Compression Molding
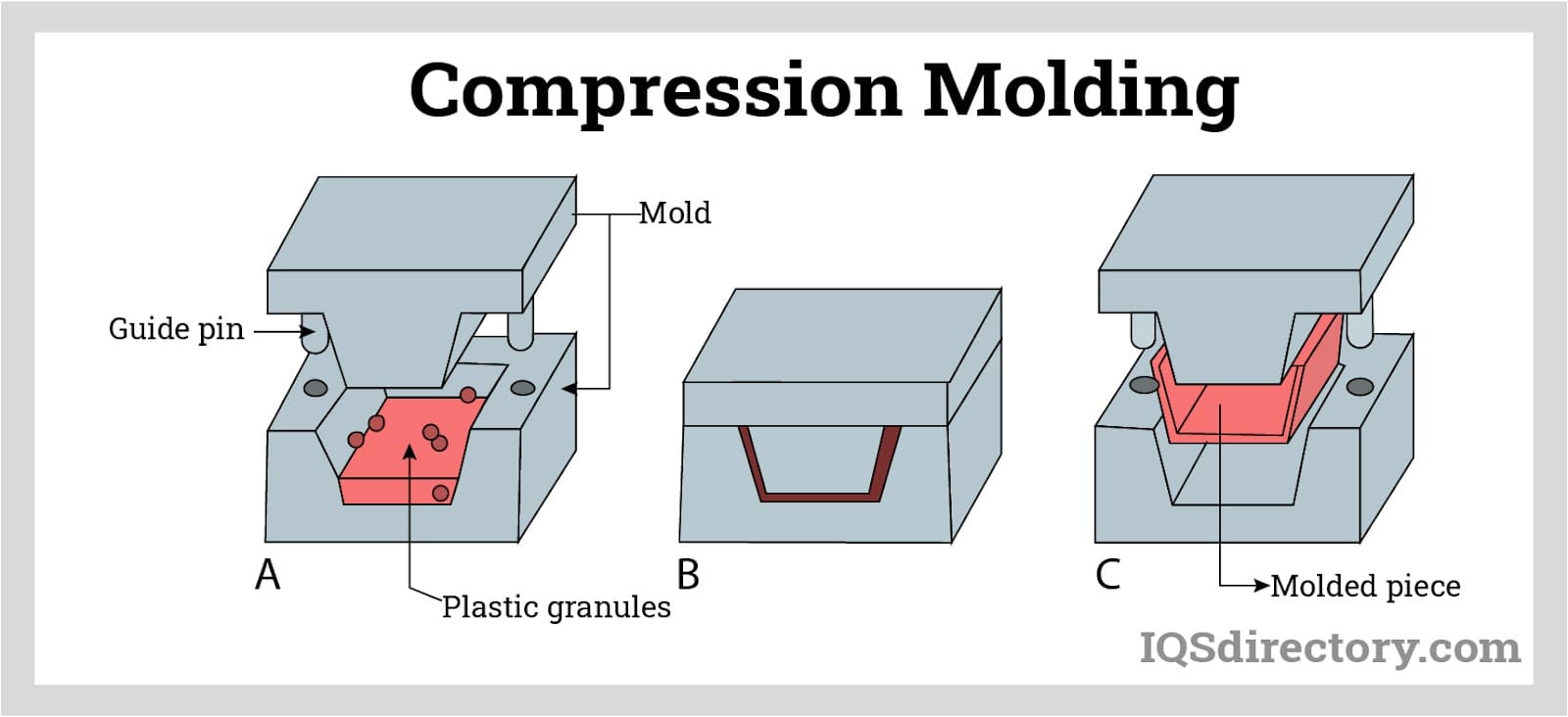
Molding is a manufacturing process that uses a mold - the latter being a solid container used to give shape to a piece of material. It is a forming process. The form is transferred from the mold to the material by...
This article takes an in depth look at grommet edging.
