Size Reduction Equipment
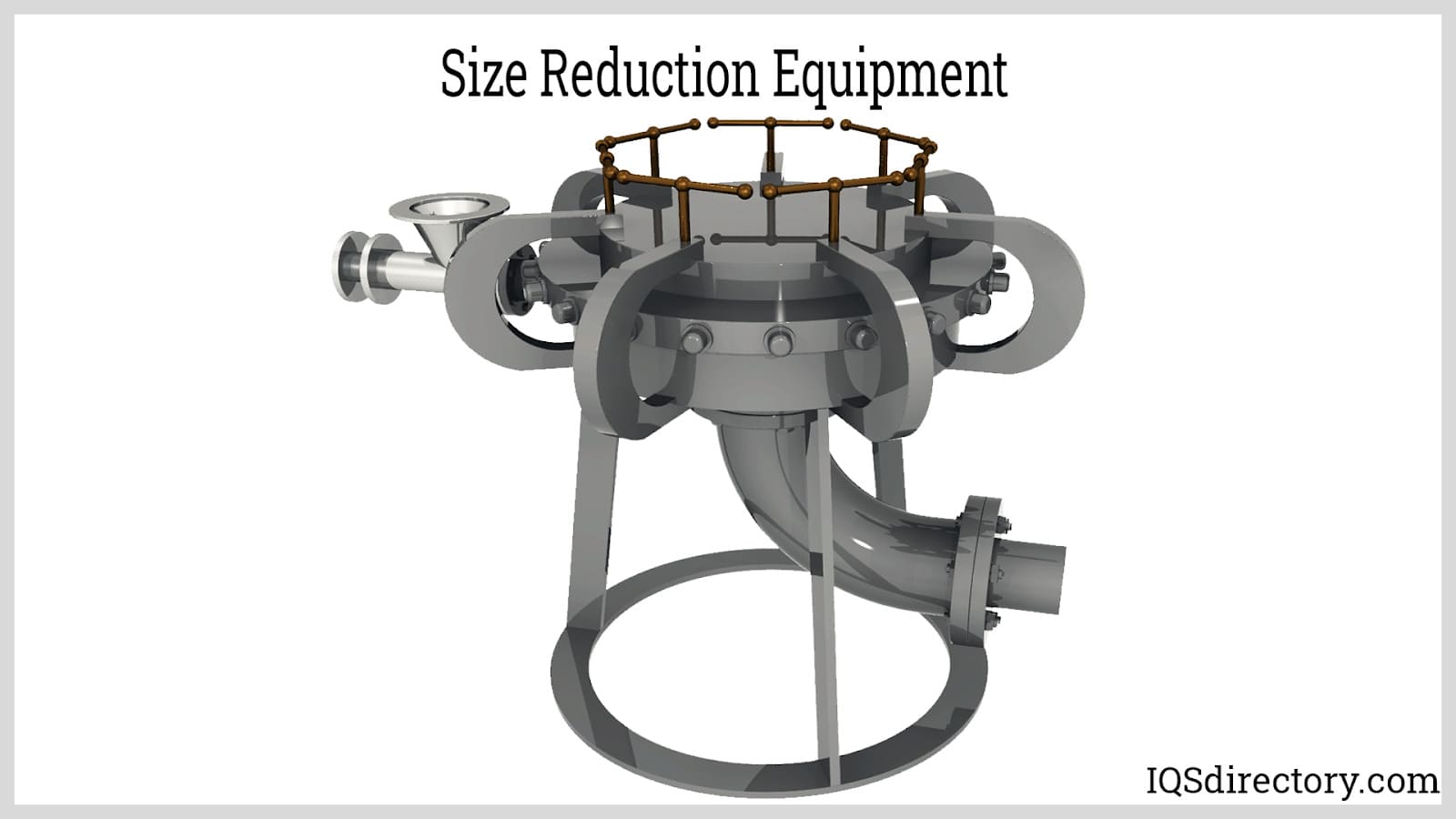
Size reduction equipment refers to machines that crush and grind materials to reduce their size. Pulverizers are a type of size equipment, the names are used interchangeably. Size reduction is an essential...
