Band Heaters
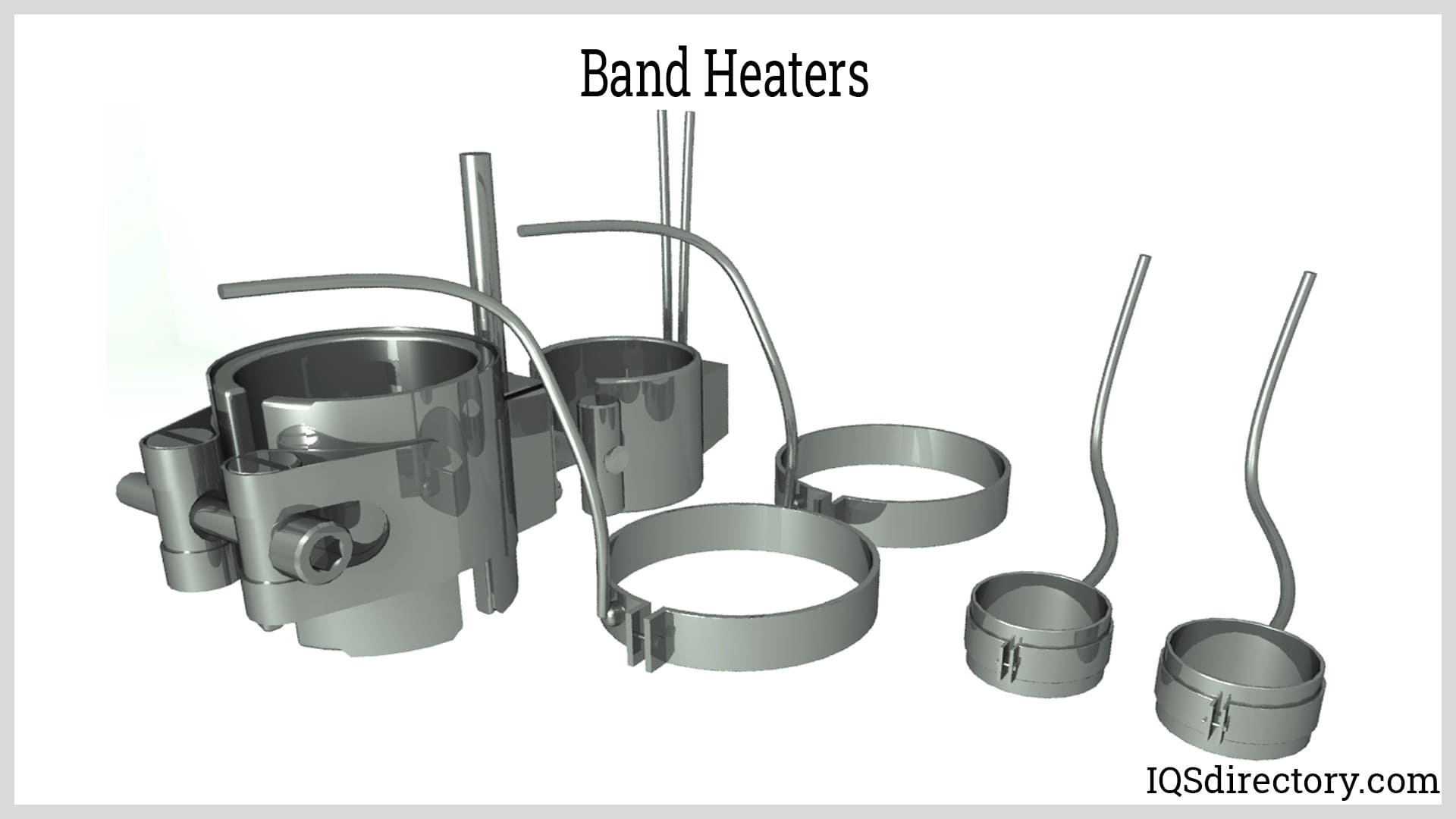
A band heater is a heating device designed to clamp onto objects and deliver external heat through both radiant and conductive methods. Its various mounting options allow for a secure and precise attachment....
