Agitators
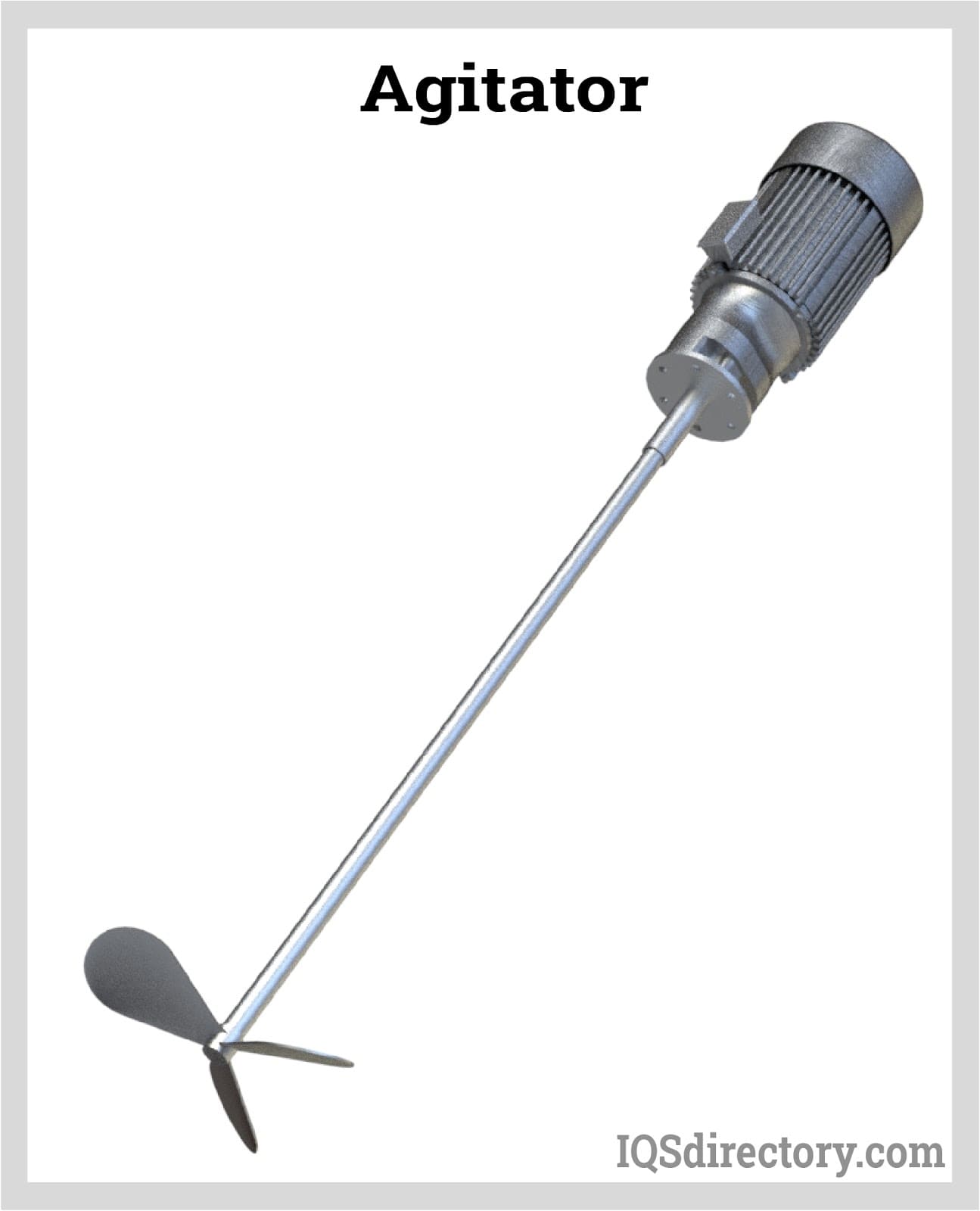
Agitators are equipment used in homogenizing media inside a tank. It works by rotating the impeller at its immersed end at a controlled speed or revolutions per minute (rpm). The work exerted by...
Please fill out the following form to submit a Request for Quote to any of the following companies listed on
The article provides in depth and complete information regarding tank mixers and their use.
You will learn:
A tank mixer is a mixing device that blends several different ingredients in a single tank to make a single solution. It is a mixing process capable of mixing wettable powders, liquids, emulsifiable concentrates, and surfactants. They mix and blend multiple products to a uniform and consistent final product. They are used for pharmaceuticals, food, beverage, water treatment, and chemical processing.
