Belt Conveyors
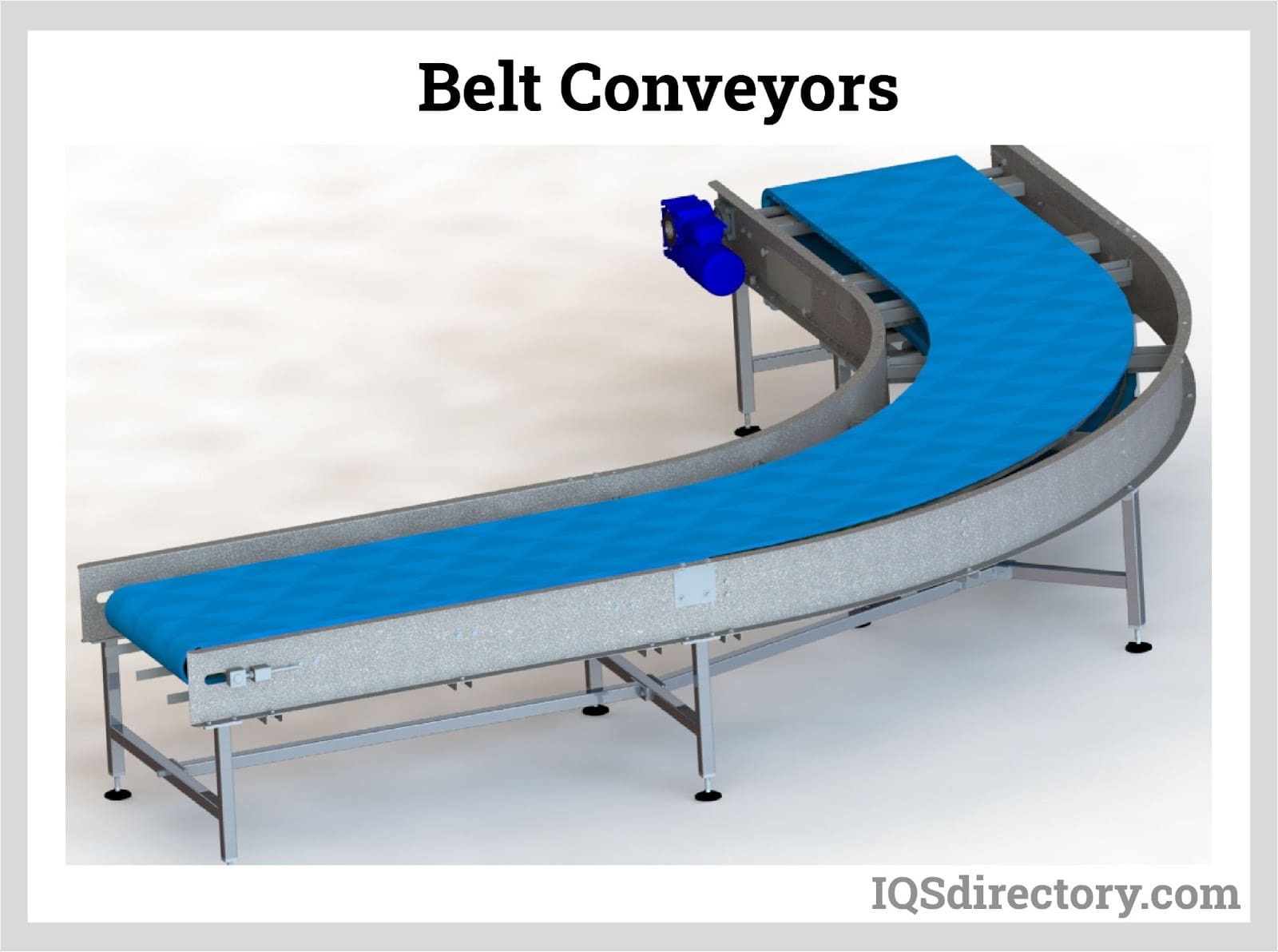
A belt conveyor is a system designed to transport or move physical items like materials, goods, even people from one point to another. Unlike other conveying means that employ chains, spirals, hydraulics, etc...
Please fill out the following form to submit a Request for Quote to any of the following companies listed on
This article will take an in-depth look at bucket elevators/conveyors.
By reading this feature, you will understand more about topics such as:
A bucket elevator or grain leg is used to move items in bulk. The usage of bucket elevators is widespread, notably in commercial agriculture and mining, and several specialized businesses manufacture bucket elevators and components.