Please fill out the following form to submit a Request for Quote to any of the following companies listed on
This article takes an in depth look at electric heaters and their advantages.
It will cover topics such as:
Electric heating is achieved by using a resistor within an electric circuit. This resistor has few free electrons, so it does not conduct electricity easily. As electrons encounter resistance, heat is generated, which provides the energy needed for electric devices to function. Although electric heating is highly efficient, it can be costly due to the high amount of electrical energy required. Electricity is more expensive compared to other energy sources like water, gas, and fossil fuels. However, electric heaters often have lower purchase and installation costs, making them attractive to buyers. For domestic use, electric heaters are typically insulated with plastic materials to prevent electric shocks and reduce energy loss.
Electric heaters consist of a heating core that warms up when an electric current flows through it. There are two main types of heating cores used in these devices: oil-filled cores and dry cores. Dry cores, typically made from ceramic, are lightweight and leak-proof. These ceramic radiators are energy-efficient and excel at retaining heat, which enhances their overall effectiveness. The radiator's outer body is usually constructed from aluminum or steel, which aids in energy dissipation.
The oil-filled radiator contains oil that is heated to provide warmth, and it does not require refilling throughout the product's lifespan. The thermal liquid inside the radiator remains effective for the duration of its use. Resistor coils in these heaters can be either exposed and mounted on insulators, embedded in refractory insulation with a metal enclosure, or enclosed in a glass case within a printed circuit. Additionally, the radiator features fins that enhance heat dissipation by increasing the surface area.
All the electric heaters have a heating element that is an electrical resistor. They work on the principle of Joule’s law. These resistors convert the electrical energy into heat energy by emitting radiant energy. Resistors may be made up of metal alloy wires, non metallic carbon compounds, or any printed circuits. Modern electric devices use nichrome metal as heating elements. The electric heaters use nichrome metal wires as active elements with ceramic insulation.
There are generally three types of electric resistance heating wires that are used in modern resistors.
Open wire consists of nickel-chromium resistance wire mounted on ceramic or mica insulation. Proper protection of this wire is crucial, as direct contact with the wire by users or metal objects can result in severe electric shocks.
Open ribbon wire is similar in material to open wire but features a larger exposed surface area. This increased exposure heightens the risk of electric shocks if it comes into contact with objects or individuals.
Tubular cased wire consists of nickel-chromium resistance wire encased in a layer of magnesium oxide powder, which is then enclosed in a heat-resistant steel tube. This construction provides protection against electric shocks and enhances durability, ensuring a long-lasting performance.
Electric heaters operate based on Joule's Law. They consist of electrical elements that generate heat to warm the heater's core. When an electric current flows through the resistors within the heater, these resistors heat up and release energy as heat. This heat dissipates into the surrounding area, warming the core of the heater and achieving the desired temperature throughout the space. The electric current passing through the resistors charges the cathode in the electron tube, resulting in the production of heat.
Heat transfer occurs through three primary modes: conduction, convection, and radiation. Each mode processes heat differently. Let’s explore each method individually.
This method of heat transfer involves the transfer of heat from one heated molecule to the next, or between substances in direct contact. Energy is thus transferred from one substance to another through direct contact. Many electrical devices utilize this heat transfer method. The rate of heat conduction is influenced by the temperature gradient; higher temperatures result in a higher rate of conduction.
The convection mode of heat transfer is employed in immersion water heaters and other low-temperature heating equipment. When air contacts the heated element, it expands and rises, causing the cooler air to move in and replace it. This circulation of hot and cold air throughout the room or container aids in heating the air or water. The efficiency of the convection process depends on factors such as the temperature above the heated element, the size of the heater’s surface, and the heater’s placement.
Radiation is the heat transfer process where heat is emitted from a heated source and reaches other substances without heating the medium or anything in between. Most electric heaters use this method, radiating heat energy to warm their surroundings.
