Band Heaters
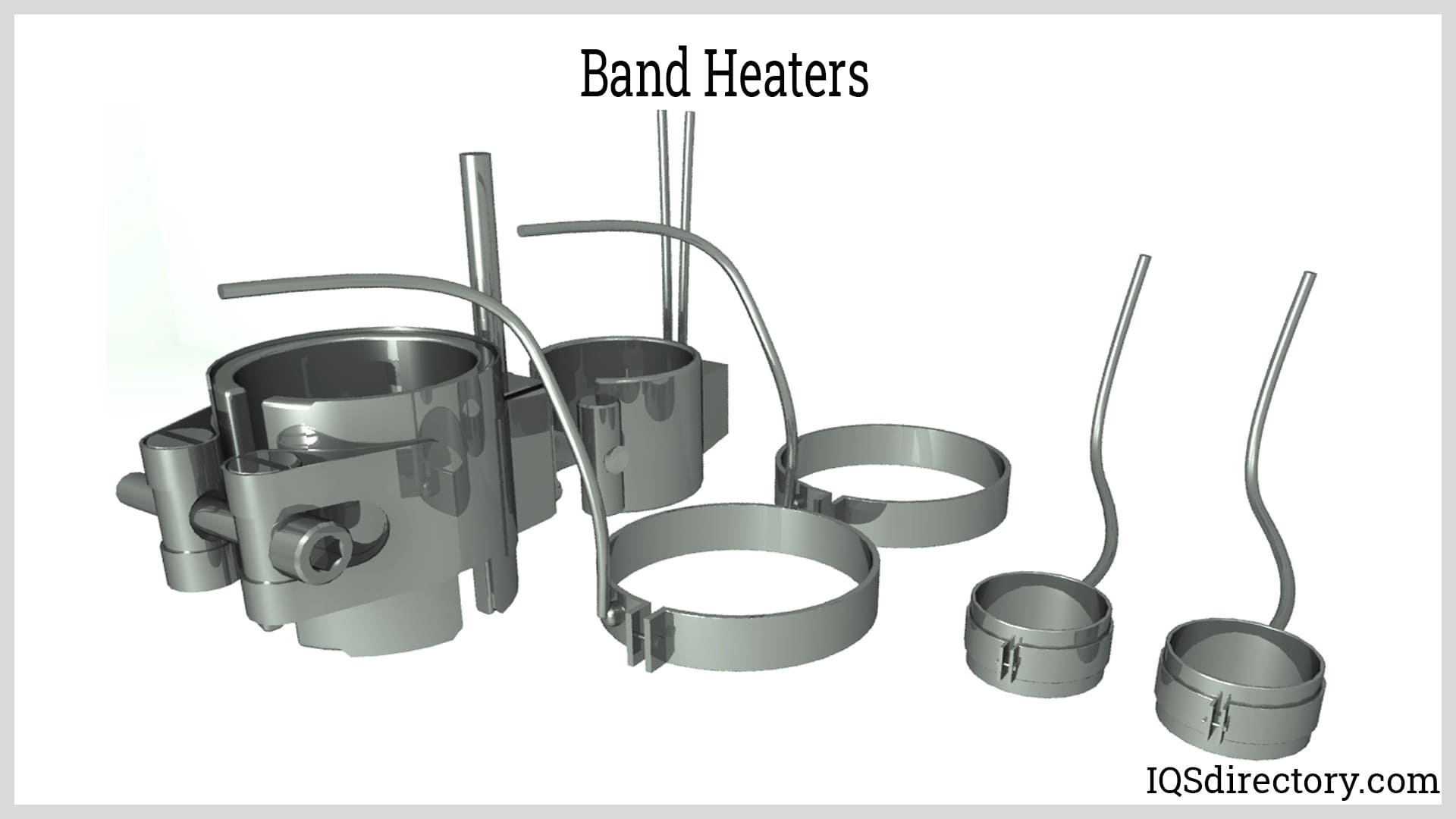
A band heater is a heating device that clamps onto objects to provide external heat using radiant and conductive heating. The different mounting methods of band heaters makes it possible to secure them tightly and...
