Pressure Vessels
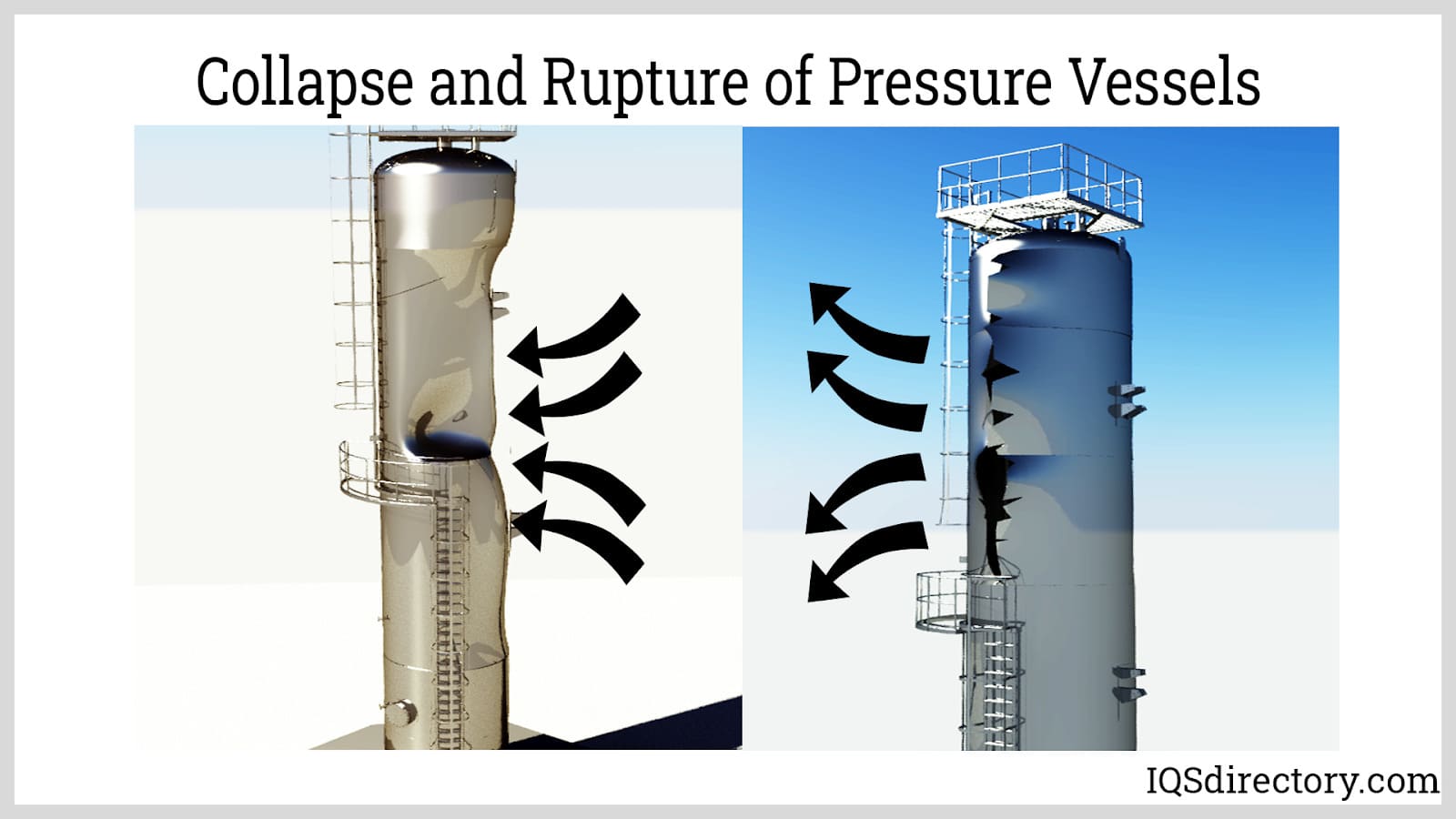
Pressure vessels are enclosed containers used to hold liquids, vapors, and gases at a pressure significantly higher or lower than the ambient pressure. They are widely used in various industries such as...