Please fill out the following form to submit a Request for Quote to any of the following companies listed on
This article will take an in-depth look at types of mills.
The article will bring more detail to topics such as:
This chapter will discuss what mills are and the typical components of mills.
A mill is a machine that is used to break down solid materials into smaller pieces by cutting, grinding, or crushing. The process of milling includes the use of force that acts on a material to tear it apart and reduce its size. Milling improves the performance of ingredients, and the products made from them. The two basic forms of milling are dry milling and wet milling where dry milling uses particle to particle contact while wet milling suspends materials in a slurry.
There are numerous types of mills, and materials processed by them. The first mills were manually operated, powered by animals, or powered by the wind or water. Modern mills are powered by electricity, which provides more power and saves on labor costs.
With a mill, solid materials are ground using mechanical force that breaks down the structure of the material by overpowering its interior bonding. Solid material is changed into small particles, grain, and various shapes. Milling also refers to the process of breaking down, sizing, separating, or classifying material like mineral ore. For example, rock crushing or grinding are used to produce uniform particle size for construction or the separation of rock and soil for filler or land restoration.
Milling is used to remove or separate contaminates or moisture from soil to make dry fill to be used for transportation or filling. Milling serves the following engineering purposes:
Mills are complex pieces of equipment that have a wide assortment of parts and components that have to work together to achieve a desired outcome. Although there are several different designs of mills, all types have certain components and pieces that are common. The most basic and beginning component of a mill is its shell, which has to be strong, durable, sturdy, and resilient to be able to withstand the demands of the milling process.
Shells are made of a thick steel plate that is welded and sealed into a cylinder such that it will not distort or be susceptible to failure. For the best possible results, shells are electronically welded using an automated process. A basic feature of all mills is their ability to withstand impact and heavy loads. Holes are drilled in the shell such that bolts can be used to hold the liner of the mill, which is not necessary with wedge type liners.
Flanges are designed to meet the dimensions and material that will be processed by a mill. They must be uniform in diameter and may have recesses and undercuts near the arbor sleeve. It is essential that flanges be properly maintained in regard to flatness, finish, balance, and wear. The securing of flanges must be completed with care since over tightening can warp a flange and cause other damage.
The shell liner is a protective covering that lines the inner part of the shell and protects the mill shell from forces created by the milling process. They are made of various materials depending on the type of mill and material to be milled. Rubber liners are used in ball mills while metal liners are used in autogenous (AG) and semi-autogenous (SAG) mills. The design of the liner of a mill determines the movement of the media.
Mill heads are made of iron or steel. They are bolted to the flange of the shell and are conical shaped or have a starfish design. Ball, rod, preliminary, Ballpeb and Compeb mills have conical heads while longer Ballpeb and Compeb have starfish heads, which offer extra support and strength due to the braces. An essential part of a mill head is its trunnion bearings that provide support for the revolving material in the mill.
The pinion shaft is the drive mechanism for a mill that moves the gear train that turns the mill assembly. It is mounted on roller bearings that have a decreased friction coefficient, which requires minimum lubrication and has excellent seal. Lubrication is provided from a reservoir located at the bottom of the gear housing where a lubricating pinion mates with the main gear.
Smaller mills of less than 250 hp have a V belt drive while larger mills of over 250 hp have direct drive. The motors for direct drive mills have wound rotor motors that are connected directly to the pinion shaft. Several types of motors are available to drive a mill with varying torques that are determined by a mill’s design and its manufacturer.
Mill feed chutes come in a wide array of shapes, sizes, and configurations. The use of a chute depends on the industry and type of material to be milled with mining, cement, and rock production having the choice of mills with or without a chute. The types of feeders include combination, spout, scoop, and drum types.
Once the material has been ground and processed, it is removed from a mill through the discharge unit. Discharging completed material from a mill can be completed in different ways depending on the design of the mill. In many cases, it resembles pouring liquid from a pitcher or barrel. The types of discharge methods or units are overflow, peripheral, and diaphragm.
Grinding media is used to refine and reduce particle sizes to produce a wide variety of shapes and sizes to meet application needs. There are several varieties of grinding media that include metallic and non- metal types, each of which is designed to process various kinds of materials. The selection of the type of grinding media determines the success of the grinding process.
