Agitators
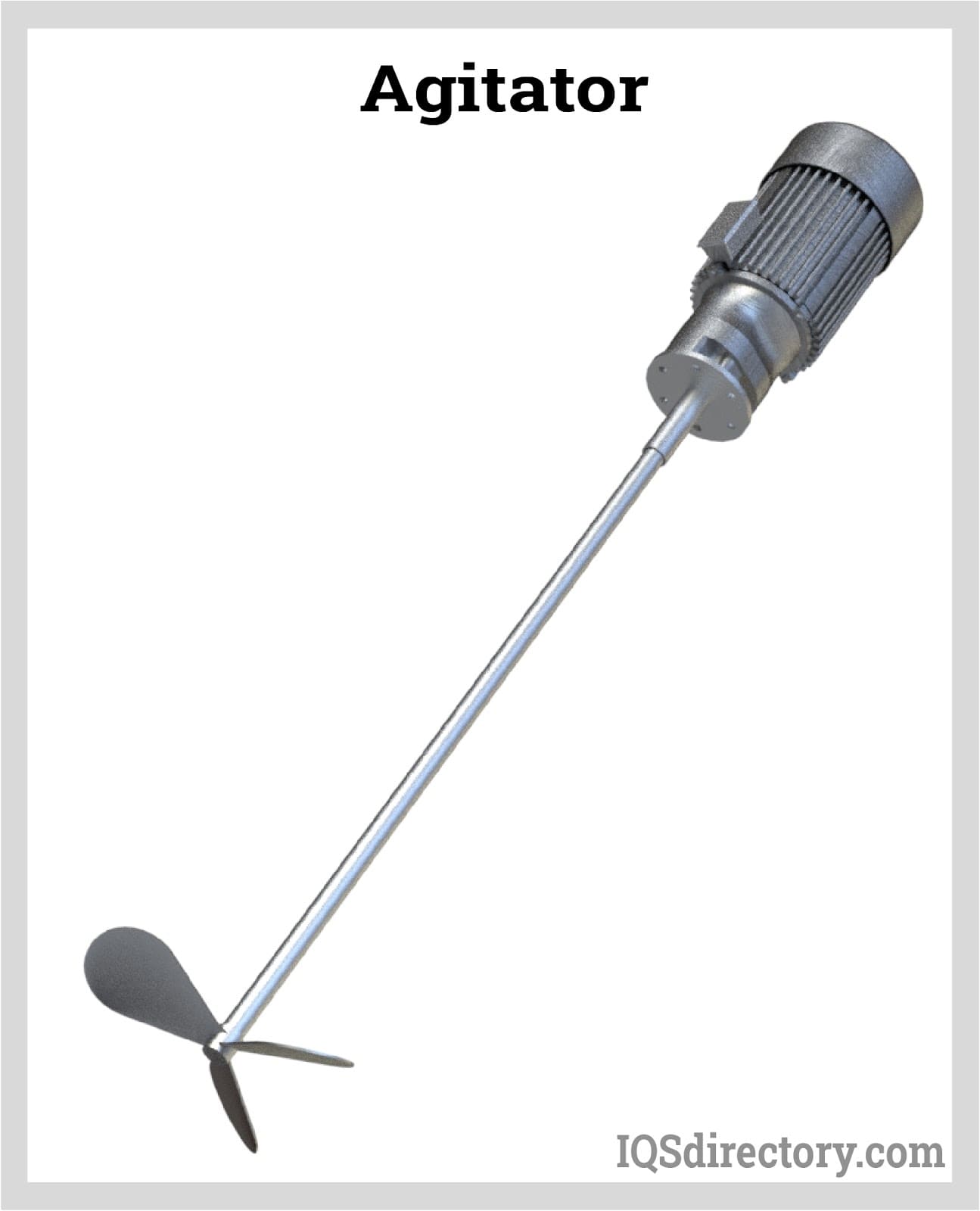
Agitators are equipment used in homogenizing media inside a tank. It works by rotating the impeller at its immersed end at a controlled speed or revolutions per minute (rpm). The work exerted by...
Please fill out the following form to submit a Request for Quote to any of the following companies listed on
This article takes an in-depth look at homogenizers.
