Bucket Conveyors
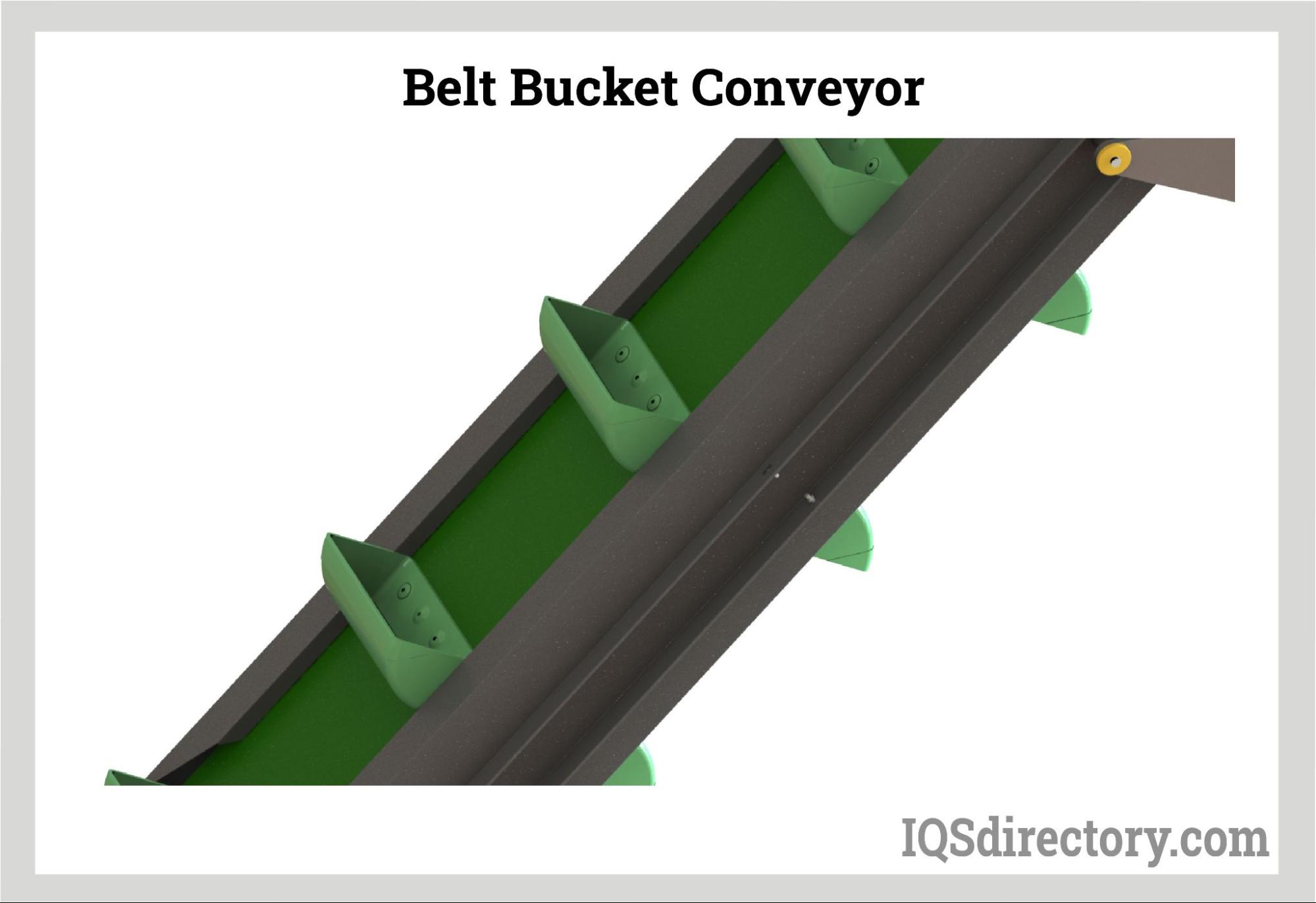
A bucket elevator or grain leg is used to move items in bulk. The usage of bucket elevators is widespread, notably in commercial agriculture and mining, and several specialized businesses manufacture bucket elevators and...
