Aluminum 1100
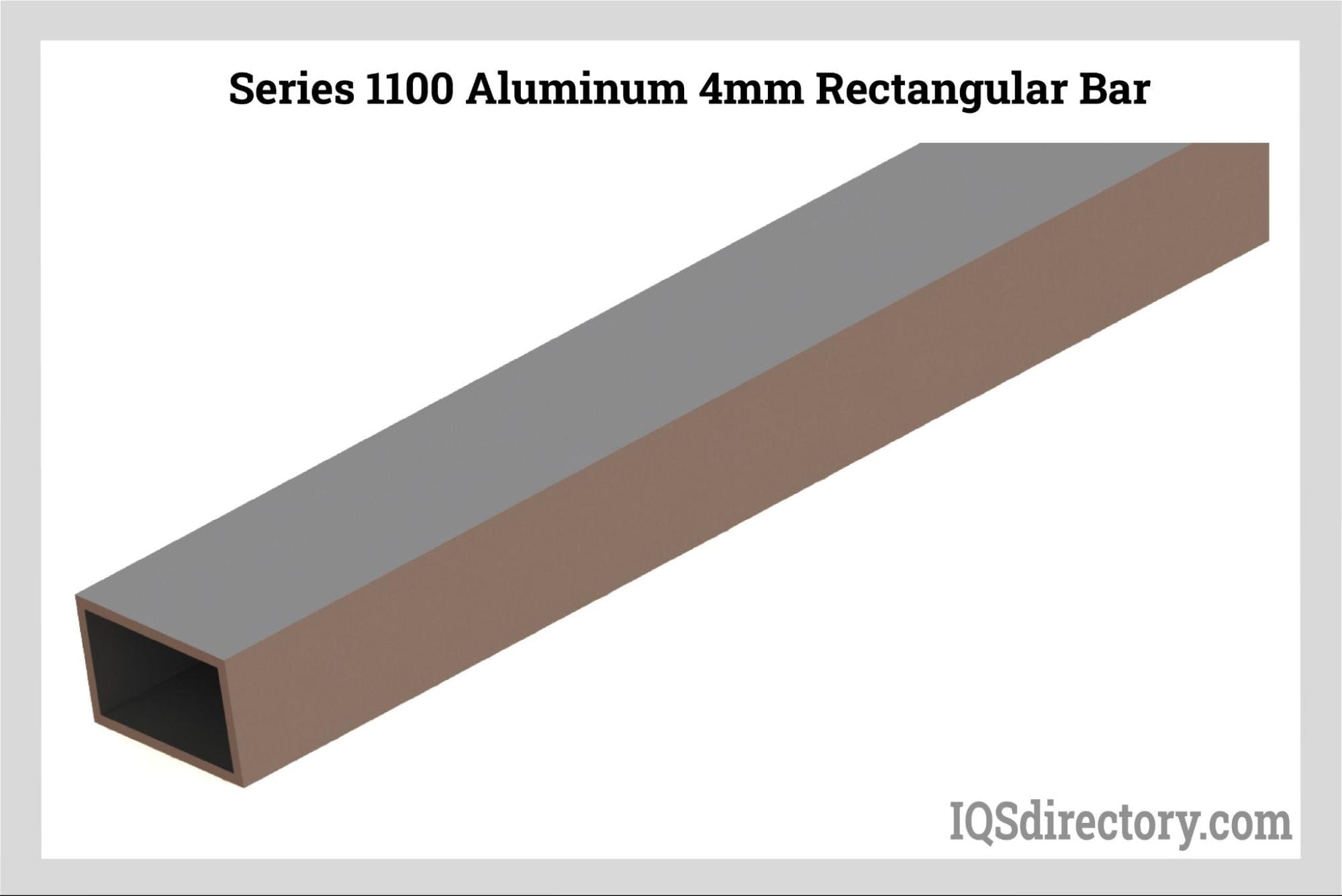
Aluminum 1100 is the softest of the aluminum alloys, which makes it easy to shape and form into a wide range of products for industrial and home use. It can be cold and hot worked but is frequently shaped by...
Please fill out the following form to submit a Request for Quote to any of the following companies listed on
This article will take an in-depth look at metal alloys.
The article will bring more detail on topics such as:
This chapter will discuss what metal alloys are and their characteristics.
Metal alloys are the result of combining two or more elements in order to make a new material. They can consist purely of metal elements or of metal and non-metal elements combined. Although combining metals creates a new metal, the resulting alloy keeps all the characteristics of the original metals, including electrical conductivity, opacity, ductility, and luster.
