Automatic Screwdrivers
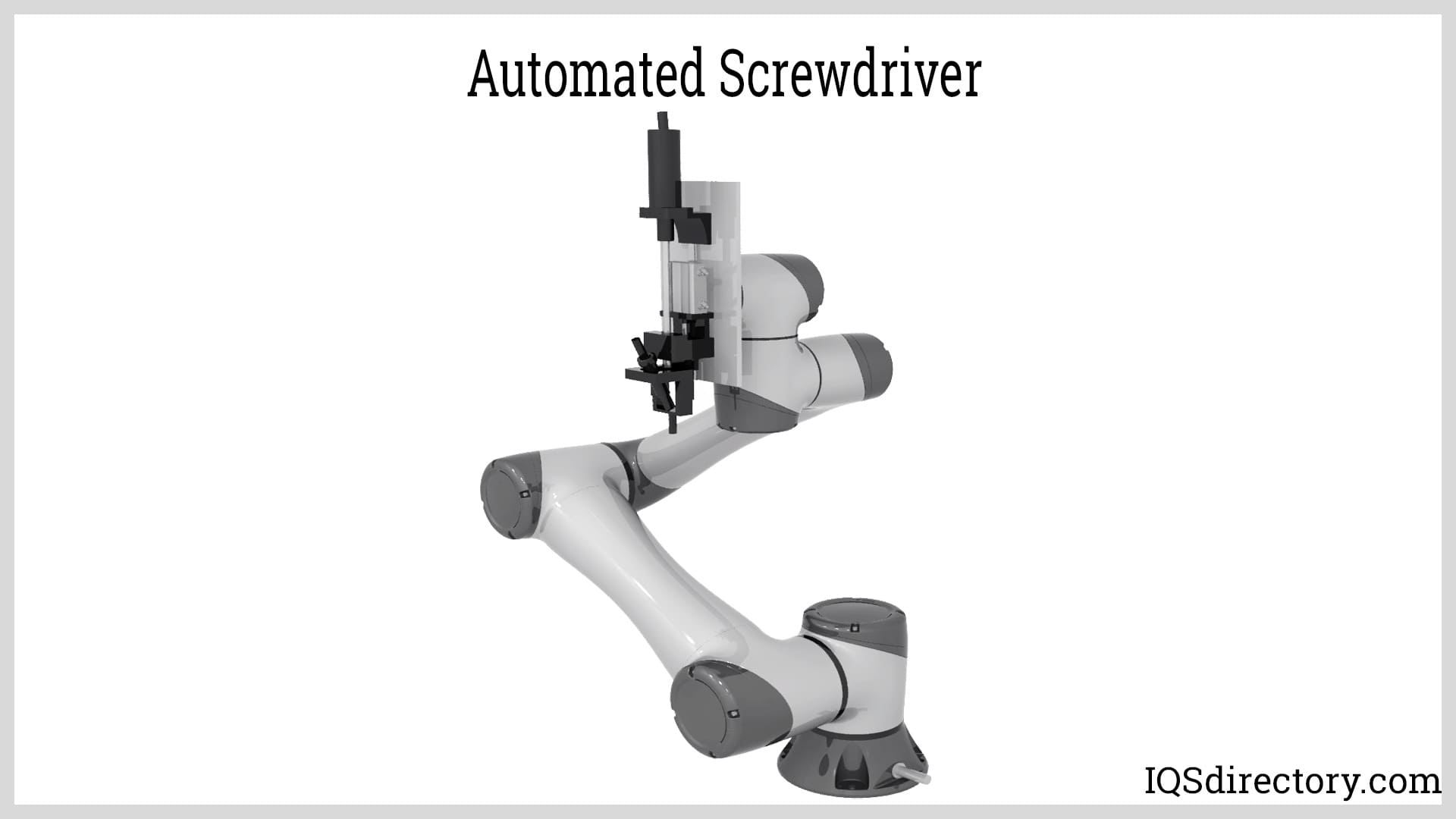
An automatic screwdriver is a piece of equipment that automatically inserts screws into a product during assembly and production. Since every production operation is unique and requires a...
Please fill out the following form to submit a Request for Quote to any of the following companies listed on
This article will take an in-depth look at warehouse automation.
The article will provide more detail on topics such as:
This chapter will discuss what warehouse automation is and how it works.
Warehouse automation is the process of replacing repetitive tasks with systems that are automated. The main goal is to remove labor-intensive duties that consume time. As a result, the workers can focus more on important tasks like quality control.
Material handling automation and warehouse automation refers to the implementation of software to take over tasks that are simple tasks that require little effort to complete. Bulk material handling automation equipment is capable of conveying, loading, unloading, weighing, processing, and feeding an array of bulk solid materials. They perform as robots in manufacturing to assist in material handling.
Digital automation with robotics reduces manual procedures by using data and software and uses automatic identification and data capture (AIDC) technology, such as mobile barcoding. Its advantages include the capacity to interface with enterprise resource planning (ERP) systems, improved safety, increased security, and more-effective data management. Digital automation with robotics eliminates human mistakes and cuts down on manual operations. AIDC technology, such as mobile barcode scanning and RFID (radio frequency identification), improve material handling automation, customer service, boost employee morale, and lowers operating costs caused by human error.
