Rubber Bushings
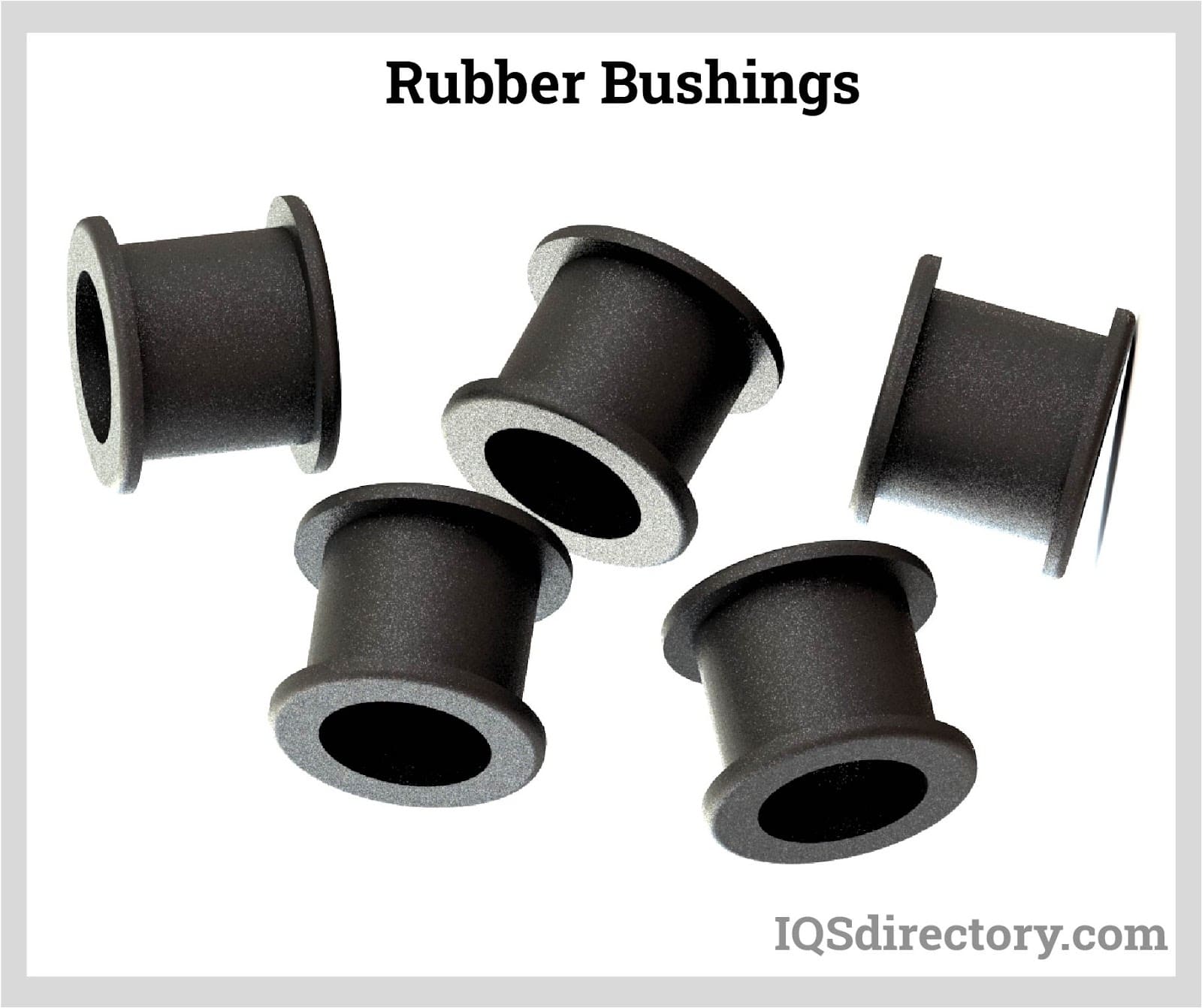
A rubber bushing is a form of vibration isolator that is placed between two parts to limit the motion between them and absorb, mollify, and buffer the energy produced by their interaction. They are very...
Please fill out the following form to submit a Request for Quote to any of the following companies listed on
This article takes an in-depth look at extruded rubber.