Please fill out the following form to submit a Request for Quote to any of the following companies listed on
This article will take an in-depth look at belt conveyors.
The article will bring more understanding on topics such as:
This chapter will discuss what a belt conveyor is and its components.
A belt conveyor is a system designed to transport or move physical items like materials, goods, even people from one point to another. Unlike other conveying means that employ chains, spirals, hydraulics, etc., belt conveyors will move the items using a belt. It involves a loop of a flexible material stretched between rollers that are actuated by an electrical motor.
Because the items being transported vary in nature, the belt material also varies by the system it is employed in. It commonly comes as a polymer or a rubber belt.
A standard belt conveyor system has a head pulley, tail pulley, idler rollers, belt, and frame.
The head pulley is coupled with the actuator and the electric motor. It drives the conveyor, acting as the pulling force. The head pulley is located at the point that the conveyor offloads, known as the discharge end of a belt conveyor. Since it drives the whole system, it is often necessary to increase the traction of its belt with a rough jacket covering its outer surface. The jacket is referred to as a legging.
The head pulley usually has the largest diameter of all the pulleys. Sometimes a system can have multiple pulleys that act as drive pulleys. The pulley at the discharge end, is a drive roller usually with the biggest diameter, and will be identified as the head pulley.
This is located at the loading end of the belt conveyor. Sometimes it comes with a wing shape to clean the belt by letting material fall aside to the support members.
In a simple belt conveyor setup, the tail pulley will be mounted on guides usually slotted to allow the belt’s tension. In other belt conveying systems as we shall see, tensioning of the belt is left to another roller called the take-up roller.
These are rollers employed along the length of the belt to support the belt and load, prevent sagging, align the belt, and clean up the carryback (material left sticking on to the belt).
Idler rollers can either do all of the above or any one of them, but in any space, they will always act as support for the belt.
There are many different idler rollers for different functions, as listed below:
Troughing idlers will have three idler rollers set up in a configuration that makes a “trough” of the belt. They are located on the side that carries the load on the belt conveyor. The idler in the center is fixed, with the two on the ends able to be adjusted. This is so the angle and depth of the trough can be varied.
These idlers, when employed, will reduce spillages and maintain a constant cross-sectional area along the length of the belt conveyor. Maintaining a constant cross-sectional area is important for stability.
This idler has rubber disks placed at set distances along the axis of the roller. On the extreme ends, the rollers are much closer so that they can support the belt edge, which is prone to tear. The spaced-out disks will break off any connected carryback/ leftover material and reduce material building up on the bottom of the belt. This is a common cause for mistracking (when the belt shifts to one side of the system and causes misalignment).
Sometimes the disks are helical like a screw and the idler will be called a rubber screw idler roller. The function will remain the same. An example of a screw idler roller is depicted below.
The screw idler can also be made out of rubber helix. Screw idlers are most common where a scrapper that takes off carryback would not be feasible, especially on mobile belt conveyors.
Trainer idlers keep the belt running straight. It works against mistracking. It achieves this by a central pivot that swerves the roller back to the center should the belt drift off to one side. It also incorporates two guide rollers to act as guides for the belt.
In setting up a belt conveyor, the belt is perhaps the most intricate.The tension and strength are important since the belt takes a lot of punishment when loading and ferrying the material.
The growing demand for longer conveying lengths has catalyzed the research into new materials, though this always comes at a cost. Stronger belts that adhere strictly to environmentally friendly rules tend to come with high setup costs, sometimes the costs can hardly even be justifiable. On the other hand, if an economical approach is taken, the belt usually fails, resulting in high operating costs. Costs for the belt should usually range below 50% of the total cost for the belt conveyor.
