Industrial Mills
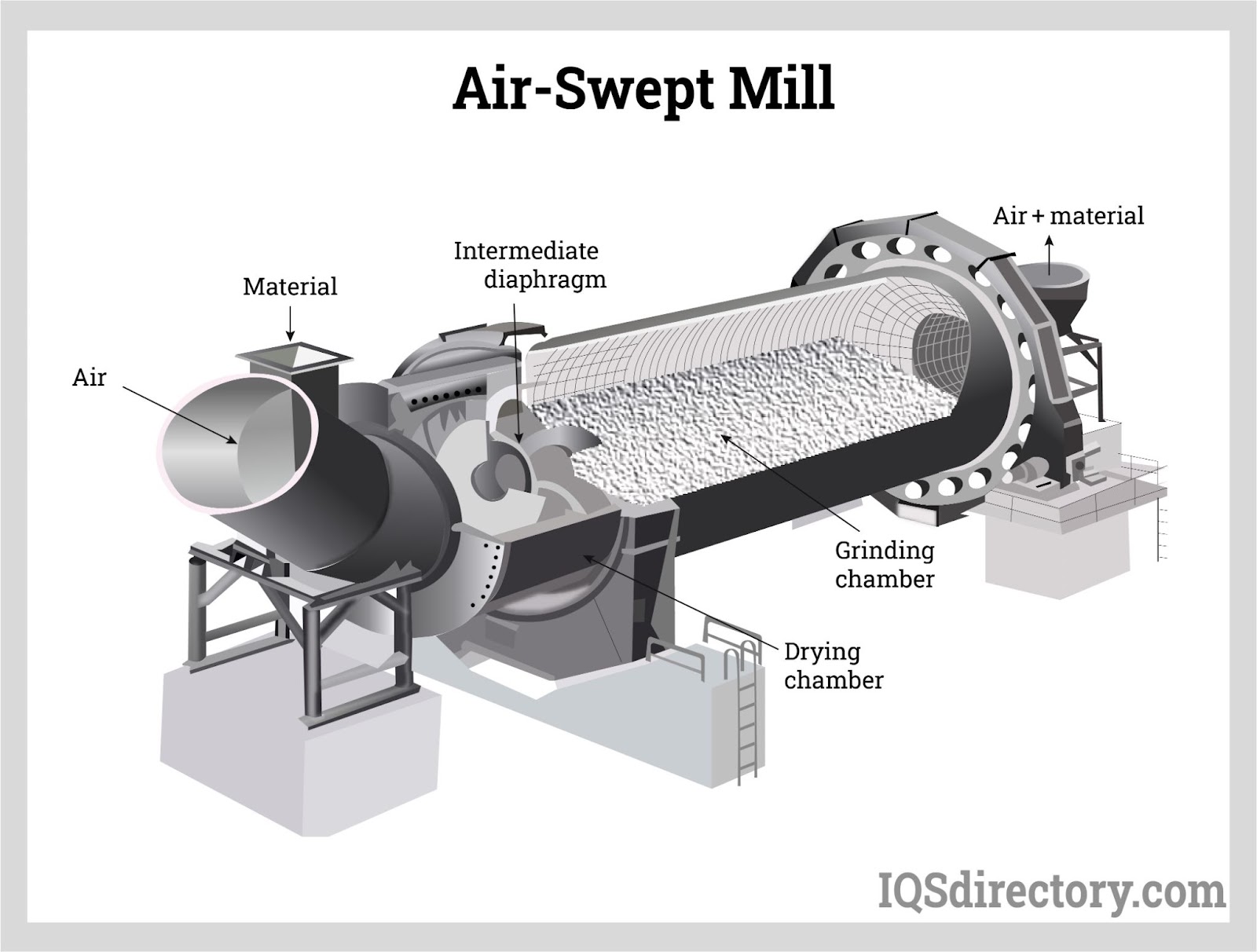
A mill is a mechanical device that is often a structure, appliance, or machine that is used to break down solid materials into smaller pieces by cutting, grinding, or crushing them. Many industrial processes involve...
Please fill out the following form to submit a Request for Quote to any of the following companies listed on
This article will take an in-depth look at size reduction equipment.