Read further and learn more about:
Grommet edging protects electrical cables, wires and other sensitive components from abrasion and chafing as they pass through or over rough or sharp edges or surfaces. Chafing can lead not only to loss of data and operational control but also to catastrophic fires, electric shock, equipment damage, and health and safety issues for personnel.
Every piece of machinery or manufactured product has openings that are punched or stamped into its panels and/or enclosures through which wiring is passed as necessary. The cutting action most often leaves the metal or plastic panels with an abrasive burr and rough surface.
Grommet strips, sometimes called trim, are applied directly onto these panels, enclosure walls or bulkhead surfaces to protect wiring from these sharp edges.
They are composed of a range of substances: nylon, EPDM, PVC, silicone rubber, polyethylene (PE), and an encapsulated metal spring fastener strip substrate. One of the major differences between products is that nylon, EPDM, PVC, silicone and PE grommets can often require adhesive to ensure they stay on, whereas encapsulated metal spring fastener grommets do not.
Wire chafing occurs when the weight of the cable applies pressure to (a.k.a. ‘rubs on’) the edge it is crossing. This wears away at the wire’s insulation, potentially exposing the bare wires. Grommet edging is designed to not only to prevent abrasion but also to absorb shock, dampen vibration, and prevent heat transfer which can also influence abrasion/wire damage.
They can be installed with finger pressure but how well they stay on varies significantly by product type especially if the grommet has to go in a circular opening, around corners or on irregular edge runs. For example, nylon grommets will often require the application of adhesives and “fixturing”- using tape or clamps to keep the grommet in place while the adhesive cures. This process can add significant cost and time to manufacturing. Encapsulated metal spring fastening grommets do not suffer from this drawback.
Grommet strips are supplied in different sizes to fit different sheet thicknesses and in fixed and continuous lengths. Some manufacturers will produce custom lengths.
Grommet edging is used in practically every manufacturing sector that produces powered equipment. Volume users include industries such as aerospace, automotive, rail, telecommunications, power, medical, construction, military, mining, and forestry.
Manufacturers/OEMs rely on grommet edging to prevent chafing and ensure safe and reliable equipment operation.
Grommet edging is made from either a flexible and resilient extruded polymer like nylon, PTFE, EPDM, PVC, silicone rubber and polyethylene, or a metal spring clip substrate encapsulated in a polymeric coating.
Grommets have a U-shaped cross-section and most have “fingers” or “castles” along their length to make the strip more flexible…and in the case of encapsulated metal substrate grommets to provide a strong gripping force onto the edge. The main types fall into these groups:
These are the original grommets made of molded nylon 6/6 like the Mil Spec version MS21266 which have been used since the 1940s.
Nylon is a thermoplastic, synthetic polymer that has high strength, high dimensional stability, with good abrasion, chemical, and corrosion resistance. It is not degraded by exposure to UV, and it can operate between -40°F – 122°F (-40°C – 50°C) temperatures. However be aware that over time nylon and any adhesive used with it degrades. Nylon is inherently hygroscopic so exposure to moisture will plasticize/soften the nylon which can loosen the grommet. In dry environments nylon gives up water which can make it brittle which again makes it susceptible to dis-bonding from the edge.
Nylon has low surface friction, so the insulation of the wire will not degrade. As a molded strip, it conforms to 2 axes but as its molded "fingers" or "castles" provide no gripping force onto the edge, it often requires adhesives and fixturing for effective installation.
If glue is needed to ensure performance, then installing a nylon grommet like MS21266 requires a multi-step process which includes bonding prep with Scotch-brite abrasive, cheesecloth, VOC solvent and disposable gloves, application of the bonding material, followed by fixturing with tape or clamps to ensure the grommet stays in place while it cures for up to 12 hours, and, lastly, inspections and clean up often requiring Hazmat disposal procedures. This long, slow process adds considerable time and cost to total installation expense.
