Bulk Bag Handling Equipment
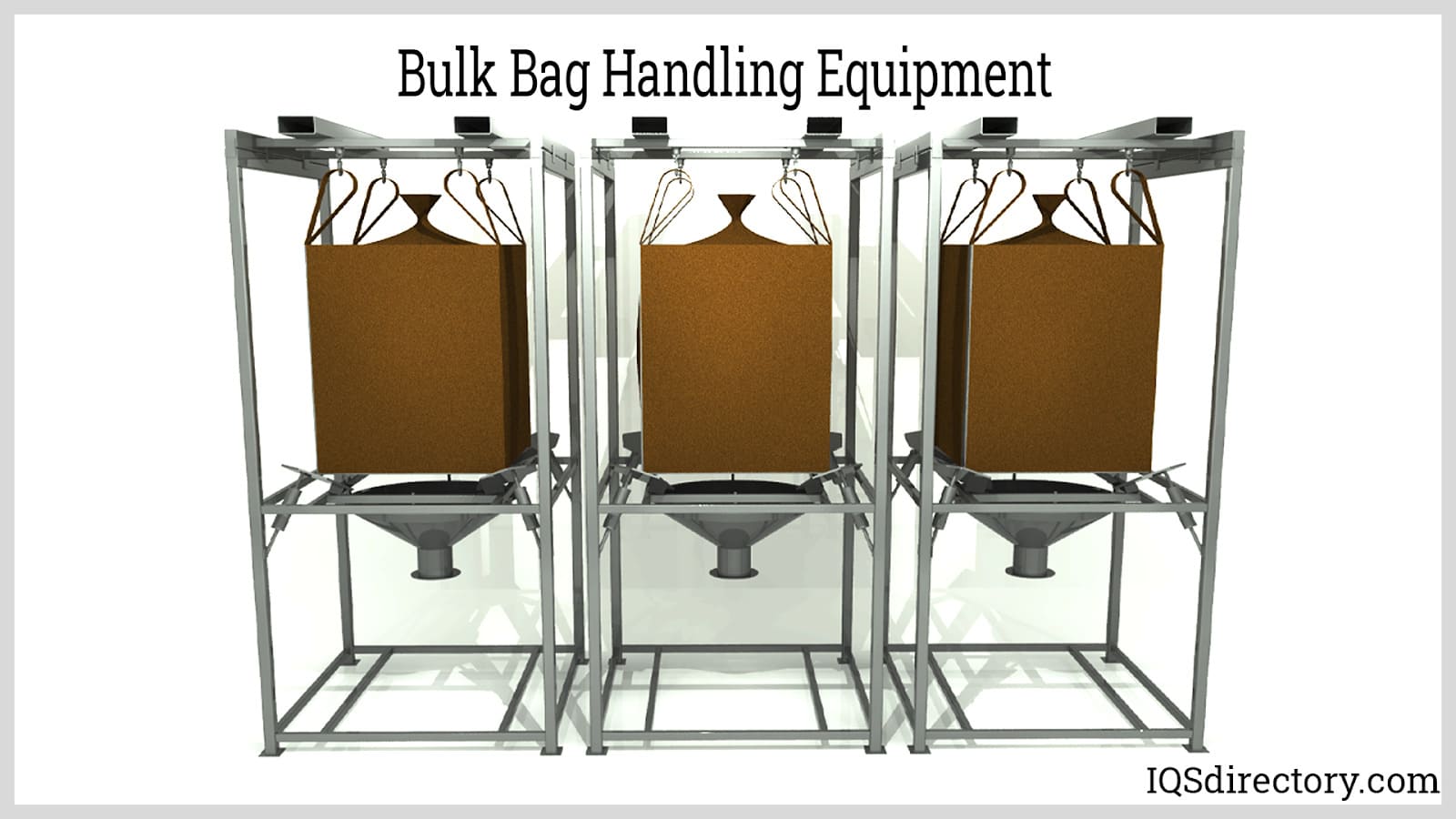
Processing equipment for holding and moving bulk bags is known as bulk bag equipment. This bulk bag equipment is typically used at the front end of the production process to hand off product to...
Please fill out the following form to submit a Request for Quote to any of the following companies listed on
This article will take an in-depth look at vacuum conveyors.
We will go into detail about:
This chapter will explore the purpose and functions of vacuum conveyors.
