Plastic Corrugated Boxes
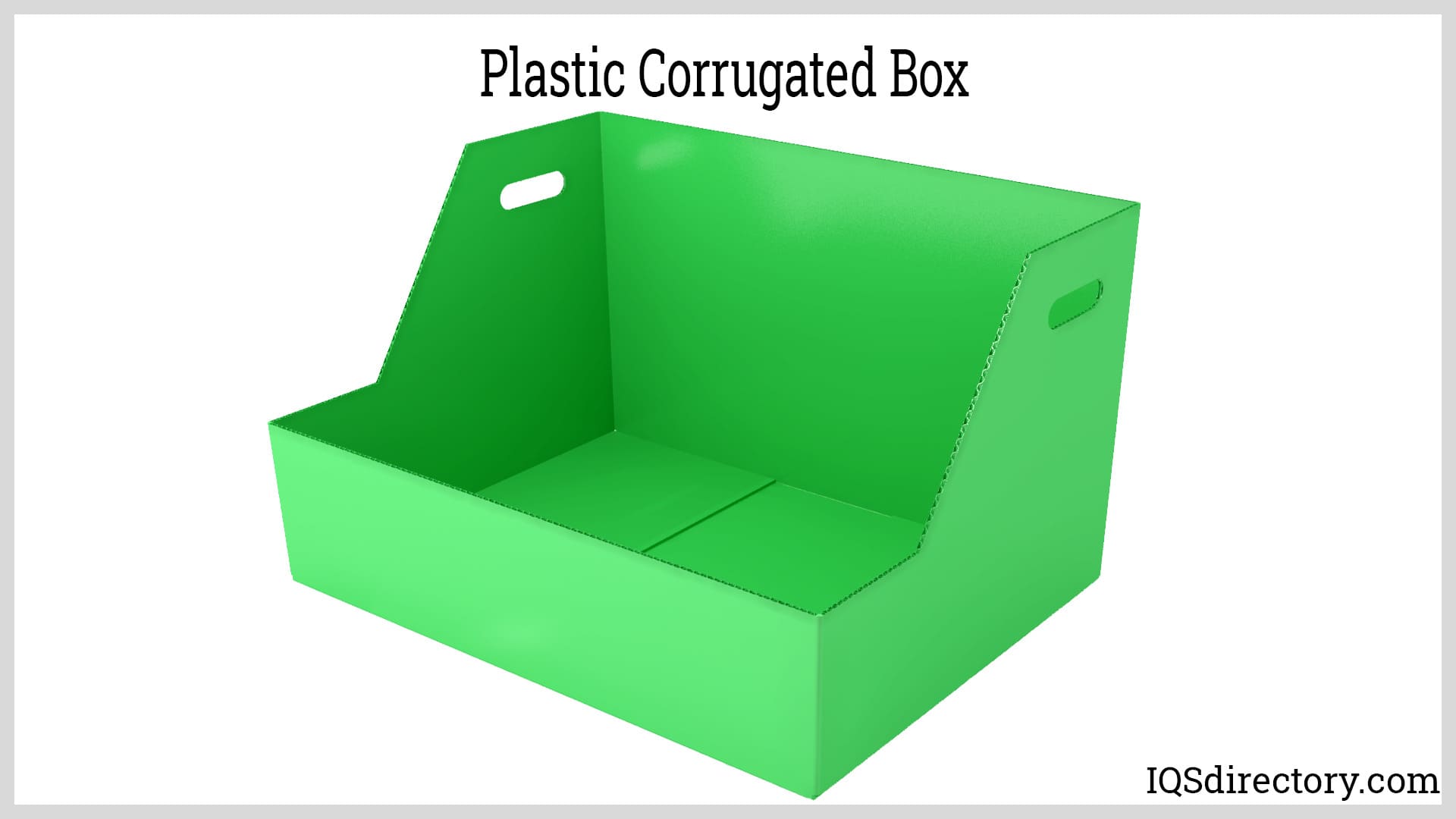
A plastic corrugated box is a disposable container with three layers of material consisting of an inner layer, an outer layer, and a middle layer on its sides. Corrugated plastic is known by various names, including...
