Automation Systems
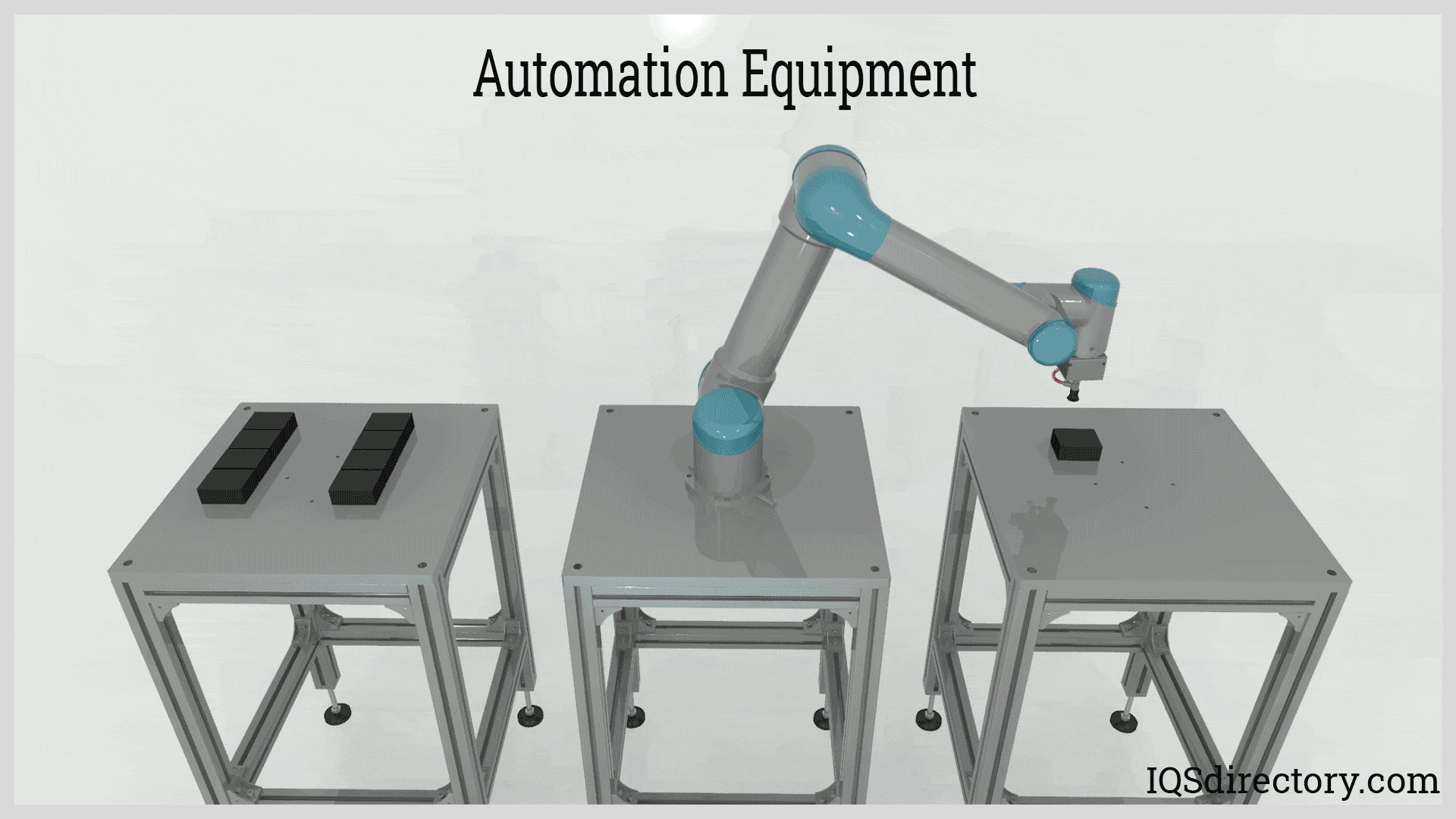
An automation system is an integration of sensors, controls, and actuators designed to perform a function with minimal or no human intervention. The field concerned in this subject is called Mechatronics which is an...
Please fill out the following form to submit a Request for Quote to any of the following companies listed on
This article contains everything you will need to know about automatic screwdrivers and their use.