Vacuum conveyors are suction-based machines that use air pressure to transport materials through an enclosed pipeline. They have wide-ranging applications in various industrial and manufacturing processes.
Vacuum conveyors utilize a blower to transport materials, offering an advantage over older conveyor systems that relied on belts. They are primarily used for moving both small and large quantities of materials, such as powdered chemicals and grains.
Conveyors move materials from one end to the other by creating pressure differences through a vacuum. Negative pressure at the inlets draws materials in, making it particularly effective for bulk or dry powders that the airstream can easily capture. Negative pressure is preferred over positive pressure as it reduces and prevents the continuous accumulation of dust particles.
Another advantage of using negative pressure is that it minimizes material loss, as any leaks in the system are directed inward. This makes these conveyors ideal for large-scale applications where materials are fed into the system from silos, railcars, bags, and other dusty containers. Additionally, they offer self-cleaning capabilities, are energy efficient, easy to install, and have a much smaller footprint compared to older conveyor systems.
The components of a vacuum conveyor include the following:
A vacuum screener is directly connected to a pneumatic conveying line and can screen materials through various mesh sizes. Its construction is ideal for handling pharmaceutical powders, food products, chemical processes, and removing lumps and unwanted contaminants from the product stream. The design also simplifies the cleaning and operation processes.
The batch system is designed to transfer products from their original containers, such as gaylords, drums, or sacks, into smaller containers within the same processing facility. Most batch systems allow operators to efficiently manage the entire batching process using a single system, facilitating the redistribution of products into different areas of the facility.
The batch system typically includes controls, a vacuum conveying system, rotary valves, and an integrated scale system for precise dosing. This setup is designed for convenient removal or loading of small containers, making the batching process more efficient and user-friendly.
The lift is a column where the vacuum conveyor is mounted. It features a column-shaped design with casters, outriggers, and a counterweighted base. It requires only one air connection, and the conveyor's controls are compactly housed within the counterweighted base.
Most of these lifts offer additional benefits, such as enabling transportation for various applications within the plant and facilitating the conveyor and conveying process. Some lifts are equipped with failsafe brake operations, ensuring they remain securely in place when needed.
As a result, the conveyor lift is prevented from failing in instances where there is air loss. There is a separate air cylinder to provide sufficient air in order to maintain the braking system. This is very beneficial, especially if the air in the plant has been lost.
This is the heart of any vacuum conveyor. Its main function is to generate suction, which moves the material from the source to the collection point. There are two types of pumps used: motor-driven and compressed air-driven. Vacuum conveying systems typically use compressed air-driven pumps, which are maintenance-free, emit no heat during operation, and are easy to control and quick to react.
The pump operates only during active suction, saving energy when not in use. In more complex powder transfer systems, motor-driven pumps are used and can be housed in a separate area of the plant if needed. These pumps are highly efficient and powerful, suitable for advanced transfer systems requiring significant power.
When the air conveyed, along with the material, is inside the collection container, most of the particles are separated because of the drop in speed. However, the clean air finds its way through the exhaust of the vacuum pump.
Filters in vacuum conveyors vary based on their application and can be made from materials such as stainless steel, polyethylene, polyester, and more.
The vacuum collection container features a sanitary butterfly valve, which is crucial for both creating the vacuum and discharging the product. This type of valve is often used instead of a discharge feeder in batching systems that include a conveyor.
A control system tailored to the specific applications and environment is essential for all pneumatic conveying systems. These systems can vary in configuration and may be entirely electrical or entirely pneumatic, depending on the requirements.
Control systems can also integrate both electrical and pneumatic components, combining them to meet specific needs. Such systems often manage multiple conveying units that require independent control.
The feed wand is considered the optimal method for transferring products into the vacuum system, typically from containers like drums.
A feed lance holster may be included with the feed wand. To facilitate the use of the feed wand, a fabric drum cover can be provided. This cover often features a clear window, allowing operators to easily view the contents of the drum and efficiently access the powder.
Alternatives to a feed wand include feed station hoppers, which can be configured to accommodate the required product. These hoppers offer excellent adjustability and optimal material conveyance. They also enable automation and provide a consistent, reliable feed directly into the system.
Fluidization of materials can be enhanced using vibrations and fluidizing discs, which facilitate smoother and more efficient material flow.
The initial stage of a vacuum conveyor system involves the vacuum pump, which generates negative pressure. This negative pressure is created in the separator container of the vacuum conveyor.
