Automatic Screwdrivers
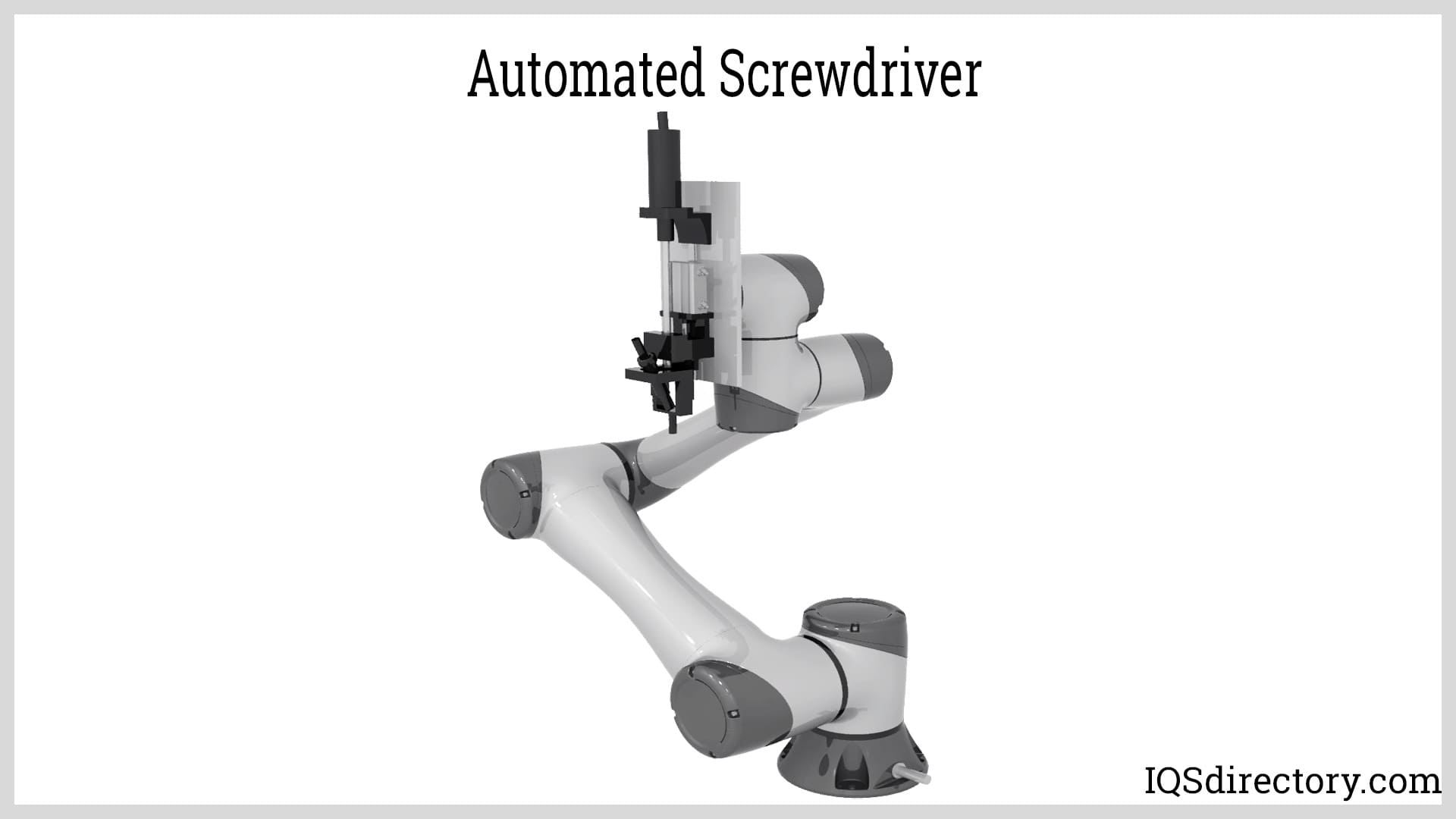
An automatic screwdriver is a piece of equipment that automatically inserts screws into a product during assembly and production. Since every production operation is unique and requires a...
Please fill out the following form to submit a Request for Quote to any of the following companies listed on
This article will give an in-depth discussion about collaborative robots.
The article will bring more understanding about:
This chapter will discuss what collaborative robots are and considerations when selecting a collaborative robot.