Electric heaters come in various types, each designed for specific functions and environments, making them suitable for use in homes, offices, and industrial settings. Some common types include air heaters, ceramic heaters, cartridge heaters, band heaters, coil heaters, drum heaters, industrial heaters, and Kapton heaters, among others.
Air heaters Air heaters are a type of electric heater that uses air to warm the surrounding environment. This category includes forced air heaters, radiant heaters, and space heaters. Forced air heaters use a fan or blower to circulate air, allowing cold air to enter the heater and return as warm air. Radiant heaters, on the other hand, rely on heat radiation from a heated element, with convection helping to distribute the warm air around the area. Space heaters are self-contained units that can operate using any of the aforementioned methods.
In an air heater, heat transfer occurs through convection, a process where heat is transferred via a fluid or medium. This creates a convection current, which can be either free-flowing or forced. Forced convection involves circulation generated by a pump or fan, while free-flowing convection relies on temperature variations and concentration gradients to drive the current.
Air heater is a broad type with about 7 options. They are duct heaters, enclosure heaters, forced air heaters, heat torches and flame heaters, radiators, space heaters or room heaters, and tubular heaters.
Duct heaters are designed to generate heat within gas streams. They are installed in the path of moving air or gas so that the air passing through the heater is warmed as it flows through the duct.
Enclosure heaters are specifically designed for use within enclosures. They help prevent freezing, offer protection, and regulate humidity levels inside the enclosure.
Forced air heaters use forced convection to circulate air from the heat source through a blower or fan.
These devices produce concentrated flames or streams of extremely hot air or gas. Heat torches and flame heaters are primarily used in industrial applications.
This type of air heater features coils through which heated liquids, such as oil, hot water, or steam, are circulated.
Space heaters, or room heaters, are designed for indoor use and do not emit harmful pollutants or poisonous gases. They are also portable, allowing for flexible placement.
Tubular heaters are typically used for customized heating applications, as their tubular elements can be bent into various shapes to fit specific needs.
Band heaters are ring-shaped heating devices designed to be clamped around cylindrical heating elements. They transfer heat through conduction from the outside of the elements. Some band heaters are clamped on the inner diameter of the heating elements. Typically, they are equipped with ceramic or mineral insulation to minimize heat loss to the environment.
Band heaters are insulated with specialized materials to minimize heat loss to the environment. Insulation options include ceramic, mica, fiberglass, or, in some cases, no insulation at all. Some band heaters may use a combination of these insulation types. While uninsulated band heaters may be used in premium applications, they are less energy-efficient. Ceramic insulation is highly effective as it resists both chemicals and heat, with ceramics made from non-metallic materials like clay being particularly durable due to high-temperature hardening. Mica is another excellent insulation material, known for its heat and acid resistance, making mica-insulated band heaters both efficient and reliable.
Key dimensions to consider for band heaters include the inside and outside diameters of the band, as well as its thickness and width. It is crucial to ensure that the inside diameter of the band matches the outside diameter of the cylinder to which it will be attached.
Band heaters offer various features, including cooling options, probe holes, cutouts on the bands, and expandable designs. They are attached or clamped to the heating material using several clamping methods. Examples of mounting options include bent-up flanges or tabs, built-in straps, separate straps, barrel nuts, and wedge locks or mounts.
To ensure optimal performance of band heaters, several parameters must be considered. These include the maximum operating temperature, required voltage, and sheath temperature. The maximum operating temperature refers to the highest temperature the heater can reach at its sheath covering. The required voltage indicates the minimum amount of alternating current needed for the heater to function properly.
Band heaters use a protective covering or sheath for their heating elements. This sheath can be made from various materials, including aluminum, brass, copper, iron, nickel alloy, steel, or stainless steel.
Termination type refers to the methods used for making electrical connections to the heater. Band heaters may offer several termination options, including insulated leads, armored cable leads, metal braided leads, flexible conduit leads, parallel screw terminals, terminal boxes, and quick disconnects.