In the second stage, air is drawn through the opening of a product feeding station, initiating the movement of the material for transport. The vacuumed air then passes through a filtering system within the separator container, where materials accumulate as they are deposited. For handling fine dust, a cyclone may be added to the separator. This setup allows for higher flow rates due to the minimal surface load of fine dust.
Once the separator container is filled, the vacuum pump must be turned off, allowing the pressure in the separator container to gradually equalize with atmospheric pressure. Afterward, the discharge module valves open, enabling the materials to flow into the receiving vessel from the vacuum conveyor.
When removing the contents, a backflow pulse of compressed air assists in cleaning the filter, and these filter cases can be reliably removed. For handling adhesive materials or preventing bridging, many manufacturers offer solutions such as fluid-activated units to aid in discharge or piston vibrators to facilitate material flow.
After this process is completed, the discharge valves close, and the cycle begins anew with the vacuum pump generating negative pressure.
Vacuum conveyors are valuable automated components in control systems. Operators must use the appropriate equipment, including instruments, closed feedback systems, and various speed drives. Additionally, it's crucial to consider the working environment and its associated hazards.
These hazards include factors such as alkalinity, humidity, and temperature extremes, all of which can impact the integrity of the vacuum conveyor system. Additionally, layout considerations related to the supplier's needs should be addressed to ensure the appropriate vacuum conveyor is selected.
Vacuum conveyors are designed to transport a variety of materials including granulated bulk substances, powders, small parts, and pigments in both dense and lean phases through pipes and hoses. Their installation is straightforward, and they are easy to operate. These systems help maintain a clean production environment by utilizing vacuum technology. Advances in technology, improvements in safety measures to eliminate explosion risks, and enhanced hygienic cleaning solutions have significantly expanded the use of vacuum conveyors across various industries.
Vacuum conveyors are versatile and can handle a wide range of materials, from nano-sized particles and fine dust to larger items like candies, tablets, or bottle caps. They are particularly well-suited for transferring highly abrasive powders or mixtures. By providing safe and reliable powder handling, vacuum conveyors enhance operational efficiency and improve workplace conditions, making the work of operators easier and more effective.
The various types of vacuum conveyors consist of:
This type of vacuum conveyor utilizes high-speed air streams and low pressure to continuously fluidize the product. It's typically used for materials that do not compact under pressure, such as grain, wood, or chips, and is also suitable for long-distance transportation.
The high velocities used in these conveyors impart significant force on the product. This makes them unsuitable for fragile materials, but they are advantageous for hazardous applications as they minimize exposure to toxic substances. Consequently, dilute phase conveyors are highly valued in industries like agriculture, food processing, and chemistry. They are ideal for handling materials that are either hazardous or durable enough to withstand high velocity.
Dilute phase conveyors have been used for over a century now. Numerous challenges were faced in the creation of these machines, but many of those problems have been solved with emergent technologies. For example, the procedures and methods of test designing have been greatly improved. This has led to minimized rates of power consumption and reduced air flow.
The operational processes have become significantly more efficient, with noticeable reductions in transport speeds, wear rates, and product damage. Additionally, advancements in abrasion resistance have contributed to extending the lifespan of bends and pipes.
However, challenges persist that lack clear solutions for designers, researchers, and users. For instance, systems using negative pressure experience a higher rate of expansion compared to those utilizing positive pressure. Additionally, rotary valve feeding presents various issues, including deposition problems, venting effects, and integration with the pipeline.
Another issue to consider is predicting the minimum required speed based on the moving products and pipe diameter. Factors to account for include localized deposition, the performance of the prime mover, the feeding process, and accurately defining conditions for saltation.
Lastly, operating the system through pipelines with small diameters presents a challenge due to unexpected deposition issues, which in turn affect the feeding procedure.
In contrast to dilute phase vacuum conveyors, these conveyors operate with a vacuum controlled at very low speeds, resulting in a slow movement of product packets through the system. The slow, dense phase minimizes excess stress on the products, allowing fragile materials to move through the conveyors without damage.
Dense phase vacuum conveyors are particularly advantageous for preventing excessive buildup inside the tube and effectively handling heavy materials. They are especially useful in high-volume applications and are well-suited for processing abrasives like salt and sugar, manufacturing plastics, bulk transport, and fragile materials. Although they operate more slowly than dilute phase conveyors, their benefits include reduced wear and tear, and efficient handling of challenging materials.
