Industrial Shredders
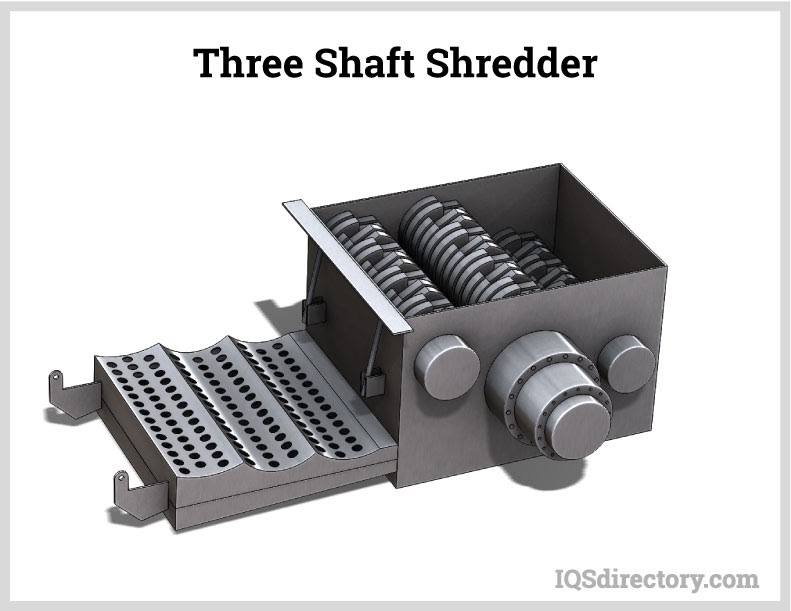
An industrial shredder is a piece of heavy duty equipment designed to shred dense and light materials to prepare them for recycling or for the destruction of unusable products. They are an environmentally sound device that...
Please fill out the following form to submit a Request for Quote to any of the following companies listed on
This article takes an in depth look at cardboard shredders.
You will learn more about topics such as:
A cardboard shredder is a machine designed to turn cardboard boxes and sheets into small shards or strips. Specialty cardboard shredders are configured to convert cardboard into flexible perforated material for packaging. Cardboard shredders can produce cushioning, flat netting, chips, shreds, or strips and should not be confused with paper shredders though they have a similar design.
The cardboard shredding process includes transforming cardboard into tiny chips, long strips, perforated sheets, or small pieces depending on the design of the cardboard shredder and how it is used. They prepare recyclable cardboard for repulping and processing or to create packaging materials for shipping products.
The volume of cardboard produced as packing, shipping, and product display material is a convenient and a vital part of moving products and protecting them from harm. The wide use of cardboard presents a second problem: disposing of used cardboard and avoiding placing it in a landfill.
A major part of the repurposing and remanufacturing of cardboard is related to the use of cardboard shredders that easily and efficiently break down cardboard fibers into various forms. Though there are several companies that sell cardboard shredders, their functions are divided into perforation and shredding.
Aside from the various methods to shred and severe cardboard, there is another group of machines that are designed to repurpose cardboard by perforating it. The cutting cylinder for a cardboard perforator has blades designed to cut and perforate the cardboard without actually cutting it. The result of the perforating process is an elongated, flexible, stretched, and cushioned form of paper that can be used as a packing material.
Though a perforator does not totally destroy cardboard and cut it into little pieces, it is considered to be another method for taking used cardboard and enhancing it for further use.
Though paper shredding produces dust, it isn’t of sufficient amount to be of concern unless it is part of an industrial operation. When shredding cardboard, due to the size of the material, large amounts of dust are created that must be captured and controlled.
Cardboard shredders with dust control have a flanged outlet positioned above the cutting blades with ductwork that connects the shredder to a dust collector. To ensure smooth movement of the dust filled air, a fan inside the dust collector chamber pulls the cardboard dust through a high efficiency particulate air (HEPA) filter, which captures the dust from the air and forces the filtered air back into the environment.
To keep the filter clear and clean, compressed air in the dust chamber sends short pulses of air against the filter in the opposite direction of the flow of dust filled air.