A belt is made up of components such as:
Since this is the skeleton of the belt, it has to provide the tensile strength needed to move the belt and the lateral stiffness for supporting the load. It must also be capable of absorbing loading impact. The belt is a loop so it has to be joined; this is known as splicing. Because some of the splicing methods require the use of bolts and fasteners, the carcass must be able to provide an adequate and firm base for these fasteners.
The carcass is commonly made of steel cord or textile ply. Textile ply is made from fibers like aramid, polyamide, and polyester. If only one ply is used, a PVC-coated textile carcass is also common. Carcasses can have even six layers piled on each other. The carcass can also include the edge protection that is very much needed in bulk conveyor belts.
This is a flexible material made of rubber or PVC. The covers get exposed directly to the weather elements and the working environment. Careful consideration of the covers must be made depending on the intended use. The following usually require attention, flame resistance, low-temperature resistance, grease and oil resistance, anti-static, and food grade.
The carrying side of the conveyor depending on the load, the angle of inclination of the conveyor, and general use of the belt all have special features. It can be corrugated, smooth, or cleated.
Other applications like scrap conveyors in CNC machines will employ a steel belt conveyor since this won’t wear as much as other conventional materials would do.
In food processing industries, PVC, PU, and PE belts are also used for the preservation of food and to minimize contamination.
Plastic belts are fairly new, though due to their vast advantages, they are slowly gaining momentum. They are easy to clean, have a wide temperature range, and have good anti viscosity properties. They are also resistant to acids, resistant to alkaline substances, and saltwater.
The frame, depending on the loading, height of operation, and distance to be covered will vary. They can come in a simple setup that can be represented by a cantilever. They can also be trusses in the case of larger loads. Extrusions of Aluminum are also employed for simple and lightweight operations.
The frame design is a critical aspect of conveyor design. A badly designed frame can cause:
On the frame, other accessories can also be mounted like walkways and lighting as depicted above. Lighting situations will require sheds and guards to protect the material. Loading and discharge chutes can also be mounted. Knowledge of all these possible add-ins is important to avoid uncalculated overloading.
This chapter will discuss the types of belt conveyors. These include:
The surface just under the belt on this version of a conveyor belt is made of a series of rollers. The rollers are closely stacked so that there is hardly any sagging of the belt.
They are suitable for both long and short distance conveying. In some instances, they can be so short that they only employ two rollers for the entire system.
When using gravity to load, the roller belt conveyor is one of the best options to pick. If one used manual loading, the shock would damage the rollers easily since they usually have internal bearings. These bearings plus the generally smooth surface of the rollers greatly reduce friction which makes it easy for conveying.
Roller bed belt conveyors are used mainly where there is hand sorting, assembling, transporting, and inspection. Examples include in:
The flat belt conveyor is one of the most common conveyor types. It is typically used to transport items within a facility. Internal conveyance requires a series of powered rollers/ pulleys to pull the belt.
The belts employed for the flat belt conveyor vary from fabrics, polymers to natural rubbers. Because of this, it becomes versatile in terms of materials to be transported. It is also very easy to align with the tail pulley usually mounted so it can be adjusted to align the belt. It is generally a low speed conveyor belt.
The flat belt conveyor applications include:
In contrast to flat belt conveyors that use a “seamless” loop of a flexible belt, Modular Belt conveyors use a series of interlocking rigid pieces commonly made from plastic or metal. They function more like a chain does on a bicycle.
This gives them a huge advantage over their flexible belt counterparts. It makes them rugged because they can work over a wide range of temperatures and PH levels.
When a section of the belt becomes damaged, one can easily replace that particular section alone rather than the flexible belts where the entire belt would have to be replaced. Modular belts can travel, using only one motor, around corners, straight lines, inclines, and declines.
As much as other conveyors can do the same, it comes at the cost of complexity and funds. For applications that may require the “unorthodox” width greater than the length, type of conveyor, modular belt conveyors will achieve that feat much easier.
