Automatic Screwdrivers
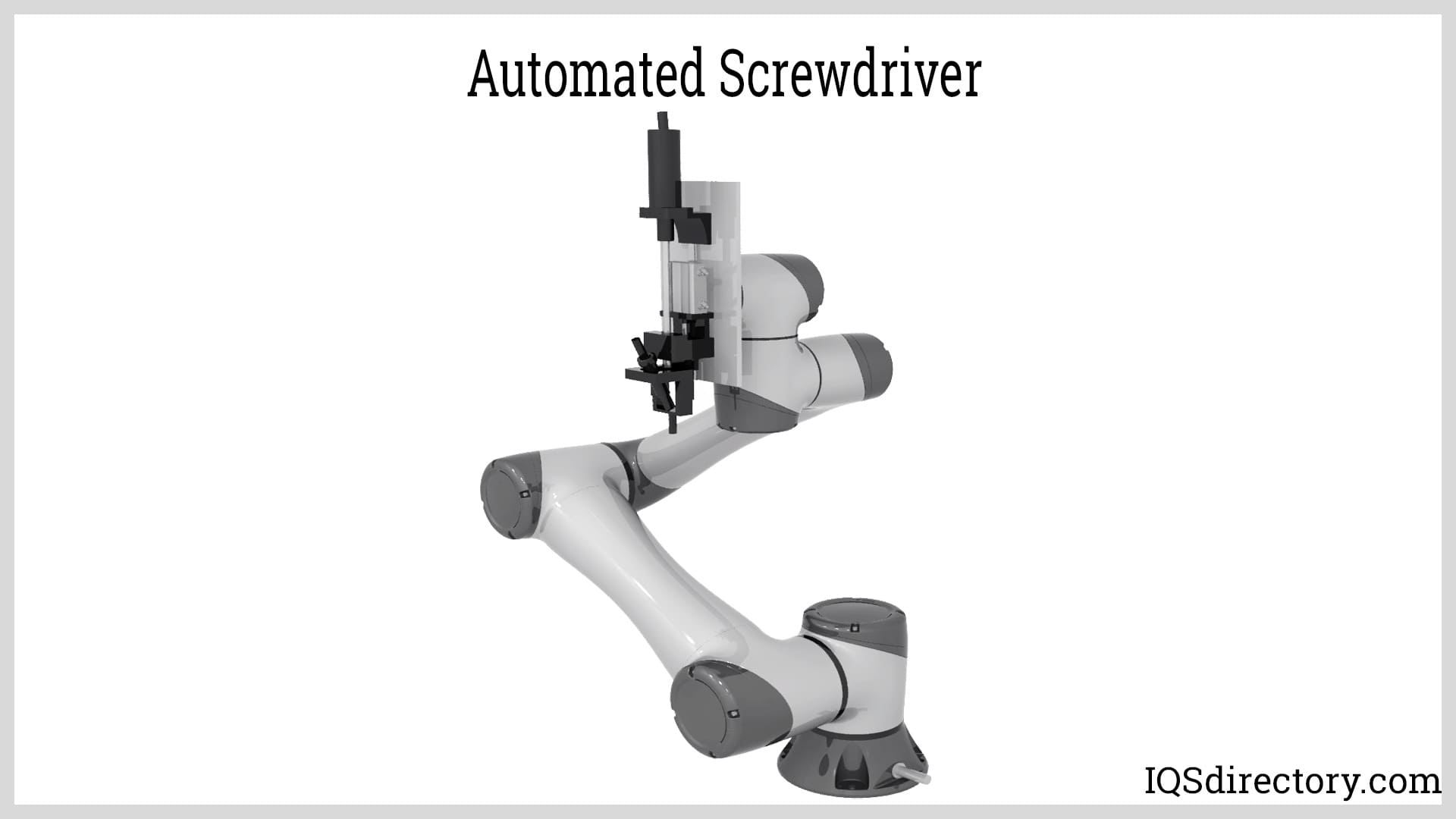
An automatic screwdriver is a piece of equipment that automatically inserts screws into a product during assembly and production. Since every production operation is unique and requires a...
Please fill out the following form to submit a Request for Quote to any of the following companies listed on
This article contains everything you need to know about robotic system integration and its use.
You will learn
Robotic system integrators are companies that provide assistance in automating a wide range of applications. They help design robotic technologies that best suit the needs of an operation for a company and solutions as to how to incorporate robotics into an industrial process. Robot manufacturers produce an infinite number of robotic solutions for a wide variety of applications, which are designed for general use.
