Central Vacuum Systems
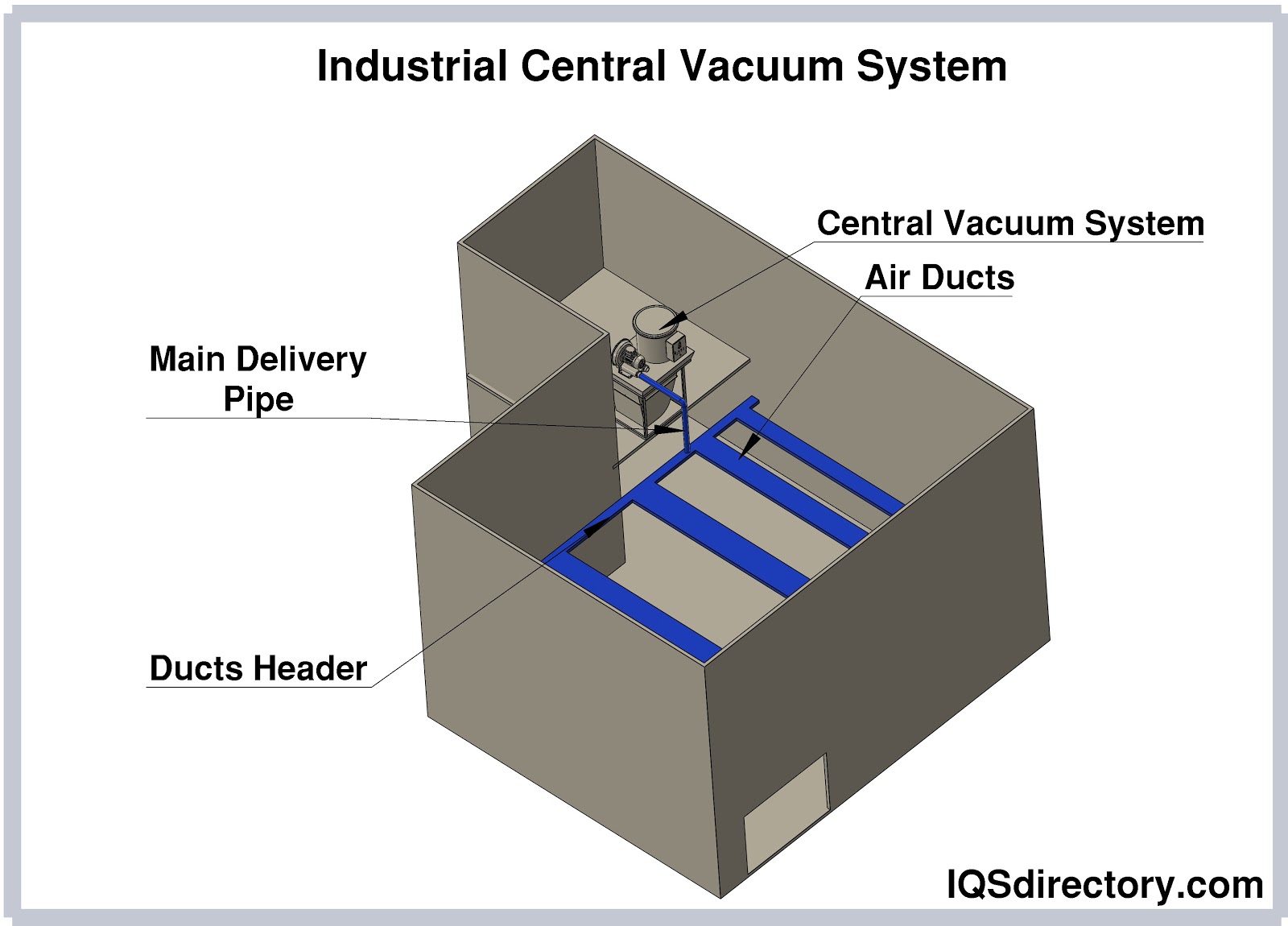
A central vacuum system is a cleaning mechanism that is built into a building for ease of use, access, and maintenance. Vacuum and pressure are created by a centrally located motor to remove dirt, dust, and debris...
