Nylon Tubing
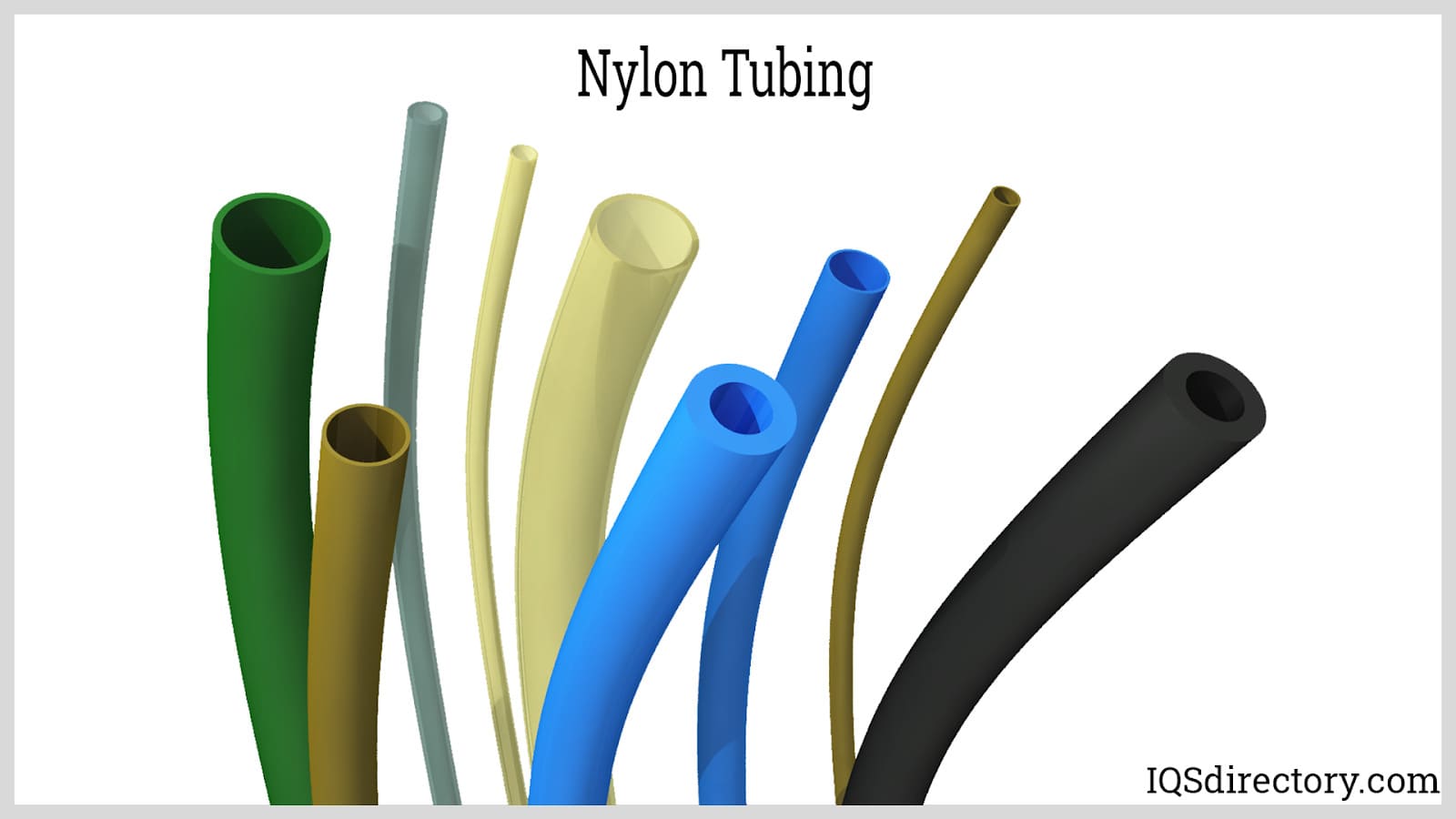
Nylon tubing, also known as polyamide tubing, is a type of tubing made from polyamide resin, which has a strong resistance to abrasion. It is used in high-pressure and high-temperature applications...
Please fill out the following form to submit a Request for Quote to any of the following companies listed on
This article takes an in depth look at Poly Tubing.
