Ceramic Magnets
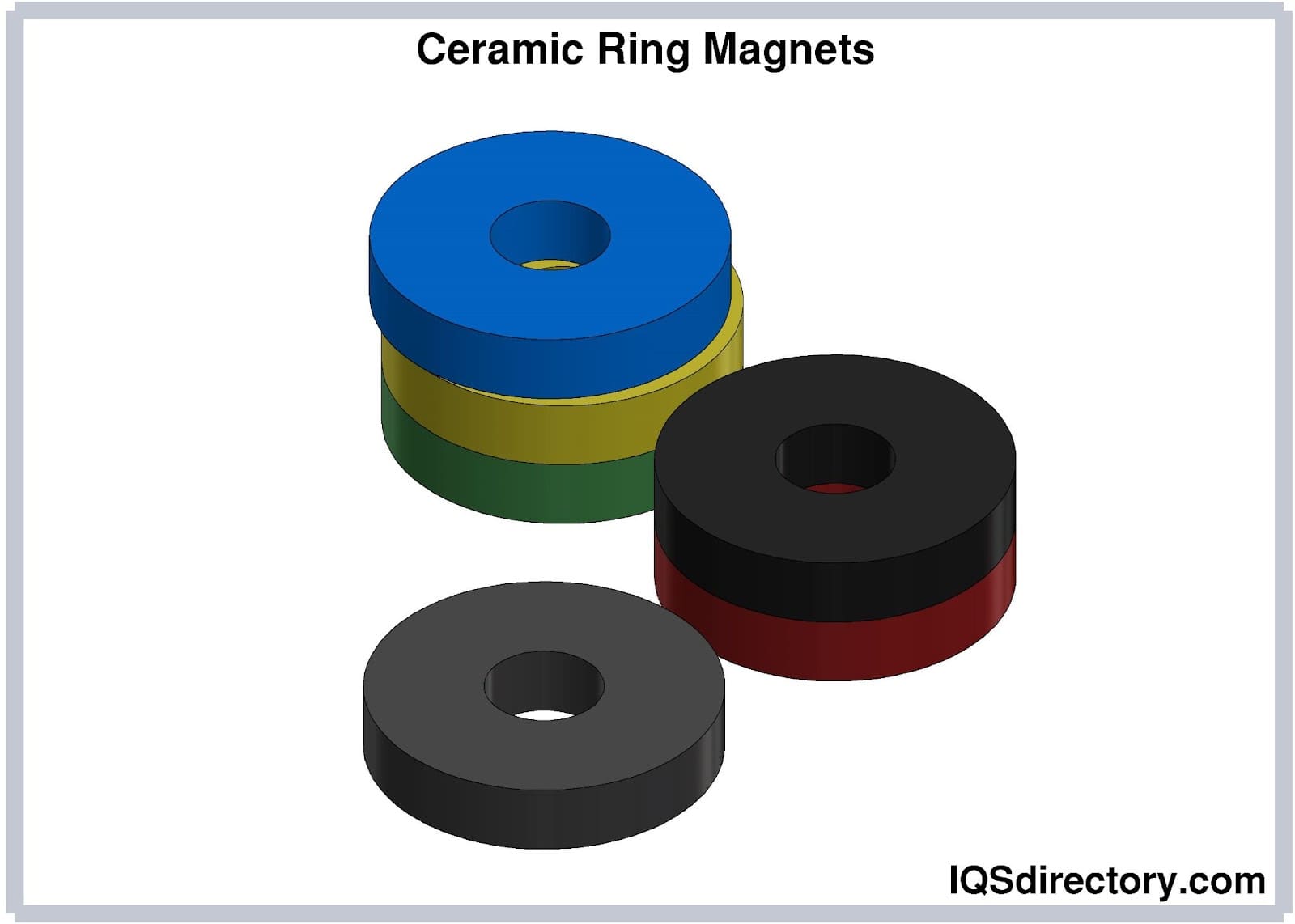
A ceramic magnet, also known as a ferrite magnet, is a permanent magnet made by combining iron oxide and strontium carbonate. They are a man made magnet produced by heating the two elements to...