The article will bring more detail on topics such as:
This chapter will discuss what size reduction equipment is, its construction, and how it functions.
Size reduction equipment refers to machines that crush and grind materials to reduce their size. Pulverizers are a type of size equipment, the names are used interchangeably. Size reduction is an essential component of a wide range of industrial processes.
Manufacturers of size reduction equipment offer size reduction equipment that can be used on a wide range of materials, including coal, shale, brick, concrete, wood, limestone, and even plastics. Because size reduction equipment has so many applications and is used to process such a diverse range of materials, an equally diverse range of size reduction equipment configurations is required to accommodate them.
Every size reduction machine is designed with a certain throughput or fuel grinding capacity at a particular Hardgrove Grindability Index (HGI) number based on a definite raw coal volume, desired fitness level, and moisture content. These factors are important and should all be taken into consideration when discussions of size reduction equipment capacity become serious. A well-performing size pulverizer or reduction machine also needs good fuel fineness and optimum airflows, among other performance attributes, to achieve prime combustion for a boiler. Size reduction media vary in design, but they all have some things in common: grinding media. Grinding media is also moved by the use of a motor which provides the rotary action which makes pulverizing possible.
The friction in size reduction equipment is a result of grinding media, which can refer to many different coarse materials such as non-sparking lead, ceramics, brass, bronze, and flint. Crushers also come in materials including steel, stainless steel, and stainless steel with wear-resistant coating.
Ceramic is any of the different brittle, hard, corrosion-resistant, and heat-resistant substances created by shaping and firing non-metallic, inorganic material, like clay, at elevated temperatures. General examples are porcelain, earthenware, and brick.
Some elements, like silicon or carbon, may be regarded as ceramics. Ceramic materials endure chemical erosion, which happens in other materials exposed to caustic or acidic environments. Ceramics typically can endure very elevated temperatures in the range of 1832°F to 2,912°F (1,000°C to 1,600°C). This makes them ideal for grinding where temperatures can get very high.
The modern ceramic substances categorized as advanced ceramics include tungsten carbide and silicon carbide. Both are treasured for their abrasion resistance and therefore find usage in applications like the wearing plates of size reduction devices in mining operations.
Non-sparking lead is categorized by its lack of ferrous metal (iron and steel), implying it does not cause sparks during the grinding process. Lead is highly ductile, dense, and malleable and is a bad conductor of electricity; however, lead is resistant to corrosion and very durable.
Brass is a zinc and copper alloy that can be mixed in different amounts to obtain electrical, chemical, and mechanical properties. Brass is comparable to bronze, another copper alloy, which utilizes tin instead of zinc. Both brass and bronze also may include small amounts of a variety of elements, including lead, arsenic, phosphorus, aluminum, silicon, and manganese. Brass is still generally utilized in applications where resistance to corrosion and reduced friction are needed. Brass is at times utilized in cases where it is pertinent that sparks not be produced, such as in milling machines.
Bronze is a copper alloy, usually with 12 to 12.5% of tin and sometimes with more metals (like aluminum, nickel, zinc, or manganese) and often metalloids or nonmetals like silicon, phosphorus, or arsenic. These additives create a variety of alloys harder than pure copper or with increased beneficial attributes, like ductility, strength, or machinability. This makes bronze ideal for size reduction equipment. In addition, bronze struck against a material will not create sparks, unlike steel.
Flint is a sedimentary crystalline type of quartz mineral, classified as a variety of cherts that are found in marly limestone or chalk. Flint is typically black, dark gray, green, brown, or white in color, and, at times, has a waxy or glassy appearance. Flint pebbles are utilized as media in ball milling to grind materials fin the ceramics industry. The pebbles are handpicked depending on their color. Blue-gray pebbles have a low chromophoric oxide content and are less harmful to the ceramic composition color after firing.
Steel is an iron alloy usually made with a fraction of carbon to enhance its fracture resistance and strength compared to other iron forms. The growth in steel's durability in comparison to pure iron is conceivable by lowering iron's ductility only. As crushing media, steel could be made into balls or bars.
High carbon steel bars may be used in place of balls. This size reduction equipment has a very consistent fine output and low power usage. It is not suitable, however, for very tough objects. It is most effective with sticky objects that may stick balls together in inert granular materials, since the grander weight of the bars makes them pull apart again.