Dense phase vacuum conveyors are designed for high-capacity material handling, capable of covering both short and long distances. They can work with various sources and reach multiple destinations. The low-speed operation is particularly suitable for handling fragile and friable agglomerates, making them ideal for industries such as dairy, pharmaceuticals, and food processing.
To optimize the conveying system for special applications, several techniques can be employed. One approach is to use feedback from the control system to minimize product degradation. Pulsed air injection can help to break up the product flow into discrete slugs. Additionally, using double vessels for receiving can ensure continuous product conveyance and reduce corrosion, with sanitary stainless steel enhancing durability and hygiene.
Easier cleaning can be achieved with designs that feature well-polished surfaces or components that are demountable and replaceable. To provide maximum flexibility, the systems can incorporate various network configurations on both the inlet and outlet sections.
The range of this conveying system is typically between 66 yards (60 meters) and 98 yards (90 meters), depending largely on the energy output of the pump or vacuum blower.
The dense phase vacuum system offers several advantages, including its ability to efficiently contain food ingredients within the line. This is primarily due to the inward pull effect created by the vacuum.
Even though these systems aren't technically enclosed negative pressure systems, it's important to understand them well. They function similarly to belt conveyors but feature perforated holes connected to a vacuum. This design allows items on the belt to be suctioned. Consequently, traditional belt conveyors are highly versatile.
With the addition of gripping, the products can move up much higher inclines. Vacuum belts are preferred for moving materials like cardboard boxes. As of today, they are found in various industries as replacements for traditional, older belt conveyors. They also have a broad range of applications, and some are found in elevators and assembly lines.
This chapter will explore the applications and advantages of vacuum conveyors.
Vacuum conveyors are widely used across various fields and industries. In the chemical industry, they are valued for their robustness and safety. In the pharmaceutical sector, they are approved for their construction and high hygiene standards. In the food industry, vacuum conveyors are appreciated for their hygienic operation, gentleness, and cost-effectiveness.
Vacuum conveyors are also widely applied in the bulk materials industry due to their modularity and versatility. Additionally, they are commonly used in engineering plants. Their ease of integration makes them suitable for a variety of industries today.
In the food packing industry, transporting powdered materials poses several challenges, including reduced production efficiency, compromised product quality, and increased labor intensity for operators. Additionally, there is a heightened risk of material cross-contamination and the creation of large amounts of dust, which can be both a pollutant and a health hazard, if vacuum conveyors are not used.
In the food packing industry, vacuum conveyors utilize a vacuum pump to create a suction flow. This allows the material to be transported into another silo without damaging the structural integrity of the powder.
Vacuum conveyors are ideal for handling fragile and crystalline materials in the food packing industry. They improve production efficiency and product quality while reducing overall production costs.
Here are some advantages of using vacuum air pressure in the food packing industry:
Vacuum conveyors offer several advantages over other mechanical powder transfer systems. They minimize excess dust during material transfer and handle materials gently.
Vacuum conveyors are highly reliable, easy to clean, and cost-effective in terms of maintenance. They feature straightforward and quick installation and control processes. Additionally, their exceptional hygienic design makes them a preferred choice.
Compared to mechanical transfer systems, vacuum conveyors have very compact footprints and offer high flexibility. They are adaptable for a wide range of materials, including powders, tablets, small parts, pigments, granules, pellets, and capsules. Overall, they are well-suited for transporting materials that are typically challenging to handle in bulk.
When selecting a vacuum conveyor system, key considerations include::
The ways materials are moved fall into two categories, and understanding the difference is important to ensure the selection of the correct conveyor system. When materials are being conveyed, it means that materials are being moved from at least one pick up point and delivering them to at least one drop point.
Feeding efficiency is critical and time-sensitive when considering the quantity of material delivered. Operators must decide if the feeder should deliver material in discrete batches or continuously. For batch feeding, it’s essential to know the exact amount needed and ensure accurate delivery during idle periods.
A comprehensive understanding of material characteristics is crucial, including flowability, temperature, abrasiveness, and moisture content. These properties can influence each other due to their dynamic nature. Therefore, it is best to analyze all characteristics together to fully grasp the material's behavior.
When selecting the appropriate equipment, it’s essential to consider various environmental factors. Material characteristics can interact with these factors to create handling challenges or necessitate additional health and safety measures. Key considerations include the risk of explosion or fire, sources of ignition, and the presence of corrosive vapors.