Since they are non-metallic, easy to clean, and porous to gas and liquids, modular belt conveyors can be applied in:
Cleated belt conveyors will always have a barrier or cleat in their design. The cleats work to separate equal segments on the belt. These segments keep particles and materials that might otherwise roll back or fall off the conveyor during inclines and declines.
The cleats come in different shapes and sizes which include:
This cleat will be standing at 90 degrees to the belt to give support and flexibility to delicate items. It is most suited to do light jobs and handling small parts, packaged goods, and food products.
Because of its orientation, it can easily resist leverage forces. It can be used to scoop granules and hold them against gravity. It can be employed to hold light to medium weight granules.
These cleats are less than 5cm in height to have the same effect that a trough has. They can be used to transport heavy or big bulks of material because of their relatively short cleat, which can withstand high impacts.
These cleats are used to aid the runoff of liquids after washing off items like vegetables and fruits. Lugs and pegs are a cost-effective way to convey substances and items that do not need to be supported all along the length of the belt such as large cartons or rods. They can also be used to selectively move products that exceed a wanted size and even hold single products in place.
Other uses of Cleated Belt Conveyors include:
This conveyor uses a frame that is fabricated already curved so as to carry items around tight corners. It is used where space is limited and winding conveyors would save space. The curves can go as steep as 180 degrees.
Modular plastics with interlocking segments are used but only if the conveyor has a straight run before it curves. Flat flexible belts will be used if the belt is primarily only curved.
Incline conveyors require tighter tension force, higher torque, and traction on the belt surface to prevent items from falling off the belt conveyor. Thus, they will incorporate a gear motor, a center drive, and a take up. The belt must also have a rough surface to allow for greater traction.
Just like cleat conveyors, these also carry items up a gradient not letting the items fall off. They can also be used to boost the gravitational flow of fluids.
In the pharmaceutical and food industries, sterilization and harsh washing usually need to happen, in line with health and safety guidelines. Washdown and sanitary conveyors are designed to handle sanitary procedures of that nature. The belts employed here are usually flat belts that are relatively thin.
Sanitary wash-down belt conveyors are used in items coming from extreme temperatures like freezers and furnaces. Sometimes they have to work in hot oil or glaze. Because of how well they can handle greasy environments, they are sometimes used to offload oil drums and crates from ships.
A troughing belt conveyor is not a distinct type of belt because troughing can be incorporated in any conveyor type.
It utilizes a belt that forms a troughed shape because of the troughing idler rollers under it.
The troughing idler rollers have a central roller that has a horizontal axis of rotation, the outer two rollers (wing rollers) have an axis lifted at an angle to the horizontal. The angle is usually around 25 degrees. Troughing only happens to the top idler rollers and never really at the bottom.
Higher angles of troughing will cause permanent damage to the belt. If the belt is troughed at steeper angles, it will retain its cup shape and will become difficult to clean, difficult to track as well as break the carcass of the belt. It also might reduce the amount of surface contact with the idler rollers, which ultimately reduces the efficiency of the belt conveyor system.
Trough belts usually operate in one plane, which is either horizontal or inclines, but inclines that are only until 25 degrees. The belt must have a radius big enough so that it can still touch all the rollers in the troughing idler. A sharper angle of troughing means the belt will not touch the center idler roller, thereby undermining the structural integrity of the belt as well as the efficiency of the conveyor system at large.
Magnetic belt conveyors are a transport device used to position and control ferrous metal pieces and parts. They use ferrite or neodymium magnets to transport materials and are ideal for small parts that would not normally fit on a traditional belt conveyor. Magnetic belt conveyors function exactly like traditional belt conveyors. What differentiates magnetic belt conveyors from other conveying systems is their use of magnets to take advantage of material’s magnetic properties.