Read further to learn more about topics such as:
A homogenizer is a mixer used to create a uniform and even mixture by forcing material through a narrow, confined space. Multiple forces such as turbulence and cavitation, in addition to high pressure, are used to distribute the contents of a solution evenly. Homogenizers have a positive displacement pump and homogenizing valve assembly. The pump forces the material to be processed under pressure through a small gap between the valve seat and the valve. The force of the pressure and the movement through the valve causes turbulence and mixing. Multiple industries rely on homogenizers to produce stable, uniform, and consistent products. Aside from mixing, homogenizers are used for emulsifying, suspending, grinding, dispersing, and dissolving. The pharmaceutical, beverage, and chemical industries rely on homogenizers for the production and quality of their products.
Homogenizers are used with high shear mixers, batch mixers, and paddle mixers and are installed downstream to create finer mixtures. However, some homogenizers cannot accept products with highly coarse components due to the risk of high energy consumption, decreased flow rate, heat generation, and increased material wear. Upstream of the homogenizer, mixers condition and prepare materials by premixing them.
The development of homogenizers started in the early 1900s when Auguste Gaulin invented a piece of equipment for homogenizing milk. The equipment was composed of a three-piston, positive displacement pump with capillary tubes fitted at the discharge. The capillary tubes acted as a throttling device that converted fluid pressure into velocity. Downstream of the capillary tubes was a concave valve where the jet of milk droplets impinged.
Subsequent developments in the engineering of homogenizers lead to replacing the capillary tubes with a single small tube. The most important aspect was the small gap featured by the tube where the homogenization process happened. As a result, different gap geometries have been developed and further improved the equipment's applications.
Several theories have developed over the years regarding the process of homogenization using high pressure. The two most prominent surviving theories are the globule disruption by turbulence and cavitation theories. These two remaining theories offer good examples of the influence of various forces on the homogenization process.
The theory of globule disruption by turbulence or micro whirls is built on the idea that a liquid jet forms at the outlet of a gap, with small eddies forming as the jet breaks up. As pressure increases, the velocity of the jets increases, producing smaller eddies with more energy. When a droplet in an eddy hits a droplet of its same size, it deforms and breaks up. The idea of this theory is that homogenization varies with the amount of homogenizing pressure.
With cavitation theory, pressure changes during homogenization cause bubbles (cavities) in a liquid. As the bubbles grow, they implode or cavitate and release energy. The collapsing and imploding bubbles generate kinetic energy that surrounds particles in a liquid, creating high-speed jets that break up the particles. Bubbles collapsing on the surface of particles send energy directly to the particles and break them apart. The process of collapsing and imploding bubbles creates turbulence in a liquid that results in cavitation.
Homogenizers are used to mix emulsions and suspensions. An emulsion is a mixture of two or more liquids that are normally immiscible due to their liquid-to-liquid phase separation. This liquid to liquid phase separation is brought by several physical mechanisms, such as surface tension, polarity or repulsion, and viscosity. Homogenized emulsions are sometimes called colloids, a term used to cover a broader mixture classification.
A suspension is a mixture composed of solid particles that settle down and cannot be dissolved completely in the mixture. The separation of the solid particles is brought about by their large size, which is around hundreds to thousands of times larger than that of the dispersed particles in a homogenous solution. Suspensions are non-homogeneous mixtures that disperse in liquids and are 100 times the size of the particles in a solution.
Particles in suspensions vary in size, with some particles visible to the naked eye. Homogenization supplies the force to combine suspensions with a solution and is one of its main functions.
Knowing the types of heterogeneous mixtures processed by a homogenizer, it is evident how a homogenizer works. A homogenizer works by breaking or subdividing the dispersed components into smaller particles and then distributing them evenly throughout the mixture. The action created by the homogenizer continuously disrupts the formation of large particles due to immiscibility and precipitation.
The homogenization process happens within the homogenizer valve, which is the main component of the equipment. Earlier, it was explained that the first homogenizer valve was an assembly with a capillary tube and a concave valve. The capillary tube throttled the fluid pressure and converted it into kinetic energy. The concave valve served as an impact surface for the fluid jet. Modern designs replaced the capillary tube with a seat that mates with the valve at an appropriate clearance to create a small gap for throttling flow. Within this gap, the fluid experiences the right flow conditions for homogenization through different physical principles.
Homogenizing action is created by the combined effect of three main physical principles:
Shearing in fluids is primarily caused by friction between fluid molecules due to viscosity. In a no-slip condition, adjacent fluid molecules have the same velocity. However, when a disruption such as acceleration caused by a rotor-stator or deflection caused by an impact ring is present, different velocities develop because of the fluid’s internal friction. At the boundary layer, or the layer between the homogenizer surface and the fluid, the velocity of the fluid is zero. Away from the boundary layer, the velocity of the fluid approaches the same magnitude as when the fluid was in no-slip condition. Shearing is experienced by a large particle or droplet when it is caught between fluid layers with different velocities. The shear forces break down large particles and droplets into smaller sizes.
