AC DC Power Supply
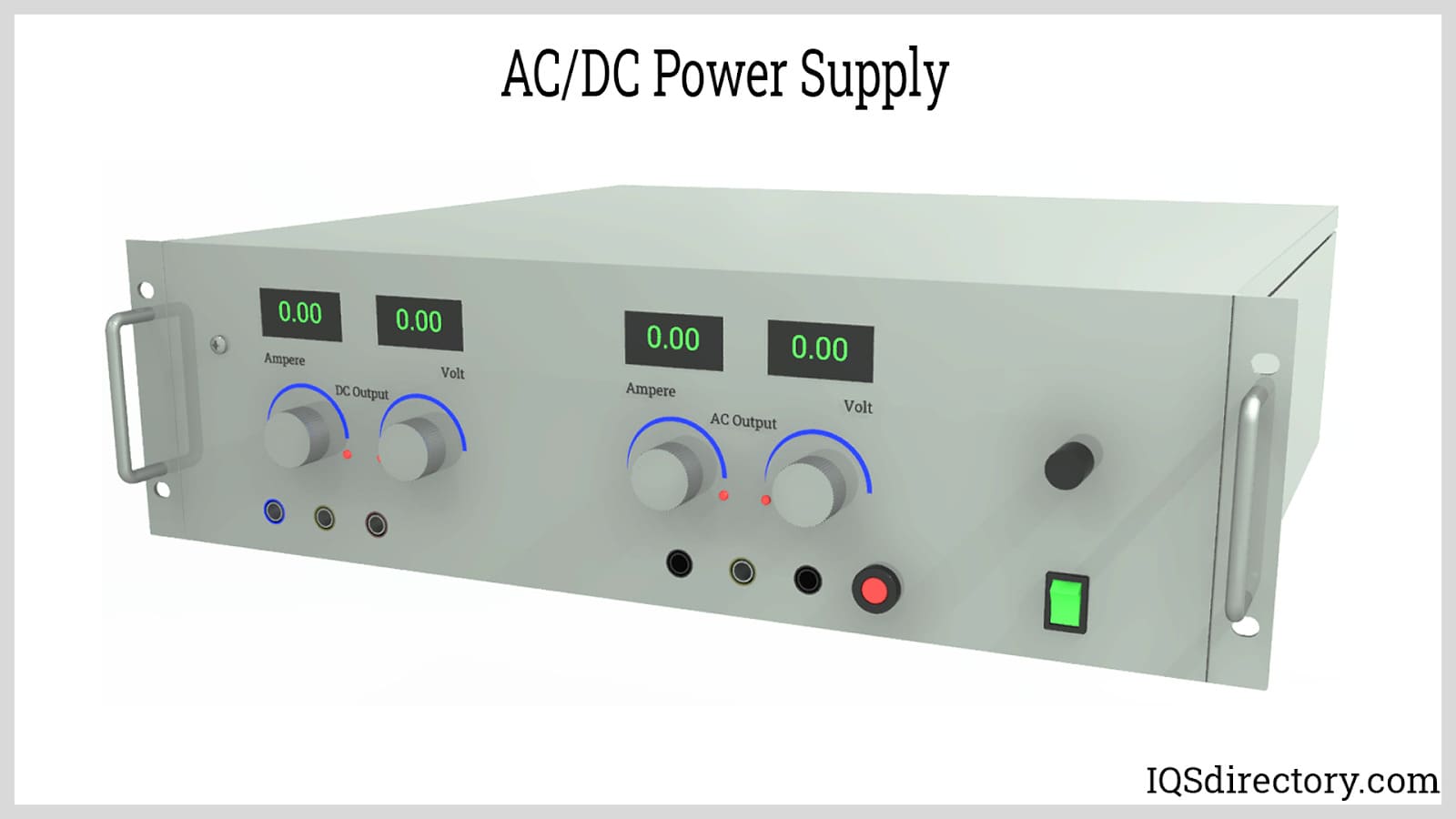
Power supplies are electrical circuits and devices that are designed to convert mains power or electricity from any electric source to specific values of voltage and current for the target device...