Manufacturers of robots rely on robotic system integrators to use their expertise and knowledge to assist end users with choosing the correct robotic solution to fit a unique set of conditions. Robotic system integrators play a critical role in channeling, distributing, and creating automated robotic solutions.
Each robot integrator specializes in a certain set of solutions since it is not possible for an integrator to have a solution for every possible situation. Integrators are selected in accordance with the process they are integrating and have the skill set that fits an application. They are chosen in accordance with their success in providing solutions for a particular application.
The focus of robot system integrators varies between material handling, warehousing, and supply chain robots and ones for manufacturing, production, and assembly. Customers choose a robot system integrator dependent on the integrator’s specialty.
In many ways, a robotic system integrator is a partner that works with their clients to develop the perfect solution for the client’s production challenges. The essential and most distinguishing characteristic of a robotic system integrator is their knowledge and understanding of robotic solutions. After a detailed examination and evaluation of a client’s processes, a trained robotic system integrator will provide an outline of the various approaches to implementing robotic solutions.
Of the many factors regarding the selection of a robotic system integrator, experience is the most vital parameter. The definition of experience extends beyond having knowledge of robotic systems and how they work but applies to the industries with which they have worked. A robotic system integrator that specializes in material handling would be unqualified to produce a robotic solution for an assembly operation, and an expert in welding robotic methods would be unable to assist in inventory applications.
In the initial steps in searching for a robotic system integrator, clients have to be aware of the many varieties and types of specialists and select one that has knowledge of their particular industry and processes.
A robotic system integrator with experience in a specific industrial or supply chain function must be aware of the best solutions available. In many cases, clients are completely unaware of the intricacies and complexities of robotic capabilities. They depend on their robotic system integrator to provide them with the highest quality solutions to perfectly match their operation.
One of the challenges of being a robotic system integrator is developing a customized plan for every client since no one solution applies to all applications. Robot manufacturers produce thousands of different robotic systems that can be used in a wide array of industrial operations. Each device is of the highest quality and performs to its expectations. It is the job of the robotic system integrator to know the many available solutions and choose the correct combination of solutions for the client.
Once the selection process is completed, the robotic system integrator outlines a plan of how to implement and deploy the robots in the client’s environment. Each step of the plan clearly details the various robots and how they will interact without interfering with each other’s functions.
The plan is the next important key to the success of a robotic implementation. The client needs to have a clear understanding of how each of the elements work together to improve efficiency, maximize up time, enhance productivity, and reduce cost in comparison to their present operation.
A major factor of the plan is the financial, technical, regulatory, and safety factors that are the obligation of the client with the financial aspect clearly delineated. Clients will take the cost factors and compare them to their present operation. The robotic system integrator may have to point out that the initial cost may seem prohibitive but when amortized over several years there will be significant savings.
All plans look good and perfect on paper but tend to need adjustments when put into action. An experienced robotic system integrator is well aware of the foibles and problems that are inherent in the implementation of a plan and are prepared to provide solutions. Each element of the integration has to be tested, perfected, and adjusted such that the various components work seamlessly to a positive and productive outcome. In this part of the process, robotic system integrators must pay close attention to the most minute details to optimize performance and ensure success.
Robotic system integration requires constant and ongoing support. This particular factor can be a deal breaker, especially in cases where the client is unfamiliar with the technical aspects of robotic functions. It is very doubtful that a client will come across a robotic system integrator that does not offer continual support. Aside from it being excellent customer service, it also provides an opportunity for a robotic system integrator to display their skills and aptitude to other clients.
In 2012, the Robotics Industries Association (RIA) introduced a certification process for robot integrator programs that serves as the benchmark for evaluating the technical expertise of robotic system integrators and the excellence of their business practices. If a robotic system integrator displays an RIA certification, they have achieved the highest possible proficiency, experience, and success in their profession.
The process of certification is far more than applying to receive a piece of paper. It involves on site audits, assessment of system integrator personnel, examination of safety training, and a list of other criteria, each of which has to have attained the highest rating. Companies that have successfully completed certification have the capabilities, skills, and acumen to deliver the highest possible quality service.
The types of robotic system integrators are as varied as there are industrial operations. They run the gamut of functions, applications, processes, and operations with each one specializing in a particular form of robotics. When installing, implementing, or updating robotic systems, a robotic system integrator is the perfect choice for ensuring the success of the integration process.
As the demands of technology continue to grow and expand, robotic systems are becoming more and more a necessity. Since technology has advanced so rapidly, it is essential to hire an expert who knows the field and can provide the best possible solutions.
Warehousing has been implementing a wide assortment of robotic solutions for many years to reduce the time for sorting, storing, picking, and packing orders. The huge uptick in robotic solutions has come with the growth of e-commerce and online retailing, which requires on time and timely deliveries.