Read further to learn more about topics such as:
Extruded rubber is a group of products made by softening and pressurizing an elastomeric compound and forcing it to flow through a hard tool called a die. The resulting product is a continuous piece of material that has the same cross-section throughout its length. The shape of the cross-section depends on the die profile. Thousands of different die profiles are used by many industries, such as automotive, aerospace, electronics, building construction, consumer goods, and much more.
Rubber extrusion is a widely used process that creates uniform shapes and profiles with little to no waste at an economical cost. Products produced by rubber extrusion are durable, long-lasting, and resistant to the effects of chemicals, heat, cold, impact, and abrasion.
Extrusion is a popular process that was introduced in the 1930s for producing products with a continuous profile, such as rods, pipes, and tubes. It is a simple process that has been adapted to the manufacture of all sorts of materials that can be softened and extruded. Aside from rubbers, other materials that can be extruded are metals and plastics.
Rubber is an elastic material that can be transformed using different compounding ingredients. Like plastic, it is light, durable, and easily shaped using a profile die. Although processing and shaping rubber takes less energy, the final products have all of rubber’s beneficial properties. One of the main attractions of rubber is its low production cost regardless of the type of rubber being processed.
Plastic and rubber can be extruded together under a process referred to as co-extrusion, producing products that are rigid yet soft. The process of co-extrusion makes it possible to take advantage of the positive properties of both materials. Combining the two yields a more economical product that is readily available, high-quality, and versatile.
There are an endless number of benefits derived from the extrusion of rubber since it allows for the production of many products. Customers can choose products of different shapes, configurations, designs, and lengths that are produced efficiently with a limited amount of waste.
Quality – One of the main benefits of extruded rubber products is their quality due to their resistance to heat, cold, aging, friction, abrasion, and normal wear and tear.
Resistance – Extruded rubber is able to withstand the normal abuse that products endure during their use.
Cost Savings – One of the main reasons that extruded rubber is so widely used is its cost, which is due to the small amount of waste produced by the process.
Diversity – Rubber extrusion is capable of producing any form of product or design including special, unique, and unusual ones. There is an endless number of varieties, types, and shapes regardless of how different.
The rubber industry is currently dominated by tire production, which accounts for two-thirds of global demand. The balance is split between non-tire automotive applications, industrial, footwear, electrical, and others. Extruded rubber is used in the majority of non-tire automotive and industrial applications. Examples of extruded rubber products are detailed below.
Rubber Bushings: Extruded rubber bushings are used as shock absorbers in a working piece of equipment. They isolate moving parts from each other and prevent vibration and noise from being transferred throughout the equipment. They are commonly seen in automotive systems, particularly in suspension components.
Most rubber bushings are shaped as hollow cylinders, which can be easily produced from an extrusion process. It is cut to length according to the dimensions of the part or shaft where it goes into. Some rubber bushings are used as bare rubber only, while some are enclosed and bonded in metal casings or sleeves.
Rubber Trims: Rubber trims are extruded products that are used to protect the edges or surfaces of rigid objects from sudden impacts. Examples of such objects are panels, windows, doors, removable covers, and hatches. Aside from impact protection, they also provide an air-tight or water-tight seal between the mating parts.
There are thousands of rubber trims profiles available, and often, they are custom-made to suit a special application. One of the most common rubber trim shapes is a U-channel. The edge of the rigid part is inserted on the channel and is fixed into place by fasteners and adhesives.
Rubber Tubing, Hoses, and Piping: Tubes, hoses, and pipes, regardless of the material type, are produced by an extrusion process. They are used with hydraulic and pneumatic equipment with silicone tubing capable of being used to manufacture food and drugs.
Rubber’s excellent flexibility allows it to be bent into shape without incurring damage. This property makes these types of products desirable for connecting different parts of equipment for transferring fluids such as compressed air, oil, water, and chemicals.
Rubber Bumpers: Like rubber trims and rubber bushings, rubber bumpers take advantage of the material’s shock-absorbing capabilities. Aside from this property, the compounding ingredients for making rubber bumpers add some amount of abrasion resistance to enhance their durability. They are commonly used in trailer truck docks and loading bays, jetty and boat fenders, and road safety devices. The typical cross-section of rubber bumpers is a D-shape profile. This allows one side of the bumper to be fixed on a wall while the other side absorbs the impact. The circular shape of the impact-absorbing side prevents damage to the colliding vehicle.