They could, however, possess traits that are distinct from those of the pure metals, such as greater hardness or strength. In some circumstances, an alloy may keep a metal’s vital qualities while lowering the material's overall cost. In other instances, the combination of chemicals endows the component metal elements with synergistic qualities like corrosion resistance or mechanical strength.
For practical purposes, the alloy components are often quantified by mass percentage, whereas atomic fraction is used for fundamental scientific research. Depending on the atomic configuration that gives rise to the alloy, alloys are often categorized as substitutional (an alloy where some atoms of the base metal are replaced with atoms of another element) or interstitial ( a bond primarily made between metals) alloys. They may also be divided into heterogeneous, which involves two or more phases, intermetallic, and homogeneous, which involves a single phase. An alloy may consist of a mixture of metallic phases or a solid solution of metal elements (a single phase in which all metallic grains (crystals) have the same composition).
An alloy is a combination of chemical components that produces an impure material (admixture) with metal-like properties. By combining two or more elements, of which one must be a metal, alloys are formed. In contrast to impure metals, such as wrought iron, which are less regulated yet are frequently thought of as useful, an alloy has additional components which are carefully managed to achieve desired qualities. Typically referred to as the base metal or primary metal, that metal's name may also be used to refer to the alloy. The other ingredients of an alloy may or may not be metals, but they will dissolve when combined with the molten base since they are soluble in it.
The mechanical characteristics of alloys are frequently very different from those of their base metal. Alloying a metal with another soft metal, such as copper, can change a metal that is typically highly soft (malleable), such as aluminum. Despite the fact that both metals are relatively ductile and soft, the final alloy of aluminum will be stronger.
The excellent ductility of iron is exchanged for the increased strength of an alloy termed ‘steel’ by adding a small quantity of non-metallic carbon. Steel is one of the most practical and widely- used alloys because of its extremely high strength, its ability to maintain a sizable degree of toughness, and for its capacity to be significantly modified by heat treatment. Steel may be made more corrosion-resistant by adding chromium (making stainless steel) or more electrically-conductive by adding silicon (making silicon steel).
Pure metals are single phase metals that have one type of atom and a uniform structure. They are unlike alloyed metals, which are a combination of pure metals, in percentages, to create a unique form of composite metal with its own properties and qualities. When metals are in their pure state, they have a characteristic mass, melting point, and physical properties. The properties of pure metals are the reason that they are used for alloys, since as pure metals, with some exceptions, they are not as strong, rugged, or durable as alloyed metals.
All metal products contain some form of pure metal that has been alloyed. Although there is a long list of pure metals from the periodic table, a select few are commonly used for commercial products and are found in every type of metal product. Iron, aluminum, copper, zinc, titanium, chromium, and nickel are a few of the metals that are used to produce commercial and industrial products.
The various forms of alloys that are produced from pure metals are an essential part of modern society. Metallurgists and engineers are constantly finding new and innovative ways to combine pure metals to make strong and durable alloys. During the bronze age, metallurgists discovered ways to combine pure metals to manufacture stronger and more durable products. For a metal to be considered pure, it must contain 99% or more of a metal and not be alloyed.
Copper was one of the first metals discovered by humans. It is a highly malleable metal with exceptional thermal and electrical conductivity. Copper is corrosion resistant and is highly durable. Unlike other pure metals, copper is often used in its pure state due to its conductivity, especially with electronic products. Copper’s ability to endure high moisture environments has made it one of the longest lasting metals.
Like copper, aluminum is also used in its pure state due to its high thermal and electric conductivity, workability, and corrosion resistance. Pure aluminum is soft and silvery white and is part of the boron group of metals with an atomic number of 13. Aside from its many alloyed versions, pure aluminum is found in powerlines, beer kegs, window frames, automobiles, and kitchen utensils. When aluminum is exposed to oxygen, it forms a protective oxide layer that shields its surface from the effects of the environment.
Iron is a brittle, hard metal that corrodes when exposed to moist air and high temperatures. Of all the iron mined, the major portion of it is used to produce steel by alloying it with carbon. The wide use of iron is due to its low cost and strength. Iron is a gray, silvery metal with magnetic properties and is highly reactive with acids. In the presence of air and water, iron rusts easily, which is the reason that it is normally alloyed such that it can retain its strength. Pure iron is 99.8% pure with small amounts of carbon, manganese, and other elements.
Nickel, like aluminum, forms a passivation layer when exposed to oxygen, which protects it against the corrosion. Also, like aluminum, nickel is a silver white metal but, unlike aluminum, it has a golden tinge. Nickel is a hard ductile metal that is chemically reactive and is magnetic at room temperature. It is frequently alloyed due to its corrosion resistance and is used as a coating. Products made from nickel include wiring, batteries, and electrodes. Aside from its resistance to corrosion, like copper and aluminum, nickel has good thermal conductivity, which is the reason it is used for heat exchangers.