Metallic grinding media includes carbon steel, forged steel, stainless steel, and chrome steel, which come in the form of balls, beads, bars, and tiny cylinders.
Non-metallic grinding media includes alumina balls, glass beads, silicon carbide balls, silicon nitride balls, ceramic balls, and zirconium balls. These media are used where contamination is a concern. The choice of non-metallic media is highly dependent on the type of material to be processed since the wrong choice can damage the interior lining of a mill.
There are typically four main different categories of mills that are usually used in the grinding, crushing, or fine-cutting of materials. These categories are detailed below.
A conical mill is a type of mill that is used to reduce the size of materials uniformly. It is also referred to as a conical screen machine. It is a hammer mill alternative. As the name implies, the mill varies in its diameters between its opening, in which the feed enters, and where the product leaves. The conical mill functions by having the required product fed into the mill either by the force of gravity or a vacuum. The rotating impeller will force the material outward to the conical screen surface. The materials are resized on the conical screen surface, and, once finished, the product drops through the chamber where it is collected below.
Conical mills are made in a variety of shapes and sizes from tabletop lab models to robust, high- capacity and full-size machines which can be used in the processing of large quantities of materials. The impeller and the screen can be customized for different individual uses. The milling machines can be used not only for the reduction of particle sizes but also for the deagglomeration, dispersion, sieving, and mixing of particles. The applications of a conical mill vary but are mostly found within the food, cosmetics, chemical, and pharmaceutical industries. They are used, as an example, in the breaking down of damaged pharmaceutical tablets before grinding them and reforming them back to their desired shape.
The conical mill has exceptionally marked advantages when compared to other mills. The conical mill has low noise pollution, minimum heat and dust releasing, and a more-uniform particle size, flexibility in design, and a higher carrying capacity. The principal concept of the conical mill originated back in 1976 and has been developed little by little where, today, they are made with a variety of sieves and impellers. The mill head is mounted on a mobile hoist which allows for an easy up-or-down movement for container docking, tablet presses, and other processes. The mill head of a conical mill can be dismounted for easy cleaning access.
Modern hammer mills operate on a rather straightforward principle. To crush the intended material, one needs a suitable engine, strong crushing hammers, and knives. A quick-moving rotor’s hammer impacts the stationary powder bed. The hammer mills break down the materials between the hammers and the casing and then sieve them until they are refined enough to fall through the sieve at the bottom. The hammer mill handles both the fibrous and brittle materials. The fibrous materials will require projecting parts on the casing to facilitate a cutting motion. Hammer mills are categorized into one of two types, namely the horizontal shaft or the vertical shaft. Abrasion-resistant materials can be used to coat and protect impact surfaces made of materials like steel or stainless steel.
Hammer blades can have flat or sharp edges on each side of the blade. The shape of the hammer is varied to suit the mill or the desired task at hand; the most basic shapes adopted for a hammer are either a stirrup shape or a bar shape. Stainless steel hammers can be used to handle pharmaceuticals. Tablet granulation involves the use of bar-shaped hammers. Stirrup hammers, meanwhile, are used to produce a finer particle size.
There are swing or rigid hammers available for use. The free-swinging screen gives clearance in between the hammers and the screens and will increase if an excessive build-up takes place inside the mill. An enclosed chamber is made to enclose the mesh screen or grid and this allows the materials to pass through. There are no woven screens for this type of mill, but rather a metal sheet that has holes and slots in varying thicknesses is used as a screen.
The particles are fed into the crushing chamber through the feeding mechanism. The hammer mill makes use of gravity or a metering system for feeding and this greatly depends on the design of the hammer. In some applications where the product’s uniformity is important, the metering systems are recommended since they eliminate any variables that may hinder the quality of the resultant product. In this case, a pneumatic rotating valve can be found between the crushing chambers; a feeding hopper is a good example of this type of mechanism.
The insertion of particles into the crushing chambers is facilitated entirely by the force of gravity. A control box can be used to turn the machine on or off. The electric motor and feeding system can be controlled depending on user requirements. Some pharmaceutical milling machines have a display panel that allows users to monitor every process that is done. The mill can run at high speeds between 2,500 to 60,000 revolutions per minute. The hammers will typically rotate either clockwise or anticlockwise on the horizontal shafts. This can be affected by the rotation of the rotor.
