Nylon Tubing
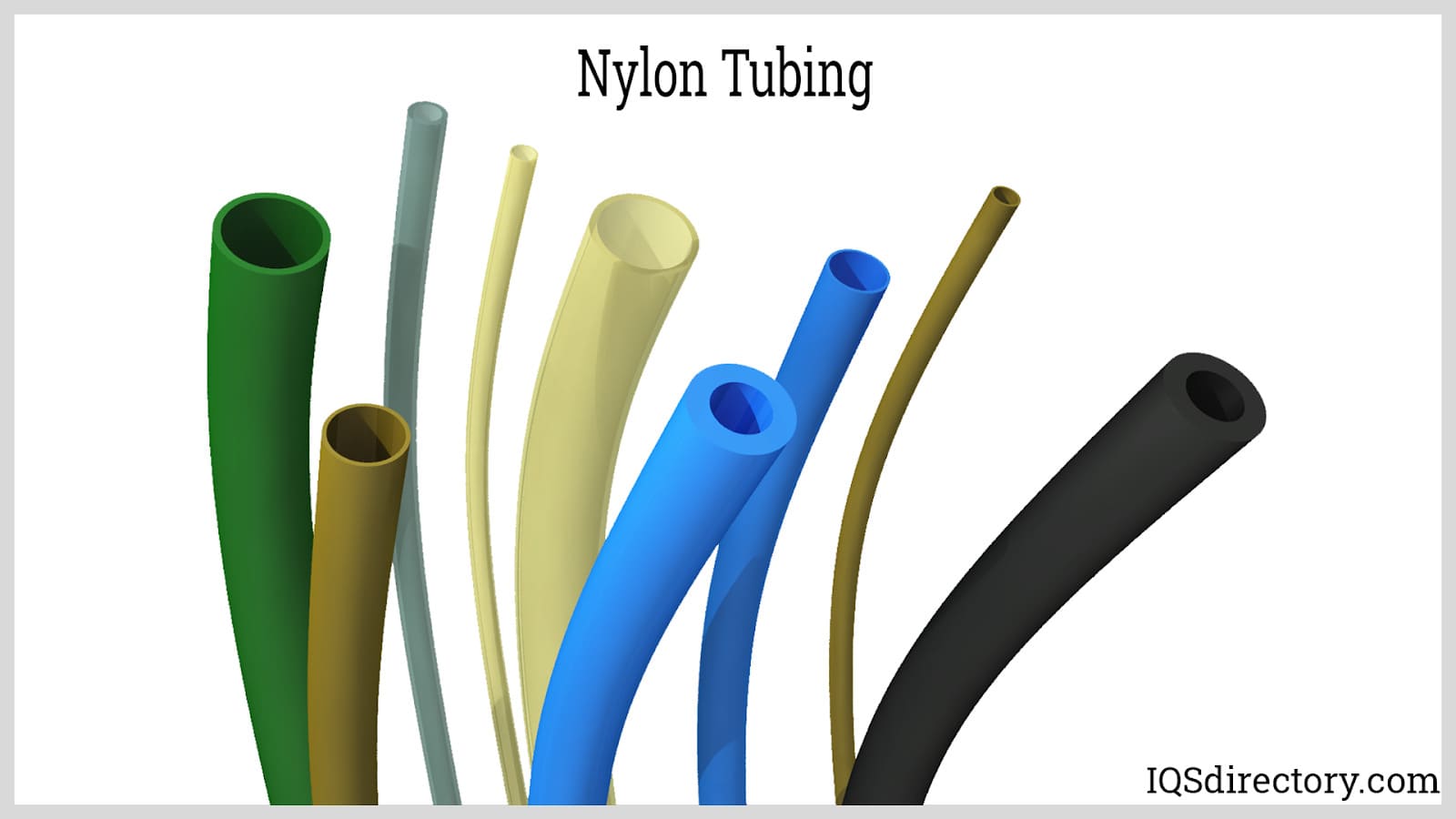
Nylon tubing, also known as polyamide tubing, is a type of tubing made from polyamide resin, which has a strongresistance to abrasion. It is used in high-pressure and high-temperature applications...
