Compression Molding
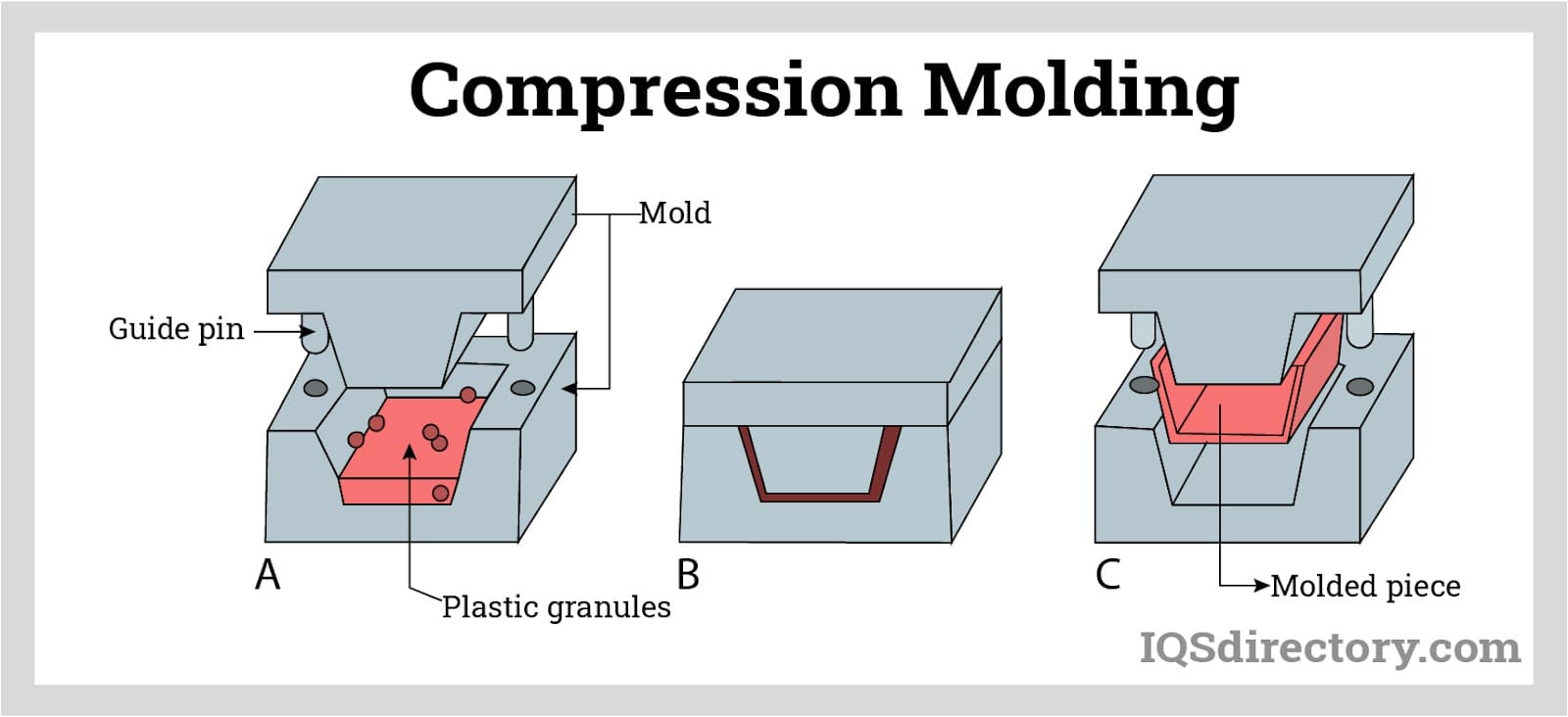
Molding is a manufacturing process that uses a mold - the latter being a solid container used to give shape to a piece of material. It is a forming process. The form is transferred from the mold to the material by...
Please fill out the following form to submit a Request for Quote to any of the following companies listed on
This article will provide a reader with more information regarding topics, including:
There are several methods to perform rubber overmolding, and each method has its own unique advantages and disadvantages. The choice of method typically depends on the design and material requirements of the product being manufactured, as well as the volume of production, cost considerations, and desired level of precision.