Digital automation technology implementation requires upfront expenditures, which are expenses that cover the time and resources needed to deploy the systems, educate staff, and pay for the necessary hardware, software, and maintenance contracts. Digital automation raises the chance of lost or damaged data as well as cybersecurity risks.
Technology may be used to reduce staff from needing to travel across various parts of the warehouse and create more effective workflows through physical automation. Automation with robotics increases warehouse capacity and efficiency and improves dependability and scalability of services. The disadvantages include hefty initial expenditures, a lack of a competent personnel to operate and maintain the system, high maintenance costs, and equipment designed for specialized uses.
Organization and careful preparation are required for firms to benefit from automated warehouse systems. Large-volume warehouses and distribution facilities with room for specialized equipment are better suited for these systems.
Overall, warehouse automation falls into two categories- physical automation and digital automation. Digital automation is dependent on the use of electronics and software to minimize manual processes in order to increase the number of vendors and customers. An example of digital automation software is a warehouse management system or automatic identification and data capture.
From a warehouse perspective, digital automation can provide enhanced security, reduced legal and operational risks, more efficient enterprise resource planning, and improved safety. Human errors are eliminated and manual processes are minimized. The implementation of digital automation with robotics technology requires a large initial investment. The costs incurred include support contracts, software, hardware, resources, and the time required for training employees and implementing the system.
Physical automation on the other hand refers to the reduction of employee labor by the use of warehouse automation equipment. Automated guided vehicles, robots in manufacturing, and robotic integration are examples of physical automation. Their use means goods are transported with minimal effort by employees. In the warehouse, there is improved efficiency and capacity.
Another advantage of physical automation with robotics is that there is the scalability of services, enhanced reliability, and improved performance. The drawbacks are a scarcity of workforce that is sufficiently skilled to maintain and manage the system, the upfront expenses, and the high maintenance costs.
This chapter will discuss the different levels of warehouse automation. The automation drivers will also be discussed in this chapter.
The different levels of warehouse automation include:
Low automation in a warehouse or factory is characterized by manual processes. It relies greatly on personnel. The moving of material, collection of data, operation of factory machines, and construction of products is done by employees with a low-automation approach. However, low-automation warehouses or plants may consist of pieces of equipment that are automated. Low automation can be prone to inconsistent and low productivity, errors, limited operating hours, high turnover from workers, poor or defective parts, and unexpected stoppages.
A warehouse management system is a set of processes and policies that are meant to organize the distribution center, or work, of a warehouse and ensure efficiency so that objectives are all met. The main use of a warehouse management system is to note the departure and arrival of inventory in and out of the factory. From the beginning point, the exact location of stock in the warehouse is recorded and the available space is optimized, thereby maximizing efficiency.
When using automation technology, the tasks that are carried out by an automated process are run by a program that is executed during a work cycle. For work cycle programs to be run properly, there should be an automated system to run these advanced functions. Advanced automation is seen in factories as robots in manufacturing that are focused on producing high-quality, cost-efficient goods.Manufacturing robots are capable of completing a wide range of functions from the beginning of processing to the final product.
To maximize operations inside and outside of their warehouses and increase efficiency, an increasing number of businesses are investing in logistics automation. Automated storage and retrieval systems (AS/RS) at logistics centers provide increased productivity and efficiency in the processes of receiving, storing, and distributing items. Additionally, it reduces warehouse costs brought by mistakes and improves the security of the workers and the goods.
Automated warehousing systems, which are influencing businesses across many industries, include:
One of the most difficult tasks in the warehouse is processing orders since it takes up a significant amount of time and resources. When picking orders manually, employees search the warehouse for the SKUs they require, then gather them in a cart or on material handling automation equipment to package and distribute the items.
Some businesses use automated storage systems and robotics integrators in their logistics facilities to simplify and expedite this process. Mini-load systems (AS/RS for boxes) are the best option for businesses with intensive picking procedures. The systems allow operators to assemble orders with the help of roller conveyors and stacker cranes. Robotic integration has been successful in enhancing processing for picking procedures.
Automated material handling systems, which are designed to do pick and place, or transferring items from one position in order to arrange and put them in another, are another alternative utilized to assist in picking. Logistic automation systems sort products and manage their quality in addition to moving them rapidly and error-free.
The repetitive nature of transferring goods consumes a significant amount of labor. Streamlining other activities and having automated material handling systems for product movement makes it possible for workers to focus on other, higher-value tasks.
Automated transportation options are typically included in automated warehouse systems. The most popular ones include roller conveyors for boxes and bins, as well as pallet conveyor systems. These can either link the warehouse and the production zone, or the various zones of a logistics facility. Both automated guided vehicles and autonomous mobile robots are popular choices for maximizing the efficiency of these systems. These robots can navigate the warehouse independently of human supervision.
