Belt Conveyors
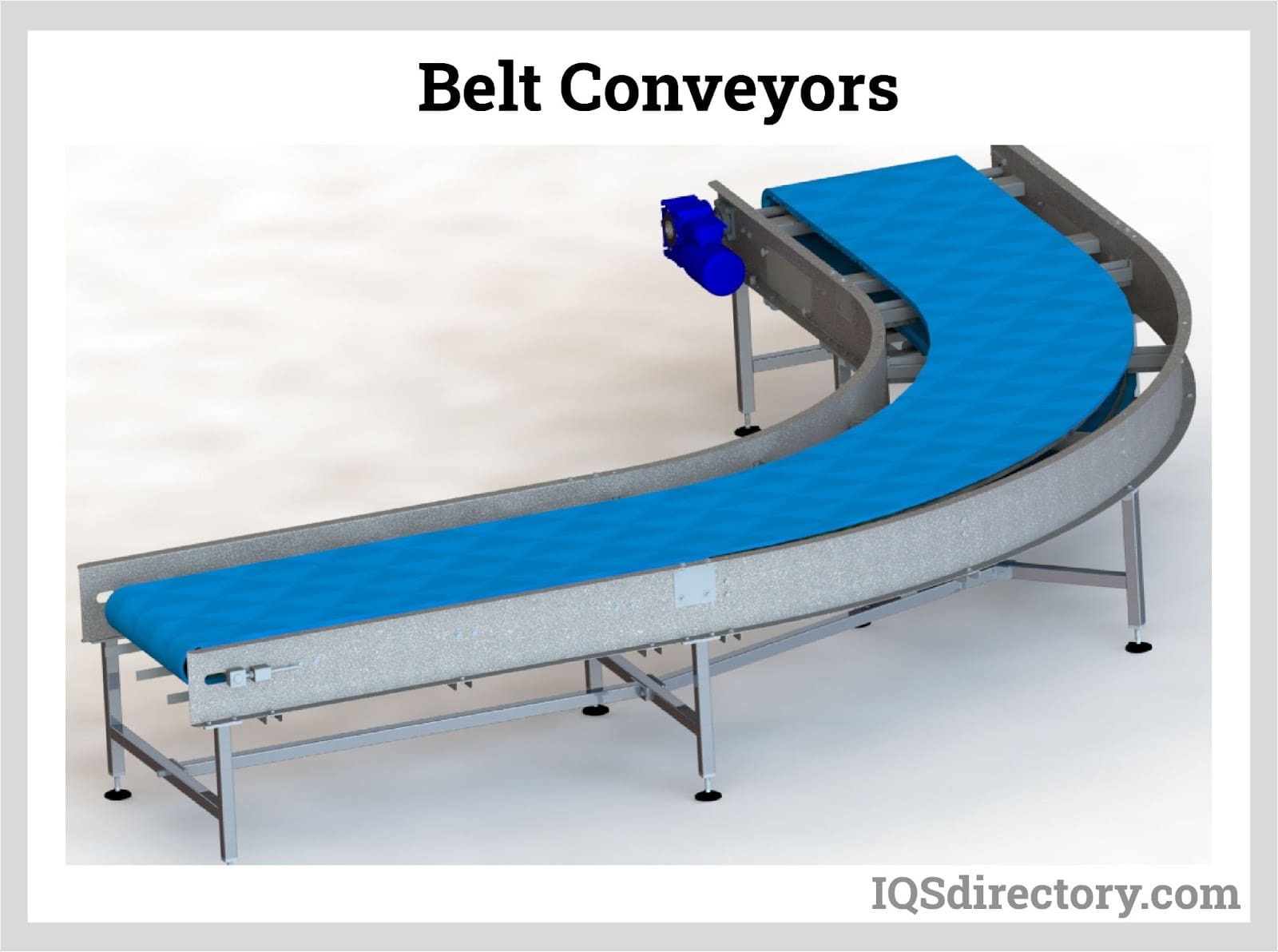
A belt conveyor is a system designed to transport or move physical items like materials, goods, even people from one point to another. Unlike other conveying means that employ chains, spirals, hydraulics, etc...
Please fill out the following form to submit a Request for Quote to any of the following companies listed on
This article takes an in-depth look at roller conveyors.
You learn details on topics such as:
Roller conveyors are part of material handling systems that use a series of evenly spaced cylindrical rollers to move boxes, supplies, materials, objects, and parts across an open space or from an upper level to a lower level. The frame of roller conveyors is at a height that makes it easy to access and load materials manually. Items transported by roller conveyors have rigid, flat surfaces that allow materials to move smoothly across the rollers.
