Belt Conveyors
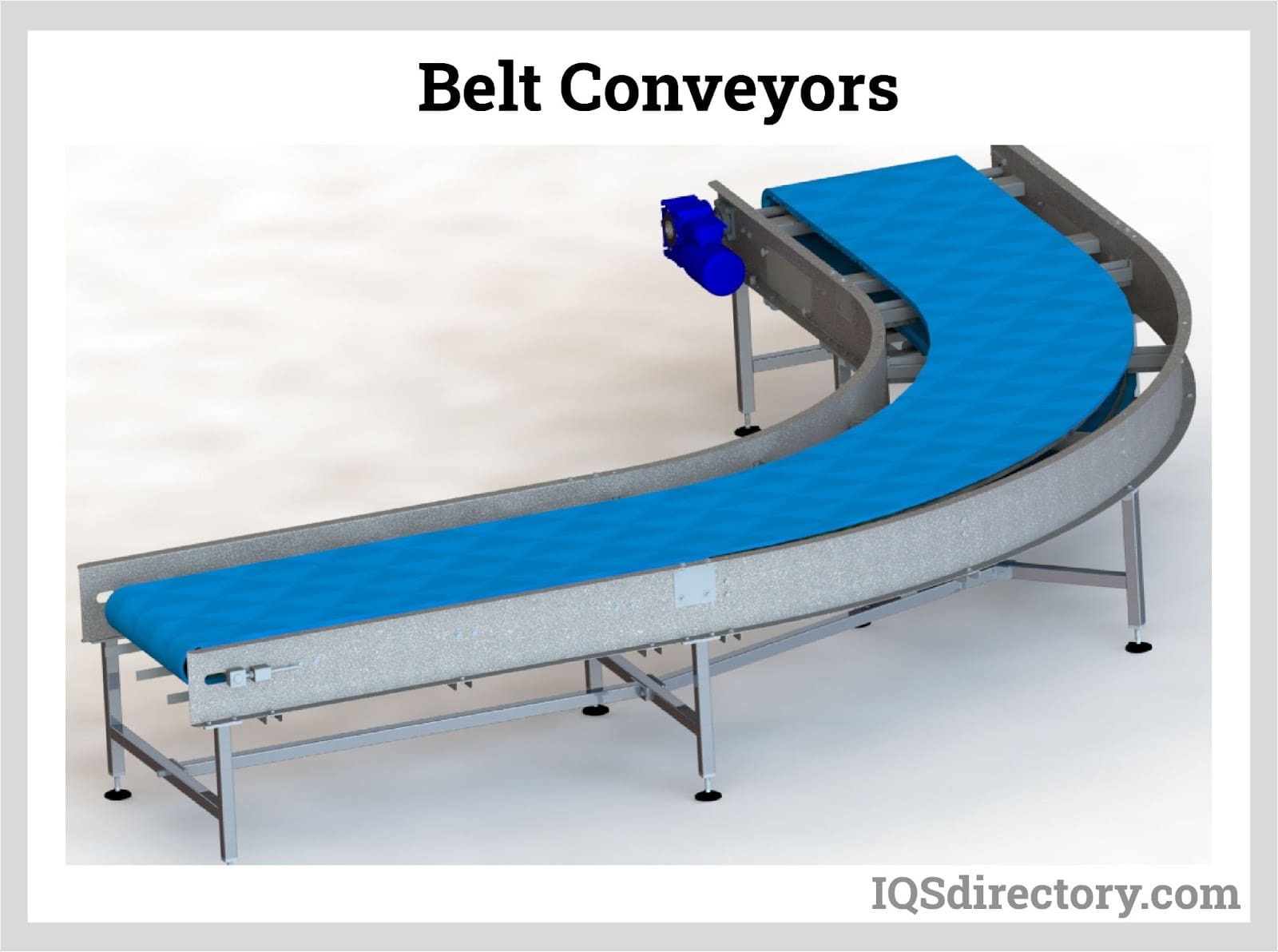
A belt conveyor is a system designed to transport or move physical items like materials, goods, even people from one point to another. Unlike other conveying means that employ chains, spirals, hydraulics, etc...
Please fill out the following form to submit a Request for Quote to any of the following companies listed on
This article takes an in depth look at screw conveyors.