Please fill out the following form to submit a Request for Quote to any of the following companies listed on
This article contains everything you need to know about Cartridge Heaters.
You will learn more about topics such as:
A cartridge heater is a cylindrical tubular heating device that provides concise and precise heating for various forms of materials, machinery, and equipment. Unlike an immersion heater, a cartridge heater is inserted into a hole in the item to be heated to furnish internal radiant heat. They are used in a wide range of manufacturing processes for providing precisely directed localized heat.
Cartridge heaters are easy to install and provide an even heat pattern with watt density to fit the needs of the application. To facilitate installation, heaters have a slightly smaller diameter than the diameter of the hole into which they are installed to provide a snug tight fit.
A common function for cartridge heaters is to heat metal blocks from the inside at a predetermined wattage to meet the needs of the application. For the heating of metal blocks or dies, a hole is drilled into the piece with a diameter larger than that of the cartridge heater.
The construction of a cartridge heater begins with a ceramic core with a resistance wire wrapped around it. The core and resistance wire are encased in a dielectric metal sheath made of steel or stainless steel. Heat is transferred from the resistance wire to the sheath and on to the material to be heated.
Operating wattage of cartridge heaters can be low, medium, or high. They are designed to withstand temperatures of up to 1400°F or 760°C. Cartridge heaters provide localized heat accurately and precisely that is sufficiently concentrated to meet the needs of a wide range of manufacturing applications.
A cartridge heater is selected and installed in an application in accordance with its wattage and the required heat for the application.
The use of a cartridge heater begins with the point of insertion. For heavy duty cartridge heaters, there is an insertion port or point on the device to be heated. In the case of metal molds and metal blocks, holes are drilled.
For uniform shaped pieces that need to be heated, hole placement is simply a matter of drilling a hole for the cartridge heater to be able to provide the most radiant heat. For complex machinery and molds, the placement of the hole becomes more complicated and requires precision planning.
The image below is of a plastic mixing block with an insertion point for a ten inch cartridge heater with a five inch heat length.
An important consideration for the placement of a cartridge heater is its diameter in relation to the placement hole. The basic rule is that the diameter of the heater be undersized by 0.004 of an inch relative to the hole where it is being placed. If you measure the diameter of a cartridge heater, it will never measure its labeled size. The chart below is a reference guide for hole diameters compared to cartridge heater diameters.
Cartridge Heater Diameter | |||||
---|---|---|---|---|---|
Imperial | Metric | ||||
Hole Diameter | Actual Maximum Diameter | Actual Minimum Diameter | Hole Diameter | Actual Maximum Diameter | Actual Minimum Diameter |
0.125" | 0.124" | 0.120" | 6 mm | 5.97 mm | 5.87 mm |
0.16" | 0.155" | 0.152" | 6.5 mm | 6.48 mm | 6.38 mm |
0.19" | 0.186" | 0.183" | 8 mm | 7.98 mm | 7.85 mm |
0.25" | 0.249" | 0.244" | 10 mm | 9.96 mm | 9.85 mm |
0.31" | 0.312" | 0.308" | 12 mm | 11.96 mm | 11.86 mm |
0.38" | 0.374" | 0.369" | 12.5 mm | 12.47 mm | 12.34 mm |
0.5" | 0.499" | 0.494" | 13 mm | 12.98 mm | 12.85 mm |
0.625" | 0.624" | 0.619" | 15 mm | 14.99 mm | 14.86 mm |
0.75" | 0.749" | 0.741" | 16 mm | 15.95 mm | 15.82 mm |
0.94" | 0.936" | 0.928" | 17.5 mm | 17.47 mm | 17.27 mm |
1" | 0.999" | 0.991" | 20 mm | 19.96 mm | 19.76 mm |
1.25" | 1.249" | 1.241" | - | - | - |
1.9" | 1.910" | 1.890" | - | - | - |
2.38" | 2.385" | 2.365" | - | - | - |
The heated length is the length of the cartridge heater minus the unheated or cold portion. For optimal performance, the heated length should match the length of the item being heated. Any portion that is unheated will create hot spots and cause the heater to fail. The standard for hi-density cartridge heaters is 10 mm at the lead end and 6 mm at the disc end. A 152 mm heater would have a heated length of 136.5 mm.