Please fill out the following form to submit a Request for Quote to any of the following companies listed on
This article gives deep industry insights into plastic containers. Read further to learn more about:
Plastic containers are storage units fabricated from various forms of polymers produced from crude oil or natural gas. Different chemical processes are used to transform the crude petroleum materials into thermoplastics, which are engineered to be shaped, configured, and formed into highly durable, long-lasting, and sturdy shipping and storage containers. Since their introduction at the beginning of the first industrial revolution, plastic containers have become an essential part of industrial processes and shipping operations.
Depending on the size of the desired container, plastic containers are made by injection molding or rotary molding, with larger uniform versions commonly manufactured using rotary molding. The different methods of production can create any number of plastic containers, from soda bottles to shipping containers several feet high and wide.
Plastic has been around since as early as the 1840s when a German named Eduard Simon discovered polystyrene. This finding was followed by the discovery of celluloid. These breakthroughs were the earliest demonstrations of the polymerization process, the main chemical process for creating plastics. The first plastic containers were plastic bottles. The boom in plastic bottle production came in the 1930s when cellulose acetate was used as raw material. Further development led to the use of low-density polyethylene (LDPE) and polyvinyl chloride (PVC), which were more suitable for mass production.
Today, plastic containers are available in different shapes and sizes. Advances in manufacturing methods brought large bulk containers, thin and transparent clamshell packs, and impact-resistant plastic cases. The global market size of plastic containers is estimated to be around $86 billion in 2018. This is expected to grow by 4% from 2019 to 2025. Examples of industries that have a high demand for plastic containers are beverage, food, pharmaceutical, cosmetics, household consumer goods, industrial lubricants, and petroleum products.
The most commonly used material for plastic containers is polyethylene terephthalate (PET). It is used for producing mineral water, carbonated drink, and juice bottles. Next is HDPE which is used for the packaging of household goods such as shampoo, cleaning materials, detergent, etc.
The basic chemicals for producing plastics typically come from petroleum and other fossil fuel-based compounds. Examples of such chemicals are ethylene, propylene, styrene, and acetylene. These monomers are simple organic molecules with a double bond and some functional groups. The presence of double bonds and functional groups allows monomers to react with one another to form long, chained molecules or polymers. This process is known as polymerization.
One or more types of monomers can be polymerized to form a polymer chain. Combining two or more types of monomers is a common way to give plastics better characteristics. The resulting polymers are then mixed with different ingredients through the process of compounding. Additives, fillers, and reinforcements are compounded to add additional properties intended to suit a particular application. Examples of these imparted properties are thermal stability, aging resistance, flame resistance, clarity, and color. After compounding, plastics are ready to be formed into different products, including containers.
Plastic polymers can be broadly classified as thermoplastic and thermosetting polymers.
Thermoplastic polymers, or thermoplastics, have polymer molecules that can be repeatedly rearranged by heating and cooling. Heating thermoplastics liquify or soften them. No chemical change takes place during this process. This is because of the absence of crosslinking evident in thermosetting polymers. Subsequent cooling returns the material to its solid state. This heating and cooling process allows the plastic to be formed into different shapes.
Plastics made from these types of polymers have functional groups that form the crosslinks between the molecules. Thermosetting polymers or thermosets cannot be softened through heating. Once heated, it undergoes a chemical reaction that permanently changes its properties. Processing thermosets include an additional process called curing. Curing is the process of creating crosslinks between polymer chains. This finalizes the properties of the plastic.
Since its mass production in the 1950s, plastics have been regarded as the "wonder material". Though considered an environmental problem today, it will be difficult for other materials to take its place. Plastics are cheap, light, strong, tough, and do not corrode. That is why plastics are suited not only for producing plastic containers and other everyday products. Below are some of the advantages of plastic containers.