Dark warehouses have become more common as a result of warehouse automation. These are completely-automated facilities with no need for lighting because there is no human contact there.
High inflow/outflow traffic and automated processes that increase productivity and maximize resources are characteristics of these facilities. Because dark warehouses consume less energy, businesses may reduce expenses and guarantee the sustainability of their supply chains. By automating all processes, they also get rid of mistakes.
Two of the busiest activities in the warehouse are entries to, and departures from, the docking sections. Automatic truck loading and unloading systems are frequently implemented by businesses wanting to expedite cargo inflows and outflows.
It is possible to load and unload items in the warehouse rapidly due to this automated transportation technology, which needs little human involvement. These systems, which are located at the loading docks, automatically load and unload cargo from trucks with little assistance from operators. Among its benefits are increased speed and reliability in the transportation of products both in and out of the facility.
A common trend in logistics is automated warehouse management. Companies that need precise control over the operations and goods in their logistics facilities may choose to digitize activities using a warehouse management system (WMS) to meet the demands of operations that are becoming more and more demanding.
For businesses looking to automate their warehouses, a SaaS (software as a service) WMS solution, which is cloud-based, is a very helpful choice because data processing and storage are outsourced to external servers. According to a Grand View Research survey, companies choose to use cloud-based WMS software since it is more affordable to adopt than on-premise alternatives.
One of the pillars of supply chain automation is its ability to produce complex information (big data) for logistics. Automated warehouses provide a vast amount of potentially-useful data about products, including their origin, destination, size, and contents. Companies can maximize their supply chains and get more out of their facilities by analyzing all this data and turning it into valuable information that can assist with decision-making.
Big data is essential for ensuring that the AS/RS are functioning effectively since it allows for the optimization of various automatic handling equipment activities by providing vital information like sales data, for example.
The different types of warehouse automation include:
Goods-to-person is the most-used procedure for the reduction of congestion and maximizing efficiency. This section consists of carousels, conveyors, and vertical lift systems. When they are applied properly, they can rapidly increase the speed of warehouse picking to great effect.
Lightweight products are stored within the system and transported automatically for picking by the operator. This reduces walk time and offers accurate pick and inventory data.
Goods-to-person can be easily paired with picking technologies like artificial intelligence- powered robotics, providing fully-automated solutions for piece picking. They are easily scalable to meet and match a company’s growing demand.
The workstation screens show the exact item that is required by the operator. Order errors, that are often a challenge in high-demand and high-speed environments, are minimized.
Goods-to-person procedures provide many benefits and are usually opted for because of their efficient use of space, dynamic functionality, integration with other technologies, and their elimination of order errors.
Other advantages of goods-to-person systems include the integration of warehouse software, storage consolidation, better space utilization, and increased operational uptime. When dealing with goods-to-person technologies, factors that need to be considered include peak season needs, facility layout and space, automation system integration and technology, floor slab integrity, production rates, and the future objectives of the business.
They are also known as mobile robots. They are not bound by a fixed range of movement. This means they are self-contained and they can move along a surface, space, or line. They are not the same as a robotic arm which consists of joints and links to a base. However, in most cases, the two are combined. They serve as a platform to attach robotic arms so that they can carry out versatile functions like scanning, remote handling, and probing.
The design of automated guided vehicles is very complex as compared to that of robotic arms. Besides the issues of locomotion, there are many other aspects to consider such as path planning, perception, localization, and motion control. Automated guided vehicles are classified into the following categories.
This is a robust, flexible, and accurate automation solution that was made to meet the requirements of producers and operators of automated guided vehicles. Their advantages are that they are flexible and scalable.
These are defined as automated guided vehicle navigation systems in a forklift. They are mostly used to stack pallets at different heights and are suitable for ground-level lifting of pallets.
Automatic guided vehicles (AGVs) are load carriers that move over a facility's floor without a driver or operator on board. They are computer-controlled and wheel-based. Software-based guidance systems as well as sensor-based guiding systems control their movement. AGVs offer safe load transportation because they follow a predetermined course, accelerate and decelerate accurately, and have bumpers that automatically detect obstacles. Transportation of raw materials, work-in-progress, and completed items in support of robotics manufacturing production lines, as well as storage/retrieval to support picking in distribution and warehousing applications, are typical uses for automated guided vehicles (AGVs).
These are also known as the automated guided cart. They function by driving below a basket and slightly lifting it. They perform their duty at the destination without any intervention. Their use is mainly in hospitals. They are used for the delivery of medical supplies, food, and linens.
These are also known as tagger-guided vehicles. They are used to pull trailers or carriers that are undriven. They can handle multiple loads as compared to underride AGVs and forklift AGVs; the reason behind this is that these load-carrying vehicles do not have to perform any additional lifting exercise. However, towing automated guided vehicles are used solely for transport. They are not able to position the loads to their designated locations.
These automated vehicles are made for the transportation of palletized or unitized goods. They do not lift the load from the ground. This is done by other equipment such as forklifts, conveyors, and cranes.