You will learn:
An automatic screwdriver is a piece of equipment that automatically inserts screws into a product during assembly and production. Since every production operation is unique and requires a different type of automatic screwdriver system, the sizes, designs, capabilities, and configurations of automatic screwdrivers vary with each type having the single purpose of inserting screws. Automatic screwdrivers provide the speed, accuracy, quality, and efficiency that is required by modern production operations.
The process for screw driving using an automatic screwdriver involves picking screws that are fed to a screwdriver unit that securely attaches the screws to an assembly. They consist of a screw driving unit, controller, and screw feeder, which work together to perform the attaching or screwing process.
The use of an automated screwdriver is based on a set of assumptions. If an inordinate number of staff members are involved in the screw driving process, the use of an automatic screwdriver is a labor saving solution. Additionally, if a process repeatedly uses the same type of screw for an operation or process, an automatic screwdriver is an ideal cost saving method for improving production efficiency.
Automatic screwdrivers are an essential part of production operations for bulk productivity, process rate control, and flexibility. They operate quickly, reliably, and efficiently and require little to no maintenance. The outstanding characteristic of automatic screwdrivers is how rapidly they operate without the need or intervention of workers. Automatic screwdrivers consistently place, attach, and secure thousands of screws with exceptional accuracy and programmed torque.
When discussing the types of automatic screwdrivers, the two factors that need to be considered are in regard to the mechanism of an automatic screwdriver and its delivery system, which includes robotic arms. Automatic screwdrivers are available in as many varieties as there are DIY electric screwdrivers with each type having features that fit into an automatic screwdriver system. The selection of the delivery mechanism is influenced by the type of product and the size of the screwdriver.
The five automatic screwdriver systems that are described below are a small representation of the many types of automatic screwdriver systems with custom designed systems being developed to fit specific assembly processes or applications. Whether a system has a single automatic screwdriver or multiple ones is another factor that differentiates the different types. Additionally, manufacturers are constantly exploring the programmability for automatic screwdrivers, a factor that further separates the various types.
A gantry type automatic screwdriver moves horizontally along the X Y axes using a servo motor drive and sliding table. The structure has X axis rails and Y axis bracket rails for positioning assemblies. Gantry automatic screwdrivers are programmable with automatic screw feeders. They can have multiple screwdrivers that are positioned by the movement of the X axis rails. Pieces to be connected are placed on the Y axis platform that moves in accordance with programmed instructions.
Although a gantry automatic screwdriver connects assemblies automatically, it has an operator that places materials and unloads it. Unlike automatic screwdrivers that are part of an assembly line, this form of automatic screwdriver is portable and not attached to a robotic system. Gantry automatic screwdrivers can be adjusted for operating with any type and size of screw, which makes it flexible and adaptable.
A key feature of gantry automatic screwdrivers is their torque monitor, which is a necessity for all forms of automatic screwdrivers. A torque monitoring system allows users to adjust torque specifications to the requirements of the screws being used and the requirements of an assembly.
Automatic screwdriver robots are designed to perform the repetitive tasks of screwing and unscrewing of bolts, nuts, or screws. They are programmed to complete such tasks with precision accuracy and efficiency to help reduce labor costs and increase productivity.
The parts of an automatic screwdriver robotic system include a robotic arm, a screwdriver unit, vision system, control system, and a user interface. The robotic arm is responsible for the movement and positioning of the screwdriver and is designed with joints that allow for smooth movement. Screwdriver tools for robotic screwdrivers take different forms from ones with standard screw settings to ones that are customized to meet special applications.
In the modern era, vision systems have become a necessary component of robotic systems. Such systems consist of cameras and sensors that identify the location and orientation of the screwdriver for accuracy and alignment purposes. The visual systems of robotic screwdriver systems are similar to evaluation comparators that are used for product quality identification.
As with all technological equipment, the final portion of an automatic screwdriver robot is its user interface, which allows users to program the torque, type of screw, program movements, and the operating sequence of an automatic screwdriver robot. Computer interfaces for automatic screwdrivers take several forms with the majority being designed for specific applications and processes.
The cost savings and labor-saving aspects of automatic screwdriver robots have radically increased their use as manufacturers have learned how economical they are to operate and how easily they fit into processing assemblies.