Injection molding is one of the most commonly used methods for rubber overmolding. This method involves injecting molten rubber into a mold that contains the substrate, which is typically made of plastic or metal. Once the rubber has cooled and solidified, the mold is opened, and the finished product is removed. Injection molding is a popular choice because it allows for high precision and repeatability, making it ideal for high-volume production runs.
Compression molding is another popular method for rubber overmolding. This method involves placing the substrate in a mold, which is then closed and heated to a specific temperature. Molten rubber is then added to the mold, and pressure is applied to force the rubber to conform to the shape of the substrate. The mold is then cooled, and the finished product is removed. Compression molding is a good choice for products with complex geometries or low-volume production runs.
Transfer molding is another method used for rubber overmolding, which is similar to compression molding, but with the addition of a transfer pot or chamber. This chamber is filled with molten rubber, which is then injected into the mold through a channel. Transfer molding is a good choice for products that require high precision and intricate designs.
LIM is another method for rubber overmolding. LIM involves injecting a liquid rubber into a mold, which is then cured in the mold. LIM is a popular choice because it allows for fast cycle times, high precision, and the ability to over-mold on delicate substrates or electrical components.
Two-shot molding is a process of creating a product by injecting two different materials into a single mold. This process is often used for rubber overmolding, as it allows for the creation of products with multiple layers or sections of different materials.Two-shot molding is a useful method for rubber overmolding when products require specific design requirements or multiple layers of different materials. The process can help reduce manufacturing costs and improve overall efficiency, making it a popular choice for many industries.
Ultimately, the choice of method depends on a variety of factors, including the complexity of the product, production volume, desired level of precision, and cost considerations. Each method has its unique advantages and disadvantages, and the choice of method should be made based on the specific needs of the product being manufactured.
Design considerations play a crucial role in rubber overmolding as they determine the quality, functionality, and durability of the final product. Here are some of the most important design considerations and how they impact rubber overmolding:
The choice of materials used in rubber overmolding is critical, as the materials must be compatible with each other to ensure a strong bond between the core component and the rubber overmold. Factors such as the material hardness, coefficient of thermal expansion, and chemical resistance must be considered when selecting materials.
The surface finish of the core component is an important factor in rubber overmolding, as it determines the adhesion and bonding strength between the rubber and the core component. A rough surface finish can result in poor bonding and a weak final product. Therefore, it is important to ensure that the surface of the core component is smooth and free from defects such as scratches and burrs.
Tolerances refer to the acceptable range of deviation from the specified dimensions of the core component. It is essential to design the core component within acceptable tolerances to ensure that the rubber overmold fits accurately and securely around the core component. Poor tolerances can result in a weak bond between the rubber and the core component, resulting in a lower quality final product.
Undercuts are recesses or protrusions on the surface of the core component that are not perpendicular to the molding direction. Undercuts can make it difficult to remove the core component from the mold after the rubber overmolding process. Therefore, it is important to consider the design of the core component to avoid undercuts, or to use a mold release agent or a sliding core to facilitate the removal of the core component.
The thickness of the rubber overmold is an important consideration in rubber overmolding, as it affects the strength, durability, and flexibility of the final product. A thicker rubber overmold can provide greater durability and vibration resistance, but it can also increase the weight and cost of the final product. Therefore, it is important to strike a balance between the desired performance characteristics and the cost of production.
Draft angles are the angles at which the surface of the core component slopes to facilitate the removal of the molded part from the mold. Draft angles are essential in rubber overmolding, as they prevent the rubber from tearing or becoming damaged during the removal process. Typically, draft angles of 0.5-1.5 degrees are recommended for rubber overmolding.
In summary, careful consideration of these design factors can help ensure the quality, functionality, and durability of rubber over molded parts. Designers and engineers should work closely with rubber overmolding manufacturers to ensure that the final product meets the desired specifications and requirements.