The popularity of tank mixers is due to their reliability and efficiency. They are cost saving devices that make it possible to combine varied ingredients in a single mixing process. There are several varieties of tank mixers each designed to serve the needs of a specific application.
Tank mixers have common components designed to enhance their efficiency and mixing process. How the components are assembled varies between the types of tank mixers and their manufacturer. With tank mixers, there is a wide variety of sizes from portable ones to large anchored tanks that are top mounted and plate mounted.
The motor is the power source that drives the impeller, creating the mixing action in the tank. The motor size and power rating depend on the size and viscosity of the liquid being mixed.
The impeller is the rotating component of the mixer that generates the mixing action. Different impeller types, such as propellers, turbines, and high-shear impellers, are designed to handle different flow rates and viscosity levels.
The shaft connects the impeller to the motor and is responsible for transmitting the power from the motor to the impeller. The shaft should be made of a material that is corrosion-resistant and durable.
The seal is used to prevent liquid from leaking out of the tank through the gap between the shaft and the tank wall. It should be designed to handle the temperature, pressure, and chemical properties of the liquid being mixed.
In many cases, tank mixers are custom designed to specifically meet the needs of a particular industry since each mixing application has its individual and unique challenges. Engineers take the common components of a tank mixer and arrange them to be efficient and easy to operate. It is for this reason that there are several types of tank mixers, which change according to the type of impeller, mixing speed, and the materials that can be mixed.
These mixers are mounted on the top of the tank and are used for mixing high-viscosity fluids. They are available in different impeller types, such as propeller and turbine, and can be equipped with a variable speed drive for greater control over the mixing process.
These mixers are installed on the side of the tank and are ideal for mixing low-viscosity fluids. They are also available in different impeller types and can be designed for in-tank cleaning.
These mixers are installed on the bottom of the tank and are used for mixing high-viscosity fluids that require heat transfer. They are equipped with a heating jacket or coil that enables heating or cooling of the liquid being mixed.
These mixers use a magnetic coupling to transfer power from the motor to the impeller, eliminating the need for a shaft seal. They are ideal for mixing corrosive and hazardous fluids and are easy to clean and maintain.
These mixers can be easily moved from one tank to another, making them ideal for smaller operations or temporary mixing requirements. They can be equipped with different impeller types and power ratings.
Static mixers are stationary mixers that use a series of baffles or elements to mix fluids as they flow through the mixer. They are typically used in low-viscosity applications where the goal is to achieve a uniform mixture without using a mechanical mixer. Static mixers are often used in the chemical and water treatment industries.
Jet mixers use a high-velocity stream of liquid or gas to create turbulence in a tank, which helps to mix the contents. They are often used in applications where high shear forces are required, such as in the homogenization of liquids or the dispersion of gasses. Jet mixers are commonly used in the chemical, pharmaceutical, and food and beverage industries.
In-line mixers are mixers that are installed in a pipeline, rather than in a tank. They use a combination of high velocity and turbulence to mix the contents of the pipeline. In-line mixers are often used in the chemical, food and beverage, and pharmaceutical industries, where it is important to maintain a constant flow of mixed fluids.
High shear mixers use a combination of high speed and high turbulence to mix the contents of a tank. They are often used in applications where the goal is to achieve a very fine, uniform mixture. High shear mixers are commonly used in the chemical, pharmaceutical, and food and beverage industries.
Each of these types of mixers has specific applications where they are most effective. The selection of the appropriate mixer will depend on the specific requirements of the application, such as the viscosity of the fluids being mixed, the desired mixing intensity, and the size and geometry of the tank or pipeline.
Selecting the right type of tank mixer is crucial for ensuring optimal performance and efficiency. There are several factors to consider when choosing a mixer, including the viscosity and specific gravity of the liquid being mixed, the volume of the tank, and the desired mixing speed and intensity. Integral to this process is having a clear understanding of the mixing problem that is going to be resolved.
Viscosity is the measure of a liquid's resistance to flow. The viscosity of a liquid can range from thin and watery to thick and sticky. The higher the viscosity, the more difficult it is to mix the liquid effectively. When selecting a tank mixer, it is important to consider the viscosity of the liquid being mixed and choose a mixer that is capable of producing enough shear force to effectively mix the liquid.
Specific gravity is the ratio of the density of a liquid to the density of water. It can have an impact on the type of mixer that is selected. In general, liquids with higher specific gravity require more energy to mix than liquids with lower specific gravity. When selecting a tank mixer, it is important to consider the specific gravity of the liquid being mixed and choose a mixer that is capable of providing enough mixing energy to effectively mix the liquid.