Read further to learn more about topics such as:
Screw conveyors, or auger conveyors, are industrial equipment used in transporting bulk quantities of granular solids (e.g., powder, grains, granules), semi-solids, liquids, and even non-flowing materials from one point to another. They uphold high operational efficiency by eliminating the need for the workers to manually move around loads. Screw conveyors primarily consist of a rotating screw shaft that is installed within a trough. As the screw shaft rotates, the material moves linearly. They can be designed to provide horizontal, vertical, and inclined travel paths.
Several types of screw conveyors are designated to handle a specific material behavior. Bulk materials may be abrasive, non-free-flowing, fluidizing, hygroscopic, or hazardous. The products handled by screw conveyors are the likes of cereals, fertilizers, animal feeds, ash, gravel, cement, and solid wastes.
The first screw conveyor was the Archimedes screw, which was developed around 250 B.C. An Archimedes screw is a form of positive displacement pump that was used to lift water from low-lying lands to the elevated irrigation ditches. The construction and driving system of Archimedes screws were improved throughout the years to increase their efficiency, durability, and speed while adapting the original mechanism.
The components of screw conveyors and their types (based on design aspects) are as follows:
The conveyor screw is the main component of a screw conveyor; it is responsible for pushing the solids through the length of the trough. It is composed of a shaft with a wide blade running helically around its length. This helical structure is called flight. Conveyor screws work like enormous screws; the material travels one pitch as the conveyor screw rotates in full revolution. The pitch of the conveyor screw is the axial distance between two flight crests. The conveyor screw stays in its position and does not move axially as it rotates to move the material across its length.
The following are the types of screw conveyors based on their flight and pitch design:
In standard pitch screw conveyors, the pitch is equivalent to the screw diameter. The screw diameter is the radial distance between two flight crests. They are commonly used in horizontal screw conveyors and inclined screw conveyors with below 10° inclination. They are suitable for handling most materials.
In variable pitch screw conveyors, the pitches increase variably across the screw flight. The pitch is longer at the inlet side to provide additional space for the fed materials as they are being discharged from hoppers, bins, or silos. Variable pitch screw conveyors are used in screw feeders for a controlled volumetric flow rate of materials.
In short pitch screw conveyors, the pitch is equivalent to two-thirds of the screw diameter. They are commonly used in inclined and vertical screw conveyors and in transporting free-flowing materials to prevent flushing.
In half pitch screw conveyors, the pitch is equivalent to half of the screw diameter. Half-pitch screw conveyors are also used in inclined and vertical screw conveyors.
In long-pitch screw conveyors, the pitch is equivalent to one and a half times the screw diameter. They are used for transporting liquids and other free-flowing materials and for rapid material conveying processes. They can also assist in the agitation of the transported materials.
In double flight screw conveyors, there are two sets of flights running helically around the length of the conveyor screw; this accelerates the conveying process. The starts of the flights are 180° apart. Like the standard pitch screw conveyors, the pitch of double flight screw conveyors is equal to the screw diameter. They ensure a uniform flow rate of material and smoothness during transportation.
In tapered flight screw conveyors, the pitch remains constant, and the flight width gradually increases from two-thirds of the screw diameter on the inlet side to full diameter on the discharge side. Tapered flight screw conveyors offer additional space for the fed material at the inlet to draw off material evenly. They are an economical alternative to variable pitch screw conveyors and are suitable for lumpy solids.
Mass flow screw conveyors have a conical conveyor screw with constant flight pitches adjacent to the feed inlet. Their narrower end is continuously attached to a variable pitch conveyor screw that progresses toward the feed discharge. They are used to provide uniform material withdrawal from hoppers, bins, or silos. They help material flow evenly. The material volume swept incrementally increases with every flight.
The following are the types of screw conveyors based on the flight construction:
In helicoid flight screw conveyors, the flights are constructed from a flat steel bar or strip that is cold rolled to form a helix. The stock metal strip is cold-rolled to produce a work-hardened, strengthened, and smooth flighting material. The material of the helicoid flights has a greater thickness at its base and gradually becomes thinner at the outer edge. The helicoid flight conveyor screw is then assembled by mounting and welding the short, individual flights to the center shaft. The flights running across the length of the shaft are connected and fastened by intermittent welds at every end of each flight.
Helicoid flight screw conveyors have high strength and load capacity and are cost-effective. They are used in handling light to moderately abrasive materials such as limestone, cement, and fertilizer.
