Electrical Plugs
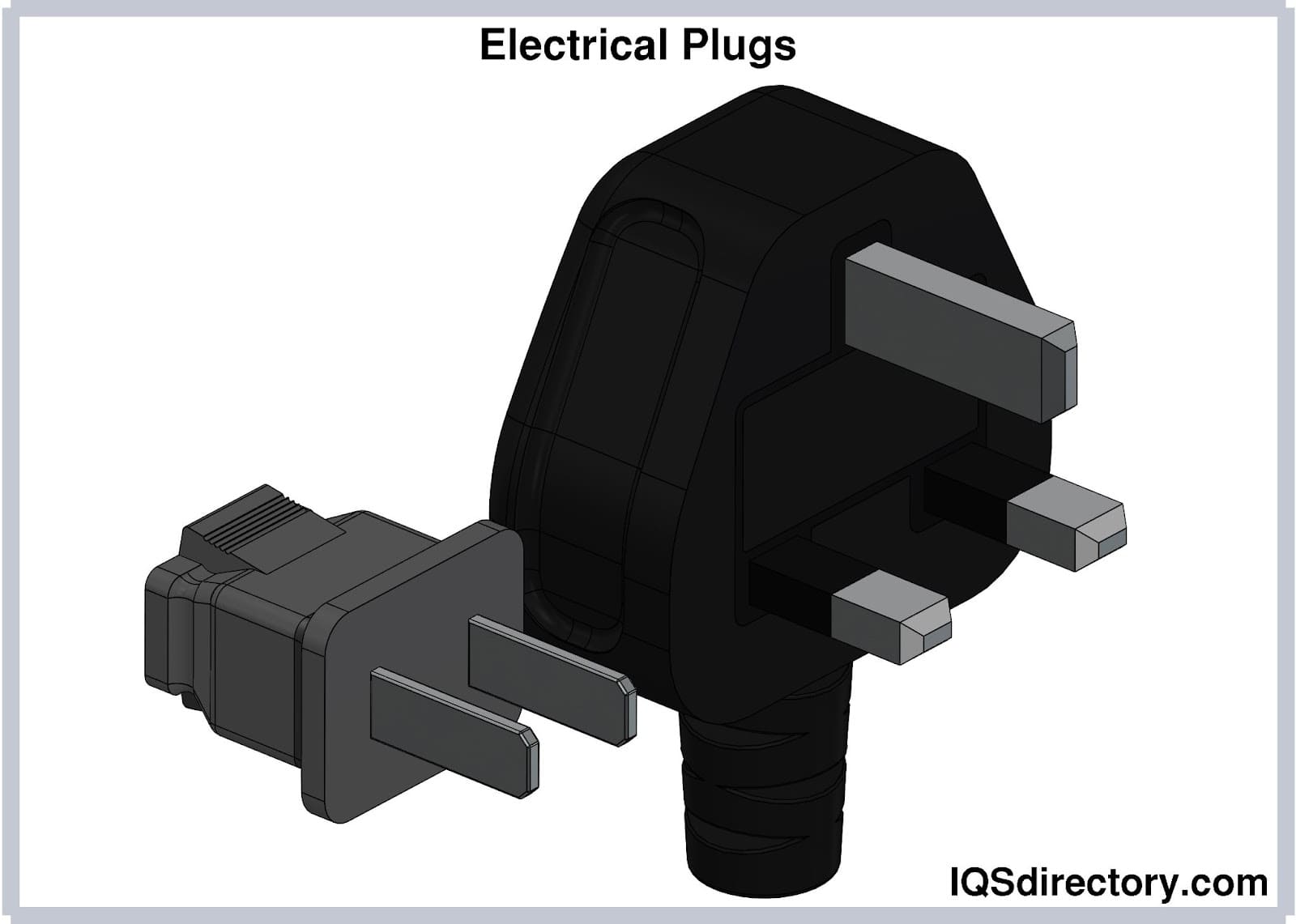
Electrical plugs, commonly known as power plugs, are devices responsible for supplying and drawing current from a receptacle to the circuitry of an electrical appliance...