Please fill out the following form to submit a Request for Quote to any of the following companies listed on
This article will take an in-depth look at explosion-proof vacuums and dust collectors.
You will understand more about topics such as:
Explosion-proof vacuums are vacuum systems that use compressed air, electricity, and cyclonic motion to prevent the ignition of gasses or vapors and operate at temperatures that will not ignite a possibly flammable atmosphere. Replacing motors with compressed air prevents explosions from being started by sparks from motors, friction, or heat from moving parts. Plugs, switches, and arcing motors can generate sparks in regular electric vacuum cleaners.
The components of explosion-proof vacuums are joined together and grounded to safely discharge any built-up static and avoid sparks or other explosion threats. Explosion-proof vacuums do not directly use electricity or electrical cables that could create sparks and potentially produce dangerous circumstances.
Explosion-resistant vacuums have metal drums used to collect the dust and keep it confined to avoid potential explosion. When the drums are full, they are sealed and discarded. Metal drums are containment units for hazardous material when collected.
Industrial explosion-proof vacuums use electricity, the Venturi effect (see chapter 3 for more information), and cyclonic energy as part of their process. The method used to collect dust, dirt, and debris depends on the type of material and its class and division since each type of explosion-proof vacuum is rated for a variety of specific materials. Therefore, when purchasing an explosion-proof vacuum, it is important to understand the different classifications and divisions to get the type of vacuum that matches the conditions and waste materials. Miscalculations in the collection of volatile materials are hazardous and dangerous.
Explosion proof dust collectors are air purifying devices that remove combustible gasses and enhance air quality in commercial or industrial settings by trapping gas vapors and particulates. They filter and trap the solid pollutants and ones that the government has outlawed in response to the air pollution crisis. Raw gas comes into the dust collector where filters purify it and separate dust from it after which clean air is released. Manufacturing and industrial operations release dangerous particles that can harm the lungs and cause health issues. Dust collection systems collect the particles through a network of filters and separators to change the tainted air.
Dust collecting systems are combustible gas removers and air cleaning systems used to remove particulate matter, gas vapors, and prevent ambient air pollution and explosions. They collect dust using ducting, air purifiers, pleated filters, and containers. The various systems have different configurations, designs, and components depending on the manufacturer and the types of dust being collected.
Ductwork for explosion proof dust collectors is carefully designed and planned to guarantee that the system will operate safely. The size of the ductwork determines the pipe's size, the amount of air needed, the length of pipe required, the number of machines being serviced, and the kinds of particles being extracted. Air is brought into the dust collector by fans with each type of collector varying to meet the needs of the air cleaning process and type of combustible material.
Blowers, or fans, move polluted air from the workplace into the ductwork, filtration, and cleaning systems. Even though fans or blowers may have straightforward designs, several things must be considered when installing them in a dust collection system.
The first consideration is the quantity of air that needs to be moved. It is expressed as a cubic foot per minute (CFM). Static pressure across the entire system is the next factor with the composition of the air, its temperature, combustibility, and moisture content being other factors. Blowers can be centrifugal or axial, where an axial blower is like a standard fan, and a centrifugal blower pulls in air at an angle.
The core of air purification for dust collection systems is in its dust filters. A blower draws air from the work area into the filter, which removes airborne particles. The amount of air flowing through a square foot of the filter is known as the air-to-cloth ratio. The efficiency of a filtration system improves as the ratio decreases. After gasses are removed, particulate matter falls into a container or receptacle. The material of a filter and its loading rate affect the container's design with all explosion proof dust collectors using HEPA or ULPA filters.
The various components of an explosion-proof vacuum must meet a set of government standards to be classified as explosion-proof. The housing, filters, hoses, and other elements are made of durable and strong materials that can withstand demanding and hazardous conditions.
Heavy Duty Housing: The housing can contain any explosion and has a stainless steel outer shell that does not crack or dent. Anti-sparking substances reduce the possibility of electrical discharge. In addition to stainless steel, explosion-proof housings may be made of reinforced fiberglass.