The use of cobot systems has been rapidly growing in recent years as producers have found that the blending of staff with technology increases productivity and efficiency while improving the quality of products. Collaborative automatic screwdrivers are designed to work with people or other manufacturing applications. The introduction of collaborative automatic screwdrivers has been due to their size, low cost, flexibility, adaptability, precision, and collaborative abilities.
Unlike complex large robotic systems, collaborative automatic screwdriver systems are smaller, require less space, and are more affordable than larger systems. For a cobot system to be approved for use in a process, it must be able to fit into the existing system and be safe for operators. Innovative engineering and technological advancements have led to the development of collaborative automatic screwdrivers that are just as effective as larger versions but more practical for all types of operations.
Part of the improvement in cobot use is due to the advancements in effectors, which is at the end of a robotic arm that holds the screwdriver. Known as the end of arm tool, an effector is designed to operate at the commands of its human user and its software. It reacts to surrounding stimuli and is the aspect of an automatic screwdriver that completes the screw driving process.
With cobots, the effector is the essential part of the process and is obedient to the positioning and commands of its coworker. While the arm is programmed to position the tool and screw, the effector holds the tool in position for the completion of the process. If all the other aspects of a cobot operate properly, the effector is necessary for the final step.
A typical automatic screwdriver is capable of screwing one type of screw multiple times. The process is efficient and quick with workpieces being passed through, have screws connected, and moved on to the next process. This aspect of automatic screwdrivers is the reason for their popularity. As the use of automatic screwdrivers has increased, users have asked for automatic screwdrivers that can be used with several different screws at the same time.
Different screw geometries necessitate different feed methods and different tool heads. An automatic screw driving robot has been developed that can change feed systems and drive several tools automatically. The system is built on software that can be input with a sequence of positions. In addition to performing screw driving, the system can place workpieces, setting boards, pins, balls, and gripping components.
The system for automatic tool changer screwdriver consists of a screw driving unit with an effector that has quick release capabilities. Multiple feed units can be programmed into the system, which is determined by the number and types of different screws and can be positioned internally or externally.
Tool changing is locked into the tool station. An encoder uses a code to select the proper tool to be used for a process, which prevents the use of the wrong tool and screw. The system is designed such that manual interference shuts down the system and stops robotic motion.
The drive head for a multiple spindle automatic screwdriver is capable of driving multiple screws of different sizes and types into a part in one operation or at programmed intervals. Each screwdriver can be programmed to operate independently in accordance with the requirements of an application. The system operates with a blow feeder and can be configured for bolts, pins, rivets, and set screws.
A multiple spindle automatic screwdriver has several automatic screwdrivers mounted and positioned to bore holes in a workpiece. They are an alternative to having several automatic screwdrivers and a way to save space when there isn’t enough room. For normal operation, multiple spindle automatic screwdrivers are mounted on platen assemblies, which can be positioned on fixtures, robots, or indexing stations. Feeding units can be single or dual exit systems, are integrated into the multiple head attachment, and are combined with a single bowl feeder for one type of screw.
The purpose of automatic screwdrivers is to simplify, streamline, and automate the process of screwing. The basic parts of an automatic screwdriver are the screw feeder, screwdriver unit, and various types of control systems. The feeder sorts and dispenses the screws. The screwdriver or drivers receive the screws from the feeder and screw them into an assembly, product, component, or part. These two factors work in unison and are programmed by the controller that oversees the system and determines the rate of feed, the torque of the screwdriver, and the positioning of the screws.
The feeder for an automatic screw drive system can take several forms but has the responsibility of supplying an automatic screwdriver with screws. Feeders have a hopper for loading screws, a feeding mechanism, and a tracking system that guides the screws to the screwdriver unit. The sophistication of the guiding system is what makes a screw driving system efficient since screws have to be properly positioned in order to be screwed into a workpiece.
Screw feeders are a tabletop automated assembly located at the top of the screwdriver system designed to deliver screws to a fixed point where they are picked up by a magnetic bit or some form of vacuum assembly. They come in several sizes, lengths, and configurations such that they can easily be integrated into an application.
With a vacuum feeder system, screws are picked up by a suction tube with negative pressure and positions the screw over the screw hole. Once the screw is in position, the screwdriver moves down to fasten the screw. The feeding mechanism can feed multiple screws to a single screwdriver or have multiple tubes to deliver multiple screws to several screwdrivers as in a multiple spindle automatic screwdriver.