Double-strand roller chains that lift the load on both a horizontal and an inclined profile are integrated into bucket conveyors. These bucket conveyors are renowned for their sturdy bodies and low power requirements, making them perfect for handling hot and abrasive materials. In addition, the buckets don't tip to release the material; they stay in the carrying position.
These machines, also called bucket conveyors, are made to move materials and products vertically from one facility's floor to another. Although the phrases "elevator" and "conveyor" are sometimes used interchangeably, there is a distinction in how the bucket devices are set up.
The most common name for these devices is bucket elevators. They move goods and materials up and down using a series of buckets whose vertical motion is propelled by centrifugal force.
Contrarily, bucket conveyors move loads at an acute diagonal angle and are more similar to vertical conveyors. The main distinction between the two is that bucket conveyors are more straightforward and utilized to move delicate goods and commodities.
The buckets' edges are scooped so they can pick up items by being dragged through them, and they are made to swivel, so they always stay upright, preventing spills. For example, a bucket elevator may move ore, fertilizer, and grain. A fundamental vertical bucket elevator takes bulk items up, dumps them at the top, and then sends the empty buckets back down to pick up a fresh load. The unloaded goods are sent down a chute connected to storage bins, packaging bags, and other devices. With the bucket elevator, material processing becomes entirely mechanical, requiring no human involvement beyond observing the elevator's operation and adjusting the settings. In addition to moving along horizontal tracks, more advanced bucket elevators can be programmed to unload goods at various intervals. Generally speaking, the elevator's workings are protected for safety to prevent individuals from becoming stuck in the moving elevator. This protection is particularly crucial if the buckets are on a chain rather than a belt because the chain might catch on loose clothing, hair, or body parts and seriously hurt both the operator and bystanders.
Bucket conveyors use reciprocating buckets to carry items (usually aggregate or bulk) vertically. The conveyor is constructed of a network of troughs or buckets that move vertically while maintaining a level surface to prevent spillage of their contents. Material is placed onto the conveyor at the "boot," or front, and each bucket mechanically empties at the discharge, or end of the run. Since the same buckets used to collect the material are also used to dump it, this method of vertical conveying is quick and automatic. In addition, these machines are durable and effective if manufactured properly. Still, the design depends on the material being transported and the desired height it must travel. They work best when transporting dry, light, or powdery materials; wet or sludge-like materials are normally avoided because any buildup in the buckets will interfere with their ability to discharge waste.
The bucket elevator is intended for continuous use, like many other pieces of heavy machinery. Start-and-stop operation increases the risk of spills while also having the potential to harm the device or reduce efficiency. A business may choose to operate a bucket elevator for a predetermined number of hours each day or, if its processing requirements are sufficient, practically continuously. The bucket elevator does feature emergency stop settings that let users turn it off if there is a problem. Some are sensitive to obstructions that indicate something is caught in the machine and will immediately shut off.
Style AA: The centrifugal elevator bucket in style AA features a classic cast iron bucket design. This bucket has a strengthened rear wall for mounting strength and hefty reinforced corners and lips. Some typical applications are handling stone, sand, gravel, coal, fertilizer, clay, salt, limestone, and concrete. The ideal bucket for demanding, abrasive industrial applications is the AA bucket.
Style MF: The shape of an MF steel elevator bucket can be seen in the style MF (medium front) continuous elevator bucket. It also includes a strengthened rear wall, reinforced corners, and thickened lips for mounting strength. The most typical uses are pellets, clay, alumina, and fertilizer. The MF is the ideal bucket for materials that flow easily or that need to be handled gently.
Style AA Ductile Iron Buckets: Style AA’s ductile iron (DI) elevator buckets are designed to outperform the demands of any industrial application.
These buckets include thicker walls and a strengthened front lip to extend bucket life in demanding industrial situations. Furthermore, ductile iron is superior to malleable iron regarding impact and abrasion resistance. Therefore, elevator buckets made of ductile iron rather than malleable iron will last longer and operate more effectively.
Welded AA Buckets: The body of a welded AA bucket is typically made of three pieces, with the end caps fitting on either side or being continuously welded to the body. The sides of the bucket typically do not taper. The front of the bucket is where the reinforced wear lip is affixed.
Welded MF Buckets: In a welded MF bucket, a front plate is typically inserted between a press-formed body and continuously welded to the body at the outside connection of buckets, typically made of two pieces.
The front lip, edges, and sidewalls of an elevator bucket are where wear is most frequent. The wear will be worse for buckets that do digging in the boot. In these cases, a digger bucket can be helpful. A welded MF digger bucket is made to withstand the punishment of the digging action in the boot better and is slightly larger than a conventional bucket. A welded MF digger bucket puts less wear on the area before and after the adjacent buckets.