Please fill out the following form to submit a Request for Quote to any of the following companies listed on
Here is everything you need to know about the manufacture of plastic tubing and its use.
You will learn:
Plastic tubing is a form of tubing manufactured from a mixture of a polymer and a variety of chemicals to form a material that can be solid or flexible. Since its first use in the 1950‘s, plastic tubing has revolutionized industrial processes and has found a use in a wide variety of applications.
Plastic tubing is popular is due to its adaptability and flexibility. It is produced in a wide variety of wall thicknesses, diameters, tolerances, and strengths using a combination of materials to specially fit many applications.
The flexibility, durability, and adaptability of plastic tubing make it applicable for industrial applications that require long wear and endurance as well as commercial use in consumer products and homes. The main benefit of plastic over steel, aluminum, or other materials is its strength, light weight, and cost-effectiveness since it is far less expensive to produce.
Pneumatic tubing is flexible and capable of handling the compression of a pneumatic system. It is ideal for outdoor applications since it can endure temperatures ranging from -4° F to 140° F (-20° C to -60° C), which makes it useful in any environment or situation. In general use, plastic pneumatic tubing can withstand 115 PSI at 68° F (20° C).
Clear plastic mailing tubes are used as a method for deliveringliterature, samples, and promotional materials. They have heavy, thick walls designed to endure the rugged handling of the mail service and come in a wide variety of lengths and diameters.
Banking makes use of plastic tubing in two ways. The long tubes that reach from the teller to the customer are made of thick-walled, sturdy plastic. The carriers that carry the customer‘s transaction through the tubes are also made of sturdy thick-walled plastic.
Plastic tubing for farming is used for water systems since it is simple to install, durable, long-lasting, and does not corrode or rust. The quality that makes them the most useful for farming is that they can run for hundreds of feet without the need for joints or connectors.
Several types of plastic tubing are used to move liquids. In the case of drinking beverages, plastic tubing must be Food and Drug Administration (FDA) grade and meet the standards for pressure, temperature, and cleanliness. Plastic tubing for liquids is made from silicone, polyurethane, polyethylene, nylon, or PVC.
Plastic is a major part of the construction of automotive parts. Plastic tubing is used for fuel lines and fuel fillers for its flexibility and endurance.
As with automobiles, many of the parts on marine equipment include plastic parts. One of the components of a boat is its bilge pump tubing, which can be made of PVC for its abrasion resistance and flexibility. The heavy-duty qualities of PVC tubing make it chemical and oil-resistant.
Medical tubing is used to deliver fluids to and from the body and is made from small, complex custom plastic extrusions. It has to be produced in an isolated environment, away from any possibility of contamination. Medical grade tubing is manufactured with single, dual, or triple lumens and cut to lengths or made into reels.
Peristaltic, or roller pumps, are designed to move liquids through flexible plastic tubing. A rotor with wipers attached to its circumference turns and squeezes the tubing, which moves a liquid at an even rate.
The two methods for the manufacture of plastic tubing are extrusion and pultrusion. The difference between the two methods is how the molten plastic moves through the die. With extrusion, the molten plastic is pushed through the die, while with pultrusion, it is pulled through.
There are several steps to the extrusion process. The main ingredient is a polymer resin, which is referred to as nurdles, pellets, granules, flakes, or powder, that is fed into a hopper mounted on the extruder‘s barrel. The resin descends through the feed throat of the hopper into the barrel that has a screw that moves the resin toward the die. During its movement down the barrel, pushed along by the screw, the resin is slowly heated to melting temperature. Extrusion uses highly technical equipment to control the temperature, speed, force, tension, and time of the process.
Flexible and rigid tubing is formed using the extrusion process. In coextrusion, two or more materials can be combined to form tubing with a rigid core and flexible exterior.