Please fill out the following form to submit a Request for Quote to any of the following companies listed on
This article will take an in-depth look at AC power cords.
The article will bring more detail on topics such as:
This chapter will discuss what AC power cords are, their construction, and how they function.
An AC power cord is a detachable way of providing an alternating current of electric energy from a mains power supply to an electrical appliance or equipment. Serving industries like retail, commercial, industrial, electronics, entertainment, and residential, AC power cords are utilized for applications such as lighting, electrical power tools, household appliances, shop equipment, musical instruments, and many personal uses.
AC power cords utilize AC current; this is a flow where electrons reverse direction periodically. This flow of electrons transmits energy from a power source to electric equipment through a cord. The cord is a cable made of a conducting wire, generally copper, covered by cord covers, insulation, and an outer rubber or polymer jacket which protects the wire. The makeup of individual cord differs according to application.
Three main factors determine construction and materials:
Copper is an electrical conductor in various types of electrical wiring. Copper wire is utilized to generate power, transmit power, power distribution, electronic circuitry, telecommunications, and numerous kinds of electrical devices. Copper and its alloys are also used to produce electrical contacts. Electrical wiring in construction is the most vital market for the copper wire industry. Approximately half of all mined copper is utilized to produce cable conductors and electrical wire.
Two copper wires or more run side by side are braided, twisted, or bonded together into a single assembly from a copper cord. Stranding the wires can make electrical cords more flexible.
Copper wiring in a cord can be bare or it can be plated with a thin layer of tin to lower oxidation. Sometimes silver or gold is used too. Plating can extend wire life span and soldering is made easier. Coaxial cables and twisted pairs are constructed to prevent electromagnetic interference, inhibit signal radiation, and offer transmission lines with definite properties. Shielded cables are wire mesh or encased in foil.
This is a measurement of how well a conducting material moves an electric charge. This is an important attribute in electrical wiring systems. The electrical conductivity rating of copper is higher than for all metals. Copper electrical resistivity is 16.78 nΩm at 20 degrees Celsius. The theory of solid state metals aids in explaining copper’s remarkably high electrical conductivity. In a copper atom, the conduction band, or the outermost 4s energy zone, is only partially filled, making several electrons able to move electric current. When an electric field is subjected to copper wire, the electron conduction increases towards the positive end, hence producing current.
These electrons face resistance to their movement by collision with impure atoms, lattice ions, vacancies, and imperfections. The average distance moved between collisions is referred to as the "mean free path." This is inverse and proportional to the metal’s resistivity. Because of copper’s superconductivity, toughened copper is the standard in all countries where other conducting wires of electricity are compared to. Electrolytic-tough pitch copper is the major copper grade utilized for electrical applications. ETP copper has a small oxygen percentage.
Many metals which conduct electricity are lower in density than copper but need a bigger cross sectional area to move the same charge and might not be functional when small space is an important requirement. Aluminum is 0.6 times of the copper’s conductivity. The cross sectional size of aluminum conductors should be 0.56 times bigger than copper while the current carrying capability is the same.
Silver is one metal whose electrical conductivity is higher than that of copper. Silver’s electrical conductivity is 1.06 times that of hardened copper metal on the IACS scale. Silver’s electrical resistivity is 15.9nΩm at 20 degrees Celsius.
It is a measurement of the force needed to pull material like a structural beam, a rope or wire to the point of breaking. The tensile strength of an object is the maximum tensile stress it can endure before breaking.
The high strength of copper resists neck-down, stretching, breaks, and creep nicks and therefore also prevents service interruptions and failures. Copper is heavier than aluminum for conductors of the same current carrying capacity. Increased weight offsets its high tensile strength.
This material's capability to be deformed deform when subjected to tensile stress. It is often shown by the material's capability to be pulled into a wire. Ductility is very pertinent in metalworking since materials that break or crack in subjection to stress can’t be rolled, hammered, or drawn. The ductility of copper is higher than other metal conductors besides silver and gold. Since copper is highly ductile, it is easily drawn down to radii with extremely close tolerances.