The screws loaded into the hopper use a feeding mechanism that separates the screws and guides them to a trackway that aligns the screws for the screwdriver. When the screws enter the screwdriver unit, they are picked up by the bit holder that uses a vacuum unit or magnetic system. The bit holder properly positions the screw for insertions into the workpiece.
Screwdriver units can take several forms, which include ones with a single automatic screwdriver, ones with several screwdrivers, and ones capable of inserting different screws. The motor of the screwdriver unit supplies the power while the clutch controls the torque, and the bit holder holds the bit. Once the screw has been positioned from the feeder unit, power is supplied to the screwdriver unit to insert screws into the workpiece or assembly.
The necessary torque for tightening the screw is determined by the control unit. Torque control is an essential part of the process and ensures that a sufficient amount of force is applied during screw insertion. The amount of torque is adjusted in accordance with the assembly or screwing function. The adjustment of torque gives automatic screwdriver systems flexibility such that they can be used for a variety of screwing applications.
The three types of screwdriver units are handheld, fixed, and movable. The handheld version of screwdrivers are the typical ones that are used for DIY projects and home use. Fixed automatic screwdrivers are ones that are used in automatic screwdriver systems and have screws fed to them. They are referred to as fixed since they are normally part of a production assembly and work as a unidirectional tool for locking screws in workpieces as they are loaded by an assembly line or manually.
Movable screwdriver units can be semi fixed or part of a robotic arm. The semi fixed type screwdriver unit can be part of a rotating system that moves in accordance with an assembly operation. They are programmed to move to various parts of a workpiece to lock screws in place. The motion of semi fixed screwdrivers is along the X and Y axis in a manner that is similar to that of a gantry type automatic screwdriver.
Robotic movable screwdriver units are highly sophisticated technologically advanced automatic screwdriver units that are widely used in manufacturing and assembly operations. Their precision capabilities make it possible to use them for the assembly of delicate and sensitive pieces of equipment and machinery. Robotic screwdriver units have a screw drive attached to the end of a robotic arm, which is the effector and makes it possible to position the screwdriver in any direction. The movement, positioning, and torque of a robotic screwdriver unit is programmed into the unit using specially designed computer software.
With automatic screwdrivers, spindles take different forms depending on the design of the screwdriver. The basic function for a spindle is the same regardless of automatic screwdriver design, which is to rotate and tighten screws. At one end of the spindle is the motor that drives the bit that tightens the screw into the workpiece. To ensure a safe and proper connection, the controller has a torque sensor placed between the motor and the spindle. Additionally, the spindle has a depth sensor to measure the depth to which the screw is driven in accordance with the programmed configuration.
Different screwdriver spindles are used for different screwing processes. Variations in spindles are dependent on the materials of a part to be screwed and the length and thicknesses of the screws. When a spindle is changed or adjusted, its parameters are entered into the control system.
Automatic screwdriver spindles have stroke compensation that regulates the end load pressure of the spindle. Variable configurations adapt to all screwdriving cases regarding stroke lengths, sensors, and drive units. Electrical or pneumatic power drives the spindle and controls its stroke such that it does not drive through the base of the workpiece.
Controllers are integrated into an automated screwdriver system. They monitor and control the screwdriving process to ensure speed, accuracy, torque, depth, and feed. Part of their work involves controlling the stroke of the spindle and monitoring communications with other aspects of the assembly process. Much like every other part of an automatic screwdriver system, controllers come in several forms and include ones that are very simple with straight forward parameters and ones with numerous interfaces for evaluation of the process. The majority of controllers, regardless of their complexity, have touch screen displays with some versions having handheld units for remote programming.
More advanced controllers have sensors and comparative cameras that ensure the accuracy of the process and serve as quality control. These highly technical types of controllers are capable of detecting errors and correcting them during the assembly process. They collect data on the insertion of screws, angle of the workpiece, the amount of torque, and the rate of the feeding process.
The rapid rate at which an automatic screwdriver system operates necessitates various controls that monitor each aspect of the process. The feeding, picking, insertion, and screwing processes are continuously and constantly monitored down to the smallest detail. If the feeding hopper is empty, the automatic screwdriver system stops and restarts when the hopper is refilled.