Chromium is another form of pure metal that forms a protective oxide layer. It is a lustrous, brittle, hard metal that is mainly used to produce stainless steel and plating due to its bright polished appearance. Chromium exists in oxidation states from -2 valence up to 6 valence with 0, 3, and 6 being the most stable. The wide use of chromium is due to its bright and shiny appearance that improves the looks of products such as cars and household appliances.
Pure zinc is used as a protective coating due to its resistance to corrosion. It is a bluish white metal that is widely used as an alloy. Alloys of iron and steel include a zinc layer for galvanization, which enhances iron and steel’s resistance to corrosion. Zinc is commonly alloyed with aluminum and copper to improve their strength, durability, and other properties and characteristics. As the amount of zinc increases, copper and aluminum become stronger, more durable, and highly resilient but more difficult to work.
Titanium has a high strength to weight ratio, does not rust, and is exceptionally resistant to all forms of chemicals. The grades of pure titanium are 1, 2, 3, and 4 with grade 1 being soft and formable while grade 2 is a little stronger. Grade 3 is stronger than grades 1 and 2 and is weldable and corrosion resistant. Grade 4 is the strongest of the pure titaniums and the least malleable or moldable. It can be cold worked and is very strong, durable, and weldable. Of the various pure metals, titanium is one of the more flexible since it can be used in its pure state and is alloyed with other metals to produce very durable materials.
The different types of metal alloys include:
Steel is an alloyed metal made up of iron with a few tenths of percent of carbon, which improves its strength and fracture resistance. The temperature of steel determines its crystalline or allotropic forms of body center cubic or face center cubic. The interaction of the allotropes of iron with the other elements of steel give steel its distinctive and unique properties.
Carbon steel is divided into three types, which are low carbon, medium carbon, and high carbon, with low carbon containing 0.3% carbon, medium 0.6%, and high 1.5%.
Alloy steels are made by combining carbon steel with other elements, such as chromium, cobalt, molybdenum, nickel, tungsten, or vanadium. The wide variety of alloys makes it possible to create a steel with any number of properties. The drawback to alloy steel is its high cost, which is overcome with alloy steel's resistance to corrosion and damage over time. How alloys are combined to make alloy steel determines its strength and durability.
Tool steel is used to make tools. It’s known for being hard as well as heat and scrape-resistant. There are six grades of tool steel, which are:
Aside from the different types of steel alloys, steel is further classified using the types of applications for which it was produced, its manufacturing process, and its smelting methods. Steel is manufactured by hot and cold rolling, drawing, casting, and forging. The various smelting methods include rimmed steel, killed steel, and semi killed steel.
Steel is an iron and carbon alloy. Steels that include at least 10.5% chromium, less than 1.2% carbon, and other alloying elements are known as stainless steels. Other elements, such as nickel, molybdenum, titanium, niobium, manganese, etc., can be added to stainless steel to further improve its mechanical and corrosion resistance. Due to its chromium component. a layer of chromium oxide develops on the material‘s surface when it comes into contact with oxygen. This passive layer is what provides stainless steel with the unusual ability to resist rust.
Items made of stainless steel are simple to clean; common cleaning agents (detergents, soap powders) work well and don‘t scratch the surface. Stainless steel perfectly satisfies the needs of decorative items and kitchenware that must be cleaned frequently and thoroughly. Stainless steel comes in a wide range of surface textures, including matte, brilliant, brushed, and etched.
Stainless Steel Types | Composition |
---|---|
Ferritic | 0.08-0.2% Carbon, 11-18% (17%) Chromium, Iron |
Martensitic | 0.2-1% Molybdenum, Iron, 0.1-1% Carbon, 12-14% Chromium |
Austenitic | 0.15-2% Carbon, Iron, 10-20% Nickel, 17 – 25% Chromium |
Duplex | 1-6% Nickel, Iron, < 5% Molybdenum, 19-28% Chromium |
Stainless steel is a distinctive and beautiful material that may be embossed or colored. It is frequently utilized by architects for street furniture, interior design, and components of a building’s ‘envelope.’ At room temperature, stainless steel outperforms most other materials in terms of its mechanical strength.
It is particularly ductile, elastic, and hard, allowing it to be utilized in challenging metal-forming processes (such as deep stamping, flat bending, extrusion, etc.) while providing resistance to severe wear (friction, abrasion, impact, elasticity, etc.). It also provides excellent mechanical performance at both low and high temperatures.