Pulverizers process material continuously or in batches by taking incoming objects, usually on a conveyor belt, spinning it and crushing and grinding them, then putting them to the exit. They may also heat, cool, or ventilate materials as they exit.
The considerations when choosing size reduction equipment include:
If the original sample particle size is coarse, it could be essential to utilize two different size reduction machines, one for primary size reduction and the second for fine grinding, to obtain analytical fineness.
Choosing an appropriate grinding tool is also part of the choosing process for finding the right size reduction equipment for the material. The essential options are abrasion resistance, hardness, energy input, and possible contamination.
The different types of size reduction equipment include:
Pulverizers can be used in applications such as pulp creation in paper production, turning soil, crushing scrap, tire shredding, and recycling. The pulverizers are usually categorized as impactors, crushers, or grinding mills. Impactors, which are also known as impact crushers, use impaction, which is a force transmitted via a collision or two bodies striking each other. Crushers use pressure generated by two forces opposing each other. Crushers are used to reduce the size of large, dense materials like rocks into dust. Grinding mills break down materials using friction which is a result of grinding media. Such media can be coarse materials like ceramics, flint, non-sparking lead, and brass.
The pulverizers are discussed below:
Ball mills are industrial crushing machines that are categorized by their usage of a loose crushing medium. Ball mills are one type of size reduction machine. Ball mills, together with impact crushers, grinding mills, and a range of other tools, are utilized for the reduction of all varieties of objects for all varieties of purposes.
Size reduction is a significant part of many industrial procedures, making ball mills and other size reduction mechanisms important to these businesses and in high demand. Particularly in procedures that include the mixing of objects, the smaller the particles of the objects, the simpler and more thorough the mixing becomes.
Ball mills are beneficial machines for alloying metal procedures for this purpose. They can grind and crush the constituent objects into very small granules, making them easy to combine. Ball mills are also used for the particulate size reduction of cement, black powder, silicates, fertilizer, and even a variation of non-ferrous and ferrous metals. Ball mills are quite similar in operating concept and construction to rock tumblers, which utilize a milling medium to polish stones in a revolving cylinder.
Ball mill machinery typically includes a motor, cylinder, and crushing medium. The crushing happens in the cylinder. The objects to be crushed are put into the cylinder together with crushing media. Crushing media may be made of many objects; a few examples are steel and lead-antimony alloys, also nonmetals like ceramics and flint. When crushing medium and objects to be crushed are mixed in the cylinder, the latter is rotated by a big motor. As the cylinder is rotated, the crushing medium is tossed around in the cylinder, smashing the object when they move.
After enough time has elapsed, the objects are crushed into tiny particles. Once adequately crushed, the objects may be released from the cylinder and substituted with new objects to be crushed. This procedure may be continuous, or it can be carried out in batches. Continuous ball milling is the continuing automatic loading of objects to be crushed and offloading of crushed objects. Depending on the milling operation scale, ball mills may be adequately small to be fitted on a workbench or big enough to fill up entire rooms.
Crushers are tools constructed to reduce big waste materials for easy recycling or disposal. One of the most prevalent types of size reduction equipment, crushers are commonly utilized to reduce the size of big rocks, turning them into easily manageable rock dust, small rocks, or gravel. Crushers can break apart or compress soft objects such as gypsum, phosphate, and limestone to very hard objects such as asphalt and ore.
There are many kinds of crushers. Some of the most generally utilized crushers are gyratory crushers, cone crushers, and jaw crushers. Gyratory crushers and jaw crushers function well on both hard and soft objects and are often used in industries like mining for crushing big quarried objects like ore. In construction, these crushers are used to reduce big building objects such as concrete and stone. Lastly, industrial manufacturing is used to process big, dense objects.
Cone crushers, which are most suitable for medium to very hard objects, are beneficial for industries. These include metallurgical, for the processing of big inert granular materials supplied by mining metal like copper and iron ore. They are also used in road building for the crushing of building objects like concrete and asphalt. Lastly, chemicals for the crushing of minerals are utilized to process chemicals like silicic acid and phosphate. Crushers are also utilized in automotive, demolition, smelting, and manufacturing industries.