The operating temperature of a cartridge heater is dependent on the application. Factors that influence the operating temperature are watt density, fit inside the hole, and thermal conductivity of the material being heated. When cartridge heaters are used at high temperatures, a special electrical terminal is required. Another precaution is to have lead wires at a temperature lower than their maximum limit.
The watt density is the heat flow rate or surface loading that is measured in watts per square inch of heated surface area.
It is important to avoid having water, moisture, plastic, or other contaminants on the leads or the end of the heater. Moisture can be removed by baking the cartridge heater in an oven.
To avoid over temperature, the heater needs to snugly fit in the hole. If it is not properly fitted, it will overheat and burn out. Additionally, the leads should be out of the hole where they can reject heat, and the heated length should be completely enclosed in the material being heated.
The heater should operate 80% of the time. If it has a constant cycle of hot to cold and back to hot, the internal wires will oxidize, and the heater will fail.
The fit of the bore has to be ideal for the application. A poor fit can cause the heater to seize in the bore and block the hole.
A cartridge heater should never be completely inside the hole. A portion of it, usually the leads, should be located on the outside. On the other hand, a cartridge heater should be fully inserted without any gap at the inserted end. This is especially true of the heat length.
A cartridge heater should never be operated at its highest watt density. A control of the watt density at a lower level increases the useful life of the heater.
The image below is a three zone multi-zone cartridge heater being inserted into a nine zone plate.
The control of power is an important consideration for high watt density applications. Although on-off switches can be used, they can cause fluctuations in the temperature of the heater and the part. Thyristor power controls can extend the life of a cartridge heater and eliminate on-off cycling.
There are several types of temperature controls and sensors that can be used with cartridge heaters. Surface mounted temperature sensors are used the most. Thermocouples, RTDs, and thermistors have an adhesive backing allowing them to be mounted on the surface of a heater.
Digital temperature controllers come in several varieties with different input and output designs with thermocouple and RTD inputs being the most popular with a DC pulse output. A DC pulse output makes it possible to go to larger relays to switch the heater load and use proportional control.
The longevity and useful life of a cartridge heater can be significantly improved with the use of a cartridge heater control system. Although on-off switches can be an easier and more convenient method for using a cartridge heater, they do not provide the necessary control for accuracy and precision for a heating process.
The variations in cartridge heaters include maximum temperature, watt density, type of applications, heated length, overall length, tube diameter, and the type of heating element. These factors determine the kind of cartridge heater as well as how it will be used.
The basic construction of all cartridge heaters is the same regarding wiring, core, and casing. There are variations in the metals used, wires, and cores. The quality and longevity of a cartridge heater depends a great deal on the materials used to manufacture it.
Cartridge heaters with a thermocouple heat the surface directly and use complex formulas to determine wattage, density, and fit. The internal thermocouple is the sheath temperature, which makes them useful where space is limited. Thermocouples monitor sheath temperature of an electric radiant element and send a 4 to 20 ma signal to the DCS when the set temperature is exceeded.
The main purpose of thermocouples is overtemperature protection. The power and sensor leads of the thermocouple are placed outside the sheath together. There are many varieties of thermocouple cartridge heaters that are designed for specific applications. The thermocouple can be attached to the middle or inside of the heater.
Flanged cartridge heaters can be attached to the piece to be heated with a flange permanently attached to the exterior end of the heater. This type of configuration ensures a more secure fit of the heater.
