a reddish, very ductile metal that belongs to Group 11 of the periodic table...
Aluminized steels are steels that have been hot-dip coated with pure aluminum or aluminum-silicon alloys. This hot-dip coating process is termed hot-dip aluminizing (HAD)...
Aluminum 1100 is the softest of the aluminum alloys, which makes it easy to shape and form into a wide range of products for industrial and home use. It can be cold and hot worked but is frequently shaped by...
The term "aluminum coil" describes aluminum that has been flattened into sheets where their width is significantly higher than their thickness and then "coiled" into a roll. Stacks of individual aluminum sheets are difficult to...
Aluminum piping and tubing is silvery-white, soft, and ductile. The metal belongs to the boron group. Aluminum is the third most abundant element present on earth. Aluminum has low density. When exposed...
Metals are a group of substances that are malleable, ductile, and have high heat and electrical conductivity. They can be grouped into five categories with nickel falling in the category known as transition metals...
Stainless steel grade 304 is an austenite stainless steel that is the most widely used and versatile of the various grades of stainless steel. It is a part of the T300 series stainless steels with...
Stainless steel is a type of steel alloy containing a minimum of 10.5% chromium. Chromium imparts corrosion resistance to the metal. Corrosion resistance is achieved by creating a thin film of metal...
Stainless steel grades each consist of carbon, iron, 10.5%-30% chromium, nickel, molybdenum, and other alloying elements. It is a popular metal used in various products, tools, equipment, and structures that serve in many industrial, commercial, and domestic applications...
Steel service centers are companies that specialize in procuring steel directly from mills and manufacturers and supplying them to the customers. They are fundamental to the steel supply chain...
Stainless steel can be fabricated using any of the traditional forming and shaping methods. Austenitic stainless steel can be rolled, spun, deep drawn, cold forged, hot forged, or stippled using force and stress...
Stainless steel tubing is a multifaceted product that is commonly utilized in structural applications. Stainless steel tubing diameters and variations vary greatly based on the application requirements and are...
Titanium metal, with the symbol Ti, is the ninth most abundant element in the earth‘s crust. It does not occur in large deposits, yet small amounts of titanium are found in almost every rock...
Tungsten is a rare naturally occurring chemical element on earth. It is known to be one of the toughest metals on the earth. It is usually a tin white or a steel gray metal. Tungsten is common for its high tensile...
Aluminum is the most abundant metal on the Earth’s crust, but it rarely exists as an elemental form. Aluminum and its alloys are valued because of their low density and high strength-to-weight ratio, durability, and corrosion resistance...