Rubber overmolding is typically performed using different types and grades of rubber materials, each of which offers unique properties and advantages. The type and grade of rubber used depend on the application requirements of the finished product. Here are some of the most common types and grades of rubber used in rubber overmolding:
Silicone rubber is a popular choice for rubber overmolding applications because it offers high thermal stability, chemical resistance, and flexibility. It is also biocompatible, making it suitable for medical applications.
Ethylene Propylene Diene Monomer (EPDM) rubber is another popular choice for rubber overmolding. It offers excellent resistance to weathering, ozone, and UV radiation, making it suitable for outdoor applications.
Neoprene rubber is a synthetic rubber that offers excellent resistance to oil, chemicals, and heat. It is often used in industrial applications where resistance to harsh environments is required.
Natural rubber is a flexible and durable material that is made from the sap of rubber trees. It offers excellent elasticity and tear resistance, making it suitable for applications such as seals, gaskets, and hoses.
Nitrile rubber is a synthetic rubber that offers excellent resistance to oils, fuels, and chemicals. It is often used in automotive and industrial applications where resistance to harsh environments is required.
Now that we’ve explained the different types of materials used to create rubber overmolded products, let's examine the grades of rubber overmolding more closely. The grades of rubber used in rubber overmolding are typically defined by organizations such as the American Society for Testing and Materials (ASTM) and the Society of Automotive Engineers (SAE). These organizations establish standards for rubber materials and assign grades based on specific criteria such as their resistance to heat, oil, weathering, and other factors.
The ASTM D2000 standard is commonly used to define grades of rubber materials. This standard defines a range of specifications for rubber materials and assigns a letter and number combination to each grade. The letter designates the type of elastomer, while the number designates the quality level of the material.
For example, the letter "S" designates a silicone elastomer, while the letter "N" designates a nitrile elastomer. The number designation for each grade is based on specific performance characteristics, such as tensile strength, elongation, and compression set.
The choice of rubber grade can have a significant impact on the performance and durability of a rubber over molded product. For example, a high-grade rubber material may be required for applications that require high levels of resistance to temperature, chemicals, or UV radiation. On the other hand, a lower grade rubber material may be sufficient for applications that do not require such high levels of resistance.
In summary, different types and grades of rubber are used in rubber overmolding, each with its unique properties and advantages. The choice of rubber material depends on the application requirements of the finished product, and rubber grades are used to describe the quality and consistency of rubber materials.
Rules and regulations regarding rubber overmolding are typically aimed at ensuring that products are safe for consumers and meet quality standards. While there is no specific history of regulations related to rubber overmolding, the use of rubber materials in various industries has been regulated for many years. The following are some of the most important rules and regulations that apply to rubber overmolding:
The RoHS Directive is a European Union regulation that restricts the use of certain hazardous substances in electrical and electronic equipment. This regulation applies to rubber materials used in products such as cables, wires, and other electronic components that may be used in rubber overmolding.
The REACH Regulation is another European Union regulation that requires the registration and evaluation of chemicals used in the manufacture of products. This regulation applies to rubber materials used in a wide range of products, including those that may be used in rubber overmolding.
The FDA regulates the use of rubber materials in products that come into contact with food, drugs, and medical devices. This regulation applies to rubber materials used in products such as seals, gaskets, and hoses that may be used in rubber overmolding.
The ASTM develops and publishes standards for rubber materials used in a wide range of products. These standards cover properties such as hardness, tensile strength, and elongation, and may be used to ensure that rubber materials used in rubber overmolding meet specific quality and performance standards.
The ISO develops and publishes standards for rubber materials used in various industries. These standards cover properties such as temperature resistance, chemical resistance, and mechanical properties, and may be used to ensure that rubber materials used in rubber overmolding meet specific industry standards.
In summary, rules and regulations related to rubber overmolding are aimed at ensuring that products are safe and meet quality standards. These regulations include the RoHS Directive, the REACH Regulation, FDA regulations, ASTM standards, and ISO standards, among others. Compliance with these regulations may be required in various industries, and failure to comply can result in legal and financial consequences for manufacturers.