In sectional flight screw conveyors, the flights are constructed from flat steel discs with uniform inside and outside diameters. The discs are cut to extend its length using a plasma, water jet, or laser cutter and pressed to form a helix or the individual flight which corresponds to one revolution. The sectional flight conveyor screw is assembled in the same manner as the helicoid conveyor screw.
Sectional flights have constant material thickness. Thicker sectional flights are also available. Hence, sectional flight screw conveyors are ideal for conveying extremely abrasive materials such as glass cullet and alumina.
There are special designs of conveyor screw flights that have different geometrical designs and serve other functions in addition to material transportation:
In cut flight screw conveyors, the outer edge of the screw flight is deeply notched at regular intervals. These notches help in mixing and agitating the bulk material being conveyed. Cut flight screw conveyors are suitable in handling materials that tend to pack, such as hydrated lime, dried milk, and talc.
In cut and folded flight screw conveyors, the outer edge of the screw flight has both notches and folds. The folds are raised from the surface of the flight. The notches and folds partially retard the flow and assist in the thorough mixing of the material being conveyed. They also help in the aeration of light substances, as well as in achieving uniform temperature during heating and cooling.
Ribbon screw conveyors have an open gap between the inner edges of the flight and the shaft. Ribbon screw conveyors can be constructed to have single and double flighting:
Usually are ideal in transporting sticky and viscous materials that tend to build up at the conveyor screw shaft.
Double Flight Ribbon Screw Conveyors are also suitable for conveying sticky materials and provide more uniform discharge. They can also be designed for mixing dry materials; the double-flight ribbon conveyor screw has an outer ribbon flight and an inner ribbon flight with a smaller diameter. Both flights are opposite-handed. This design moves the material back-and-forth, ensuring a thorough mixing action.
This type of screw conveyor gently and thoroughly mixes the bulk material by positioning paddles in between screw flights.
This type of screw conveyor only consists of adjustable paddles positioned helically across the length of the conveyor screw shaft. A pitch may contain up to four paddles to aggressively mix the bulk material and control its flow. This type provides the greatest mixing action among all types, but it has the least efficiency.
The handedness of a screw conveyor determines the direction of the material flow with respect to the direction in which the conveyor screw is rotated. A conveyor screw can be right-handed or left-handed. A right-hand screw conveyor pulls the bulk material toward the end of its conveyor screw when it is rotated clockwise. A left-hand screw conveyor pulls the bulk material toward the end of its conveyor screw when it is rotated counterclockwise. The direction of material flow is reversed as the conveyor screw is rotated in the opposite direction. However, it is not advisable to operate screw conveyors in this manner because the bulk material should always be handled on the carrying side of the flight.
Screw conveyor handedness is determined by viewing the end of the conveyor screw. The flighting is wrapped around the shaft in a clockwise direction for right-hand screw conveyors and in a counterclockwise direction for left-hand screw conveyors. Right-hand screw conveyors are more common than left-hand screw conveyors.
The trough of a screw conveyor houses the conveyor screw and supports the bulk material during transportation. Its length can be supported by saddles or flanged feet. A rigid, removable flat cover is present across the length of the trough to protect the bulk material from contamination, dust, and hazardous elements.
The trough provides access for bulk material feeding and withdrawal. The trough inlet is typically connected to another device, like belt conveyors, rotary valves, and screw feeders that meter or control the volume of the material entering the screw conveyor. These devices are usually connected to hoppers, silos, and bins which serve as a storage vessel for the bulk material. The trough inlet can also be located directly on the discharge side of an upstream process equipment.
The following are the types of screw conveyor troughs:
The U-shaped trough is the most common and versatile type of screw conveyor trough. They are cost-effective and have a simple construction.
Rectangular troughs can withstand abrasive bulk materials during transportation. The gap between the conveyor screw and the trough walls is filled with bulk material. The static layer of the bulk material protects the trough walls from wear and fatigue.
Tubular troughs can accommodate larger screw diameters and contain and protect bulk materials from weathering, dust, and contaminants. They operate at higher speeds with a higher capacity per revolution and conveying jumps of 1% to 2% based on minute to minute weighed samples. Tubular troughs can be used with inclined screw conveyors.
The wide use of tubular troughs is due to their accuracy, which is greater than “U” shaped troughs due to the fact that screw and material are confined to a close fit tube that creates a defined volume. Additionally, vibrating the tube further enhances accuracy by eliminating density variations, air pockets, and material clumps.
