Nylon Tubing
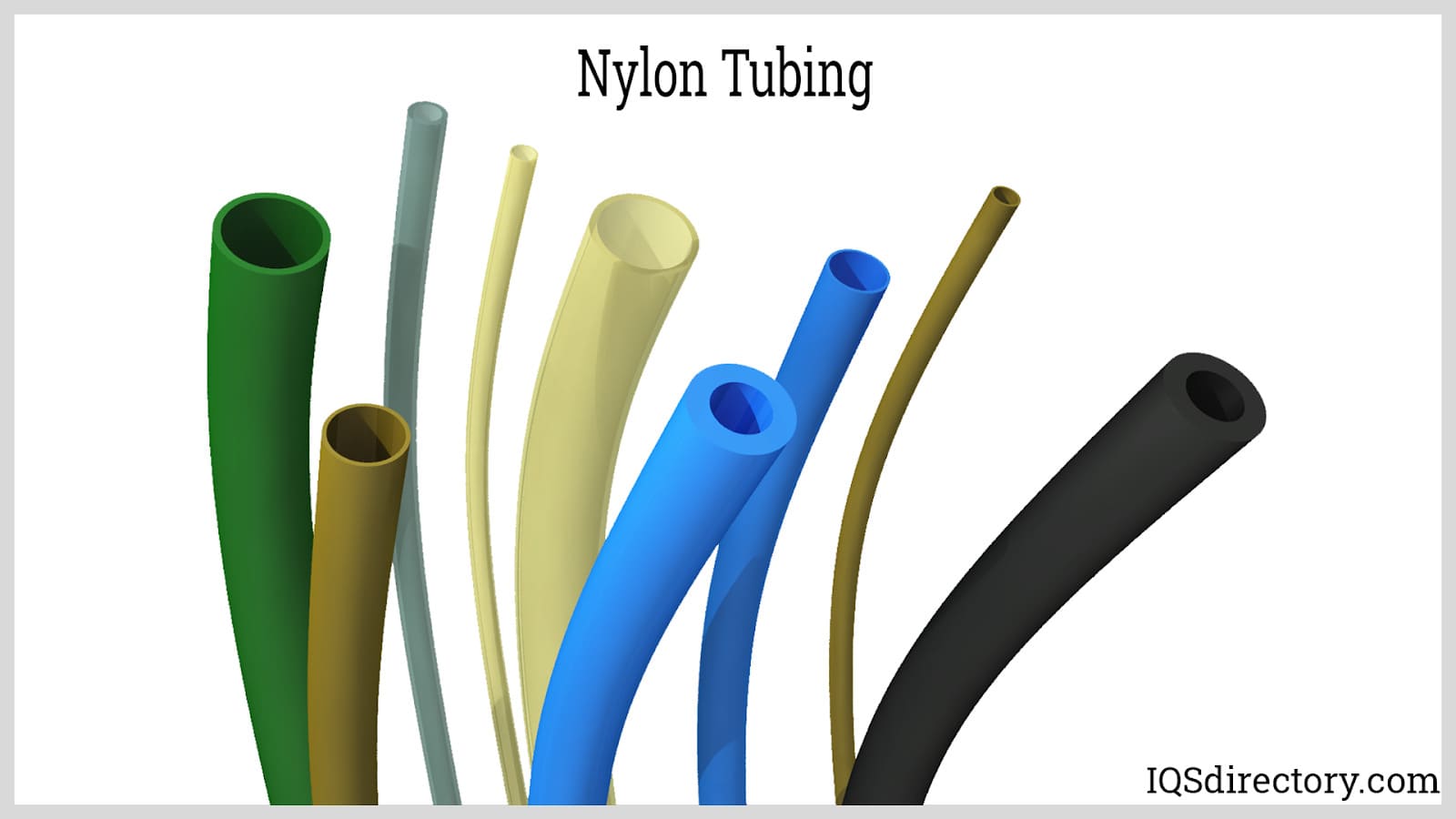
Nylon tubing, also known as polyamide tubing, is a type of tubing made from polyamide resin, which has a strong resistance to abrasion. It is used in high-pressure and high-temperature applications...
Please fill out the following form to submit a Request for Quote to any of the following companies listed on
This chapter will discuss what silicone tubing is, including its manufacturing process.
