Cardboard Balers
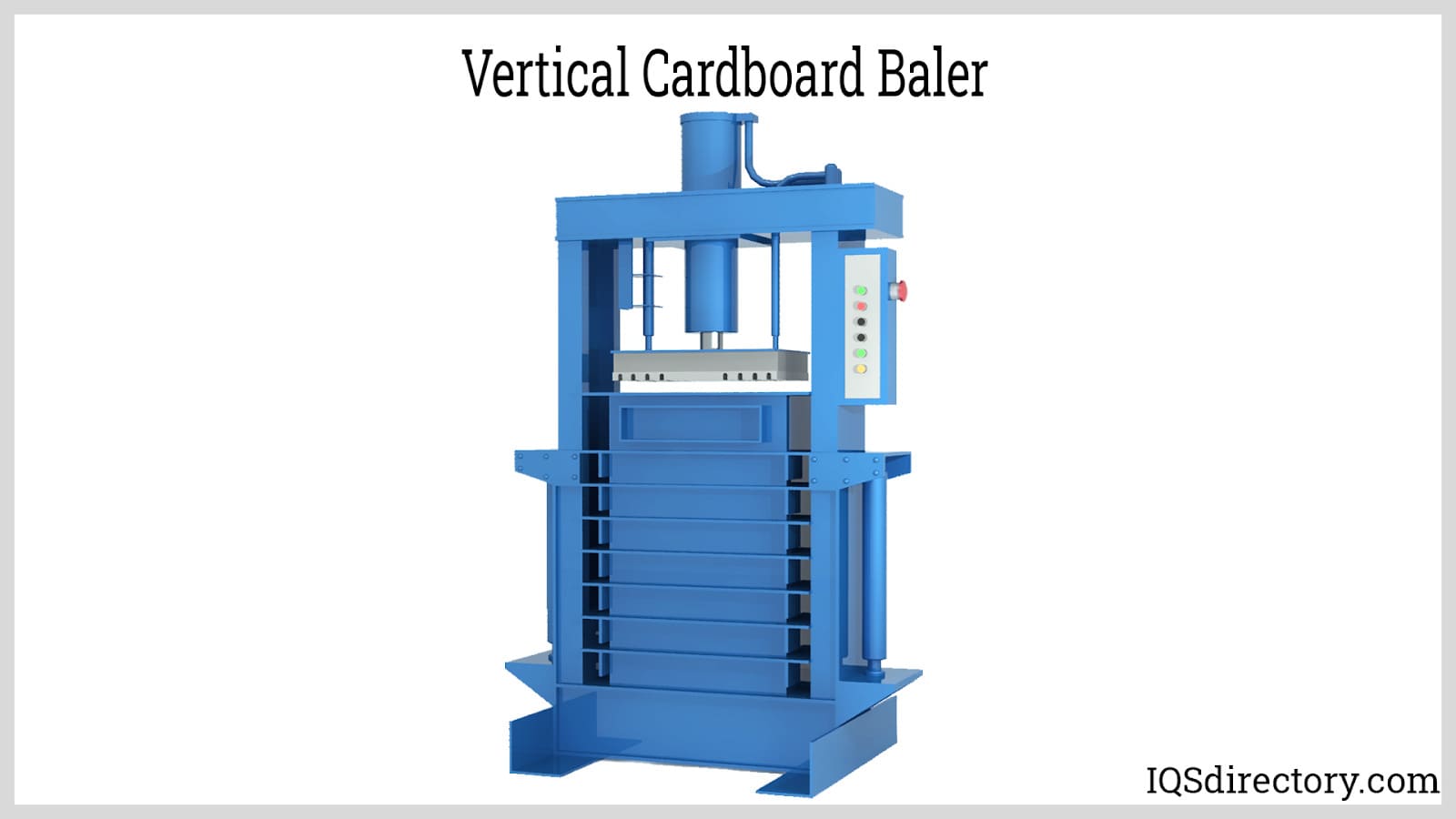
A cardboard baler is a mechanism that uses a metal plate driven by a hydraulic ram to apply tremendous pressure and force to crush, compact, and compress pieces of cardboard into tightly formed and easy to transport cubes and...