Plastics are great materials when it comes to formability. Plastics can be molded, cast, rolled, pressed, stamped, extruded, and so on. They can be formed into complex shapes, including those that are difficult or impossible for other materials. The dies and tools used to form plastics are also easier to make. Forming plastic containers does not require as much pressure as that forming glass or metal containers.
Plastic containers do not corrode or degrade the same way as metals. Metals develop rust, which weakens the structural integrity of the container. Rust also poses the threat of product contamination, especially for food and pharmaceutical products. Only a few materials can compare to the degradation resistance of plastic. One example would be glass which has many limitations when used as containers.
Plastics have densities around 0.8 to 1.5 times that of water. Steels have densities of around 7.8 times while glass and ceramics are around 2 to 3 times. This shows that plastics are significantly lighter than metals and glass used for the same application. Moreover, some plastics are engineered to have a high strength-to-mass ratio. Containers made from these plastics have thinner walls, further reducing their mass.
Plastic containers can be made from different types of chemicals through various processes. Each type of plastic has inherent mechanical properties. These properties are modified by compounding special additives that can improve its flexibility and strength. Examples of these additives are glass and carbon fibers. Adding fibers into a plastic matrix creates a composite material with better tensile and flexural strength.
Plastics are made from long, chained molecules that arrange themselves in crystalline or amorphous structures. Their structure gives them inherent elasticity, so plastics do not fail easily through brittle fracture and cracking. Tearing is an issue resolved by including additives or by using a polymer base with high tensile strength.
The appearance of plastic containers is fully customizable. Plastic containers can be made into clear, translucent, or fully opaque products. They can also have different colors by adding pigments. When it comes to surface characteristics, plastics can have a variety of finishes and textures without using expensive secondary operations.
Because of their chemical and wear resistance, plastic containers do not degrade easily under normal conditions. This gives them a long service life. Some plastic additives further enhance their durability by imparting resistance to oxidation and ultraviolet radiation. However, the downside of their long life is their negative impact on the environment. When not managed properly, they can quickly accumulate and harm ecosystems.
Like glass and metals, plastic containers can be recycled. Traditionally, plastics are recycled through heating and melting. By heating, plastics are melted and formed into raw materials for manufacturing new plastic products. However, melting is only applicable to thermoplastics. Advanced processes are also being developed; generally, these methods chemically convert plastics into monomers that are used as fuels for power generation.
Plastic containers are easy to form and require less energy to produce than metal and glass containers. Plastics are easily shaped when heated, requiring only a moderate amount of pressure. Plastics can even be formed by compressed air. The temperature of its melted state is not as high as metals and glass. Plastics in this state can be injected and molded without the need for expensive dies and tools.
Most plastic containers have a number embossed at the bottom. These numbers indicate the type of plastic used in making the container. This system allows straightforward identification for proper segregation during recycling. The type of plastic is determined by the type of polymer used in creating the resin. Each polymer type is processed and recycled differently.
A good rule to follow is iullustrated below. Numbers three and six are not readiy accepted by most recycling systems, while the rest can be recycled normally.
Numbers one to six are common materials, enumerated in order below. The last number, number seven, is composed of miscellaneous plastics such as polycarbonate and ABS.
PET is the most used plastic material for plastic containers. It is known for its low permeability to carbon dioxide, particularly the biaxially oriented types, which makes it ideal for producing bottles for carbonated beverages. Since it absorbs water from its surroundings, it can be processed using molding machines and dried.
The chemicals of PET do not leak, which is one of the reasons it is used for food processing. Additionally, this physical property makes it a very safe plastic capable of continuous use. The recyclability of PET has made it the main focus of modern plastic container manufacturing. When it is recycled, it is used in countless applications.