Silicone tubing is a tough elastomer with high strength, flexibility, and resistance. Silicone tubing can be stretched without tearing and is highly versatile. It cannot be weakened with repeated bending and twisting due to its significant flexibility. Because silicone tubing is very hygienic and non-toxic, it can be produced as a medical-grade material, making it a popular choice for healthcare and medical applications.
Silicone has properties that allow it to work well over a broad range of temperatures and adapt easily to sudden changes in weather and temperature. Silicone tubing has a major role in a variety of industries and applications involving the transfer of liquids and gasses. It has a fantastic range of properties that make it the preferred material for tubing in many situations.
Silicone exhibits excellent properties, including UV and heat resistance, making silicone tubes ideal for the electrical and aerospace industries. It is easy to clean and sterilize the material, making it ideal in environments that prioritize hygiene, such as medical and pharmaceutical industries and food production. Silicone tubing is available in different sizes and grades, such as high-temperature silicone tubing.
High-temperature silicone tubing can resist extreme variations in temperature, unlike plastic or rubber tubing. Food-grade silicone tubing is also a very reliable and FDA-compliant material that exhibits stability, temperature resistance, and non-stick properties. This, in turn, makes it ideal for the production of food and beverages. Medical-grade silicone tubing is another type that meets several requirements for cleanliness and non-toxicity that are necessary for the medical industry.
Silicone tubing is manufactured through a widely used method called the rubber extrusion process.
The extrusion process is preferred because it is cost-effective and can produce large batches of products in a very short lead time. This part-forming process is generally performed by rubber fabricators. The process is initiated when a heated and cured silicone-formulated compound is preformed into a slab or strip.
The next step is to feed the formed silicone into a screw extruder. The screw extruder forces the compound through the hardened steel die. The extruder head holds the die in place, and the die shapes the silicone tubing once the silicone has been forced through. The silicone profile then exits the die and is cured by being continuously pulled through a heated and cured oven.
Several ovens are used to circulate hot air vertically and horizontally: salt bath cures, steam vulcanization, and infrared cures. Some fabricators prefer to perform the vulcanization of the silicone after it has been extruded into a long trough filled with salt water. However, this technique has the main challenge of choosing the right raw materials that are capable of performing best in their specific temperature and mechanically controlled processes and will enable the final products to meet specifications.
The difference between these two processes starts from the shape of the product, application field, and production direction. The extrusion process produces regular round shapes in any number of lengths, while the molding process is capable of producing irregular shapes in restricted lengths.
With the extrusion process, after passing over a length greater than 50 feet, the vulcanization of the tunnel used for drying must be re-sulfurized. Theoretically, the silicone tubing of the extrusion process is infinitely long without having a stop at the inlet. The other process used is the solid-liquid injection process, which utilizes liquid glue production. This method of production is a bit similar to plastic injection. It is initiated by injecting the liquid glue into the mold after high-temperature sulfurization.
Next, the liquid glue is de-molded. This solid-liquid injection process exhibits a rich product structure. Since the products are produced by liquid glue, their hardness is much lower than that of the products formed by the silicone tubing extrusion. Solid-liquid injection silicone tubing is very soft and smooth compared to extruded silicone tubing. Solid and liquid injection silicone tubing is mostly used in the power industry.
Silicone has good properties of resistance and insulation, which is why it is preferred in the power industry. The solid-liquid injection produces fixed and irregular shapes, while the extrusion process produces long round tubes. Both methods can withstand ultra-high voltage characteristics and are used in power transmission lines and terminals.
The silicone tubing extrusion process is mostly utilized in the medical field for cooperation with the solid-liquid injection process. The extrusion process is mostly responsible for producing drainage pipes. The liquid injection process mainly functions to produce irregular pipes. The extrusion process produces regular pipes, but the raw materials of the liquid process and the cost of all aspects of the equipment will be more than the cost of the extrusion process. Therefore, when producing regular pipelines, the lower-cost extrusion process can be utilized.
The size of a silicone tube determines its use. For example, small silicone tubing is commonly used for electrical sleeving because of its thin walls and flexibility. Medium-sized silicone tubing is utilized for carrying liquids and powders. Finally, large silicone tubing is mostly utilized in applications involving air ducts and dielectrics.