The hardness, flexibility, and strength of copper make it very simple to work with. The copper wire may be installed easily and simply without special tools, pigtails, washers, or joint compounds. Copper is flexible so joining it is easy, and it’s hard so connections are kept securely in place. It can be twisted or bent easily with no breaking. It can be terminated and stripped during service or installation with way less danger of breaks or nicks. Also it can be terminated without using special fittings and lugs. All these factors combined makes it easy for manufacturers to make power cables using copper wire.
Aluminum wire is a kind of electrical wire for residential houses or construction that utilizes aluminum electrical conductors. Aluminum offers a better weight to conductivity ratio than copper. Therefore it is also used for power grid wiring, including power distribution lines, and overhead transmission lines. It has weight and cost benefits over copper wires.
Aluminum is an exceptional electrical and thermal conductor, having about 0.6 times copper conductivity, both electrical and thermal, while only having 0.3 times the density of copper. Aluminum is intensely affected by AC magnetic fields through eddy current induction as a result of its high electrical conductivity.
Aluminum has certain properties compared to copper, making it an undesirable wire as an electrical conductor. These properties all lead to likely fire hazards because of loose connections. These qualities are as below:
Aluminum is highly resistive to current flow, which implies that, given the same amps, aluminum wires should be of a bigger diameter than would be needed by copper wires.
Aluminum will break and fatigue down more easily when bent and subjected to other stresses than copper, which has more ductility. Fatigue causes the wire to internally break down and will gradually resist current, causing a build-up of excess heat.
In subjection to moisture, aluminum will go through galvanic corrosion when it touches certain dissimilar metals.
Exposure to oxygen causes degradation to the wire’s outer surface. Aluminum wire oxidizes more simply than copper wire. Aluminum oxide compound is created by this process and it is less conductive than oxidized copper. As time lapses, oxidation can degrade connections and creates fire hazards.
Aluminum is malleable and soft, so it is very sensitive to compression. If a screw on aluminum wiring is overtightened, the wiring will continually "flow" or deform even if the tightness has stopped. These degradations will make loose connections and increase resistance in that area.
More than copper, aluminum contracts and expands with changing temperatures. Over time, this will cause a connection between the device and the wire to degrade.
The electrical current causes vibration while it passes through the wire. In aluminum, this vibration is more intense than it is in copper, so, as time lapses, it may cause connections to become loose.
Insulation is a non-conductive material in a cord’s construction. It is also sometimes referred to as dielectrics in radio frequency cords. Insulation is resistive to current leakage, which prevents the conductor’s current from touching other conductors and cords nearby. It also maintains the wire’s material integrity by shielding it from environmental threats like heat and water. The effectiveness and longevity of a wire depend on the insulation.
There are numerous various types of wiring and cord insulation materials offered, and they differ depending on the application. The three major insulating materials are rubber, plastic, and fluoropolymer. Wire insulation and cord insulation are basically the same. Wire insulation is the insulation of one conductor that is wire definition. Cord insulation is generally a cord made of multiple conductors/wires. Cord insulation may mean the type of insulation covering each wire or cord insulation as a whole. The insulation type and insulation level for a cord depend on the application use.
The plastic insulation used can be:
PVC is quite cheap and easy to implement cable and wire insulation materials with the ability to be utilized in various applications. PVC insulation material ranges in temperatures from -55° Celsius to 05° Celsius and is flame resistant, abrasion, and moisture. It can also withstand exposure to ozone, gasoline, acids, and solvents.
PVC may be utilized as insulation material for food-related and medical purposes since it is odorless, nontoxic, and tasteless. PVC insulation material may be utilized in thin-wall and heavy applications. However, it must not be utilized where extended flex and flexibility life are needed at a low temperature. When utilized in retractile cord uses, it presents flexibility below average. PVC presents capacitance loss and high attenuation, meaning that energy is lost when utilized in electrical systems.
Semi-Rigid PVC is primarily utilized as primary insulation and is extremely resistant to abrasion. Semi-rigid PVC is resistive to acid, heat, water, and alkali. It is also retardant to flame.