A cross cut cardboard shredder makes the same cuts as a strip cut shredder with the addition of a second cut that cuts across the long ribbons. The results of the cutting method are tiny little pieces that resemble confetti or small particles. The difference between cross cut shredders is determined by the type and size of the cut material, which can vary from a fraction of an inch or a few centimeters up to a few inches or decimeters.
Industrial cross cut shredders can be high volume shredders with conveyors as a feeding mechanism. To enhance the cutting process, some designs have paddle wheel crushers that compress the cardboard before it enters the cutting blades. Cutters are made from high grade alloys capable of withstanding constant use.
Dual shaft cardboard shredders work slowly and quietly. They have two sets of blades that are mounted on shafts that face each other. When activated, the two sets of blades rotate into each other making them capable of shredding thick heavy cardboard of two or three ply. Dual shaft shredders are more powerful and dynamic than common shredders and can cut several types of materials, including cardboard of any thickness or size.
The majority of dual shaft cardboard shredders have a single motor. Some configurations have double motors that increase the speed and efficiency of the shredding process. The dual cutting blades grab the feed material and shred it into small minute pieces.
A major benefit of four shaft cardboard shredders, aside from their ability to shred heavy duty cardboard materials, is their reliability and low maintenance. Four shaft cardboard shredders are workhorses that use four sets of revolving blades to shred large pieces of cardboard.
Four shaft cardboard shredders provide processing speed and great power to produce shreds of extremely small sizes.
The shredding of cardboards includes shredders that are capable of tearing boxes apart into smaller pieces. This form of shredder is a preprocessing method used to prepare cardboard for baling, where the boxes are ripped apart before being baled. There are various ways the boxes are fed into the shredding process, including conveyors and feeders where boxes are dropped in.
The shredding of boxes requires three or more shafts or rotors that pull in the material to tear it apart. The spiral design of the rotors increases the force and capacity of the shredder. Due to the thickness and consistency of the material, a box shredder operates at a slower speed. This aspect creates less dust and noise.
Single rotor cardboard shredders have a small footprint and are designed for shredding cardboard and other light materials. The different types of single rotor cardboard shredders have various methods for feeding cardboard into the rotor cutting tool. To ensure that the cardboard is cut to the correct size, the shredder has a screen underneath the cutting rotor for controlling the size of the cut material.
Strip cut cardboard shredders have a similar function to the common paper shredder. A set of rotary blades cuts the cardboard into strips that are the same length as the cardboard sheets. Strip cutting cardboard shredders destroy the structure of the cardboard, leaving long slender ribbons.
One of the major benefits of strip cut cardboard shredders is the speed at which they cut. They have fewer moving parts and tend to have less need of maintenance.
All shredders operate the same way with a housing, rotor, blades, motor or motors, feed system, and power supply. The strength, design, and configuration of the different shredders vary according to the type of material they are made to shred, with paper shredders having less strength and endurance than shredders for larger materials.
The variations in cardboard shredders are between those designed exclusively for cardboard and those capable of shredding more robust materials, including cardboard. Shredders designed exclusively for cardboard are a more resilient and stronger version of paper shredders with blades capable of cutting cardboard of an inch or more thick.
There are several different designs of feeders for cardboard shredders from very simple ones where workers throw cardboard sheets and boxes into a hopper from which they are pulled into the cutting blades. Other methods include conveyors that feed cardboard at a steady rate.
The rotor contains the cutting blades that mesh together to shred the cardboard and are the main part of the shredding mechanism. The number of rotors varies from a single shaft design to ones that have several rotors working in unison. As the number of rotors increases, the efficiency of the shredder improves as well as its capability to handle heavier and thicker cardboard.
Every manufacturer has different designs and cutting styles for their machines. The individual styles have been engineered to shred cardboard in different sizes, from strips and chunks to small confetti like pieces.
Placing cardboard that is too large for the number of shafts can cause the shredder to constantly jam and strain the motor. In the selection process during purchasing, the size, number, and capacity of the rotors have to be chosen to match the type of cardboard that will be shredded.
The motor of a cardboard shredder powers the rotors as they shred the cardboard material. Several factors determine the horsepower and speed of the motor, including the size of the rotors, the type of material, the speed of the motor, and the amount of cardboard to be shredded.
The size of motors varies to match the many shredder designs, with ones of 200 volts up to ones with several horsepower. Motors are precision engineered to specifically match the requirements of the application.