Please fill out the following form to submit a Request for Quote to any of the following companies listed on
This article will take an in-depth look at high voltage power supply.
The article will look at topics such as:
An electromagnetic interference (EMI) filter is an electrical component or circuit designed to eliminate unwanted frequencies from power lines or other signals that could disrupt a system. It takes an AC or main power input, processes it to remove noise, and outputs a clean signal to enhance device performance. Often known as a choke, an EMI filter reduces high-frequency electromagnetic interference in power and signal lines. These filters are categorized as low pass, high pass, bandpass, or band reject and typically include passive components like capacitors and inductors arranged in LC circuits or more complex configurations.
EMI filters utilize the characteristics of capacitive and inductive materials to eliminate high-frequency noise from a signal. They work by absorbing or reflecting the noise mixed with the true signal, resulting in a cleaner output.
Inadequate protection against EMI can impair the performance of electrical equipment by inducing unwanted currents and voltages in the circuitry. EMI can be either conducted or radiated. Conducted EMI travels along a physical path from the source to the receiver.
Radiated EMI, on the other hand, does not require physical contact and propagates through the air. This type of interference occurs when a device emits electromagnetic energy in the form of an electric field, potentially causing damage by overwhelming the equipment's circuitry. The emissions can spread over long distances and disrupt device operation.
While external EMI can harm equipment, internal EMI can create interference within a system. This happens when sensitive components are placed near high-voltage or high-current power management circuitry, leading to electromagnetic interference between the circuits.
EMI filters come in a variety of sizes, designs, shapes, and configurations, all designed to shield sensitive equipment from electrical noise. They are generally categorized into two main types: active and passive filters.
Active EMI filters use an internal power supply to generate a counteracting current that cancels out disturbances. These filters detect the input voltage and produce a current flow in the opposite direction to neutralize any interference. They employ active electronic components and internal circuitry to filter out unwanted frequencies.
In contrast, passive EMI filters work by absorbing unwanted energy rather than generating a counteracting current. They utilize passive components such as capacitors, resistors, transformers, and inductors, which are tuned to create electrical resonance at specific frequencies or frequency bands. These filters help to suppress harmonic currents and reduce voltage distortion within electronic systems.
The widespread use of EMI filters is attributed to their effectiveness in protecting sensitive electronics from damage caused by radiation from electronic devices. They eliminate disruptive currents from signal and power lines while allowing acceptable currents to pass through.
Single-phase EMI filters are designed for use in common and differential mode applications. These filters are general-purpose devices intended to reduce noise in power lines. A single-phase EMI filter restricts the amplitude of interfering voltages on AC power lines, preventing their propagation.
For more robust noise suppression, three-phase EMI filters are designed to handle higher levels of interference through a three-phase filtering system. They operate within a frequency range of 47 Hz to 400 Hz and are typically used with frequency converters, motor drives, and machine tools. Three-phase EMI filters are available in two types: Wye and Delta.
A widely used passive EMI filter is the ferrite choke, which functions as an inductor with capacitance for low-pass filtering. Ferrite chokes, also known as ferrite clamps, ferrite collars, EMI filter beads, or ferrite ring filters, help to attenuate high-frequency signals and are commonly installed around the power lines of devices like laptops.
Ferrite is a magnetic substance that, when wrapped around a power supply, provides inductive resistance to the signals passing through it. This type of EMI filter exhibits nonlinear characteristics, with its resistance varying based on changes in load current and voltage drop. Additionally, the performance of ferrite chokes can be influenced by fluctuations in current and temperature.
Installing a ferrite choke involves placing it around the wire connected to the equipment. The choice of ferrite choke size and type depends on the wire's diameter, ranging from 3 mm for headphone cables to 13 mm for 12-gauge or 120-volt power cords. For best results, the ferrite choke should be positioned approximately 5 cm from the device connection, as it performs more effectively when placed close to the device.