Medium silicone tubing is often employed in the pharmaceutical and food industries, mainly in applications where hygiene is critical. Platinum silicone tubing is a common all-rounder tubing free of ketones and peroxide. This makes it ideal for the medical, food, dairy, and vending industries. This type of silicone tubing ensures taste preservation and does not taint the product it carries. Cured silicone tubing is also utilized as a general-purpose tubing that can be used with food.
The different types of silicone tubing include:
Silicone peroxide tubing is available in a translucent format in different diameters. This type of silicone tubing mostly suits applications that do not require high purity, repeated sterilization, and critical dosing. Silicone peroxide tubing is most commonly used for different pump and transfer applications.
These applications include automotive and industrial applications. This product can withstand temperatures as high as 392°F (200°C). In addition, peroxide-cured silicone tubing is more cost-effective than many other compounds. This makes it most suitable for general tubing applications.
Platinum-cured silicone tubing has many advantages over peroxide-cured silicone tubing. These advantages make it very popular in the food and beverage industries. This type of silicone tubing exhibits a high tear strength. It can operate in a broad range of temperatures ranging from -40°F (-40°C) to 392°F (200°C). This enables the use of this product in many different applications and environments without deterioration.
Platinum-cured silicone tubing contains no peroxide by-products, is non-yellowing, and is translucent, black, or white. This type of silicone tubing is most suitable for use in peristaltic pumps. It also has a long life expectancy, which makes it suitable for this application compared to other products. Platinum-cured silicone tubing can be used in hot or cold water applications. It is predominant in the non-invasive medical and pharmaceutical industries.
As suggested by the name, this type of silicone tubing is specifically designed and manufactured for use in the dairy industry. This is because of the product’s high mechanical wear and tear strength properties. In addition, most silicone dairy tubes are platinum-cured, bringing many benefits to this tubing over other tubing products. For example, silicone dairy tubing is non-yellowing and does not contain any peroxide by-products.
This tubing does not harden or corrode after long periods of use. It also features an extra-smooth inner bore for improving flow rate and hygiene levels.
Silicone fuel tubing is most commonly utilized in the radio-controlled model car industry. This type of silicone tubing exhibits high resistance to methanol and nitro fuels, keeping the fuel cleaner and reducing the tubing’s deterioration. This tubing is found in many different aesthetically pleasing colors to match any car color. It must be noted that silicone fuel tubing is designed to be used with radio-controlled model cars and is not ideal for use with petrol.
High-temperature silicone tubing is resistant to extreme temperature variations. The name of a silicone hose is typically followed by a number, like 550. This number indicates the hose's absolute maximum point of heat tolerance. Choosing the appropriate high-temperature silicone hose will be simple if temperatures are anticipated properly.
High-temperature ducting products do require one point of distinction, though. A hose may be able to withstand very high temperatures, but this does not mean it won’t burn or catch fire. The difference between a product's thermal resistance and burn point is that the term "burn point" describes a substance's capacity to ignite when in contact with fire. It should be verified that the hose was manufactured following the requirements for flame retardant materials if you need a high-temperature duct that can withstand coming into contact with flames.
A high-temperature silicone hose may need to be flexible depending on the application's requirements. A high-temperature duct that can bend and flex in confined spaces is extremely useful. A silicone high-temperature hose is flexible but may eventually experience flex fatigue if continually bent. If the material is flexed in numerous ways, it may eventually rip. A high-temperature silicone hose will often maintain its straight shape unless manually bent.
A high-temperature silicone hose can resist harsh chemicals and temperatures. The silicone compound has the capacity to withstand chemical exposure. A silicone high-temperature hose can often withstand coming into contact with specific oils, solvents, and gasses. The best course of action is to confirm that a silicone hose is compatible with the chemicals used in the application.
For usage in food and beverage applications, food-grade silicone is a strong, long-lasting substance that offers a healthier, more inert substitute for plastics. The absence of plasticizers in silicone makes it much less likely for BPA and other dangerous chemicals to leak into food and beverages. It also stops flavors and aromas from transferring to the food or beverage it contacts. Silicone is a great material for food storage and transportation to combat single-use plastics since it is strong, non-porous, and temperature-tolerant.