The uses for roller conveyors include accumulation applications, reduction of product inertia, and high speed sorting. Drive roller conveyors have rollers attached to a motor by a chain, shaft,or belt. The use of drive rollers equalizes the velocity at which materials are moved, can be reversible, and can have the capability of moving goods from a lower level to a higher one. They are used in bi-directional applications where the conveyor’s motor can change a product's directional movement.
Roller conveyors have design features that enable them to serve the needs of specific applications. Although roller conveyors vary according to their structure, mode of movement, and other manufacturer features, all roller conveyors have the same basic characteristics.
Powered roller conveyors have small belts and plastic spools that give traction to the rollers. Friction belts or chains placed beneath the conveyor of a powered roller conveyor are used to power its heavy duty rollers and are connected to a shaft that spans the length of the conveyor's frame, which is linked to an electric motor that drives the rollers.
Rollers for roller conveyors are metal cylinders fitted into its frame with sets of bearings on either end of the cylinder. There are several types of conveyor rollers each of which is designed to fit the needs of the product being transported. Rubber and plastic rollers increase friction while steel and aluminum rollers have a smooth surface. Rollers are selected for their ability to keep products on the conveyor, and their ability to maintain the integrity of products.
Plastic conveyor rollers are an economical roller and are designed to handle light loads. They are easy to install and require little maintenance. Plastic conveyor rollers meet the noise standards of the Occupational Safety and Health Administration (OSHA). Since plastic does not corrode, rust, and is resistant to the effects of moisture, they have a longer useful life. Plastic conveyor rollers are easy to clean and are used to transport food packaging in the food industry.
Nylon rollers are used for medium to heavy loads and have the durability and strength that enables them to withstand constant use. They are made of synthetic polymers that are resistant to abrasion, chemicals, and corrosion. Nylon conveyor rollers, like plastic conveyor rollers, are lightweight, easy to install, and produce limited noise due to their low vibration.
Rubber coated rollers have a rubber coating placed over steel, stainless steel, or solid plastic rollers. The rubber layer improves the grip of the roller and provides protection for the roller and products. The types of rubber coatings vary in accordance with the industry where they are used. Rubber coated rollers are resilient, soft, and have the ability to grip smooth materials.
As with all rubber products, rubber coated rollers are anti-static, chemical resistant, customizable and durable. They are used by the automotive industry, printing, and packaging and fabrication. Rubber coated rollers have increased friction between the roller and materials that prevents slippage.
Steel and stainless steel rollers are the most popular conveyor roller materials due to their durability and smooth surface. They are simple to clean, long lasting, strong and capable of moving heavy materials. Steel and stainless steel are used as the core for plastic, nylon, and rubber rollers due to their smooth surface and exceptional strength.
Stainless steel rollers are compatible with any material, can accommodate smaller diameters, have precision bearings or are fixed shafts and can be adjusted to meet shipping needs.
The frames of roller conveyors can be permanently positioned or temporarily placed and are made of steel, stainless steel, or aluminum. The convenience of temporary roller conveyors makes it possible to assemble and disassemble them for repositioning. Of the choices of structural metals, aluminum roller conveyors are lighter and are used for moving lighter loads.
Support legs for roller conveyors come in different sizes, materials, and styles to meet the needs of the conveyor and its loads. They can have a tripod design or “H” design with “H” design legs categorized as light duty, medium duty, and heavy duty. Support legs are made of channel and capable of accommodating different diameter rollers.
Roller conveyor motors are 24 volt DC motors that use less energy and have less torque, which makes them safer. A motorized roller conveyor is divided into zones with each zone having a motor driven roller (MDR) that is connected to the other rollers in the zone. The DC motors are built inside a roller in a zone and are controlled by an operator that determines the speed and direction of the movement of the conveyor.
Non precision bearings, such as sleeve bearings and bushings, have a looser tolerance and lower accuracy. They are made of the same materials as precision bearings and are used for smaller loads and lower speeds. The term “non precision” refers to their lack of accuracy and precision. They are used in applications where tight tolerances are not necessary.
Angular contact ball bearings make contact with the line of action of the load at an angle to the bearing's load. The inner and outer ring raceways of angular contact ball bearings are designed and developed to be positioned close to each other in the bearing axis' direction. This enables them to handle combined radial and axial loads. Types of angular contact ball bearings include single row, double row, and four point contact ball bearings.