With a critical temperature above 1472°F (800°C), stainless steel offers the best fire resistance of all metallic materials when employed in structural applications. Stainless steel has a fire resistance rating of A2S1D0 and emits no harmful fumes.
Alloys made of aluminum are very robust, reliable, and adaptable. They are one of the most popular metal materials, along with steel, and are highly sought-after in engineering, construction, and automotive applications. Iron, copper, magnesium, silicon, and zinc are elements commonly used in aluminum alloys. When aluminum is molten (liquid), the alloy components are combined, and when it cools, a homogeneous solid solution is created. These other elements could account for up to 15% of the alloy's bulk.
Alloys made with aluminum are frequently lightweight and resistant to corrosion. Although aluminum has some incredible qualities when it is pure, it would not be strong enough for most applications requiring high durability. Due to this reason, it is mixed with other elements to create alloys, which are far more robust and appropriate for use in industrial applications. When engineers want to lower the weight of a product (like an airplane) without sacrificing its strength, aluminum alloys are especially appealing.
Aluminum may become far stronger and, in some situations, even outperform steel with the appropriate mix of components. Many aluminum alloys feature the same advantages as pure aluminum while also being more affordable due to their lower melting point.
Many other metals, such as chromium, iron, molybdenum, and copper, easily alloy with nickel. This makes it possible to create a wide range of alloys that exhibit extraordinary high-temperature strength, outstanding resistance to corrosion, and high-temperature scaling. Other distinctive features include shape memory (the ability of a metal to return to its original shape when heated) and low coefficient of expansion (the extent to which a material expands when heated).
The chemical industry uses pure nickel because it resists corrosion well, especially when exposed to alkalis. Due to its ability to guard against electromagnetic interference, it is also utilized in transducers.
Due to their thermal expansion properties, nickel-iron alloys are the preferred material for glass-to-metal seals, and as soft magnetic materials. With 36% nickel and the remaining iron, Invar (UNS K93600) is exceptional in that it has essentially little thermal expansion at room temperature. This makes it useful in applications that demand high dimensional stability, such as in precision measuring devices and thermostat rods.
Due to its extremely low rates of thermal expansion, it is also utilized at cryogenic temperatures. The best soft magnetic qualities are found in alloys with 72–83 percent nickel, which are used to make transformers, inductors, magnetic amplifiers, magnetic shields, and memory storage devices. Seawater, non-oxidizing salts, and alkaline solutions do not easily corrode nickel-copper alloys. The most popular one is Alloy 400.
In the absence of oxidizing ions like cupric (copper-based) and ferric (iron-based), as well as dissolved oxygen, nickel-molybdenum alloys are very resistant to reducing acids. Nickel-chromium alloys are distinguished by their excellent electrical resistance, good high-temperature strength, and high resistance to corrosion at both normal and high temperatures (resistance to scaling).
The usual composition of modern bronze is 88 percent copper and 12% tin. Bronze still has many uses and is extremely interesting historically. Since copper is alloyed with tin or other metals, bronze is tougher than copper. Additionally, bronze is more easily melted and may therefore be cast easier. It is far more corrosion-resistant and tougher than pure iron. Historically, iron began to replace bronze in tools and weapons due to its abundance compared to copper and tin, not because it had any intrinsic advantages like strength.
The percentages of aluminum, iron, and nickel in aluminum bronze range from 6% to 12%. It is a sturdy alloy with superior wear and corrosion resistance. Aluminum bronze is the ideal alloy for pumps, valves, and other hardware exposed to corrosive fluids
Cupronickel is a bronze alloy combining copper with 2% to 30% nickel.. The alloy exhibits strong thermal stability and resistance to corrosion, especially in steam or wet air. In seawater, it is also superior to other kinds of bronze. Ship hulls, pumps, valves, electronics, and marine gear are among the applications for cupronickel.
Red silicon bronze and red silicon brass are both components of silicon bronze. Red bronze has less zinc than red brass, which has 20% zinc and 6% silicon. Lead content is low in silicon bronze, which may also contain manganese, tin, or iron. Silicon bronze is extremely strong and resistant to corrosion. Many pumps and valve stems are made of silicon bronze due to these traits.
Despite its popular name, nickel silver doesn't actually contain any silver. Its silvery hue is how it got its name. Zinc, nickel, and copper are all present in nickel silver. It has fair corrosion resistance and is moderately strong. Dinnerware, decorations, optical devices, and musical instruments all employ nickel silver.