Crushers primarily work breaking apart or compressing materials as an effect of transference of a force given by mechanics through an object which is molecularly stronger than the object it is crushing. Crushers keep objects between parallel surfaces. They then force these surfaces onto each other with adequate force to deform or fracture the material. They all depend on the same standard of compression, but different kinds of crushers work in different ways. Jaw crushers are simple to spot against other crushers types because they have a familiar construction with vertical "jaws." One of the jaws is fixed while the other is moveable, with its mobility generating the energy needed for compression.
Gyratory crushers are comparable to jaw crushers but differ in the sense that they are shaped with a conical head and concave surface. The motion in gyratory crushers is created through an eccentric layout. Cone crushers, however, are more comparable to gyratory crushers than jaw crushers. Cone crushers are more conically shaped, with a big top inlet for letting through the big objects and a very small bottom outlet for the smaller, crushed objects to exit. Usually, cone crushers work by crushing objects between a concave hopper and an eccentrically gyrating spindle, all of which are secured by wear-resistant material.
Grinding mills are tools constructed to break huge quantities of solid objects into small particles. Grinding mills can process a range of objects and operate through varying methods. In the past, animals, windmills, and waterwheels powered grinding mills, but today industry grinding mills are very powerful and able to perform more intense tasks.
Grinding mills are applied in a wide range of industries. In gristmills, for instance, grinding mills are used to grind grains like maize. Ball mills are typically used to mill coal in power plants or produce black powders for fireworks. Ceramic and paint material is also crushed in a similar method.
Grinding mills involve a rotating cylinder where materials to be ground are loaded. The cylinder is loaded with a grinding medium that smashes other objects while the cylinder rotates. Grinding mills may be miniature enough to fit on work benches or big enough to fill up entire rooms. Various grinding mills are available, including hammermills, ball mills, roll crushers, and jaw crushers.
An impactor is a type of size reduction machine that uses impaction as a collision-fashioned force, in opposition to applying sheer pressure to deform or break apart various objects. Impaction is a force conveyed through the hitting or colliding of one body with another. Crushing happens as the result of the pressure generated by two opposing forces.
Sometimes utilized as a secondary way of size reduction rather than a primary way, impactors are also sometimes called impact crushers. Capable of being utilized on a wider range of objects, impactors are usually utilized for crushing non-abrasive, soft objects like gypsum, phosphate, soft metallic cores, seeds, and coal. However, they may also be utilized to crush abrasive, hard objects like gravel, basalt, asphalt, and concrete. However, they are most suitable for objects of medium hardness.
Many industries use impactors, including bridge and road construction, for the impaction of building objects. In mining, impactors can be used for work on quarried and mined materials. Industrial manufacturing uses them for the impaction of different materials for usage in more processing applications. Lastly, water conservancy impacts inert granular materials needed for various applications.
There are two primary impactor types: a vertical shaft impactor (VSI) and a horizontal shaft impactor (HSI). An HSI crusher has curtain liners, adjustable liner plates, and impeller bars. The impaction procedure starts when the materials reach the breaker plate, where fixed hammers are on the external edge of a rotating rotor. Despite the varying types, all impactors have the design features of a metal cage that works to contain the objects and has outlets at the base to let the crushed objects leave once they have reached the desired size. HSI crushers must not be utilized for abrasive, hard objects and are most suitable for soft objects like dolomite aluminum, weathered shakes, and clay. A VSI crusher is similar in design to an HSI crusher but also has a crushing chamber constructed to throw the objects against and a high-speed rotor that impacts the objects utilizing speed rather than only surface force. As an effect, VSI crushers have higher efficiency and are more powerful than HSI crushers. They are better fit for harder objects like metallurgical slag, quartz minerals, magnesium sand, bauxite, and limestone.
Jaw crushers are size reduction machines that use a blend of crushing jaws and gravity to pulverize materials. Jaw crushers are so titled because of their jaw-like setup. They are significant machines in a wide range of industrial processes. Trash compressing in recycling facilities and waste management, boulder crushing in mining operations, and materials management and disposal during demolition or construction projects are just a few of these processes.