This type of silicone tubing is reliable. Its advantages include stability, temperature resistance, and non-stick properties. This makes it most suitable for use in the food and beverage industries. Food-grade silicone tubing does not react with food ingredients and fluids and can be sterilized in standard autoclaves. It features surface qualities that resist the buildup of transported material on the inside.
Using food-grade silicone, building robust and long-lasting food-grade components is simple. Specific advantages of selecting food-grade silicone over other plastics include the following:
Specially designed medical-grade tubing meets the stringent standards for cleanliness and non-toxicity for medical devices. The United States Pharmacopeial Convention (USP) has developed a sequence of six tests that cites specific standards to be followed for the certification of medical devices. The first requirement that silicone tubing must adhere to is biocompatility, a necessity for medical tools, devices, and equipment that will come in contact with human tissue. In addition, USP Class VI specifies that silicone tubing resists adhesion and prevents bacterial growth.
Because of its flexibility and versatility, silicone tubing is the preferred solution for pharmaceutical, biotech, and medical treatments. It is a safe and economical solution with the purity and hygienic standards required for medical use.
The benefits of medical-grade silicone tubing include:
This type of silicone tubing meets many requirements for cleanliness and non-toxicity necessary for use in the medical field. It is sterile and non-reactive. Medical-grade silicone tubing also features compound compositions that make it completely non-toxic, odorless, and tasteless. It does not have any tendency to support the growth of bacteria. To make this type of silicone tubing pure, it is enhanced by processes like platinum curing before manufacture. Medical-grade silicone tubing does not react with sensitive drugs and body tissues.
Shear is a force that acts tangentially to a surface that it passes over and develops due to an increase in the velocity gradient of a fluid. Tangential force causes a fluid to move in layers at different velocities, a factor that causes resistance between the layers, exerts force on the cells moving through the tubing, and can damage or destroy the cells.
The force placed on the cells releases proteases, unprocessed product, host cell proteins, and DNA into the fluid, which reduces product quality, decreases yield, and can interfere with measuring equipment, each of which has to be limited. A method to reduce shear force is the use of fittings that can cause turbulence and backflow that will increase shear stress.
Overmolding is a production process for creating fittings with exceptionally smooth interiors that reduce turbulence and limit shear stress. Overmolded junctions are leak resistant, smooth flowing connections produced in Y’s, T’s, crosses, and reducers and are cell saving.
Barbed fittings slide easily into silicone tubing for making connections. Unfortunately, the construction of barbed fittings creates turbulence and backflow that can lead to shear stress. The result of the shear stress is entrapment that causes dead volume and incomplete product recovery.
Overmolded connectors provide a smooth seamless transition at junctions, have smooth continuous uninterrupted flow without entrapment and shear stress, and full product recovery.
This assortment of colored tubing has thick walls and is made of general-purpose silicone rubber, making it appropriate for usage at high vacuum levels. Colored silicone tubing is available in a wide variety of colors. Among other applications, it is used in the electrical industry for sleeving electrical cables.
This type of silicone tubing is suitable for use in applications that do not require high-pressure hoses or compound purity of a high level. In addition, because of its excellent thermal and flexibility properties, it can be utilized on most domestic appliances and hobby or workshop applications.
This chapter will discuss the applications and benefits of silicone tubing.
The applications of silicone tubing include:
Silicone tubing exhibits properties that make it useful in the medical field. It has already been seen that silicone tubing is very tough, easy to clean, and easy to sterilize. Because of these properties, it is valued by medical practitioners. However, one of the most important properties that silicone tubing exhibits from a medical standpoint is its biocompatibility. This means that it is neither harmful nor toxic to living tissues and is unlikely to yield an allergic response. This makes it a popular material for medical implants, drains, catheters, feeding tubes, and other medical products that have biocompatibility as a key requirement.
Silicone tubing is vital for these devices. It provides important sealing, gasketing, and safe fluid transfer properties that are not possible when most other materials are used. The medical sector utilizes silicone tubing that is usually of a higher grade. Its manufacture is performed using the continuous extrusion and vulcanization process. It is possible to produce very fine tubes often used for capillaries. Wider tubes that can be used to transport crucial fluids can also be produced.