The volume of the tank being mixed can have an impact on the type of mixer that is selected. Larger tanks may require more powerful mixers, while smaller tanks may be adequately mixed by less powerful mixers. When selecting a tank mixer, it is important to consider the volume of the tank being mixed and choose a mixer that is capable of providing adequate mixing energy for the volume of the tank.
The desired mixing speed and intensity can have an impact on the type of mixer that is selected. Some applications require high-speed, high-intensity mixing, while others require more gentle mixing. When selecting a tank mixer, it is important to consider the desired mixing speed and intensity and choose a mixer that is capable of providing the necessary mixing energy for the application.
All of these factors can affect the selection of a tank mixer. For example, a high-viscosity liquid may require a mixer with more powerful shear forces, while a low-viscosity liquid may be adequately mixed with a less powerful mixer. A larger tank may require a more powerful mixer to provide adequate mixing energy, while a smaller tank may be adequately mixed with a less powerful mixer. The specific gravity of the liquid being mixed can also impact the selection of a mixer, as liquids with higher specific gravity may require more energy to mix effectively. Finally, the desired mixing speed and intensity can impact the selection of a mixer, as different mixers are capable of producing different levels of mixing energy.
The selection of materials for tank mixers is also an important consideration, as it can affect the performance, durability, and safety of the equipment. Factors to consider include the chemical compatibility of the material with the liquids being mixed and the temperature and pressure requirements. Materials used to produce a mixing tank range from plastics, glass, and rubber to steel and copper.
The material used for the mixer must be compatible with the chemicals being mixed. Some chemicals may react with certain materials, leading to corrosion, contamination, or other issues. It is important to carefully review the chemical compatibility chart for any materials being used in the mixer.
The material used for the mixer must be able to withstand the pressure or temperature requirements of the application. Some materials may become brittle or fail under high pressure or temperature conditions, while others may not provide adequate insulation for hot or cold applications.
Based on this knowledge of these factors, common materials used for tank mixers include stainless steel, carbon steel, and plastics such as polyethylene and polypropylene. Below is an explanation of each of these materials regarding their use as tank mixers.
Stainless steel is a popular choice for tank mixers because it is corrosion-resistant, durable, and easy to clean. It is commonly used in food and beverage, pharmaceutical, and chemical processing applications.
Carbon steel is a more affordable option than stainless steel, but it is not as corrosion-resistant. It is commonly used in applications where corrosion is not a significant concern.
Plastics such as polypropylene and polyethylene are lightweight, corrosion-resistant, and affordable. They are commonly used in chemical processing and water treatment applications.
Coatings, such as epoxy and ceramic, are used for protection against corrosion and wear in high-stress applications. When selecting materials for tank mixers, it is important to consider the requirements of the application and consult with a supplier or manufacturer for advice on the best materials to use for a tank mixer in order to ensure reliable and safe operation.
As with any type of industrial equipment, scheduled maintenance is essential to the performance and longevity of a tank mixer. Maintenance helps detect any issues and prevent more extensive damage or failure. Manufacturers advise the use of a maintenance schedule that assists in tracking any variations in a tank mixer's performance. Most important is lubrication due to the continual and constant use of tank mixers.
Regular inspections should be conducted to check for signs of wear and tear, damage, or corrosion. These inspections should also include checks for proper alignment, lubrication, and tightness of bolts and fasteners.
Lubrication of bearings, gears, and other moving parts should be performed regularly to ensure proper operation and reduce the risk of premature failure.
Regular cleaning of the mixer is important to remove any buildup of material that can interfere with the mixer's operation or cause contamination.
Calibration of any sensors or control systems used in the mixer should be conducted regularly to ensure accurate readings and prevent errors.
Any worn or damaged parts should be replaced promptly to avoid further damage or failure of the mixer.
Meanwhile, when repairs may finally be necessary, the proper steps are suggested.
The first step in repairing a mixer is identifying the problem. This may involve troubleshooting the system to determine the cause of the issue. Once the problem has been identified, the mixer may need to be disassembled to access the damaged or faulty parts. The damaged or faulty parts can be repaired or replaced depending on the severity of the damage. Once the parts have been repaired or replaced, the mixer should be reassembled and tested to ensure proper operation.
After repair, the mixer should be tested and calibrated to ensure that it is functioning properly and within the appropriate parameters.