Please fill out the following form to submit a Request for Quote to any of the following companies listed on
Here is the most complete guide on the internet about
You will learn:
This chapter will discuss what pressure tanks are, their manufacture, and how they function.
Pressure tanks are vessels that are used to store, hold, and/or convey gasses, vapors and fluids at pressures greater than atmospheric pressure, also known as high pressures.
Pressure vessels are sealed containers used to store liquids, vapors, and gasses at much higher or lower pressures than the surrounding atmosphere. They are widely utilized in a variety of industries, including petrochemical, gas and oil, chemical, and food processing. Pressure vessels include items such as reactors, flash drums, separators, tanks, and heat exchangers.
Each pressure vessel should be used within its specified temperature and pressure limits, which are the safety limits of the pressure vessel. Pressure vessel design, construction, and testing are meticulously carried out by qualified individuals and are governed by rules since the accidental release and leaking of its contents pose a risk to the surrounding environment. The American Petroleum Industry (API) 510 Pressure Vessel Inspection Code and the American Society of Mechanical Engineers Boiler and Pressure Vessel Code Section 8 are popular standards.
The main difference between pressure tanks and pressure vessels is maximum allowable operating pressure (MAOP). As the name suggests, "pressure vessels" refers to an equipment that is designed to handle pressure over an atmospheric pressure (above 15 PSI). The MAOP of pressure vessels can be up to 3000 PSI and even higher under special cases. Pressure tanks are meant to be for static storage of fluids and have an MAOP of 15 PSI or below atmospheric pressure.
Appropriate design and boiler safety standards compliance for pressure vessels is ASME Sec VIII Div. either 1 or 2 or 3. Comparable International safety standard compliance in European countries is BS5500 and other nationally known codes. Accordingly, pressure tanks generally appropriate for service and corresponding maximum pressures complying to respective industry codes are as below:
Lastly, pressure vessels are closed equipment, while pressure tanks may be either open or closed top type (especially for vertical cylindrical construction). For instance, a fuel tank is open to the atmosphere via a breather. This usually has pressure equal to the atmosphere. Also tanks are much larger than vessels and maintenance of the latter is more hazardous as chances of explosion are higher.
The manufacturing of pressure tanks involves:
Steel and stainless steel are the ideal materials for pressure tanks. Steel is an excellent choice since it is long-lasting, strong, and capable of retaining its structure even when subjected to heavy impact and/or harsh temperatures. Stainless steel possesses all of the aforementioned characteristics, as well as being easy to clean and corrosion resistant, making it an excellent material for pressure tanks used in hygienic processes such as beverage and food processing, medical or laboratory applications.
Aluminum, carbon fibers, titanium, zirconium, and other high strength polymers are some of the other materials that manufacturers can use to make pressure tanks. Furthermore, if the requirements of the intended application necessitate it, pressure tanks can be coated with polymers, rubber, metal, or ceramic substance that helps maintain the tank's structure and prevents leaks.
The criteria for choosing material involves:
The parameters used in pressure vessel design calculations are as follows. Such characteristics are crucial in determining the shell and head wall thickness.
Design Pressure: This is a parameter used to compute the vessel specifications. It is generated from the peak operating pressure, which is the pressure surges expected during upset conditions like start-ups, emergency shutdowns, and process irregularities. It is always above the maximum operating pressure of the system. A vessel's pressure release mechanism is also dependent on this characteristic to reduce the risk of explosions. The design pressure is recommended to be 5-10% higher than the peak operating pressure. Design pressure must be specified to withstand one complete vacuum (-14.7 psi) for vessels that may be subjected to vacuum pressure.
Maximum Permitted Working Pressure (MAWP): The MAWP is the maximum allowable pressure determined at the top of the equipment at which the vessel must function at its design temperature. It is the maximum pressure that the vessel's weakest point can withstand at its design temperature. The American Society of Mechanical Engineers (ASME) defines the MAWP value, which companies utilize to ensure that the vessel does not run over this value in order to implement safety standards and prevent explosions. MAWP is distinct from design pressure. MAWP is a broad property based on the physical constraints of the material. Corrosion and wear reduce the material's MAWP. The design pressure, however, is determined by the process's operating conditions and may be less than or equal to the MAWP.