You will learn more about topics such as:
Poly tubing is a highly flexible, lightweight, and durable tubing that is produced from polyethylene, polypropylene, and polyurethane, polymers that are made from the polymerization of ethylene. It is a very versatile form of tubing that has break and crack resistant walls. The main types of poly tubes are high density polyethylene (HDPE) and low density polyethylene (LDPE).
The term poly tubing is a generic term used to encompass all the forms of tubing made from the various types of polymers derived from crude oil and natural gas. The wide use of poly tubing is due to its low cost with polyethylene being the least expensive of the resins.
The main difference between HDPE and LDPE is flexibility. LDPE is very flexible while HDPE is very rigid and rugged. Regardless of this difference, LDPE and HDPE have the same strength and resilience. Of the various methods used to make tubing, poly tubing is most commonly made using extrusion.
A popular type of resin used to manufacture poly tubing is polyurethane that can be made flexible or rigid. Its long history began during World War II when it was developed as a replacement for rubber. The exceptional durability of polyurethane and its excellent performance in comparison to rubber substantially increased its popularity during the war and after.
The materials used to make poly tubing are polyurethane, polypropylene, and polyethylene, which are made of a polymer chain of ethylene molecules that include carbon and hydrogen molecules. The raw materials to create the polymers to manufacture poly tubing are taken from crude oil and natural gas with natural gas being the preferred source. The final thickness and density of poly tubing depends on the application for which it will be used. The wall thickness and rigidity of the material determine its classification.
The two general types of poly tubes are HDPE and LDPE with HDPE being very rigid and inflexible while LDPE is more pliable and forgiving. Regardless of the variations in thickness, both forms of polyethylene begin with the application of heat to petroleum.
The process of manufacturing poly tubes begins with the manufacturing of the raw material, polyethylene. The production of polyethylene (PE) involves the polymerization of ethylene from crude oil or natural gas. PE is a member of the family of polymers that range in configuration from low density to high density with each of the various forms having different properties and characteristics. The molecular structure of polyethylene can be seen below.
When discussing the methods used to produce poly tubes, there are four distinct processes that are commonly described, which are extrusion, injection molding, blow molding, and rotomolding. Though all four methods involve the heating of the polyethylene material, each method has a very unique approach to shaping the tubing.
How poly tubing is produced determines how it will be used. Each process gives the final product different characteristics and properties.
Extrusion is the most common of the production methods used to produce poly tubes. As with all of the methods of poly tubing production, extrusion begins by heating rosin pellets that are fed into a hopper where a screw moves them along toward the die that has the profile of the tube.
As can be seen in the diagram above, the material enters the barrel of the extruder through the throat of the hopper. The screw in the middle of the barrel forces the material along the barrel. As the beads move through the barrel, they are gradually heated in the various melting or heating zones; this allows the beads to melt gradually to lower the risk of overheating.
As the melted material leaves the barrel, it passes through a screen track and breaker plate in order to increase pressure and remove impurities. The pressure on the material as it leaves the barrel is at 5000 psi; this is necessary to ensure a uniform melt. After the breaker plate and screen track, the molten material enters the die where it is shaped into a tube.
The extrudate is pulled through a water bath to cool. Since plastic is an excellent thermal insulator, it retains heat and is difficult to cool. A controlled vacuum is used to keep the new formation and prevent it from collapsing.
Rotational molding is a heat process where powdered, granular, or liquid plastic is placed in the mold. As the mold is heated, it rotates, forcing the plastic powder to melt and adhere to the sides of the mold. The process of rotational molding is used to produce large poly tubes and poly tubes with intricate and complex configurations. It is an expensive and time consuming method since each tube is individually molded.
The main reason for using rotational molding is the accuracy in forming poly tubes at just the right thickness. As with extrusion, once the shape is formed, it is cooled. In the case of rotational molding, it is cooled at room temperature or using a mist spray or a combination of spray and room temperature.
The pultrusion method is a combination of pulling the material to be shaped and extruding it. Pultrusion uses pressure to force a molten material through a profile as extrusion does; pultrusion does this by pulling the material through. Tubing is formed by pulling the heated material through a die. As it is pulled through, it moves over a mandrel that helps the shaped material hold its configuration during the curing process.