One of the essential elements of any air cleaning system is HEPA filters, which can remove 99.9% of particulate matter. They are used in all cleanrooms and hygienic environments. Specially designed HEPA and ultra low particulate air (ULPA) filters are used with explosion-proof vacuums. They are a critical component that enhances the safe use of explosion-proof vacuums. With the capability of capturing 0.2 microns (µ) sized particles, HEPA filters clean and capture hazardous dust to ensure safe, clean air is exhausted from an explosion-proof vacuum.
Explosion-proof vacuum cleaners are grouped into classes, divisions, and power ratings with special products developed for unique work areas. To understand explosion-proof vacuums, it is important to understand the different classes and divisions.
The National Electrical Code has developed a system of classifications, divisions, and groups that clarify the specific capabilities required of an explosion-proof vacuum. Additionally, the Occupational Safety and Health Administration (OSHA) has standards for explosion-proof vacuum cleaners that outline necessary safety features for operators.
OSHA standards state that vacuum operators must take extra precautions when operating explosion-proof vacuum cleaners in locations with flammable gasses, vapors, or liquids. Metal-to-metal contact, hot surfaces, static electricity, blazing embers, flames, and electrical sparks can cause ignition and explosions.
Classification by area refers to classifying rooms, sections, and areas separately, a classification method that provides information on potentially dangerous situations and hazardous compounds that may be present. The evaluation includes an identification of the necessary safety gear and practices that should be practiced and followed in an area.
The North American classification system is found in the National Fire Protection Association (NFPA) Publication 70 NEC and CEC which outlines the kinds and amounts of dangerous materials present that could serve as an ignition source for a fire or explosion.
Class is the first of the three categories used to characterize an area. The three classes are Class I, Class II, and Class III, established by NFPA Publication 70 NEC and CEC. Each class details a potential type of hazardous material.
The explosive properties of a substance can change depending on what is being used. These properties include the materials' ignition temperature, safety clearance, and maximum explosive pressure. Gasses that are flammable and combustible are separated into additional classes.
The temperature class refers to the ignition temperature of dangerous and hazardous material and is the lowest temperature at which a material will ignite. It is a descriptor for the levels of thermal energy that an explosion-proof vacuum can produce. The ratings for temperature classes are referred to as T classes, which begin at T1 and run to T6.
Each of the classes has two divisions used to determine the likelihood of the presence of a hazardous material with explosive potential.
Division I: Division I indicates a high possibility of some ignitable substances.
Division II: Division II indicates a low amount of ignitable materials.
The group definition covers atmospheric hazards mainly emphasizing flammable and combustible substances. There are seven groups that include Group A to Group G, each group defining atmospheric contaminants.
Single-phase electric explosion-proof vacuums are used for cleaning dry explosive dust such as aluminum, magnesium, titanium, and gunpowder and can be used with Class 1, Division 1, Group D materials in Class II, Division 1, Groups E, F, and G locations. As with all explosion-proof vacuums, they are designed to operate in harsh and hazardous conditions. They have various sets of HEPA filters and an explosion-proof pressure switch with filter status indicators. Most single-phase explosion-proof vacuums will automatically stop working when their filters are full or blocked.
Three-phase electric explosion-proof vacuums collect combustible dust and have one or more HEPA filters classified for use with combustible materials. They have a stainless steel chamber and container with electrical requirements for Class II Division 2 environments and are equipped to handle Group E metal dust. As with the single phase explosion-proof vacuums, three-phase models come with a filter cleaning indicator, with some models having a manual dust filter shaker for dedusting the filters.
A Venturi explosion-proof vacuum uses a Venturi tube to create suction, a process where the construction in the Venturi tube causes air to speed up and slow down. As air passes through the constriction, low pressure is created to produce a vacuum. The suction created is more powerful than that created by an electric vacuum.
In a Venturi explosion-proof vacuum, compressed air is forced by a compressing nozzle into a chamber. As the air is forced through the nozzle, it speeds up but suddenly slows down after entering the mixing chamber. The negative air pressure created by the air velocity reduction creates suction in the vacuum line. The mixture of vacuumed air and debris is sent through a filter. With compressed air, negative pressure in the metal drum creates suction through a connected hose.