Rubber Gaskets and Seals: While most gaskets and seals are made from die-cutting and injection molding, they can also be made from extrusion. Extruded gaskets and seals are typically used in weatherproofing cabins, enclosures, cars, equipment housings, and electrical panels. The rubbers used in the production of these products are selected for their chemical resistance and resilience against external harm such as heat, sunlight, and oxidation. Rubber gaskets and seals are available in both hollow and solid profiles. Regardless of the profile, it is important that the material can easily be compressed between the mating surfaces to properly form a tight seal.
Rubber Cord Stock or O-Rings: O-rings are special types of gaskets that have a uniform cross-section and have ends connected together forming a ring. While popularly known as having a circular cross-section, other shapes are sometimes used. Typical O-rings made from injection or compression molding processes are limited to small equipment such as valves and quick-connect joints. However, when it comes to large equipment such as vessels and tanks, they are made from a long cord stock. The cord stock is an extruded rubber cut to length according to the circumference or perimeter of the mating parts. To form the O-ring, the ends of the cord stock are bonded together by a strong adhesive or through vulcanizing.
Medical Silicone Rubber Tubing: Of the various types of extruded rubber products, medical silicone rubber tubing is the highest quality and most well designed due to the high standards required by the medical industry. Manufacturers are required to adhere to strict standards in medical products, including medical silicone tubing.
The inherent characteristics of extruded rubber products depend on the chemical and physical properties of its base elastomer chain. The elastomer chain is composed of the carbon-based polymer backbone with several active sites or functional groups. The chemical composition of the elastomer chain determines the type of rubber material.
On top of the general properties such as elasticity, thermal and electrical insulation, and shock-absorbing properties, a specific kind of rubber material is chosen for its inherent chemical resistance, aging and degradation resistance, mechanical properties, and cost. Below are the different types of rubber materials used in the production of extruded rubber.
Styrene-Butadiene Rubber (SBR): Styrene-butadiene or SBR is a product of copolymerization between styrene and butadiene. SBR is one of the most important types of rubber which are used to produce not just extruded rubber parts but also to manufacture tires, gaskets, and shoes. It is a general-purpose rubber that competes with natural rubber in terms of market share. SBR is preferred due to its better abrasion, tear, and thermal resistance than natural rubber.
Ethylene Propylene Rubber (EPM, EPDM): EPDM is made from the copolymerization of ethylene and propylene with the addition of diene, which facilitates curing. When diene is not used, the result is referred to as EPM and is only curable by peroxide. Both EPDM and EPM have good weathering resistance, good insulating and dielectric properties, excellent mechanical properties both at high and low temperatures and chemical resistance. They compete with NBR in terms of production volume when used in automotive sealing applications.
Fluorocarbon (Viton) Rubber (FKM): FKM rubbers are known as fluoro-elastomer materials. They are made from the copolymerization of vinylidene fluoride (VDF) with other chemicals such as hexafluoropropylene (HFP), tetrafluoroethylene (TFE), and so on. It is known commercially as Viton, which is a trademark of DuPont. FKM is generally known to be highly resistant to almost all chemicals, aside from having good mechanical properties. They are perfect to produce cord stocks for making O-rings and other sealing products.
Silicone Rubber: Unlike other rubber materials, which have a carbon-based polymer backbone, silicone rubbers have a silicon-oxygen chain bonded with methyl, vinyl, and phenyl functional groups. These materials are characterized to have good oxygen, ozone, heat, light, and moisture resistance. However, they are more expensive and have poorer mechanical properties than organic rubber. They are used in many industrial applications, but they are most popularly used in food and drug manufacturing.
Rubber extrusion is a downstream process that involves compounding, heating, kneading, pressurizing, extrusion, and vulcanizing. It uses rubber and chemical feedstock from a number of primary plant processes in the chemical and petrochemical industries.
By itself, rubber extrusion is a fairly straightforward process. In the simplest sense, it only involves feeding the rubber material into the extruding machine, gathering the extrudate, vulcanizing it, and then cutting and splicing according to the client’s specifications. However, there are many parameters at play. One is the formulation of the rubber compound. The second is the extruding parameters such as temperature, throughput rate, and vulcanizing time. The process must be carefully controlled to create a reliable product.
Below is the step-by-step rubber extrusion process.