Please fill out the following form to submit a Request for Quote to any of the following companies listed on
This article takes an in depth look at alnico magnets.
You will learn more about topics such as:
An Alnico magnet is a type of permanent magnet crafted from a blend of aluminum, nickel, iron, cobalt, and various other materials. These magnets can be found in isotropic, non-directional forms, or anisotropic, directional forms. After being magnetized, they possess a magnetic strength that is 5 to 17 times greater than that of magnetite or lodestone, which are naturally occurring magnetic substances known for attracting iron.
Alnico magnets feature a minimal temperature coefficient and can be adjusted to achieve high residual induction, making them suitable for high-temperature environments up to 930°F or 500°C. They are commonly employed in situations requiring corrosion resistance and are also used in different types of sensors.
Introduced in the 1930s, alnico magnets are highly valued in permanent magnet motors due to their unique magnetic characteristics and stable temperature coefficient. They preserve their magnetic field well, are resistant to demagnetization, and maintain their magnetism even at elevated temperatures. Unlike some other magnets, alnico magnets cannot be cold worked and are manufactured through processes such as sintering or casting.
Initially, naturally occurring lodestones were used by explorers to locate the magnetic north pole. It wasn't until the first industrial revolution that artificial magnets were developed, eventually leading to the creation of alnico magnets.
Alnico magnets are created through sintering or casting processes, involving a blend of aluminum, nickel, and cobalt. To boost their magnetic strength, additional elements such as iron, copper, or titanium are incorporated. The casting method involves pouring a molten alloy into a mold, typically made of resin-bonded sand. Magnets produced via casting tend to be larger and offer superior magnetic properties and performance compared to those made through sintering.
Casting allows for the customization of alnico magnets into intricate shapes and designs, which is not feasible with sintering. Regardless of whether casting or sintering is employed, alnico magnets are too brittle and rigid to be cold worked and must be manufactured using heated materials.
The grade of an alnico magnet is determined by its chemical composition. Below is a chart illustrating various grades of alnico magnets.
Dura Magnetics | ||||||||||
---|---|---|---|---|---|---|---|---|---|---|
Dura Magnet Grade | Residual Induction Br |
Coercive Force Hc |
Intrinsic Coercive Force Hci |
Maximum Energy Product (BH)max | Max Operating Temp | |||||
Nominal | Nominal | Nominal | Minimum | Nominal | Nominal | |||||
k-Gauss | Telsla | k-Oersted | KA/M | k-Oersted | KA/M | MG Oe |
KJ/m3 | °C | °F | |
Alnico 5 | 12.2 | 1.22 | 600 | 48 | 630 | 50 | 5 | 40 | 500°C | 930°F |
Alnico 5B | 12.22 | 1.22 | 650 | 52 | 660 | 53 | 5.5 | 44 | 500°C | 930°F |
Alnico 5 DG | 12.5 | 1.25 | 690 | 55 | 700 | 56 | 6.5 | 52 | 500°C | 930°F |
Alnico 5-7 | 13 | 1.3 | 700 | 56 | 740 | 59 | 7.5 | 60 | 525°C | 980°F |
Alnico 8-HC | 7 | 0.7 | 1,750 | 139 | 1,750 | 139 | 4.5 | 36 | 525°C | 980°F |
Alnico 8 | 8.2 | 0.82 | 1,500 | 119 | 1,600 | 127 | 5 | 40 | 525°C | 980°F |
Alnico 8B | 8.8 | 0.88 | 1,500 | 119 | 1,650 | 131 | 5.5 | 44 | 525°C | 930°F |
Alnico 8C | 9 | 0.9 | 1,380 | 110 | 1,440 | 115 | 7.5 | 60 | 525°C | 930°F |
Alnico 9 | 10.5 | 1.05 | 1,410 | 112 | 1,440 | 139 | 9 | 72 | 525°C | 930°F |
The production method for alnico magnets is determined by factors such as size, weight, and intended application. Large and intricate magnets, which can weigh several pounds, are typically produced through casting. In contrast, smaller magnets that are required in large volumes are generally manufactured using the sintering process.