Modern extrusion is monitored by computerized equipment to ensure the final cross section perfectly matches the engineered profile.
Pultrusion, like extrusion, is a continuous feed process used to produce a tubing profile. Unlike extrusion, pultrusion pulls reinforced fibers that have been wetted in a thermoplastic resin through a die. Polymerization happens as the fibers go through the die.
Pultrusion is a low-maintenance and, efficient method for producing plastic tubing that is corrosion resistant as well and has thermal conductivity.
Acrylic tubing is clear, impact and UV-resistant, and half the weight of glass. It is used in a wide variety of applications from lighting to various industrial processes.
PVC tubing is chemical, corrosion, abrasion, and wear-resistant with excellent flexibility. It is used in several industrial applications.
The main difference between CPVC and PVC is CPVC‘s higher corrosion resistance at higher temperatures.
Fiberglass plastic tubing is pultruded and is a combination of fiberglass and thermoset polyester or vinyl. It comes in hundreds of shapes and is corrosion and UV ray resistant. Fiberglass tubing is used as an electrical insulator and has dimensional stability.
Nylon tubing is lightweight and has corrosion and abrasion resistance, which makes it useful for a variety of industrial applications. It has excellent elastic memory that makes it capable of being flexed multiple times over long periods without exhibiting fatigue or fracturing. Nylon tubing is impact-resistant, even at below freezing temperatures and has very low moisture absorption.
Polycarbonate tubing is capable of withstanding harsh environments. It is lightweight and strong but also flame and impact resistant. Polycarbonate tubing can be machined and drilled without cracking.
Polyethylene tubing has a waxy, tough texture and is used for its resistance to erosion from water and chemicals. It has a very high resistance to cracking under stressful environmental conditions.
Polystyrene tubing is lightweight, flexible, and durable, which makes it useful for safely transporting fluids and gasses. It has excellent vapor and moisture resistance and comes in burst prevention rates to meet heat resistance standards.
Silicone tubing is popular in medical applications due to its cleanliness and non-toxicity. It has a similar elasticity to rubber tubing and is therefore flexible in its usage. Silicone tubing is rated by the NSF at food grade temperatures and can operate in temperatures between -100°F and 500°F (-73°C to -260°C).
The most common form of vinyl tubing is PVC, which is polyvinyl chloride. Vinyl tubing is resistant to chemicals, lightweight, exceptionally strong, non-toxic, and transparent, with a high melting point.
Polypropylene tubing is very similar to polyethylene but is more rigid, has a higher melting point, can be made optically clear, and is puncture and chemical-resistant. It can be used in environments with temperatures that range from freezing to 275°F (135 °C).
High-density polyethylene tubing has an exceptional strength-to-density ratio with a low risk of shattering, corrosion, and other malfunctions or failures. It is used for the transfer of water, air, and chemicals. HDPE can be sterilized by boiling, and it can withstand high pressure and resist abrasion.
PTFE tubes are flexible and able to withstand temperatures that range between -390°F to 500°F (-234°C to -260°C), as well as being resistant to corrosive liquids and gases. One of its main features is that it will not crack when in high-temperature environments. It is commonly found in laboratories and chemical operations.
EVA tubing is flexible, impact resistant, able to withstand very low temperatures, and resistant to grease, oil, and UV rays. It is used in hospitals, surgical situations, and the pharmaceutical industry. The temperature range for EVA tubing is between -76°F and 140°F (-60°C to -80°C) and meets FDA standards.
Polyurethane tubing is resistant to abrasion but is flexible, and kink-resistant with excellent memory qualities. It easily stretches and flexes but returns to its original shape. PU tubing is used in high pressure and medical situations or where flexibility is important. Its resistance to gasoline, oils, and other petrochemicals has made it a choice for fuel lines or other similar applications.
There are many machines available to produce plastic tubing in the United States and Canada. These machines are important in today's society as they play a critical role in the manufacturing industry, enabling the efficient production of plastic tubing used in various applications such as irrigation parts , medical devices, automotive components, and more. We discuss many of these leading machines below.
