Automatic Screwdrivers
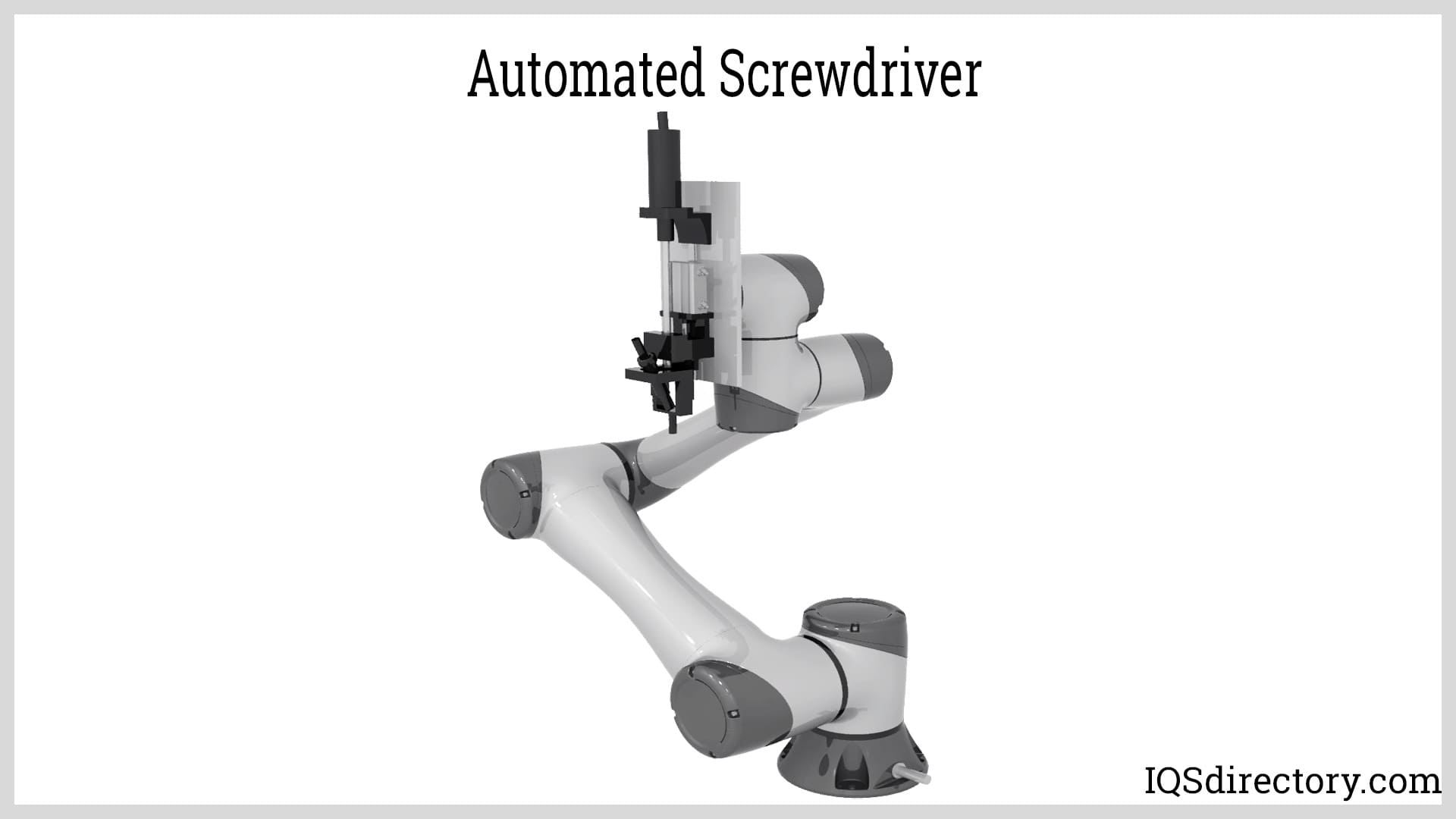
An automatic screwdriver is a piece of equipment that automatically inserts screws into a product during assembly and production. Since every production operation is unique and requires a...
Please fill out the following form to submit a Request for Quote to any of the following companies listed on
This article takes an in-depth look at industrial robots.
Read further to learn more about topics such as:
An industrial robot is an automated system composed of sensors, controllers, and actuators mounted on an articulated frame. It performs specific tasks and operations in manufacturing or processing environments. These robots operate continuously, executing repetitive movements based on a programmed set of instructions. By reducing or eliminating the need for human intervention, industrial robots enhance processing speed, capacity, and quality.
