AC DC Power Supply
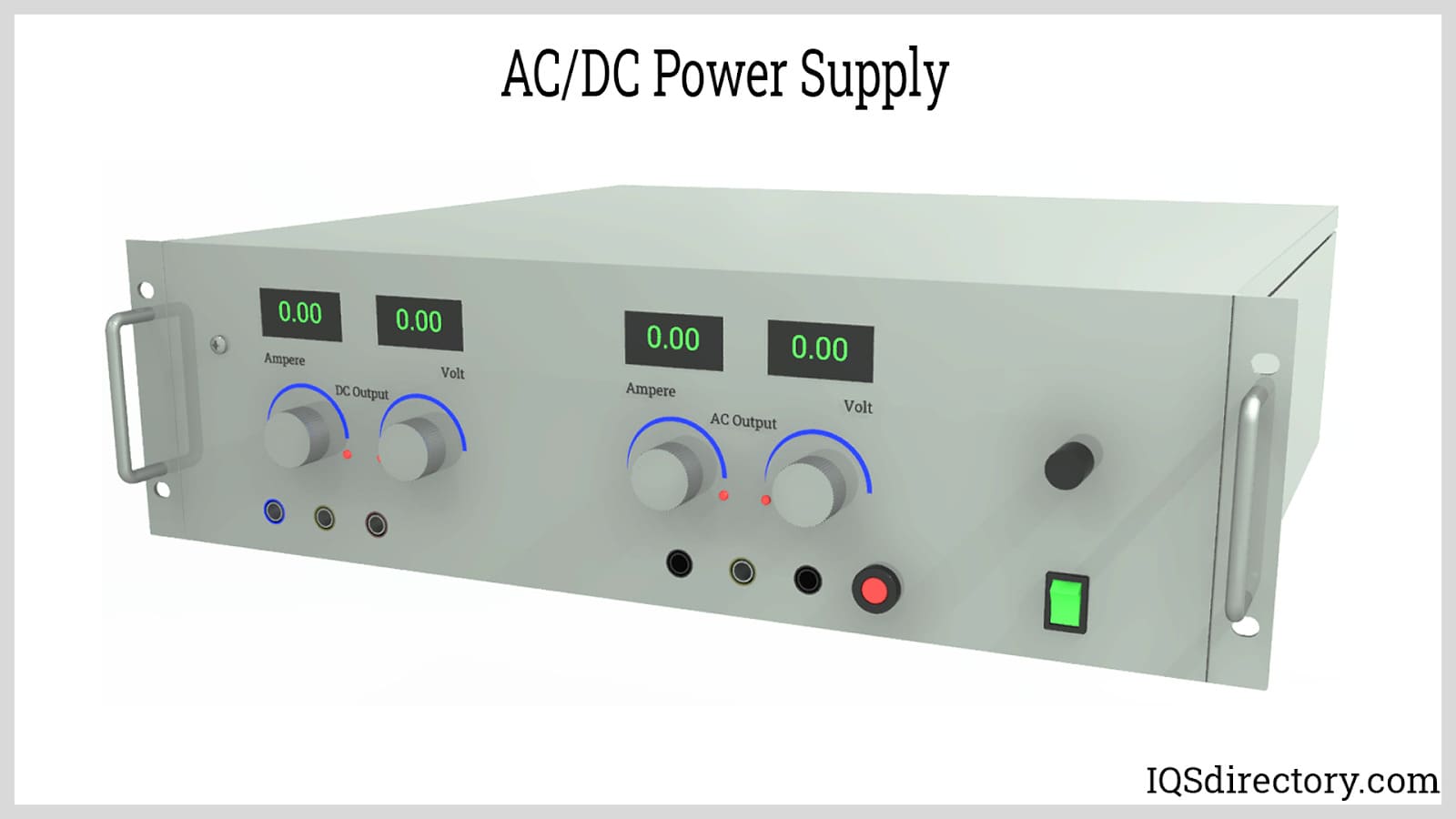
Power supplies are electrical circuits and devices that are designed to convert mains power or electricity from any electric source to specific values of voltage and current for the target device...