Design Temperature: The maximum allowed stress is temperature dependent, as strength declines with temperature rise and becomes brittle at extremely low temperatures. When determining the maximum allowed pressure, the pressure vessel must not be operated at a higher temperature. The design temperature is always higher than the maximum operating temperature and lower than the minimum.
When determining the design temperature, there are a few general guidelines to follow. The design temperature is recommended to be 500 degrees Fahrenheit above the peak operating temperature and -250 degrees Fahrenheit below the minimum operating temperature. The maximum allowance is recommended to be 250°C for vessels operating between -30 and 3450°C. The designer must consider disturbances that have a significant impact on the temperature of the pressure tank.
Maximum Tolerated Stress: The maximum acceptable stress is calculated by multiplying a safety factor by the maximum allowable stress. The safety factor compensates for potential deviations from the ideal pressure vessel construction and operation.
Joint Effectiveness: Welded joints are classified into four types in the ASME Boiler and Pressure Vessel (BPV) Code. The ratio of junction efficiency is that of the unwelded plate's virgin strength to the welded plate's strength. The strength is generally reduced at the welded joint. Welded joints are presumed to be weaker without more inspection and radiographic testing because flaws like porosity may be present. ASME BPV Code Sec allows for joint efficiency.
Corrosion Allowance: There are numerous rules of thumb for estimating corrosion allowances, which may or may not be arbitrary to the manufacturer. In general, corrosion allowance should be between 1.5 and 5 mm. The corrosion allowance is recommended to be 0.25 – 0.38 mm per year or 3 mm over a ten-year period. Meanwhile, the corrosion allowance for corrosive conditions can be 8.9 mm, 3.8 mm for non-corrosive streams, then 1.5 mm for air receivers and stream drums. Because wall thickness impacts heat transfer rate, corrosion allowance in heat exchanger equipment must be modest.
The metal sheet is forged, rolled, and welded to form the vessel's shell and heads. The metal sheet thickness is the wall thickness, which is determined by careful calculation taking into account the aforementioned criteria. Auxiliary equipment, devices, and accessories are installed in order for the pressure vessel to function properly:
Post-weld heat treatment is used to reduce stress from joining and forming.
All pressurized containment vessels can be built to the specifications of the American Society of Mechanical Engineers, abbreviated ASME. ASME tanks, as they are commonly referred to, are built to meet the ASME quality requirements for design, construction, fabrication, use, and maintenance. These pressure tanks must also be inspected regularly in order to maintain their ASME certification. Because ASME standards are so widely used, many manufacturers automatically design tanks that fulfill them. While ASME certification is rarely necessary, most customers want to know that their products are of high quality and safe, and ASME certification provides that confidence.
Other local and international standards, such as those defined by UL, ASTM International, TUV, the USDA, ISO, Canada, the European Union, and others, can also be met by pressure tanks. The majority of manufacturers also make non-code vessels. An experienced pressure tank manufacturer nearby may be contacted for the most up-to-date and relevant information about the possibilities and needs of a customer’s application.
Pressure vessels are designed to function by achieving the amount of pressure required to perform an application function, such as holding air in a scuba tank. They can either provide pressure directly through valves and release gauges or indirectly through heat transfer. Possible pressure levels range from 15 psi to 150,000 psi, with temperatures frequently exceeding 400°C (750°F). A pressure tank can store anything from 75 liters (20 gallons) to thousands of liters.
Considerations when choosing pressure tanks include:
The material utilized in building a pressure tank is one of the most significant factors involved in its manufacturing. Prices can vary based on the type of material utilized. Carbon and low alloy steels, nickel alloys - Monel, Inconel & Hastelloy300, series & high temp SS, 2205 & 2507 duplex stainless steel, and aluminum are among the materials utilized in the fabrication process. Process conditions drive material selection. Depending on the tank’s intended function, it is necessary to pick the best material for the job.