The most common form of power system for cardboard shredders is electrical since it is readily available and takes up less space. The differences in the amount of power are related to the type and size of the cardboard shredder and how it is used. Cardboard shredders that are constantly used and run all day use more power. The majority of cardboard shredders are engineered to use as little power as possible and are very economical.
Cardboard is a widely used material for packing, shipping, storing, and displaying products and items for sale. It has become a staple of modern society and a necessity. At some point, for all cardboard, there is a time when it reaches the end of its usefulness. For many years, when that time arrived, it was thrown into the back of a garbage truck and dumped in a landfill.
With the rising concern for the environment and continuing search for repurposing of used materials, several methods have been developed for disposing of cardboard. In some cases, it is packed into bales and sent to be repulped and made into new boxes. In other cases, it is perforated and slit to form packing material.
The shredding process has been developed to dispose of paper and to destroy sensitive documents. Cardboard shredders work much like paper shredders but are heavier duty as well as larger and more powerful. Shredding of cardboard serves several purposes aside from saving the environment.
A cardboard shredder makes it possible to take in large volumes of cardboard and shred it for reshipping of products. Instead of having bundles of cardboard sitting around waiting to be picked up, it can be shredded for outgoing packages. Less waste is produced, and removal fees are eliminated.
The main focus of all businesses is supporting the green initiative and environmental concerns. Manufacturers and producers are constantly searching for methods to show their belief in sustainability and eco-friendly processes. By shredding cardboard, businesses can let their customers know that they have a plan for properly disposing of materials and avoiding placing the materials in a landfill.
The generation of volumes of cardboard has become a part of manufacturing and production operations. Whether cardboard is fully assembled or broken down, it still requires storage space. Cardboard shredders drastically reduce the space that cardboard can occupy and its footprint. Piles of crushed cardboard boxes that require several square feet of space can be shredded into bits such that they require less space.
A serious problem in a work area is debris and clutter that can slow down operations and block process movement. Piles of cardboard can be a blockage for workers and a fire hazard. By quickly removing it in a solid state cardboard shredder, the dangers of tripping over it or having it catch fire are removed.
There are several waste processing companies that purchase cardboard for resale to cardboard manufacturers. They purchase, pick up, and remove shredded cardboard for it to be reused for repulping and box manufacturing.
A key purpose for recycling cardboard is to preserve the forest since less paper will be necessary for cardboard production, which reduces the number of trees that will be needed. The production of paper products requires 15 billion trees to be cut down each year. Repurposing, reusing, and recycling cardboard by shredding reduces that number.
The wood used to produce the paper for cardboard comes from birch and pine tree pulp. These are fast growing trees with a high amount of recyclable content. They are easily managed and harvested as well as support the sustainable initiatives of the cardboard business.
For many years, air pollution and its effects on the earth have been a major concern. Air filtering equipment has been designed to meet the requirements and demands of the Environmental Protection Agency (EPA). A part of air pollution is the disposal of cardboard by incineration. Cardboard is manufactured using coatings and adhesives that are environmentally friendly but not designed to be burned.
Cardboard shredders reduce the amount of cardboard that has to be burned in a landfill. By reducing the size of cardboard into small chips and strips, it can be easily disposed of or reused such that it does not need to be burned.
Papermaking requires a great deal of water for the pulping process. The use of shredded cardboard to make new cardboard products assists in saving water. In the repulping process, 80% less water is required, which is a savings of 7000 gallons or 25,000 liters of water for every ton of recycled cardboard.
Of the recyclable products, cardboard has the highest percentage, which lowers the required energy to produce it. Recycled cardboard requires 75% of the energy necessary to make recycled cardboard using 50% less electricity.
There are significant resource savings from recycling and repurposing shredded cardboard. By recycling one ton of corrugated containers, it is estimated that one barrel of oil, six million Btus of energy, 3902 kWh of energy, and five cubic feet of the landfill are saved. The recycling of cardboard can supply an estimated 70% of the necessary resources for the cardboard manufacturing industry.
Shredded cardboard is easier to store, ship, and recycle. The shredding process breaks down the solid cardboard into small fragments that can be packaged and moved easily. The overall weight of the pieces is less than the solid board, which makes storage much easier. The lighter weight of the shredded cardboard reduces the amount of fuel necessary to ship it.