Position the ferrite choke about 5 cm from the device connection, as it performs more effectively when closer to the device.
Differential mode passive EMI filters are designed to diminish high-frequency AC currents in circuits that carry low-frequency AC or DC currents. These filters can be used individually or combined in groups with multiple inductors placed at various points. Differential mode refers to the signals or noise that travel in opposite directions through a pair of lines.
A differential mode passive EMI filter mitigates noise in a device by employing a component with wires wound around a magnetic core. This magnetic component counteracts rapid changes in current, creating a choking effect on differential mode noise. This reduces the amplitude of the frequency, minimizing its impact on circuit operation.
Differential mode EMI filters come in various types to meet different application needs. They vary based on coil winding, materials, and magnetic core types. These filters are commonly used in power supplies and converters, solar inverters, wind power systems, automotive electronics, and telecommunications.
A common mode passive EMI filter is designed to block high-frequency noise that affects power lines. This noise can originate from sources such as radio signals, unshielded electronics, inverters, and motors. In common mode, current flows in the same direction through both lines. The magnetic flux within the EMI filter generates an opposing field that attenuates and removes the noise.
When common noise encounters a common mode EMI filter, magnetic flux is generated in both windings of the core. The core is designed to produce a rotating magnetic field, functioning like an inductor with resistance that corresponds to the frequency of the noise. This setup allows low-frequency signals to pass through while impeding high-frequency noise.
Common mode EMI filters are classified by the frequency range of an application, which are radio frequency (RF) filters and audio frequency (AF) filters. Common mode AF filters are designed to suppress noise in the audio frequency range up to 30 KHz that include switch mode power supplies, AC/DC rectifiers, electrical ballast, power inverters, and variable frequency drives. With common mode RF filters, noise frequencies are higher above 30 KHz, such as USB, HDMI, LVDS, CAN bus, and ethernet applications.
The distinction between AF and RF common mode EMI filters lies in their core materials. AF filters use solid iron cores, whereas RF filters are constructed with powdered ferromagnetic core materials.
Line chokes are integrated into the variable frequency drive (VFD) input or output circuits to create a magnetic field that limits current by generating a voltage opposing the current flow. They offer protection against spikes, transients, and harmonics and can be installed either on the input side or the output side of the VFD. When installed on the input side, they are known as line reactors, while those on the output side are referred to as load reactors.
Line chokes are used in VFDs with ratings of 1 KVA and are effective for managing sinusoidal and harmonic current flows, especially where significant harmonic distortions are present. By introducing a voltage with opposite polarity to the applied voltage, line chokes reduce the rate of current change and limit the applied current.
Three-phase line chokes are connected to the mains supply leading to the inverter, helping to mitigate harmonics generated during the rectification of the mains for a DC link. They are essential for minimizing extra current drawn by an inverter or other devices and address issues arising from problems in the mains supply.
When there is a considerable distance, over 100 feet, between the motor and the VFD, a load reactor is utilized to prevent voltage spikes from being amplified due to the long distance. In this context, a line choke helps to reduce current to a safe level, protecting the VFD's thyristors from overheating and damage. This setup is beneficial when multiple drives are connected or when there is a power supply imbalance.
Line chokes are placed in series on AC power lines and are designed to improve power quality as well as reducing EMI effects. They are used in motor control systems and power lines.
RF chokes are fixed inductors designed to block high-frequency AC signals from radio frequency devices while permitting low-frequency DC signals to pass through. They effectively reject all frequencies except for DC signals. RF chokes have high impedance across a broad frequency range to attenuate unwanted frequencies. Higher frequencies encounter significant resistance, preventing their passage.
An RF choke typically consists of a coil of insulated wire wound around a magnetic core or a ferrite bead attached to a wire. The winding patterns are engineered to minimize self-capacitance and enhance performance.
RF chokes are employed in radio frequency circuits, such as those in antennas and transmitters, to prevent RF signals from disrupting circuit functionality. Their high inductance and low resistance make them well-suited for blocking RF signals while allowing lower frequency signals to pass.