The cylindrical shaped heaters are the cylindrical shaped ones with resistant heating elements. The heating element of the cartridge heater is insulated to prevent the sheath from touching the heating element. This sheath or sleeve that encapsulates the heater also provides a protective barrier. The cartridge heaters are usually inserted into the heated material and its cylindrical shape is used in many applications.
Before selecting cartridge heaters, several specifications should be considered, including the maximum operating temperature, sheath material, required voltage, sheath density, watt density, and other features. For industrial applications such as melting, casting, or molding, cartridge heaters can operate at temperatures up to 1500°C. Key dimensions to consider are the nominal diameter and the cartridge length or heated length.
The sleeve, sheath, or jacket is the protective material surrounding the heater's heating element. It can be made from various materials, including aluminum, iron, copper, nickel alloy, brass, stainless steel, or steel, each with distinct properties. Cartridge heater insulation options include ceramic, mica, fluoropolymer, fiberglass, or magnesium oxide. Ceramic insulation is made from non-metallic materials that harden at high temperatures and is resistant to chemicals and acids. Mica insulation consists of colored silicates, also resistant to chemicals and acids. Fluoropolymer insulation is used in applications involving harsh chemicals. Fiberglass insulation is popular for its strength, durability, and resistance to caustics. Magnesium oxide has a high melting point and can withstand extreme temperatures.
Flat ceramic fiber heaters are constructed with iron-chrome-aluminum heating elements and a thick layer of ceramic fiber insulation, all enclosed in a non-curved box. These heaters can be customized into various shapes and sizes to meet specific needs. Ceramic fiber heaters are known for their rapid heating capabilities, excellent temperature uniformity, fast recovery rate, and quicker cooling compared to other heaters. They offer several configuration options, including fully heated surfaces, unheated sides, or insulated edges. Other important specifications to consider include the maximum operating temperature, AC voltage requirements, and watt density.
Ceramic fiber heaters offer various options for heating coil configurations: coils can be fully embedded within the insulating material or partially embedded. Fully embedded coils provide several benefits, such as protection from media splatters that could cause fuming or sparking. However, flat ceramic fiber heaters with partially exposed coils may not achieve very high temperatures.
Coil heaters, also known as cable heaters, are elongated heating elements made from uncoiled segments of square or round tubular heating elements. They can be straight or shaped into various configurations, such as star-shaped or spiral-wound, depending on the application requirements. This flexibility allows for designs that enhance surface area or improve heat transfer capabilities. Coil heaters are encased in a non-metallic insulated sheath to protect against overheating and damage.
Coil heaters feature a layered heating element typically insulated with nickel-chromium alloy, which provides excellent resistive properties and generates heat. The insulation materials used can include ceramics, mica, magnesium oxide, fluoropolymer, and fiberglass. The sleeve material options for these heaters are diverse and may include aluminum, brass, iron, nickel alloy, rubber, stainless steel, and steel.
Coil heaters are configured based on their termination methods. They can be connected using various options, including plug configurations, terminal boxes, armored cables, metal braided cables, and plain leads.
Coil heaters are typically straight but can be customized into various shapes and sizes. They usually have square, rectangular, or round cross sections, but can also be formed into shapes such as star-wound, spiral-wound, closed coils, or straight cables. Straight cables are designed to pass through equipment, while closed coils provide optimal heat distribution. Spiral-wound heaters are low-profile and generate high temperatures, making them suitable for restricted areas. Star-wound coils are used in pipes to create turbulent air flow, enhancing heat generation. Most coil heaters operate on AC voltage and can be configured for either single-phase or three-phase power. Key dimensions for coil heaters include inner diameter, outer diameter, length, and width.
Duct heaters Duct heaters are used to generate heat in moving gas streams. They are installed within the gas stream, creating forced flow heat convection. In addition to convection, these heaters emit radiation, transferring thermal energy to surrounding components. This method is ideal for applications such as molding, baking, drying, and preheating solid objects. Duct heaters are designed to withstand explosions and are suitable for use in hazardous environments.