An effector is a mechanism that is associated with robotic arms and is located at the end of the arm in a way that is similar to a hand. There are an endless number of uses for effectors that run the full gamut of industrial functions. Automatic screwdriver effectors are just one of the many types of effectors. In essence, without an effector, a robotic arm is useless. A common use of effectors for automated screwdriver systems is as a part of a collaborative process or CoBot.
Effectors can be highly sophisticated and programmed with various functions that ensure the quality and efficiency of the screwing process. They can be programmed with error detectors and the ability to handle multiple sized screws such that one effector can apply multiple screws in a single cycle. The two functions of an effector for screwing involve grasping the screw and driving it into the workpiece.
The grasping portion of an effector has two fingers and a joint for roll, yaw, and pitch using a V shaped groove, which aligns the screw. The driving part of an effector is above the gripper and has two rigid links and a flexible one. A link guide prevents the flexible link from swinging and provides up and down motion. The robotic arm with the gripper and screwdriver of the effector work together to connect, insert, and tighten the screw.
The key to the effectiveness of an automatic screwdriver system is the power provided to the screwdriver, which can take different forms depending on the design of the system. The selection of an automatic screwdriver ensures that connections are made correctly. Accuracy, timing, speed, and torque play an important role in the choice of the power for an automatic screwdriver.
The first factor to consider when choosing an automatic screwdriver is the type of power system that will be used with the main types being electric and pneumatic. Both power systems have their advantages and are commonly used for high production operations. Although some companies prefer using manually operated screwdrivers, the majority of manufacturers are changing to automatic screwdriver systems for their efficiency and accuracy.
Electric automatic screwdrivers can be programmed for speed and torque, which can be changed as the need arises. Unlike pneumatic automatic screwdrivers, electric automatic screwdrivers make it possible to adjust the screwdriver during a cycle. RPMs can be increased or decreased based on torque sensing feedback from the controller. Screw joints are programmed into an automatic screwdriver in regard to torque and degrees of angle for a snug fit.
The torque of an automatic electric screwdriver is measured using the motor load, which is an extremely accurate and low-cost measuring technique. The wide use of electric automatic screwdrivers is due to their accuracy and controllability. The many positive features of electric automatic screwdrivers make them more expensive than pneumatic automatic screwdrivers due to their engineered precision control.
Highly efficient and accurate electric automatic screwdrivers have a transducer that measures the calibrated torque that is applied at a joint. The transducer provides feedback to the controller, which uses the data to detect and trace tightening errors. Unlike clutch automatic screwdrivers, transducer electric automatic screwdrivers allow users to set torque according to the requirements of the job and the type of screw.
Pneumatic automatic screwdrivers use vane air motors that deliver compressed air to power the screwdriver. A mechanical clutch turns off the screwdriver when it reaches its preset torque value. The wide use of clutch type screwdrivers is due to their exceptional accuracy and precision for tightening. Clutch type screwdrivers are easily adjustable and have a transducer to change torque. The use of pneumatic automatic screwdrivers is based on their accuracy and high power to weight ratio. They are a low maintenance alternative to electric automatic screwdrivers and can fasten hard and soft joints.
Constructed for production environments, pneumatic automatic screwdrivers are durable, allow for speedy assembly, and are affordable, compared to electric automatic screwdrivers. They can be used in any level of automation with automatic screw feeding systems. Pneumatic automatic screwdrivers can fit into any size manufacturing setting and offer a cost effective fully automated production solution.
The screw feeder provides a constant supply of screws to an automatic screwdriver unit and reduces cycle times. The feeding system delivers screws to the screwdriver tip in the correct position and ready for fastening. The complexity of screw feeders is due to the difficulty of picking and placing screws. Smaller screws increase the difficulty of picking and placing, which necessitates more attention to programming the feeder. The process of placing a screw becomes more challenging when the screwing process is added to an assembly operation.
Screw feeders deliver screws to a fixed point where they are picked up by an automatic screwdriver using a magnetic bit or vacuum. They come in several sizes, lengths, configurations, and are made of steel, stainless steel, and aluminum. Screw feeders have variable or stepped pitch, a tapered diameter, and the ability to handle mass flow.
Bowl, rail, and hopper are three of the basic types of screw drive feeders. The choice of screw feeding method is determined by screw size, screw orientation, the interface, and loading method.