Different grades of alnico magnets are made using various proportions of cobalt, aluminum, and nickel. For example, an alnico 6 magnet consists of 8% aluminum, 16% nickel, 24% cobalt, 3% copper, 1% titanium, and less than 1% ferrous metals. The precise amounts of these materials are melted together in an induction furnace. To ensure proper mixing and melting, the mixture is heated to 1750°C or 3182°F.
The casting process involves pouring the molten mixture into green sand molds, which have been made large enough to account for any shrinkage that may take place during cooling. For some sizes of alnico magnets, several molds are placed together and connected by gates. When the molten magnet material is poured into the mold, it travels through the gates to all of the individual molds such that several magnets are produced in a single casting.
Once the molten material is poured into the mold, it is allowed to cool. The cooling process, as well as the final surface finish of the magnets, can be influenced by factors such as the amount of sand used, its grain size, and its properties. As the mold cools, the mold shell burns away and breaks down, leaving behind a small residue of sand on the surface of the alnico magnets.
Shell molds are created using a mixture of sand and resin. When the molten alnico material is poured into these molds, the sand and resin melt away completely, leaving behind the final shape of the alnico magnets.
The design of molds for casting alnico magnets can be quite detailed and complex due to the versatility of the mold materials. Shrinkage during the molding process is a persistent issue and is carefully considered throughout the manufacturing process.
Fettling is a technique used to eliminate excess material from castings. For alnico magnets, this involves removing the gating system that allowed the molten material to flow into the mold. Fettling is carried out using different grinding methods. Given that alnico magnets are prone to brittleness and chipping, this process requires careful handling to avoid damaging the magnets.
Alnico magnets acquire their magnetic characteristics through a heat treatment process. This process involves heating the magnets to temperatures as high as 1250°C or 2282°F. During this phase, the magnets are placed in a magnetizer and subjected to a strong magnetic field while they cool, a step known as hardening. To further stabilize and refine their magnetic properties, the magnets are then placed in large tempering ovens for several days. This heat treatment not only enhances their magnetic qualities but also improves their ability to withstand temperature variations.
The application of grinding techniques varies among manufacturers. Some alnico magnets are shipped directly after heat treatment without additional grinding. In other cases, grinding is employed to achieve precise dimensional tolerances and meet specific requirements. This process ensures that the magnets conform to the necessary specifications.
Testing of final products is crucial to evaluate the design, performance, and quality of the completed alnico magnets. Various tests may be conducted, including the hysteresis loop test, which assesses magnetic properties, as well as measurements using a gauss meter and a flux meter to gauge the magnetic field strength and flux density, respectively.
Hysteresis Loop Test - The hysteresis loop offers information about the magnetic properties of a material and shows the relationship between the induced magnetic flux density and the applied magnetic force. The size and shape of the loop shows what kind of material the magnet is made from. For high quality alnico magnets, the loop is as wide as possible. Alnico magnets are one of the four materials that meets the hysteresis loop parameters.
Gauss Meter - A gauss meter measures the direction and intensity of a magneticfield using the hall effect, which is the relationship between electric current and magnetic fields. When an electric current is passed through a magnetic field, the force of the field will push the electrons to one side.
Coating alnico magnets is generally unnecessary due to their high corrosion resistance. However, their resistance can vary based on the magnet grade and the specific chemicals they encounter. In environments exposed to saltwater, alkaline solutions, or inorganic acids, alnico magnets may be coated with materials such as nickel, zinc, or specialized paints to enhance durability.
Even when coating is not required for protection, it may be applied for aesthetic reasons, such as for school projects. Often, these magnets are painted red, which has earned them the nickname "red magnets." The coating or painting process is the final step, and the poles can either remain unpainted and shiny or be buffed and polished for a finished look.
An alnico magnet remains unmagnetized until it undergoes the magnetization process. During heat treatment, these magnets are aligned to establish their specific poles and direction. Before this magnetization, they are known as slugs and lack an active magnetic field. Most alnico magnets are anisotropic, meaning they are magnetized in a single, specific direction.