Duct heaters use various heating elements, including open coil, tubular, and finned types. The sheath insulation options are similar to those used in other heaters and include ceramic, fiberglass, mica, or no insulation. Open coil heating elements are insulated with ceramic material, which isolates the resistive heating elements. They are a cost-effective choice for heating inert and non-corrosive gases when insulation is not necessary. Tubular heating elements provide both insulation and protection, making them suitable for high-temperature and high-airflow environments. Finned elements are designed for closed spaces and feature large fins that enhance heat dispersion.
The specifications for duct heaters are similar to those for other types of heaters and include maximum operating temperature, heating capacity, maximum air flow, and sheath material. Key dimensions to consider for duct heaters are the height, width, and length of the unit.
Immersion heaters are designed to be placed directly into the substance that needs heating, typically a liquid. They heat the liquid by direct contact. These heaters often come equipped with pipe threads, flanges, and other mounting hardware. Immersion heaters are explosion-proof and suitable for use in hazardous conditions. Key specifications for immersion heaters include performance characteristics, heat capacity, density, and sheath material.
Immersion heaters use various sleeve and sheath materials to protect the heater from damage. Insulation materials include iron, nickel alloy, steel, stainless steel, aluminum, brass, copper, and synthetic rubber. Steel sheaths can withstand temperatures up to 400°C and are typically used for heating oils. Copper sheaths are rated for temperatures up to 180°C and are used for heating municipal water. Nickel alloys can handle temperatures ranging from 760°C to 870°C and are used for heating water, strong and radiant alkaline solutions, air, and gases. Stainless steel sheaths are rated for up to 650°C and are used for heating deionized and process water, as well as some acids.
Mechanical specifications are crucial for immersion heaters. These include mounting options, such as threaded or flange mounts, as well as thread diameter, heated length, and the number of elements. Immersion heaters can be equipped with either threaded or flange mounting options, and the number of heating elements can vary according to the heater's specifications. An increase in the number of heating elements enhances the heater's overall heating capacity.
Flexible heaters are typically crafted by carving, screen printing, or winding heating elements, allowing them to be bent and flexed easily to fit various surfaces. This flexibility ensures optimal surface contact for effective heating. Common types of flexible heaters include silicone rubber, Kapton film, carbon-printed, and transparent heaters. Each type offers unique specifications and can be customized in different shapes and colors. These heaters are known for their even heating, efficiency, reliability, and accuracy, with excellent moisture and chemical resistance. Their flexibility allows them to adhere to various substrates, making them highly adaptable for industrial, commercial, and military applications. Flexible heaters are thin, lightweight, and suitable for harsh environments and vacuum applications. They can operate at temperatures up to 260°C, with a continuous use temperature of 200°C.
Successful heating applications rely on effective and efficient heat transfer. Flexible heaters achieve this by conforming to the surface that requires heating, minimizing energy loss and ensuring complete thermal energy transfer from the heating elements. When designed and installed properly, flexible heaters provide uniform heat distribution. Additionally, these heaters often come equipped with various sensors and temperature controls, such as thermostats, thermal fuses, thermoresistors, and other electronic components, enhancing their performance and precision.
Kapton heaters, made from polyamide, feature a thin, lightweight polymer film known for its excellent tear resistance, tensile strength, and dimensional stability. These heaters are used in conjunction with flexible heaters and offer robust resistance to fungi, radiation, and various substances. The heater foil includes circuit patterns that reduce production costs while delivering optimal heating performance. Kapton heaters provide outstanding thermal and dimensional stability and are even used in space applications due to their excellent vacuum performance. They are resistant to chemicals, acids, and solvents, and their good adhesive properties make them suitable for bonding with metals. Kapton heaters can be joined with other alloys, such as nickel, copper, or iron. They have a density that is twice the watt density of many other heaters.
Silicone rubber heaters come in two main types: wire-wound and etched foil. In wire-wound heaters, resistance wire is coiled around a fiberglass core for added stability and support. Etched foil heaters, on the other hand, consist of thin metal foil with a wire wound into smaller to medium-sized patterns.