Please fill out the following form to submit a Request for Quote to any of the following companies listed on
This article provides a detailed look at baling machines.
You will learn:
A baler machine is a compacting device that uses a ram to compact and compress materials into rectangular bales that can be shipped, stored, sent on for further processing, or recycled. They are designed to take similar and dissimilar waste and change them into configurations that are easy to handle and organize. The end result is a maximization of space and optimization of assets.
Agricultural products and waste are baled to preserve their value and make them capable of either being properly removed or used as raw material. Animal fodders are products such as hay, grass, and straw used for feeding domesticated livestock; in order to meet the nutritional needs of the livestock, fodder with high amounts of energy and protein is desired. However, animal fodder is bulky and can easily decompose, which must be compromised with drying and molding. In addition, heat is generated as the fodder spoils, which can cause spontaneous combustion.
Baling helps to control the moisture content of the fodder. Too little moisture causes hay to become dry and lose its nutritional value; too much can cause spoilage and, in turn, combustion. Baled animal fodders are usually wrapped in plastic sheets or covers to help with moisture retention.
Industrial balers improve the material handling of items mostly used for recycling facilities. Balers make the materials smaller, denser, heavier, and stackable. This improves the efficiency of hauling the items, producing large economic benefits. On top of that, recycling baled products significantly improves throughput rates due to easier feeding. This results in reduced operating costs.
Balers were first introduced in the 1930s to help farmers manage the size of haystacks. Before automatic balers, hay was cut manually and gathered into haystacks using rakes and forks. As mentioned earlier, it was already recognized that there is an optimal size for a haystack. It must not be too large to promote heating and combustion nor too small to promote drying and degradation.
The first automatic balers were round balers called Roto-Balers, launched in 1947 by Allis Chalmers. Other types of balers also emerged, such as rectangular and small square balers. Both were used for agriculture.
Early scrap material balers were in the form of compactors patented by MS Wells in 1941 as a means for compacting oil cans. Come the 1970s, these were further developed to compact household wastes by using hydraulic pressure from water lines.
Balers are chosen depending on the type of material to be baled, material loading methods, required purity, required dimensions for transport and milling, and throughput. Since the main point of using balers is to produce an economic advantage, it is important to keep in mind the difference between the baler’s investment and operating costs against the savings produced from storage and transportation cost reductions. Selecting a large, high-throughput baling machine may not be the best option. There are many baling machines available on the market that serve particular materials and specifications.
As the name suggests, this type of baler compresses materials by using vertical, downward force. Vertical balers are sometimes referred to as downstroke balers. These machines are usually used for recycling cardboard, plastics, metals, and foam. The compression chamber is located at the side of the machine in an elevated position. The compression is provided by the ram, which is actuated either by hydraulics or by an electric motor. Once the chamber is filled, the ram moves downward, crushing the materials.
Vertical balers take up less space than horizontal balers. Because of this, they are practical for small-scale applications such as supermarkets and retail stores. Their construction is more compact, making them less expensive. Their cost tends to be a fraction of the price of a horizontal baler. When it comes to the variety of materials processed, vertical balers have the advantage since they can process almost all types of recyclable materials. However, the downside is that their output is not mill standard due to less available compaction force and inconsistent sizes. Inconsistent density and sizes make bales inefficient to transport. Also, this adds additional processing steps to the recycling mill, making them difficult to sell. Some manufacturers offer heavy-duty vertical balers that have powerful pistons actuated by high-power reciprocating pumps. Their robust construction allows them to compact scraps into dense, standard-size bales.
Horizontal balers use horizontal force to compress the materials. Unlike vertical balers, the materials are not loaded directly into the chamber but are collected by a hopper on top of the machine, where the material sits on top of the ram. Conveyor, sorting, and shredding systems can be integrated to aid in loading, making them more convenient and less labor-intensive for operators. For the process to be efficient, the loaded materials must be prevented from jamming, clogging, or preventing the movement of the ram.
Horizontal balers are larger than vertical ones, enabling them to process high volumes. Larger forces are also available, producing denser bales that can weigh up to half a ton. Horizontal balers produce uniform bales, making them more suitable for transport and processing.