OEMs have traditionally used glue to ensure the nylon grommets stay in place because they tend to suffer from “coil set” or “straight set” depending on how they are made. If the nylon grommet is spooled post manufacture, it will retain residual curvature or “coil set” from the spool. This will cause it to bend away from straight (and even curved) edges and dis-bond. If the nylon strip is not spooled, it will have a tendency to remain straight - a.k.a. “straight set” - and will resist being bent. This is a problem for curved edges or circular penetrations as the grommet will want to dis-bond from the edge - even when glue is used.
Operationally application of glued nylon grommets can be problematic. They can be difficult to apply to burred metal edges because the nylon has little or no give so it gets caught easily leading to multiple attempts. Once installed the work has to be inspected carefully for proper adhesion. Unfortunately its tendency to dis-bond generates a high rework rate which adds cost and time and drives up the cost of poor quality. From a quality standpoint, a product that has grommets smothered in adhesive does not convey a high quality precision product or process.
Given its many limitations, nylon is best used for long straight runs without corners or curves. However, even then, given its coil set tendency, some manufacturers will apply adhesive to ensure the grommet stays in place.
Many OEMs are switching to the encapsulated spring fastening metal substrate version which solves these issues.
Encapsulated metal based grommet edging consists of a spring stainless steel substrate encapsulated with a durable flame retardant thermoplastic (TPE) and in some variants an added cushion for even greater protection.
The precision spring stainless substrate offers strong edge retention that eliminates the need for installation adhesives - providing a 49% lower installed cost compared to nylon grommets and glue.
They have excellent abrasion resistance given their low coefficient of friction. They are also resistant to corrosion, water absorption and are flame rated to UL94 V-0. They offer excellent electrical insulation while also resistant to many chemicals and are UV stable. They are manufactured using powder coated precision metal stampings and thermoplastic extrusions.
They are applied with just finger pressure - no glue - yet have superior retention because the spring steel core is designed with castles, or gripping teeth, that angle into the edge creating a force that grips the edge without adhesives.
Utilizing the optimum stainless alloy that maintains its clock spring flexibility, they can be easily removed and replaced multiple times without fatigue or degrading retentive strength and have been successfully static load tested to 20G on all three axes without adhesives.
The angled out "lip" on each castle helps guide and align the installation of the grommet onto an edge even if the edge has burrs, thereby speeding the self-aligning grommet edging installation and assembly process. Coil set and straight set are eliminated because the flexible spring steel substrate allows the strip to be preformed, applied, removed and adjusted as needed without any loss in retention.
This newer grommet has shown itself to offer best-in-class performance at a 49% lower total installed cost compared to nylon, PTFE or PE grommets and glue because there is no long, slow multi-step process of glue prep, application, fixturing, curing, clean up or frequent rework.
EPDM, or ethylene propylene diene monomer, is a synthetic rubber. It is classified as an M-class rubber under ASTM standard D-1418. EPDM has a saturated polymer backbone and an active site for cross-linking; this enables it to have high durability, resiliency, flexibility, and thermal stability. It is resistant to heat, UV, and ozone and is a good electrical insulator. However, it is incompatible with hydrocarbons and halogenated solvents.
Often extruded with a steel wire substrate core, it is self fastening and rarely needs adhesives. It is favored for larger openings and surfaces that do not need a low profile solution but need a durable edge treatment without critical environmental performance requirements.
Given its relative rigidity and its bulk, it is best used on straight edge runs as it will not conform well to sharp corners or irregular shaped edge turns with tight radii.
PVC, or polyvinyl chloride, is a synthetic thermoplastic. PVC is naturally rigid and can be modified by the addition of plasticizers, such as phthalates and adipates, to make it flexible consistent with its aluminum core that supports good retention without adhesives.
Flexible PVC is commonly used in grommet edging; it is an economical alternative to synthetic rubber. PVC has high tensile strength, density, and impact resistance. It is a good electrical insulator and is resistant to corrosion and most chemicals.