With this variety of mill, the feed material is usually between 4 to 8mm in size and is fed into the grinding chamber through the intake chute located at the door of the mill. The size reduction takes place in between the axially-adjustable disc stator and the rotating grinder disc that operates at very high peripheral speeds concerning the cutting or shearing principle. The actual grinding is done in stages through a grinding gap originating from the inside to the outside. The ground product exits the milling zone through the defined gap and, whenever a precise top restraint is required, the mill can be used in combination with a suitable screening machine.
The large and oversized particles are rerouted back to the feeding zone where they are reprocessed. This mill is usually used to finely grind plastics at an ambient temperature using this type of technology. If, however, the feed material happens to be heat sensitive the cryogenic mode is used.
Unlike fine-cut mills, coarse-cut mills are used in areas of application where the materials to be ground are not required to be finely crushed. The cutting tools in this type of mill allow for an easy and not as rigid milling process. These types of mills are usually used in the food industry where some food particles are ground and are not to be finely crushed but, rather, moderately crushed. Coarse milling makes use of specialized milling screens that can lightly crush and cut the sharp edges of the materials to be milled.
The screen is mechanically-rotated by the rotary forces with the materials inside. The fast-rotating rough surfaces cut the material’s edges, trimming them to smaller sizes as required by the users. Typical examples of products manufactured through this type of mill include sugar and coarse salt. They are powered mostly by electricity for better machine efficiency, but some mills are used in homes where a hand crank is used to grind the materials.
A common part of the reduction process is a grinding mill that takes grain sized materials that are larger than that which is required by a process and breaks them down to fine powder. Grinding mills are reduction machines that process materials into a finer form. They include rod mills, ball mills, and attrition mills. Grinding mills reduce materials by grinding, pulverizing, or comminuting materials to a fine powder and do not perform crushing or granulation processes.
The characteristics of the materials selected for a grinding mill are hardness, brittleness, toughness, abrasiveness, stickiness, softness, melting temperature, close grained or cellular, specific gravity, moisture content, chemical stability, homogeneity, and purity with hardness being the most important characteristic. Grinding material that is too hard can damage the mill and is processed by specialized grinding mills.
Brittleness, the degree to which a material breaks, is a necessity for grinding mills since grinding materials that are not brittle is difficult. In addition, moisture content has to be considered due to the fact that moist materials will stick to the interior surface of a grinding mill.
In the initial stages of the grinding mill process, the final size of the processed material is determined using the degree of fineness as the parameter. This is normally a proportion of the original material that is finer than its original size. Fine grind milling has a proportional percentage of 90% up to 95% of the original material with demanding applications requiring proportions of 99%.
Grinding mills are divided into tumbling, rolling, and very fine grinding mills with fine grinding mills being high speed hammer mills, vibrating mills, pin mills, turbo mills, fluid energy mills, and stirred mills. A grinding mill circuit includes the feed system, mill, classifier, separator, and product collector. Closed circuit grinding mills return large particles for remilling while open circuit grinding mills do not feedback in a loop.
The different types of mills, belonging to the categories of mills previously listed above, include:
Wet grinding is also known as wet milling. It is a process in which the materials are in a liquid form or a slurry sludge. Agglomerates are usually broken down using this type of mill. Throughout history, companies have been manufacturing machines that were designed to process damp materials. As time progressed, people started to form newer products which needed microscopic particles. The demand for these materials increased, but the mills present at that time were unable to keep up. The equipment had to be changed and so did the processing capabilities.
The initial process associated with wet grinding is known as de-agglomeration. For example, some products like paint molecules will end up clumping together to create agglomerates and cause the product to have tiny lumps inside it. The machines will take in this product and process it through a close-tolerance clearing which forces the particles to break apart. To keep the particles from restructuring, the formulation must be perfect in order to coat all the particles and keep them from restructuring.