Tin bronze, often known as phosphor bronze, is made up of 0.01% to 0.035% phosphorus and 0.5% to 1.0% tin. This alloy has a fine grain, a low coefficient of friction, and a high fatigue resistance in addition to being durable and strong. Bellows, washers, electrical equipment, and springs are among the things that use phosphor bronze.
The majority of titanium alloys feature titanium as the primary metal while also containing small amounts of other metals or substances. Like other alloys, titanium alloys are created by combining titanium in a certain proportion to other metals and chemical components. The mixture is allowed to cool after the ideal ratio has been reached. The titanium alloy material is then sold, transported, or used in another way.
Orthopedic and dental implants are the only typical uses for pure titanium, whereas titanium alloy is used in a wide range of other applications such as aerospace engineering, high-temperature engines, medical and marine processing, and athletic equipment. Although titanium is present in many alloys made of other metals in trace amounts, these materials are not referred to as titanium alloys unless titanium constitutes a significant portion of the mixture.
There are several types of titanium alloy, even though they are all made of pure titanium combined with other metals or chemical ingredients. Alpha stabilizers, like oxygen or aluminum, are used in alpha titanium alloys, for instance, to give them their distinctive properties.
On the other hand, a limited quantity of beta-stage stabilizers can be found in near-alpha titanium alloys. Due to its softness and ductility, grade 1 titanium alloy is the easiest to work with when using cold-forming metalworking techniques. On the other hand, grade 38 titanium alloy has a substantially higher tensile strength.
Although there are 38 common types of titanium alloys, the most common titanium alloy mixture features a composition of 90% titanium, 6% aluminum, and 4% vanadium. This mixture is known as Grade 5. Grades 1 through 38 of titanium exist, with grade 38 being the most recent titanium alloy created. The grades are listed chronologically based on their creation and do not refer to their strength or any other feature.
Titanium grade 5, sometimes referred to as Titanium 6AL-4V, is regarded as acceptable for use in military applications. The typical application for this grade of titanium alloy, which is stable in temperatures up to 752 °F (400 °C), is in the extremely hot and swiftly rotating aircraft turbines.
Columbium, another name for niobium, is a gleaming, ductile metal that is mostly utilized in alloys. It enhances the characteristics of steel and is frequently utilized in structural applications, jet engines, and gas pipelines. Niobium metal plates, rods, and sheets are utilized as sputtering targets (sites/places targeted to be coated with another material) and chemical processing machinery due to their resistance to corrosion and performance at high temperatures. It becomes a superconductor at very low temperatures. Extremely potent electromagnets are created from superconductive niobium wire for usage in particle accelerators and magnetic resonance imaging.
Niobium alloys have strong high-temperature strength and creep/cold flow properties (albeit less so than molybdenum), good thermal conductivity because of their high melting points, and superior chemical resistance to environments including liquid lead alloys. These factors lead to their classification as a structural material for the fuel assembly and rod coating in commercial high temperature LFRs. Although they have slightly less strength than Mo-alloys, Nb-alloys like C-103 (89 wt% Nb, 10 wt% Hf, 1 wt% Ti) and Nb-1Zr (99 wt% Nb, 1 wt% Zr) are typically easier to fabricate and more workable. Nb-alloys, like other refractory materials, can be produced using powder metallurgy to get qualities close to those of the wrought product. They are also simple to weld using TIG or other methods.
Tantalum is a refractory blue-gray metal that can withstand high temperatures while still maintaining its important physical and chemical properties. The high melting point and stress resistance of tantalum-tungsten alloys define them. The resulting alloy's characteristics combine those of tantalum, which has a high corrosion resistance, with tungsten, the periodic table's element with the highest melting point. Due to its chemical inertness and high melting point, it was originally utilized commercially in dental equipment and incandescent light bulb filaments.
Tantalum has long been valued for its ability to resist corrosion in situations that are unfavorable to most other metals. Tantalum has been compared to glass in terms of its ability to resist corrosion, yet it is also ductile and has strength comparable to steel. Tantalum initially interacts with oxygen on the surface, creating a passive oxide layer that gives it corrosion resistance. The electronics sector currently uses the majority of the tantalum produced for capacitors. Porous anodes are created by pressing and sintering tantalum powders.
Tantalum oxide is produced anodically on tantalum, and the stability and dielectric characteristics of this layer are what give tantalum capacitors their outstanding performance. Applications needing compact form factors and great reliability over a wide range of operating voltages and temperatures use tantalum capacitors. Tantalum capacitors are utilized in high-risk fields like the military, aerospace, and healthcare.