In the swaging process, all of the elements are added to the heater, including the core, resistance wiring, and oxide powder, before the swaging process. Mechanical swaging forces the heater into a die that confines and reduces its diameter and compacts the interior components. This process enhances the heat transfer process and improves efficiency.
Magnesium Oxide is the oxide power that is used to fill the elements. It is an electrical insulator that allows heat to travel through but prevents electric shock if anyone comes in contact with the element when it is energized.
The specifications for a miniature cartridge heater are a length of three inches or less with diameters of 3.175 mm, 3.97 mm, 4.76 mm. The exterior of miniature cartridge heaters is usually made of 304 or 316 stainless steel. Most miniature heaters are swagged for shock and vibration resistance as well as dielectric strength.
With multi-zone cartridge heaters, each section of the heater has its own wound coil and power leads with two leads for each zone. In some configurations, the zones will have a single common wire for one of the leads, which allows for control of the individual sections. A benefit of the multi-zone system is the ability to turn off a zone when it is not needed, lowering the required energy.
Square cartridge heaters have a square or rectangular shape instead of the round diameter configuration. They have the same capabilities as round tubular cartridge heaters and are capable of being swagged and compacted. They can be clamped into milled slots on a tool surface to provide cost effective heating. Their unique configuration allows for easy removal for cleaning and maintenance.
Much like a flanged cartridge heater, threaded fittings ensure a secure tight fit of the cartridge heater in the application. Threaded fittings allow for fast swift removal and installation. Moisture seals are normally added for further protection.
The split sheath design of cartridge heaters allows the heater to expand to maximize heat transfer by increasing the contact with the walls of the bore. To enable the expansion process, the ceramic core of the heater is eliminated and replaced by tightly packed magnesium oxide (MgO) that is placed around the heater coil. This configuration increases dielectric strength and heat transfer. The stability and strength of split sheath cartridge heaters enhances their longevity and prevents bore seizure.
High density cartridge heaters deliver exceptional power in relation to their size and spread heat evenly over the casing of the heater. They are built to withstand rugged and tough working conditions such as high temperatures, vibrations, shocks, and expansion and contraction. Standard high density cartridge heaters have a cylindrical ceramic core with tightly wound resistance wire. The placement of the resistance wire allows the heater to have more than one power zone.
High temperature cartridge heaters are made for high temperature applications with temperatures that range between 1400°F or 760°C up to 1600°F or 870°C. Most high temperature cartridge heaters are swagged to maximize heat transfer and vibration resistance. Typical applications that use high temperature cartridge heaters are hot stamping, heat staking, sealing bars, forming, and heating platens.
The main function of a cartridge heater is to supply localized heat to assist manufacturing processes. They are designed for optimum performance to supply heat precisely and efficiently.
The effectiveness of a cartridge heater depends on its dielectric strength, heat transfer to the sheath, and heat transfer from the sheath to the metal being heated. Dielectric strength is measured by how well the heater keeps electric current in the coil.
The die casting process involves placing molten metal in an open or closed die to shape and produce various shapes and forms. An essential part of the process is to ensure that the temperature of the metal is monitored and controlled. Cartridge heaters are placed in a hole in the die such that it can carefully and accurately control the temperature of the molten metal. The process is closely regulated to guarantee the quality of the final casting.
The mold process is like the die process with variations regarding materials and methods. As with dies, it is necessary to closely monitor the solidification temperature of the heated metal. To assist in controlling the process, cartridge heaters are inserted into the mold. During solidification, the cartridge heater keeps the heat constant to avoid weaknesses and unevenness in the molded part.
Cartridge heaters are a close tolerance aid for the injection molding process serving as a method for temperature control. Their capacity to efficiently transfer heat ensures that the process reaches the desired temperature rapidly without wasting time or energy.