The second procedure takes the particles and then shears them down to the desired sizes. There are many items associated with these mills designed and equipped with components that can break down the particles. There are fluidizing diskettes, spacers, and materials added inside the chamber which are agitated by the shaft circulating the disk. The clearances between the medium, diskettes, and the shaft are small and, as the particles are forced through the spaces, the pressure will cause these particles to break apart. After numerous passes through the machine, particles are reduced down to sub-micro levels; it may take several passes through for them to be perfectly broken down.
Rotor stator wet milling is mainly used by the pharmaceutical industry to reduce particle size. The process of rotor stator wet milling takes particles with strong bonds and breaks them down for future processing. The rotor spins inside the stator that creates action that pulls the material through the slots in the stator. As particles are fed through the narrow gaps between the stator and rotor, their size is sheared down.
The principle behind the process of a rotor stator wet mill is to break down materials by dispersing them in a liquid. Shearing takes place in the narrow gaps between the static cone shape of the stator and the rapid rotation of the cone shaped rotor. The rotor and stator are made from hardened, durable materials such as steel and corundum. Each rotor stator wet milling manufacturer designs their equipment with different sizes for the rotor and stator to fit the required comminution.
The phrase “ball mill” is used to define a grinding mill that has spherical balls inside. The length covered by the mill is equal to the diameter of the mill body. They are widely used in metallurgy, electric power, and mining activities. The ball mills are very adaptable and can be used across a wide variety of materials and have an outstanding capacity. Their main characteristic is that ball mills are very effective at processing both wet and dry materials.
Balls are used in ball mills to grind materials. The ball mill is switched on and allowed to begin rotating, either on its vertical or horizontal axis. The material is put into the chamber of the ball mill, where it is subjected to the spinning balls. The balls strike the contained substance as they bounce about in the ball mill while it spins. These blows have enough force to reduce the material to a finer, less coarse medium as the material gets ground into a finer, powder-like material by the rotation's force.
A ball mill has to reach critical speed in order to function. The critical speed of a ball mill is the speed at which the contained balls start to revolve along the inside walls. The balls inside a ball mill will remain motionless at the bottom where they will have little to no effect on the material if the threshold speed is not reached.
Ball mills have some key differences from conventional milling equipment. First off, a cutting tool is absent from ball mills. Ball mills use the force of moving balls instead of the rotary cutting tool that conventional milling machines use. They don't require a cutting tool as a consequence.
Ball mills and conventional milling machines differ from one another in their distinct functions. Ball mills and conventional milling equipment are both used to grind materials into smaller pieces. Ball bills can handle materials like ore, ceramics, and paint, whereas conventional milling machines can handle huge workpieces.
In a tube mill, the grinding bodies are spherical but the length of the mill body is longer in proportion to the diameter. They consist of rotating cylinders with a perfectly plain interior and hard round balls. The lining of the mills is made of hardwood or iron alloys like steel or manganese steel.
The revolving cylinders that make up a tube mill typically have a simple interior. On their interior walls, there are a lot of flat balls. They are different from roller mills in that they don't have a separate cooling system for the welded arc, which means a third cooling source is needed. Additionally, they frequently employ more advanced welding tools, such as cutting-edge laser welders. To further enhance the quality of the end product, the tubes are occasionally hand-woven as well. Perhaps the best-known use of these mills is their creation of plumbing tubes or pipes in sizes that are typically available in plumbing material warehouses and construction supply stores. Tube mills typically consist of a long, cylindrical drum with a number of balls on each side of it that can spin at very high rates and provide the hardness required for drainage systems.
Similar to belt grinders, tube mills operate by the operator loading the material (whether wire or sheet steel) into the drum, which then activates the "grinders." When cutting wire or sheet steel to the required diameter, the "grinder" will oscillate back and forth within the cylinder. For this technique, some will use a manual crank, while others will utilize an electric motor. A common version of this fundamental technique involves either inserting wire from the inside or completely removing the object by grinding it from outside. This is done to get a constant diameter and constant profile that will make fitting and cleanup simple.
For the purpose of actually grinding ore, tube mills combine two revolving discs, one of which contains a ball, with a grinding wheel. Before being spun around the spindle and over the grinding surface, material (often steel) that has been flattened is placed inside the ball mill. As they move through, the balls within the disc are chipped off, leaving only the edges that are then used to create the metal's cutting edge. The majority of belt grinders operate in a similar manner.