Please fill out the following form to submit a Request for Quote to any of the following companies listed on
This article will take an in-depth look at DC/DC power supplies:
A DC/DC power supply, known as DC/DC Converter, is a power supply that uses DC voltage as input instead of AC voltage. The main purpose of DC/DC power supplies is to produce a regulated voltage output for electronic and electric devices. Unlike AC voltage, DC voltage cannot be stepped up or stepped down using a transformer.
A DC power supply has two major power inputs:
An AC input can be rectified and filtered to produce a DC voltage, which is then applied to a regulator circuit, generating a constant DC output voltage. The output can range from less than a volt to >1000 volts.
A DC voltage with typical values, 5V, 12V, 24V, or 48V, can also be accepted by a DC power supply as an input. The output voltage can also be generated; this ranges from less than a volt to >1000 volts DC. A battery or harvested energy (solar cells, fuel cells, etc.), which derive their electrical power from other energy sources, can also be used as power inputs for a DC power management subsystem.
The DC power management subsystem is normally integrated with the electronic system of portable equipment. An AC adapter, a power unit that is plugged into the AC line outlet and gives a DC output voltage, is usually included in portable equipment that powers the unit. If there is a system battery, an AC adapter can also be used to recharge it.
Small amounts of energy from solar power, thermal energy, wind energy, or kinetic energy can be harvested by a power converter that can operate with ultralow voltage inputs. Once harvested, this energy is accumulated and stored for future use as a power source.
As discussed in the previous chapter, a DC power supply can be generated from an AC line. Most electrical and electronic circuits require a DC voltage source that is constant regardless of the change in the input. Although DC batteries can be used as an input, this option is expensive and requires replacement from time to time. So, it is necessary to first convert an AC input into a DC voltage source and regulate it to serve this purpose. This conversion has four major steps and can be represented by a diagram called Regulated DC Power Supply Block Diagram.
A step-down transformer is used in the first step of AC-DC voltage conversion. It is a device that converts a high primary voltage to a lower value (secondary voltage). A step-down transformer has two coil windings: primary and secondary, with the former having more coil winding turns than the latter.
The primary winding is connected to the main AC line. The secondary winding is isolated from the primary winding but electro-magnetically coupled with it.
There are three classifications of step-down transformers:
This type of step down transformer steps down both the current and input voltage ratings to produce a smaller current and voltage output.
This type of step down transformer consists of a primary winding and a secondary winding with a center split. In effect, the voltage output will have a center split (eg. 12V to 0 to 12V).
This type of step down transformer is used to achieve the desired output through secondary coils (eg. 0-12V, 0-18V). This is possible because of the several tappings within the secondary winding.
The transformer output is then received by the rectifier circuit as an input.
The second step of the AC-DC voltage conversion process is rectification. It is the step in which the AC voltage is converted into the corresponding DC quantity.
A rectifier is used to perform this process. It is an electronic circuit that consists of diodes.
Controlled and uncontrolled are the two major categories of rectifiers where controlled rectifiers use SCRs or thyristors while an uncontrolled rectifier uses diodes.
Rectifiers can also be classified as half-wave rectifiers and full-wave rectifiers.
A half-wave rectifier circuit utilizes a single diode. Half of the AC input signal is converted by a half-wave rectifier circuit into a pulsating DC output signal while the other half signal is lost. There are two types of half-wave rectifiers:
Three phase rectification is known as polyphase rectification circuits and are similar to single phase rectifiers in that it has three single phase rectifiers connected together. They are used when single phase rectifiers do not provide sufficient power.
Multi phase rectifiers are used to reduce harmonics in three phase rectifiers and consist of two 6 pulse rectifiers in series with 12 diodes to feed a DC bus. They stagger the current waveforms and improve the waveforms. They cancel the 5th and 7th harmonics making the first harmonic of significance the 11th one, which keeps voltage harmonic distortion below maximum levels.
The configuration of multi phase rectifiers continues into 18 pulse rectifier with three sets of 6 pulse rectifiers. As each additional rectifier is added, their cost and footprint increases.
A full-wave rectifier circuit consists of more than one diode. Both-half cycles (positive and negative) of the AC are converted into DC. Therefore, a double output voltage is generated. A full-wave rectifier circuit is classified into two types:
Since the output from the rectification process is a pulsating DC voltage with a high ripple content, a smoothening process called DC filtration is employed to remove these ripples from the waveform.