Food production demands the same type of accuracy and control necessary for die casting and molding with the basic difference being assisting in the accurate preparation of food. This is especially true in high volume food production where the cooking temperature is required to be constant throughout a production run. Heat control by cartridge heaters are major components in every aspect of food preparation.
The proper control of heat is an essential part of patient treatment in the medical field. Many curative processes require exceptionally close heat control for the safety of the patient and the success of the cure. Some of the uses for cartridge heaters include heat control of baby incubators, kidney dialysis machines, and injector ports. In a wide variety of medical applications, cartridge heaters are used to heat aluminum or stainless steel subassemblies to provide exceptional heat transfer and uniform temperature.
Engine block heaters prevent coolant and lubricants from freezing, which would cause severe engine damage if not heated. At very low temperatures, core plugs can be forced out of the engine block due to ice forming in the cooling galleries. Expansion plugs, sealing discs, welch plugs, or core plugs are placed around the engine block and cylinder head during the casting of an engine. They seal holes left in the engine block.
Of the different types of block heaters, cartridge heaters are the most effective and easiest to install. The process of thermal induction that cartridge heaters use quickly and efficiently heats the fluids in an engine and prevents freezing.
The extrusion process requires that the molten plastic be evenly heated when being forced through the mold by the screw. Cartridge heaters are installed in the extrusion process to assist in maintaining constant heat for the stability of products.
The benefits of cartridge heaters for the extrusion process include rapid warming and a very long service life. As with all cartridge heaters, ones for the extrusion process have to be customized to fit individual applications and can be inserted into the die to assist in maintaining a constant temperature.
Regardless of the use or type of cartridge heaters, the main components are the same but change and are altered to meet heat and size requirements. An important factor that cartridge heater engineers are most aware of is watt density, which is the rate of heat being transferred through the surface of the heater.
Watt density is a determining factor in the useful life of a cartridge heater. The higher the watt density, the higher the temperature becomes inside the heater. As the temperature rises, the components of a heater operate at a temperature that is at their maximum allowable limits. Excessive temperatures can shorten the lifespan of a heater.
The basic structure of a cartridge heater includes a ceramic core, resistance wire, insultation, a sheath, and lead wire. These common factors are arranged differently by manufacturers to improve the quality and heating capabilities of their products.
The split sheath type of cartridge heater does not have a core but contains a continuous running wire that is immersed in an insulating material. This type of cartridge heater is a recent development designed to overcome specific cartridge heater flaws.
Though ceramic is a common type of core, magnesium is also used. For cartridge heaters with a core, the resistance wire, which is usually nickel chromium, is wound around the core.
The heating coil is the resistance wire for the electrical load. There are several different options for resistance wire. The most common and popular variety is nichrome (NiCr), or nickel chromium, a type of wire that is used in heating elements such as toasters and space heaters. As with other electrical heating elements, the number of turns per inch around the core determines the watt density. Current flowing through the wire heats it, which heats the sheath of the cartridge heater.
To prevent the resistance wire from touching the sheath, the sheath is filled with insulation, which is normally magnesium oxide (MgO). If the resistance wire is allowed to touch the sheath, it would ground, short circuit, and melt the sheath causing heater failure.
While the sheath is being filled with MgO, the sheath is vibrated to ensure a tight complete packing. When a cartridge heater is swagged, the insulation is further packed and tightened.
The two functions of the sheath are to serve as the container for the cartridge heater elements and transfer heat to the material being heated. When inserted, the sheath is in continual contact with the material and efficiently transfers heat.
Various forms of alloyed metals are used to produce the sheath and include stainless steels 304 and 316 and Incoloy 800. For certain applications, the sheath is acid and corrosion resistant.
The chart below lists a few of the common metals used for sheaths with nichrome and Incoloy, a nickel alloy, being the most common.