Baler manufacturers are constantly looking for methods to keep horizontal balers from jamming and assist in maintaining production. Several types of anti-jamming devices have been developed, such as shear blades that cut material off efficiently and keep the baling process continually moving.
With horizontal balers, the material to be baled sits on top of the main ram and can cause it to slow or jam. Shear blades cut away the protruding material that is above the chamber. Its action prevents jamming and allows the ram to make the compression stroke. Although vertical balers perform the same function as horizontal balers, they are unable to use shear blades, which requires that materials for vertical balers be pre-cut prior to being placed in a vertical baler. Shear blades, saw-toothed or staged, enhance the efficiency of a horizontal baler and prevent delays in processing.
Single ram balers produce compression using a single hydraulic cylinder. This is the most common type of baler used for material recycling. This type can be horizontal or vertical, depending on the orientation of the ram. Horizontal single ram balers can be divided further into closed-end and open-end extrusion balers.
Closed-end (closed-door) balers compact materials using a single ram against the chamber door. After compaction, a chamber door opens to release the bale. Automatic ejection rams are also added to aid in releasing the compacted bale.
Horizontal closed-end balers are the standard for the industrial baler industry. They allow businesses to make larger and heavier bales regardless of the types of materials being baled. Their main feature is the closed-off baling chamber, which is smaller in comparison to open-end auto tie balers. Waste material is compressed using a single ram that uses the weight of its force to compact the material.
Closed-end balers operate automatically and do not require an operator. They activate when their chamber is filled to capacity and continue operation until the material is compressed. Closed-end balers may repeat compaction multiple times until the chamber is completely full and the ram can no longer move.
Open-end balers compress the materials through a long extrusion chamber. This is often called continuous horizontal baling. The ram compresses the bale against the side of the previous bale formed in the extrusion chamber. It is a faster process than closed-end balers and eliminates the need for other parts, such as ejection rams and separation doors. A common feature of open-end extrusion balers is their automatic tying mechanism, which is useful for high-rebound products such as cardboard, rubber, and textiles.
As with closed-end balers, open-end balers operate automatically but continuously without ever stopping due to their open-end design and tying mechanism. They are a highly dependable tool for companies that have a high volume of waste and multiple shifts.
An open-end baler is a heavy-duty extrusion-type baler that quickly and efficiently compresses a huge volume of waste material. Regardless of their constant motion and high-end operation, open-end balers are economical and energy-saving due to the design of their single ram.
Open-end balers come with one or two rams, with the two ram type being able to work quickly and compress a wider range of materials. The chamber of an open-end baler is under constant tension due to the continuous pressure it applies. The increased tension ensures that the bales produced are tight, secure, uniform, and dense. To prevent damage to the mechanism, the baling cylinder releases tension between bales.
Two ram balers, also known as two cylinder balers, are baling machines that compress material using a single ram, with a second ram as a control mechanism. They can be vertical or horizontal in orientation, with one ram to compress the material while the second ram controls and removes it from the baler. These machines are suitable for compacting high-rebound materials such as rubber. They have the advantage of being able to handle large and high-density materials. Two ram balers are widely used with materials that rebound during the compression phase. The position of the rams makes it possible to contain and control the force of the rebound effect.
Another common configuration of two ram balers is the L-shape, where the material is compressed on one axis. After this initial compression, it is then compressed on the other axis. Since the two ram baler opening is not limited by the bale width, they can have a larger feed opening for more convenient loading. For bulkier materials, a larger opening allows for a higher rate of loading while lessening the chances of material bridging in the hopper.
Another advantage of two ram balers is less tie wire usage. By producing a denser bale, less wire is required to secure the shape of the material. Since compacting more materials and exerting more pressure forces materials to undergo plastic deformation (wherein the material will not retain its original shape), two ram balers produce bales that do not change their dimensions over time. In turn, the bales produced do not require stronger ties.
As the name suggests, liquid extraction balers not only compact materials but drain liquid from them. This is particularly useful for baling rejects from food, bottled goods, and brewed goods production. The main difference between liquid extraction balers and other types is the materials used for their construction. Almost 90% of their structural parts are made from stainless steel, while the rest are coated with anti-wear and corrosion paint. This is to prevent the liquid from degrading parts of the baler. Also, liquid extraction balers feature a closed-loop catch system that captures the extracted liquid. This allows for clean and efficient liquid collection and discharge.