Features/Characteristics: Davis-Standard's Thermatic® series extruders are renowned for their versatility, allowing manufacturers to produce a wide range of plastic tubing with different sizes, shapes, and materials. These extruders are designed to offer excellent process control, uniformity, and high output rates, making them popular choices for various industries.
Features/Characteristics: Milacron's TP series extrusion machines are known for their efficiency and precision in plastic tubing production. They come equipped with advanced controls and automation systems, enabling easy adjustments and optimization of the extrusion process. The TP series is favored for its high throughput, reliability, and ease of maintenance.
Features/Characteristics: Conair's MedLine® extruders are specifically designed for medical tubing applications, making them popular in the healthcare industry. These machines offer exceptional quality control and cleanliness to meet stringent medical standards. They are equipped with features that minimize contamination risks during production.
Features/Characteristics: Arburg's ALLROUNDER series injection molding machines are known for their precision and versatility. While typically associated with injection molding, some models within this series are capable of producing plastic tubing through a process known as "tube molding" or "pipe molding." These machines offer high repeatability and allow for mass production of intricate tubing designs.
Features/Characteristics: Wilmington Machinery's Series III blow molding machines are popular choices for producing hollow plastic tubing, such as bottles and containers. These machines are designed to deliver consistent wall thickness, excellent dimensional control, and fast cycle times, making them suitable for high-volume production.
It's important to note that advancements in technology and industry trends may have led to the introduction of newer and more advanced machines since this posting. Therefore, it is recommended that you check with manufacturers, suppliers, and industry experts for the latest information on leading machines used for plastic tubing production in the United States and Canada.
With the wide variety of materials and applications for plastic tubing, producing tubing to fit a specific application requires a close examination of the qualities required. Since plastic is such a resilient material, it is easy to decide to use it as a component. The difficulty arises when deciding on the necessary features.
Measuring the mechanical properties of a material, and its tensile strength, is the first determination for choosing a material. Tensile strength is the amount of stress plastic can endure before breaking. The tensile strength of plastic varies from 12,400 psi to over 20,000 psi. The chart below has a list of a wide variety of plastics and their megapascal tensile strength at 73°F (23°C).
Tubing is measured by the inside diameter (ID) and outside diameter (OD), which can vary between 0.125" to 4" in (0.3 to 10 cm). The measurement between the ID and OD is the wall, a means for determining the strength of the tubing.
The wall thickness is determined by subtracting the ID from the OD (OD) and dividing the answer by two.
The flexibility of plastic tubing is determined by the material used to manufacture it. PVC, polyurethane, and silicone are flexible materials, with silicone being the most flexible.
There are a variety of fittings for plastic tubing that include compression, push to connect, quick turn, threaded, barbed, socket, and flanged. Determining the type of fitting should be in accordance with how the tubing will be used.
There is a limitless number of colors used to make plastic tubing, which also includes translucent and clear.
Plastic tubing can be made to any length, depending on the needs of the application. It can be a few inches up to hundreds of feet.
When examining the cost of plastic tubing and comparing it to steel or stainless steel, for tensile strength, steel, and stainless steel are far stronger. The biggest difference between plastic and steel is cost. For the cost of producing a half dozen stainless steel tubes, hundreds of flexible plastic tubes can be made.
The durability and strength of plastic depend on wall thickness and resin blend. The strength of plastic tubing is proportional to the amount of stress it will endure. Plastic can take a great deal of abuse before it gives out.
All plastic is corrosion resistant. The type of polymer used determines the amount of corrosion resistance. The types of the most corrosion resistant-plastics are polyolefins and PVC. Polyolefins are polyethylene and polypropylene, which come in various densities and molecular structures for ease of design.
The resin for plastic tubing can be manufactured with antimicrobial properties included in the pellets. Plastic tubing with antimicrobial properties is required for food storage, coolers, water tubes, and medical tubing. The antimicrobial additive prevents contamination and keeps the tubing sanitized.