Cyclone explosion-proof vacuums separate dust from the vacuum stream and force dust particles into a collection drum. The process keeps dust particles from being trapped in the filtration system while removing them from the environment. The vacuum creates a vortex that sucks waste material downward. The shape and size of the created cyclone prevent particles from entering the flow of the vacuum.
The vacuum process for a cyclone explosion-proof vacuum increases its operating time and decreases the number of times required to clean the filter.
Pneumatic explosion-proof vacuums do not use electricity, a motor, or any moving parts. They are ideal for vacuuming explosive materials such as flour, carbon dust, titanium powder, and aluminum powder. Pneumatic explosion-proof vacuums come with static-suppressing components that eliminate concerns about the effects of static electricity.
The main power source for pneumatic explosion-proof vacuums are portable air compressors. They use a Venturi system to create a vacuum that pulls in debris. Pneumatic explosion-proof vacuums are quiet and lightweight, which makes them easy to use. In addition, they are highly versatile, capable of removing wet or dry waste, and can have drums of 18 gallons up to 55 gallons.
Single, dual, and quad Venturi explosion-proof vacuums and pneumatic vacuums are powered by compressed air. They are the most used type of explosion-proof vacuum because they do not use any electrical motor that could create static electricity. An air powered explosion-proof vacuum is attached to an airline to generate vacuum power. All air-powered explosion-proof vacuums depend on Venturi tubes to create their vacuum using portable air compressors.
Explosion-proof dust collectors gather dust and purify the air using various filtration processes but can remove explosive or combustible dust. Dust collectors used to collect explosive materials can be large dust-collecting units with special filtration systems or portable castors. They are equipped with tools to manage, suppress, and control combustibles.
Although explosion-proof dust collectors are made to prevent explosions, they are selected based on the requirements of the specific types of dust they are intended to collect. All organic dust is explosive and must be collected using an explosion-proof dust collector.
“Go or no go" testing is the first step in the process when potentially explosive or flammable particles are present. Next, collected dust is evaluated at its location using various processes and further examined by OSHA. These procedures provide guidance for choosing the best dust collection method.
The initial phase of combustible analysis begins with a DHA (dust hazard analysis), which covers combustion risk, characteristics of the environment, chances of combustion, and potential damage. This particular analysis can be completed at a facility and is unrelated to government regulations.
The more critical step in dust analysis is completed by OSHA. It is referred to as PHA (process hazards analysis), a broader and more detailed analysis of the potential of combustible dust. In addition, NFPA standards 61, 484, 654, 655, and 664 outline the characteristics of various types of dust and how to control and prevent dust explosions.
Pulse jet dust collectors are baghouse dust collectors that use pulsed jet air to shake dust-coated cloth bag filters clear of debris. Differential pressure sensors measure the amount of pure air and the pressure of contaminated air. Cleaning the filters begins when the pressure is too high.
One of the most popular dust collection systems is the jet dust collector because it requires less maintenance, can remove high-density dust, and has great filter performance. However, they are very large, require exterior installation, and take up more room than other dust collectors. Product recovery and dust collection, separating and filtering explosive media, metalworking chips, poisonous media, central vacuum cleaning, and pneumatic conveying are all excellent uses for pulse jet dust collectors.
Industrial dust collectors remove pollutants from workplaces, plants, manufacturing facilities, and commercial and industrial spaces that require a high standard of cleanliness. Pollutants produced in these environments, such as volatile organic compounds, hydrocarbon, and solvent fumes, must be removed from the air and disposed of since they can affect the environment and biological systems. Explosion proof duct collectors have a system of filters that remove gas vapors and dust that collect the gas vapors and make them inert.
Regulatory and insurance companies occasionally demand that dust collectors be used to ensure a healthy work environment due to the potential health risks to employees and other issues with air quality. In addition, to further protect workers, some rules call for specific levels of soundproofing due to the operation of loud machinery.
An electrostatic precipitator grabs and holds pollutants using electrostatic force supplied by a set of connected wires. As air passes through the wires, it is electrically charged and ionized, after which it is delivered via an electrostatic field to the collection plates. The charged air particles cling to the collecting plate and are left behind as the remaining cleaned air travels exits.