There are two primary methods for magnetizing magnets: static and pulse. The static method is used for creating smaller magnetic fields, while the pulse method is employed for generating more intense fields. In both cases, the magnetizer applies a magnetic field along a predefined direction across the entire magnet.
The pulse method involves intermittent magnetic fields because the magnetic coil requires cooling between pulses. A power capacitor bank discharges electricity into the coil, producing short but intense pulses lasting less than a second, with currents reaching tens of thousands of amperes. During magnetization, alnico magnets are placed between the poles of the magnetizer to ensure full saturation.
Before starting the sintering process, the raw materials must be finely ground into a powder. The elements are carefully measured and mixed to achieve the desired composition. This finely ground powder is then subjected to substantial pressure to form a dense, compact shape.
Sintering is a powder metallurgical technique that involves aligning the magnetization axis during the pulverization of the raw materials before they are pressed into molds. The pressing process can be done perpendicular to create a magnetic field oriented in that direction, which enhances the performance of the magnets. For ring-shaped alnico magnets, a parallel pressing technique is used to achieve the desired magnetic properties.
Sintering, also known as frittage, is a process that forms a solid material by applying heat and pressure without fully melting the components. This heat treatment technique is used to consolidate loose, granular materials into a solid mass. During sintering, the atoms of the material diffuse and bond together, eliminating most of the porosity between particles and pressing them into a cohesive form without reaching the melting point.
This method is particularly effective for producing small alnico magnets, as it efficiently combines aluminum, iron, nickel, cobalt, and other elements. Sintering enhances the material properties, such as strength and structural integrity, by solidifying the components into a durable magnet.
The die used for compressing the material is heated to 2300°F (1260°C) in a hydrogen furnace, which can achieve these high temperatures. The furnace is constructed from stainless or carbon steels, with molybdenum serving as the heat shield to protect the furnace's structure.
Following the sintering process, alnico magnets are extremely hot and must be cooled down. During the cooling phase, the magnets are exposed to an external magnetic field to enhance their strength. This external field typically results in the magnets becoming anisotropic, which is the most common magnetic orientation. Without the application of an external magnetic field, the magnets would remain isotropic, lacking a specific directional magnetic property.
Sintered alnico magnets, like their cast counterparts, generally do not need a coating for protection. Since these magnets are formed directly in a die, they do not require additional grinding, shaping, or forming. Coatings, such as zinc, nickel, or paint, are applied mainly for identification or aesthetic reasons. This coating process is carried out before the magnets undergo magnetization.
The final phase in the sintering process is magnetizing the magnets. While the magnetic direction is set during cooling, the magnetic field strength needs to be enhanced through magnetization, as it remains insufficient initially. To fully magnetize sintered magnets, a pulse generator is used, delivering pulses at intervals of one-fifth of a second.
Alnico magnets require a magnetizing field of 3 kOe (kilooersteds). Electrical coils or solenoids are employed to provide this field and complete the magnetization of the sintered magnets.
Alnico magnets are available in a diverse range of shapes and sizes to suit various applications. They are used in everything from small toys and electric guitars to industrial machinery in factories. These magnets can be shaped through either sintering or casting, with casting being the more prevalent method.
Bar or block magnets are used in schools for experiments, such as demonstrating magnetic fields. They are the weakest shape because of the small area of the poles but are the most common shape. Bar magnets can be used in automation, separation, and holding applications.
Bar magnets can also be used to magnetize other objects. When a bar magnet is rubbed against a metal item, it aligns the electrons within the metal, thereby inducing magnetism. This magnetization is not permanent but can persist for a certain period.
Cylinder magnets feature straight, parallel sides, a circular cross-section, and a hollow core aligned with their length. They are utilized in a variety of applications including seals, sensors, coin collection machines, and guitar pickups. Cylinder alnico magnets are particularly valued in amplifiers, actuators, and motor applications for their high flux density. In the medical field, their strength and adjustability make them useful for specialized applications.
Rod alnico magnets are cylinder shaped and are used in tools and parts. They have high coercivity, strong flux output, and remain stable at high temperatures up to 1000°F or 537°C. Alnico rod magnets have higher residual energy induction and low coercive force compared to ceramic and rare earth materials.