Pulverizer manufacturers have answered to the various materials reduction requirements of the industry with a diverse range of crushing and pulverizing equipment. Jaw crushers vary in operating capacity and size, but as a rule, they lie somewhere in the mid of the full range of crusher size. In some instances, they may be made for portability, which is the case in most mining jaw crushers. Usually, their size is comparable to the size of a storage shed.
A jaw crusher works by moving a retractable plate away and towards a fixed plate. The plates are laid at an angle inside a vertical channel. When materials to be crushed are loaded on the vertical channel, the retractable plate moves away and towards, crushing the materials as it is moving forward and releasing crushed materials down outside the channel while it retracts. Jaw crushing is a multiple-phase procedure because the plates are set at an angle. Large objects are partly crushed at the vertical channel’s top and move down as they are broken down. Jaw crushing is a kind of imprecise crushing procedure and will not create the finely grained crushed materials which other crushing procedures can. For instance, grinding mills and hammer mills have turning crushing devices that grind and crush materials again and again until they are small granules. However, jaw crushing is sometimes not utilized for crushing very small objects. If properly matched with an application, jaw crushers are an efficient and valuable crushing method.
A stone crusher is a type of size reduction machine used to break apart or compress a variety of large stones. Stone crushers commonly feature a high yield and big crushing rate, and while they may be utilized as primary crushers, they are also at times used as secondary and tertiary crushers. Industries that utilize stone crushers include energy, transportation, petrochemical smelting, and industrial manufacturing.
The stone, varying from soft minerals to very hard stones, may include limestone, slag quartz, granite, sandstone, copper ore, iron ore, cement, marble, and more. Since stone crushers may be used on such a wide range of materials, they are used in various applications in industries like mining for the crushing of quarried and mined stone. Metallurgy is for the crushing of big stones into small stones that may be utilized in the process of working metal into components and parts. Stone crushing can be utilized to process various chemicals. Stone rubble previously used as building materials can also be crushed. Finally, crushers can remove debris left over by the demolition of roadways, buildings, canals, bridges, and a variety of other structures.
There are a few types of crushers that are used for crushing stones, including cone crushers, jaw crushers, impact crushers, and hammer crushers. Utilizing compression, jaw crushers have two "jaw-like" surfaces. Jaw crushers feature a mobile jaw and a fixed jaw. The mobile jaw allows crushing by applying force on the stones and forcing them onto the fixed jaw. Cone crushers, which are shaped conically, offer crushing by squeezing the stones between a covering concave hopper and a gyrating spindle powered by an eccentric layout. Both components are enclosed by wear-resistant materials, which protect them from the numerous broken pieces of stone.
Very often utilized as secondary crushers, hammer crushers have swinging arms on a rotating shaft that crush the stones onto the iron cage of the crusher. Once crushed, a screen below the crusher permits fine stone pieces to fall out. Also called a hammermill, another kind of hammer crusher is a changeable hammer mill that runs alternately in both directions. Lastly, impact crushers break apart stones by means of impact, which is a collision-wrought force. Impact crushers come in two main types: vertical shaft impactors (VSI) and horizontal shaft impactors (HSI).
A grinder, often called a grinding machine, is a power tool used for grinding materials. It is a type of machine which cuts using an abrasive wheel. Each grain of abrasive on the surface of the wheel cuts a tiny piece from the material using shear deformation.
Grinding is utilized to finish materials that should have high surface quality (the surface has low roughness) and great accuracy of dimension and shape. As the accuracy in sizes in grinders is of the order of 25*106 mm, it tends to be used as a finishing process and removes fairly small metals of about 250um to 500um depth. However, there are other roughing uses where grinders quickly remove high amounts of metal. Thus, grinding is a diversified field.
The grinder has a bed with a position to hold and guide the material and a power-driven wheel spinning at the needed speed for grinding. The wheel manufacturer’s rating and diameter determine the speed. The grinder’s head is able to move over a fixed object, or the object may be moved while the grinder's fixed.
Granulators are devices designed to granulate matter into a grain. What distinguishes granulators from size reduction machineries like grinders or shredders is that granulators take big materials and make them very small than a grinder can do. Granulators typically have an open rotor setting, meaning air can simply flow around the rotor and cool the material. A closed rotor granulator, however, operates at high speeds. The materials are generally ground down to the level of maize meal, or, at other times, even smaller. The size range of these grains is 0.008 to 0.16 inches (0.2 to 4 mm).