These are also known as tunneling automated guided vehicles. Their main use is the transportation of goods to an assembly point. With them, navigation is very easy. This is because they are maneuverable, meaning they can orient and fit into assembly stations.
These are used mostly in steel and paper mills. This is where the rolls of products that are finished are transferred for distribution or storage. They are equipped with more safety equipment as compared to other types of automated guided vehicles and they also feature very robust construction.
hese are also known as small load carriers. Mini automated guided vehicles are meant to transport small parts and work in fleets or swarms. They have great flexibility and can move at high speeds. Their locomotion consists of a system that maintains their stability and minimum turning of the radius. They are commonly used in selective racking systems.
Autonomous mobile robots are made in such a way that they automatically move without anyone on board to pilot them. They are capable of performing various duties due to their use of sensors. These sensors help AMRs to understand their environment and interpret it in a way they can comprehend. Overall, the main reason for using autonomous mobile robots is to minimize repetitive actions, such as moving pallets from one place to another. As a result of their use, operators will have more time for tasks that require greater attention.
AMRs and automated guided vehicles (AGVs) have many similarities, but they also have some key differences. The biggest of these distinctions is flexibility. AMRs are not required to follow rigid, predetermined routes like AGVs. In contrast to AGVs, autonomous mobile robots choose the most effective path to complete each job and are built to collaborate with humans during picking and sorting activities.
The use of autonomous mobile robots comes with great advantages such as:
Another advantage of using autonomous mobile robots is that there is improved safety. This is because they have built-in cameras and sensors which help them to define and interpret their environment and avoid collisions.
Robotic arms employ “machine learning" to delve further into distribution and increase its productivity. Automated picking systems are being introduced into labor-constrained warehouses due to advancements in technology. As technology advances and labor-strapped logistics operators strive to automate in order to meet rising demand, more robots that can pick up individual things are being used in warehouses. Robotic arms controlled by software are being used by businesses to sort apparel and e-commerce packages, pack industrial supplies and bread, and, in certain circumstances, and for selecting electronics and consumer goods from bigger bins to prepare orders for delivery.
Technology won't soon replace human jobs, according to experts. However, the most recent developments demonstrate that warehouse robots are developing as the computer vision and software that direct them advance, enabling them to take on additional duties that have previously been performed by people.
As an example, in its IMTS 2022 display, KUKA ROBOTICS will introduce "Sensitive Cobotics," which it refers to as the automation of the future in the shape of its new LBR iisy cobot. The LBR iisy rapidly and simply integrates into any system as ready-to-use automation. Robotics manufacturing applications range from controlled, pre-determined production procedures to open, unstructured work settings with variable working circumstances. Any robotics manufacturing application can rapidly and effectively incorporate the collaborative robotic devices.
In accordance with pallet configuration, a robotic palletizer may handle one or more units at once and arrange the items in a variety of layers on a pallet after taking them off a conveyor. Different pallet designs and product varieties may be easily accommodated by robotic palletizing technologies.
Additionally, palletizing and depalletizing robots can be trained to manage several SKU infeeds on a single line. The robot can choose and position different SKUs on various pallets by using information sent to it by vision systems. Depending on the stacking patterns and needs, a single robot choosing a single product at a time can palletize at a pace of 8 to 30 cases/min. If the robot is picking rows of products or whole layers, the rate can increase even further.
Although SCARA and articulating arm robots are perhaps the most well-known types of robots on the market right now, gantry manufacturing robotics are used for completing large tasks in a small amount of area. Gantry robots are manufacturing robots, also known as Cartesian robots, that are used in automation assembly lines and automation production lines, but have not been taken seriously as robots. This is changing, however, as a result of their straightforward construction, low cost, scalability, and their motors and control software options.
96% of the space and dimension of a cubic work environment can be used by gantry robots. They are frequently hung from an X or X/Y axis beam on a solid framework, just like their eponymous and more-famous larger relative, the gantry crane. X, Y, and Z are typically used to define coordinates in three axes. Three degrees of mobility are possible due to the right angle arrangements of each axis. The inclusion of a second member for additional support at one or both ends further distinguish gantries. Gantries can be easily scaled to enormous sizes in all three axes, unlike arm-style robots. Gantry robots are best suited for tasks when minimum extra orientation is required, or if the pieces may be arranged before the robot picks them up.
The benefits of a Cartesian gantry robot include:
The drawbacks of the Cartesian gantry robot include:
These are systems that have to do with the retrieval and storage of cargo in specific locations within a warehouse. They are made and designed in such a way that they get the materials automatically. Therefore, they can perform these tasks on their own and remove the need for employees or operators to perform these tasks. Automated retrieval systems are present in many configurations depending on the type of operation the warehouse is based on. They may utilize vertical lift modules, carousels, shuttles, or cranes. Automated storage retrieval systems come with their benefits which are as follows.
With a pick-to-light system, an employee must first scan a barcode to read a specific order associated with this barcode system. Workers are then directed to the location of the storage rooms where their ordered things are kept using gadgets that employ light. The products to choose from to satisfy the order will then be shown by the lights on the racks.