Cavitation happens when a fluid experiences a large pressure drop. Typically, a pump that introduces the fluid at a higher pressure is located upstream of a homogenizer valve. The pressure of the fluid is converted into kinetic energy as it passes through the homogenizer valve. When the pressure drop is large enough, the vapor pressure of the fluid exceeds the absolute pressure inside the homogenizer. This allows the momentary formation of cavities from small pockets of vapor. Shockwaves are released upon the collapse or implosion of these cavities, breaking the particles and droplets in the mixture.
The last physical principle involved in homogenization is turbulence. Turbulence occurs when the fluid attains high velocity. The high velocity creates irregular motions within the fluid. These irregular motions are a form of energy dissipation wherein the kinetic energy of the fluid is converted into internal energy in the form of eddy currents and some amount of heat. The eddies generated help break the particles into finer sizes.
The extent to which each physical effect contributes to the homogenizing process depends on the design of the homogenizer valve and fluid properties such as temperature, pressure, composition, and viscosity. Still, most studies and experiments indicate that the turbulence effect is the primary mechanism for creating homogenization.
The generation of shearing, cavitation, and turbulence effects is not limited to a homogenizer valve. The other types operate differently than the original homogenizer but produce the same effect.
The high-pressure homogenizer (HPH) is the earliest type of industrial homogenizer developed and is frequently described in this article. Its versatility and homogenizing efficiency make it some of the most common homogenizer equipment in industrial and manufacturing setups.
High-pressure homogenizers, referred to as piston homogenizers, consist of a high-pressure pump and a homogenization valve. The high-pressure pump is a positive displacement reciprocating type since these types are inherently suitable for viscous fluids and remain efficient while experiencing variations in flow and pressure. High-pressure homogenizers have three or more pistons or plungers. Selecting a reciprocating pump with more plungers stabilizes the delivery of fluid into the homogenizer valve and reduces equipment vibration.
The pressure delivered by the pump depends on the type of fluid. Most homogenizers used in the food and pharmaceutical industries operate at around 8,000 psi up to 40,000 psi (550 bars up to 2,750 bars).
The homogenization valve, as previously described, is composed of a seat, valve, and impact ring. As the premix fluid passes through the valve, its velocity increases, creating turbulence. The turbulence, in turn, develops eddies that break down the components of the premix. The small gap between the seat and the valve helps create strong shearing forces, which also contribute to the disruption of components. Upon exiting the gap, cavitation occurs. The implosion from the cavitating fluid creates shockwaves that break the components. Cavitation further improves the efficiency of the homogenizing process.
The homogenizer valve is the most important part of a homogenizer assembly. There are different types of homogenizer valves. Each type has its advantages and drawbacks; these make them suitable for a particular application. Below are the types of homogenizer valves.
The radial diffuser valve is also known as the standard valve since it is the most extensively used in various industries. It consists of a plug and a seat. A typical design features a movable seat for adjusting the gap between the two parts.
In this type of homogenizer valve, the premix fluid initially flows axially and is deflected at a 90° angle by the plug. This forces the fluid to flow radially along the small gap. After exiting the gap, the fluid stream hits an annular surface called an impact or wear ring.
The main advantage of a radial diffuser valve is its ability to control the homogenizing pressure by adjusting only the gap size while the flow rate is kept constant.
An axial flow valve resembles an orifice valve. The small gap is created by an orifice, a venturi, or a short tube. Other axial flow valve designs feature a moving needle used to adjust the gap. The gap between the needle and the seat is oriented axially, hence the name. In a way, this is similar to a radial diffuser valve, which uses a plug.
The premix remains flowing axially as it passes through the orifice. Shearing, cavitation, and turbulence also take place within the small gap. Upon exiting the gap, the fluid jet is expanded without an impact chamber, unlike what is seen in a radial diffuser valve.
The design of axial flow valves varies depending on how the homogenizing pressure is controlled. Designs that only use static components control the homogenizing pressure by varying the flow rate. Designs that feature a moving needle control the pressure by adjusting the gap size.
In a counter jet valve, the incoming stream of premix fluid is divided into two or more streams using microchannels. These microchannels serve as the gap for homogenizing the premix fluid. Upon exit, the streams are at a high velocity and are made to impinge on one another. The microchannels direct the streams into a small area called the interaction chamber.
aThe benefit of using a counter jet valve is the operation without moving parts. Thus, they have greater reliability than radial diffuser valves. Moreover, no impact ring tends to wear over time due to the continuous impingement of the fluid.