Collaborative robots, collaborative robot systems, or cobots are the newest technology in robotics that have significantly changed the landscape of the automation world. They are designed to work with workers in a collaborative fashion to assist in the performance of repetitive tasks. They are able to do this because they have sensors that give them a “feel” for the conditions. If there is an interruption in a robot's operation, they go into safe mode while traditional robots would continue and potentially injure someone.
Collaborative robots come from automation equipment, which is a class of production equipment that is utilized to automatically carry out some production operations. The other types of equipment involve automation cells, conveyors, industrial robots, and special devices such as turn-over machines and lifters.
Collaborative robots use the same tools as other robots in the same positions and applications. Several manufacturers all over the world are concentrating on manufacturing tools for collaborative robots, which allow a robot to learn new operations and become even more versatile. The tools can be split into many categories: Vision, End of Arm Tooling (EOAT), Grippers, Software, Range Extenders, Supply, and Safety Systems.
Vision systems provide the collaborative robot with visibility. With 3D or 2D cameras, cobots can locate objects, recognize patterns, and scan barcodes. This brings many advantages, but the biggest benefit has to do with the product's supply. Normally, a collaborative robot needs organized supplies of objects to pick items up. This is not always necessary with vision because the collaborative robot sees the location of the product. It is also probable to utilize a vision system to perform optical inspections, for instance, checking items for abnormalities. Artificial Intelligence has increasingly provided opportunities in this space.
There are many choices in the space of vision, and the option of a type of system is dependent upon the application the collaborative robot has to do. The difference is in flexibility, cost, and ease of use. As said, there are two kinds of camera types, 3D and 2D.
A 2D camera is low-priced than a 3D camera, but it is also less ample in terms of abilities. These cameras can calculate the width and length of an object, but they aren’t able to measure height as well.
3D cameras can calculate the width, height, and length of an object. This extends the opportunities extremely, but it also has a big price tag. Owing to the height calculation, 3D cameras are impeccable for objects whose heights vary or if objects have to be stacked. For example, packing or palletizing boxes.
End of Arm Tooling is a combined word for all types of tools that can be mounted to a collaborative robot. For example sanders, screw machines, sensors, tools, changers, glue dispensers, welding, and soldering tools. The development of such tools has risen significantly in modern years, so collaborative robots can help more production companies to raise their production capacity.
EOAT has provided a lot of opportunities to teach the cobot new applications. Development of these tooling means in the future even more applications can be made by a cobot. Below is a number of the various EOAT tooling:
A dispenser is utilized to mount a glue or sealant syringe on the end of the cobot. This enables a collaborative robot to move in the desired pathway and distribute glue or sealant very evenly and precisely. Thus, there is little loss of product because exactly how much sealant or glue is needed can be set.
Screwing machines enable collaborative robots to attach products independently or in collaboration with a worker. Screwing is a repetitive, monotonous task that can be boring for humans. A collaborative robot, together with a screwing machine, can simply keep up this job for long durations of time and is also very accurate.
With a sander at the robot’s end, a collaborative robot can sand, polish or deburr surfaces. The built-in sensors ensure that the cobot will continuously do this with the exact same force, which guarantees consistent quality. The robot can be taught to follow a path easily using a user-friendly software.
Collaborative robots have built-in sensors by design to make the cobot collaborative and sensitive. But sometimes there may be extra sensors because a job needs higher sensitivity. An external force torque sensor is available for this task.
Soldering and welding are precise tasks. Collaborative robots are very precise and hence perfect for doing welding tasks. By putting a welding torch or soldering iron to the cobot, it is probable to automate soldering and welding processes.
Grippers allow the collaborative robot to pick up things and place them down again elsewhere. There are many kinds of grippers for different tasks. These include vacuum grippers, magnetic grippers, and finger grippers. Each gripper is appropriate for different tasks. For instance, a vacuum gripper for picking boxes up and a soft gripper for food. There are specifications for grippers, like gripping width, gripping force, and payload.
There are different kinds of grippers that are appropriate for different materials. To know which gripper is most appropriate, it is best to know the weight and the material of the objects that have to be picked up.
Electric grippers are appropriate for more intricate tasks since they can be regulated better on many parameters, for instance finger positions or grip force.
Pneumatic grippers are appropriate for less intricate tasks and are controlled with compressed air. They are frequently somewhat simpler to utilize, cheaper to purchase, have a high grip force, and are less heavy than other grippers.
When precision is needed, three- or two-finger grippers are the best solution. The grippers can adjust to the object’s shape, picking them and holding them firmly.