With a pick-to-light system, an employee must first scan a barcode to read a specific order associated with this barcode system. Workers are then directed to the location of the storage rooms where their ordered things are kept using gadgets that employ light. The products to choose from to satisfy the order will then be shown by the lights on the racks.
Pick-to-light systems and put-to-light systems are simply the opposite of each other. The workers scan the barcode as the first step and the lights mounted on the rack will show where the material is to be selected from in storage under a pick-to-light system; with a put-to-light system, lights are used to direct workers where to put items. The advantage of pick-to-light and put-to-light systems is that there is an increase in productivity. It is estimated that the use of pick-to-light systems can cause an increase in productivity by about thirty to fifty percent. There is also an improvement in picking accuracy. Workers are less likely to make mistakes. This is because they no longer have to manually determine the location from which to place or pick items. Another advantage of these systems is that the training costs are reduced. This is because these systems are intuitive and simple. The whole training process for these systems can take as little as 30 minutes.
This is a method that is used to communicate verbal commands to aid factory employees in fulfilling their orders and duties. Usually, voice picking and tasking systems are merged with enterprise resource planning software or warehouse management systems. As soon as an order comes in, the voice picking and tasking system will automatically determine the needs of the order.
Afterward, they will verbally deliver the message to the employees who take the commands from a headset. The employee is directed to the exact location of the item to be picked and told the amount or quantity required. Employees can converse with the system to confirm locations as well as other quantities. Voice picking and tasking systems come packed with numerous benefits and some of these are:
This is a method of eliminating the manual labor element by automatically selecting materials that are on a conveyor system and directing them to locations that are specified in the warehouse. Automated sortation systems make use of various technologies to implement this. They use sensors, barcodes, and scanners. Generally, automated sortation systems can be categorized into two groups, namely case sorters and unit sorters. Case sorters can handle whole totes, while unit sorters are capable of handling only individual items. Automated sortation systems also come with their benefits. These benefits are:
These are robots that are made in a way so they may work side by side with human workers. Collaborative mobile robots are used for the reasons of minimizing errors, maximizing operating speeds and efficiency, and freeing up employees’ time for other tasks. It has been noted that the use of collaborative mobile robots has a direct impact on efficiency. They are used in various operations such as palletizing, packing, inspecting, and picking.
Technically, drones are robots which do not have advanced onboard computers and are used to manage inventory. Drones scan barcodes to perform warehouse counts, notify the staff of products that require restocking and goods that are positioned in the wrong. They are used for deliveries as well by some warehouse automation companies who are increasingly exploring the use of drones.
This chapter will discuss the reasons to automate a warehouse and how to automate it.
An inefficient warehouse has a big negative impact on the experience of the customer. Warehouses that are automated are capable of doing more with less and they thrive under increasing customer demand. The use of automation in warehouse operations provides a large number of advantages ranging from minimizing errors to running more efficiently.
Some of the benefits frequently cited are that operational costs and labor are reduced, service to customers is improved, there is minimal human error, the employees are satisfied, resources are utilized better, errors due to shipping are also reduced. There is improved order fulfillment due to material handling automation and coordination.
The automation of a warehouse needs a well-written project plan. There is a need to consider all the stakeholders, do a risk assessment, create a project schedule, and also perform an analysis of deliverables and goals. Initially, there must be the formation of a support team and the assignment of a project manager. The team will carry out the project schedule and create a timeline as well as a deliverables calendar. There is a need for implementation support plans.
These will have feedback from all management levels, warehouse managers in different locations, and corporate leadership. Finally, there is a need to choose automation that best suits the business being run. There is a need to do thorough research when doing automation options. Different automation processes must be studied and considered. The process of warehouse automation can be broken down into the following steps.
Formation of an implementation team - This has to be a committee of stakeholders who have more knowledge and experience on the current capabilities, challenges, and performance of the warehouse. The team must be able to understand the available gaps in technology that require to be filled. There can be additions to this team of experts, who should have great experience in supply chain and demand automation with relevance to the operations of the warehouse.
Collection of critical data – For the automation of a warehouse to be successful, it has to depend greatly on the supply chain operations and critical business operations. Before there is implementation of automation technology, the current data infrastructure and collection procedures have to be evaluated. This is because there is a need to assign ownership of that data to information technology stakeholders that are skilled in this area.
Evaluation of inventory controls – The control of inventory is found at the center of warehouse operations. Standard operating procedures have to be determined first before the implementation of the warehouse automation solution. These standard operating procedures have to be included for shipping, purchasing, receiving, inventory loss, and customer satisfaction. To be able to measure the success of automated procedures and processes, the key performance indicators must be defined.
Implementation of a warehouse management system – The warehouse management system has software that can track and help manage inventory, minimize labor costs, manage warehouse operations, and improve customer service. The system selected should be able to function well with current software and support mobile devices.
Determining the best automation solution – Determining a warehouse automation solution is very essential. It has to align with specific company goals and meet customer demand.