It naturally has flame retardant properties, but in sensitive electronic applications at elevated operating temps it can off-gas chlorine creating a potential corrosive environment for nearby metal contacts. Its profile design offers self-fastening application and rarely needs adhesives, yet the softer aluminum core that makes it pliable and allows it to be re-worked to accommodate sheet thickness variations also means it can be scuffed off an edge more easily.
Again, given its relative rigidity, it is best used on straight edge runs or very broad radii applications as it will not conform well to corners or irregular shaped edge turns.
Silicone rubber, aka polydimethylsiloxane, is an inorganic synthetic elastomer. It is a thermosetting polymer that has superior flexibility and durability. It is resistant to most chemicals, corrosion, UV, and ozone. It is a good insulator and can withstand high temperatures.
It also has high abrasion resistance and a low coefficient of friction that protects the insulation of the cable well from chafing. Like the EPDM profiles, it too has a steel wire substrate. It is self fastening and rarely needs adhesives.
Given its relative rigidity, it is best used on straight edge runs as it will not conform well to corners or irregular shaped edge turns.
Polyethylene is a lightweight and durable thermoplastic. It has good abrasion resistance given its low coefficient of friction. It has low water absorption, excellent electrical insulation, and is compatible with chemicals except hydrocarbons, oils, and oxidizing agents.
It is also cheaper than many other materials used in grommet edging. However, it has lower temperature resistance, is susceptible to UV degradation and has no flame retardant properties. This has decreased its use over time.
The lower unit cost per piece associated with this material is offset by the frequent need to use adhesives to ensure fastening and retention which increases the total installed cost.
In addition, like nylon, application of PE grommets, with their narrow gapped castle tips, can be difficult to insert onto sheet metal edges, especially if burred metal edges are present because there is little or no give in the material so it can often get caught, and multiple attempts have to be made to apply correctly.
There are a number of niche variants of grommet edging.
Teflon (PTFE) grommets are sold in similar formats to nylon that are for predominantly high heat exposure applications such as ovens, engines or heat shields. Teflon can also be used in slide and glide applications as it has a very low coefficient of friction. The drawbacks are that it is expensive and it requires fastening, and as such special chemical etching of the grommet is necessary for any adhesive to work.
All metal/High Heat: There is a non-encapsulated all metal grommet that is ideal for high heat applications and often used in automotive and aero applications (engine heat shields, furnaces). In this case, no adhesive is required as the inward leaning metal castles create the gripping force.
Here are four of the key tests performed on grommets to verify their performance and reliability:
A salt spray test is a fast standardized way to evaluate the corrosion resistance and suitability of the polymer strip or the polymeric coating protecting the underlying metallic substrate. In this test, the grommet is exposed to dense saltwater fog inside an enclosed testing chamber to check if accelerated corrosion occurs. The salt spray is typically acetic acid salt, sodium chloride, simulated acid rain, or simulated seawater. The result of this test is reported as either pass or fail.
UL94 is known as the Standard for Safety of Flammability of Plastic Materials for Parts in Devices and Appliances testing. This standardized test is formulated by Underwriters Laboratories in the USA. The test rates materials according to their tendency to extinguish or spread flames after a specimen is ignited. The following are the UL94 ratings arranged from least flame-retardant to most flame-retardant:
UL94 Rating | Definition |
---|---|
HB | Slow burning on a horizontal part. |
V-2 | Burning stops within 30 seconds on a vertical part. Flaming particle drips are observed. |
V-1 | Burning stops within 30 seconds on a vertical part. Particle drips which are not inflamed are observed. |
V-0 | Burning stops within 10 seconds on a vertical part. Particle drips which are not inflamed are observed. |
5VB | Burning stops within 60 seconds on a vertical part. No particle drips are observed. A burn-through hole is present. |
5VA | Burning stops within 60 seconds on a vertical part. No particle drips are observed. A burn-through hole is not present. |
A Taber Abrasion Test ASTM D 1044 tests the abrasion and wear resistance of a material. In this test, a specimen of known dimensions and weight is placed under two grinding wheels that exert a load and rotate for a set number of rotations. This creates the abrasion.