The design is the most important factor in producing a new pressure tank. The tank must be designed in such a way that it can withstand harsh industrial demands. Weld construction is a critical part of the design, and any flaws in it can result in catastrophic failure. BEPeterson designs all vessels to ASME specifications using the most recent version of the program Compress. Fabrication experience must be used to optimize designs so that all cost concerns are fully used.
While buying a pressure tank, care must be taken that it follows any of the subsequent industry standards and specifications:
Manufacturers execute a variety of tests to verify the load bearing capacity and performance of the tank under harsh situations. Ferrite Testing, Hydro-testing, PMI (Positive Material Identification), He Leak Testing, Dimensional – Fero Arm, Radiography, and NDE – PT, UT, MT are among the tests performed. This factor will provide information about the tank’s capabilities.
This chapter will discuss the classes and types of pressure tanks.
It is a tank that keeps the pressure in a well water system constant. A pump, either a submersible or a jet well pump, pumps water from the ground into the residence in a home water well system. A well pressure tank also serves as a reservoir, storing water for the home and signaling the pump when the water level drops and needs to be refilled. There are three types of pressure tanks in this class discussed below.
Also known as galvanized tanks or stainless steel pressure tanks, the water and air charge are held in a single tank. To avoid corrosion, they usually have an interior coating. The material used to coat the tank and avoid corrosion is referred to as "glass lined" or "epoxy coated."
There is no separation of air and water in a single tank. This type of tank is still in use despite not being as possible. To achieve the pressure required to serve your home, compressed air presses down on the water. While they are often larger than other varieties of tanks, their capacity is comparable to that of smaller tanks. As a result, the pump may cycle on and off more frequently, resulting in premature pump wear and failure. They can be susceptible to getting water-logged because of the air loss through pin-holes becoming corroded.
They are divided into two compartments: one for air and one for water. They're divided by a rubber diaphragm that's permanently connected to the tank's inside and raises and lowers with the water level.
As water is forced into the bottom part, the diaphragm pushes up into the air chamber, triggering a switch that turns the pump off.
While this is an efficient process, it is not without flaws. One possibility is for the diaphragm to come away from the inside of the tank, allowing water to flow into the top chamber. In the event this happens, the tank ought to be replaced. Another issue is when the diaphragm folds over itself, resulting in a false reading, leading to early pump burn-out and tank failure.
The air and water are separated into two chambers. The bladder is a big balloon filled with air that contracts and expands, causing the pump to activate. They don't have the problems of a single chamber or a diaphragm tank because they're self-contained. Another benefit is that because the air and water are kept separate, the air is not absorbed into the water and thus no additional air is required. Air bladders also have a longer lifespan than diaphragms.
A steam drum is an essential component of a water-tube boiler. At the top of the water tubes, there is a reservoir of water/steam. The drum collects the steam produced by the water tubes and serves as a phase separator for the water/steam mixture. Build up of hotter water is aided by the density differential between cold and hot water. Steam is thus saturated inside the steam drum.
The separated steam is extracted from the drum's top section and dispersed for use in the process. Continued heating of the saturated steam produces superheated steam, which is generally used to power a steam turbine. Saturated steam is extracted from the drum's top and re-enters the furnace via a superheater. The water and steam mixture enters the steam drum via riser tubes, and the demister separates the water droplets from the steam, generating dry steam. It comes with a safety valve, a water-level indicator, and a level controller. The boiler's feed-water is likewise sent to the steam drum via a pipe. The boiler's feed water is also delivered to the steam drum via a feed pipe that runs the stretch of the steam drum inside the drum.
A steam drum is used alone or in conjunction with a mud-drum or feed water drum positioned on a lower level. A boiler with both a steam drum and a mud or water drum are referred to as a bi-drum boiler, while a boiler with just a steam drum is referred to as a mono-drum boiler. The bi-drum boiler structure is typically meant for low pressure-rating boilers, whereas the mono-drum boiler construction is typically intended for higher pressure-rating boilers.
Steam drums have types which are as follows:
Three and Four Drum Boilers - These are the veterans of modern boilers, however they are still utilized in several industries.