A cardboard shredder makes it easy to dispose of large cartons and thick packing material that take up space and storage room. The process of choosing the correct cardboard shredder has to be carefully considered to ensure that the right one is selected to fit the needs of the materials, workers, and the size of the operation.
There are various factors to consider when deciding to purchase a cardboard shredder. Of most importance in the selection process is to choose a cardboard shredder that fits the needs of an organization and is flexible enough to adapt as the organization grows.
The capacity of a cardboard shredder refers to the number of sheets of cardboard it can shred at once and how thick the sheets can be. Industrial cardboard shredders can shred several thicknesses all at once, with some being able to shred boxes.
This is a critical factor, especially for multi shift operations where equipment is expected to operate several hours of the day. The run time is influenced by the amount of cardboard that needs to be processed. In shipping operations, the disposal of cardboard is a constant problem that has to be handled immediately for efficiency and to make room.
In manufacturing operations, shipping and receiving need to have a method for disposing of cardboard but not as rigorous as other material handling companies.
Cardboard shredders have a motor attached to the rotors that rotate the blades to cut the cardboard. The run time of a shredder is determined by how long it can operate before the motor overheats and how long it takes for the motor to cool down.
In the purchasing decision, there may be a temptation to buy a cardboard shredder that costs less to save. This may be an error in that a smaller device may cost less but not have the power and endurance to meet the working conditions. The size of the shredder has to meet the amount of work it is required to do. Though more powerful shredders may cost more, in the long run, their endurance, capacity, and efficiency increase their time of usefulness.
It is essential to select a cardboard shredder that is jam proof. Jamming can cause continual shut downs and work stoppages, which slows operations. The majority of cardboard shredders have jam proof mechanisms that enhance their efficiency.
The majority of industrial cardboard shredders have detectors that indicate an overload. It is a safety feature to let users know that they are passing too much cardboard through the machine or if the cardboard is too thick. It works in coordination with the jam prevention mechanism. Both features help in extending the life of the shredder.
An industrial shredder is a piece of heavy duty equipment designed to shred dense and light materials to prepare them for recycling or for the destruction of unusable products. They are an environmentally sound device that...
Scrap metal must be processed to be effectively recycled and ready for reuse. Metal shredders are machines used to process a variety of metal scraps. Metal shredders are frequently used to reduce metal debris to...
A shredding machine is equipment utilized for shredding. Shredding machines are used to reduce the size of materials. While most online sources define the shredding machine as...
Tire shredders are a type of recycling equipment used to reduce the volume of tires to scrap using high torque shredding systems. The various types of tire shredders are capable of handling large loads of...
A baler is a piece of equipment used to compress solid industrial waste or recyclable materials (e.g., paper, plastic, foam, cans, etc.) to achieve better material handling and storage. Eliminating empty space between individual items of these bulk products is a great way to save costs attributed to storage and transport...
A bowl feeder is a mechanism for supplying small parts and components to a production line or for sorting bulk items for rapid use. A self contained bowl feeder system has a bowl that sets on a spring loaded base that moves vertically...
A cardboard baler is a mechanism that uses a metal plate driven by a hydraulic ram to apply tremendous pressure and force to crush, compact, and compress pieces of cardboard into tightly formed and easy to transport cubes and...
A Trash compactor is a machine or device designed to compress, reduce, and compact a variety of materials through hydraulic, mechanical, or pneumatic force. The initial steps in the compacting process are the collection of the material to be compacted...
Vibratory conveyors are material-handling equipment used to transport fine to coarse-grained bulk materials. These vibratory conveyors are strong conveying equipment utilized for bulk commodities with fine to coarse graininess...
Vibratory feeders are short conveyors used to transport bulk materials utilizing a controlled vibratory force system and gravity. The vibrations impart a combination of horizontal and vertical acceleration through tossing, hopping, or sliding-type of action to the materials being handled...
A vibratory screening is a process that separates bulk solid materials from solids and slurries using inertial vibration that causes various sizes of particles to pass through openings in a screen or...
Modern balers are descendants of hay presses, invented in the mid-nineteenth century, that made it easier to gather and stack hay. The earliest hay presses were stationary units built into a barn and extending two to three stories into the hayloft...