The pultrusion process makes it easy to produce a wide variety of lengths and thicknesses. The continuous, unidirectional lengths are cut to size after the curing process.
An interesting offshoot of pultrusion is pullbraiding. As the tubing is pulled through, the fibers are braided together while they are still hot. Layers of different angles can be accomplished by changing the braiding method.
Pultrusion and pullbraiding create tubing with exceptional stiffness and an exceptional strength to weight ratio. The advantage of pullbraiding over pultrusion is that it produces balanced tubing that can be used with a wide range of loads as well as have a distinct appearance.
There are numerous machines available to produce poly tubing in both the United States and Canada. These machines are important in today's society as they enable the efficient and cost-effective manufacturing of poly tubing, which is used in various industries such as medical, agriculture, food and beverage, and chemical. We discuss many of these leading machines below.
Features: The Davis-Standard DS-SPF is a popular blown film extrusion machine known for its versatility and precision in producing poly tubing. It offers advanced control systems, high output rates, and the ability to process a wide range of polymer materials. This machine's popularity is also attributed to its consistent and reliable performance.
Features: The Gloucester Engineering X-SERIES flat die extrusion machine is widely used for producing poly tubing due to its precision and high output rates. It offers enhanced melt homogeneity, temperature control, and a modular design, allowing customization for specific applications.
Features: The W&H VAREX II is a high-performance blown film extrusion machine that is widely used for producing poly tubing. It offers advanced automation, high output rates, and precise control over film thickness, making it suitable for a wide range of applications in the packaging industry.
Features: The Macchi Coex Flex is a leading co-extrusion machine that can produce poly tubing with multiple layers, offering enhanced properties like barrier protection and strength. It is popular for its ability to combine various resins and efficiently control layer thicknesses, ensuring optimal performance in demanding applications.
Features: The Leistritz ZSE MAXX twin screw extrusion machine is widely used for producing poly tubing due to its excellent mixing capabilities, consistent melt quality, and high production rates. Its user-friendly interface and robust design make it a popular choice for various polymer processing applications.
These machines have gained popularity in the industry due to their advanced features, reliability, and ability to meet the demanding requirements of producing high-quality poly tubing efficiently. Keep in mind that manufacturers may have introduced newer models or updates beyond this article’s posting date, so it's advisable to refer to the latest information and sources for up-to-date details.
Poly tubing is formed from polyethylene—the most commonly used plastic since it is safe to use with chemicals, gasses, and fluids. Most engineers and designers know polyethylene tubing as poly tube or PE. It is often compared to polyurethane, a plastic that was developed during World War Two as a replacement for rubber.
Polyethylene is not as flexible as polyurethane but has greater resistance to moisture, cracking, and puncturing. The exceptional strength and resilience of PE has made it the first choice for the production of corrosion free piping.
Polyethylene is a polymer, which is a chain of single units called monomers. The monomers join together to form polymers with polyethylene being the most common. Though this is the basic structure of polyethylene, there are many variations of it that have different densities, molecular weight, and crystallinity. The difference between the various types of polyethylene is due to the extent of the number of branches each type has.
HDPE has the lowest number of branches and is a cost effective and tough thermoplastic. The process for producing HDPE involves low temperature and low pressure to produce a density of 0.941 g/cm3. The lower number of branches is due to how tightly the molecules are packed together with stronger underlying intermolecular forces.
HDPE is chosen as a production plastic due to its high tensile strength, weather resistance, water resistance, translucence, toughness at low temperatures, and resistance to chemicals. The other positive characteristics of HDPE include resistance to solvents, dilute acids, alkalis, and alcohols and moderate resistance to oil and grease.
LDPE has more branches than HDPE with a mixture of long and short chains. LDPE has a semi-rigid structure and is produced using high pressure. The result of the high pressure process is that LDPE does not have the same intermolecular strength as HDPE, making the crystal structure less tightly packed. These factors contribute to LDPE having exceptional ductility but lower tensile strength.
Similar to HDPE, LDPE has resistance to dilute acids, alkalis, and alcohols but has average resistance to hydrocarbons, mineral oil, oxidizing agents, and halogen hydrocarbons. It has high impact strength at low temperatures and good insulating properties. Since LDPE is Food and Drug Administration (FDA) approved, it can be used for food processing and packaging.