In power roller conveyors, angular contact ball bearings support the conveyor line shaft, a long cylindrical rotating shaft that is connected to the rollers by belts and drive spools. When the shaft is powered, it moves the load by powering the rollers. Angular contact ball bearings, shaft, belts, and drive spool make the operation of a roller conveyor quiet and efficient.
Pillow block bearing, also known as plummer block bearing, are means for supporting the shaft. They are commonly used with conveyor systems and have a single bearing that is mounted parallel to the conveyor. Pillow block bearings have a mounting block that houses the bearing and is bolted to a support surface.
The purpose of pillow block bearings is to handle misalignments and deflections of the shaft. They are widely used due to their ability to handle axial and radial loads.
Roller conveyor sprockets are gears that mesh with conveyor chains to transfer rotary motion to the rollers of a powered roller conveyor. The sizes of roller conveyor sprockets vary according to the number of teeth in their gears, power transmission, diameters, and the length of their bore. They can have plastic hubs, which are only used with light to medium loads. Steel hubs provide more strength and are able to handle heavier loads.
Roller conveyor curves are included in a roller conveyor system to change the direction and flow of materials without changing the orientation of the materials. They are designed to move items around corners, curves, and obstacles or equipment. Curve design is influenced by its angle, which needs to be at least 30° and no more than 90° with curve angles of more than 90° requiring special engineering.
Rollers for roller conveyor curves are conical or cylindrical shaped to be able to adjust the radius of the curve. They are designed to handle cardboard boxes, plastic crates, tires, and lightweight items. Roller conveyor curves are adjusted for the size and weight of the goods being transported and have support rollers on their frame.
Additional features of roller conveyor curves include side guides that can have a fixed or adjustable design. Although single curves are the traditional type of roller conveyor curve, S designs are also used as a floor space saving configuration. Spiral roller conveyors spiral from one level of a system to another level and are used in systems that have limited space. Other roller conveyor curves are split, multi-track, and double deck.
There are several forms of roller conveyors, which are differentiated between powered or motor driven roller conveyors and gravity roller conveyors. Of the two types, gravity roller conveyors are the simplest form and operate by products being manually pushed along the surface of the rollers. The term motor driven or powered roller conveyors covers a number of roller conveyors with each type having a different power system.
Gravity roller conveyors are the most basic form of roller conveyor and consist of a frame with rotating rollers, support legs, and the use of gravity to move materials. They transport light to medium weight loads and do not have a motor, which makes them the most cost effective material movement choice.
Made of steel, aluminum, and plastic, gravity roller conveyors can have curves, slide rails, supports and hanging brackets, sensors, and pop up stops. They are used as temporary conveyors and replacements for skate wheel conveyors in heavy duty applications where stacking loads do not need special scheduling. One of the features of gravity roller conveyors is their ability to be positioned during loading and unloading of products to make the process more efficient and less time consuming.
Belt driven live roller conveyors have a motor that powers each roller with a motorized belt that allows for control of the movement of materials. Loads can be halted, turned and side unloaded or slide loaded, and reversed. The power driven belts of BDLR conveyors make it possible to move materials vertically and around curves. Some versions have a shaft that runs perpendicular to the rollers that positions and moves the belts that move the rollers.
Some belt driven live roller conveyors have their rollers set higher than the frame to support goods that are wider than the frame. BDLR conveyors are used to transport clean and dry medium to heavy loads and can be paused or reversed.
Chain driven roller conveyors are powered by a chain drive connected to each roller. The configuration of chain driven roller conveyors is different from a single chain driven roller conveyor that powers the rollers with one long chain. The rollers on a chain driven roller conveyor have sprockets attached to each roller that powers and turns the roller.
Power transfer is high in chain driven roller conveyors, which makes them suited for medium to heavy loads. As with other powered roller conveyors, the power on a chain driven roller conveyor can be reversed allowing movement of materials in both directions.
Applications for chain driven roller conveyors include palletizing, filling, load staging, and strapping. Chain driven roller conveyors are not as powerful as roll to roll powered roller conveyors. They are very durable and provide optimal performance in harsh and hazardous conditions.
Line shaft roller conveyors are driven by a rotating shaft that is attached to the rollers by drive spools and belts with one spool for each roller. The belts for each roller run from the shaft to the spool that turns the roller. When the shaft is powered, it turns the belts that turn the spools that turn the rollers.