Horseshoe magnets are essentially bar magnets bent into a U shape, enhancing their strength by aligning the poles in the same direction. This configuration makes them effective at picking up metal objects of various sizes, depending on their strength.
Pot, holding, or mounting magnets are designed for various holding applications, serving as alternatives to traditional fixtures and fasteners. These magnets offer the advantage of easy removal and repositioning, unlike permanent fastening solutions.
Ring magnets are cylindrical with a central hole and are sometimes called donut magnets. The orientation of their north and south poles is determined by their polarization method. Typically, one half of the magnet is north, and the other is south, but some polarizations divide the magnet into quarters or eighths.
Ring magnets find applications in scientific experiments and medical fields. For individuals with implanted cardioverter defibrillators (ICDs), which deliver shocks to correct irregular heart rhythms, ring magnets can be used to temporarily disable the device if it malfunctions. Placing a ring magnet on the patient’s chest, directly over the ICD, can stop the device from delivering unnecessary shocks.
Alnico magnets exhibit excellent resistance to oxidation and corrosion, typically eliminating the need for protective coatings, plating, or surface treatments. They are highly resistant to damage from oils, solvents, gasoline, and alcohol. However, their iron content makes them susceptible to surface corrosion if exposed to water for prolonged periods, as well as to alkali solutions and inorganic acids.
While a coating is generally unnecessary for protection, manufacturers often paint alnico magnets to enhance their appearance and mask their natural dark gray color. Red is the most commonly used color, though chrome or nickel coatings are also options.
Alnico magnets can be coated or plated with a variety of materials, depending on the application requirements. Coatings may be applied for aesthetic purposes, to improve bonding, for internal applications, or to increase surface hardness.
Alnico magnets are used for applications with high operating temperatures. They are used where a strong permanent magnet is required. such as electric motors, electric guitar pickups, microphones, sensors, loudspeakers, and cow magnets.
Alnico magnets are a preferred choice for many applications due to their high flux density and strong magnetic lines of force, offered at a reasonable cost. They also feature the lowest reversible temperature coefficient of any magnet, at just 0.02% per degree Celsius, ensuring excellent temperature stability.
Alnico rotor magnets are designed with multiple poles of alternating polarity and include a central hole for mounting on a shaft. They are highly effective in applications such as synchronous motors, dynamos, and air turbine generators.
Cow magnets are used to protect cattle from ingesting metal objects like nails, staples, and bits of baling wire while grazing. These foreign objects can lead to "hardware disease," which poses a risk to the cow's vital organs by causing irritation and inflammation. To prevent this, a magnet is given to the cow orally, usually around one year of age. The magnet then settles in the cow's second stomach, where it attracts and holds onto any stray metal, preventing further health issues.
Alnico magnets are favored in speaker systems due to their ability to precisely tune the magnetic field in the air gap, leading to optimal acoustic performance. The air gap is the space between the poles of the magnet or between the magnet and the adjacent surface. In speakers, one pole of the magnet typically envelops the other pole. The strong magnetic field in this air gap demands precise control, which is effectively achieved with alnico magnets.
Alnico magnets are commonly used in electric guitar pickups, where they play a crucial role in converting the vibrations of the guitar strings into electrical signals. These signals are then sent to an amplifier to enhance the volume of the guitar. The magnetic properties of alnico 2, 3, 4, and 5 magnets are particularly well-suited for this purpose, allowing the electric guitar to be clearly heard even in noisy environments.
Grate magnets are protective devices used in hoppers, floor openings, vertical chutes, and ducts to capture and retain fine iron contaminants. They are specifically designed to trap weakly magnetic or very fine iron particles. Once captured, these contaminants are later removed from the grate.
Highly sensitive and precise equipment relies on the electrical conductivity of alnico magnets to control electrical circuits. In alarm systems, alnico magnets complete the circuit when the system is closed and in the activated position. If unauthorized access occurs, the circuit is interrupted, triggering the alarm. In some cases, the system can also turn off devices or other equipment as part of its response.