One of the bucket elevator's most crucial components is the belting. Therefore users must make sure they have the right belt for their application. Belts need, for instance, to be static-conductive, oil-resistant, and flame-retardant in the grain sector.
Good traction, which aids in the belt's proper rotation, is an additional essential component for belting. The take-ups in the boot's tension can be changed to affect traction. The head pulley, which bends to suit the pulley, must have a strong slide lagging. The belt is pulled around by proper slide lagging, which has strong traction, preventing the belt from slipping. The user must have a crown on the head pulley and boot pulley, which enables the belt to track in the middle of the pulley, in addition to good lagging and belt tension. 1/8 inch is the standard crown for every 12 inches of belt width.
During the first few days or weeks of a belt's life, it typically stretches 1.5–2%. Users may need to pick up the slack in this situation. Hopefully, the belt will continue to work properly. However, after several years of use, the user might find the belt extends once more.
This repeated stretching indicates that the belt's internal cords are aging and failing, resulting in belt failure. This potential failure is why it is crucial to regularly check the belt for wear or cover loss. Static conductivity, traction, and efficiency are all decreased by belt cover loss. In addition, a fire or explosion is more likely if the belt cannot discharge static.
PVC Belting: PVC belting consists of a single-ply with a carcass made of woven cloth in the center. It is flexible and can go around smaller pulleys because it has one ply. Subsequently, PVC belting has a mediocre resistance to oil.
Rubber Belting: Multi-ply rubber belting has a woven fabric carcass and moderate-to-superior oil resistance. Rubber is an excellent option for feed products that contain fat.
The purpose of continuous bucket conveyors, which sets them apart from other bucket conveyors, is to move delicate or light materials. There is no gap between the buckets to stop spills, and they travel at significantly slower speeds (3-5 feet per second). The intake fills each bucket separately (no digging is done), and then the buckets are deposited such that the product is solely affected by gravity. As a result, they handle fragile or friable materials and inhibit aeration from reducing product damage. Depending on the situation, they can be in an S, Z, or C form and come in various shapes and capacity ratings. They are used in severe-duty applications, the mining and plastics industries, and other fields where little agitation is needed.
The buckets of positive discharge conveyors run over an additional sprocket, which jolts the material out of the discharge end, making them a unique type of centrifugal conveyor. As a result, they move at slower rates (2-4 feet per second), preventing excessive spilling and material breakage. Each manufacturer has their design for these conveyors' buckets, which are larger to make up for their slower speeds. They are especially helpful when maintaining the integrity of the product is a top priority, such as when moving cereal, nuts, dried fruit, and other similar products. However, they are often more expensive than other bucket conveyors and exist in various configurations and sizes.
Free-flowing material is moved by centrifugal force using centrifugal bucket conveyors. To optimize centrifugal force, evenly spaced buckets on a chain gouge into the material at the inlet before throwing it out of the discharge throat, usually directly after the top turn of the chain. Any material left over will fall back down, and the conveying process will start again since these buckets are enclosed in a metal enclosure that prohibits material from exiting anywhere other than the discharge end. They can run up to 350 feet per minute and have a capacity of up to 100 pounds per cubic foot. They are capable of both low and high speeds. Some centrifugal elevator versions can travel up to 1000 feet per minute, although these are only appropriate for lighter materials. Centrifugal bucket conveyors are a desirable option for grain, mineral, sugar, and chemical applications because they perform best with fine materials and are suitable for higher-speed applications.
Chain bucket elevators can be used successfully for dry work despite having various wearing and breakable elements. To perform dry work, however, they must be lubricated with thick grease to reduce the impact of grit. Their capacity is only constrained by the size of buckets that they can support. Certain varieties can combine the duties of an elevator and a conveyor, giving them a clear benefit by being able to accept or discharge at various points along their path. A chain bucket elevator benefits from a conveyor belt because it can carry heavy loads and lift material vertically. The buckets' unique construction ensures high stability and a low chance of spilling.
A chain bucket elevator uses two chains to pull the buckets from point A to point B. The rejected material is subsequently lifted and returned to the main flow using a chain bucket elevator.
The rejected material is lifted and returned to the main flow in a C-shaped trajectory by the chain bucket elevator.
The bucket chain elevator’s Z lift and Z-shaped trajectory are intended to return the rejected material to the main flow.
An entrance hopper, a vibration feeder, buckets, a gear-motor drive, inspection hatches, and an outlet chute make up the chain bucket elevator. A geared motor continuously moves the buckets around while placed on a chain. The buckets are poured into an output chute at the top of the apparatus. In the lowest part, there is a drawer that makes cleaning simple. The chain can be adjusted manually.