The best practices in warehouse automation include:
Ensure that warehouse automation solutions you select are able to integrate with a WMS platform. Look for a solution that allows you to automate your capabilities to handle inventory controls, maintain inventory, track and report on labor costs, and connect dashboards. Read up on WMS features and the distinctions between warehouse management and inventory management.
Invest in solutions that are scalable since technology should grow with your company. The system needs to take into consideration the addition of future warehouses, personnel, tools, and supply chain alliances like third-party logistics providers or drop shippers.
Start with a system that automates data collection, transport, and storage no matter what type and degree of automation technologies you're exploring for the future. A low-cost, low-risk road to automation is created by combining cloud-based technologies with portable barcode scanners. This environment will enable you to gather crucial warehouse performance and inventory data and store it in a consolidated cloud database for further analysis while also removing human error from the equation.
Cycle counts are a crucial component of any warehouse management system and are used to compare inventory levels to inventory data records. If you have automated data gathering systems in place, you may use mobile barcode scanning or RFID sensors to automate continuous cycle counts. Then, you may check for inventory inconsistencies using dashboards.
Since receiving is where warehouse data collection begins, you would like a system that can gather as much information as possible up front to help guide warehouse activities. Determine the dimensions, classifications, and packing of the arriving goods before creating rules in the WMS for how to manage, store, and allocate resources.
For many physical automation technologies, such as GTP and AS/RS systems, AGVs, and sortation systems, to be effective, the warehouse must have a precise layout and plenty of room. To make current warehouses and distribution centers more suitable for automation technologies, think about redesigning their designs. Work with solution providers, architects, and contractors who are aware of your particular needs. This evaluation should be budgeted for in your implementation strategy.
As technology has advanced and grown, companies have a wider range of warehousing technologies to choose from than has ever existed. From logistics automation robotics and depalletizing robotics to storage and order picking systems, these 21st Century automatic systems are a cost effective method for handling products and assisting with assembly line automation and supply.
The market for robotics integrators and logistics automation is filled with many companies that have varying technological skills and expertise. The key to the many robot integrators is the design of their services, their type of software, and their system of controls. Many companies claim to have the tools for robotic integration but may lack the expertise. Customers in the market for warehouse automation systems have to carefully investigate the different producers and select one with the expertise to meet their needs.
The focus of Formic is to make robotics integrators easy and accessible to save time, money, and labor costs. The company’s robotics systems provide an unlimited supply of labor saving logistics automation systems using robots and automation technology. Formic provides labor saving robotics for advanced robotics manufacturing, consumer packaging, and other industrial uses. The company makes it possible for companies to improve their manufacturing capabilities at minor risk.
Dematic is a supplier of automated technologies and software that are used in manufacturing, the supply chain, and distribution centers. The company offers an automated storage and retrieval system for delivering and storing inventory. Dematic has the latest technology in robotic mechatronics, guidance systems, and AI for automatic palletizing and depalletizing operations to eliminate labor with fully robotic systems. Being a full range company, Dematic provides robotic technology to small, medium and large sized companies to help improve product flow and production.
Vanderlande has vast experience in warehouse logistics automation systems and automated material handling systems and offers a wide range of solutions for parcel center logistics automation. The company’s list of integrated solutions provides fast, reliable, and innovative technologies to assist its customers improve operational processes. The recent main focus of Vanderlande has been in the area of e-commerce where it has become the first choice in logistics automation systems.
Knapp is a leading provider of warehouse robot integration systems and logistics software. The company installs automation solutions for small item, variability fulfillment operations, and various forms of AGV systems. The main goal of Knapp is to offer innovative methods for robotic integration as part of warehouse automation that targets the specific requirements of customers. Using its highly trained team of experts and engineers, Knapp designs, implements, and perfects warehouse solutions for all types of customers and conditions.
The goal of SSI Schaefer is to offer end to end automated systems for large scale integrated warehouse automation. The wide range of warehousing and supply chain solutions offered by SSI Schaefer include flat pack picking, single piece picking robotics, and AGV and AMR robot integration. The company has automated solutions for picking, conveying, shipping, storage, and material handling using customized technologies and systems.
Emerging technologies and robots have helped various businesses and their supply chains by increasing the timeliness and accuracy of product information. Warehouse robotics mostly refers to the implementation and continued use of systems that are automated. Historically, managers used automation for minimizing headcount. Now, enterprises are battling to keep adequate people on their teams since their labor costs are going up. Industrial robots have been around for a long time now but were greatly limited in terms of their capability and equipment.
The emerging warehouse robots make use of artificial intelligence in order to navigate a facility well. They can collaborate with people and pick or drop off items. There are various types of warehouse robotics systems that are used and some of them include facility management robots that can cut lawns or mop floors. There are autonomous drones that can reach tall shelves and even fly to deliver an item. There are also static robotic systems for picking, pulling, dropping, and even packing orders in boxes or specified containers. Robots play a very important role in warehouses and the duties they perform are listed below.
Sorting – Sorting seems like a simple operation for workers but its automation process is more complex. The warehouse's automated robots consist of sensors, cameras, conveyors, arms, and software codes that help them to identify a specific item and send them to the exact location for storage, retrieval, or disposal. Artificial intelligence sorting systems merge with these picking robots to correctly sort batch-picked items into required order elements.