According to data collected by scientists, PET is the greenest of the materials used to produce containers. Its ability to be recycled and refabricated is far superior to aluminum, metals, and glass.
HDPE is a type of polyethylene (PE). It is characterized as having a high strength-to-density ratio. Its molecular structure is linear, with little branching that results in higher intermolecular forces. HDPE is commonly used for making stiffer containers and bottles. Examples are water gallons, milk jugs, detergent bottles, and plastic drums. HDPE can both be reused and recycled. It is considered one of the safest forms of plastics.
Polyvinyl chloride is a type of plastic that can be formulated with different stabilizers, plasticizers, impact modifiers, processing aids, and other additives. It can be made into rigid or flexible plastic containers by modifying the amount of plasticizers. Moreover, they offer better clarity than other versatile plastics. However, PVCs have the potential to release harmful pollutants, acids, and toxins during processing or degradation. Its compounding ingredients are now being regulated by the FDA, EPA, and other organizations.
Low-density polyethylene is another type of PE. It has a branched polymer chain linked by weak intermolecular forces. This results in lower tensile strength and barrier properties. Nevertheless, it has better impact strength and resilience than HDPE. They are used for making flexible containers and bottles such as squeezable bottles, dispensing bottles, and sampling containers.
Polypropylene is a versatile polymer that can have a wide range of properties. Its properties depend on its molecular weight, morphology, crystalline structure, additives, and copolymerization. It can be made into polymers with a high degree of crystallinity. This results in higher tensile strength and hardness comparable to HDPE. Moreover, they can withstand high temperatures without losing strength or undergoing degradation. The disadvantages of using PP are its susceptibility to UV degradation and oxidation. PP is commonly used for producing drums and pails.
Similar to Polypropylene, Polystyrene is another versatile plastic modified by copolymerization and the addition of additives. They can be made into flexible, rigid, or cellular (foam) plastic forms. Polystyrene is generally prone to oxidation; thus, repeated recycling is not recommended. Furthermore, their sensitivity to oxidation causes their color to become yellowish. PS is often used for making disposable containers, such as clamshell food packaging and disposable cups.
Polycarbonate is easily processed by different molding methods, with injection molding and sheet extrusion being the most common. Its usual applications are beverage bottles and food storage containers. Polycarbonates are known for their high impact strength, heat resistance, good electrical insulation, transparency, good water barrier properties, and inherent flame-retardant properties.
Acrylonitrile Butadiene Styrene is a common plastic material characterized by good hardness and rigidity while having some degree of toughness. Protective coatings are usually applied due to their poor resistance to UV and only adequate resistance to most acids and alkalis. They are commonly used for making battery containers.
Polyamide is considered an engineering plastic characterized by its high toughness, high impact strength, resistance to solvents, good abrasion resistance, and heat resistance. The common application of PA is automotive fuel tanks.
The type of plastic forming process employed depends on the form of the plastic container. Plastic containers can be in the form of intermediate bulk containers (IBCs), drums, bottles, bags, and enclosures. Each type of plastic container has a distinct shape that suits one type of fabrication process better than others. Below are the common methods for producing plastic containers.
Injection molding is a plastic forming process that involves injecting molten plastic into a closed chamber or mold. This process has three main operations:
The most popular injection molding machine is a reciprocating screw-type extruder. Plastic is compounded by the repeated kneading and mixing of the screw. When the plastic is ready to be injected, the screw moves to push the plastic out of the extruder and into the mold.
The mold contains the shape of the plastic container. It is usually composed of two halves. One is stationary while the other can move. After molding, one half moves to release the product. The mold has several openings or channels. These are used for introducing plastic into the mold, venting air, and permitting some plastic to flow out of the mold.
Injection molding is limited to producing containers that are open on one side. Examples are pails, tubs, cups, bowls, and food containers. By itself, injection molding is not suited for producing closed, hollow products such as plastic bottles. To produce these products, an inert gas is introduced into the mold partially filled with molten plastic. This pushes the plastic on the surface of the mold, creating a hollow part. This process is known as gas-assisted injection molding.