Plastic products have the potential to be toxic. The amount of toxicity depends on the type of plastic resin used in the manufacturing process. When making the decision to produce plastic tubing, considering the toxic naturity of the materials should be part of the design process.
The characteristics of plastic tubing vary depending on the materials, configuration, and production methods used in its manufacturing. Surgical and industrial tubing widely vary in their application. Though there may be radical differences between functions, all plastic tubing has certain common features.
Plastic tubing is a hollow shaft of plastic designed to transport gas, fluids, or some form of solid, flaky material. Though circular is the most common form of a plastic tubing profile, it can come in other shapes, such as hollow tubing.
As the name implies, all plastic tubing is made of one of the many forms of plastic, which begins with a polymer. It is chosen as the base material for its strength, endurance, corrosion and rust resistance, and cost.
The strength, endurance, and transparency of plastic tubing vary according to the materials used to produce it. Regardless of those distinctions, it is one of the most-used components in manufacturing due to its low cost and versatility.
Plastic tubing can be produced with the same clarity as glass but without being as fragile or breakable with greater strength and endurance.
Plastic tubing can be manufactured to withstand any conditions or materials. Unlike other tubing types, plastic tubing does not have to be specially treated to move chemicals or corrosive substances.
Though plastic does not have the tensile strength of steel or stainless steel, it is more capable of withstanding the strain of daily wear. It is able to take significant harm and damage and still maintain its strength.
All plastics can be reprocessed and reused for the manufacturing of other products. Once plastic tubing has reached the end of its usefulness, it can be sent back to be repurposed and remanufactured as pellets or resin and sent through extrusion a second time.
The number of materials used to manufacture plastic tubing is matched by the number of types of plastic tubing, which ranges from highly sanitary tubes used in cleanrooms and surgery to drainage tubes for sewage and waste removal. Plastic tubing is engineered and designed to fit specific applications and can be formed, shaped, and configured for any number of conditions.
Corrugated tubing is used for chemical processing, in corrosive environments, in laboratories, and for high purity fluid and solvent transfer. It is very flexible and can be extended or compressed without affecting the ID. Corrugated plastic tubing can be produced in any length in a variety of ID‘s.
Heat shrinkable tubing is used as insulation for wiring. It is placed around the wire and then shrunk to fit snugly. It is resistant to fuels, lubricants, acids, and solvents at high temperatures.
Medical plastic tubing is manufactured to the exacting standards of the United States Pharmacopeia (USP) and the National Sanitation Foundation (NSF). USP Class VI defines the requirements for biological reactivity, while NSF 51 outlines the use of plastics with food products. Medical tubing has to be translucent, able to be sterilized and reusable, and nonreactive with bodily fluids or tissues.
Square plastic tubing has limited use and is sometimes used for its appearance. It has the same functions as cylindrical tubing and is able to transport liquids and gases. Due to its strength, it is included in the production of lawn furniture.
Hard or rigid plastic tubing is made from all the different types of fabricating materials. It is used as a conduit or as construction material and has multiple industrial applications.
Small diameter tubing, also known as miniature tubing, is used in applications that need regular tubing but of a smaller size. It is made from polycarbonate, polypropylene, polyethylene, polystyrene, and PVC, to name a few. It is used in electrical components, swab sticks, medical products, and dispensing tubes in various lengths.
Centrifuge plastic tubing is cylindrically shaped tubes that are placed in centrifuge slots to analyze and separate tested materials. They are high-strength, precision containers that can safely hold a wide variety of materials. Plastic centrifugal tubes are more commonly used due to their cost-effectiveness.
The regulations for the production of plastic tubing mainly pertain to its use in the food industry and the transport of water. Aside from governmental regulations, several other organizations monitor and develop specific guidelines for materials that come in contact with the public.