Alnico magnets come in various formulations with differing levels of aluminum, nickel, and cobalt. The changes in the proportions of these base metals affect the magnet's strength, leading to variations in their individual magnetic fields.
There are 29 distinct grades of alnico magnets: seventeen are cast, ten are sintered, and two are bonded. These grades are determined by factors such as the magnet's chemical composition, residual induction, coercive force, maximum energy, cobalt content, and operating temperature. Generally, as the operating temperature increases, so does the grade of the magnet.
Most alnico magnets are anisotropic, which are known for their superior strength compared to other grades. The following discussion explores various alnico grades and their applications.
The chart below offers a summary of some alnico magnet grades and their respective properties.
Grades of Alnico Magnets | ||||||||||
---|---|---|---|---|---|---|---|---|---|---|
Dura Magnet Grade | Residual Induction Br |
Coercive Force Hc |
Intrinsic Coercive Force Hci |
Maximum Energy Product (BH)max | Max Operating Temp | |||||
Nominal | Nominal | Nominal | Minimum | Nominal | Nominal | |||||
k-Gauss | Telsla | k-Oersted | KA/M | k-Oersted | KA/M | MG Oe |
KJ/m3 | °C | °F | |
Alnico 5 | 12.2 | 1.22 | 600 | 48 | 630 | 50 | 5 | 40 | 500°C | 930°F |
Alnico 5B | 12.22 | 1.22 | 650 | 52 | 660 | 53 | 5.5 | 44 | 500°C | 930°F |
Alnico 5 DG | 12.5 | 1.25 | 690 | 55 | 700 | 56 | 6.5 | 52 | 500°C | 930°F |
Alnico 5-7 | 13 | 1.3 | 700 | 56 | 740 | 59 | 7.5 | 60 | 525°C | 980°F |
Alnico 8-HC | 7 | 0.7 | 1,750 | 139 | 1,750 | 139 | 4.5 | 36 | 525°C | 980°F |
Alnico 8 | 8.2 | 0.82 | 1,500 | 119 | 1,600 | 127 | 5 | 40 | 525°C | 980°F |
Alnico 8B | 8.8 | 0.88 | 1,500 | 119 | 1,650 | 131 | 5.5 | 44 | 525°C | 930°F |
Alnico 8C | 9 | 0.9 | 1,380 | 110 | 1,440 | 115 | 7.5 | 60 | 525°C | 930°F |
Alnico 9 | 10.5 | 1.05 | 1,410 | 112 | 1,440 | 139 | 9 | 72 | 525°C | 930°F |
Alnico 2 | 7 | 0.7 | 500 | 40 | 540 | 43 | 1.5 | 12 | 450°C | 840°F |
Alnico 5 | 11.0 | 1.1 | 600 | 48 | 600 | 48 | 4.25 | 34 | 450°C | 840°F |
Alnico 8 | 8.8 | 0.88 | 1530 | 121 | 1,600 | 127 | 5.25 | 42 | 450°C | 840°F |
Alnico 2 is the second weakest among alnico magnets, characterized by its low cobalt content. It is isotropic and has a lower magnetic output compared to other types. Alnico 2 magnets are commonly used in electric guitars, where they are valued for their ability to enhance sound clarity in audio recording and performance. Despite their lower strength compared to alnico 4 and 5 magnets, alnico 2 magnets can produce a cleaner and more defined sound when used in guitar pickups.
Alnico 3 is the weakest of the alnico magnets and contains no cobalt. Like Alnico 2, it is isotropic and has a low magnetic output. Alnico 3 magnets are also used in electric guitars and offer similar sound characteristics to Alnico 2 magnets.
Alnico 4 is a relatively weak magnet, comparable to Alnico 2 and 3. It is isotropic with a low magnetic output and is primarily used in sound recording and performance applications.
Alnico 5 is the most commonly used alnico magnet, available in four cast versions and one sintered version. It provides efficient magnetic energy to circuits and is a high-grade anisotropic magnet with exceptional magnetic output. The magnetic direction of Alnico 5 is established by its crystal alignment during the molten phase. These magnets can produce large magnetic fields, but for optimal performance, they should be magnetically long and incorporate iron or steel components to minimize demagnetization.