Packaging – Warehouse automation consists of bagging machines and automated robots with customization software that help to decrease the time taken to pack goods. Some of these features work with length and weight dimensions and can compute the ideal size of the carton required for specific orders and then direct associates to the correct process for packaging items.
Transportation - There is often a great need for carting items from one side of the factory to the other. Warehouse automation systems will minimize the time required by the worker to perform this chore and provide them more time to execute more important tasks. Robotics in warehouses such as automated guided vehicles help minimize associated stress and the human footprint associated with manually performing this duty. They can transport order items from their zones to areas where they are sorted. They have unique purposes, serving as conveyors to transport bins, boxes, and other items, or as monorails to move items such as pallets around.
Replenishment – Warehouse robots can replenish workflows. Therefore, they minimize backorders and stockouts through automated re-ordering procedures. They can monitor inventory levels and send out notifications if there is a drop below a minimum threshold.
As a result, the following are the developments in robotics and automation that are enabling the modern warehouse:
In the first quarter of 2020, investments in warehouse robotics companies surged by 57% to more than $380 million. In a post-pandemic economy and in places like Japan, where there is a scarcity of workers, the use of warehouse robotics will continue to gain traction.
Cobotics is the term for a human-robot collaboration; cobotics combines robotics with cooperation. Cobots, which are robots made to collaborate with people, do not take the position of people in the workplace. AMRs are cobots used in warehouse automation that can scan their surroundings. By detecting changes in its 360-degree range of view, this cobot AMR can prevent accidents with people and human-operated equipment and can safely drive backward when required.
To meet the demand for adaptable warehouse management and automated technologies like autonomous robots, service-based warehouse marketplaces are expanding. Producers and service providers who sell automated equipment and systems are being challenged by businesses that provide subscription-based, completely automated warehouse solutions.
Drone fleets that are intelligent, driven by cutting-edge algorithms, and integrated with cloud-based warehouse management systems can help manage inventories within warehouses. To manage inventory and automate processes like cycle counting, some warehouse drones come with vision sensors or barcode scanners.
Blockchain technology is a safe, automated network that employs cryptography to establish data transfers in blocks on a public digital ledger. However, this technology is still in its infancy. Because of the sophisticated data authentication, validation, and transparency offered by blockchain technology, these processes have an impact on warehouse operations and inventory management. With shared data storage available to everyone within the secure network, blockchain databases might enable every player in complicated supply chains to connect and exchange permanent, automatic records for every transaction done.
The most well-known company adopting GTP systems driven by AGVs and AGRs is Amazon. The fleets of autonomous robots they utilize can fill mobile shelving units with stock and move them to predetermined destinations. As a result, employees may select orders with little walking or other activity required.
Automated distribution centers and warehouses currently employ autonomous robotic forklifts. Automated delivery trucks that transfer merchandise between warehouses, manufacturers, and retail outlets are anticipated to travel farther up the supply chain.
Regardless of who offers the product, there is a high demand for quick online delivery due to the "Amazon effect" of one- or two-day shipping. The need for same-day shipment will keep pushing warehouse automation, which enhances accuracy and efficiency of automated packing and shipping processes while speeding up order fulfillment operations like picking.
Industrial automation robotic floor cleaners that can maneuver intricate warehouse layouts are now on the market. In order to safely cleanse and disinfect high-touch interior environments like distribution centers and warehouses with sanitizing chemicals and UV rays, a new generation of autonomous mobile cleaning robots is already emerging.
This is now possible because of advancements in sensor technologies, cloud databases, and Internet of Things applications. Your system receives extensive information on the location of the equipment, scheduled maintenance, and accident alarms via telemetry from onboard computers.
Machine learning (ML) and API technologies are enabling automation solutions to link with ERP suites to build an end-to-end automated business platform. Additional advancements in automation and ERP software will free up back-office workers to work on other tasks that add value, are creative, and are customer-focused.
RFID sensors continue to be a driving force behind new IoT applications that optimize supply chains and warehouse operations, even if they aren't exactly considered an emerging technology. IoT technology increases warehouse visibility by offering real-time location information on inventory and equipment. RFID sensors' portability, cost, and real-time inventory tracking capabilities improve data collecting across systems.
The development of cloud-based databases and apps that can gather, analyze, and store huge datasets that are readily available will advance data analytics for warehouse operations.
This chapter will discuss the applications and merits of warehouse automation.
Warehouse automation has numerous uses and applications across different industries. They are used in robotics for manufacturing in aerospace, automotive, and agricultural industries as well as in medical facilities.
Some of the practical uses of their work in different industries include:
The advantages and benefits of an automated warehouse system are many. Modern warehouse technologies are scalable and much easier to work with in comparison to older automation solutions like conveyors.
Conveyors are fixed in place and bulky. The operators of warehouses can rent more robots to accommodate the increase in demand during peak periods and, later on, return them when the rate of demand declines. There is no need for infrastructure changes when dealing with collaborative mobile robots. Some other benefits of warehouse automation are the increase in productivity and minimum worker strain and fatigue.