The FDA oversees any products that come in contact with food or beverages. Since plastic tubing is a major part of the food industry, the FDA has established regulations specifying cleanliness and sanitary standards for food processing plastic tubing. Materials used in plastic tube production are tested for composition, additives, and properties. If it meets the requirements, it is classified as FDA compliant. FDA CFR 21 is an all-encompassing regulation that includes requirements for materials used for medical purposes.
The USDA regulates equipment used in the production of meat and poultry products. The Food Safety and Inspection Service (FSIS), a department of the USDA, provides guidelines regarding several aspects of food production following FDA requirements listed in CFR 9.
The 3A-Dairy group is a voluntary organization that has the goal of improving the quality, standards, and equipment used in the production of dairy products. Its main focus is enhancing the sanitary conditions involved in production. The organization works with food handling manufacturers that are interested in improving their methods. It gives a 3-A Sanitary Standards, Inc. compliance seal to those who meet their requirements.
The NSF was founded to standardize sanitation and food safety requirements. It has over 80 requirements for public health and safety. It covers all sectors of food production. One of its critical areas for examination and testing is all equipment that comes in contact with drinking water, such as plumbing, water treatment chemicals, and water filters.
NSF Standards that relate to Plastic Tubing are:
The USP is a public standards authority for medicines and health care items. It sets standards for quality, purity, strength, and consistency. USP Class VI standards determine the toxicity of materials and their dangers to people. Any tubes that come in contact with body tissue or muscles are tested and graded. The USP uses a variety of tests to determine if a material meets its standards.
Nylon tubing, also known as polyamide tubing, is a type of tubing made from polyamide resin, which has a strongresistance to abrasion. It is used in high-pressure and high-temperature applications...
Poly tubing is a highly flexible, lightweight, and durable tubing that is produced from polyethylene, a polymer that is made from the polymerization of ethylene. It is a very versatile form of tubing that has break and crack resistant walls...
PVC is a tough chemically resistant synthetic polymer of vinyl chloride used especially for making pipes, films and electrical insulation. It is made by polymerizing vinyl chloride, and...
Silicone tubing is a very tough elastomer that exhibits high strength, flexibility, and resistance. Silicone tubing can be stretched without tearing and is highly versatile. It cannot be weakened with repeated bending and twisting due to...
Plastic channels are plastic products that have linear extruded profiles. They have a constant cross-sectional shape across their axis. They are long and narrow structures, and their depth is relatively short. These products serve a variety of functions and uses...
Plastic extrusion, also known as plasticating extrusion, is a continuous high volume manufacturing process in which a thermoplastic material -- in a form of powder, pellets or granulates -- is homogeneously melted and then forced out of the shaping die by means of pressure...
Plastic materials are objects artificially made from organic compounds called polymers along with other additive components. They possess excellent formability, making them extremely versatile for many different fabrication and manufacturing processes...
A plastic tank is a large capacity liquid or granular storage unit that can be vertical, horizontal, below or above ground, as well as movable. They are designed to hold several gallons of a variety of substances for long periods without experiencing wear, weathering, or deterioration...
A plastic rod is a solid plastic shape made by the process of plastic extrusion or plastic co-extrusion. These have a contrast of plastic tubing and hollow plastic profiles. Plastic rods are found in various industries, including...
Plastic trim products are extruded linear profiles that can be made to any length. Because of its ability to attach, hold, and seal, plastic trim has many applications. Plastic, HDPE, LDPE, butyrate, PVC, acrylic, and...
A plastic water tank is a large capacity container designed to store water for household, agricultural, irrigation, and industrial manufacturing use. There are various types of water tanks produced to meet the needs of specific applications, with...
A poly tank is a plastic storage tank used to store, transport, and collect water, other liquids, and granular or powder materials. They are made of polyethylene or polypropylene and are a cost effective, lightweight, and easy to handle...
A coupling is a device that is used to transmit power between two shafts connected together at their ends. Couplings serve one primary purpose: to join two pieces of rotating equipment together, while...