The Qualities and Advantages of Low Density Polyethylene | |
---|---|
Low Density Polyethylene | |
Outdoor Weathering | Fair |
Impact Strength | Excellent |
Rigidity | Fair |
Coefficient of Thermal Expansion | Fair |
Heat Distortion Temperature | Good |
Clear or Opaque | Opaque |
LLDPE has the same structure as LDPE with the same number of branches, but the branches are shorter. It is produced by polymerizing ethylene with butene, hexene, and octene, which gives it a density range of 0.815 g/cm3 to 0.925 g/cm3. LLDPE has a lower tensile strength than LDPE but has been used as a replacement for LDPE in certain applications due to its impact and puncture resistance.
One of the distinctions of LLDPE is its translucent natural milky color. It has a very low environmental impact since it burns without leaving a residue but turns to carbon dioxide and water without releasing toxic fumes. LLDPE is not commonly used to make poly tubes but is used mainly for making packaging films.
The name for UHMWPE is due to its molecular weight, which is between 3.5 million amu to 7.5 million amu or ten times more than the molecular weight of HDPE. It is made tough through the use of a catalyst and ethylene with the Ziegler catalysts being the most common.
UHMWPE has excellent wear and cut resistance and is unaffected by abrasions. It has excellent corrosion resistance, which allows it to be used in aggressive and hazardous environments. The general description of UHMWPE is that it is a very high performance polyethylene.
PEX has cross linked bonds in the polymer structure that make it a high density polyethylene. It is a thermoset plastic that cannot be reheated or melted after it has been shaped and experiences degradation if melted. PEX is manufactured using free radicals that produce the cross linking by using a process that includes organic peroxides and placing the material under high pressure.
Due to PEX‘s exceptional chemical resistance and high temperature properties, it is widely used as chemical piping in heating and cooling systems. PEX is also used for its electrical and insulation properties to make high voltage cables. In plumbing, it can be stretched over nipples but return to its original shape to form a tight and firm seal.
Polypropylene tubing is rigid, has a high melting point, and is puncture and chemical resistant. The strength and endurance of polypropylene tubing makes it able to withstand temperatures ranging from below freezing to temperatures over 275o F or 135o C. The fact that polypropylene is resistant to acids and alkalis makes it an ideal resource for industrial use as part of a fluid system or liner for metal piping.
A major factor in the wide use of polypropylene is due to its low cost and high quality. It is commonly used in waste removal systems for commercial and residential applications.
As can be seen in the sample below, polypropylene tubing is produced crystal clear allowing for visual monitoring of its contents.
Polyurethane is a polymer made by combining diisocyanates and polyols, which are combined in hundreds of different ways to make different forms of polyurethane. Tubing made from polyurethane is flexible and kink and abrasion resistant. It is produced in a variety of colors, which are used as a method for coding and identifying parts of a system.
Like rubber, polyurethane has a high chemical resistance, which makes it suitable for use by several industries. It is able to withstand high pressures and has excellent hydrolytic stability.
Polybutene-1 is used in plumbing systems. It meets the demands required of mechanical performance, is exceptionally flexible, and has excellent thermoplastic properties. The popularity of polybutene-1 is due to how easy it is to install and its flexibility.
The production of polybutene-1 includes the use of the isomers of butene, which is a basic hydrocarbon with four carbon atoms. Included in the polymeric molecule are 1-butene, 2-butene, and isobutylene. The properties of polybutene-1 vary depending on how the molecules are combined.
Poly tubing is one of the most used types of tubing due to its flexibility, lightweight, durability, and corrosion resistance. It is ideal for transferring and transporting liquids, gasses, and fluids in a wide variety of applications. Since it is FDA approved, it can be used for the movement of liquids and materials in food processing.
Polyethylene tubing is used where extra strength is necessary, and there may be a possible concern over pipes or tubing corroding. An additional advantage of poly tubing is that it won‘t rot, produce odors, or damage the taste of liquids.
There are very strict requirements regarding tubing used for medical purposes. It has to meet the requirements and standards specified for medical and pharmaceutical applications as well as handle various medical fluids without damaging or contaminating them.