Alnico 8 boasts the highest coercive resistance among alnico grades and offers excellent energy density with a low reversible temperature coefficient. It is ideal for applications subject to demagnetizing fields or where a compact magnetic length is needed.
Alnico 9 features strong magnetic properties and a single crystal structure. It is employed in geological detection instruments as well as in defense and aerospace technologies. Like most alnico magnets, Alnico 9 maintains its resistance to high temperatures.
A ceramic magnet, also known as a ferrite magnet, is a permanent magnet made by combining iron oxide and strontium carbonate. They are a man made magnet produced by heating the two elements to...
Flexible magnets are composite materials with magnetic components arranged in an elastomer matrix. They are made from a combination of rubber polymer resin and ferrite powder by forming it through...
Magnets are materials that exert a noticeable force on other materials without physically contacting them. This force is called a magnetic force. The magnetic force can either attract or repel. Most known materials...
A Neodymium (Nd-Fe-B) magnet is a common rare earth magnet composed of neodymium (Nd), iron (Fe), boron (B), and transition metals. They have superior performance in applications because of their strong...
Power supplies are electrical circuits and devices that are designed to convert mains power or electricity from any electric source to specific values of voltage and current for the target device...
An AC power supply is a type of power supply used to supply alternating current (AC) power to a load. The power input may be in an AC or DC form. The power supplied from wall outlets (mains supply) and...
A bowl feeder is a mechanism for supplying small parts and components to a production line or for sorting bulk items for rapid use. A self contained bowl feeder system has a bowl that sets on a spring loaded base that moves vertically...
A DC DC power supply (also known as DC DC Converter) is a kind of DC power supply that uses DC voltage as input instead of AC/DC power supplies that rely on AC mains supply voltage as an input...
A DC power supply is a type of power supply that gives direct current (DC) voltage to power a device. Because DC power supply is commonly used on an engineer‘s or technician‘s bench for a ton of power tests...
Electric transformers are static electrical machines that transform electric power from one circuit to the other without changing the frequency. An electrical transformer can increase or decrease the voltage with...
An electromagnetic interference or EMI Filter is an electrical device or circuit that filters specific unwanted frequencies in power lines or offending frequencies that are detrimental to a system. They receive AC or main power...
By definition a power supply is a device that is designed to supply electric power to an electrical load. An electrical load refers to an electrical device that uses up electric power. Such a device can be anything from...
An isolation transformer, just like typical transformers, is a non-moving device that transmits electrical energy from one circuit to another without requiring any physical contact. It works on the idea of magnetic...
Power transformers are electrical instruments used in transmitting electrical power from one circuit to another without changing the frequency. They operate by the principle of electromagnetic induction. They are used in transmitting electrical power between...
A programmable power supply is a method for controlling output voltage using an analog or digitally controlled signal using a keypad or rotary switch from the front panel of the power supply...
An electrical transformer is a passive machine that transfers electrical energy from one circuit to another using a magnetic flux to induce an electromotive force. Transformers are used to increase (step-up) or decrease (step-down) voltages without changing the frequency of the electric current...
A toroidal transformer is a type of electrical transformer constructed with a torus or donut-shaped core. Its primary and secondary windings are wound across the entire surface of the torus core separated by an insulating material...
Vibratory conveyors are material-handling equipment used to transport fine to coarse-grained bulk materials. These vibratory conveyors are strong conveying equipment utilized for bulk commodities with fine to coarse graininess...
Vibratory feeders are short conveyors used to transport bulk materials utilizing a controlled vibratory force system and gravity. The vibrations impart a combination of horizontal and vertical acceleration through tossing, hopping, or sliding-type of action to the materials being handled...
A vibratory screening is a process that separates bulk solid materials from solids and slurries using inertial vibration that causes various sizes of particles to pass through openings in a screen or...
Electronically operated equipment depends on power transformers to convert electrical currents into voltage. Current transformers store and transport energy through power lines and grids...