These types are mostly used in scrap metal processing. These consist of two or three rams that are designed to handle heavy materials like metals. The two-cylinder ferrous baler consists of a pressing lid or a wing door that compresses the metals along with the main ram. The three-cylinder ferrous baler, on the other hand, compresses the metals in all directions. A pressing lid pre-compresses the metals to the desired baler dimension while the other two rams compress the material, similar to how an L-shaped two ram baler operates.
Like two ram balers, ferrous balers have large openings to allow for feeding more material. The openings are not limited by the dimensions of the bales produced. Material feeding is usually done by cranes.
Another characteristic of ferrous balers is that they do not use automatic tying. Since metals plastically deform when compressed, they mostly retain their shape after compaction.
A track baler is mobile, allowing the baler to be moved to the location of the scrap. They significantly reduce the amount of handling necessary for baling scrap material. The elimination of handling reduces cost, saves time, and improves efficiency. The size of a track baler makes it possible to load several tons of scrap that can be compressed and sheared. The movement and compression process of a track baler is operated by remote control.
In this machine, the materials are compressed to form a log-shaped, compacted material that is then cut to length by shearing or compacting further, forming a bale. The “logging” action acts like a pre-pressing operation. Since these machines produce sheared logs aside from high-density bales, SBLs are also called scrap shears.
The main advantage of SBLs is their portability. Most SBLs are transported by trailer trucks and are equipped with hydraulic landing gears, enabling the machine to be easily mounted onsite. This is useful in small junkyards, demolition projects, and site cleanup activities.
This type of baler is used for baling agricultural products. Round balers are usually pulled by a tractor that collects forage through the field. As the tractor gathers the forage, it is conveyed into the baling chamber, where a series of rollers and belts roll the materials. When the required density and dimensions are reached, an automatic wrapping mechanism is triggered that wraps the rolled material in mesh netting. After wrapping, the baler opens and releases the round bale.
This type of baler is used for baling agricultural products. Round balers are usually pulled by a tractor that collects forage through the field. As the tractor gathers the forage, it is conveyed into the baling chamber, where a series of rollers and belts roll the materials. When the required density and dimensions are reached, an automatic wrapping mechanism is triggered that wraps the rolled material in mesh netting. After wrapping, the baler opens and releases the round bale.
A simple baler consists of a ram, chamber, gate for material feeding, and a machine to produce compressive force. These basic parts are then modified and improved to increase the compressive forces and throughput of the machine. Accessories and other machines, such as hoppers and wire-tying mechanisms, are also integrated to eliminate manual labor. Below are the common parts of a baling machine.
Hydraulic Cylinder: This part exerts the required force to compress the material. The working fluid is pressurized by positive displacement pumps to achieve the required compression. Scrap metal baling requires tough and durable hydraulic cylinders. They must also be able to withstand shocks and side loading. Proper maintenance such as condition monitoring and lubricating is essential.
Control System: This is where commands are entered by the operator. The hydraulic system is usually controlled by programmable logic circuits or PLCs by manipulating the opening and closing of the valves. This is also where parameters such as pressure, bale dimensions, and temperature are monitored. For advanced systems, the machine is equipped with diagnostic and fault detection systems.
Conveyors: Conveyors are used for material feeding at a lower elevation. This eliminates the need for larger cranes that are usually needed to reach the height of the hopper. Loader trucks dump the materials onto the conveyor, which lifts and transports the material into the hopper.
Ejection Rams or Arms: After compression, ejection rams remove the baled material from the chamber. Fully ejecting the bale and other materials that did not form together helps to minimize contamination.
Bale Ties: These are wires or straps that wrap around the bales to prevent them from becoming loose after compaction. Bale ties must have sufficient strength to counter the rebound or expansion of the materials. There are different types of bale ties according to material, finish, and loop. Below are the most common types.
Balers are mostly used in scrap material recycling. Below are the most common uses of balers and the suggested types for each application.