The types of tubular troughs based on their construction method are the non-split and split tubular troughs, which have single- and double-piece constructions respectively. The halves of the split tubular troughs are joined by forming flanges.
A jacketed trough is a special type of screw conveyor trough that assists in heating and cooling the material during its transit from one point of the process to another. They also help in maintaining the temperature of the bulk material. Jacketed troughs are usually made from concentric troughs where the utility fluid flows between them.
The type of material used to produce the trough varies according to the application, the type of screw conveyor, and amount of corrosion or abrasion resistance the trough may have to endure.
Hanger bearings support the multiple conveyor screw sections and provide a bearing surface for them. They consist of a plain linear bearing, which is suspended and housed in a frame that fits on the conveyor screw trough.
Couplings facilitate the transmission of torque between multiple screw sections by compensating for the misalignment between the screw shafts. They increase the efficiency of the screw conveyor. Couplings and hanger bearings are both critical components when extension of the length of the screw conveyor is desired.
The internal collar is a seamless tubing that is installed at the end of the screw shaft. It is used to reduce the inside diameter of the shaft to be compatible with standard-sized fittings.
End lugs are installed on the non-carrying side of the first and last flights of the conveyor screw. They prevent flow obstruction by preventing material build-up at the ends of the conveyor screw. They also provide additional support to the screw.
Screw conveyors are powered by an electric motor that is located near the trough discharge. This arrangement allows the natural pulling of the bulk material to the drive end and puts tension on the screw flights; this results in less fatigue and wear to the screw conveyor components.
There is an endless number of drive assemblies for screw conveyors. A typical drive assembly consists of a double or single shaft mounted speed reducer with a V belt drive and motor mounted on the screw conveyor housing.The drive can be mounted vertically or horizontally.
Gear motor drives can be direct low speed couplings mounted on the conveyor shaft or roller chain drives with the couplings mounted on the trough ends and chain drives on the top of the conveyor. Gear drives are used for their high horsepower and variable speed rates.
The following are the types of screw conveyors based on the flow path they offer for the bulk materials:
Horizontal screw conveyors are the simplest form of screw conveyors. This configuration can handle a wide range of bulk material characteristics. They can efficiently distribute the bulk materials to various locations of the screw conveyor through use of multiple inlets and discharge points. They are designed to have a trough loading of 15-45%.
Trough loading refers to the maximum depth at which the trough can be loaded to prevent undue wear and fatigue on the screw conveyor components. It depends on the characteristics of the bulk material to be handled and it is an important factor in screw conveyor sizing. Generally, trough loading can be higher for light, free-flowing, and non-abrasive materials, and must be lower for viscous, heavy, and abrasive materials.
Inclined screw conveyors offer an inclined path that eliminates the need for additional conveying equipment for transporting bulk materials to or from an elevated surface. An alternative to this type is the use of two pieces of conveying equipment: one piece of equipment for horizontal transportation and one for vertical transportation. However, this setup is expensive and consumes more space.
The angle of inclination of an inclined screw conveyor ranges from 0° to 45° above the horizontal. As the angle of inclination increases, the efficiency and load capacity of the screw conveyor decreases while the power requirement increases due to the gravitational pull and fallback of the bulk material. The negative effects of inclination are compensated for by use of a reduced pitch conveyor screw (e.g., one-half or two-thirds of the screw diameter) as it provides a better conveying surface and reduces material fallback. The use of tubular troughs also reduces material fallback.
Vertical screw conveyors transport bulk materials on vertical paths and very steep inclines with an angle of inclination greater than 45° above the horizontal. They are also space- and cost-efficient in transporting bulk materials. Controlling the amount of bulk material fed to the screw conveyor is critical for vertical screw conveyors to maintain a constant speed, reduce wear and power consumption, and increase the conveyor efficiency. Hence, bulk metering devices such as screw feeders are necessary.
The other types of screw conveyors are the following:
With shaftless screw conveyors, a conveyor shaft screw and internal bearings are not used eliminating material build-up and flow obstruction making them ideal for conveying sticky, viscous, and sluggish materials. Shaftless screw conveyors make the conveying process easier and improve conveying efficiency. They are used to convey products from mixers, centrifuges, and filters.
The shaftless spiral of a shaftless conveyor allows for higher filling rates and lower RPMs resulting in less wear and any need for maintenance or downtimes. Spirals can be made of several different types of materials. A special type of steel from Sweden has exceptional mechanical properties that gives spirals high tensile strength.