Similar to RF chokes, power chokes are used to filter out noise and ensure a stable power supply. They are specifically designed to eliminate AC ripple from DC outputs, thereby providing a stable DC voltage. Power chokes are typically positioned between the mains supply and the inverter to smooth out current fluctuations. They feature high inductance and low resistance, which allows them to filter out noise effectively while permitting DC signals to pass through.
Active EMI filters utilize operational amplifiers (op-amps) and sophisticated circuitry to address both common mode and differential mode noise. These filters offer a compact and efficient solution for eliminating EMI, using components with a small footprint. The design incorporates an op-amp along with capacitors and resistors to create a streamlined circuit. Active EMI filters help reduce both the size and cost of EMI filtering while maintaining high performance.
Active EMI filters operate by detecting high-frequency noise at the supply input and generating counteracting noise currents that are fed back into the power supply. They provide 15 dB to 30 dB of common mode noise rejection for frequencies ranging from 100 kHz to 3 MHz by creating a low-resistance path for common mode noise.
While passive EMI filters are relatively bulky and account for about 30% of the volume and weight of converters, active EMI filters are more compact and provide high-quality performance. An active EMI filter is composed of a noise sensing circuit, a resonant controller, and a noise injection circuit. They offer a simpler structure, a broad operating frequency range, excellent stability, and a reduction in the size, weight, and cost of common mode chokes. This design aligns with the advancements in next-generation power electronics, focusing on higher density, enhanced performance, and reduced weight.
Amorphous core EMI filters use cores made from amorphous metal and provide significant benefits, including high permeability and minimal core loss at elevated frequencies. These filters are effective across a wide frequency range, making them adaptable for various uses. Their high permeability and low loss characteristics enable a compact design, which is both smaller and lighter than other types, without sacrificing performance.
Amorphous metal cores are crafted from a non-crystalline alloy, usually comprising iron, silicon, and boron. This distinctive structure endows them with magnetic properties that make amorphous metal cores particularly efficient at mitigating EMI, especially in the presence of high voltage spikes.
Amorphous core EMI filters are applied in a range of scenarios, including power supplies, motor drives, telecommunications systems, and audio/video equipment. They effectively reduce both conducted and radiated EMI, ensuring that sensitive electronic devices operate correctly and preventing interference with adjacent equipment.
Amorphous core EMI filters come in different types, including common mode and differential mode configurations. Common mode filters target noise that affects both the line and neutral conductors, while differential mode filters focus on noise that occurs between the line and neutral conductors.
Electromagnetic interference occurs when unwanted electrical currents interfere with the intended signals of an electronic device. This interference, often referred to as noise or electromagnetic noise, can originate from external sources or be generated by components within the device itself. EMI can disrupt the normal operation of the device, leading to unintended behaviors, signal quality issues, component failure, temporary glitches, or even permanent damage.
Both conducted and radiated types of EMI can severely affect a device and its performance. The effects may range from reduced functionality and performance degradation to complete system failure. This highlights the crucial importance of EMI filters in maintaining the reliability and efficiency of electronic systems.
Natural sources of EMI are unpredictable and can occur suddenly, often causing significant and enduring damage to unprotected devices. In critical scenarios, natural EMI can affect military equipment, electronic tracking systems, and transportation technologies, which are particularly vulnerable given society's heavy reliance on electronic devices.
Types of natural EMI
Sunlight can interfere with satellite transmissions when it aligns directly behind a satellite, creating electromagnetic noise that disrupts communication signals. Snowstorms can also affect cell phone service, generate radio static, or cause interference with laptops and computers.
Residential EMI primarily arises from wireless signals and various electronic appliances. While it typically doesn’t cause severe damage, it can lead to annoying disruptions in service and negatively affect the performance of electronic devices.
As society increasingly relies on electronic devices and innovations, the number of EMI sources has risen. The proliferation of electronic gadgets has resulted in a higher density of electromagnetic currents. Devices like cell phones, laptops, and tablets are often used close together, increasing the likelihood of EMI impacts.