Bowl feeders, known as vibratory bowl feeders, are a common form of part feeding device used to orient parts for an assembly operation. They are widely used for feeding bulk amounts of components to machines, in this case, automatic screwdrivers. The use of vibratory bowl feeders is due to their ability to handle a wide range of part sizes while taking up very little space.
Electromagnets in a bowl feeder use vibrations to align and feed screws to the screwdriver unit. The electromagnets create the vibrations, which are converted into mechanical vibrations. A conveying track on the feeder moves screws to the screwdrive unit.
Hopper feeders, that are known as screw conveyor hoppers, consist of a hopper and screw conveyor or rail. One screw at a time is released from the hopper using vibrations, pneumatics, or a simple mechanical mechanism. The screw is properly oriented and sent through a feed tube or along a rail to the tip of the screwdriver where it is attached to the workpiece. Once a screw is inserted and placed, the hopper releases another screw in a continuous and uninterrupted fashion.
With a vacuum automatic screwdriver system, screws are picked up by a vacuum with negative pressure and positioned over the screw hole. The screwdriver is fitted with a nosepiece from the vacuum pump system to receive the screw. The nosepiece sucks in the screw and holds it steady for attachment. Each step of the process happens quickly and increases the speed of fastening and decreases assembly time.
Unlike magnetic systems that can only work with ferrous metals, vacuum systems work with non-magnetic metals and plastics. Nose pieces and hoses are adjusted to fit the heads of several types of screws. Vacuum pickup systems are ideal for automated screwdrivers due to their precision in placing screws for fastening. Vacuum feeders are normally used where access to the fastener is tight and hard to reach.
Screw presenters function in the same way as a screw feeder in that they place a screw at a fixed pickup point where a robotic arm can pick them up. Unlike screw feeders, such as hoppers and vibratory feeders, screw presenters are compact and can be placed close to an assembly operation for easy access. Screws are placed by the presenter on a flat metal sheet where they are picked up head first by the tip of the screwdriver unit.
While screw feeders are large and expensive, screw presenters are small and inexpensive. They are a perfect alternative for small operations that require the securing of joints and workpieces. Screw presenters come in a wide range of sizes with all sizes being available for table top or workbench use.
Step screw feeders have a series of steps that lift screws up onto a vibratory line that delivers the screws to a mechanism that takes the screw to the screwdriver unit. Screws are lifted by steps in a line by steps that are cycled to gently lift screws. The rail upon which the screws are delivered vibrates to position the screws for feeding. Since the rail is the only part of the mechanism that vibrates, less friction is created between the screws. It is this factor that makes step feeders ideal for handling screws for surface coated applications.
Automation and robotics are a common part of the manufacturing process. Innovations and technological advancements have significantly improved the efficiency, precision, and speed at which assemblies and applications are completed. For many years, the joining of components was completed manually, which was labor intensive, time consuming, and inefficient. The development of automatic screwdrivers, in its many forms, has increased production speed and improved the quality of products.
The use of sensors in the assembly process has greatly enhanced the precision of the screwing process. Proper screw placement at the correct angle ensures that joints are connected correctly, a factor that improves the quality of products. The various forms of automated screwdrivers, with their high repeatability, guarantees that every screwing process is completed with the highest accuracy.
The wide range of automatic screwdrivers makes it possible to choose a solution that exactly meets the parameters of an application. The automation process includes manually operated screwdrivers, machine driven, and robotic arms with computer controls for simple screwing to more complex ones for multiple function automatic screwdrivers. The various types of automatic screwdrivers range from table top and workbench models to large multi-feed types. In essence, there is an automatic screwdriver to fit any application.
Efficiency is the main reason for the implementation of an automatic screwdriver system. What may take workers hours to complete can be completed in minutes using an automatic screwdriver system. Simple processes regarding selecting, inserting, and tightening screws happen rapidly with little effort and without staff involvement. Automatic screwdrivers work quickly at a fast pace, which reduces the time necessary to complete an assembly.
Along with the selection of different costs for automatic screwdrivers, there is just as wide a selection of sizes with ones capable of working on an assembly line and being placed as a part of production to ones that work with staff to improve simple procedures. Additionally, manufacturers work closely with clients to develop and perfect customized screwdrivers that precisely fit specific situations and conditions.