There are many techniques to remove the gathered debris from the collection plates, such as shaking, scraping, or simply cleaning them. In addition, the electrostatic precipitator process is modified for larger particles, such as ash and particles that require more energy.
Cyclone dust collectors are inertial separators that remove particles from the air using centrifugal, or cyclonic, air movement in a hopper chamber. The centrifugal cyclonic motion in the hopper chamber forces larger particles against the exterior wall of the chamber, from which they fall into a collection chamber.
The types of cyclone dust collectors include enormous outdoor ones made for cement industry manufacturing to lab-sized ones used in the pharmaceutical industry. Cyclone dust collectors come in different configurations for enhanced efficiency to meet the needs of various applications. They are also used to ensure worker safety and equipment longevity.
Downdraft tables can automatically remove dust from a work area or can be activated by a worker. Before the development of downdraft tables, workers cleaned their work area by sweeping across the work surface and pushing waste material into a hole in a work table.
The main purpose of downdraft tables is to capture exhaust powders, fumes, fine particulates, heavier-than-air particles, and lighter-than-air particles. They have perforated grills that evenly distribute airflow. Air enters through an exhaust chamber directly underneath the top of the table and is drawn down through the perforated top. Filters in the exhaust chamber catch dust as fine as 0.5 microns (µ).
Shaker dust collection systems are used with large particulate matter operations such as wood dust or plastic chips. A filter bag suspended inside the dirty air plenum collects dust on its exterior. The connection duct for a shaker dust collector is located below the hopper. As the velocity of the air decreases when the air enters the dust collector, larger particles fall into the hopper. In contrast, smaller ones are collected on the exterior of the filter bags.
The rattling of the filters releases the collected particles into the collection bin or hopper.
Shaker dust collectors can have a segmented system or an interrupted airflow system. The system’s design allows for continuous operation without taking the system offline. Shaker dust collectors are used in foundries, steel mills, mines, and smelting plants where it is impossible to provide compressed air to clean the filter.
Wet scrubbers are also known as wet dust collectors and use a scouring fluid to gather gasses and particulates, with water being the most popular solvent. Contaminated air enters the bottom of the scrubber and passes through the packed bed with a downward-flowing water solvent that collects the pollutants.
There are specific requirements for liquids used in wet scrubbers. They are chosen by how their chemical composition mixes with contaminants. Positive, negative, or uncharged solutions absorb materials. Therefore, chemical composition must be compatible with the pollutants and capable of binding them.
Portable dust collectors are designed for small-scale dust collecting for repair shops, commercial facilities, and small projects. They are designed to reduce debris from welding, cutting, grinding, and other dust-collecting processes. Unlike a vacuum, portable dust collecting systems can work with lower pressure, allowing them to operate continuously.
The design of portable dust collectors includes self-cleaning filters and an auger for dust discharge. Regardless of their size, portable dust collectors, normally with a bag house design, are just as efficient as their larger counterparts. They are made of heavy-duty materials and are tightly sealed.
Cartridge dust collectors have cloth filters made for specific purposes. They are advantageous when less room is needed to maintain the same airflow as a bigger baghouse system. Cartridge dust collectors reduce safety risks by having fewer filters, increasing fabric surfaces in a smaller space, and allowing for outside filter changes. These features decrease the time required to change the filters and labor costs.
The size of cartridge dust collectors makes them ideal for commercial and industrial settings where there is extremely fine, light, or moderate dust, such as during the manufacture of pharmaceuticals, powder coatings, metalworking, woodworking, fume collection, thermal spray, and other activities.
Laser Plasma Cutting: Laser cutting uses a focused laser beam for tighter tolerances. In manufacturing, stainless steel is cut using the plasma cutting process that combines gasses. Cutting with lasers and plasma generates fumes, smoke, dust, and oxides. As a result, it is crucial to have a laser fume extractor to ensure the safety of workers and the efficient use of machinery. Many laser-cutting systems have built-in duct ports for dust collection. The air-to-cloth ratio and total draw are two laser dust collector characteristics.
Food Processing: Common ingredients like sugar, flour, and spices are created using processes that produce explosive dust. As materials are processed and packaged, tiny particles from mixing and blending are discharged into the atmosphere. Dust collectors collect and gather dust particles.