Bi Drum Boilers - are utilized for both power and steam generating. They are no longer used for power generation and have been superseded by single drum boilers because bi drum boilers are non-reheat machines. As a result of the plant's high heat rate, a once through boiler or a single drum boiler is more viable. Bi drum boilers are extensively used in process steam generation because they can adjust to high load variation and respond to load variations.
Single Drum Boilers - are mostly used in power plants to generate electricity. Because the stress concentration is lowered to a larger extent in single drum boilers, the pressure limit is higher than in bi drum boilers. There is only one drum, to which the downcomers are welded. Single drum boilers are appropriate both for the reheat and non-reheat boilers. They can be configured as corner tube boilers, in which the downcomers act as the frame, or as top supported boilers, in which the entire boiler assembly requires an external frame and is supported by the top drum.
Ammonia storage is essential in a variety of industries. Because of the physical features of ammonia, high pressure storage tanks or low temperature refrigerated vessels are frequently required. Large quantities of chemicals, such as ammonia, pose a number of issues, including safety, health, and environmental considerations.
Low-pressure storage of ammonia has gained popularity for two reasons. For starters, it necessitates far less capital per unit of volume. Secondly, it is safer than sphere storage, which employs higher-than-atmospheric pressures. With the widespread industrial production of ammonia, now it has become usual practice to store ammonia at atmospheric pressure and -33°C.
For storage of larger amounts up to 50 000 tonnes of ammonia, on site storage tanks are used and they operate at -33 °C.
A hot water tank (also known as a hot water storage tank, hot water thermal storage, unit thermal storage tank, hot water cylinder, and heat storage tank) is a type of water tank that is used to store hot water for space heating or domestic consumption.
Because of its large specific heat capacity, water is an excellent heat storage medium. This means that it can mass more heat per unit weight than other substances. Water is inexpensive and non-toxic. A well-insulated tank can keep stored heat for days, lowering fuel expenses. Hot water tanks may have a gas or oil burner system as well as electric immersion heaters. Some employ an external heat exchanger, such as a central heating system or warm water from another energy source. In the household environment, the most common are an electric immersion element, fossil-fuel burner, or a district heating scheme.
Water heaters for washing laundry or bathing feature thermostat controls to set the temperature, which ranges from 40 to 60°C (104 to 140 degrees Fahrenheit), and are connected to the home cold water supply.
When the water in the tank contains a high concentration of dissolved minerals, such as limestone, boiling the water causes minerals to precipitate (scaling). After only a few years, a tank may suffer leaks due to corrosion, a problem aggravated by dissolved oxygen in the water, which promotes corrosion of both the tank and the fittings.
A process tank is a vessel or other container used for mixing or batching chemicals, wastewater, feeds, or other components, or for preparing one or more components to produce a desired result. The phrase encompasses all associated pipework and other fixtures required for the vessel's intended operation.
This chapter will discuss the applications and benefits of pressure tanks.
Pressure tanks can retain and carry substances used in a wide range of sectors, including food and beverage, chemical, recreation, plastic and polymer resins, rubber, military and defense, water and filtration of chemical, wastewater and treatment of water, pharmaceuticals, oil, fuel, and energy.
Furthermore, they are frequently associated with well systems, from which residential residences and structures obtain their water supply. Other pressure tank applications include nuclear reactor vessel operation, autoclaves, recompression chambers, and road vehicle air brake reservoirs, powering of air tools, and the functionality of diving cylinders and other cylinders of gas utilized in medical, chemical, and industrial processes. The most common pressure tank applications are discussed below.
A pressure vessel is frequently used as a receiver in the oil and gas industry where physical and chemical processes occur at high temperatures and pressures. Although the columns serve various functions, their construction is comparable. Distillation columns are used to separate feed streams or streams into numerous sources based on the boiling temperatures of the feed parts. Because of their comparable production processes, pressure vessels and columns are typically obtained from the same manufacturers.