A programmable logic controller (PLC) controls the electric motor that turns the shaft. With the absence of chains and sprockets, line shaft roller conveyors operate quietly and smoothly. The shaft runs the length of the roller conveyor and is placed below the rollers to one side of the frame.
A line shaft can power over 100 feet of straight and curved rollers, boosting the conveyor system's efficiency. They are used for accumulation, sorting, low back pressure, and medium to light duty loads
Line shaft roller conveyors are not suitable for hostile or harsh environments and should never be used in wet, oily conditions, at slow speeds, or on inclines. Materials being moved must be able to make contact with three rollers at all times.
With traditional accumulation conveyor systems, materials on the conveyor are allowed to bump into each other and stack up, a condition that creates pressure between materials that can damage the quality of products. In those types of conveying systems, material movement is uncontrolled and continues regardless of products being stopped and stationary.
Zero pressure roller conveyors or pressureless accumulating conveyors have zones driven by 24 volt DC motors controlled by photoelectric sensors. A central controller receives feedback from the sensors that lets it know if the zone ahead for a product has anything in it. If it does, the controller stops movement preventing the build up of back pressure.
Each zone of a zone pressure roller conveyor has a powered roller, sensor, and three or four slave rollers. The powered roller is connected to the controller, which determines when products can leave or enter the zone. The rollers are powered by an internal motor linked to non-powered slave rollers by O-rings.
Zero pressure roller conveyors are available as kits to repurpose older conveyor systems and are used for automation applications requiring timing, rate of movement, and consistency. While more complex and electronically actuated than past roller conveyors, zero pressure roller conveyors are efficient, regulate material flow, and provide a smoother transfer of goods.
Motor driven live roller conveyors have slave drive transportation rollers with small 24 volt DC motors built into the rollers. The conveying system is divided into zones that have a motor powered roller and three or four slave rollers with each zone serving as an accumulation zone. Controller cards control the movement of products and the motors of the rollers using photoelectric sensors.
Motor driven roller conveyors are ideal for accumulation due to their small size. They eliminate the need for PLCs or complex pneumatic systems. The transportation rollers of the system are slave driven using bands that are easily replaced. In order to function with declines, inclines, or speed changes, belts are used with the MDR rollers.
Merge roller conveyors, or combiner roller conveyors, capture products that are flowing from multiple feed lines. They are normally used for collecting products from upstream lines into a single product stream. They are used for light and medium loads with live roller conveyors used to combine two to four lines. The design of merge live roller conveyors includes fixed or powered rollers to combine the infeed.
The major benefit of merge roller conveyors is to reduce the need for manual manipulation of products and their ability to combine upstream and downstream processes. They improve warehouse product flow and further minimize the use of labor for product placement and movement. Merge roller conveyor designs make it possible to easily reposition and reorient them.
Since their introduction in 1908, roller conveyors have become an essential part of product movement, assembly, and supply chain operations. They are versatile and adaptable pieces of equipment capable of handling any size load. Over the years, the use and sizes of roller conveyors has radically changed as new designs and functions are constantly being introduced.
The uses for roller conveyors includes:
Every application for roller conveyors requires a specially designed roller conveyor that precisely fits the needs of an application. The most efficient use of a roller conveyor requires that it be engineered to fit the location where it will be used. Custom designed roller conveyors include various modular units, such as straight segments, curves, transitions between conveyors, mergers, types of power, and separators. Each of these factors has to be carefully considered and worked into a total roller conveyor system.
One of the challenges of developing a custom designed roller conveyor is the determination of whether the system will be a single unit stand alone system or be a more inclusive design with intertwined assets and components. Additionally, it is necessary to examine whether the system will be powered as well as the type of power such as chain, belt, or roller.
Airports make extensive use of roller conveyors, which include check in conveyors, baggage handling systems, and baggage loading. The types of roller conveyors include gravity and powered roller conveyors depending on the type of baggage or package handling.
There are several types of assembly roller conveyors that vary between overhead conveyors, belt conveyors, and roller conveyors. Conveyor systems can be noisy, distracting, and uncomfortable for workers, which is the reason that, when possible, manufacturers use roller conveyors due to their reliability, durability, and smooth and quiet operation.
An important tool of the supply chain and warehousing is the forklift that can quickly move products and goods. Many supply chain managers use roller conveyors to avoid the use of forklifts in product movement since roller conveyors are less expensive, relieve the workload for workers, and make product movement quicker.