Blow molding forms plastic containers by inflating a softened plastic compound inside a mold. The main operations of blow molding are:
As in the injection molding process, blow molding also uses screw extruders for compounding and heating the plastic. In creating the preform, the process is divided into two types: extrusion blow molding and injection blow molding.
Extrusion blow molding extrudes the preform into a hollow tube suspended on one end. Injection blow molding, on the other hand, creates the preform by injecting plastic into a mold with a core for air supply. Both processes use air to shape the preform against the mold.
Blow molding is best suited for producing hollow plastic products such as bottles, water jugs, tube packaging, intermediate bulk containers (IBCs), and storage tanks.
Rotational molding, commonly referred to as "roto molding", is a plastic casting technique used to produce hollow and seamless plastic containers. This process does not use pressure to form its product. Instead, it forms the container by spreading the plastic melt on the inner surfaces of the mold through rotation. Its operation is summarized as follows:
There are different rotational molding machines that differ by the number and configuration of the molds and how the molds are heated and rotated. Examples of rotational molding machines are clamshell, turret, shuttle, and swing machines.
Since there are no high pressures involved, the molds used for rotational molding are inexpensive, and larger products can be formed. Rotational molding can also produce double-walled containers without any secondary processing.
Some products of rotational molding are industrial and agricultural storage tanks, drums, carboys, insulating boxes, and trash bins.
Thermoforming is the process of heating thin plastic sheets to their forming temperature and stretching them over a mold. It is a secondary plastic forming process that does not use raw plastic resin for compounding. Rather, it uses a plastic sheet or film produced from preliminary processes such as extrusion or calendering. The steps involved in thermoforming are:
There are four main types of thermoforming: vacuum, pressure, mechanical, and twin sheet forming. Each method differs in how pressure is applied to create the thermoform. Vacuum, pressure, and twin sheet thermoforming all use compressed air to press the plastic sheet against the mold. Mechanical thermoforming has two dies that press against each other to deform the plastic.
Thermoforming is limited to producing parts with relatively thin walls. Moreover, the process is prone to defects such as inconsistent thickness, webbing, and warping. It is not suited for producing containers requiring rigidity.
Common thermoforming containers are those used for food and pharmaceutical applications, which are designed for single use. Examples are disposable cups, clamshell containers, and trays.
Compression molding shapes the plastic resin by pressing it against two molds. This process is preferred when forming large thermosetting plastic products. The process is summarized below.
Typically, the compression press is closes downwards. Upward-closing compression presses are also available. The mold has internal heating elements that soften the plastic charge. This allows the plastic to flow according to the shape of the mold. The heat also cures the plastic. During curing, some plastic may release gasses that are vented through an additional phase called degassing.
Compression molding is also used for molding containers with fiber components. Glass or carbon fibers can be added while preforming the plastic charge.
Like injection molding which uses two mold halves, compression molding is limited to producing containers that are open on one side. Examples of compression molding containers are large bins, tubs, and trays. Plastic caps for bottles can also be made by compression molding.
Plastic containers are a common part of everyday life. Their uses are endless and include gas cans, airline and railroad shipping containers, suitcases, garage storage containers, barrels, drums, and tool boxes. The durability of various types of thermoplastic materials is the foundation of the plastic container industry, which has diligently engineered and perfected new forms of containers to meet the ever-growing demand.
Plastic folding boxes are a growing trend in the packaging industry. They are a cost-effective and elegant method for displaying products. Plastic folding boxes offer a clear view of a product while protecting the product from damage. They are made from a full array of thermoplastic materials and have the same endurance and stability as other plastic containers. Packaged products are kept secure during shipment to ensure safe delivery. Plastic folding boxes can be customized with graphics, artwork, and logos to enhance product presentation.