Stainless steel and carbon steel are the two most often utilized building materials in the oil and gas industry. Other components, in addition to the external body, are required for a pressure vessel to be usable, like vessel internals and distillation trays. Such components are extremely complicated, necessitating standards that differ greatly from those required for the manufacturing of pressure vessels, which are provided by specialized vendors.
It is a pressure tank in which an activity (chemical reaction) takes place, resulting in a fundamental change in the container's content. These can be operations like combining one or more items to make a new product, separating one product into one or more other products, or eliminating directions from an existing product to make something else. Various types of pressure vessels can be simultaneously employed in the chemical industry.
There are a variety of reasons why the energy business requires pressure tanks in general. One of the primary reasons for its use in the energy sector is to limit hazardous gasses. Excess gas is frequently stored in areas such as oil refineries and metal works. Furthermore, nuclear power facilities employ special pressure vessels known as Reactor Pressure Vessels (RPVs). RPVs are enormous cylindrical steel containers housing a core, generated steam, and cooling water, which require excellent dependability to survive high temperatures and pressures, as well as neutron irradiation, making the RPV the most crucial pressure barrier in a nuclear power plant. It is to be noted, however, that not all power reactors have a reactor pressure tank.
Pressure tanks are used in industrial settings such as nuclear reactors and mining. Aside from that, they are utilized in everyday tasks such as heating water and distillation. They are completely safe for storing liquid gasses. They are helpful for storing and transporting volatile chemicals, including propane, ammonia, and LPG.
The benefits of utilizing pressure tanks in water distribution systems include, above all, extending pump life and lowering the effect of hydraulic shocks on the unit when the pump is activated. Pumped water enters the vessel, compressing the air present.
Elastic Deformation - Elastic buckling or elastic instability, vessel shape and stiffness, as well as material parameters, provide buckling resistance.
Brittle Fracture - This type of fracture can happen at low or moderate temperatures. Brittle fracture has occurred in vessels composed of low carbon steel during hydrotest in the 40° – 50°F range where tiny faults exist.
Excessive Plastic Deformation - The ASME main and secondary stress limitations are intended to avoid enhanced plastic deformation and gradual collapse.
Stress Rupture - Progressive fracture caused by creep deformation caused by fatigue or cyclic loading. Creep is a time-based phenomenon, while fatigue is a cycle-based phenomenon.
Plastic Instability – The term "incremental collapse" refers to the accumulation of cyclic strain or cumulative cyclic deformation. Cumulative damage causes vessel instability due to plastic deformation.
Stress Corrosion - Chlorides are widely known to cause stress corrosion cracks in stainless steels; similarly, caustic service could cause stress corrosion cracks in carbon steel. The selection of materials is crucial in these services.
High Strain – low cyclic fatigue is strain-governed and is most common in low strength and high ductility materials.
However, the benefits of pressure tanks far outweigh the pressure tanks drawbacks.
Pressure vessel closures are pressure-retaining devices that allow easy access to pipelines, pressure vessels, pig traps, filters, and filtration systems. Pressure vessel closures often enable maintenance staff access. An elliptical access hole form is typically utilized, allowing the closure to be inserted through the opening and twisted into the working position, and is kept in place by an outer bar secured by a central bolt. Internal pressure prevents it from being opened accidentally while under load.
Pressure tanks are vessels that are used to store or convey gasses, vapors, and fluids at pressures greater than atmospheric pressure, also known as high pressures. They come from pressure vessels which are sealed containers that store the same contents. Steel and stainless steel are the ideal materials for pressure tanks. Material selection, design industry standard, and pressure tests conducted are to be considered when choosing a pressure tank. Several various types of tanks may be considered as pressure tanks. These examples are hot water tanks, ammonia tanks, steam drums, process tanks, and refractory lined vessels.
Pressure vessels are enclosed containers used to hold liquids, vapors, and gases at a pressure significantly higher or lower than the ambient pressure. They are widely used in various industries such as...
Stainless steel tanks are widely used in food, beverage, dairy, medicine, cosmetics, and other manufacturing processes where cleanliness and purity are important. These are also used in industrial plants for storing chemicals and gases where strong resistance from chemical degradation is required...