Capacitor filters, LC filters, choke input filters, and π type filters are the commonly used filters for this purpose.
In a capacitor filter, the capacitor charges as the instantaneous DC voltage increases until it peaks. When the voltage value reduces, the capacitor then discharges gradually through the regulator.
The final step involves maintaining the output DC voltage to a constant value using a regulator.
With the help of a regulator, fluctuations in output DC voltage brought by changes in input from AC mainline, load current (at the output of the RPS), or other variable factors like temperature will be eliminated.
The following regulators can be used in this step:
Regulated power supplies and unregulated power supplies are the major classifications of DC power supplies. Regulated power supplies are subdivided into two types: linearly regulated and switch mode. Switch-mode power supplies can be primary or secondary switch mode.
The list below describes each DC power supply type and design.
An unregulated power supply uses the AC mainline as the input. The AC voltage passes through a step-down transformer first. The lower secondary voltage is then rectified and converted into the corresponding DC quantity. The output voltage of the rectifier is then smoothed by a capacitor. As the name suggests, unregulated power supplies do not have a regulator as part of the circuit. In effect, any changes in the mainline will directly affect the output.
Unregulated power supplies have a simple design, making them durable with a typical efficiency of around 80%.
The primary use of unregulated power supplies is electromechanical applications, which do not need definite output voltages, e.g. for the supply of contactors.
Linearly regulated power supplies employ the AC-DC conversion process discussed in Chapter 3.
The AC mains voltage is stepped down to a lower level using a transformer, and it is rectified and filtered. The final step involves regulation of the smoothed DC voltage, commonly using a power transistor, to maintain the output at a constant value.
For linearly regulated power supplies, the power transistor acts as a variable transistor.
As it passes through the power transistor, there will be high losses in energy; this energy is emitted as heat. The power supply is therefore required to be properly ventilated.
Due to these losses, linearly regulated power supplies normally have an efficiency of about 50%.
Highly precise medical devices require very exact output voltage. For this application, linearly regulated power supplies are often utilized.
Primary switch mode power supplies employ rectification of the AC main line, filtering, and chopping/switching in the first few steps.
When a DC voltage is chopped, it only means that it is periodically switched at a frequency of 40-200 kHz with the use of a power transistor.
While power transistors act as variable transistors in linearly regulated power supplies, these are used as switches instead in primary switch mode power supplies.
A square-wave AC voltage is generated in the chopping/switching step, which is then used as input for the high-frequency transformer in the secondary circuit. The voltage is then rectified and smoothed again.
Depending on the load, the chopping rate can be varied to control the quantity of energy transformed to the secondary circuit.
Due to the use of high-frequency AC voltage, primary switch mode power supplies can use transformers which are typically smaller than required for low-frequency transformation.
Primary switch mode power supplies can use a wide range of input voltage. A DC voltage can also be used as an input. This is because the input voltage does not directly affect the output voltage.
A short-time buffer is also possible up to 200 ms, which is essential if the mains voltage breaks down.
It should be noted, however, that the power buffering failure time is restricted by the capacitor size.
A larger capacitor size can provide higher capacity and longer buffering time, but this is not desirable in small power supplies. Hence, the power supply should be optimized to have the "just right" buffering time and capacitor size.
Primary switch mode power supplies are widely used in electronics and electromechanical applications.
Secondary switch mode power supplies are quite similar to primary switch mode power supplies, but the chopping is completed on the secondary side.
In effect, a larger transformer is required to transform the 50/60 Hz mains voltage.
Mains pollution, however, is reduced because the transformer can also act as a filter.
In industrial applications, the primary switch mode power supply is the most widely used type because of its input voltage range, high efficiency, and small size.
DC/DC power supplies are part of many products since electronic devices use DC power, including portable electronics, such as laptop computers and mobile phones, which are sourced with energy from batteries. Such devices have several small circuits with each having its own requirements for levels of voltage that differ from the one supplied by the battery or an exterior supply, which is often lower or higher than that of the supply voltage. Some larger DC/DC power supplies are used to optimize the power yield from photovoltaic systems and to charge batteries. Most DC/DC power supplies regulate the voltage output, such as LED power supplies.