The magnets on a magnetic belt conveyor are spaced along the bed of the conveyor with sufficient power to resist the effects of gravity. The size of the size the materials has little effect on the efficiency of a magnetic belt conveyor since the strength of the magnets can be changed to meet different conditions and requirements.
Magnetic Belt Conveyors - Magnetic belt conveyors are the most common type of magnetic conveyor because they are easy to construct and operate. They have a magnetized sheet metal belt with permanent magnets or a series of electromagnets that force ferrous materials to stick to the conveyor belt.
Aside from the presence of the magnets, magnetic belt conveyors function like traditional belt conveyors. They are used to move cans of goods, parts, ore, and other metals with magnetic properties and can move products vertically, up inclines, and upside down.
Magnetic Separator Belt Conveyors - Magnetic separator belt conveyors are a specially designed type of magnetic conveyor that are used to separate ore from loose dust and debris. As material moves along the belt, non-magnetic material falls to the side while magnetic material adheres to the belt. Magnetic separator conveyors are divided into dry and wet types. The difference between the two is that dry types do not have to have materials wet to do the separation while the wet type requires material to wet.
When designing a conveyor belt, the major parameters to be considered are:
To aid the selection of the motor, one must first know what the effective pulling force required for the conveyor is.
For a simple horizontal conveyor, the effective pulling force is given by the formula below:
Fu=µR · g(m+ mb+ mR)
Where:
Fu=Effective pulling force
µR =Friction Coefficient when running over roller
g = Acceleration due to gravity
m =Mass of goods conveyed on the whole length of the conveyor
mb =Mass of Belt
mR =Mass of all rotating rollers minus mass of drive roller
For a system on an incline, the effective Pulling force is given as below:
Fu=µR · g · (m + mb+ mR) + g · m · sina
Where
Fu =Effective Pulling Force
µR =Friction Coefficient when running over roller
g = acceleration due to gravity
m = mass of goods conveyed on the whole length of the conveyor
mb =Mass of Belt
mR =Mass of all rotating rollers minus mass of drive roller
a =Angle of inclination
Once the pulling force is determined, it becomes easy to come up with the torque and hence the motor to use and the gearbox will follow after.
The speed of the conveyor will be the circumference of the drive pulley multiplied by the revolutions per unit time.
Vc=D · F
Vc =Speed of conveyor belt in ms-1
D =Diameter of drive pulley in meters.
F =Revolutions of drive pulley per second
Take-up is an important component in maintaining and achieving optimum belt tension. This will contribute greatly to the process and its mechanical stability.
A properly tensioned belt will wear evenly and will contain material evenly in the trough and run centrally when going over the idlers.
All conveyors will always experience some stretch in their length and width. Generally, it is acceptable that a new belt will stretch with an additional 2 percent of its original length. Since this fraction will add to the length of the belt, the entire belt will have a slack. This slack will have to be taken up in order to retain optimum tension.
The longer a conveyor is, the bigger the stretch will be. Using the 2 percent stretch, a 2-meter long conveyor can stretch 40mm, but a 200-meter long conveyor will slack 4 meters.
Take up is also profitable when the belt has to undergo maintenance. In such a case the take-up is simply let loose and the personnel will undertake maintenance with ease.
There are many configurations of take-ups, each having its own pros and cons. The common configurations of belt conveyor take-up are the gravity take-up, screw take-up, and the horizontal take-up.
The screw take-up configuration uses mechanical force to take up all the slack in the belt. It achieves it by adjusting a threaded rod that is attached to one of the rollers, especially the tail roller. This threaded rod will be on each side of the roller so it can also work as an alignment procedure. Since this is a hands-on manual approach, screw take-up is often called manual take-up.
Another style is called the top angle take-up. Though it is also popular, it needs a large and heavy tail frame to archive. The guards also have to be large.
Screw take-ups are a cheap and effective way of controlling belt tension for relatively short conveyors and are the easiest and standard take-up choice for many.