There are fewer injuries incurred. Additional advantages of an automated warehouse include reduced operating costs, increased accuracy, and fewer shipping mistakes. There is space optimization in automated warehouses to maximize the use of vertical space by storing items in locations that cannot be accessed easily by humans.
The use of drones and some retrieval solution systems makes it much easier to access these much higher storage locations. The investment in the automated warehouse is a good financial decision because there is a lot of money saved from reduced errors, there are fewer injuries incurred, and there is increased productivity.
Warehouse automation is the process of using automated technology to take the place of repetitive operations. The major objective is to eliminate time-consuming and labor-intensive tasks. As a result, employees are better able to concentrate on crucial jobs like quality control. However, warehouse automation refers to the use of software to replace tasks that are now done manually and does not always entail the employment of robots or other devices. Over time, the use of automated warehouses has immensely benefited civilization. Robotics manufacturing is used by the automotive industry and retail, which are some of the sectors that use this emerging technology. They have seen significant changes with the advent of artificial intelligence that has dramatically increased worker productivity and efficiency.
An automatic screwdriver is a piece of equipment that automatically inserts screws into a product during assembly and production. Since every production operation is unique and requires a...
An automation system is an integration of sensors, controls, and actuators designed to perform a function with minimal or no human intervention. The field concerned in this subject is called Mechatronics which is an...
Collaborative robots, also abbreviated as Cobots, are the newest technology in robotics. They have changed the automation world significantly. These robots can work safely together with workers, hence are...
An industrial robot is an autonomous system of sensors, controllers, and actuators that executes specific functions and operations in a manufacturing or processing line. They operate continuously through repetitive...
Robotic system integrators are companies that provide assistance in automating a wide range of applications. They help design robotic technologies that best suit the needs of an operation for a company and solutions as...
An AGV forklift is a driverless self-operating robotic device that has the ability to carry, lift, retrieve, and place loads for easy transfer from one location to another. An automatic guided vehicle (AGV) forklift is a computer controlled mechanism that...
Automated guided vehicles (AGV) or mobile robots are types of guided robotic systems that are not bounded by a fixed range of motion. Rather, it is self-contained and can move along a line, surface, or space...
An autonomous mobile robot (AMR) is a self-propelled self-powered mechanism designed to perform repetitive tasks or organizational functions using an internal guidance system. They are able to navigate their...
A belt conveyor is a system designed to transport or move physical items like materials, goods, even people from one point to another. Unlike other conveying means that employ chains, spirals, hydraulics, etc...
A bowl feeder is a mechanism for supplying small parts and components to a production line or for sorting bulk items for rapid use. A self contained bowl feeder system has a bowl that sets on a spring loaded base that moves vertically...
A conveyor system is a method for moving packages, products, supplies, parts, and equipment for production, shipping, or relocation. The different types of conveying systems include pneumatic, screw, belt, and roller. The construction of individual systems depends on the materials...
Palletizing is the process of putting items on a pallet. The process of emptying the loaded objects in the reverse pattern is known as depalletizing. A pallet is a flat, square-shaped platform used to transport and...
A pallet stacker is a machine designed to assist the user in lifting, moving and handling palletized materials with ease. A pallet itself is a flat and horizontal structure used to support goods in a sturdy fashion...
A palletizer is an automated material handling machine used to stack and orient several individual products into a single load for a more convenient and economical method of handling, storage, and shipment. Palletizers are usually part of a bigger packaging process...
Pneumatic conveying is a method for transferring bulk materials, like powders and granules, using compressed gas or air, from one processing center to another. Material is moved through an enclosed conveying line or tube using a combination of pressure differential and airflow from a blower or fan...
A robotic palletizer is a type of palletizer that employs a robotic arm to pick, orient, and place individual products and arrange them into a single stack of load. They are the next generation of palletizers, and they will supersede conventional palletizers...
Roller conveyors are a type of conveyor belt that allows objects to skate on its surface by using rollers, which are equally spaced revolving cylinders. They transport stuff from one location to another...
Screw conveyors, or auger conveyors, are industrial equipment used in transporting bulk quantities of granular solids (e.g., powder, grains, granules), semi-solids, liquids, and even non-flowing materials from one point to another...
Vibratory conveyors are material-handling equipment used to transport fine to coarse-grained bulk materials. These vibratory conveyors are strong conveying equipment utilized for bulk commodities with fine to coarse graininess...
A vertical conveyor is an engineered mechanical method for moving goods, products, supplies, parts, and components from a lower level to a higher level or from a higher level to a lower level. They are...
Vibratory feeders are short conveyors used to transport bulk materials utilizing a controlled vibratory force system and gravity. The vibrations impart a combination of horizontal and vertical acceleration through tossing, hopping, or sliding-type of action to the materials being handled...
In 1954, when Arthur "Mac" Barrett, of Barrett Electronics Corporation, unveiled the first AGV, he named it Guide-o-Matic and described it as a driverless vehicle...