Efficiency, regulation time, weight and size, residual ripple, costs, and fields of application are the most important factors to be considered when selecting a power supply for new engineering applications and the upgrading of existing installations.
A DC-DC converter is a type of DC power supply that uses DC voltage as an input. The main function of DC-DC converters is to generate regulated output voltage for electric and electronic applications. Unlike AC, DC cannot be changed from one voltage level to another (step up or step down) using a transformer. Instead, a DC-DC converter is used for this purpose and can be considered an equivalent of a transformer.
Like transformers, DC-DC converters convert the input energy into a different impedance level. No energy is generated inside the converter since all the output power comes from the input power. In real applications, energy losses occur inside the converter and are consumed by components in the circuit. Due to advances in components and circuit techniques, DC-DC converters can have an efficiency as high as 90%.
DC/DC power supplies are found in non-isolated or isolated configurations. The structure of isolated converters has the output and input circuits isolated galvanically without a path for DC current between the output and input. Isolated converters are used to separate the output and input circuitry for dangerous voltage isolation or electrical noise. Isolated converters provide several output voltages from one converter.
Non-isolated converters feature DC connection between output and input via common ground between output and input circuits. This type of converter can be made smaller and less expensive than isolated converters. Non-isolated converters can produce a negative voltage output from a positive voltage input.
A type of DC-DC converter that is used for stepping up or down the voltage by a small ratio (< 4:1).
Non-isolating converters do not use dielectric isolation between the input and output.
Some of the examples include 24V/12V voltage reducers, 5V/3V reducers, and 1.5V/5V step-up converters.
DC-DC converters are useful in the following applications:
DC power supplies have four basic outputs or modes, including constant voltage, constant current, voltage limit, and current limit. Power supplies can be designed as various combinations of these outputs to fit various applications.
The circuit consists of a control element in series with a rectifier and load device. Linear power supplies have this type of regulation. The main advantages of series regulation are:
A pre-regulator added to a series regulator allows circuit techniques to be applied for medium and high-power design applications. The pre-regulation also increases the efficiency by 10-20% by minimizing power dissipation in the series regulating components. The main advantages of series regulation with pre-regulation are:
Switching regulation in a basic switching supply is composed of a series of connected transistors that serve as opened and closed switches. The main advantages of switching regulation are:
This type of regulating technique is used in high power applications. The main advantages of SCR are:
Like the constant voltage power supply, but it has less precise regulation characteristics.
Like the constant current power supply, but it has less precise regulation characteristics.
There are numerous types of DC/DC converters on the market, including buck, boost, non-inverting buck-boost and flyback converters. Buck converters provide a lower output voltage than the input voltage, while boost converters are used to provide an output voltage higher than the input. Buck-boost converters provide an output voltage that is above or below that of the input, a feature that is useful in battery powered applications where a long battery run time is of utmost importance.
Flyback converters are used for lower power below 100 W. They operate on the principle of storing energy in the magnetic component of a power supply when the power switch is ON and delivering it to the output when the power switch is off. Flyback converters offer isolation between the input and output voltage, which make them useful for polarity inversion and reducing system noise.
These four types of converters are the predominant ones. The decision of which one to use depends on the necessary size, performance, cost, and application requirements.
The development of integrated circuits with advanced features and functions makes it possible to operate power supplies at higher switching frequencies. This allows designers to decrease the size of magnetic components like transformers and output filter inductors in switching power supplies.
Higher switching frequencies rapidly replenish the output of a capacitor’s charge enabling designers to use smaller and fewer output capacitors while achieving fast and accurate dynamic output performance. The commercialization of wide band gap power semiconductors, such as silicon carbide (SiC) and GaN transistors, enables higher switching frequencies, with lower switching losses, making it possible for power supply designers to achieve higher power densities than possible with Silicon MOSFETs.
A power supply consists of a switching system that breaks a constant source of power into controllable increments of energy. It is followed by a filtering system to reconstitute the increments back into a steady source of usable output power. In its simplest form, a non-isolated power supply consists of a switching transistor, a diode, an inductor, and an output capacitor. Multiple topologies can be implemented using these four circuit elements and the appropriate control circuitry to achieve the desired output voltage and efficiency.