Tungsten alloys, often known as heavy alloys, typically include 90–97% tungsten with the remaining metals acting as a matrix to increase the ductility and machinability of the finished alloy. Since these alloys are made by individual makers for very specific purposes, unlike steel or aluminum alloys, there is no real naming standard for them.
Tungsten is an excellent alloying component and can also serve as the foundation for other alloys; in the alloying process, tungsten has become a crucial component. Tungsten’s unique characteristics help endow base metals with high strength, corrosion resistance, and other beneficial qualities. Common alloys of tungsten include:
In the heavy metals sector, tungsten-nickel-iron alloys are the most popular alloys. Because they are generally unmatched by almost any other metal alloy in terms of density, ductility, and strength, tungsten-nickel-iron alloys are very common.
In the metals business, nickel-copper alloys are important for a few specific activities. Copper alloys are required if magnetic permeability is involved. Despite having lesser tensile ductility and strength, copper is still a useful material to use for cancer systems and operations, shielding electrical sensors, and rotating inertia members in guiding systems because of its lack of magnetic characteristics.
Based on the benefits provided by its characteristics, tungsten carbide is the most significant tungsten compound. On the Mohs scale of mineral hardness, tungsten carbide rates between 8.5 and 9, just behind diamonds at a solid 10. Tungsten carbide is also halfway between lead and gold in terms of density and stiffness, and it is nearly twice as rigid as steel. A chemical reaction between carbon powder and tungsten metal powder produces carbide. Carbide inlays are incredibly resistant to chemical corrosion and assaults and while still maintaining the strengths of unalloyed tungsten. 60% of all jobs that utilize tungsten employ tungsten carbide,
Molybdenum (Mo) is typically made using powder metallurgy procedures. Mo powder is hydrostatically compacted and sintered at roughly 3812°F (2100°C) to create molybdenum metal. Hot work is done between 1598 and 2300 degrees Fahrenheit (870-1260°C). Moly can only be used in non-oxidizing or vacuum conditions at high temperatures because it produces a volatile oxide when heated in air over around 1112°F (600°C).
At temperatures up to 3452°F (1900°C), moly alloys maintain good mechanical stability and strength. Compared to ceramics, its high ductility and hardness offer a greater tolerance for flaws and brittle breakage. Due to its superior thermal conductivity, minimal thermal expansion, and excellent mechanical strength at high temperatures, molybdenum is the material of choice for managing difficult thermal applications. It is the preferred material for use in heat sinks for electronic chips as well as vacuum/inert furnaces.
The excellent electrical characteristics of molybdenum have also led to its use in microelectronics as an electrode for photovoltaics and a thin film transistor in flat panel displays. Molybdenum is most commonly used as an alloying component for stainless steels, tool steels, and high-strength, low-alloy steels to improve their anti-corrosive qualities.
The melting point of molybdenum, a glossy, silvery metal, is 4748°F (2620°C), while its boiling point is 10,040°F (5560°C). Molybdenum is one of the best-performing metals in refractory settings because of its high strength, stiffness, and resistance to softening at rising temperatures. Excellent heat conductivity and a low thermal expansion rate contribute to these peak attributes.
For its durability and workability, the copper and zinc alloy known as brass has had a significant historical impact. The first brass, known as calamine brass, was probably created by the reduction of combinations of copper and zinc ores and dates to the Neolithic period. Brass, an alloy of copper and tin, is frequently referred to as bronze in ancient texts. The amount of zinc determines how malleable a brass is; brasses with more than 45% zinc are unworkable in either a hot or cold environment.
Brass Alloy Type | Composition |
---|---|
Manganese Brass | 1.3% Manganese, 29% Zinc, and 70% Copper |
Red Brass | 5% Zinc, Copper, 5% Lead, and 5% Tin |
Yellow Brass | 33% Zinc, Copper |
Admiralty Brass | 1% Tin, Copper, 28% Zinc |
White Brass | >50% Zinc, Copper |
Aluminum Brass | 2% Aluminum, 22% Zinc, 76% Copper |
Lead-free Brass | Zinc, Copper, and < 0.25% Lead |
Nickel Brass | 5.5% Nickel, 24.5% Zinc, and 70% Copper |
Although a granulated version is employed in brazing (soldering), these brasses, also known as white brasses, are of little economic significance. They also serve as the foundation for several alloys used in die casting. The malleable brasses can be further separated into those that can be worked cold (often those with less than 40% zinc) and those that must be worked hot (usually those with a higher zinc content).
These malleable brasses, also referred to as alpha brasses, are frequently employed in the production of pins, bolts, screws, and cartridge casings. The beta brasses (50-55% copper content) are less ductile but stronger and can be used to make window and door fittings, faucet handles, sprinkler heads, and other fixtures. Other elements, in addition to copper and zinc, are often added to brasses to enhance physical and mechanical qualities, corrosion resistance, machinability, or to change color.