However, the drawback is its dependence on flow rate to control the homogenizing pressure. On top of that, since it divides the premix stream using multiple channels, it needs a high flow rate to operate properly. This limits the homogenizing pressure attained by the valve.
With a microfluidizer, the product enters through an inlet reservoir and is pulled into a pumping system that pushes it into an interaction chamber at pressures up to 30,000 psi. In the chamber, the product is subjected to high shear rates, energy dissipation, and impact forces as it is pushed through microchannels, where it collides with the walls and its particles. The constant applications of the various forces disrupt cells to create uniform droplet size reduction.
Mechanical homogenizers use mechanical work as the main source of energy for breaking the premix components. They function similarly to a high shear mixer. The premixed fluid or feed can be introduced at atmospheric pressure, low, or medium pressure, much lower than that of a high-pressure homogenizer. Instead of using a valve, rotating parts are used such as cones, blades, and paddles. The rotors are mated with an appropriate stator to create the desirable conditions for homogenization. The homogenization process relies on the mechanical tearing caused by the moving parts. Nevertheless, the previously mentioned physical principles involved in disrupting the particles still apply to mechanical homogenizers.
Below are the most popular types of mechanical homogenizers.
A colloid mill is a homogenizer composed of a conical rotor and stator. The rotor and the stator are separated by a small clearance where the premix will flow due to shear and centrifugal forces. As the premix is gravimetrically fed into the rotor-stator assembly by a hopper, it is thrown outward towards the exit slot or holes. The high rotating speed (around 3,000 to 15,000 rpm) of the rotor causes a tremendous amount of shearing, which breaks the components of the premix fluid. Moreover, since the fluid is accelerated by the rotor, high fluid velocities can be achieved. With enough velocity, turbulence is also developed.
The magnitude of shearing can be adjusted by varying the clearance between the rotor and stator. However, decreasing the clearance will negatively affect the flow rate of the product. This limits the resulting particle size, which is not as fine as particles made by high-pressure and ultrasonic homogenizers.
Colloid mills are used for highly viscous products or products with high amounts of suspended solid particles.
In terms of construction, these homogenizers are the closest to high-shear mixers. Their rotor-stator assembly is sometimes called a mixing head, generator, or probe. The assembly is lowered into a batching tank, vessel, tube, or container where the premix fluid is homogenized.
Rotor-stator homogenizers work by accelerating the fluid tangentially, but because of fluid inertia, it does not completely flow together with the rotor. Instead, the fluid flows towards the shear gap or the region between the rotor tip and the stator. High-velocity differentials and turbulent fluid flow are inside the shear gap, producing high shear rates. The rotor and stator profile, their separation distance, and other features such as holes and slots control the resulting particle size.
Materials enter the rotating fixed rotor system at high speeds in an up-and-down direction to form a spiral shape. The suction created by the rotor and stator forces the sample between them, subjecting it to high shearing forces. Solid samples are incompatible with rotor-stator homogenizers, and multiple samples take time and labor.
Bead mills (sometimes referred to as ball mills) are homogenizers that employ beads for mechanically grinding and breaking large particles dispersed in the premix fluid. The beads are grinding media that reduce particle size by strong impact and shearing forces.
The beads are loaded inside the container and are in contact with the premix fluid. They are then agitated by internal, rotating components such as paddles and blades. Agitation can also be done by centrifugally spinning the container at extremely high speeds. Agitation using rotating components is typically seen in larger homogenizers in line with the production stream. Agitation through a centrifugal action is commonly used in laboratories for preparing homogenized product samples.
These homogenizers use blades as their rotor. Unlike the colloid mills and rotor-stator homogenizers, they do not have a shear gap formed with a stator. The shearing effect is developed only by the high-speed rotation of the blade. Their construction and operation closely resemble that of a blender.
Blade-type homogenizers are less efficient than rotor-stator types. Their homogenizing ability is sufficient for creating a well-emulsified and dispersed mixture, but the resulting particle size is not as fine as those produced by the other types of homogenizers. Abrasive media such as beads are used to increase their homogenizing efficiency.
Ultrasonic homogenizers, also known as sonicators or sonic disruptors, take advantage of a physical principle called ultrasonic cavitation. Ultrasonic frequencies are sound waves vibrating at 20 kHz or higher. Cavitation is induced by creating alternating rarefaction and compression periods at ultrasonic frequencies. Hence, the primary cause of component disruption is the cavitation effect.