Silicone tubing is highly regarded for use in analytical instrumentation because of the need for flexible and sterile equipment.
Silicone tubing is excellent for electrical insulation, making it suitable for use in electronics across several industries. It is mostly used for insulating electrical components in automotive enclosures.
Since silicone tubing is non-toxic and has a smooth inner and outer surface, it is utilized mostly in water filtration and purification systems.
Food-grade silicone tubing is optimal for dairy processing equipment, beverage dispensing, and other food industry applications requiring sterile and flexible materials with high chemical and heat tolerance.
In the aerospace industry, silicone tubing is extensively utilized in equipment like climate control and conveyance systems. Because silicone tubing has high tensile strength, flexibility, and temperature resistance, silicone tubing is also used for vacuum seals on vehicles and aircraft.
Other uses of silicone tubing are listed below:
The benefits of silicone tubing include:
Silicone tubing is highly flexible over a range of temperatures. Compared to some high-temperature rubber tubing, silicone tubing does not become soft when exposed to high temperatures or harden at low temperatures. This makes it ideal for use in extreme environments.
Silicone tubing has a broad temperature range, allowing it to withstand temperatures from -130°F to 600°F (-90 to 315.5°C). Silicone tubing is also resistant to UV radiation and ozone; therefore, it is less likely to degrade from exposure. This property makes silicone tubing ideal for outdoor use or aerospace applications.
Silicone tubing exhibits high tensile strength. Because of this quality, its wear, tear, and breakage are reduced. This makes it most suitable for high-traffic industries like plumbing and food service. Silicone tubing has a long life expectancy because of its flexibility and toughness. It does not easily crack or break because it has good elongation at break and tensile strength. This allows it to withstand the daily stressors of a brewery, dairy farm, water treatment plant, milking parlor, or aquarium.
Silicone tubing has many color options available and can be color matched.
Food and medical-grade silicone tubing have a smooth inner and outer surface finish, making them suitable for applications where a smooth, sterile surface is required. This surface helps to prevent contamination like that found in food service, medical, and analytical instrumentation industries.
Silicone tubing exhibits excellent properties, including extreme durability, resilience, and resistance against repeated compression cycles.
Silicone tubing is resistant to surface penetration or hardness ranging from 20 Shore A to 90 Shore A.
Silicone tubing is pliable, allowing it to be utilized in confined or high-pressure applications where a more rigid rubber material would break or tear. In addition, silicone tubing allows easier monitoring and controlling of fluid flow.
Silicone tubing can withstand ultraviolet radiation (UV) and impede pathogen growth. This, in turn, makes it ideal for use in food processing, pharmaceutical, and medical industries. Additionally, silicone tubing is hygienic and sterile. It does not bolster the growth of bacteria or any solid buildup. Silicone tubing also offers good resistance to ozone and weather. Finally, it offers protection against salt water, cleanser, synthetic concoctions, and different chemicals.
Silicone tubing can be manufactured in various sizes and lengths.
Silicone tubing is easy to clean with little effort. It does not become fragile, brittle, or stiffened even after repeated use of chemicals.
Silicone tubing does not interact with what it carries. This makes it appropriate for food, water, air, and beverage applications because it does not tarnish the nature and quality of the products being handled.
Despite all of these advantages, It is not recommended to use silicone tubing for transporting concentrated fuels or oils since these materials are capable of breaking down the structure of the tubing.
This chapter will discuss how to clean, sterilize, and join silicone tubing.
Regular line cleaning is crucial if silicone tubing is used in a food production area like a homebrew setup or a soft drink dispensing machine. Silicone tubing is easy to clean and is ideal for home brewing setups since it can be boiled to clean off all the gunk inside the hoses. This cleaning method must be performed regularly to prevent buildup, blockages, or unsavory smells.
When silicone tubing is used in other applications like the automotive industry, cleaning the pipe's interior may not be regularly required or necessary. One of the easiest ways to clean silicone tubing is to use hot soapy water to wipe down or push through the tubes.
Since silicone is highly resistant to heat, it does not matter how hot the water is. However, if certain cleaning products are used on silicone tubing, they will react negatively, causing damage and discoloration. Therefore, avoid using WD40 or petroleum-based cleaning products when cleaning silicone tubing.