These include the lead brasses, which are simpler to machine, the naval and admiralty brasses, whose resistance to corrosion by seawater is improved by a small quantity of tin, and the aluminum brasses, which offer strength and corrosion resistance in situations where the naval brasses may falter.
Brass alloys include:
1.64% iron, 1.02% tin, 60.66% copper, and 36.58% zinc. It is suitable for marine applications due to its toughness, hardness, and corrosion resistance.
A malleable metal with less than 35% zinc that can be used for pressing, forging, and other related tasks. Alpha brasses have a face-centered cubic crystal structure and only one phase.
This brass is a copper (between 60% and 85%) and zinc composition. It is used to mimic gold as a source of less-expensive jewelry.
Alpha-beta brass is often known as duplex brass, which contains 35–45% zinc. The β'-phase is body-centered cubic, tougher, and stronger than the α-phase, which it also contains. Brasses for alpha-beta are typically hot wrought. Muntz metal also features a trace amount of iron.
Iron-carbon alloys with a carbon concentration greater than 2% are melted to create cast iron. The metal is placed into a mold once it has been melted. Wrought iron and cast iron are produced differently. Cast iron cannot be manipulated with hammers or other tools. Cast iron contains 2-4% carbon and other alloys, as well as 1-3% silicon, which enhances the casting performance of the liquid metal.
There are other compositional variances in cast iron alloys. Manganese and other contaminants like sulfur and phosphorus may also be present in trace concentrations. The finer points of chemical composition and physical characteristics can also be used to further distinguish between wrought iron and cast iron.
Some of the cast iron alloys include:
The flake-shaped graphite molecules in gray iron give the metal its name. The graphite flakes are broken when the metal fractures, giving the shattered metal's surface its gray color. This is the source of the name gray iron. By changing the graphite composition and cooling rate during manufacture, it is feasible to regulate the graphite flakes' size and matrix composition.
Gray iron has a lower tensile strength and is less ductile than other types of cast iron. However, it provides a higher amount of vibration damping (the ability to reduce energy by absorbing vibration) and is a superior heat conductor. It is superior to all other cast irons in its damping capacity; it is 20–25 times greater than that of steel.
Iron carbide is created when carbon atoms mix with iron at the proper carbon concentration and rapid cooling rate. This indicates that the solidified substance has very few or no free graphite molecules. Because there is no graphite present, the broken face appears white when white iron is sheared. Its cementite microcrystalline structure has a high compressive strength, strong wear resistance, and is hard and brittle.
Although the brittleness of white iron deters it from being useful on its own as a manufacturing material, its abrasion-resistance occasionally makes it useful as a coating material to be added on a product's surface in some particular applications such as shell liners, pipe fittings, or cement mixers. This can be accomplished by making a portion of the mold out of a good heat conductor. In contrast to the remainder of the casting, which cools more slowly, this will swiftly remove heat from the melting metal from that particular location. Ni-Hard Iron is one of the most often used grades of white iron. This product has exceptional qualities for low impact, sliding abrasion applications due to the inclusion of chromium and nickel alloys.
Duralumin is an alloy containing 90% to 94% aluminum, 4% copper, 1% magnesium, and 0.5 to 1% manganese. These alloys are very tough. They are utilized in applications that call for hard alloys, such as the vehicle armor employed in the defense sector.
Duralumin is a lightweight, tough aluminum alloy. These were also the first deformable aluminum alloys commonly used. There are a few minor variants that vary in composition, type, and temper, with an average yield strength of 450 MPa.
In addition to being a tough, lightweight, and robust aluminum alloy, duralumin is impermeable yet reflecting. Because it is a malleable metal, it is simple to form. It is an excellent heat and electrical conductor. It has no smell and produces aluminum oxide when it interacts with nearby oxygen. Finally, it is corrosion-resistant.
Duralumin features a thin, corrosion-resistant surface made of a layer of pure aluminum that covers the core. In their normal form, duralumin alloys are generally pliable and workable. They are easily rollable, foldable, and forgeable. Additionally, they can be drawn into a variety of forms.
This chapter will discuss the applications and benefits of alloy metals.
Metal alloys are mixtures of various metals that retain the good qualities while excluding the undesirable ones. As a result, the compound is more durable than its pure metal parent. Since pure metals are frequently brittle, they are combined to form alloys which produce materials that are stronger yet more workable. In contrast to pure metal, where all of the atoms are the same, metal alloys have a variety of atoms. As a result, the atoms in metal alloys have a harder time moving around, making them typically much stronger and harder than pure metals. By employing alloys, one can construct stronger buildings or create stronger products. Stainless steel is an incredibly strong alloy.