It is best for usage in plenum spaces. This is a building space on raised floors or dropped ceilings left open to enable air circulation. Standard PVC is regarded as a non-plenum insulation choice since it does not show the attributes needed for safe use in plenum areas. The insulation should meet more strict fire safety standards to be rated plenum.
PE is mostly utilized in low-capacitance and coaxial cords because of its classic electric attributes. It is at times utilized in such applications for the fact that it is fairly cheap and may be foamed to lower dielectric constant to 1.50. This makes PE a prevalent choice for cords needing transmission at high-speed.
PE may also be cross-sawn to create high resistivity to cut-through, cracking, solvents, and soldering. It can be utilized in temperatures starting from -65°C to +80°C. All PE densities are hard, stiff, and inflexible. This plastic is also flammable. Additives may be utilized to make it retardant to flame, but it will trade off the dielectric constant, increasing power loss.
Polypropylene insulation (PP) is similar to PE but has a bigger temperature range from -30°C to +105°C. It is used generally for thin-walled primary insulation and may be foamed to enhance its electrical attributes.
PUR is popular for its extraordinary toughness, flex life, and flexibility also at low temperatures. It also has remarkable chemical, abrasion, and water resistance ratings. This plastic functions well in retractable cord applications and is a common choice for salt spraying and low temperature military applications.
PUR is a flammable plastic. It may be made retardant to flame, but this trades off surface finish and strength. PUR's main disadvantage, however, is its poor electrical properties. As a result, it is utilized more for jackets than insulation.
CPE is very resistant to oil, heat, and weather. CPE is a cheaper, more eco-friendly substitute than CSPE. Its dependable performance when subjected to fire also makes it a favorable substitute for PVC insulation. CPE is usually used in control and power cords and industrial power plant uses.
Nylon is usually preferred over soft insulation plastics. It is a tough jacket, showing strong chemical, cut-through, and abrasion resistance, particularly in thin walled applications. It is also exceptionally flexible. One drawback of nylon is its moisture absorption. This deteriorates some of its electrical attributes.
The rubber insulation used can be:
TPR is used to substitute true thermoset rubber. It has enhanced colorability, a wider functional temperature range, and high processing speeds. It also exhibits excellent weather, age, and heat resistance without curing. TPR is not cut through resistives but may be utilized in applications where the other attributes of rubber are needed.
A synthetic thermoset type of rubber, neoprene should be vulcanized to achieve its desired properties. It shows excellent cut-through, oil, abrasion, and solvent resistance. Neoprene is also popular for its extended life service, extensive range of temperature, and usability. It is outstandingly retardant to flame and self-extinguishes. Neoprene is particularly best for portable cord sets and is mostly utilized in military products.
Silicone is extremely flame-retardant, heat-resistant, and may be utilized in temperatures reaching 180° Celsius. It is averagely resistant to abrasion and exceptionally flexible. Advantages include good bonding attributes and a long storage life, which are important for numerous electrical applications.
EPR is popular for its exceptional thermal and electrical characteristics, enabling a small cross-sectional size for the same carrying load capacity of other cords. It is usually used in high-voltage cords. EPR is oxidation, heat, weathering, water, alcohol, acid, and alkali resistance.
The flexibility of this rubber makes it also suitable for temporary applications and installations in mining. EPR temperature ranges from -50°C to 160°C, however it is not as resistant to tears as other insulation materials. It is also comparatively soft and could need more care through installation to deter damage.
Rubber insulation usually alludes to both SBR compounds and natural rubber, each offered in various formulas for usage in an extensive range of applications. Because formulas differ, so does the temperature range and primary properties. While this kind of insulation has very low ozone and oil resistance, it shows decent electrical properties, low-temperature flexibility, and alcohol, water, and abrasion resistance.
The fluoropolymer insulation can be:
PFA has various temperature ratings dependent on cord construction, starting from -65°C up to 250°C. It also has a poor dissipation factor, making it electrically efficient as an option. It does not show thermoset properties, restraining it to usage only in handpicked applications. PFA is also an expensive insulator.