The packaging industry has high demand for conveying systems that move packages and for the process of stacking and sorting of packages. Depending on the application, either gravity or driven roller conveyors are used for package processing.
Roller conveyors for the food and beverage industry are challenging to design due to the regulations, restrictions, and standards placed on the industry. In many cases, roller conveyors have to meet three levels of cleanliness to qualify as possible for food and beverage use.
One of the main uses for metal working roller conveyors is the separation and identification of scrap. They are ideal for this purpose due to their heavy construction and versatility.
The few industries listed above are a small sample of the many industries that use and depend on roller conveyors as an essential part of their operation. From automobile manufacturing to robotics, roller conveyors are an important part of product movement.
The popularity of roller conveyors is due to their versatility and ability to adjust to different conditions. Temporary roller conveyors can be moved to where they are needed while permanent roller conveyors are long lasting and sturdy. Since their introduction in the early twentieth century, roller conveyors have found use in a varied number of industries with conventional and unconventional applications.
The Occupational Safety and Health Administration (OSHA) has guidelines for the operation of conveying systems. The American National Standards Institute (ASNI) has safety considerations for conveyor design based on the American Society of Mechanical Engineers (ASME) guidelines. Both organizations continually review and update their standards and requirements to reflect new developments and technological advancements.
Conveyor safety standards are incorporated in:
Conveying systems are machines with interacting pieces that rely on one another to function properly. The various types of roller conveyors are pieces of equipment that necessitate a maintenance schedule to ensure proper performance. To effectively maintain a system and avoid problems, it is important to schedule regular examinations of a conveyor’s components that contribute to its overall performance.
The drive chain and sealed roller bearings must be oiled. Operators should be trained as to the proper inspection procedures in regard to bearings, rollers, shafts, belts, and DC motors.
Driver rollers need to be cleaned to avoid system blockages. Residue or debris collected during material movement must be wiped from the surface of the rollers. Cleaners used on rollers have to be products designed for the specific roller. Stainless steel rollers, for example, must be sprayed with water then washed with a detergent. Preventative maintenance can address minor issues before they become major ones and ensures proper equipment performance
Preventative maintenance involves examining conveyor rollers for flexible and smooth movement, drive chain or belt wear, and how level rollers are. Rollers should move in one direction and the same direction. Wobbling or non-movement of rollers is an indication of a problem, which should be addressed immediately. Since bearings fail due to wear, they should be regularly checked.
As with any tool, roller conveyors that operate continuously endure wear and degradation due to the conditions of the environment where they are used. High temperatures and humid conditions have a negative effect on roller conveyors, which necessitates an increase in the number of times they should be examined. A key to the continued successful performance of a roller conveyor is intervals of downtime that allows the system to cool.
A conveying system can be integrated into an operation in a variety of ways to improve efficiency and speed. There are several factors to consider before installing a roller conveying system in order to customize it to the needs of the application.
Conveying system manufacturers consider the available space while designing a system. This step necessitates the identification of interaction sites, clearances, impediments, or any other areas that may impede material movement. Though automated systems are the most popular, whether the system is motorized or manual is determined by how it is used.
The frame is often made of aluminum or steel, depending on the amount of loading on the system and the value of the rated frame's capacity. Rollers are substantially more variable in composition because they come into direct contact with products and can influence their movement. Some rollers are covered in plastic or rubber to increase friction, while others are just aluminum or steel drums. A properly selected roller keeps products on the line while not compromising its integrity.
The size of the material on the conveyor, as well as the ideal layout of the conveyor, must be determined so that it does not impede the movement of products. Individual roller sizes are determined by the load and loading conditions. Heavy, high impact loads, for example, necessitate large rollers, whereas slow, low impact loads use smaller rollers.
The spacing of rollers is determined by estimating the length of the load touching the conveyor surface and calculating the spacing so that three rollers are at all times in contact with this surface. High set rollers are used for loads that are wider than the width of the conveyor frame. Low set rollers are used to contain products inside the roller conveyor frame.
Once the system has been set out and given a pattern, the quantity of material it can carry must be established. Overloading a system can lead to malfunctions or work stoppages. The overall length, bed breadth, and drive system have an impact on load capacity. Gravity roller conveyors are ideal for flat-bottomed, light to medium weight goods like totes, boxes, and bags but cannot be used with extremely delicate and cumbersome geometries like electronics and manufacturing parts.