In contrast to ball mills, rod mills employ long rods as the grinding medium. Similar to grinding balls in a ball mill, the rods tumble inside the mill to grind materials like limestone or various ores. The length-to-diameter ratio is kept between 1.4 and 1.6 to avoid circumstances that might result in rod charge tangling. Rod mills may process feed as small as 50 mm and deliver products with sizes ranging from 3000 mm to 270 mm. Line contact between the rods that stretch the length of the mill produces the grinding action. In order to simulate a row of roll crushers, rods spin and tumble in a parallel orientation. As a result, the generation of slime is reduced and coarse material is ground more effectively.
Only the overflow mill—not the end peripheral discharge or the center peripheral discharge—is one of the three primary types of rod mills widely used. Rod mills for wet grinding are often employed in the mineral processing sector. Although it is utilized in some places, dry grinding has drawbacks and should only be used when absolutely required. Because the rods are rolled rather than cascaded, rod mills run at a slower pace than ball mills. Rod mills require less steel than ball mills for a comparable grind because the media and ore make better contact at a reduced speed. Broken and damaged rods should be removed in order to keep the rod charge in excellent operating order. Rod mills often demand more operator focus. The rods must remain almost parallel to each other at all times. Rod tangles and reduced grinding action are the two effects of misaligned rods. The highest rod length is around 6.1 meters (20 ft). As a result, rod mills' length, diameter, and capacity are constrained. Bulkier rods exerting force on the loaders and liners cause the mill liners to wear out more quickly.
Pebble mills, a type of ball mill, rely on natural pebbles instead of spherical balls that roll about in the medium, crushing materials put inside. They are used to grind hard materials such as minerals, glass, advanced ceramics, and semiconductor materials down to 1 micron or less in size. Pebble mills are also now referred to as ceramic-lined mills. The pebble mill's residence duration ensures that every particle receives uniform treatment, leading to a narrow dispersion of particle size.
Flint rocks were used as the grinding material of pebble mills for a very long time. Nowadays, industries employ grinding medium with an aluminum oxide composition of 90% - 96% and high-alumina brick. Aluminum oxide (alumina) brick, which is exceptionally durable and won't contaminate most items, is used to line the new pebble mills.
Small-sized alumina grinding mediums are half-filled in the slowly-rotating containers. The particles are continuously struck between the grinding media as the vessel rotates, the media is elevated, and it cascades down. The benefit of pebble mills being self-contained is that it helps protect workers from exposure to the milled product. Both dry and wet grinding may be done using pebble mills. When wet grinding is used, the granules are also disseminated in the liquid.
In the grate-discharge mill, the diaphragm is in the form of grating and it confines the ball discharge to the end of the mill. The space between the diaphragm and the other end of the mill holds a scoop of the ground material.
In the air-swept mill, a powerful stream of air is channeled through the mill and it removes the small and finer particles that are produced in the grinding process. The airstream is passed through the classifier and the large rejected materials are returned to the mill. It has balls in its horizontal rotating device which is powered by an outer gear.
Mixing, by definition, involves the systematic creation of one material by intermingling two or more different individual ingredients or particles. The ingredients are usually fed into a rotating impeller through a trailing edge. By mixing, the material flow throughout the vessel is completely dependent on the type and the size of the particles. The rotating speed of the impeller is also an important aspect. There are three types of mixers, namely the horizontal mixer, spiral mixer, and planetary mixer. The horizontal mixer has the capability of mixing large amounts of new mixture before it is passed out into a trough for easy transportation. The spiral mixer, on the other hand, has spiral blades that rotate to aid the mixing process with unparalleled efficiency.
The planetary mixer is a basic home appliance that is used to mix various foodstuffs. It comprises a stationary bowl and rotating blades at the base that cut down and crush material, mixing them into one. Mixing is comparable to dispersion and they both involve the mingling of particles. The mixing employs a flow-driven process to obtain results. Two or more liquids are then melded and an applicable soluble solid is dissolved. The size of the impeller in mixing is dependent on the various properties of the ingredients. These properties include viscosity and texture.