Additionally it is important to use high-quality replacement parts and have the repairs performed by a qualified technician. Neglecting repairs can lead to decreased performance, increased risk of damage or injury, and even equipment failure.
Custom designs and the adaptability of tank mixers makes them a valuable asset for several industrial processes. What is most valuable about tank mixers is their durability, which is a characteristic that is essential for production and assembly operations. Equipment that consistently performs helps in avoiding downtime and production delays.
Tank mixers can improve product quality by ensuring that ingredients are thoroughly mixed and blended. This can result in a more consistent product with fewer defects or inconsistencies. Tank mixers can also help to prevent sedimentation and ensure that ingredients are evenly distributed throughout the mixture.
Tank mixers can increase efficiency by reducing mixing times and minimizing the need for manual labor. Automated tank mixers can also be programmed to mix batches of products on a regular basis, which can help to streamline production processes and reduce downtime.
Tank mixers are versatile and can be used for a wide range of applications across different industries. They can be used for mixing liquids and solids, as well as for dissolving, dispersing, and emulsifying ingredients.
Tank mixers can be a cost-effective solution for mixing and blending processes. They can reduce the need for manual labor and can help to minimize material waste. Tank mixers can also be designed to be energy-efficient, which can help to reduce operational costs.
Tank mixers can improve safety by minimizing the need for manual mixing, which can reduce the risk of workplace injuries. They can also be designed to be explosion-proof, which can help to prevent accidents in hazardous environments.
Tank mixers can be easily scaled up or down to meet the needs of different production processes. This can make them a versatile solution for companies that need to adjust their production processes as demand changes.
Tank mixers are typically designed for easy maintenance, which can help to minimize downtime and reduce maintenance costs. Many tank mixers are designed to be easy to clean, which can help to prevent contamination and ensure product quality.
Tank mixers can provide consistent results across different batches of products. This can be especially important for companies that need to ensure that their products meet strict quality standards.
Tank mixers can help to reduce waste by ensuring that ingredients are thoroughly mixed and blended, which can help to minimize material waste. They can also be designed to be energy-efficient, which can help to reduce waste associated with energy consumption.
Tank mixers can be customized to meet the specific needs of different applications. They can be designed to handle different volumes and viscosities of liquids, as well as to accommodate different types of impellers and mixers.
Tank mixers are found in any production operation that requires the mixing or blending of products or materials. They are an essential part of the pharmaceutical industry for their ability to take an assembly of ingredients and blend them into a smooth and pliable mixture. The most obvious use of tank mixers is in food production where blending and mixing are important to the flavor and taste of a product.
Tank mixers are widely used in the food and beverage industry for mixing ingredients, homogenization, blending, and emulsification of food products. They are commonly used in the production of dairy products, bakery goods, beverages, and sauces, among other food products.
In chemical processing, tank mixers are used for mixing and blending of various chemical compounds, such as adhesives, paints, coatings, resins, and polymers. Tank mixers can also be used for dissolving solids into liquids, and for mixing two or more liquids with different viscosities.
In the pharmaceutical industry, tank mixers are used for mixing and blending of active pharmaceutical ingredients (APIs) with excipients, as well as for the production of suspensions, emulsions, and creams. They are also used for the production of sterile solutions and injectables.
In water treatment, tank mixers are used for mixing chemicals and coagulants with water to facilitate the removal of impurities, such as bacteria, viruses, and other contaminants. They are also used for mixing and blending of chemicals used for pH adjustment, flocculation, and disinfection.
Tank mixers are used in cosmetics manufacturing for mixing and blending of ingredients, such as oils, emulsifiers, thickeners, and fragrances. They are commonly used for the production of creams, lotions, and gels.
In biotechnology, tank mixers are used for mixing and blending of biological materials, such as cell cultures, fermentation media, and protein solutions. They are commonly used in the production of vaccines, antibodies, and other biopharmaceuticals.
Tank mixers are used in the petrochemical industry for mixing and blending of various petroleum products, such as fuels, lubricants, and additives. They are also used for the production of specialty chemicals, such as surfactants and solvents.
In the mining industry, tank mixers are used for mixing and blending of chemicals used for the extraction of minerals from ores. They are also used for the production of slurry solutions, which are used for transporting minerals through pipelines.
Tank mixers are used in the pulp and paper industry for mixing and blending of chemicals used for pulping, bleaching, and de-inking of paper products. They are also used for mixing and blending of adhesives, coatings, and other chemicals used in paper manufacturing.