Quality control is a crucial aspect of rubber overmolding as it ensures that the final product meets the desired specifications and requirements. Here are some key aspects of quality control in rubber overmolding:
The temperature and pressure conditions during the molding process can have a significant impact on the quality of the final product. Therefore, it is essential to closely monitor and control these conditions to ensure consistent results across multiple parts.
The surface finish of the final product is an important quality characteristic that can affect the appearance, functionality, and durability of the product. Therefore, it is important to inspect the surface finish of each part to ensure that it meets the desired specifications.
Dimensional accuracy refers to the extent to which the final product meets the specified dimensions. A deviation from the specified dimensions can affect the functionality and performance of the final product. Therefore, it is important to inspect the dimensional accuracy of each part to ensure that it meets the desired specifications.
The material properties of the final product, such as hardness, chemical resistance, and tensile strength, are critical quality characteristics that determine the performance and durability of the product. Therefore, it is important to test the material properties of each part to ensure that they meet the desired specifications.
Performance testing involves testing the final product to ensure that it meets the desired performance characteristics, such as grip, durability, and vibration resistance. Performance testing may involve subjecting the product to simulated real-world conditions, such as exposure to extreme temperatures, humidity, or impact.
There are several inspection techniques that can be used to ensure the quality of rubber over molded parts, including visual inspection, dimensional measurement, and material testing. These inspection techniques can help detect defects and ensure that the final product meets the desired specifications.
Documentation and traceability are important aspects of quality control, as they provide a record of the manufacturing process and enable any issues to be identified and corrected. Manufacturers should keep detailed records of each part, including its design specifications, materials used, and any inspections or tests performed.
In summary, quality control is a critical aspect of rubber overmolding that ensures the consistency, functionality, and durability of the final product. Manufacturers should implement a comprehensive quality control program that includes monitoring and controlling the molding conditions, inspecting the surface finish and dimensional accuracy, testing the material properties and performance characteristics, using appropriate inspection techniques, and maintaining detailed documentation and traceability.
In addition to the design consideration, quality control considerations, and various other considerations previously discussed regarding rubber overmolding, there are still more factors to contemplate regarding one’s selection regarding rubber overmolding, including:
Tooling plays a critical role in rubber overmolding, as it determines the final shape and dimensions of the part. Manufacturers must carefully design and build the tooling to ensure that it can withstand the stresses of the molding process and produce high-quality parts.
Rubber overmolding can be an expensive manufacturing process due to the complexity of the tooling and the need for specialized equipment. Manufacturers must carefully consider the cost of materials, tooling, and labor when deciding whether to use rubber overmolding for a particular product.
Rubber overmolding can have an impact on the environment due to the use of chemicals and energy during the manufacturing process. Manufacturers must consider ways to minimize the environmental impact of rubber overmolding, such as using eco-friendly materials and processes.
By considering these various topics and factors, manufacturers can optimize their rubber overmolding processes and produce high-quality parts that meet their customers' needs.
While rubber overmolding offers many benefits, there are also some negatives and limitations that should be considered when deciding whether to use this process for a particular application. The following are some of the most common negatives and limitations of rubber overmolding:
Rubber overmolding typically requires the use of specialized equipment and tooling, which can be expensive to produce. This can be a significant barrier to entry for manufacturers, particularly those who are producing products in low volumes.
The design of the final product is limited by the tooling used in the over\molding process. Changes to the design may require the production of new tooling, which can be costly and time-consuming.
The materials used in the overmolding process must be compatible with each other to ensure a strong bond between the two materials. This can be a challenge, particularly when using different types of rubber or rubber materials with different chemical properties.
Rubber overmolding may not be the best choice for large production volumes, as the process can be slow and labor-intensive.
While there are many types of rubber materials available for overmolding, certain materials may not be suitable for certain applications due to factors such as temperature resistance or chemical resistance.
Ensuring consistent quality can be a challenge with rubber overmolding, particularly when producing large volumes of products. Quality control measures must be in place to ensure that each product meets the required specifications.
In summary, while rubber overmolding offers many benefits, there are also some negatives and limitations to consider. These include high tooling costs, limited design flexibility, material compatibility issues, limited production volume, limited material options, and quality control challenges. Manufacturers must carefully consider these factors when deciding whether to use rubber overmolding for a particular application.