Balers are used for compacting steel cans, aluminum cans, steel sheets, radiator caps, copper wires, and clips. For lighter metals such as cans and sheets, a two ram baler is enough. But for compacting heavier, thicker metals, ferrous balers consisting of three hydraulic cylinders are more suitable.
Balers are used for materials such as cardboard, office papers, magazines, newspapers, and so forth. An average office worker produces about 2 pounds of paper products per day. Mixed paper makes up an estimated 70% of office total waste. Large recycling plants use horizontal single ram balers with automatic tying mechanisms. For small to medium-scale storage and recycling, standard mill-size balers and stand-alone vertical baling machines are sufficient.
This includes PET and HDPE bottles, plastic films, rigid PP containers, rigid and flexible PVC materials, and electronic and automotive plastic scraps. Before feeding to the recycling facility, proper sorting must be done according to type, origin, and characteristics. For baling multiple types of plastics, it is important to prevent contamination between cycles to comply with the recycling facility standards.
Foams are light materials with low densities, taking up much space when stored. Some foams, such as most polyurethane foams, are thermosetting plastics. This means their properties change upon curing, which cannot be reversed. This makes it difficult to recycle such foams, and the only way to manage these wastes is through incineration or landfill storage. Balers help minimize space consumed by compressing weights of more than a thousand pounds into a volume of about 45 cubic feet.
This includes used clothing, carpets, rugs, wool, and other fibrous materials. Baling textiles is different from baling other materials such as steel and plastic since it uses less force but requires the process to be clean and stain-free. The main objective of baling textiles is to reduce the space consumed for hauling and transportation efficiency. Most balers used for textiles are vertical balers.
As mentioned in the earlier chapters, balers are used in compacting animal fodder to help control moisture and retain nutrients. Balers originally emerged as a solution for bundling and storing haystacks. The concept is then applied to scrap material handling. Round balers are the most common for animal forage baling.
As mentioned in the earlier chapters, balers are used in compacting animal fodder to help control moisture and retain nutrients. Balers originally emerged as a solution for bundling and storing haystacks. The concept is then applied to scrap material handling. Round balers are the most common for animal forage baling.
A cardboard baler is a mechanism that uses a metal plate driven by a hydraulic ram to apply tremendous pressure and force to crush, compact, and compress pieces of cardboard into tightly formed and easy to transport cubes and...
A Trash compactor is a machine or device designed to compress, reduce, and compact a variety of materials through hydraulic, mechanical, or pneumatic force. The initial steps in the compacting process are the collection of the material to be compacted...
Modern balers are descendants of hay presses, invented in the mid-nineteenth century, that made it easier to gather and stack hay. The earliest hay presses were stationary units built into a barn and extending two to three stories into the hayloft...
A cardboard shredder is a machine designed to turn cardboard boxes and sheets into small shards or strips. Specialty cardboard shredders are configured to convert cardboard into flexible perforated material for packaging...
A bowl feeder is a mechanism for supplying small parts and components to a production line or for sorting bulk items for rapid use. A self contained bowl feeder system has a bowl that sets on a spring loaded base that moves vertically...
An industrial shredder is a piece of heavy duty equipment designed to shred dense and light materials to prepare them for recycling or for the destruction of unusable products. They are an environmentally sound device that...
Scrap metal must be processed to be effectively recycled and ready for reuse. Metal shredders are machines used to process a variety of metal scraps. Metal shredders are frequently used to reduce metal debris to...
A shredding machine is equipment utilized for shredding. Shredding machines are used to reduce the size of materials. While most online sources define the shredding machine as...
Tire shredders are a type of recycling equipment used to reduce the volume of tires to scrap using high torque shredding systems. The various types of tire shredders are capable of handling large loads of...
Vibratory conveyors are material-handling equipment used to transport fine to coarse-grained bulk materials. These vibratory conveyors are strong conveying equipment utilized for bulk commodities with fine to coarse graininess...
Vibratory feeders are short conveyors used to transport bulk materials utilizing a controlled vibratory force system and gravity. The vibrations impart a combination of horizontal and vertical acceleration through tossing, hopping, or sliding-type of action to the materials being handled...
A vibratory screening is a process that separates bulk solid materials from solids and slurries using inertial vibration that causes various sizes of particles to pass through openings in a screen or...