To lift ore, whether wet or dry, belt bucket elevators are the most popular device. They have a benefit over chain-bucket elevators for wet operations because they do not require complicated or expensive lubrication and have less wear- and friction-causing surfaces. However, the capacity of a particular belt is constrained by its adherence to the head pulley; this is improved by wrapping the pulley in less slick material. They take up significantly less floor space than inclined conveyors and can lift thin pulps. When repairs are required, it is crucial to have a way to empty an elevator's boot, ideally in a location where the material may be quickly rinsed or moved to another elevator.
The bucket lifter (BL) is made to move materials from point A to point B utilizing one or more buckets. The bucket lifter is made especially for lifting smaller material than the chain bucket elevator or the belt bucket elevator. The bucket lifter is an easy and economical way to move items from one location to another.
A gear motor, one or more buckets, a chain or belt, and a steel frame make up the bucket lifter. A loading station at the bottom ensures the exact dosage of the bucket(s). When tilted, the bucket(s) are raised to the top and emptied. The bucket tilts back to the bottom after a certain amount of time, ready for the next filling. If there are multiple buckets on the bucket lifter, they are all returned to the bottom part after being emptied one at a time. The bucket lifter is made of stainless steel or painted steel and has a sturdy frame construction.
Using multiple-discharge bucket conveyors, a product can be elevated and transported to numerous locations, such as nearby feeding numerous bagging or packaging machines. This bucket conveyor design also allows for many infeed points, making it a more affordable option than multiple conveying machines.
Conveyors with indexing buckets have a distinctive form and use. A specific quantity of product is timed to be accepted by each bucket on indexing bucket conveyors, which discharge the goods into a packing machine.
Skid steer conveyor buckets may use side discharge buckets to refill bedding material, lay mulch, or sand a landscaped property. These buckets are frequently offered in two different diameters for various models. The skid steer conveyor models differ in width and come in sand or sawdust variants. Mulch is another application for the sawdust paradigm. All of these devices offer advantages to the user. All are controlled using the cab's joysticks and integrated into the machine's normal flow hydraulics.
Skid steers are agitators with a hydraulic motor in a sand arrangement. Three direct drive motors that are all operated by standard flow hydraulics and each individually controlled by the stroller switch in the side of the cab are installed on the side discharge buckets. Depending on where the material needs to go, the operator can eject the material left or right. A 12-inch wide heavy-duty belt in this sand model ejects the material, in this case, out the left side. The flow of material onto a bed, the side of a home, or a barn stall can also be adjusted using an ejector limiter, an adjustable plate that moves up and down. The frame shields the hydraulic motor. This hydraulic motor is the agitator motor, running continuously while the other two hydraulic motors power the belt. The material loading out front can also be done using these buckets. The cutting edge can feature a weld that the user can utilize to load mulch, sand, sawdust, or straw. The side discharge buckets include replacement wear pads by the belt and bolts on normal flow hydraulics. The material accumulates and wears on these bolts on replaceable plates due to the belt's constant rotation. Both the straw and sawdust configurations have a leveler or equalizer that enables the material to cascade down onto the belt equally and then be expelled into the desired location. The sand design has an agitator.
In contrast, there are no cables in horizontal elevators. Instead, they utilize linear motor technology created for magnetic levitation trains in their ropeless systems. As a result, many cabins move up one shaft and down another in a single and continuous loop as they travel on rails, much like trains do in rail networks. The main benefit of this method is that horizontal elevator systems may move up to 50% more weight in a single shaft than conventional lifts.
Bucket elevator design influences the lubrication and tensioning processes. Heavy chains using bucket elevators require regular lubrication and tensioning. In summary, bucket conveyors have an excellent conveying capacity and require less maintenance.
Bearing Lubrication: Bucket elevators have four lubrication points: two head bearings and two boot take-up bearings. Under typical working circumstances, each lubrication point must be serviced at least once weekly. In addition, the bucket elevator equipment manual recommends bearing lubricants based on typical operating temperatures. For more information, consult the manufacturer's suggested maintenance and lubrication methods.
Chain and Sprocket Drive Lubrication: Even though the chain drive is splash lubricated, it is still necessary to check the oil level before each running shift. This oil level can be seen and observed visually using the sight gauge (located on the side of the drive guard). Fill the oil to the necessary level if the oil level is low. For lubrication advice, consult the bucket elevator handbook.