Modern electronics, with their enhanced performance, tend to generate more electromagnetic interference. The pursuit of higher performance leads devices to operate at elevated frequencies, producing electromagnetic noise over a wider frequency spectrum. This has driven EMI filter manufacturers to develop solutions that address contemporary needs and safeguard crucial devices.
Various types of Human Residential EMI
Due to the nature of industrial equipment, they are capable of causing large scale EMI and severe interference in essential technologies. The list of industrial sources of EMI is endless and can cause widespread impact such as disruption of hospitals, military operations, and power grids. Examples of high-frequency sources of EMI include transmitters, transformers, inverters, microprocessors, and controls.
Categories of EMI in Human Industry
In addition to natural and man-made sources of EMI, internal noise sources within a system also play a role. For instance, digital circuits in smartphones can interfere with signal reception and transmission. Complex circuitry with sensitive components placed near high-voltage power management can lead to electromagnetic interference between components. Designers must consider component density and its impact on EMI to ensure proper functioning of sensitive circuits.
Modern electronics often use switch mode power supplies to achieve high efficiency. However, the on-and-off switching of field effect transistors in these supplies generates EMI. This interference can be mitigated using differential mode (DM) EMI filters.
Before choosing an EMI filter, it's crucial to assess the specific requirements of the electrical system. Different EMI filters have varying limits, frequency ranges, and suppression methods. Review filter data sheets that include insertion loss data and tables, which indicate the loss in signal power between the filter’s input and output and the attenuation provided at specific frequencies, measured in decibels.
Conducted noise, whether common or differential, depends on its location and propagation method. During data collection, charts for both common and differential noise are available. Analyzing this data helps determine the failure margin for each frequency, assessing whether the filter provides enough attenuation to bring noise levels below acceptable limits. Similar tests should be conducted for radiated noise as well.
After gathering data, it's important to review the system's requirements and specifications, including voltage, current, operating and ambient temperatures, dielectric withstand voltage, leakage current, and feed system type. Evaluating these specifications ensures that the filter can handle the system's needs without compromising performance or reliability.
Single-phase EMI filters are typically rated for 250 VAC and are compatible with any AC voltage below this threshold. For three-phase systems, filters are generally rated for 480 VAC. Some single-phase filters are available with ratings up to 277 VAC or 300 VAC for higher voltage applications.
Current ratings for EMI filters can range from less than 1 amp to over 1000 amps. This rating indicates the maximum continuous current the filter can handle within its specified temperature range. It should match or exceed the maximum input current of the device. While most filters can tolerate higher inrush currents, they may fail if the rated current is exceeded for prolonged periods.
To determine the current rating of a device, examining its safety certificate, such as the UL report, can be useful. The report provides details on the full load nominal input and the recommended filter rating. Additional power supplies and AC loads may require filters with different ratings.
There are two temperature considerations: ambient and operating. Ambient temperature refers to the maximum temperature at which a filter can handle its full rated current, typically between 40°C and 50°C. If the operating temperature exceeds the ambient temperature rating of the filter, the current rating must be derated.
The operating temperature is the range within which the filter can function safely, usually between -25°C and 85°C or 100°C for most filters. Using a filter outside this range can lead to component damage.
Leakage current is the current that flows from the line and neutral to ground when line voltage is applied to the filter. This is caused by the line-to-ground capacitor within the filter. EMI filters with Y capacitors can add additional leakage current. Regulatory standards limit leakage current and must be adhered to strictly for safety.
Power systems differ globally and include configurations beyond single phase, 3 phase delta, and 3 phase wye. EMI filters are designed for these configurations and DC circuits but can be adapted for other systems with minimal adjustments. It is essential to identify and match the input power supply type with the selected filter.
The term "stages" refers to the number of circuit repetitions within a filter. A single-stage filter has one circuit, while dual-stage and multi-stage filters include additional circuits. Increasing the number of stages generally enhances filter performance.