The milling process is somewhat different between mixing and dispersion processes. Mixing goes a step further as there is particle-size reduction. A pre-dispersed blend that requires additional particle-size reduction is then taken to a mill for the processing unit. The mill components take on the particles using numerous mechanical forces from the medium, pegs, and screens, to achieve the required particle breakdown. This process helps make the best use of the yield of the ingredients and, in many cases, the functionality of the product. In the case of coatings and inks, it aids with color development, film attributes, and product flow.
Concerning the ideal resulting particle size, the mill can be modified and the environmental temperature controlled to achieve the anticipated results. There are several types of mills on the market, and the selection process can be daunting. There are many key features to investigate during this period, and equipment suppliers often offer experimental services to ensure an appropriate match between equipment and request is met.
This chapter will discuss the applications and benefits of mills. The maintenance of milling machines will also be discussed in this chapter.
Mills are used in a wide variety of industries for basic home applications. Some of the main applications are listed in this section.
The pharmaceutical and chemical manufacturing industries make use of mills to grind and break down large particles to form powders or fine-grained medicines. The required ingredients are crushed and ground in hammer mills to obtain an intermediate powder grade. The hammer mill is typically used to obtain a nearly-precise grain size. This type of mill is only held back by the fact that it can not process sticky ingredients since they can get stuck to the perforated screen.
In the food processing industry, the mills can be used in the crushing and grinding of various types of legumes. They are used to crush nutshells, soybeans, certain seeds, and various types of beans. A hammer mill that has lower hammer blows is usually used to remove the hard shells.
The mills are also used in micronization in the medicinal and pharmaceutical industries. The small medicine grains are ground so that they can be fit into capsule packages in very precise quantities. The mills, therefore, come into play as they reduce the sizes of the particles within the medicines before they are inserted into their respective packages.
Mills also serve an important role as the large particles are broken down into smaller particles so that they can be dissolved into solvents more quickly. Scientifically, smaller particles have a quicker rate of dissolving and thus save time and expenses on resources.
Another important application of industrial mills is that they are used to mix two or more dissimilar solid powders. They aid in producing a consistent mixture of the two compounds to form a perfectly-bonded fibrous solid compound.
Numerous ingredients bring about active reactions when they are added to some formulations. Therefore, these ingredients are slightly crushed by mills to improve their chemical activeness.
The automobile and mechanical industries make use of mills for versatile scrapping processes. Both extra, unneeded materials and spent metals are processed inside the mills where they are crushed before they are sent off for melting. After melting, the resulting product is then used in the production of new components or recycled.
Modern milling machines are used in industrial and home applications because they come with notable benefits which make them favorable when compared to other machines that perform similar functions. For instance, the size and robust build of the milling machine give it a tremendous supporting structure which allows it to handle huge and heavy parts without damaging itself. Furthermore, the mills are made from interchangeable parts that can be replaced so that the mill remains operational despite any damages it may face.
Modern machines are also controlled by computers to enhance control options for varying parts and components to be ground. The rate of grinding or the cutting tools to be used can be changed by computers for better machine efficiency. The usage of the mills provides a perfect touch and finish to the components being ground and thus reduces possible human errors. Additionally, the use of computer programs in the mills ensures that the processes are completely automated. Some components or ingredients added to the mill require very fine and accurate cuts which are difficult to obtain manually.
The mills are also customizable to suit end-user requirements or transportation and packaging constraints. They also come in with a wide variety of cutters that can be used for different scenarios and can perform these cuts simultaneously while saving valuable time and power. It also has the capability of producing complex shapes due to the availability of multi-teeth and single-cutting tools. Their simultaneous cutting also allows for the production of individual pieces or ingredients in large batches at a time.
Despite their unparalleled advantages, milling machines do come up with a notable number of disadvantages. For instance, the mills are quite expensive to purchase because they require a huge initial investment. They also run on electricity or various fuels and they do not go easy on the bills as they rack up fairly substantial operating costs. Transportation of these machines is very difficult since they come in various shapes and sizes with unbounded weight classes. It is, therefore, quite difficult to transport them from one point to another. Apart from purchasing and operating costs, milling machines are not easy to use and they require extensive and skilled manpower to operate. This means that milling machines can not be easily operated by laymen.