In most applications, power is distributed at higher voltage levels to achieve required system efficiency levels. The task of the power converter is to step down the incoming voltage to a lower value that is required by the load. These types of power converters, that provide an output voltage lower than the input voltage, are called buck converters.
When the switch SW is closed or ON, the energy is transmitted from Vin to the load. By controlling the ON and OFF times, the energy transferred or transmitted to the output can vary. The ratio of the ON time (switch on time + switch off time) is the duty cycle of a power converter, which is a number between 0 and 1. The output voltage of a power converter can be changed from 0 V to almost Vin by controlling the SW ON-time.
In the case of a buck converter, the inductor is connected directly to the output capacitor and load. The inductor current flows continuously through the diode to the output even when the switch is open through the antiparallel connected diode. When used as a regulated output converter, the duty cycle is regulated or controlled by the power supply controller to maintain the desired constant output voltage regardless of the changes in Vin or system parameters. Non-isolated buck converters can achieve high efficiencies of up to 98%.
Boost converters use the same circuit elements but arranged in a different format to provide different performance characteristics. Boost converters increase the input voltage, providing an output voltage greater than the input voltage. In the boost converter, the power is transmitted to the output in a two-step process with the inductor acting as a temporary or interim storage element. When the Switch SW is closed, the current flows into the inductor. The longer the switch is ON, the higher the magnetic energy that is stored.
The diode blocks current from flowing back from the load with the output voltage being held up by the output capacitor. When the switch is opened, the energy stored in the magnetic field of the inductor flows through the diode, recharges the capacitor, and replenishes the energy delivered by the capacitor to the load when the switch SW is ON. This two-step process results in high peak currents in components and impacts efficiency in higher power applications, which limits it to lower power applications.
Buck-boost converters are hybrid integrations of buck and boost power converters. They combine buck circuits on the input and boost ones on the output side with a shared inductor between them. The advantage of this topology is its ability to regulate the output voltage whether the input voltage is above or below the desired output voltage. The output remains steady as the battery moves from a fully charged state to a fully discharged state.
These types of power converters are very popular in battery powered applications where the output load voltage must be maintained even when the battery is discharged to its lowest operating limit. The benefit of this approach for battery powered end products is they can have an extended run time and maintain the same performance through the discharge of the battery.
When Vin is higher than Vout, (about 14.5V when a fully charged battery is connected in a 12V load system), the circuit operates in buck mode with the boost switch SW2 remaining open and the output Diode-2 continuously conducting. When the input falls below the set Vout level, while the battery is being discharged, the input switch SW1 will remain ON and the circuit will behave like a boost converter with SW2 operational to maintain the output voltage. A single control circuit performs the output voltage control and determines whether the buck or boost operating mode is required.
A synchronous rectifier performs like a diode, allowing current to pass in one direction. When using regular power diodes as freewheeling diodes or rectifying diodes, the conduction losses on these diodes can be unbearably high, especially at high currents where VF is close to 0.6 to 0.7 volts.
To lower the losses, power MOSFETs are used in place of rectifier diodes and freewheeling diodes. The power losses are significantly improved compared to standard diodes or even Schottky diodes. Driving the power MOSFETs, synchronously with the main power switches can be a complex step requiring special controllers. The benefits, however, outweigh the complexity and cost and is an approach that has been adopted in all types of switching power supplies.
Battery eliminators are inexpensive DC power supplies with a compact design. They function as a battery whenever a battery is not available. Battery eliminators are typically used on battery-operated equipment. They can provide 18V DC power to devices that are normally powered by automobile batteries and can be used in CB radios and automotive stereo systems.
The various types of battery eliminators come with an ON/OFF switch and rotary switch that is turned to select the target output DC voltage. Units come with outputs of 1.5V to 6V 9V, and 12V with increments of 1.5V. They can be operated continuously and safely in a dead short.
A constant voltage supply provides a constant and adjustable voltage with a design that is more complex than battery eliminators. They come with a voltage and current meters, which allows the monitoring of voltage and current supply values. Voltage is maintained as a DC power supply. Output voltage is adjusted using a knob. With some units unable to be adjusted down to zero volts.