One of the basic concerns in manufacturing is keeping workers on task and at their workstations. Collaborative robots work with employees to finish processes and assist in redundant or repetitive tasks such that workers can concentrate on more complex and mental work.
Over the last thirty or forty years, assembly operations have been slowly integrating robotics into the process to avoid human errors, reduce assembly times, and provide detailed inspection of final products.
There is an endless number of robots that are available to be integrated into production, manufacturing, material handling, hospitals, and other industries. All a client has to do is ask and a robotic system integrator will provide a robotic solution. There is a robot for every type of operation and process and a robotic system integrator who knows where to find the one to fit the job.
An automatic screwdriver is a piece of equipment that automatically inserts screws into a product during assembly and production. Since every production operation is unique and requires a...
An automation system is an integration of sensors, controls, and actuators designed to perform a function with minimal or no human intervention. The field concerned in this subject is called Mechatronics which is an...
Collaborative robots, also abbreviated as Cobots, are the newest technology in robotics. They have changed the automation world significantly. These robots can work safely together with workers, hence are...
An industrial robot is an autonomous system of sensors, controllers, and actuators that executes specific functions and operations in a manufacturing or processing line. They operate continuously through repetitive...
Warehouse automation is the process of replacing repetitive tasks with systems that are automated. The main goal is to remove labor-intensive duties that consume time. As a result, the workers can focus more on...
An AGV forklift is a driverless self-operating robotic device that has the ability to carry, lift, retrieve, and place loads for easy transfer from one location to another. An automatic guided vehicle (AGV) forklift is a computer controlled mechanism that...
Automated guided vehicles (AGV) or mobile robots are types of guided robotic systems that are not bounded by a fixed range of motion. Rather, it is self-contained and can move along a line, surface, or space...
An autonomous mobile robot (AMR) is a self-propelled self-powered mechanism designed to perform repetitive tasks or organizational functions using an internal guidance system. They are able to navigate their...
A belt conveyor is a system designed to transport or move physical items like materials, goods, even people from one point to another. Unlike other conveying means that employ chains, spirals, hydraulics, etc...
A bowl feeder is a mechanism for supplying small parts and components to a production line or for sorting bulk items for rapid use. A self contained bowl feeder system has a bowl that sets on a spring loaded base that moves vertically...
A conveyor system is a method for moving packages, products, supplies, parts, and equipment for production, shipping, or relocation. The different types of conveying systems include pneumatic, screw, belt, and roller. The construction of individual systems depends on the materials...
Palletizing is the process of putting items on a pallet. The process of emptying the loaded objects in the reverse pattern is known as depalletizing. A pallet is a flat, square-shaped platform used to transport and...
A pallet stacker is a machine designed to assist the user in lifting, moving and handling palletized materials with ease. A pallet itself is a flat and horizontal structure used to support goods in a sturdy fashion...
A palletizer is an automated material handling machine used to stack and orient several individual products into a single load for a more convenient and economical method of handling, storage, and shipment. Palletizers are usually part of a bigger packaging process...
Pneumatic conveying is a method for transferring bulk materials, like powders and granules, using compressed gas or air, from one processing center to another. Material is moved through an enclosed conveying line or tube using a combination of pressure differential and airflow from a blower or fan...
A robotic palletizer is a type of palletizer that employs a robotic arm to pick, orient, and place individual products and arrange them into a single stack of load. They are the next generation of palletizers, and they will supersede conventional palletizers...
Roller conveyors are a type of conveyor belt that allows objects to skate on its surface by using rollers, which are equally spaced revolving cylinders. They transport stuff from one location to another...
Screw conveyors, or auger conveyors, are industrial equipment used in transporting bulk quantities of granular solids (e.g., powder, grains, granules), semi-solids, liquids, and even non-flowing materials from one point to another...
Vibratory conveyors are material-handling equipment used to transport fine to coarse-grained bulk materials. These vibratory conveyors are strong conveying equipment utilized for bulk commodities with fine to coarse graininess...
A vertical conveyor is an engineered mechanical method for moving goods, products, supplies, parts, and components from a lower level to a higher level or from a higher level to a lower level. They are...
Vibratory feeders are short conveyors used to transport bulk materials utilizing a controlled vibratory force system and gravity. The vibrations impart a combination of horizontal and vertical acceleration through tossing, hopping, or sliding-type of action to the materials being handled...
In 1954, when Arthur "Mac" Barrett, of Barrett Electronics Corporation, unveiled the first AGV, he named it Guide-o-Matic and described it as a driverless vehicle...