Traditional industrial robots must not be confused with a newer robotic technology called collaborative robots. Collaborative robots, or cobots, work closely and simultaneously with a human operator. They are safe to use around human operators as they have a maximum speed limit for cobot operation and are limited as to how much force they can generate. This, along with more precise motor current sensing, allows them to stop if encountering an object or an operator.
The core structure of an industrial robot is its arm, which consists of links and joints. Links are rigid segments that extend throughout the robot's range of motion, while joints connect these links and allow for either translational (prismatic) or rotational (revolute) movement. The arrangement and configuration of these components determine the various types of industrial robots.
Central to the robot's functionality is the end-of-arm-tool (EOAT), or end effector. The EOAT is the part of the robot that interacts with the product or process by performing tasks such as moving or orienting. It is responsible for executing specialized operations, including welding, measuring, marking, drilling, cutting, painting, and cleaning.
When implementing an industrial robotic solution, a process owner can choose between working with a manufacturer or an integrator. An industrial robotics manufacturer is a company that produces robots in-house, often referred to as original equipment manufacturers (OEMs). Being responsible for the design and production of the robots, manufacturers are well-positioned to offer expert guidance on the installation, operation, and maintenance of their machines.
An industrial robot integrator supplies robotic systems that are made by an OEM. A robot integrator, or “system” integrator, can provide a complete “turn-key” robotic work cell with parts feeders, end effectors, and guarding to form a complete work cell. Robotic integrators have a wider array of solutions since they can offer more products and represent more than one company for each robot category.
This chapter explores the benefits of integrating industrial robots into a manufacturing system. Although the initial investment and capital costs can be substantial, industrial robots offer numerous economic and intangible advantages. Their efficient performance often leads to a return on investment within 2 to 5 years, making them a valuable addition to manufacturing operations.
Faster Rate of Production: Higher production rate is the number one reason for investing in an industrial robot system. Robots do not experience fatigue nor slow down after continuous operation. They can efficiently reduce production times when designed, operated, and maintained properly. Their processing speed is much faster than humans. This allows them to perform a calculated, quick series of movements, regardless of the complexity.
Higher Load Capacity: Industrial robots have actuators several magnitudes stronger than their human counterparts. The typical "muscle" in an industrial robot is a "servo motor." These motors are sized for the particular robot and can be sent to a precise position, enabling modern robots to reach repeatability numbers of better than .003". The servo motors, coupled with high precision planetary or cycloidal gearboxes, can generate tremendous forces to suit almost any task. These factors allow robots to easily and efficiently lift heavy weights that are far from the capabilities of manual labor.
Improved Safety: Common workplace hazards include extreme temperatures, high pressures, heavy loads, fast movements, and high-speed rotations. Industrial robots are useful in operations involving these hazards to eliminate the risk of injury or fatalities. They can better withstand harmful working conditions than their human counterparts. Moreover, robots improve workplace safety since they do not make mistakes or cause accidents due to poor judgment as with human operators.
Lower Operating Cost: Less wasted raw material and fewer human resource costs are some of the economic benefits of industrial robots. Once the robotic system is invested in, there are operating savings, better product quality, and a faster production rate. Efficient use and handling of raw materials are due to robotic systems' accurate and precise operation. This can lead to lower product rejection rates. Regarding workforce costs, manual labor operations are usually more expensive for the same volume of work. Many miscellaneous costs associated with manual labor, such as government-mandated benefits, living allowances, and training, are not associated with the cost of operating a robotic system.
Better Repeatability and Precision: A robotic system's manner of doing work is consistent despite running after hundreds or thousands of cycles. Without human intervention or change in their programming, robots can efficiently execute the same sequence of operations repeatedly and precisely. Its movement patterns, range of motion, force exerted, speed, and other operating parameters are minimally affected by external factors. This leads to consistent and predictable product quality and operating rates.
High Accuracy: Robotic systems inherently have higher operating accuracy than human operators. They can easily perform the exact actions intended by their program. This characteristic is important in manufacturing processes that require tight tolerances, such as automotive and aircraft parts production. The accuracy and repeatability of a robotic system come through the use of precision rotary encoders, which give precise position information to the robot's controller that uses the information to control the robots speed, movement profile, and end-of-point positioning.
Excellent Product Quality: Today, industrial robots are the equipment behind many precision manufacturing processes. This is attributed to both repeatability and accuracy. These characteristics allow the robot to produce products with consistent properties that are free from errors caused by common mistakes and subjective judgment.