The hipot test evaluates the dielectric strength of the insulation by applying a DC voltage between the line and ground. This test helps identify weak points in insulation or manufacturing defects. The voltage used is the rated value specified by safety standards, though higher requirements may necessitate adjustments to the filter.
EMI filters come in various sizes, performance levels, interconnections, and mounting types. In some cases, custom-designed filters may be required to meet specific application needs.
The type of equipment and its components are critical in selecting an appropriate EMI filter. Whether for AC/DC converters, manufacturing equipment, medical devices, RF modules, or other equipment, the filter must align with the application's nature. Factors such as clock frequencies and switching frequencies influence the emission profile of an EMI filter.
In power systems, cables and wiring can act as antennas for high-frequency noise, particularly when using open-frame power supplies without the shielding found in enclosed types. The design of power supplies often poses significant challenges in eliminating and mitigating radiated and high-frequency conducted emissions. To effectively address high-frequency noise, it is crucial to install an EMI filter, as it helps prevent the coupling of noise back through the radiated mode.
Following these EMI filter installation recommendations can help ensure optimal filter performance:
EMI sources often require a multifaceted approach for effective mitigation. During the installation process, it is beneficial to have a variety of EMI filters available. This approach enhances the efficiency of installation and reduces overall filter costs. Manufacturers and suppliers of EMI filters typically offer support services to aid in the selection, design, and installation of filters, as well as to provide guidance on cable routing and noise suppression techniques.
Key components of an EMI filter include capacitors and inductors. Capacitors are used to shunt noise away from the load, while inductors block or reduce noise. Additionally, EMI filters may include circuit protection components such as a fuse, metal oxide varistor, input surge current limiting resistor, and output transient voltage suppressor.
The fuse safeguards the power source and the conductors feeding into the power supply by being placed in series with the input. It is installed on the non-ground input terminal, ensuring that when the fuse opens, no voltage reaches the power supply. Fuses are chosen based on the application's voltage, current, response time, and operating temperature requirements.
The term "varistor" is derived from combining "variable" and "resistor," reflecting its function. A varistor offers over-voltage protection through voltage clamping. It adjusts its resistance automatically as the voltage fluctuates and is designed to absorb transient energy. An input fuse is installed between the varistor and the input power source.
The input surge current limiting resistor helps manage the initial surge of current when AC voltage is introduced to the power supply. This is essential to handle the quick charging of the capacitor that occurs at the moment the input voltage is applied.
Rapid changes in the load can cause the output voltage to fluctuate, resulting in what is known as a transient response. The Transient Voltage Suppressor (TVS) diverts these voltage spikes caused by external sources at the output terminal to safeguard the power supply. While a varistor can serve as a TVS, it is typically not used on the output side due to the lower output voltage in comparison to the input side.
The Differential Mode (DM) choke, combined with the input capacitor, acts as a low pass LC filter to minimize the conducted noise voltage on the input conductors, preventing it from affecting the power source. It is engineered to handle the peak input current effectively.
The Common Mode (CM) choke generates significant resistance to diminish common mode currents traveling through the input conductors. The markings on the CM choke denote the winding direction and orientation. These chokes are selected based on their capability to manage maximum current and ensure adequate power dissipation.
The input capacitor is positioned across the input power lines to divert differential noise and prevent it from reaching the voltage source. These capacitors are constructed to X or Y safety standards, allowing them to be directly connected to the AC input line and endure surge conditions.
The Y capacitor is positioned between the input and output to mitigate mode voltage noise on the output power supply. It is engineered to fail safely as an open circuit if there is a breakdown between the input and output. This Y safety isolation capacitor is essential due to the waveform generated by the primary switching transistor and the parasitic capacitance between the primary and secondary sides of the isolation transformer.
Filtering components are positioned at the power supply's output terminal and close to the load. These components are chosen based on their effectiveness in minimizing output ripple voltage to a level that is acceptable for the load.