A variety of applications are available for designing and programming collaborative robot applications. Each collaborative robot has its own instinctive, user-friendly software. In addition, simulating applications are available which can be utilized to construct a solid integration of the robot before continuing to its actual realization.
Traditional robots require a lot of time and knowledge to program movements and can only do a few actions. Unlike traditional robots presently in use in industry, a collaborative robot is simple to program. Through user-friendly programs and mobile software, collaborative robots can learn new moves. A cobot can also be manually moved into needed positions and stored in the software. Because a robot is very simple to program, it can be rapidly implemented into operation, and it is also possible to make them do different tasks.
RoboDK is a dominant and cheap robot simulator. The application package has a broad library of over 500 robot arms while being very user-friendly. No programming knowledge is needed, and robot simulation is swiftly and easily programmed. RoboDK utilizes offline programming, meaning it is possible to program the cobots out of the production space. The application can be utilized for various production projects, such as machine tending, pick-and-place, welding, packaging, and palletizing.
Range extenders enable collaborative robots to gain more range in the horizontal axis and/or the vertical axis and create more possibilities for automation. Normally, cobots work only around their one axis from where the foot is joined. By putting them on a range extender, they can move vertically and horizontally, enlarging the field of operation. Not only does this create more automation possibilities, but it also improves productivity. In the instance of a palletizing application, for instance, robots can stack more and higher boxes. For example, a collaborative robot can move forward and back in front of a big machine to do a job at different points in the operation.
Collaborative robots are categorized by their ease of usage and quick installation. They can be attached to the Range Extenders fast and easily. Owing to user-friendly programs, communicating with the cobot is also simple to set up.
Safety involves all tools that take part in human collaborative robot cooperation’s safety such as screens or sensors which detect when a person is getting very close to the robot.
Supply systems include machines that offer the items to be dealt with to the robot. A tool which always places screws in the same position ready for the cobot and screw machinery helps pick the screws up and bring them together into the final product. Vibrating plates also ensure that accumulated items are parted from each other again.
To make a collaborative robot extra versatile, there are different automatic tool changers in the market. These tools make it conceivable for a collaborative robot to change tools entirely autonomously, enabling it to carry out multiple operations. For instance, in an assembly application, a single collaborative robot would first utilize a gripper to put all the parts in the suitable place, and then utilize a screwdriver to assemble the whole thing. Ultimately, this improves the robot's productivity, creates more output and cuts its return on investment.
The various considerations when selecting a cobot include:
What applications will the collaborative robot take over? What tasks are dirty, dull, hazardous, or physically challenging? Needed requirements – reach, accuracy, payload, and so on. Will a collaborative robot be a better machine than an industrial robot? Which tasks can this fill potentially where there is a gap in staff? Which employees can be moved to more cerebral jobs?
Also looking at the international standard ISO 10218 first and second parts. It discusses the four types of cobot features: stop, hand guiding, speed, safety-monitored and separation monitoring, and force and power limiting. Do they fit the applications?
Secondly, it takes substantial skill to incorporate a cobot. Does anyone in the company have the time and skills needed to do this, or must a systems integrator be used to handle everything? A systems integrator will walk through the machine shop and assuredly tell what works and won’t work. They have performed all types of setups for a number of customers before, and they can offer something that will cost less even though the system integration is being outsourced. The reason is that there is no need to begin from scratch and reinvent the wheel.
Secondly, it takes substantial skill to incorporate a cobot. Does anyone in the company have the time and skills needed to do this, or must a robotic integrator be used to handle everything? A robotic integrator, also known as a system integrator, will walk through the machine shop and tell what works and won’t work. Robotic integrators have performed all types of setups for a number of customers before, and they can offer something that will cost less even though the system integration is being outsourced. The reason is that there is no need to begin from scratch and reinvent the wheel.
A key factor when determining the use of a collaborative robot is risk assessment. Although collaborative robots have sensors that stop their motions such that they don't injure anyone, they can still injure a person even with their sophisticated sensors. For a collaborative robot to be safe and function properly, they need to be fully guarded for the safety of workers.
Thirdly, there must be open communication with every individual, from the executives to be bought-in from to the workers who can be working with a cobot daily if it is implemented.
Collaborative robots are a new invention in the robotics industry, with several types. Programming and safety features determine the different kinds of collaborative robots. Each kind of collaborative robot deploys special technologies and methods for maintaining a safe operating environment.
Power and Force Limiting collaborative robots are what many people think when they hear the name collaborative robots. These cobots are designed to enable direct collaboration with human employees without needing extra safety barriers, external scanners, or vision systems.