Robots can be fitted with the right types of end effectors to perform the work properly and smoothly without causing damage to the finished product. Some robots are even used to perform delicate surgical operations under the supervision of the operating team and MDs.
More Compact Production Area: The higher load capacities, faster throughput, and integrated end effector of industrial robots can save space. There is no need for additional equipment to aid human operators in performing their job. Production through manual labor typically requires a larger space for accommodating several workstations to increase the manufacturing line’s throughput. The same may be able to be achieved by a single industrial robot.
While industrial robots are frequently used for basic pick-and-place operations, they also perform a range of more complex and critical functions thanks to advanced control technologies, powerful actuators, and sophisticated sensors. Below are some of the most prevalent applications of industrial robots:
Product Assembly: Industrial robots are widely used as assembly machines. They are suitable for highly repetitive but precise tasks that are tedious for a human operator. Their EOAT is usually mechanical grippers that pick, place, and orient small or large parts in quick succession. Sensors are optional and are typically used for recalibrating the accuracy of the robot‘s movements.
Modern end effectors are usually equipped with sensors to ensure that they have the correct part and the part is in the correct orientation for the assembly process. In addition, some robots can use a machine vision camera attached to the end effector to perform dynamic positioning based on the actual location of an assembly that may vary during production.
Non-Conventional Machining: Common non-conventional methods of machining include waterjet cutting, laser cutting, abrasive jet machining, electric discharge machining (EDM), and plasma cutting. These non-contact machining processes perform material removal by using highly concentrated streams of water, light, electric charge, or another physical entity. The concentrated stream erodes, vaporizes, or melts the material.
High amounts of energy are involved in these processes, potentially damaging the product or the machine itself if not controlled properly. Industrial robots are used to control the cutting path of the machine accurately. The right cutting speed, stream stability, and accurate control of machine parameters such as power, pressure, and flow rate are properly maintained using digital industrial robots.
Palletizing and Depalletizing: Palletizing is the process of combining several individual products into a single load for more efficient product handling, storage, and distribution. On the other hand, depalletizing is the opposite: it‘s the disassembly of a palletized load. Both of these processes are labor-intensive and can quickly become process bottlenecks. Robotic palletizers are used for their better product handling and cost-efficiency. EOATs integrated into robotic palletizers are mechanical, pneumatic, and vacuum grippers that operate by picking, orienting, and stacking items, similar to the operation of assembly machines.
Painting and Coating: Painting and coating is a sensitive operation that requires highly accurate and repeatable movements to create a layer with uniform thickness. On top of the required accuracy and precision, painting involves working with potentially hazardous chemicals. Many pigments and solvents are poisonous, and some can even create an explosive atmosphere. All these hazards are mitigated by using industrial robots.
Deburring: Another capability of modern industrial robots is deburring. This is a process where the robot holds a rotating tool, usually a sanding drum, wire wheel, or carbide deburr tool, and follows a pre-programmed path to deburr and smooth parts from casting or injection molding. The advantage of using a robot for deburring is that there is usually debris or dust that the operator would be exposed to during the deburring process. Since a robot's path is repeatable, there is better consistency in smoothing between parts.
Inspection: Robotic inspection systems can use measuring devices such as optical sensors, proximity sensors, force transducers, ultrasonic probes, and even complete machine vision systems to perform inspection tasks on parts or assemblies. These machines are typically used to precisely measure the dimensions of a product to maintain quality and consistency. Other inspection applications include non-destructive testing (NDT) of welds, wherein a robotic system automatically moves and controls ultrasonic probes or arrays.
Industrial robots are categorized based on their arm configuration, which consists of links and joints. By altering the number and type of these components, robots can be configured in various ways. Below are the six main types of industrial robots.
Cartesian Robot: A Cartesian robot is composed of three prismatic joints. Thus, the tool is limited to linear motion at each axis but can still generate circular moves through kinematic models that allow circular interpolation.
The name Cartesian is derived from the three-dimensional Cartesian coordinate system, which consists of X, Y, and Z axes. Cartesian robots are the simplest robotic system since their operation may only involve translational movements. They are suitable for applications that only require movement at right angles without the need for angular translations.
Since one or two of a cartesian robot’s prismatic joints can be supported at both ends, they can be built to handle heavier loads than other robot types. An example of a Cartesian robot is a gantry machine. Gantry machines, also known as gantry cranes, are used to pick and place large, palletized loads.