Sheath | |
---|---|
Metal | Sheath Characteristics and Color |
Aluminum | Silver White, Malleable, Duct, Light Weight With Good Electrical, Thermal Conductivity, and Oxidation Resistant. |
Brass | Excellent Strength, High Temperature Resistance, Electrical Conductivity, Corrosion Resistance, and Low Magnetic Permeability. |
Copper | Reddish, Ductile, Malleable, Heat Conductivity, and Electricity Conductivity. |
Iron | Heat and Electricity Conductivity and Strongly Magnetic. Usually Combined with Other Metals. |
Nickel Alloys | Most Common of the Sheath Materials. Corrosion Resistant and has Exceptional Strength. |
Nichrome | High Thermal Conductivity, High Operating Temperature, Corrosion Resistant, Oxidation Resistant. |
Stainless Steel | Chemical and Corrosion Resistant With A High Pressure Rating. |
Steel | Malleable, Ductile, Exceptional Tensile Strength, Conductive, and Durable. |
The sealing process is designed to contain and seal the contents of the cartridge heater. This part of the process is completed once the MgO has been packed tightly around the coil and core. A common type of sealing material is epoxy, which allows the heater to pass various electrical tests and ensures dielectric material performance and prevents shorts.
There are a wide variety of termination types that differ according to the type of cartridge heater and the manufacturer. As can be seen in the diagram below, the leads can exit the cartridge heater in several different ways with straight being the standard method. In applications where the leads may be exposed to harmful chemicals or extreme heat, they are shielded with metal or silicone.
The kinds and types of lead wires vary depending on the conditions where the cartridge heater will be used. The lead wire provides the electrical connection for the cartridge heater. Since the lead wire is essential to the smooth and efficient operation of the cartridge heater, it is carefully selected to match the application and conditions. For high temperature cartridge heaters, fiberglass insulated wire is commonly used. The chart below provides a brief description of cartridge lead wires with their temp rating and qualities.
Cartridge Heater Lead Wires | ||
---|---|---|
Type Wire | Rating | Qualities |
Durable | 1022°F / 550°C | Flexible Not Waterproof |
TGGT | 482°F / 250°C | Durable Not Waterproof |
Teflon | 482°F / 250°C | Abrasion Resistance, Waterproof Small OD |
Silicon Rubber | 302°F / 150°C | Flexible, Waterproof Easily Marked |
Braided Silicon Rubber | 392°F / 200°C | Flexible, Waterproof Abrasion |
The seizing of cartridge heaters presents multiple problems for operation production and efficiency. When a cartridge heater seizes, it is stuck in the application and has to be removed by drilling it out of the hole, a process that causes major delays.
The problem of seizing led to the development of the split sheath cartridge heaters that expand in the hole to make contact with the material being heated. As the cartridge heater cools, it retracts and can be easily removed.
Another method to prevent seizing is the use of an anti-seize coating that is applied as the cartridge heater is inserted. Anti-seizing coatings are a high temperature, insulating, and thermally conductive coating that minimizes oxidation and improves heat transfer. It can be brushed or sprayed on to form a thin layer making it easy to insert the cartridge heater into the hole.
The diagram below provides an outline of the various components and parts of a completed cartridge heater.
Cartridge heaters have become an essential part of industrial processes that require localized heating. The popularity of cartridge heaters is due to their ability to provide efficient, precise, responsive, and dependable heat.
Cartridge heaters are exceptionally durable, capable of performing in the harshest conditions. They can be configured and designed to fit any industrial heating operation from warming molten plastic to keeping metal molds hot.
The many sizes, types, configurations, and adaptations of cartridge heaters makes them an ideal method for providing directed heat. Cartridge heaters can fit into any application that requires a powerful source of heat. They fit snugly into an application and transfer heat at the required focal point.
Cartridge heaters regulate air temperature devices and components that produce condensation that could damage them such as control panels and closed circuits. In the packaging process, they guarantee the smooth flow of glue.