Rubber Compounding: The compounding process is where the formulation of the rubber material takes place. The main elastomer compound, which can either be NBR, SBR, BR, FKM, and so on, is thoroughly mixed with additive ingredients to obtain the desired properties of the product. The additive ingredients improve and complement the intrinsic set of properties of the main elastomer. Below are some of the compounding ingredients manufacturers use in rubber extrusion.
As the rubber goes through the extruder barrel, the constant rotation of the screw masticates and mixes the material. The screw is composed of a set of engineered and carefully machined screw elements that have a profile that either heats, kneads, or pressurizes the rubber. As the rubber is heated, its flowability increases, which prepares it for the next stage of the production process.
Extrusion: The extrusion operation takes place at the end of the extruder barrel. At this point, a tool called a die is installed, which has an opening that contains the cross-section of the finished material. This opening is designed to compensate for any dimension changes that occur after extrusion. Typically, the extrudate swells after leaving the die and during the vulcanization process.
As the rubber is pressurized by the screw, it is forced to flow through the die to become an extrudate. This extrudate now resembles the physical features of the final product. The extrudate is ejected from the machine and guided by a set of rollers and wheels to bring it to the next step.
Vulcanizing or Curing: The vulcanizing stage, as mentioned earlier, is done to fix the physical and chemical properties of the finished product. In a more detailed perspective, this process is where the cross-links between elastomer chains are created. Sites within the rubber’s long molecular chain bind with each other using vulcanizing agents such as sulfur and peroxide. This yields an interconnected molecular structure that acts like a stretchable, meshed material that returns to its original shape in its rested state.
To initiate the vulcanizing process, the extrudate is further heated or held at elevated temperatures of around 140 to 160°C. This could take several minutes depending on the rubber compound and vulcanizing agents used. Vulcanizing time is shortened by vulcanizing modifiers such as activators and accelerators.
Various plastics and rubbers can be combined in the co-extrusion process. The design of the produced component determines the types of rubber and plastics that will be used. This aspect of the process has to be carefully monitored to ensure the quality of the final product.
The process of co-extrusion includes the extrusion of layers of material at the same time, requiring multiple extruders to melt the rubber and plastic before they are combined. The combination of the two materials takes advantage of their beneficial properties to create a stronger and more resilient product.
A rubber bushing is a form of vibration isolator that is placed between two parts to limit the motion between them and absorb, mollify, and buffer the energy produced by their interaction. They are very...
Rubber sheets are basically sheets made of rubber or cloth that are coated with rubber to improve the mechanical properties of rubber sheeting such as increased tensile strength and reduced elongation...
Rubber trim is an extruded, sometimes molded, elastomer that is used to protect the edges or surfaces of objects from sudden impacts. They are usually found on panels, windows, doors, removable covers, and hatches...
Molding is a manufacturing process that uses a mold - the latter being a solid container used to give shape to a piece of material. It is a forming process. The form is transferred from the mold to the material by...
Rubber gaskets are elastic components used for mechanically sealing the microscopic gap between two mating surfaces or joints. Examples of these surfaces are flange faces of piping and fittings, mating surfaces of an...
Rubber injection molding is when uncured rubber is transformed into a usable product by injecting raw rubber material into a mold cavity made of metal. The applied pressure produces a chemical reaction like...
Rubber molding is a process of transforming uncured rubber or an elastomer into a usable product by transferring, compressing, or injecting raw rubber material into a metal mold cavity...
There are several methods to perform rubber overmolding, and each method has its own unique advantages and disadvantages. The choice of method typically depends on the design and material requirements of the product being...
A rubber roller is a machine part that is composed of an inner round shaft or tube covered by an outer layer of elastomer compounds. The inner shaft is made of steel, aluminum alloys, or other strong and rigid material composites...
Rubber to metal bonding is when a rubber part has to be adhered to a metal part, a metal component is chemically prepared and is attached or encapsulated as part of the process to become a bonded rubber part...
Rubber tubing, also known as rubber hose or rubber piping, is made of natural and synthetic rubber and is used to circulate and transport liquids and gases for household and industrial uses. The natural or synthetic rubber materials used for the manufacture of rubber tubing...
Silicone rubber molding is a method for shaping, forming, and fabricating silicone rubber parts and products using a heated mold. The process involves compressing or injecting silicone rubber into a mold...
A grommet edging is a flexible rubber or plastic strip that covers rough and sharp surfaces found in openings and edges of panel walls to protect the passing electrical cables, wires, and other sensitive components...