EMI filters are available in various configurations, such as panel mounts with resin or glass encapsulation, surface mounts compatible with PCB layouts, board mounts, d-subminiature connectors, and both single-phase and three-phase power line filters. Essentially, there's an EMI filter suited for virtually every type of electronic, power, signal, and AC/DC application. Their role is crucial in maintaining the high performance and reliability of electronic devices.
EMI filters are primarily used to safeguard electronic devices. They prevent sensitive equipment from being affected by both conducted and radiated noise, which can lead to damage and operational issues. It's essential for all electronic devices to be equipped with an EMI filter to ensure their proper functioning.
Ensuring the safety of electronic equipment involves adhering to a comprehensive set of codes, regulations, and standards. These regulations are particularly relevant in industrial settings where EMI filters are used, as they can generate significant EMI and RFI. Manufacturers of EMI filters are knowledgeable about these requirements and ensure their products meet all necessary standards. Non-compliance with EMI regulations can result in fines, penalties, and even shutdowns in various countries.
While residential electronics might not experience this issue as frequently, high-frequency interference can lead to system shutdowns in industrial and manufacturing environments. EMI filters play a crucial role in maintaining the uninterrupted operation of electronic systems by preventing interference, errors, and malfunctions. Their effectiveness in minimizing issues also helps lower maintenance and repair expenses, positively impacting overall costs.
EMI filters contribute to long-term cost savings, enhance system reliability, and ensure operational continuity, aligning with both national and international standards. As electronic circuit complexity grows, so does the potential for electromagnetic disturbances, increasing the risk of operational errors. EMI filters are essential for mitigating these risks and ensuring stable, error-free performance.
An EMC plan provides a comprehensive overview of a new product, including its testing procedures. It includes detailed information about the product, the specific EMC tests conducted, and the outcomes of those tests. This plan ensures a structured approach to testing and serves as a documented record, helping laboratories deliver precise and coherent data. As sensitive electronics become more prevalent, EMI filters play a key role in managing electrical input currents, which can be monitored and used to safeguard the tested items.
Power supplies are electrical circuits and devices that are designed to convert mains power or electricity from any electric source to specific values of voltage and current for the target device...
An AC power supply is a type of power supply used to supply alternating current (AC) power to a load. The power input may be in an AC or DC form. The power supplied from wall outlets (mains supply) and...
A DC DC power supply (also known as DC DC Converter) is a kind of DC power supply that uses DC voltage as input instead of AC/DC power supplies that rely on AC mains supply voltage as an input...
A DC power supply is a type of power supply that gives direct current (DC) voltage to power a device. Because DC power supply is commonly used on an engineer‘s or technician‘s bench for a ton of power tests...
A programmable power supply is a method for controlling output voltage using an analog or digitally controlled signal using a keypad or rotary switch from the front panel of the power supply...
An AC power cord is a detachable way of providing an alternating current of electric energy from a mains power supply to an electrical appliance or equipment. Serving industries like...
Electrical plugs, commonly known as power plugs, are devices responsible for supplying and drawing current from a receptacle to the circuitry of an electrical appliance...
Electronic connectors are devices that join electronic circuits. They are used in assembling, installing, and supplying power to electrical devices. Connectors are an important component of every electronic equipment used in...
An electric switch is a device – usually electromechanical – that is used to open and close an electric circuit. This disables and enables the flow of electric current, respectively...
A NEMA connector is a method for connecting electronic devices to power outlets. They can carry alternating current (AC) or direct current (DC). AC current is the typical current found in homes, offices, stores, or businesses...
A power cord is an electrical component used for connecting appliances to an electrical utility or power supply. It is made from an insulated electrical cable with one or both ends molded with connectors...
Push button switches are electrical actuators that, when pressed, either close or open the electrical circuits to which they are attached. They are capable of controlling a wide range of electronic gadgets...
Thomas Edison developed the power distribution system in 1882. He wrapped a copper rod in jute, a soft shiny fiber from plants, as an insulator. The jute wrapped copper rod was placed in a pipe with a bituminous compound...