A conveying system's speed is measured in feet per minute (fpm). The average speed of most conveying systems is 65 feet per minute, which is how fast a person walks when carrying a 50 pound load. Although this is average, the speed of a roller conveying system can be adjusted to suit the application.
Roller conveying systems are available in a wide range of shapes, styles, sizes, and configurations. They might be straight, angled, horizontal, or curved with pockets or slats as well as z-frames. If hundreds of feet must be crossed, a more efficient design, such as a line shaft roller conveyor, should be considered as a means to conserve energy. Roller conveyors can be installed in any facility or structure as long as careful consideration is given to each of the factors related to its use.
The drive system moves materials on an automated conveying system and has counter bearings to keep goods moving. The convenience of drive systems is their ability to move goods in both directions and be positioned in the middle of the system, its beginning, or its end.
Depending on the design of a drive system, it can have single or variable speeds that are driven by a 24 V DC motor attached to gears, rollers, or a shaft. Variable speed drives allow variations in material flow rates.
Product mobility, control, and the placement of a roller conveyor are additional critical factors that are examined when designing a roller conveyor. The function of a roller conveyor can be affected by heat, dust, dirt, and moisture, which may require the use of more durable designs such as shaft driven or chain driven models. Zero pressure models with precision timing are ideal for conditions where there is possible back pressure. Although gravity models have a simple structure, they are susceptible to the same effects of deterioration that more complex roller conveyors are.
The Occupational Safety and Health Administration (OSHA) regulates conveyor systems, which must meet federal safety standards. The regulations are known and followed by all conveyor manufacturers. Conveying systems are a preventative strategy that keeps personnel from having to lift and transport heavy objects.
Aside from the need for constant maintenance, which is common with any piece of equipment, there are disadvantages to roller conveyors that can limit their selection and use. These factors should be considered such that the chosen type of conveying system meets the needs of the application.
A belt conveyor is a system designed to transport or move physical items like materials, goods, even people from one point to another. Unlike other conveying means that employ chains, spirals, hydraulics, etc...
A bucket elevator or grain leg is used to move items in bulk. The usage of bucket elevators is widespread, notably in commercial agriculture and mining, and several specialized businesses manufacture bucket elevators and...
Processing equipment for holding and moving bulk bags is known as bulk bag equipment. This bulk bag equipment is typically used at the front end of the production process to hand off product to...
A conveyor system is a method for moving packages, products, supplies, parts, and equipment for production, shipping, or relocation. The different types of conveying systems include pneumatic, screw, belt, and roller. The construction of individual systems depends on the materials...
A conveyor belt is a material handling system designed to move supplies, materials, and components using an efficient and effortless process that saves on time, energy, and cost. The design of conveyor belts includes two motorized pulleys with the conveyor material looped over them...
Flat belts are power transmission belts that are flat and made of rubber, synthetic composites, or leather. They are used to transfer rotational power in industrial equipment and conveyor systems. Flat belts have a low profile with a positive grip, which...
A vertical conveyor is an engineered mechanical method for moving goods, products, supplies, parts, and components from a lower level to a higher level or from a higher level to a lower level. They are...
Vibratory conveyors are material-handling equipment used to transport fine to coarse-grained bulk materials. These vibratory conveyors are strong conveying equipment utilized for bulk commodities with fine to coarse graininess...
A machine guard is a mechanism whose role is to act as a safety barrier between a worker and machines used in manufacturing facilities, factories, plants, and warehouses. Furthermore machine guards keep vehicles out of certain areas...
A metal conveyor belt is a conveyor belt that uses metal in the form of flat sheets or woven wire mesh as its belt surface. The use of a metal surface enhances the ability of a conveyor to handle parts and...
Pneumatic conveying is a method for transferring bulk materials, like powders and granules, using compressed gas or air, from one processing center to another. Material is moved through an enclosed conveying line or tube using a combination of pressure differential and airflow from a blower or fan...
Screw conveyors, or auger conveyors, are industrial equipment used in transporting bulk quantities of granular solids (e.g., powder, grains, granules), semi-solids, liquids, and even non-flowing materials from one point to another...
A timing belt is made of rubber with hard teeth capable of interlocking with camshafts and crankshafts cogwheels. It is an integral component of an internal combustion engine responsible for...
A v-belt is a flexible machine element used to transmit power between a set of grooved pulleys or sheaves. They are characterized as belts having a trapezium cross-section...
Vacuum conveyors are suctioning machines that utilize air pressure in order to move materials through an enclosed pipeline. Vacuum conveyors have broad applications throughout the industrial and...