Further, improving human safety, force, and power limiting cobots are constructed without exposed motors, sharp corners, or pinch points. For power and force limiting collaborative robots to safely operate alongside human employees, the collaborative robots have sensitive built-in collision monitors. These monitors enable the cobot to sense possible collisions and halt immediately if the cobot comes into contact with a person. Power and force limiting collaborative robots are presently limited to small applications.
Safety monitored stop collaborative robots are frequently used for applications which will have the least human interaction with the cobot. This type of collaborative robot uses a traditional industrial robot attached with different safety sensors to sense when a human enters into the cobot’s workspace. Once the robot senses a human inside the work space, the robot will instantaneously stop working, allowing the human worker to work safely alongside it. Once the human has completed their job, the robot can be re-started by the push of a button.
Speed and separation collaborative robots, also called “fenceless” cobots, work better when there is less interaction with a human, but a human requires easy access to the cobot. Safety laser range scanners are generally utilized to set up areas near the cobot’s workspace. When a person gets close to the robot, its motions slow down, and then halt if that human gets closer to the cobot’s workspace. As soon as the human operator moves away from the cobot’s workspace, the collaborative robot automatically reverts to the normal speed.
Finally, hand guiding collaborative robots feature a safety rated part on the end of the cobot’s arm to enable an operator to manually move or guide the robot around. Hand guidance is frequently utilized to easily and quickly program new cobot paths and positions using a hand. It’s perfect for mobile applications where the robots travel between stations and need retraining to complete different jobs, and when the robot has to be reprogrammed regularly for a new task.
The four main types of collaborative robots described include every kind of robot with the intention of some amount of human interaction while operating. Not all are made for continuous collaboration, but each has a number of safety competencies to avoid serious injury.
Collaborative robots have been a significant development in the automation industry—the first robotics technology which allows safe working directly along human workers. The four types of cobots have emerged in a quite short time, and more are possibly going to arise as the industry matures.
This chapter will discuss the applications and benefits of collaborative robots.
Production work like packing goods, refilling stocks, or assembly line work is categorized as repetitive and monotonous. This kind of work is frequently the source of RSI, Repetitive Strain Injury, which is a condition caused by doing the same movement repeatedly.
By having a robot do the work of a human, the human would be able to concentrate on other tasks. Tasks that need creativity and solution-leaning thinking, like quality control or maintenance.
Giving workers solution-oriented and creative tasks enhances the work they perform and increases a worker’s personal development. It also inspires flexibility and diversity, creating a beautiful work environment. Factors like these ensure that workers find more meaning in the work they perform, become more involved, and productive.
Due to the many tools, comprehensible software and adaptability, cobots are capable of performing a number of tasks. The combination of various abilities means that a countless number of activities can be joined into one whole automation application. In theory, a cobot is able to learn anything. In practice, there are a number of applications which recur very often, as below.
Polishing, sanding or deburring requires a controlled action. Due to built-in sensors, a collaborative robot can follow any line whilst applying a constant force onto the surface. This allows the cobot to offer consistent quality. Ideal for wooden, stainless steel or metallic surfaces.
Simple, monotonous screwing jobs are perfect for cobots. With the proper tools and software, the cobot can simply be programmed to bring into line an object with a hole, put pieces with precision and utilize equal force continuously. It is impossible for people, but a cobot can simply sustain it for 40 hours/week.
Pick-and-place is picking and moving around objects, such as picking pieces from bins and grouping them on treadmills. Pick-and-place is a simple application that can grow in complexity with added tools. Different tools that could be added include a double gripper, sensitive gripper, or materials with different sizes.
Bin picking is relative to pick-and-place, but the objects aren’t conveyed in a standardized way. Due to vision technology and smart software, the cobot identifies materials in a bin, then picks them up one at a time. Bin picking also works for supplying a conveyor belt.
Machine tending puts parts in a bending, CNC lathe machine, or other kind of machine. While the robot carries out its task, operators are free. This improves operator safety and gives them time for higher level tasks. It also improves production and productivity can go on after usual working hours for business flexibility and greater output.
Palletizing can be configured more efficiently by collaborative robots. A box is picked up by an electric vacuum gripper and placed on a pallet. New technologies remove the need for an outer air supply and hoses, which simplifies integration, reduces costs, and makes low noise and causation.