Silicone tubing is utilized in a variety of medical instruments and equipment because it is easy to sterilize. Several sterilization methods that can be normally carried out in a medical laboratory are available. The first and most widely used method of silicone tubing sterilization is called gamma irradiation. However, this technique may change the properties of the silicone and result in a higher propensity for the silicone material to kink. Another alternative to gamma irradiation is called electron beam irradiation, which has similar physical effects.
The third method of silicone tubing sterilization is called ethylene oxide. It is an effective sterilization method because the silicone tubing absorbs the ethylene oxide, but the ethylene must be removed before the machine’s use.
The methods of joining silicone tubing include:
IPA is used to lubricate the silicone so that it will slide over a barbed fitting. IPA absorbs water and is, therefore, inherently hygroscopic. IPA is used in its pure form when used with silicone tubing. It is easy to obtain and is relatively cost-effective.
IPA is also effective in that it evaporates without leaving a residue on medical devices. Its main disadvantage is that it takes longer to dry. This can make the process time-consuming, thus slowing down the production rate and costing the manufacturer more time and money. Other techniques, like applying low temperature to the silicone tubing, assist in speeding up the drying process.
Another method of joining silicone tubing is to use silicone oil-based lubricants. This method is most commonly used by engineers; it is intuitive since using silicone fluid to join silicone ensures the materials’ compatibility. However, silicone oil has some major disadvantages.
The first disadvantage is that its application can be very messy due to the nature of the oil, which never evaporates and is engineered to stay on a surface indefinitely. Silicone tends to migrate to other surfaces easily; therefore, if a manufacturer only needs to coat a specific part of a device, it is hard to contain the fluid during coating. This, in turn, will make the coating and joining process time-consuming since more cleanup is required once the part is joined.
The risk of contamination is also increased during the coating process since the oil can attract and capture dust and dirt in the surrounding environment. Even if a clean room is used, there is an increased chance of contamination. Furthermore, medical-grade silicone costs more than other lower grades used in other industries.
The process of silicone swelling can be likened to when a sponge absorbs water. The silicone tubing swells in size like a sponge when it starts absorbing the solvent, then shrinks. After shrinking, it will recover its original dimensions once the solvent has evaporated. This results in a tight-seal attachment to the metal part or barbed fitting. Silicone swelling makes attaching silicone tubes or parts with barbed fittings quick and simple.
Since the silicone only needs an increase in size by 1 to 2% in many cases, the complete swelling process can occur in less than a minute. First, the silicone end to be connected to the barbed fitting is dipped into a vessel of the swelling agent. The swelling of the submerged tube or part starts almost immediately. The time the tubing remains in the solution determines how much it will swell. This can be accurately timed in high-volume operations to ensure maximum efficiency.
The swelling solvent immediately starts to evaporate once the part has been removed from the fluid. As the swelling solvent evaporates, the part recovers its original state. Compared with other methods, the whole silicone swelling process – both the swelling of the silicone and the recovery of the silicone back to its original size – can be very quick.
With barbed fittings, barb serrations or ridges grip the interior wall of the connecting tubing and form a tightly sealed surface without damaging the wall of the tubing. Barbed fittings, often called hose barbs or hose barbed connectors, are commonly used because they are easy to install.
The tight seal of barbed connectors makes them useful for low-pressure applications of 200 psi or lower for fluids, gas, and airflow. The seal of the connection depends on the interaction between the surface of the connector and the tubing wall.
Push-to-connect fittings are similar to barb fittings without barbs or ridges. They involve the use of a specially shaped connector. The tubing is pushed into the connector with a securing ring that holds the tubing in place. For the tubing to fit properly, it has to be cut into a 90o cleanly cut end with uniformity and evenness. The gripper ring in the connector holds the tubing in place and makes it possible to easily remove the tube when necessary.
PFA compression fittings are similar to push-to-connect fittings but have a mechanism that forms a tighter and more secure connection. They are made from PFA fluoropolymer and are designed for rigid and semi-rigid tubing. PFA compression fittings are multi-component fittings that squeeze the outer diameter of the tubing to form a tight, secure connection.