Lighter forms of plastic folding boxes are used for product display and shipment. Other forms of plastic folding boxes include heavy-duty shipping containers, which have solid plastic sides that fold flat when not needed. They come in a wide variety of sizes and have interlocking corners for quick setup and stability. These heavy-duty plastic folding boxes are capable of carrying over 100 lbs (45 kg) but easily collapse to be stacked when not in use.
Plastic barrels are made from high-density polyethylene, which gives the barrels their strength and toughness. They are ideal for any form of industrial operation, including transfer, storage, waste disposal, fluid and parts storage, and packaging. The thermoplastic materials of plastic barrels can withstand the effects of chemicals and hazardous materials. Unlike drums and barrels made of metal, they are resistant to rusting and corrosion, increasing their longevity.
Plastic gas cans are made from all different types of thermoplastics and are engineered to be able to safely hold gas. They come in several gallon sizes, from one gallon to over ten gallons, and provide a safe and convenient way to transport and store gas. Under normal conditions, plastic gas cans can store gas for close to a year without seepage or leaks due to the molecular structure of the various polymers.
Plastic shipping crates are highly durable, strong, and sturdy crates that are designed for years of constant use as well and resist stress associated with long-distance transport. The large size of plastic shipping crates requires that they be manufactured using rotary molding to ensure that the crates have an even wall thickness and a single seamless unit.
The interior space of a plastic shipping crate is capable of handling extremely heavy materials, such as electrical tools and equipment or displays for conventions. They come in sizes to meet any shipping needs.
The four plastic containers described above are a small sampling of the wide selection of plastic containers available from plastic container manufacturers, who produce standard sized containers and custom designed ones to fit unique and unusual applications.
A plastic corrugated box is a disposable container with three layers of material consisting of an inner layer, an outer layer, and a middle layer on its sides. Corrugated plastic is known by various names, including...
Plastic crates are containers used for moving or transporting goods from point A to point B. They are also used for storage and are made of exclusively or partially plastic material. The basic material is plastic...
A plastic tote is a box type portable storage container that is made of resilient and durable plastic that is capable of withstanding heavy duty use in industrial and residential settings. They come in...
Nylon tubing, also known as polyamide tubing, is a type of tubing made from polyamide resin, which has a strong resistance to abrasion. It is used in high-pressure and high-temperature applications...
Plastic materials are objects artificially made from organic compounds called polymers along with other additive components. They possess excellent formability, making them extremely versatile for many different fabrication and manufacturing processes...
A plastic tank is a large capacity liquid or granular storage unit that can be vertical, horizontal, below or above ground, as well as movable. They are designed to hold several gallons of a variety of substances for long periods without experiencing wear, weathering, or deterioration...
Plastic tubing is a form of tubing that is manufactured from a mixture of a polymer with a variety of chemicals to form a material that can be solid or flexible. Since its first use in the 1950‘s, plastic tubing has revolutionized industrial processes and has found a use in a wide variety of applications...
A plastic water tank is a large capacity container designed to store water for household, agricultural, irrigation, and industrial manufacturing use. There are various types of water tanks produced to meet the needs of specific applications, with...
A poly tank is a plastic storage tank used to store, transport, and collect water, other liquids, and granular or powder materials. They are made of polyethylene or polypropylene and are a cost effective, lightweight, and easy to handle...
Poly tubing is a highly flexible, lightweight, and durable tubing that is produced from polyethylene, a polymer that is made from the polymerization of ethylene. It is a very versatile form of tubing that has break and crack resistant walls...
PVC is a tough chemically resistant synthetic polymer of vinyl chloride used especially for making pipes, films and electrical insulation. It is made by polymerizing vinyl chloride, and...
Silicone tubing is a very tough elastomer that exhibits high strength, flexibility, and resistance. Silicone tubing can be stretched without tearing and is highly versatile. It cannot be weakened with repeated bending and twisting due to...