Cobots are useful for inspection and quality testing in a number of industries. For instance, a robot can put objects in a testing equipment and sort them. Based on vision technology, opportunities for cobots to carry out visual inspection are there.
Gluing and sealing are exceptional jobs for a collaborative robot. A glue or sealant syringe is mounted on the cobot end. The cobot travels along the required path and consistently dispenses the sealant or adhesive.
Soldering and welding are jobs that must be done with the greatest precision. Cobots are more precise than people and will provide more consistent quality. Collaborative robots can weld and solder in many applications.
Due to their adaptability and the fact that they can be taught anything, cobots can be utilized anywhere. There are many industries where cobots are perfectly appropriate and have been successfully integrated already.
The need for automation in the food industry has risen in recent years. Several reasons like rising demand, stringent worker safety and food safety are a source of this. Automation for the food industry is more intricate than other industries, since it is difficult for robots to work with food products directly. The arrival of cobots and recent gripper technology changed this.
The plastics industry is categorized by low-volume, high-mix production. This means a wide variety of products in tiny quantities. This type of production procedure is difficult for automation since the production procedure often changes. Collaborative robots changed this since they are simple to alter and can be taught new operations.
In the packaging industry, there’s a rising demand for small sequences and more customization. Collaborative robots can respond to this effortlessly, such as putting products in boxes. In addition, collaborative robots are ideal for stacking boxes on pallets. Operations in the packaging industry are frequently physically repetitive and demanding. By freeing employees of these, production grows and worker satisfaction grows.
The electronics industry frequently operates with tiny products which need to be carefully handled. Collaborative robots are furnished with different sensors that make them sensitive robots. Therefore, they are exceedingly appropriate for working with these types of products. Cobots can be utilized to automate quality control or a testing process.
The pharmaceutical industry frequently works with big quantities, and good inspection is of great importance. It is also imperative that the error margin is as low as possible. These types of features make this industry good for automation. The bigger the production quantity, the more beneficial it is to automate. Because cobots do the same task accurately and frequently, the margin of error is minimized.
The automotive industry has profited from robot automation for years. Big industrial robots have been utilized for car assembly for years. Developments like small series dimensions and a rising demand for customization means that collaborative robots also have become useful for this industry.
In the metal industry, low-volume high-mix production is progressively common. A large selection of products in small quantities. This type of production space is ideal for collaborative robots, since cobots can be rapidly converted if the productivity demands it. Tasks which cobots can perform in the metal industry are soldering, welding, loading CNC machinery, and press brakes.
The benefits of collaborative robots include:
Compact – Cobots are compact, small robots and can hence be utilized just about anywhere in a production operation without taking up a lot of space.
Installing and Programming – A cobot is easy to install by anyone and easy to program. With handy applications and software for desktops and smartphones, a cobot is functioning in no time.
Flexible – A cobot can simply learn new tasks and is thus able to operate in different areas in the production process.
Mobile – Cobots are light and simple to move around. Mounted on a moveable workbench, they can simply perform new jobs at a different place within a company.
Consistent and Precise – Cobots continuously carry out actions in a constant way with an exactly constant force. This guarantees the same quality and accurately arranged parts.
Positive Impact on Employees – Employees are freed from dangerous or monotonous actions and are allowed to develop themselves by carrying out more creative work.
Reduction of Costs of Production – Through the usage of cobots, procedures are efficient and production increases. Ultimately, this causes a better bottom line.
The collaborative robot may need a restricted working space to ensure worker’s safety. The initial cost of configuring the collaborative robot’s cell may be substantial. Work speed could be hampered if there’s safety processes put in place. The collaborative robot might have to halt every time it detects the presence of a person in its working space.
Some collaborative robots are designed to slow down when a human being comes close and totally shut down when he/she is closer to create safety concerns. For better employees and collaborative robot integration, expensive measures might have to be introduced. Since the robots are collaborative, they can’t work in the absence of human supervision and assistance.
The RIA ISO/TS 15066 technical specifications and the ISO 10218 safety standards explain the safety performance and functions of a collaborative robot. Published in 2016 the RIA TR15.606-2016 Cobots document outlines safety needs relative to robot systems and collaborative robots and is a United States Adoption of ISO/TS 15066. Under TS 15066, speed and force monitors of collaborative robots are configured based on human contact area, application data, and workspace hazards.
The RIA TR15.806-2018 Guidance to Testing Force and Pressure in Collaborative Robot Application text gives guidelines on finding conditions of the measurement devices, test measurements, and accurate testing methods. It also outlines metrics and test methods for measuring the forces and pressures associated with transient and quasi-static contact actions of collaborative applications.