The specimen is weighed at the end of this test to see how much was lost from the abrasion action. The less it loses, the higher the resistance. The abrasion resistance is categorized based on the weight lost, the number of revolutions, the load applied, and the type of wheel. For example, 8 mg loss over 5000 cycles @ 1 kg load on a C17 Wheel.
In key categories like automotive and aerospace, the operating environment acting on components can be extreme with vibration, pressure, and acceleration creating loads on systems and components that can reach 20 G’s. It is critical that components perform for the success of the operation (or military mission) as well as the safety of operators.
MIL-STD 1344A, Method. 2005.1 is the established test method protocol for testing electrical connectors.
In this test, the parameters can vary, but for example the Device Technologies, Inc., Mil Spec grommet M22529/2 was subjected to 8 hours of longitudinal and 8 hours of perpendicular vibration and was able to withstand forces equivalent to rms G 41.7.
Molding is a manufacturing process that uses a mold - the latter being a solid container used to give shape to a piece of material. It is a forming process. The form is transferred from the mold to the material by...
Rubber injection molding is when uncured rubber is transformed into a usable product by injecting raw rubber material into a mold cavity made of metal. The applied pressure produces a chemical reaction like...
Rubber latches are latches made of rubber or are composed of rubber components. They are used in the automotive, aerospace, and medical equipment industries due to their flexibility, durability, and non-abrasive properties...
Rubber molding is a process of transforming uncured rubber or an elastomer into a usable product by transferring, compressing, or injecting raw rubber material into a metal mold cavity...
There are several methods to perform rubber overmolding, and each method has its own unique advantages and disadvantages. The choice of method typically depends on the design and material requirements of the product being...
Silicone rubber molding is a method for shaping, forming, and fabricating silicone rubber parts and products using a heated mold. The process involves compressing or injecting silicone rubber into a mold...
A rubber bushing is a form of vibration isolator that is placed between two parts to limit the motion between them and absorb, mollify, and buffer the energy produced by their interaction. They are very...
Extruded rubber is a group of products made by softening and pressurizing an elastomeric compound and forcing it to flow through a hard tool called a die. The resulting product is a continuous piece of material that has the same cross-section throughout its length...
Rubber gaskets are elastic components used for mechanically sealing the microscopic gap between two mating surfaces or joints. Examples of these surfaces are flange faces of piping and fittings, mating surfaces of an...
A rubber O ring is a mechanical gasket in the shape of a torus or donut and is used for static and dynamic applications where there is relative motion between parts and the possibility of friction. Some of the benefits of rubber O rings are...
A rubber roller is a machine part that is composed of an inner round shaft or tube covered by an outer layer of elastomer compounds. The inner shaft is made of steel, aluminum alloys, or other strong and rigid material composites...
Rubber sheets are basically sheets made of rubber or cloth that are coated with rubber to improve the mechanical properties of rubber sheeting such as increased tensile strength and reduced elongation...
Rubber to metal bonding is when a rubber part has to be adhered to a metal part, a metal component is chemically prepared and is attached or encapsulated as part of the process to become a bonded rubber part...
Rubber trim is an extruded, sometimes molded, elastomer that is used to protect the edges or surfaces of objects from sudden impacts. They are usually found on panels, windows, doors, removable covers, and hatches...
Rubber tubing, also known as rubber hose or rubber piping, is made of natural and synthetic rubber and is used to circulate and transport liquids and gases for household and industrial uses. The natural or synthetic rubber materials used for the manufacture of rubber tubing...
Urethane casting is the process of injecting polyurethane and additive resins into a soft mold usually made of silicone elastomer. The casting process is similar to injection molding; injection molding differs by using hard, metal molds...