Polar Robot: Polar robots, also known as spherical robots, use the three-dimensional polar coordinate system r, θ, and φ coordinate. Instead of having a work envelope in the shape of a rectangular prism, polar robots have a spherical range. Their range of motion has a radius equal to the length of the link connecting the EOAT and the nearest revolute joint. This configuration allows polar robots to have the farthest reach for a given arm length compared to other robot types. The range of a polar robot can be further extended using a second link connected by a prismatic joint. Because of their wide reach, polar robots are commonly used in machine loading applications.
Cylindrical Robot: As the name suggests, a cylindrical robot has a cylindrical range of motion. This type consists of one revolute joint and two prismatic joints. The revolute joint is located at the arm's base, allowing the rotation of the links about the robot's axis. The two prismatic joints are used for adjusting the radius and height of the robot’s cylindrical work envelope. In compact designs, the prismatic joint used for adjusting the arm’s radius is eliminated. This one revolute, one prismatic joint configuration is useful in simple pick and place operations where the product feed is located only in one place.
Selective Compliant Articulated Robot Arm (SCARA): A SCARA is a type of robot with an arm that is compliant or flexible in the horizontal or XY-plane but rigid in the vertical direction or Z-axis. Its translational movement on a single plane describes its “Selective Compliant” characteristic. A SCARA has two links, two revolute joints, and a single prismatic joint. The links and the base are connected by the revolute joints oriented at the same axis. The prismatic joint is only for raising or lowering the EOAT. The resulting work envelope of a SCARA is a torus. Its application is similar to that of a cylindrical robot.
Delta Robot: A delta robot consists of at least three links connected to an EOAT and a common base. The EOAT is connected to the links by three undriven universal joints. On the other hand, the base is connected by either three prismatic or revolute-driven joints. The driven joints work together to allow the EOAT to have four degrees of freedom. For designs using prismatic joints, a fourth link or shaft is usually connected to the EOAT to enable rotation. The EOAT of a delta robot can move along all Cartesian axes and rotate around the vertical axis, resulting in a dome-shaped work envelope. The simultaneous action of the three driven joints makes delta robots suitable for high-speed pick and place applications.
Articulated Robot or Anthropomorphic Robot: Articulated robots are the most common robots used in manufacturing processes. They perform more complex operations such as welding, product assembly, and machining. EOATs mounted on articulated robots are designed to have a full six degrees of freedom. The robot arm consists of at least three revolute joints. A fourth revolute joint can be added to the wrist of the arm for rotating the EOAT. Its work envelope is also spherical, similar to that of the polar robot type.
When selecting a specific robot, various design factors must be considered. Different applications demand specific performance parameters that must be weighed against the required investment. While higher specifications generally offer better performance, the associated costs increase almost exponentially.
Number of Axes or Degrees of Freedom: The number of axes and degrees of freedom define the ability of a robot to move and orient the EOAT across a three-dimensional space. The definition of the degrees of freedom is in regard to the direction of a motion and the types of motion. The six degrees of freedom are forward or backward, up or down, left or right, yaw, pitch, and roll. Depending on a robot’s design, it can have all six axes, with a higher number giving it greater flexibility for its robotic arm.
Typical industrial robots used in simple pick and place applications have three to five axes, while robots used for more versatile applications have a full six degrees of freedom or more. For example, an assembly robot may have four degrees of freedom, while a robot performing complex operations such as welding may have over six degrees of freedom to be able to perform highly complex procedures.
Accuracy and Repeatability: These are the two main characteristics determining the effectiveness of a robot in performing its tasks. Accuracy refers to the ability of a robot to position itself or its load at a specific point, which is measured by determining how close its final state is to a set state defined by the user.
Repeatability is the measure of how the robot maintains its final position across several operating cycles. This is measured by getting the average of the distances between the final positions of the EOAT or a point on the robot after each cycle. Repeatability is the primary concern when selecting a robot, as a pre-programmed position can always be “touched up” to get the robot where it needs to be, but the repeatability of a robot defines the consistency of an operation.
These usual definitions of accuracy and repeatability are known as the static case, which pertains to the ability of the robot to bring itself to a certain displacement. They are used to evaluate the path, position, and orientation of a robot and are necessary factors that must be achieved every time a robot and end effector is set in motion.
These usual definitions of accuracy and repeatability are known as the static case, which only pertains to the ability of the robot to bring itself to a certain displacement. Accuracy and repeatability can also be applied to the speed and acceleration of the robot.