Silicone rubber heaters are wire-wound, offering excellent strength and durability while maintaining their performance and lifespan even under flexing. These heaters are highly versatile and can be adapted to fit any three-dimensional shape, or customized into various shapes as needed. Termination options include ring terminals and spade terminals. Silicone heaters are protected by a range of materials, including rubber and fiberglass sleeves.
Strip heaters consist of heating elements, a sheath, and mounting hardware. They feature fins designed to maximize heat radiation over a wide area. Strip heaters are typically bolted or clamped to surfaces or walls to enhance heat transfer efficiency. These indoor heaters are used for applications such as cabinet warming, baking ovens, and vacuum dehydration. They operate by heating a thermoplastic sheet over an electric element, allowing the plastic to melt and be molded into various shapes. Made from thermoplastics like acrylic, strip heaters utilize convection for heating and can operate at temperatures up to 1200°C.
Foil heaters are compact units with heating elements sandwiched between two layers of aluminum foil, making them ideal for surface heating applications. They typically operate at a sheath temperature of 300°F and come in lengths ranging from 4" to 60". Foil heaters can be equipped with thermostats and various cut-outs, and are available in low voltages as well as 120 or 240 volts. These heaters are constructed with multiple layers, including aluminum foil, an insulating sleeve, a premium-grade resistance element, and insulated leads. There are three main types of foil heaters: self-adhering, mechanically fastened (flexible), and mechanically fastened (semi-rigid). They offer different terminal options for connections, such as flexible leads, straight quick connectors, flag quick terminals, and spade terminals.
Electric heating offers both benefits and drawbacks. In this chapter, we will explore the advantages and disadvantages of electric heaters.
A band heater is a heating device designed to clamp onto objects and deliver external heat through both radiant and conductive methods. Its various mounting options allow for a secure and precise attachment....
A cartridge heater is a cylindrical, tubular heating device that delivers focused and accurate heat to a variety of materials, machinery, and equipment. Unlike an immersion heater, a cartridge heater is inserted into a hole in the item being heated, providing internal radiant heat...
Ceramic heaters are electric heaters that use a positive temperature coefficient (PTC) ceramic heating element to generate heat through resistive heating. Ceramic materials have a high electrical resistance and...
A flexible heater is designed from materials that can bend, stretch, and adapt to the shape of the surface being heated. Common types of flexible heaters include polyimide film, silicone rubber, and tape....
An immersion heater is a quick, cost-effective, and efficient solution for heating liquids in tanks, vats, or equipment. Also known as bayonet heaters, these devices feature heating elements that can be directly inserted into a container of water, oil, or other substances to heat the entire contents....
Infrared heating is a method that warms surrounding objects through infrared radiation. Thermal energy is transferred directly to cooler bodies via electromagnetic waves in the infrared spectrum....
Infrared heating is a method that warms surrounding objects through infrared radiation. Thermal energy is transferred directly to cooler bodies via electromagnetic waves in the infrared spectrum....
A heating element is a material or device that converts electrical energy into heat through Joule heating. This process occurs when a conductor generates heat as electric current flows through it....
Radiant heaters are systems that produce heat internally and then radiate it to nearby objects and people. A basic example of a radiant heater is the sun. On a sunny day, the warmth we feel on our skin is due to the radiant heat emitted by the sun....
An AC power cord is a detachable component used to deliver alternating current from a mains power supply to an electrical appliance or equipment. It is commonly used in various industries such as......
Electrical plugs, also known as power plugs, are devices used to connect an electrical appliance to a receptacle, allowing the transfer of current to the appliance's circuitry....
A NEMA connector is a type of plug used to connect electronic devices to power outlets. It can handle both alternating current (AC) and direct current (DC). AC is the standard current used in homes, offices, stores, and businesses...
A power cord is an electrical component used to connect appliances to a power supply. It consists of an insulated electrical cable, with one or both ends equipped with molded connectors...
Thomas Edison developed the power distribution system in 1882. He used jute, a soft, shiny fiber from plants, as an insulator by wrapping it around a copper rod. This jute-wrapped copper rod was then enclosed in a pipe filled with a bituminous compound....