Rubber overmolding offers a number of benefits that make it a popular choice for many manufacturing applications. Some of the key benefits of rubber overmolding include:
Rubber over molding can improve product performance by providing a non-slip grip, shock absorption, vibration dampening, and enhanced durability. These characteristics can make products more comfortable, safer, and longer-lasting.
Rubber over molding enables designers to incorporate multiple materials into a single part, which provides greater design flexibility. This can result in more complex and innovative designs that are not possible with other manufacturing processes.
Rubber over molding can be a cost-effective manufacturing process, particularly for high-volume production runs. This is because it eliminates the need for assembly and reduces waste, resulting in lower production costs.
Rubber over molding can improve the appearance of a product by adding color, texture, and other decorative elements. This can make products more visually appealing and help them stand out in the market.
Rubber over molding can improve the ergonomics of products by providing a comfortable and non-slip grip. This can reduce fatigue and improve user performance, particularly for products that are used for extended periods.
Rubber over molding can improve the durability of products by providing a protective layer that resists wear and tear. This can increase the lifespan of products and reduce the need for maintenance or replacement.
Rubber over molding can provide a waterproof seal for products that are exposed to water or other liquids. This can be particularly important for products used in wet or humid environments, such as electronics or outdoor equipment.
Rubber over molding can reduce noise levels by dampening vibration and providing a soft cushioning effect. This can be important for products that produce noise, such as power tools or machinery.
Rubber over molding can provide thermal insulation for products that are exposed to high or low temperatures. This can protect sensitive components and improve product performance in extreme environments.
Overall, rubber over molding offers a wide range of benefits that can improve the performance, durability, aesthetics, and functionality of products. These benefits, combined with the versatility and flexibility of the process, make rubber over molding a popular choice for manufacturers across many different industries.
Rubber overmolding is used in a wide range of industries, including automotive, medical, consumer electronics, and industrial equipment. Here are some examples of how rubber overmolding is used in these, and other, industries:
Rubber overmolding is used in automotive applications to improve grip and comfort, and to reduce noise and vibration. Rubber over molded components can be found on steering wheels, shift knobs, and door handles. Rubber over molded seals are also used in automotive applications to prevent water and air leaks.
Rubber overmolding is used in medical equipment to provide a secure and comfortable grip for the user. Examples of medical products that use rubber overmolding include surgical instruments, handles for medical devices, and dental tools.
Rubber overmolding is used in consumer electronics to improve the grip and durability of products. This includes products like cell phone cases, computer mice, and remote controls.
Rubber overmolding is used in industrial equipment to improve grip and reduce vibration. Examples include tool handles, hand grips for machinery, and control panels for heavy equipment.
Rubber overmolding is used in the aerospace industry to enhance the grip and durability of various components. This includes cockpit controls, aircraft handles, and switches. Additionally, rubber overmolding is used in airframe components to provide a non-slip surface for maintenance personnel.
Rubber overmolding is used in the sports and recreation industry to improve grip and comfort for users. This includes golf club handles, bicycle grips, and fishing rod handles. Additionally, rubber overmolding is used in exercise equipment, such as weightlifting bars, to reduce vibration and improve grip.
Rubber overmolding is used in the toy industry to improve the safety and durability of toys. This includes toys such as balls, action figures, and toy vehicles. Rubber overmolding provides a non-slip surface for children to hold onto, reducing the likelihood of accidents.
Rubber overmolding is used in military and defense equipment to provide a secure and comfortable grip for soldiers. This includes firearm grips, knife handles, and tactical gear. Additionally, rubber overmolding is used in military vehicles to reduce vibration and improve grip.
Overall, rubber overmolding is a versatile manufacturing process that offers many benefits to various industries. It enhances the functionality and durability of products, improves grip and comfort, and reduces noise and vibration.
The future of rubber overmolding looks bright, as the process offers a wide range of benefits that are highly valued by manufacturers and consumers. Here are a few potential developments that could shape the future of rubber overmolding:
As new materials become available, rubber overmolding may be used to create composite products with even better properties than what is possible today. For example, the combination of rubber with conductive materials could lead to new applications in the electronics industry.