Dry granulation and wet granulation are two granulation types. Wet granulation forms the granules when granulating liquid is poured on a powder bed mixed together through screws, impeller, or air. The mixture of these two materials makes the wet granules. The most typical liquids are ethanol, water, and isopropanol. Water-based solutions are usually safer to work with instead of solvent-based solutions.
When the granules are made without using a liquid, it is called dry granulation. This process is preferred in cases where the materials may be sensitive to heat and moisture. Making these granules without using moisture requires the use of compactors. In the recycling industry, granulators are very vital for many applications. This size reduction machine is best for lighter objects like rubber and plastics since these materials don’t grind well.
Rotor mills are utilized for the fine reduction of a wide range of objects for many various applications. Typically rotor mills are utilized for hard, soft, fibrous, and also samples such as liquid nitrogen, which are temperature sensitive. Other agricultural uses involve the size reduction of plant materials, fertilizers, wood, seeds, tobacco, and straw. Rotor mills can be utilized in the plastics or chemical industries for objects like synthetic resins, super-absorbent polymers, rubber granulate, powder coatings, activated charcoals, and plastics.
Many rotor mills are powered by motors and can function at varying speeds. They also have safety casings to protect the electrical components and motor from material and dust penetration. The sieves generally come with round or trapezoid holes of different dimensions, usually from 0.003 to 0.4 inches (0.08mm to 10mm). There are also choices for rings and rotors consisting of reinforced rims to provide better stabilization for the sieve.
Briquette machines use pressure and force to transform metal waste and powder into manageable bricks or blocks that can be easily transported or used as raw materials for manufacturing and production. A briquette system can work with any type of material with the right size, moisture content, and compatibility.
An essential part of briquetting is a binder that adheres the raw particles and gives them sufficient strength when formed as a brick or block. Each material in a briquette system requires a binder that fits its chemical makeup and characteristics.
Pressure for the briquette process is created by several different types of machines, including a screw type that uses an auger to press the raw material and may or may not have a heating element. Hydraulic briquette systems produce a great deal of pressure, which makes it possible for hydraulic systems to briquette all materials.
Other types of briquette machines are piston types and roller types. A piston-type briquette system has a piston driven by rotary or hydraulic power to form the material into a briquette. A roller briquette system forces the raw material between two rollers with slots or holes that press the raw materials into the slots to form the briquettes as the rollers rotate.
Briquette machinery is an ideal solution for dealing with random waste and recycling that is difficult to handle in its initial form. The force and pressure of a briquette machine can take any material and change it into a solid mass that can be manipulated and stored.
Draining presses are used to empty beverage containers, milk cartons, and food cans of their leftover contents. The press compacts the cans into discs for easy recycling. The extracted liquid is disposed of or saved to be reused. Draining presses have been used for many years by wastewater treatment facilities to extract solid waste from liquid waste. For industrial operations, draining presses are used to remove impurities and solid waste matter in industrial wastewater.
The draining press process applies pressure to waste containers that have liquids in them or to wastewater with solid matter. Dewatering or liquid removal involves applying pressure to the water or containers. The original draining presses complete the process using plate and frame presses that squeeze out fluids.
Draining presses compress and drain a wide assortment of liquid-containing materials, such as boxes, cans, plastic bottles, and food containers. They empty containers of liquid waste and make them available for reuse or compress them for disposal.
This chapter will discuss the applications and benefits of size reduction equipment.
Stone crushers have a solid foundation, so they can be expanded. Size reduction equipment is perfect for mines with big processing capability as the service life is long. This equipment produces high surface finishes. It can crush hard materials. Less pressure is put on work during operation. It can achieve highly accurate measurements. It can operate at elevated temperatures.
For jaw crushers, the structure is simple. The structure allows easy operation and easy maintenance. The lubrication mechanism has exceptional performance. It also has a low cost when compared to other stone crushers.