A defective bearing seal, when caught early, can be quick and cheap when compared to a complete bearing refit from a substantial bearing failure. The buildup of waste material residue is hard to find unless the mill is clean and it is a critical pointer in diagnosing damage to the fastener tension or any other failure issues. As a result, routine inspections for any damage to the equipment, protective coverings, and cracking of the grout should be performed regularly. An early scheduled repair can prevent more extensive damage.
However straightforward cleaning a mill may seem to be, it is not as easy as hosing the equipment down periodically. Pressure hosing a hot casting may cause it to form cracks, or shrink it beyond its contained bearing, reducing the bearing room and rotating the bearing on the shaft. A high-pressure spray fired thoughtlessly could result in water ingress behind the bearing seal and, thus, cause premature bearing disaster. It is therefore important to make sure that the staff involved is trained and competent for the washing task. It is also advisable to contact the supplier who may be able to provide other important servicing details.
In conclusion, mills are devices that may be used in households or in an industrial setting to grind, crush, or cut huge materials into smaller, more manageable components. The mills are divided into many varieties according to their intended usage. Some mills are utilized in the mining sector where they are used to crush mineral ores from stones in order to separate them from the pure metal. To ensure that the mill lasts its whole lifespan and continues to function properly and efficiently, it is also crucial to have it cleaned and maintained.
Size reduction equipment refers to machines that crush and grind materials to reduce their size. Pulverizers are a type of size equipment, the names are used interchangeably. Size reduction is an essential...
Agitators are equipment used in homogenizing media inside a tank. It works by rotating the impeller at its immersed end at a controlled speed or revolutions per minute (rpm). The work exerted by...
Drum mixers are mixers that are used for mixing free flowing materials by rotating them forward and reverse with welded chutes or flights that fluidize the mixture. The design of drum mixers gives them...
An emulsifier is an emulsion device used for colloidal dispersion of liquid droplets of immiscible liquids in the presence of an emulsifying agent. It enables the combining of non-soluble solutions or liquids...
High shear mixers, also known as high shear reactors (HSRs), rotor-stator mixers, and high shear homogenizers, are used to emulsify, homogenize, disperse, grind and/or dissolve immiscible mixtures with components of the same or different phases...
A homogenizer is a type of mixing equipment used to create a uniform and consistent mixture. It works by breaking the components and evenly distributing them throughout the solution. The components are either immiscible, have varying sizes, or are in different phases from each other...
An industrial blender is a machine for large-scale production that consists of a large tank capable of mixing and blending batches of manufacturing materials to create a reaction between the materials. The many uses for industrial blenders are due to their capacity and...
A tank mixer is a mixing device that blends several different ingredients in a single tank to make a single solution. It is a mixing process capable of mixing wettable powders, liquids, emulsifiable concentrates, and surfactants. They mix and blend...
A mixer is a complex and precise tool that is used in combining and mixing of substances and chemicals for manufacturing, production, and industrial use. There are many types of industrial mixers including...
A plastic tank is a large capacity liquid or granular storage unit that can be vertical, horizontal, below or above ground, as well as movable. They are designed to hold several gallons of a variety of substances for long periods without experiencing wear, weathering, or deterioration...
A plastic water tank is a large capacity container designed to store water for household, agricultural, irrigation, and industrial manufacturing use. There are various types of water tanks produced to meet the needs of specific applications, with...
A poly tank is a plastic storage tank used to store, transport, and collect water, other liquids, and granular or powder materials. They are made of polyethylene or polypropylene and are a cost effective, lightweight, and easy to handle...
Pressure tanks are vessels that are used to store, hold, and/or convey gasses, vapors and fluids at pressures greater than atmospheric pressure, also known as high pressures...
Pressure vessels are enclosed containers used to hold liquids, vapors, and gases at a pressure significantly higher or lower than the ambient pressure. They are widely used in various industries such as...
Stainless steel tanks are widely used in food, beverage, dairy, medicine, cosmetics, and other manufacturing processes where cleanliness and purity are important. These are also used in industrial plants for storing chemicals and gases where strong resistance from chemical degradation is required...
A vertical conveyor is an engineered mechanical method for moving goods, products, supplies, parts, and components from a lower level to a higher level or from a higher level to a lower level. They are...