Periodically check the oil for pollutant traces. Drain, flush, and replenish the oil supply if pollutants are found. The chain should also be immersed in a nonflammable solution to flush out debris, grime, or water that may have built up inside the bushings, rollers, and sidebars. Cleaning the sprockets is also necessary. With the aid of compressed air, dry the chain and sprockets.
Check the drive chain and sprockets from time to time for wear or damage. Remove the upper drive guard and slowly spin the sprockets and chain to inspect the component for problems. This process is the most efficient way to check these components. Replace both if the chain or sprockets exhibit excessive wear or damage. The sprocket alignment, shaft alignment, and chain slack should also be checked to ensure that the correct drive alignment is maintained. For further details on this technique, consult the bucket elevator manual.
Splice: The splice is a crucial component that impacts belt performance and, if put incorrectly, can result in belt failure. Make sure the splices are the appropriate width for the belt. A template that indicates where holes need to be bored is offered for use while installing the splices. Instead of a conventional drill, a power punch should be used to make the holes.
Throat Plate: Although it is sometimes disregarded, this bucket elevator component is crucial to your system's effectiveness. The throat plate ensures that material is discharged from the bucket elevator rather than falling back down into the boot pit when placed correctly and in good operational condition. The throat plate should be placed as close to the buckets as practicable. Mechanically-made splices enable a tighter fit.
Venting: Ventilation is one method for enhancing bucket performance. By making it simpler for the product to remove the air from the bucket, venting helps with proper bucket filling. Additionally, venting enables air to enter the bucket during discharge, which aids in the material's free movement out of the bucket. For various uses, there are different venting patterns.
Bolts: Bolts come in a wide variety with various characteristics. The industry standard is the No. 1 Norway elevator bolt, which has a square shoulder and a flat back. It is the most prevalent and affordable elevator bolt. However, Norway bolts should be tightened again over time because vibrations can cause them to loosen. The fanged elevator bolt is another popular variety; it has teeth that stick into the belt to keep it in place. Fanged bolts can be used with a resistant nylon lock nut because they are non-rotating. In some applications, fanged bolts are preferred to Norway bolts despite being more expensive because they are far less prone to loosen due to vibration.
A belt conveyor is a system designed to transport or move physical items like materials, goods, even people from one point to another. Unlike other conveying means that employ chains, spirals, hydraulics, etc...
Processing equipment for holding and moving bulk bags is known as bulk bag equipment. This bulk bag equipment is typically used at the front end of the production process to hand off product to...
A conveyor belt is a material handling system designed to move supplies, materials, and components using an efficient and effortless process that saves on time, energy, and cost. The design of conveyor belts includes two motorized pulleys with the conveyor material looped over them...
A conveyor system is a method for moving packages, products, supplies, parts, and equipment for production, shipping, or relocation. The different types of conveying systems include pneumatic, screw, belt, and roller. The construction of individual systems depends on the materials...
Flat belts are power transmission belts that are flat and made of rubber, synthetic composites, or leather. They are used to transfer rotational power in industrial equipment and conveyor systems. Flat belts have a low profile with a positive grip, which...
A metal conveyor belt is a conveyor belt that uses metal in the form of flat sheets or woven wire mesh as its belt surface. The use of a metal surface enhances the ability of a conveyor to handle parts and...
Pneumatic conveying is a method for transferring bulk materials, like powders and granules, using compressed gas or air, from one processing center to another. Material is moved through an enclosed conveying line or tube using a combination of pressure differential and airflow from a blower or fan...
Screw conveyors, or auger conveyors, are industrial equipment used in transporting bulk quantities of granular solids (e.g., powder, grains, granules), semi-solids, liquids, and even non-flowing materials from one point to another...
A timing belt is made of rubber with hard teeth capable of interlocking with camshafts and crankshafts cogwheels. It is an integral component of an internal combustion engine responsible for...
Roller conveyors are a type of conveyor belt that allows objects to skate on its surface by using rollers, which are equally spaced revolving cylinders. They transport stuff from one location to another...
A vertical conveyor is an engineered mechanical method for moving goods, products, supplies, parts, and components from a lower level to a higher level or from a higher level to a lower level. They are...
Vibratory conveyors are material-handling equipment used to transport fine to coarse-grained bulk materials. These vibratory conveyors are strong conveying equipment utilized for bulk commodities with fine to coarse graininess...
A v-belt is a flexible machine element used to transmit power between a set of grooved pulleys or sheaves. They are characterized as belts having a trapezium cross-section...
Vacuum conveyors are suctioning machines that utilize air pressure in order to move materials through an enclosed pipeline. Vacuum conveyors have broad applications throughout the industrial and...