PTFE is a thermoplastic insulator that has temperatures ranging from -73°C up to +204°C. It is exceptionally flexible and resistant to oil, water, heat, and chemicals. The mechanical attributes of PTFE are less in comparison to other fluoropolymer rubbers.
Thermoplastic elastomers have a mixture of polymers, usually rubber and plastic, to join the advantages of each object into one insulating material. TPE can be extruded, molded, and recycled like plastic material yet maintaining the stretch of rubber and flexibility.
TPE is generally utilized in applications where usual elastomers will not offer the needed range of physical attributes. TPE is currently being used continually in household appliances and automotive applications. Drawbacks of TPE involve bad heat and chemical resistance, higher price than other kinds of insulation, and low thermal stability.
AC power cords carry alternating current from an AC power source which is usually a wall socket to the equipment or appliance. They offer a low resistance path for alternating current to flow through. Live wire carries the 230V/120V AC from the power supply to the appliance. The current alternates periodically at 50 times per second. A neutral wire carries the current back to the power source. More precisely, neutral wire brings current to a busbar or ground typically connected distribution box. This gives current flow through an electrical system, enabling electricity to be utilized fully. Earth wire protects the user from electric shock. It does this by offering a path for a faulty current to flow to the ground. It also makes the fuse or circuit-breaker switch off the current when there is a fault.
The considerations when choosing AC power cords include:
Cord current rating refers to the amount of current a cord can carry without overstressing or overheating. It depends on several factors, including the cord insulation, current frequency, electrical resistance and ambient temperature.
Rated voltage is a necessary specification to look out for when choosing an AC power cord. Other facets of a cord’s design are affected by its rated voltage, like the thickness and type of its insulation. Most cords made for high voltage applications utilize thick thermoplastic insulations, which has normally replaced the older paper and oil insulations utilized.
AC power cords are differentiated by their connectors or more formally known as couplers. AC power connectors enable the connection between electronic devices and appliances to available power outlets. Besides connectors, plugs are also used. There are numerous types of connectors and plugs and the most common are discussed below.
An international standards body, International Electrotechnical Commission created the basis for the IEC 320 C13/C14 connector. The "320" is the figure of the specification which describes power connectors. Number "60320" is actually the official text of the standard, but general vernacular use shortens it to "320".
The AV and PC industry very commonly use the C13 line socket. C14 plug is the male connector for the C13 female socket, which is mostly placed onto a recessed chassis or panel on power transformers or PC power supplies.
A polarized power connector is mostly found on notebook computer’s AC power cords. Three circular prongs ordered in a triangular way are found on the C5 connectors. A popular slang title for this connector is "Mickey Mouse ears connector", alluding to the shape which looks like the silhouette of the cartoon character from Disney. This power cord is usually used on laptop power supplies.
It is a 2-pronged connector utilized on AC power cords for radios, power transformers, and other electronic devices. It has two circular prongs side-by-side. It is also non-polarized. C7 Power cords are generally utilized to supply low voltage equipment like portable laptop power supplies, CD players, and video or audio equipment.
The C7 connector has a polarized version. The square shape of the overmold maintains the polarized prongs of this connector on one side of the connector. This design guarantees that the neutral terminal of a device is always connected to the neutral wires of an AC supply.
C15/C16 may be utilized in conditions where the equipment temperature can be high. An instance of when this connector can be used is in data centers where equipment is close in proximity to one another in confined environments. The connectors have keys to avoid mismatching the inlet and connector "cold" and "hot" configurations. Its shape is similar to the C13/C14 connector, besides the bottom notch.
Its temperature rating is higher than that of the C13/C14 connector. It has another version, C15A/C16A, utilized in more high temperatures. This version has a rectangular ridge at the upper end of the molding. These AC power cords are utilized in industrial applications.
The terminals are horizontally oriented. The connector molding is shaped rectangular with the edges fileted. It is utilized on power cords for high-rating for electrical devices and power supplies where C13/C14 connectors are not suitable. This is usually servers or professional IT equipment. The maximum amperage rating is 15A. It can be utilized in Class I equipment.
A type G plug has an inbuilt fuse usually rated 13 A. Its main purpose is to protect the flexible power cord linking the appliance and plug. As a result, it also protects the appliance from overloading. It is probable for a type G socket to accept a type C plug.