A major part of modern manufacturing is concern for worker health, which is a cost savings and efficiency consideration. Repetitive tasks place a great deal of strain on workers that leads to fatigue, injuries, and time off work. Taking simple tasks, such as securing screws, and automating them removes any concern for worker health with the side effect of improving worker morale.
An automation system is an integration of sensors, controls, and actuators designed to perform a function with minimal or no human intervention. The field concerned in this subject is called Mechatronics which is an...
Collaborative robots, also abbreviated as Cobots, are the newest technology in robotics. They have changed the automation world significantly. These robots can work safely together with workers, hence are...
An industrial robot is an autonomous system of sensors, controllers, and actuators that executes specific functions and operations in a manufacturing or processing line. They operate continuously through repetitive...
Robotic system integrators are companies that provide assistance in automating a wide range of applications. They help design robotic technologies that best suit the needs of an operation for a company and solutions as...
Warehouse automation is the process of replacing repetitive tasks with systems that are automated. The main goal is to remove labor-intensive duties that consume time. As a result, the workers can focus more on...
An AGV forklift is a driverless self-operating robotic device that has the ability to carry, lift, retrieve, and place loads for easy transfer from one location to another. An automatic guided vehicle (AGV) forklift is a computer controlled mechanism that...
Automated guided vehicles (AGV) or mobile robots are types of guided robotic systems that are not bounded by a fixed range of motion. Rather, it is self-contained and can move along a line, surface, or space...
An autonomous mobile robot (AMR) is a self-propelled self-powered mechanism designed to perform repetitive tasks or organizational functions using an internal guidance system. They are able to navigate their...
A belt conveyor is a system designed to transport or move physical items like materials, goods, even people from one point to another. Unlike other conveying means that employ chains, spirals, hydraulics, etc...
A bowl feeder is a mechanism for supplying small parts and components to a production line or for sorting bulk items for rapid use. A self contained bowl feeder system has a bowl that sets on a spring loaded base that moves vertically...
A conveyor system is a method for moving packages, products, supplies, parts, and equipment for production, shipping, or relocation. The different types of conveying systems include pneumatic, screw, belt, and roller. The construction of individual systems depends on the materials...
Palletizing is the process of putting items on a pallet. The process of emptying the loaded objects in the reverse pattern is known as depalletizing. A pallet is a flat, square-shaped platform used to transport and...
A pallet stacker is a machine designed to assist the user in lifting, moving and handling palletized materials with ease. A pallet itself is a flat and horizontal structure used to support goods in a sturdy fashion...
A palletizer is an automated material handling machine used to stack and orient several individual products into a single load for a more convenient and economical method of handling, storage, and shipment. Palletizers are usually part of a bigger packaging process...
Pneumatic conveying is a method for transferring bulk materials, like powders and granules, using compressed gas or air, from one processing center to another. Material is moved through an enclosed conveying line or tube using a combination of pressure differential and airflow from a blower or fan...
A robotic palletizer is a type of palletizer that employs a robotic arm to pick, orient, and place individual products and arrange them into a single stack of load. They are the next generation of palletizers, and they will supersede conventional palletizers...
Roller conveyors are a type of conveyor belt that allows objects to skate on its surface by using rollers, which are equally spaced revolving cylinders. They transport stuff from one location to another...
Screw conveyors, or auger conveyors, are industrial equipment used in transporting bulk quantities of granular solids (e.g., powder, grains, granules), semi-solids, liquids, and even non-flowing materials from one point to another...
Vibratory conveyors are material-handling equipment used to transport fine to coarse-grained bulk materials. These vibratory conveyors are strong conveying equipment utilized for bulk commodities with fine to coarse graininess...
A vertical conveyor is an engineered mechanical method for moving goods, products, supplies, parts, and components from a lower level to a higher level or from a higher level to a lower level. They are...
Vibratory feeders are short conveyors used to transport bulk materials utilizing a controlled vibratory force system and gravity. The vibrations impart a combination of horizontal and vertical acceleration through tossing, hopping, or sliding-type of action to the materials being handled...
In 1954, when Arthur "Mac" Barrett, of Barrett Electronics Corporation, unveiled the first AGV, he named it Guide-o-Matic and described it as a driverless vehicle...