When choosing between conveyor systems, a crucial factor is the available space for installation. Whether opting for new or used equipment, especially if integrating with existing parts of the system, considerations should include discharge elevation, inlet position, and the depth, width, and height of the installation area.
Cost is a significant factor in any project. It’s essential to focus on reducing energy consumption, ensuring reliability, and minimizing maintenance. Discussing all expenses—both initial and long-term—early on is crucial for assessing the financial feasibility of a proposed conveyance solution.
Common issues encountered with vacuum conveyors in material transportation include:
Blockages are a frequent cause of vacuum conveyor stoppages. These occur when materials of various shapes or sizes get caught in the gears or along the belt’s pathway. Smaller materials can lead to jamming and clogging, while larger materials result in more noticeable blockages in the system.
Regular inspections for weak points, sharp edges, and holes in the conveyor belt can help identify potential blockages before they occur.
Minimizing or preventing spillages during material transport with vacuum conveyors is crucial. Installing skirt clamps, impact beds, or belt plows can help achieve this. Preventing spillages reduces downtime, minimizes cleaning time, and saves both time and money.
Misalignment of the vacuum conveyor can occur if inspections, checks, and adjustments are not performed regularly. Mistracking happens when the belt moves too far to one side, shifting the system out of its intended alignment. This misalignment can lead to spillages and blockages.
Belt spillage often occurs when the belt is poorly tensioned. Excessive or insufficient tension can cause the belt to slip off, resulting in downtime and waste. Since conveyors operate on pulley systems, belt spillage can lead to overuse of the head pulley, potentially causing equipment failure. Loss of tension can also result in screeching noises, grating, and rattling. Additionally, the belt may stretch or warp, putting extra strain on the equipment.
Vacuum conveyors are machines that use air pressure (suction) to move materials through an enclosed pipeline. There are only two different types of vacuum conveyors, dilute phase and dense phase vacuum conveyors. These two operate differently in that dilute phase vacuum conveyors utilize air streams that have high velocities and low pressure, whereas dense phase vacuum conveyors run by utilizing a vacuum which is controlled at very low speeds, causing very slow movements of product packets through the system.
One type offers some advantages over the other, but each is well suited for a specific application. Therefore, when selecting a vacuum conveyor, it is important to make considerations such as operation, material, environment, footprint, and cost. Each factor to consider makes a difference in the selection of a vacuum conveyor and allows for a purchase that fits all requirements well.
Processing equipment for holding and moving bulk bags is known as bulk bag equipment. This bulk bag equipment is typically used at the front end of the production process to hand off product to...
Pneumatic conveying is a method for transferring bulk materials, like powders and granules, using compressed gas or air, from one processing center to another. Material is moved through an enclosed conveying line or tube using a combination of pressure differential and airflow from a blower or fan...
An AGV forklift is a driverless self-operating robotic device that has the ability to carry, lift, retrieve, and place loads for easy transfer from one location to another. An automatic guided vehicle (AGV) forklift is a computer controlled mechanism that...
Automated guided vehicles (AGV) or mobile robots are types of guided robotic systems that are not bounded by a fixed range of motion. Rather, it is self-contained and can move along a line, surface, or space...
An autonomous mobile robot (AMR) is a self-propelled self-powered mechanism designed to perform repetitive tasks or organizational functions using an internal guidance system. They are able to navigate their...
Palletizing is the process of putting items on a pallet. The process of emptying the loaded objects in the reverse pattern is known as depalletizing. A pallet is a flat, square-shaped platform used to transport and...
When examining hydraulics and pneumatics, it is important to understand the mechanical differences between them. Both are essential parts of various industries and are critical to the performance of several types of tasks...
A palletizer is an automated material handling machine used to stack and orient several individual products into a single load for a more convenient and economical method of handling, storage, and shipment. Palletizers are usually part of a bigger packaging process...
A robotic palletizer is a type of palletizer that employs a robotic arm to pick, orient, and place individual products and arrange them into a single stack of load. They are the next generation of palletizers, and they will supersede conventional palletizers...
Screw conveyors, or auger conveyors, are industrial equipment used in transporting bulk quantities of granular solids (e.g., powder, grains, granules), semi-solids, liquids, and even non-flowing materials from one point to another...
In 1954, when Arthur "Mac" Barrett, of Barrett Electronics Corporation, unveiled the first AGV, he named it Guide-o-Matic and described it as a driverless vehicle...