In waste management, tank mixers are used for mixing and blending of chemicals used for the treatment of waste streams, such as municipal wastewater and industrial effluent. They are also used for the production of biofuels and other renewable energy sources.
International and national governments and organizations have established regulations, guidelines, and standards for the use of tank mixers. As with any form of industrial equipment, tank mixers require oversight for the protection of processes, the environment, and workers. These stipulations are constantly being reformed, updated, and edited to meet the needs of technological developments.
OSHA is responsible for setting and enforcing workplace safety standards, including those related to the use of tank mixers. OSHA has specific regulations that apply to the use of mixers, including requirements for lockout/tagout procedures, guarding, and personal protective equipment.
The EPA is responsible for enforcing regulations related to the handling and disposal of hazardous waste, including waste generated by the use of tank mixers.
The FDA is responsible for regulating the safety of food, drugs, and medical devices, including tank mixers used in the production of these products. The FDA has specific regulations related to the design and construction of mixers used in food, drug, and medical device production.
At the state and local level, meanwhile, there may be additional laws, regulations, and regulatory agencies that apply to the use of tank mixers. These can vary depending on the state or locality, but may include:
Many states have their own occupational safety and health agencies that enforce workplace safety standards, including those related to the use of tank mixers.
Many states also have a department of environmental protection that enforces regulations related to the handling and disposal of hazardous waste, including waste generated by the use of tank mixers.
In states with a large agricultural industry, the Department of Agriculture may have regulations related to the use of tank mixers in agricultural production.
Additionally, local fire departments may have regulations related to the storage and use of hazardous materials, including those used in tank mixing operations. Regardless of the level of jurisdiction, it is important for companies to be aware of all applicable federal, state, and local regulations related to the use of tank mixers to ensure compliance and prevent workplace injuries or environmental hazards.
As with all forms of heavy duty equipment, there are aspects of tank mixers that have to be monitored and controlled for safety reasons. Regardless of the function of tank mixers, they are a production style equipment that can be dangerous and unsafe if not properly respected and handled. When using them, it is important to be aware of conditions that can be harmful and hazardous.
Air pockets can create inconsistencies in a final product in several ways. For instance, when mixing liquids, air pockets can cause foaming, which can affect product quality and lead to inconsistent results. Additionally, in applications where a product is being mixed with a gas or air, air pockets can prevent proper blending and cause variations in the final product. It is important to design tank mixers with features that reduce the formation of air pockets, such as specialized impellers or agitation techniques.
When air pockets are present in a mixing system, the mixer may produce excessive noise and vibration as it attempts to break up the pockets. This noise and vibration can be hazardous to workers and can lead to workplace injuries or hearing loss. To reduce the risk of injury, it is important to design tank mixers with features that reduce the formation of air pockets, such as specialized impellers or agitation techniques. Additionally, workers should be provided with appropriate personal protective equipment, such as ear protection, to reduce the risk of hearing damage.
The viscosity of the product being mixed can impact the design and performance of the tank mixer. High viscosity products may require more powerful mixers or impellers to achieve thorough mixing.
Some products may be sensitive to shear, which can cause damage or degradation. It is important to choose a tank mixer that is appropriate for the product being mixed to prevent damage and ensure product quality.
The mixing time required to achieve thorough blending can vary depending on the product being mixed and the design of the mixer. It is important to monitor mixing times to ensure that products are mixed thoroughly and efficiently.
The size and design of the tank can impact the performance of the mixer. The tank should be designed to accommodate the mixer and ensure that products are mixed thoroughly and efficiently.
Proper cleaning and maintenance of the mixer and tank are important to ensure product quality and prevent contamination. The mixer and tank should be designed for easy cleaning and maintenance.
The power requirements of the mixer can impact operational costs. It is important to choose a mixer that is energy-efficient and appropriate for the product being mixed.
Tank mixers can be a safety hazard if not used properly. It is important to follow safety protocols and use appropriate personal protective equipment when operating tank mixers.
Some materials may be incompatible with the materials used in the construction of the tank and mixer. It is important to choose a mixer and tank that are appropriate for the product being mixed to prevent chemical reactions and ensure product quality.
In food and beverage, pharmaceutical, and other industries, hygiene is critical. The tank mixer should be designed to prevent contamination and allow for easy cleaning to ensure that products are safe for consumption.
Depending on the impeller and speed used, tank mixers can cause high shear on products, which can affect the final product quality. Careful selection of the impeller and mixing speed is required to minimize product shear.