Plastics Industry: Plastics are used in almost everything, including offices, cars, communication devices, and entertainment. These goods are created using polymers and a complex mixture of substances called additives. The dust and debris from plastic processing are harmful to the lungs and cannot be released into the environment. Dust collectors clean the air and prevent contamination.
Extrusion, blow molding, injection molding, and 3D printing are used to shape and manufacture plastic products. These material-combining operations release dust particles. Byproducts of these production methods must be gathered and eliminated from the air, whether it's fine dust created by sanding or deburring or by crushing and shredding recycled plastics. To provide a healthy working environment, industrial dust collecting systems are used to remove airborne particles.
A central vacuum system is a cleaning mechanism that is built into a building for ease of use, access, and maintenance. Vacuum and pressure are created by a centrally located motor to remove dirt, dust, and debris...
A HEPA vacuum cleaner is a vacuum cleaner that accepts high efficiency particulate air (HEPA) filters, is tightly sealed, and allows air to only pass through the HEPA filter. They are designed to capture particles of dust, dirt, and...
An industrial vacuum cleaner is a heavy duty piece of cleaning equipment designed to remove debris, industrial waste, construction refuse, and matter that remains after a manufacturing process or construction project...
Vacuum cleaners use suction to collect dirt, dust, waste products from industrial processes, and other debris for disposal, recycling, or reuse. They are mainly used for building maintenance and cleaning of industrial space...
Air filters are devices used to remove airborne particles, pollutants, and microorganisms hazardous to health and the ecosystem. In industrial facilities, air filters preserve the quality of products and materials and protect critical equipment from damage...
An automatic screwdriver is a piece of equipment that automatically inserts screws into a product during assembly and production. Since every production operation is unique and requires a...
An automation system is an integration of sensors, controls, and actuators designed to perform a function with minimal or no human intervention. The field concerned in this subject is called Mechatronics which is an...
A baghouse is a pollution control device that uses tubes, envelopes, or cartridges to remove, capture, and separate dirt, particulate matter, and dust from the air of a manufacturing or processing facility. The main components of a baghouse are the media or bags used to filter the particles from the air as it passes through the system...
A centrifugal blower is an air moving device that uses an impeller to pull air into a tube like structure and release it at a 90o angle. The impeller is a set of blades inside the blower that rotates at a high rate to pressurize and move air...
Collaborative robots, also abbreviated as Cobots, are the newest technology in robotics. They have changed the automation world significantly. These robots can work safely together with workers, hence are...
A dust collection system is a system that removes particulate contaminants from the air in production facilities, workshops, and industrial complexes. The system cleans air by forcing it through a series of airtight filters...
A HEPA filter is a high efficiency pleated air filter capable of capturing extremely small particulate matter down to particles that are the size of a micron (µ), or a micrometer, which is 1/1000th of a meter...
An industrial blower is a device that enhances the air flow in a workspace effectively and efficiently using an electric motor, impeller, and airfoils. The purpose and function of industrial blowers is to be a permanent addition to a workspace to increase airflow and...
An industrial fan is a highly efficient, heavy duty air flow device that is constructed from exceptionally durable materials and components to withstand stringent environments and operate longer to provide constant air flow and pressure. The strength of industrial fans is due to the materials used...
An industrial robot is an autonomous system of sensors, controllers, and actuators that executes specific functions and operations in a manufacturing or processing line. They operate continuously through repetitive...
A jet dust collector is a suction filtration unit that pulls dust ladened air into a filtration system that collects particulate matter and releases clean air. The filters of jet dust collectors are cleaned by compressed air that uses...
Robotic system integrators are companies that provide assistance in automating a wide range of applications. They help design robotic technologies that best suit the needs of an operation for a company and solutions as...
Warehouse automation is the process of replacing repetitive tasks with systems that are automated. The main goal is to remove labor-intensive duties that consume time. As a result, the workers can focus more on...
During the Industrial Revolution, when companies began producing high volumes of industrial waste like fine dust, wood dust, and other particles, an American, in 1852, S.T. Jones, applied for the first dust collector patents, a single bag filter...