This practice is not recommended and unsafe. Its primary standard is BS 1363. More standards have been produced from BS 1363, which follow the same socket and plug specifications.
This chapter will discuss the applications and benefits of AC power cords.
The applications of AC power cords include:
As with any material that bears the electrical current transfer, there are pertinent safety considerations to be observed. Polarization, or grounding, is particularly important for some higher voltage electrical equipment and appliances that may have a higher possibility of shock. Polarizing an electric plug guarantees that the appliance is connected to the ground, or neutral, side of the circuit, and the risk of potential electric shock is reduced for anyone handling the appliance. Sensitive electrical products and equipment must only be used with grounding or polarized AC power cords.
Not much maintenance can be done on AC power cords because they are passive devices with no moving parts. However some steps may be taken to make sure a cord’s life is extended. This includes making sure that the power cord is used at the rated amperage by the manufacturer to avoid overheating. In server rooms or anywhere where the power cords are many, they must be tied in an orderly manner to prevent entanglement. AC power cords should be used in dry places where moisture cannot leak into the connectors as this is preventative maintenance. Dusting the power cords regularly keeps them nice and tidy.
An AC power cord is a removable means of offering alternating current of electric energy from a mains power supply to an electrical appliance or equipment. Serving industries like retail, commercial, industrial, electronics, entertainment, and residential, AC power cords are utilized for applications such as lighting, electrical power tools, household appliances, shop equipment, musical instruments, and many personal uses. They offer a low resistance path for alternating current to flow through. Live wire carries the 230V/120V AC from the power supply to the appliance. The current alternates periodically at 50 times per second. The cord is a cable made of a conducting wire, generally copper, covered by cord covers, insulation, and an outer rubber or polymer jacket which protects the wire. AC power cords are differentiated by their connectors or more formally known as couplers. AC power connectors enable the connection between electronic devices and appliances to available power outlets. Besides connectors, plugs are also used. The choice of an AC power cord is determined by rated current and voltage.
Electrical plugs, commonly known as power plugs, are devices responsible for supplying and drawing current from a receptacle to the circuitry of an electrical appliance...
A NEMA connector is a method for connecting electronic devices to power outlets. They can carry alternating current (AC) or direct current (DC). AC current is the typical current found in homes, offices, stores, or businesses...
A power cord is an electrical component used for connecting appliances to an electrical utility or power supply. It is made from an insulated electrical cable with one or both ends molded with connectors...
Thomas Edison developed the power distribution system in 1882. He wrapped a copper rod in jute, a soft shiny fiber from plants, as an insulator. The jute wrapped copper rod was placed in a pipe with a bituminous compound...
Power supplies are electrical circuits and devices that are designed to convert mains power or electricity from any electric source to specific values of voltage and current for the target device...
An AC power supply is a type of power supply used to supply alternating current (AC) power to a load. The power input may be in an AC or DC form. The power supplied from wall outlets (mains supply) and...
A DC DC power supply (also known as DC DC Converter) is a kind of DC power supply that uses DC voltage as input instead of AC/DC power supplies that rely on AC mains supply voltage as an input...
A DC power supply is a type of power supply that gives direct current (DC) voltage to power a device. Because DC power supply is commonly used on an engineer‘s or technician‘s bench for a ton of power tests...
Electronic connectors are devices that join electronic circuits. They are used in assembling, installing, and supplying power to electrical devices. Connectors are an important component of every electronic equipment used in...
An electric switch is a device – usually electromechanical – that is used to open and close an electric circuit. This disables and enables the flow of electric current, respectively...
By definition a power supply is a device that is designed to supply electric power to an electrical load. An electrical load refers to an electrical device that uses up electric power. Such a device can be anything from...
A programmable power supply is a method for controlling output voltage using an analog or digitally controlled signal using a keypad or rotary switch from the front panel of the power supply...
Push button switches are electrical actuators that, when pressed, either close or open the electrical circuits to which they are attached. They are capable of controlling a wide range of electronic gadgets...