Poly tubing for medical use includes tubing for anesthesiology and respiratory equipment, intravenous tubes, catheters, and peristaltic pumps. When poly tubing is sold as medical tubing, it is labeled as such with a list of the standards that it meets as well as the applications for which it is appropriate.
Poly tubing or pipes are used in farming as a method for irrigating crops since it does not deteriorate, rust, or corrode. Fluctuations in irrigation canals is a constant problem since it does not provide a continuous amount of water. With poly tubing, all that is necessary is to open the outlet. Water is delivered steadily without the need to be tended to or monitored.
Though the initial cost of poly tubing or piping is higher, the cost is recouped by lower labor costs since it takes just two workers to install it. A further cost benefit is the reliability of poly tubing since it remains in position and does not shift or break. Poly tubing can be purchased in a wide variety of diameters and wall thicknesses to meet the needs of the irrigation project.
Components used for the food and beverage industry have to be manufactured such that they provide optimal sanitation and safety for consumers. For tubing to be accepted for food processing, it has to meet the legal requirements established by the FDA, which has regulations regarding any product that comes in contact with food.
The type of polyethylene tubing used by the food and beverage industry is Food Grade UHMWPE; it is capable of being used in any part of food production.
HDPE and LDPE have a high compatibility rating for most chemicals and are resistant to the effect of strong acids and bases as well as oxidants and reducing agents. They are capable of positively interacting with over 150 chemicals after having been tested with the chemicals for several days at temperatures ranging between 20° C and 50° C.
After exposure to the chemicals for 30 days, HDPE and LDPE did not show any damage and have been predicted to last a year at the same exposure level. The area where they failed was exposure to hydrocarbons such as aliphatic, aromatic, and halogenated.
Though tubing is not considered an essential part of an air compressor, its significance radically improves when it clogs or fails. Even if it does not fail, there can be power losses and lowered efficiency when the wrong tubing is used.
Poly tubes are the first choice for air compressors as a highly reliable and efficient method of delivering compressed air. For air compressor tubing to be successful, it must be able to deliver the air at sufficient volume, quality, and pressure to power the component or device it is linked to. Inappropriate tube design and connections cause an increase in costs and damage to equipment.
Polyethylene tubing is chosen for air compressors because it does not corrode or rust and is lightweight and easy to connect and install. Its smooth interior ensures that air passes easily, while its strength, resilience, and endurance ensure its longevity.
In the middle of the 20th Century, several forms of plastic or polymer tubing and piping were found to be inappropriate for use in plumbing. Several types cracked, leaked, and caused problems that led to lawsuits and litigation. In the 1980‘s, cross linked polyethylene was introduced as a replacement for other plastic materials.
PEX has been accepted in the United States as reliable for use in water systems and radiant heat systems. Though it requires special fittings, its strength, endurance, and dependability have made it the perfect solution to plumbing problems.
HDPE has been used for plumbing of non-potable water for many years. It is preferred for use with welded joints since its use eliminates the need for special equipment. HDPE is flexible and capable of withstanding harsh conditions. Its flexibility allows it to be used around corners without the need for additional joints.
Poly tubing comes in a wide range of chemical compounds, each of which has advantages to meet the needs of any application. The various types of poly tubing have benefits that make them flexible enough to fit into a plumbing system or medical procedure.
The many benefits of poly tubing have made it the most widely used tubing product on the market. Though it is lightweight and flexible, it still has the strength and endurance to withstand constant and continuous wear.
Poly tubing is not affected by temperature fluctuations and is resistant to weathering; these factors make it crack resistant. It is very useful where there are intermittent cold and warm conditions.
Every type of poly tube has exceptional strength and endurance. It is tensile strength that prevents them from cracking, stress breaking, and effects of impacts. The resilience of poly tubes is found in their resistance to abrasion wear or damage from fatigue.
Part of the reason for poly tube‘s tensile strength is its ductility. When a material is ductile, it can stretch and flex when it is put under pressure. Instead of cracking when placed under strain, poly tubes flex with the strain.
This aspect of poly tubing tends to be the most surprising considering its strength, durability, and endurance. Regardless of the size and type of tubing, it is guaranteed to be lightweight and flexible. This quality makes it an ideal building material and the perfect solution for hard to reach spots that require piping or tubing.