Screw take-ups are usually not suited to lodge the length of the stretch that happens in conveyors longer than 100 meters. In these setups, gravity take-up will be the best approach to belt tensioning.
A gravity take-up assembly uses three rollers where two are bend rollers and the other one will be a gravity or sliding roller that routinely manages the belt tension. A counterweight that will be mounted to the gravity take-up roller pulls down on the belt to preserve tension through gravity. The bend rollers direct the belt slack around the gravity take-up roller.
The full take up assembly is integrated into the bottom of the conveyor frame and makes a continuous tension on the belt. This way of self-tensioning arrangement allows the take-up to easily adjust to sudden spikes in tension or load.
So, the gravity take-up method always maintains the appropriate belt tension and avoids damages to the belt because of sudden load or tension spikes. Since gravity tensioners are self-tensioning, they need less maintenance, unlike the screw take-up method.
Their maintenance is normally needed when the belt has reached the end of its lifespan. That is when it has stretched such that the assembly will have reached the bottom of the set travel distance. When this happens, the conveyor belt will either need replacement or cut and vulcanized. A gravity take-up system is also known as an automatic take-up because it adjusts automatically.
The horizontal take-up is a substitute for gravity take-up but only when space is limited.
This take-up is similar to gravity take-up, but instead of the assembly being located below the belt, it is situated vertically behind the tail roller. This makes it especially beneficial when the conveyor is located on a grade that does not have any additional space under the conveyor.
Because the horizontal take-up will not fall below the conveyor, an arrangement of cables and pulleys is used for tensioning the belt with a weight box. The cables attached to the tail pulley, rides on a carriage which then allows it to be moved in and out of place.
This chapter will discuss the applications and benefits of belt conveyors. It will also discuss common belt conveyor problems, their causes, and the environmental effects on belt conveyors.
Conveyor belts have a wide range of applications across industries. These include:
Other conveyor applications are:
Pulleys are a necessary and essential part of belt conveyors. They help in providing drive tension and changing the direction of the movement of the belt. Belt conveyor pulleys are classified as drive, tension, motorized, snub, wing, and bend pulleys that can be smooth, rubber coated, or cast rubber.
Motorized pulleys are the driving device for a belt conveyor system and consist of a sealed motor and a protected exterior drum, which is driven by the electric motor. The drum supplies traction to drive the conveyor belt. As with most pulleys, motorized pulleys come in a variety of configurations to meet the wide assortment of needs of conveyor manufacturers.
The drive pulley supplies traction to a conveyor belt. Its surface is coated with chevrons or diamonds to supply enough friction between the belt and pulley to move the conveyor belt. They are single or double sided with one or two drives. The number of drive pulleys for a conveyor system is determined by the size of the system.
A bend pulley changes the winding direction of a belt conveyor such that it forms a closed loop. They are used as the tail roller to form the tension roller of the tensioning device and can cause the belt to be redirected. Bend pulleys have the same design as return pulleys with a smaller diameter.
A tension pulley is a return pulley used to create tension on the conveyor belt, which increases the amount of force placed on the pulley. In order to be able to endure the forces placed on the pulley, tension pulleys are solid pulleys. They have multiple uses and are used as return pulleys or can be positioned in any place along the belt. Their preferred position is as close as possible to the drive pulley.
The snub pulley works with the drive pulley. It is used to enlarge the touching areas between the belt and drive pulley. Snub pulleys increase the friction between the conveyor belt and the drive pulley, which makes them ideal for systems that require high drive power or where the conditions are contaminated.
The purpose of a wing pulley is to clear material on the return belt. It is constantly cleaning itself and has excellent traction. There are several different types of wing pulleys including spiral, heavy duty, herringbone.
Magnetic pulleys are part of magnetic conveyor belts and are part of the process of separating ferrous material from non-ferrous materials. They are made of steel with enclosed permanent magnets. As with all magnetic conveyors, they are capable of removing large and small ferrous debris.