A rotor mill is perfect for very fine batch milling of large quantities, and its speed is adjustable for different uses. Cleaning is easy, alluding to transferrable, rotor, push/fit grinding insert, and cassette. Feed hoppers, grinding chambers, and substance entrances and outlets are made of stainless steel and can also produce very fine powder. They are perfect for milling toxic objects because it can be utilized in a totally closed form.
The immense pressure and force applied in industrial pulverizers raise the risk of operator injury if good safety precautions aren’t observed. Safety things like shields, guard rails, auto shut-off controls, and sensors reduce the possibility of accidents. When properly implemented, maintained regularly, and operated by trained employees, size reduction machines are important to many procedures.
The different safety standards when handling size reduction equipment include:
The maintenance of size reduction equipment includes:
Preventive maintenance includes scheduling checks, inspecting, and servicing at regulated times as suggested by the equipment manufacturer. Scheduled inspections and checks should be practiced, adjustments should be made, and worn-out parts should be changed before a serious machine breakdown happens. Preventive maintenance is important in exploiting the equipment’s life span.
Predictive maintenance monitors the conditions of reduction while the equipment is running. This is achieved by using predictive maintenance tools like lubricating oil thermometers or temperature sensors, gauges or lubricating oil pressure sensors, lubricating oil filter condition indicators, lubricating oil tank return screen, and downtime.
Size reduction equipment is machinery that crushes and grinds materials to reduce their size. Size reduction equipment typically falls into three main types: impactors, crushers, and grinding mills. The grinding and crushing media in this equipment is usually steel, bronze, and brass. All such equipment must be operated by trained personnel. Preventative and predictive maintenance goes a long way in prolonging the life of size reduction equipment.
A mill is a mechanical device that is often a structure, appliance, or machine that is used to break down solid materials into smaller pieces by cutting, grinding, or crushing them. Many industrial processes involve...
Agitators are equipment used in homogenizing media inside a tank. It works by rotating the impeller at its immersed end at a controlled speed or revolutions per minute (rpm). The work exerted by...
A belt conveyor is a system designed to transport or move physical items like materials, goods, even people from one point to another. Unlike other conveying means that employ chains, spirals, hydraulics, etc...
A cardboard shredder is a machine designed to turn cardboard boxes and sheets into small shards or strips. Specialty cardboard shredders are configured to convert cardboard into flexible perforated material for packaging...
A conveyor system is a method for moving packages, products, supplies, parts, and equipment for production, shipping, or relocation. The different types of conveying systems include pneumatic, screw, belt, and roller. The construction of individual systems depends on the materials...
High shear mixers, also known as high shear reactors (HSRs), rotor-stator mixers, and high shear homogenizers, are used to emulsify, homogenize, disperse, grind and/or dissolve immiscible mixtures with components of the same or different phases...
A homogenizer is a type of mixing equipment used to create a uniform and consistent mixture. It works by breaking the components and evenly distributing them throughout the solution. The components are either immiscible, have varying sizes, or are in different phases from each other...
An industrial blender is a machine for large-scale production that consists of a large tank capable of mixing and blending batches of manufacturing materials to create a reaction between the materials. The many uses for industrial blenders are due to their capacity and...
An industrial shredder is a piece of heavy duty equipment designed to shred dense and light materials to prepare them for recycling or for the destruction of unusable products. They are an environmentally sound device that...
Pneumatic conveying is a method for transferring bulk materials, like powders and granules, using compressed gas or air, from one processing center to another. Material is moved through an enclosed conveying line or tube using a combination of pressure differential and airflow from a blower or fan...
Roller conveyors are a type of conveyor belt that allows objects to skate on its surface by using rollers, which are equally spaced revolving cylinders. They transport stuff from one location to another...
Screw conveyors, or auger conveyors, are industrial equipment used in transporting bulk quantities of granular solids (e.g., powder, grains, granules), semi-solids, liquids, and even non-flowing materials from one point to another...
A shredding machine is equipment utilized for shredding. Shredding machines are used to reduce the size of materials. While most online sources define the shredding machine as...
A vertical conveyor is an engineered mechanical method for moving goods, products, supplies, parts, and components from a lower level to a higher level or from a higher level to a lower level. They are...
A mixer is a complex and precise tool that is used in combining and mixing of substances and chemicals for manufacturing, production, and industrial use. There are many types of industrial mixers including...