The weight of tubing materials can be an issue for many modern applications due to sensitivity, mobility, and installation. Any form of poly tubing is far lighter than other alternative materials, especially metals. It is this one aspect of poly tubing that has made it such a useful resource for a variety of projects. Along with its lighter weight, tensile strength, and durability, the natural flexibility of poly tubing makes it adaptable for any form of installation, regardless how complex.
Corrosion is a factor that has to be continuously accounted for regarding the installation of piping since it is costly and problematic. It occurs on the outside and inside of piping and greatly affects the efficiency of equipment. Poly tubing is resistant to rust, corrosion, and rot as well as any form of biological growth. This single factor ensures a long service life and cost savings.
Leaking piping is expensive and occurs in 50% of fluid, gas, and liquid systems. Traditional pipe connections are guaranteed a certain percentage of leaks; this is outlined in their usage. The joints and connections of poly tubes use heat fusion that produces a tight, permanent, and durable leak free seal.
In the 21st Century, eco friendliness has become a major concern for industries, businesses, and manufacturers. It is used as a selling point and has become a primary concern when developing and marketing new products.
Poly tubing takes less energy to produce, is easy to transport, does not require fittings to be joined, does not emit toxins during processing, and can be recycled multiple times for use in other applications. Essentially, it is the perfect solution for tubing and piping applications.
In modern business, the one determining factor that serves as a major factor in a buying decision is cost. It is for this reason that poly tubing has been a go to material. Although copper, stainless steel, and aluminum have many positive properties, they are unable to match the per foot cost of poly tubing, which ranges between $0.40 per foot up to $0.70 per foot depending on the type and quality of tubing.
Poly tubing, and its many benefits, has become an essential and necessary part of modern manufacturing with qualities, properties, and abilities that far exceed other forms of building materials at a far lower cost.
Nylon tubing, also known as polyamide tubing, is a type of tubing made from polyamide resin, which has a strong resistance to abrasion. It is used in high-pressure and high-temperature applications...
Plastic tubing is a form of tubing that is manufactured from a mixture of a polymer with a variety of chemicals to form a material that can be solid or flexible. Since its first use in the 1950‘s, plastic tubing has revolutionized industrial processes and has found a use in a wide variety of applications...
PVC is a tough chemically resistant synthetic polymer of vinyl chloride used especially for making pipes, films and electrical insulation. It is made by polymerizing vinyl chloride, and...
Silicone tubing is a very tough elastomer that exhibits high strength, flexibility, and resistance. Silicone tubing can be stretched without tearing and is highly versatile. It cannot be weakened with repeated bending and twisting due to...
Plastic channels are plastic products that have linear extruded profiles. They have a constant cross-sectional shape across their axis. They are long and narrow structures, and their depth is relatively short. These products serve a variety of functions and uses...
Plastic extrusion, also known as plasticating extrusion, is a continuous high volume manufacturing process in which a thermoplastic material -- in a form of powder, pellets or granulates -- is homogeneously melted and then forced out of the shaping die by means of pressure...
Plastic materials are objects artificially made from organic compounds called polymers along with other additive components. They possess excellent formability, making them extremely versatile for many different fabrication and manufacturing processes...
A plastic tank is a large capacity liquid or granular storage unit that can be vertical, horizontal, below or above ground, as well as movable. They are designed to hold several gallons of a variety of substances for long periods without experiencing wear, weathering, or deterioration...
A plastic rod is a solid plastic shape made by the process of plastic extrusion or plastic co-extrusion. These have a contrast of plastic tubing and hollow plastic profiles. Plastic rods are found in various industries, including...
Plastic trim products are extruded linear profiles that can be made to any length. Because of its ability to attach, hold, and seal, plastic trim has many applications. Plastic, HDPE, LDPE, butyrate, PVC, acrylic, and...
A plastic water tank is a large capacity container designed to store water for household, agricultural, irrigation, and industrial manufacturing use. There are various types of water tanks produced to meet the needs of specific applications, with...
A poly tank is a plastic storage tank used to store, transport, and collect water, other liquids, and granular or powder materials. They are made of polyethylene or polypropylene and are a cost effective, lightweight, and easy to handle...
A coupling is a device that is used to transmit power between two shafts connected together at their ends. Couplings serve one primary purpose: to join two pieces of rotating equipment together, while...