A crowned head pulley has a cylindrical middle and tapered ends to help a conveyor belt to be driven without wobbling. They are used with flat belt drives to increase and improve stability. Crowned head pulleys use their tapered ends to force a flat conveyor belt back to the center.
The common assumption regarding belt conveyors is that they are a convenient and easy method for moving, sorting, packing, and shipping of goods and products. They have existed for years in various forms and have made a dramatic change in supply chain efficiency.
The advantages of belt conveyors include:
Regardless of the advantages of belt conveyors, they are complex pieces of equipment that have to be monitored and managed. Some of the concerns that need to be checked are:
The causes of this would include:
The causes of this would include:
The causes of this would include:
The causes of this would include:
Water, petroleum products, chemicals, heat, sunlight, and cold all influence the belt conveyor’s performance and life.
The causes and the effects can be categorized as:
A belt conveyor is a system designed to transport or move physical items like materials, goods, even people from one point to another. Unlike other conveying means that employ chains, spirals, hydraulics, etc., belt conveyors will move the items using a belt. It is critical to be cognizant of the design considerations and applications of various belt conveyors depending on the intended use.
A bucket elevator or grain leg is used to move items in bulk. The usage of bucket elevators is widespread, notably in commercial agriculture and mining, and several specialized businesses manufacture bucket elevators and...
Processing equipment for holding and moving bulk bags is known as bulk bag equipment. This bulk bag equipment is typically used at the front end of the production process to hand off product to...
A conveyor system is a method for moving packages, products, supplies, parts, and equipment for production, shipping, or relocation. The different types of conveying systems include pneumatic, screw, belt, and roller. The construction of individual systems depends on the materials...
Roller conveyors are a type of conveyor belt that allows objects to skate on its surface by using rollers, which are equally spaced revolving cylinders. They transport stuff from one location to another...
A conveyor belt is a material handling system designed to move supplies, materials, and components using an efficient and effortless process that saves on time, energy, and cost. The design of conveyor belts includes two motorized pulleys with the conveyor material looped over them...
Flat belts are power transmission belts that are flat and made of rubber, synthetic composites, or leather. They are used to transfer rotational power in industrial equipment and conveyor systems. Flat belts have a low profile with a positive grip, which...
A vertical conveyor is an engineered mechanical method for moving goods, products, supplies, parts, and components from a lower level to a higher level or from a higher level to a lower level. They are...
Vibratory conveyors are material-handling equipment used to transport fine to coarse-grained bulk materials. These vibratory conveyors are strong conveying equipment utilized for bulk commodities with fine to coarse graininess...
A machine guard is a mechanism whose role is to act as a safety barrier between a worker and machines used in manufacturing facilities, factories, plants, and warehouses. Furthermore machine guards keep vehicles out of certain areas...
A metal conveyor belt is a conveyor belt that uses metal in the form of flat sheets or woven wire mesh as its belt surface. The use of a metal surface enhances the ability of a conveyor to handle parts and...
Pneumatic conveying is a method for transferring bulk materials, like powders and granules, using compressed gas or air, from one processing center to another. Material is moved through an enclosed conveying line or tube using a combination of pressure differential and airflow from a blower or fan...
Screw conveyors, or auger conveyors, are industrial equipment used in transporting bulk quantities of granular solids (e.g., powder, grains, granules), semi-solids, liquids, and even non-flowing materials from one point to another...
A timing belt is made of rubber with hard teeth capable of interlocking with camshafts and crankshafts cogwheels. It is an integral component of an internal combustion engine responsible for...
A v-belt is a flexible machine element used to transmit power between a set of grooved pulleys or sheaves. They are characterized as belts having a trapezium cross-section...
Vacuum conveyors are suctioning machines that utilize air pressure in order to move materials through an enclosed pipeline. Vacuum conveyors have broad applications throughout the industrial and...