Cobots have leveled the playing ground for small to medium-sized industries. For years, large industries have had the benefits of automation by utilizing traditional industrial robots. But these expensive, complex and large robots were made for high volumes, low volume, and constant production operations, opposed to the high-mix production typical of smaller manufacturers.
Collaborative automation has turned into an adaptive, affordable, and user-friendly technology which allows companies of just about any size (and any level of technical capability) to improve productivity, better quality, and respond more rapidly to varying customer demands.
An automatic screwdriver is a piece of equipment that automatically inserts screws into a product during assembly and production. Since every production operation is unique and requires a...
An automation system is an integration of sensors, controls, and actuators designed to perform a function with minimal or no human intervention. The field concerned in this subject is called Mechatronics which is an...
An industrial robot is an autonomous system of sensors, controllers, and actuators that executes specific functions and operations in a manufacturing or processing line. They operate continuously through repetitive...
Robotic system integrators are companies that provide assistance in automating a wide range of applications. They help design robotic technologies that best suit the needs of an operation for a company and solutions as...
Warehouse automation is the process of replacing repetitive tasks with systems that are automated. The main goal is to remove labor-intensive duties that consume time. As a result, the workers can focus more on...
An AGV forklift is a driverless self-operating robotic device that has the ability to carry, lift, retrieve, and place loads for easy transfer from one location to another. An automatic guided vehicle (AGV) forklift is a computer controlled mechanism that...
Automated guided vehicles (AGV) or mobile robots are types of guided robotic systems that are not bounded by a fixed range of motion. Rather, it is self-contained and can move along a line, surface, or space...
An autonomous mobile robot (AMR) is a self-propelled self-powered mechanism designed to perform repetitive tasks or organizational functions using an internal guidance system. They are able to navigate their...
A belt conveyor is a system designed to transport or move physical items like materials, goods, even people from one point to another. Unlike other conveying means that employ chains, spirals, hydraulics, etc...
A bowl feeder is a mechanism for supplying small parts and components to a production line or for sorting bulk items for rapid use. A self contained bowl feeder system has a bowl that sets on a spring loaded base that moves vertically...
A conveyor system is a method for moving packages, products, supplies, parts, and equipment for production, shipping, or relocation. The different types of conveying systems include pneumatic, screw, belt, and roller. The construction of individual systems depends on the materials...
Palletizing is the process of putting items on a pallet. The process of emptying the loaded objects in the reverse pattern is known as depalletizing. A pallet is a flat, square-shaped platform used to transport and...
A pallet stacker is a machine designed to assist the user in lifting, moving and handling palletized materials with ease. A pallet itself is a flat and horizontal structure used to support goods in a sturdy fashion...
A palletizer is an automated material handling machine used to stack and orient several individual products into a single load for a more convenient and economical method of handling, storage, and shipment. Palletizers are usually part of a bigger packaging process...
Pneumatic conveying is a method for transferring bulk materials, like powders and granules, using compressed gas or air, from one processing center to another. Material is moved through an enclosed conveying line or tube using a combination of pressure differential and airflow from a blower or fan...
A robotic palletizer is a type of palletizer that employs a robotic arm to pick, orient, and place individual products and arrange them into a single stack of load. They are the next generation of palletizers, and they will supersede conventional palletizers...
Roller conveyors are a type of conveyor belt that allows objects to skate on its surface by using rollers, which are equally spaced revolving cylinders. They transport stuff from one location to another...
Screw conveyors, or auger conveyors, are industrial equipment used in transporting bulk quantities of granular solids (e.g., powder, grains, granules), semi-solids, liquids, and even non-flowing materials from one point to another...
Vibratory conveyors are material-handling equipment used to transport fine to coarse-grained bulk materials. These vibratory conveyors are strong conveying equipment utilized for bulk commodities with fine to coarse graininess...
A vertical conveyor is an engineered mechanical method for moving goods, products, supplies, parts, and components from a lower level to a higher level or from a higher level to a lower level. They are...
Vibratory feeders are short conveyors used to transport bulk materials utilizing a controlled vibratory force system and gravity. The vibrations impart a combination of horizontal and vertical acceleration through tossing, hopping, or sliding-type of action to the materials being handled...
In 1954, when Arthur "Mac" Barrett, of Barrett Electronics Corporation, unveiled the first AGV, he named it Guide-o-Matic and described it as a driverless vehicle...