As previously discussed, material selection is essential for the longevity of the tank mixer. Materials used in construction should be resistant to corrosion, and wear and tear caused by the product being mixed. Failure to select appropriate materials can result in premature failure of the mixer.
Also, as previously noted, proper installation and maintenance of the mixer are essential for optimal performance. Improper installation can lead to misalignment and cause the mixer to fail prematurely. Similarly, lack of maintenance can lead to equipment breakdown and product contamination.
Despite so many current applications, the future of tank mixers looks even brighter. The future of tank mixers appears to be closely tied to advancements in technology and innovation. Here are a few potential developments that could increase the role of tank mixers in the future:
Smart technology is becoming increasingly prevalent in all areas of industrial equipment, including tank mixers. Smart mixers may include sensors that monitor factors like temperature, pressure, and flow rate, as well as software that can adjust mixing parameters in real time based on this data.
As the demand for sustainable and energy-efficient equipment increases, we may see advancements in tank mixer design that improve efficiency and reduce energy consumption. This could include the use of more efficient motors and the development of new mixing techniques that require less energy.
As manufacturers seek to maximize the use of their equipment, we may see more versatile tank mixers that can be used for a wider range of applications. This could include mixers that can handle a wider range of viscosities, as well as mixers that can be adapted to work in different tank sizes and geometries.
As industrial equipment becomes increasingly connected, we may see tank mixers that are designed to integrate with other equipment, such as pumps, filters, and sensors. This could allow for more seamless and efficient processing, as well as improved data collection and analysis.
Advances in materials science and manufacturing techniques could lead to the development of new materials that are better suited for tank mixer applications. This could include materials that are more resistant to corrosion or wear, as well as materials that are better able to withstand high temperatures and pressures.
Overall, the future of tank mixers will likely be driven by a combination of technological advancements, changing customer demands, and environmental concerns. As the industry continues to evolve, we can expect to see new and innovative solutions for mixing a wide range of fluids in a variety of different applications.
Agitators are equipment used in homogenizing media inside a tank. It works by rotating the impeller at its immersed end at a controlled speed or revolutions per minute (rpm). The work exerted by...
Drum mixers are mixers that are used for mixing free flowing materials by rotating them forward and reverse with welded chutes or flights that fluidize the mixture. The design of drum mixers gives them...
An emulsifier is an emulsion device used for colloidal dispersion of liquid droplets of immiscible liquids in the presence of an emulsifying agent. It enables the combining of non-soluble solutions or liquids...
High shear mixers, also known as high shear reactors (HSRs), rotor-stator mixers, and high shear homogenizers, are used to emulsify, homogenize, disperse, grind and/or dissolve immiscible mixtures with components of the same or different phases...
A homogenizer is a type of mixing equipment used to create a uniform and consistent mixture. It works by breaking the components and evenly distributing them throughout the solution. The components are either immiscible, have varying sizes, or are in different phases from each other...
An industrial blender is a machine for large-scale production that consists of a large tank capable of mixing and blending batches of manufacturing materials to create a reaction between the materials. The many uses for industrial blenders are due to their capacity and...
A mill is a mechanical device that is often a structure, appliance, or machine that is used to break down solid materials into smaller pieces by cutting, grinding, or crushing them. Many industrial processes involve...
A mixer is a complex and precise tool that is used in combining and mixing of substances and chemicals for manufacturing, production, and industrial use. There are many types of industrial mixers including...
A plastic tank is a large capacity liquid or granular storage unit that can be vertical, horizontal, below or above ground, as well as movable. They are designed to hold several gallons of a variety of substances for long periods without experiencing wear, weathering, or deterioration...
A plastic water tank is a large capacity container designed to store water for household, agricultural, irrigation, and industrial manufacturing use. There are various types of water tanks produced to meet the needs of specific applications, with...
A poly tank is a plastic storage tank used to store, transport, and collect water, other liquids, and granular or powder materials. They are made of polyethylene or polypropylene and are a cost effective, lightweight, and easy to handle...
Pressure tanks are vessels that are used to store, hold, and/or convey gasses, vapors and fluids at pressures greater than atmospheric pressure, also known as high pressures...
Pressure vessels are enclosed containers used to hold liquids, vapors, and gases at a pressure significantly higher or lower than the ambient pressure. They are widely used in various industries such as...
Stainless steel tanks are widely used in food, beverage, dairy, medicine, cosmetics, and other manufacturing processes where cleanliness and purity are important. These are also used in industrial plants for storing chemicals and gases where strong resistance from chemical degradation is required...