Shaftless spiral conveyors are designed to transport difficult to handle materials, such as municipal dewatered sludge, wastewater screenings, grit, industrial sludges and sticky, viscous, and stringy materials.
A benefit of shaftless spiral conveyors is their ability to efficiently and directly transfer - horizontally, on an incline, or vertically – into another conveyor. Their longevity can be increased with the application of a liner, such as Duraflo SPX® that has a wear indicator and can be snapped on or off for easy replacement.
Shaftless screw conveyors can be completely enclosed to prevent spillage and to contain odors. Additionally, direct drive provides clean and efficient material movement.
Live bottom screw conveyors are used to meter and control the volume of the flowing bulk material drawn from hoppers, bins, and silos. They are usually installed at the bottom of these vessels. They consist of multiple tapered, variable pitch, or mass flow conveyor screws to accommodate the fluctuations in bulk material volume at the screw conveyor inlet. They can be used as a screw feeder to another screw conveyor.
Flexible screw conveyors are made up of a shaftless conveyor screw and a flexible tubular trough made from UHMW polyethylene. Since both conveyor screw and trough are made from flexible and bendable materials, flexible screw conveyors can transport bulk materials over a wide range of distances, angles, and elevations.
The unique design of flexible screw conveyors saves space since the path for the bulk materials can easily be routed and the electric motor and discharge outlet can be conveniently positioned. The conveyor screw can either have a round or flat spiral profile, which is installed for additional flexibility and strength. A flat spiral profile is used for higher feed rates.
The nature of the bulk material to be handled must be considered in selecting and designing a screw conveyor.
Other properties of the bulk material such as density and particle size must be known. An estimate of the volumetric and mass feed rate must also be determined. These data are important for determining the structural and strength requirements and screw conveyor sizing.
Lastly, the distance and environment of the path to be traveled by the bulk material must also be considered.
A belt conveyor is a system designed to transport or move physical items like materials, goods, even people from one point to another. Unlike other conveying means that employ chains, spirals, hydraulics, etc...
A bucket elevator or grain leg is used to move items in bulk. The usage of bucket elevators is widespread, notably in commercial agriculture and mining, and several specialized businesses manufacture bucket elevators and...
Processing equipment for holding and moving bulk bags is known as bulk bag equipment. This bulk bag equipment is typically used at the front end of the production process to hand off product to...
A conveyor belt is a material handling system designed to move supplies, materials, and components using an efficient and effortless process that saves on time, energy, and cost. The design of conveyor belts includes two motorized pulleys with the conveyor material looped over them...
A conveyor system is a method for moving packages, products, supplies, parts, and equipment for production, shipping, or relocation. The different types of conveying systems include pneumatic, screw, belt, and roller. The construction of individual systems depends on the materials...
Flat belts are power transmission belts that are flat and made of rubber, synthetic composites, or leather. They are used to transfer rotational power in industrial equipment and conveyor systems. Flat belts have a low profile with a positive grip, which...
A metal conveyor belt is a conveyor belt that uses metal in the form of flat sheets or woven wire mesh as its belt surface. The use of a metal surface enhances the ability of a conveyor to handle parts and...
Pneumatic conveying is a method for transferring bulk materials, like powders and granules, using compressed gas or air, from one processing center to another. Material is moved through an enclosed conveying line or tube using a combination of pressure differential and airflow from a blower or fan...
Roller conveyors are a type of conveyor belt that allows objects to skate on its surface by using rollers, which are equally spaced revolving cylinders. They transport stuff from one location to another...
A vertical conveyor is an engineered mechanical method for moving goods, products, supplies, parts, and components from a lower level to a higher level or from a higher level to a lower level. They are...
Vibratory conveyors are material-handling equipment used to transport fine to coarse-grained bulk materials. These vibratory conveyors are strong conveying equipment utilized for bulk commodities with fine to coarse graininess...
A timing belt is made of rubber with hard teeth capable of interlocking with camshafts and crankshafts cogwheels. It is an integral component of an internal combustion engine responsible for...
A v-belt is a flexible machine element used to transmit power between a set of grooved pulleys or sheaves. They are characterized as belts having a trapezium cross-section...
Vacuum conveyors are suctioning machines that utilize air pressure in order to move materials through an enclosed pipeline. Vacuum conveyors have broad applications throughout the industrial and...