An important requirement for all manufacturing processes is equipment and processes capable of withstanding the harsh conditions of production. Cartridge heater manufacturers are aware of the multiple uses and conditions that their products must endure and produce heaters to meet the conditions. These small heating devices are hard wearing and sturdy, able to withstand heavy impact and high pressure. Regardless of the conditions, cartridge heaters are the best type of heat transfer method.
Several industrial applications require a precise and controlled focusing of heat to fit the stipulations of an application. This type of precision is necessary to ensure the quality and performance of the parts and components being produced. These requirements are the main reason that cartridge heaters have become an essential part of production applications. Cartridge heaters supply heat in a minutely focused, controllable, and accurate manner using the most advanced technological engineering.
The low cost and exceptional performance of cartridge heaters makes them an economical solution to manufacturing‘s heat transfer needs. They use little energy, require minimal maintenance, and efficiently execute the heat transfer process. A concern for modern manufacturing is their environmental footprint. Cartridge heaters have no environmental impact while efficiently assisting in process heating.
A vital concern for heating processes is overheating, which can severely damage final products and the heating equipment. The temperature sensing capabilities of cartridge heaters prevent overheating eliminating the need for monitoring and management. Cartridge heaters offer focused, controlled, localized heat efficiently and unsupervised.
The temperature sensing features of cartridge heaters increase the efficiency of the heat transfer process and extend the lifespan of the heater.
One of the features of cartridge heaters that impresses manufacturers is the amount of heat that is produced from such a compact design. This aspect of cartridge heater design has led to their wide use. With a small investment, producers are able to provide highly concentrated heat and improvements to process performance.
A band heater is a heating device that clamps onto objects to provide external heat using radiant and conductive heating. The different mounting methods of band heaters makes it possible to secure them tightly and...
Ceramic heaters are electric heaters that utilize a positive temperature coefficient (PTC) ceramic heating element and generate heat through the principle of resistive heating. Ceramic materials possess sufficient electrical resistance and...
Electric heating is produced by using a known resistance in an electric circuit. This placed resistance has very few free electrons in it so it does not conduct electric current easily through it. When there is resistance in...
A flexible heater is a heater made of material that can bend, stretch, and conform to a surface that requires heating. The various forms of flexible heaters include polyimide film, silicone rubber, tape...
An immersion heater is a fast, economical, and efficient method for heating liquids in tanks, vats, or equipment. Known as bayonet heaters, they have heating elements that can be directly inserted into a container of water, oil, or other material in order to heat the entire contents...
Infrared heating is a heating method used to warm surrounding bodies by infrared radiation. Thermal energy is transferred directly to a body with a lower temperature through electromagnetic waves in the infrared region...
The idea of an electric heater seems to be out of place in modern society since most buildings have a sophisticated central heating system. That may be true, but electric heaters can be a helpful way of saving energy while providing efficient heating...
A heating element is a material or device that directly converts electrical energy into heat or thermal energy through a principle known as Joule heating. Joule heating is the phenomenon where a conductor generates heat due to the flow of electric current...
Radiant heaters are systems that generate heat internally and then radiate it to the nearby objects and people. The sun is a basic example of a radiant heater. When we feel warm on our bodies on a sunny day...
An AC power cord is a detachable way of providing an alternating current of electric energy from a mains power supply to an electrical appliance or equipment. Serving industries like...
Electrical plugs, commonly known as power plugs, are devices responsible for supplying and drawing current from a receptacle to the circuitry of an electrical appliance...
A NEMA connector is a method for connecting electronic devices to power outlets. They can carry alternating current (AC) or direct current (DC). AC current is the typical current found in homes, offices, stores, or businesses...
A power cord is an electrical component used for connecting appliances to an electrical utility or power supply. It is made from an insulated electrical cable with one or both ends molded with connectors...
Thomas Edison developed the power distribution system in 1882. He wrapped a copper rod in jute, a soft shiny fiber from plants, as an insulator. The jute wrapped copper rod was placed in a pipe with a bituminous compound...