Unlike a barb fitting, a compression fitting works on the outside of the tubing, which requires that the wall of the tubing be sturdy enough to withstand the applied pressure. The four parts of the fitting are the body, the ferrule, the gripper, and the nut. As with a push-to-connect fitting, the tubing must be cut cleanly at a 90o angle to fit smoothly.
Once the tubing is properly prepared, the nut is slid onto the tubing. The gripper is placed over the tubing and inside the nut, with its smaller end facing it. The ferrule is also placed in the nut, with its larger end facing the gripper. After the nut, gripper, and ferrule are placed over the tubing, the body of the fitting is forced over the tubing toward the nut as far as it will go.
With all the components placed on the tubing, the body of the fitting is threaded onto the nut and carefully tightened with a wrench. The delicacy of a compression fitting necessitates that it be tightened with care to avoid over-tightening that can deform the fitting.
Compression fittings come in a wide assortment of forms, including Ts and elbows, which makes them applicable for a variety of applications. They are more expensive than other types of fittings but are necessary for high-pressure applications.
As mentioned above, silicone tubing is a tough elastomer that exhibits many good properties, including high resistance to temperature ranges, high flexibility, good wear and tear resistance, and resistance to UV and ozone. These benefits make silicone tubing a popular choice in a variety of applications, such as in the medical and food industries. Its high flexibility and strength make it a better choice over other rubber materials that can be used in its place. One of the other benefits that make silicone tubing a popular choice in the medical field is that it is easy to clean. This can be easily done by boiling it to remove the dirt that builds up in the material. The flexibility and high tensile strength of silicone tubing make it suitable for various applications in the medical, automobile, dairy, food, beverage, and pharmaceutical industries. Because of the different grades in which silicone tubing is available, careful considerations must be made when opting for silicone tubing for a specific type of application.
Nylon tubing, also known as polyamide tubing, is a type of tubing made from polyamide resin, which has a strong resistance to abrasion. It is used in high-pressure and high-temperature applications...
Plastic tubing is a form of tubing that is manufactured from a mixture of a polymer with a variety of chemicals to form a material that can be solid or flexible. Since its first use in the 1950‘s, plastic tubing has revolutionized industrial processes and has found a use in a wide variety of applications...
Poly tubing is a highly flexible, lightweight, and durable tubing that is produced from polyethylene, a polymer that is made from the polymerization of ethylene. It is a very versatile form of tubing that has break and crack resistant walls...
PVC is a tough chemically resistant synthetic polymer of vinyl chloride used especially for making pipes, films and electrical insulation. It is made by polymerizing vinyl chloride, and...
Plastic channels are plastic products that have linear extruded profiles. They have a constant cross-sectional shape across their axis. They are long and narrow structures, and their depth is relatively short. These products serve a variety of functions and uses...
Plastic extrusion, also known as plasticating extrusion, is a continuous high volume manufacturing process in which a thermoplastic material -- in a form of powder, pellets or granulates -- is homogeneously melted and then forced out of the shaping die by means of pressure...
Plastic materials are objects artificially made from organic compounds called polymers along with other additive components. They possess excellent formability, making them extremely versatile for many different fabrication and manufacturing processes...
A plastic tank is a large capacity liquid or granular storage unit that can be vertical, horizontal, below or above ground, as well as movable. They are designed to hold several gallons of a variety of substances for long periods without experiencing wear, weathering, or deterioration...
A plastic rod is a solid plastic shape made by the process of plastic extrusion or plastic co-extrusion. These have a contrast of plastic tubing and hollow plastic profiles. Plastic rods are found in various industries, including...
Plastic trim products are extruded linear profiles that can be made to any length. Because of its ability to attach, hold, and seal, plastic trim has many applications. Plastic, HDPE, LDPE, butyrate, PVC, acrylic, and...
A plastic water tank is a large capacity container designed to store water for household, agricultural, irrigation, and industrial manufacturing use. There are various types of water tanks produced to meet the needs of specific applications, with...
A coupling is a device that is used to transmit power between two shafts connected together at their ends. Couplings serve one primary purpose: to join two pieces of rotating equipment together, while...
Silicone rubber molding is a method for shaping, forming, and fabricating silicone rubber parts and products using a heated mold. The process involves compressing or injecting silicone rubber into a mold...