Metal alloys are combinations and compounds of several metals and non-metals. While pure metals are chemically reactive and easily corroded, alloys can be created to withstand corrosion. Metals can be quickly eaten away by corrosion, which makes repairs expensive. Since the corrosion resistance of metal alloys is often substantially higher than that of pure metals, metal alloys aid in delaying and preventing this ongoing corrosion issue.
Compared to pure metals, metal alloys are also more adaptable. Metal alloys allow for further modifications and the enhancement of specific qualities that are more preferred in various applications of a workable material. Metal alloys combine the best characteristics of multiple materials while pure metals only contain their inherent traits, whether good or bad. In comparison to pure metals, metal alloys provide more possibilities for various projects.
Metal is combined with either another metal or nonmetal ingredient to form an alloy. In order to create a metal alloy, the components are typically melted, mixed together, and allowed to cool to room temperature. Many pure metals, such as gold’s softness, contain inherent traits which makes them unsuitable for some applications. However, metals can gain strength and other improved chemical characteristics by combining them to form an alloy. By making an alloy, other desired qualities may be improved or added like hardness, machinability, and corrosion resistance.
Aluminum 1100 is the softest of the aluminum alloys, which makes it easy to shape and form into a wide range of products for industrial and home use. It can be cold and hot worked but is frequently shaped by...
The term "aluminum coil" describes aluminum that has been flattened into sheets where their width is significantly higher than their thickness and then "coiled" into a roll. Stacks of individual aluminum sheets are difficult to...
Aluminized steels are steels that have been hot-dip coated with pure aluminum or aluminum-silicon alloys. This hot-dip coating process is termed hot-dip aluminizing (HAD)...
Aluminum piping and tubing is silvery-white, soft, and ductile. The metal belongs to the boron group. Aluminum is the third most abundant element present on earth. Aluminum has low density. When exposed...
Beryllium Copper is a versatile copper alloy that is valued for its high strength and hardness, combined with good electrical and thermal conductivity. It is a non-ferrous, non-magnetic, and non-sparking metal alloy...
A variety of copper-zinc alloys are referred to together as brass. Different ratios of brass and zinc can be used to create alloys, which produce materials with various mechanical, corrosion, and thermal properties...
Copper is a ductile, malleable, and reddish-gold metal with the capacity to effectively conduct heat and electricity. Brass and bronze, two commonly used alloys, are created when copper is combined with...
The copper sheet is a highly malleable and workable metal with outstanding electrical and thermal conductivity and corrosion resistance. Copper (Cu) is a reddish, very ductile metal that belongs to Group 11 of the periodic table...
Metals are a group of substances that are malleable, ductile, and have high heat and electrical conductivity. They can be grouped into five categories with nickel falling in the category known as transition metals...
Stainless steel grade 304 is an austenite stainless steel that is the most widely used and versatile of the various grades of stainless steel. It is a part of the T300 series stainless steels with...
Stainless steel is a type of steel alloy containing a minimum of 10.5% chromium. Chromium imparts corrosion resistance to the metal. Corrosion resistance is achieved by creating a thin film of metal...
Stainless steel grades each consist of carbon, iron, 10.5%-30% chromium, nickel, molybdenum, and other alloying elements. It is a popular metal used in various products, tools, equipment, and structures that serve in many industrial, commercial, and domestic applications...
Stainless steel can be fabricated using any of the traditional forming and shaping methods. Austenitic stainless steel can be rolled, spun, deep drawn, cold forged, hot forged, or stippled using force and stress...
Stainless steel tubing is a multifaceted product that is commonly utilized in structural applications. Stainless steel tubing diameters and variations vary greatly based on the application requirements and are...
Steel service centers are companies that specialize in procuring steel directly from mills and manufacturers and supplying them to the customers. They are fundamental to the steel supply chain...
Titanium metal, with the symbol Ti, is the ninth most abundant element in the earth‘s crust. It does not occur in large deposits, yet small amounts of titanium are found in almost every rock...
Tungsten is a rare naturally occurring chemical element on earth. It is known to be one of the toughest metals on the earth. It is usually a tin white or a steel gray metal. Tungsten is common for its high tensile...
Aluminum is the most abundant metal on the Earth’s crust, but it rarely exists as an elemental form. Aluminum and its alloys are valued because of their low density and high strength-to-weight ratio, durability, and corrosion resistance...