As automation technology improves, the rubber overmolding process could become even more efficient and cost-effective. This could lead to a wider range of applications for rubber overmolding, as it becomes more affordable for manufacturers to implement.
As more companies prioritize sustainability in their manufacturing processes, rubber overmolding could become a more environmentally-friendly option. For example, using recycled rubber materials in the overmolding process could reduce waste and decrease the carbon footprint of the manufacturing process.
Advancements in 3D printing technology could lead to new possibilities for rubber overmolding. For example, 3D printed molds could make it easier and more affordable to create custom rubber over molded products, allowing for greater flexibility in design.
Overall, the future of rubber overmolding is likely to be shaped by advancements in technology and an increased focus on sustainability. As the benefits of rubber overmolding continue to be recognized across a wide range of industries, it is expected that the process will become even more popular in the years to come.
In conclusion, rubber overmolding is a versatile manufacturing process that has many applications in various industries. Understanding the different processes used, the types and grades of rubber, and the rules and regulations governing the process is essential for producing high-quality, durable products. While there are some limitations and negatives to consider, the benefits of rubber overmolding make it an effective and efficient way to improve product functionality, durability, and safety for both today and the foreseeable future.
Molding is a manufacturing process that uses a mold - the latter being a solid container used to give shape to a piece of material. It is a forming process. The form is transferred from the mold to the material by...
Rubber injection molding is when uncured rubber is transformed into a usable product by injecting raw rubber material into a mold cavity made of metal. The applied pressure produces a chemical reaction like...
Rubber latches are latches made of rubber or are composed of rubber components. They are used in the automotive, aerospace, and medical equipment industries due to their flexibility, durability, and non-abrasive properties...
Rubber molding is a process of transforming uncured rubber or an elastomer into a usable product by transferring, compressing, or injecting raw rubber material into a metal mold cavity...
Silicone rubber molding is a method for shaping, forming, and fabricating silicone rubber parts and products using a heated mold. The process involves compressing or injecting silicone rubber into a mold...
A rubber bushing is a form of vibration isolator that is placed between two parts to limit the motion between them and absorb, mollify, and buffer the energy produced by their interaction. They are very...
Extruded rubber is a group of products made by softening and pressurizing an elastomeric compound and forcing it to flow through a hard tool called a die. The resulting product is a continuous piece of material that has the same cross-section throughout its length...
Rubber gaskets are elastic components used for mechanically sealing the microscopic gap between two mating surfaces or joints. Examples of these surfaces are flange faces of piping and fittings, mating surfaces of an...
A rubber O ring is a mechanical gasket in the shape of a torus or donut and is used for static and dynamic applications where there is relative motion between parts and the possibility of friction. Some of the benefits of rubber O rings are...
A rubber roller is a machine part that is composed of an inner round shaft or tube covered by an outer layer of elastomer compounds. The inner shaft is made of steel, aluminum alloys, or other strong and rigid material composites...
Rubber sheets are basically sheets made of rubber or cloth that are coated with rubber to improve the mechanical properties of rubber sheeting such as increased tensile strength and reduced elongation...
Rubber to metal bonding is when a rubber part has to be adhered to a metal part, a metal component is chemically prepared and is attached or encapsulated as part of the process to become a bonded rubber part...
Rubber trim is an extruded, sometimes molded, elastomer that is used to protect the edges or surfaces of objects from sudden impacts. They are usually found on panels, windows, doors, removable covers, and hatches...
Rubber tubing, also known as rubber hose or rubber piping, is made of natural and synthetic rubber and is used to circulate and transport liquids and gases for household and industrial uses. The natural or synthetic rubber materials used for the manufacture of rubber tubing...
Urethane casting is the process of injecting polyurethane and additive resins into a soft mold usually made of silicone elastomer. The casting process is similar to injection molding; injection molding differs by using hard, metal molds...
A grommet edging is a flexible rubber or plastic strip that covers rough and sharp surfaces found in openings and edges of panel walls to protect the passing electrical cables, wires, and other sensitive components...