Some models do not supply the rated current at any output voltage. In these instances, the maximum output current is proportional to the output voltage. Tie points can be available, with a current limit, to provide connections to an external digital meter (for accurate monitoring of output voltage) or other circuits.
A constant voltage/constant current supply allows a constant supply of voltage and current. Regardless of the load’s resistance, the current is maintained in a constant current mode. Typical units include fine and coarse adjustable controls for the voltage and current supply. Some models have 10-turn pots, thumbwheel switches, or pushbutton switches instead for adjustment controls. A meter is unnecessary when using thumbwheel and pushbutton switches.
Multiple output DC power supplies provide more than one DC output. They are a cost effective option for systems requiring multiple voltages.
For example, a triple output supply is used in circuit development:
With a multiple output supply, a knob or keypad is placed to set the three outputs independently. Turning ON and OFF the outputs can be done separately or all at once. This feature allows a whole printed circuit board to be powered up.
A typical unit also has features like:
A programmable supply, known as system power supplies, are integrated into a computer operated system during production or testing.
A multi-range DC power supply allows various combinations of voltage and current to operate and still provide maximum power. This is in contrast to common power supplies that provide maximum output power if operated at a certain fixed voltage and current ratings. The output power is less than the maximum if other voltage and current combinations are used in conventional power supplies.
The main advantages of multi-range supply include:
When selecting a DC power supply, one should consider the following specifications:
DC power supplies with constant current and constant voltage modes are versatile and, thus, can be used in most applications.
Another important specification to be considered is the power supply output. In general, the user should select a DC power supply with an output greater than the requirement since most projects require the addition of new functionalities at the later stage of the design cycle.
Regulation can mean load regulation or line regulation. Load regulation (usually 0.1% to 0.01%) is the amount of change in the output voltage when the load changes. Line regulation (usually 0.1% to 0.01%) is the amount of change in the output voltage when the input AC voltage changes.
Most parts of a DC power supply are temperature sensitive. Thus, one should consider checking the operating temperature range and temperature coefficient of the power supply. Ideally, a lab-quality power supply should have 0.05% /°C.
Three-phase power is normally used by larger power supplies. These are more efficient than single-phase power supplies but with higher ripple frequency.
Other specifications include ripple and noise, tracking accuracy, and DC isolation.
Power supplies are electrical circuits and devices that are designed to convert mains power or electricity from any electric source to specific values of voltage and current for the target device...
An AC power supply is a type of power supply used to supply alternating current (AC) power to a load. The power input may be in an AC or DC form. The power supplied from wall outlets (mains supply) and...
A DC DC power supply (also known as DC DC Converter) is a kind of DC power supply that uses DC voltage as input instead of AC/DC power supplies that rely on AC mains supply voltage as an input...
By definition a power supply is a device that is designed to supply electric power to an electrical load. An electrical load refers to an electrical device that uses up electric power. Such a device can be anything from...
A programmable power supply is a method for controlling output voltage using an analog or digitally controlled signal using a keypad or rotary switch from the front panel of the power supply...
An AC power cord is a detachable way of providing an alternating current of electric energy from a mains power supply to an electrical appliance or equipment. Serving industries like...
Electrical plugs, commonly known as power plugs, are devices responsible for supplying and drawing current from a receptacle to the circuitry of an electrical appliance...
Electronic connectors are devices that join electronic circuits. They are used in assembling, installing, and supplying power to electrical devices. Connectors are an important component of every electronic equipment used in...
An electric switch is a device – usually electromechanical – that is used to open and close an electric circuit. This disables and enables the flow of electric current, respectively...
A NEMA connector is a method for connecting electronic devices to power outlets. They can carry alternating current (AC) or direct current (DC). AC current is the typical current found in homes, offices, stores, or businesses...
A power cord is an electrical component used for connecting appliances to an electrical utility or power supply. It is made from an insulated electrical cable with one or both ends molded with connectors...
Push button switches are electrical actuators that, when pressed, either close or open the electrical circuits to which they are attached. They are capable of controlling a wide range of electronic gadgets...
Thomas Edison developed the power distribution system in 1882. He wrapped a copper rod in jute, a soft shiny fiber from plants, as an insulator. The jute wrapped copper rod was placed in a pipe with a bituminous compound...