The rarefaction period creates the vapor cavity, while the compression period causes it to implode. These periods happen in one cycle of an ultrasonic wave. The voids created are microscopic in scale and cannot be seen during operation, but these are high-energy, localized regions that can reach extremely high temperatures and pressures.
Ultrasonic homogenizers are composed of three parts:
Ultrasonic homogenizers are comparable to high-pressure homogenizers in terms of particle size reduction and energy efficiency. The main advantage of ultrasonic homogenizers is their operation at atmospheric pressure. Moreover, the degree of disruption can be easily varied by manipulating the generator's electrical power and the premix fluid's temperature. All this is accomplished without using any moving parts.
Aside from producing emulsions and suspensions through particle size reduction and mixing, homogenizers also perform other functions, particularly in the food and pharmaceutical industries. Their ability to mechanically disrupt microorganisms and natural compounds extends their viability as processing equipment. However, these roles are limited to high-pressure, ultrasonic, and bead mill homogenizers. These homogenizers can disrupt particles down to the nanoscale, ranging from 50 to 500 nm.
A homogenizer is a type of mixing equipment used to create a uniform and consistent mixture. It works by breaking the components and evenly distributing them throughout the solution.
Homogenizers were invented by Auguste Gaulin for homogenizing milk. The equipment was composed of a three-piston, positive displacement pump with capillary tubes fitted at the discharge.
The homogenization process happens within the homogenizer valve, which is the main component of the equipment.
Homogenizing action is created by the combined effect of three main physical principles: shearing, cavitation, and turbulence.
The three main classifications of homogenizers are high pressure (HPH), mechanical, and ultrasonic.
In addition to emulsification and dispersion, homogenizers perform other functions. Examples are microbial inactivation, cell fractionation, enzyme activation/inactivation, and compound extraction.
Agitators are equipment used in homogenizing media inside a tank. It works by rotating the impeller at its immersed end at a controlled speed or revolutions per minute (rpm). The work exerted by...
Drum mixers are mixers that are used for mixing free flowing materials by rotating them forward and reverse with welded chutes or flights that fluidize the mixture. The design of drum mixers gives them...
An emulsifier is an emulsion device used for colloidal dispersion of liquid droplets of immiscible liquids in the presence of an emulsifying agent. It enables the combining of non-soluble solutions or liquids...
High shear mixers, also known as high shear reactors (HSRs), rotor-stator mixers, and high shear homogenizers, are used to emulsify, homogenize, disperse, grind and/or dissolve immiscible mixtures with components of the same or different phases...
An industrial blender is a machine for large-scale production that consists of a large tank capable of mixing and blending batches of manufacturing materials to create a reaction between the materials. The many uses for industrial blenders are due to their capacity and...
A mill is a mechanical device that is often a structure, appliance, or machine that is used to break down solid materials into smaller pieces by cutting, grinding, or crushing them. Many industrial processes involve...
A tank mixer is a mixing device that blends several different ingredients in a single tank to make a single solution. It is a mixing process capable of mixing wettable powders, liquids, emulsifiable concentrates, and surfactants. They mix and blend...
A mixer is a complex and precise tool that is used in combining and mixing of substances and chemicals for manufacturing, production, and industrial use. There are many types of industrial mixers including...
A plastic tank is a large capacity liquid or granular storage unit that can be vertical, horizontal, below or above ground, as well as movable. They are designed to hold several gallons of a variety of substances for long periods without experiencing wear, weathering, or deterioration...
A plastic water tank is a large capacity container designed to store water for household, agricultural, irrigation, and industrial manufacturing use. There are various types of water tanks produced to meet the needs of specific applications, with...
A poly tank is a plastic storage tank used to store, transport, and collect water, other liquids, and granular or powder materials. They are made of polyethylene or polypropylene and are a cost effective, lightweight, and easy to handle...
Pressure tanks are vessels that are used to store, hold, and/or convey gasses, vapors and fluids at pressures greater than atmospheric pressure, also known as high pressures...
Pressure vessels are enclosed containers used to hold liquids, vapors, and gases at a pressure significantly higher or lower than the ambient pressure. They are widely used in various industries such as...
Stainless steel tanks are widely used in food, beverage, dairy, medicine, cosmetics, and other manufacturing processes where cleanliness and purity are important. These are also used in industrial plants for storing chemicals and gases where strong resistance from chemical degradation is required...