Work Envelope: The work envelope is the spatial specification of a robot, which is defined by its swept area, reach, and stroke. The work envelope's essential part is the space the robot's EOAT can access. The size of the work envelope depends on the type of robotic arm (Cartesian, polar, SCARA, etc.) and the length of its linkages. The parameters of the work envelope are important for machine loading and unloading applications. A larger robot requires a bigger work envelope that necessitates greater space, which must be determined prior to installation.
The function of the work envelope is to control and define the area a robotic arm may reach, which is important for creating safe zones for workers in the area of the robot. Understanding the work envelope is essential since everything a robot does is associated with its work envelope.
An automatic screwdriver is a piece of equipment that automatically inserts screws into a product during assembly and production. Since every production operation is unique and requires a...
An automation system is an integration of sensors, controls, and actuators designed to perform a function with minimal or no human intervention. The field concerned in this subject is called Mechatronics which is an...
Collaborative robots, also abbreviated as Cobots, are the newest technology in robotics. They have changed the automation world significantly. These robots can work safely together with workers, hence are...
Robotic system integrators are companies that provide assistance in automating a wide range of applications. They help design robotic technologies that best suit the needs of an operation for a company and solutions as...
Warehouse automation is the process of replacing repetitive tasks with systems that are automated. The main goal is to remove labor-intensive duties that consume time. As a result, the workers can focus more on...
An AGV forklift is a driverless self-operating robotic device that has the ability to carry, lift, retrieve, and place loads for easy transfer from one location to another. An automatic guided vehicle (AGV) forklift is a computer controlled mechanism that...
Automated guided vehicles (AGV) or mobile robots are types of guided robotic systems that are not bounded by a fixed range of motion. Rather, it is self-contained and can move along a line, surface, or space...
An autonomous mobile robot (AMR) is a self-propelled self-powered mechanism designed to perform repetitive tasks or organizational functions using an internal guidance system. They are able to navigate their...
A belt conveyor is a system designed to transport or move physical items like materials, goods, even people from one point to another. Unlike other conveying means that employ chains, spirals, hydraulics, etc...
A bowl feeder is a mechanism for supplying small parts and components to a production line or for sorting bulk items for rapid use. A self contained bowl feeder system has a bowl that sets on a spring loaded base that moves vertically...
A conveyor system is a method for moving packages, products, supplies, parts, and equipment for production, shipping, or relocation. The different types of conveying systems include pneumatic, screw, belt, and roller. The construction of individual systems depends on the materials...
Palletizing is the process of putting items on a pallet. The process of emptying the loaded objects in the reverse pattern is known as depalletizing. A pallet is a flat, square-shaped platform used to transport and...
A pallet stacker is a machine designed to assist the user in lifting, moving and handling palletized materials with ease. A pallet itself is a flat and horizontal structure used to support goods in a sturdy fashion...
A palletizer is an automated material handling machine used to stack and orient several individual products into a single load for a more convenient and economical method of handling, storage, and shipment. Palletizers are usually part of a bigger packaging process...
Pneumatic conveying is a method for transferring bulk materials, like powders and granules, using compressed gas or air, from one processing center to another. Material is moved through an enclosed conveying line or tube using a combination of pressure differential and airflow from a blower or fan...
A robotic palletizer is a type of palletizer that employs a robotic arm to pick, orient, and place individual products and arrange them into a single stack of load. They are the next generation of palletizers, and they will supersede conventional palletizers...
Roller conveyors are a type of conveyor belt that allows objects to skate on its surface by using rollers, which are equally spaced revolving cylinders. They transport stuff from one location to another...
Screw conveyors, or auger conveyors, are industrial equipment used in transporting bulk quantities of granular solids (e.g., powder, grains, granules), semi-solids, liquids, and even non-flowing materials from one point to another...
Vibratory conveyors are material-handling equipment used to transport fine to coarse-grained bulk materials. These vibratory conveyors are strong conveying equipment utilized for bulk commodities with fine to coarse graininess...
A vertical conveyor is an engineered mechanical method for moving goods, products, supplies, parts, and components from a lower level to a higher level or from a higher level to a lower level. They are...
Vibratory feeders are short conveyors used to transport bulk materials utilizing a controlled vibratory force system and gravity. The vibrations impart a combination of horizontal and vertical acceleration through tossing, hopping, or sliding-type of action to the materials being handled...
In 1954, when Arthur "Mac" Barrett, of Barrett Electronics Corporation, unveiled the first AGV, he named it Guide-o-Matic and described it as a driverless vehicle...