Gasket Materials
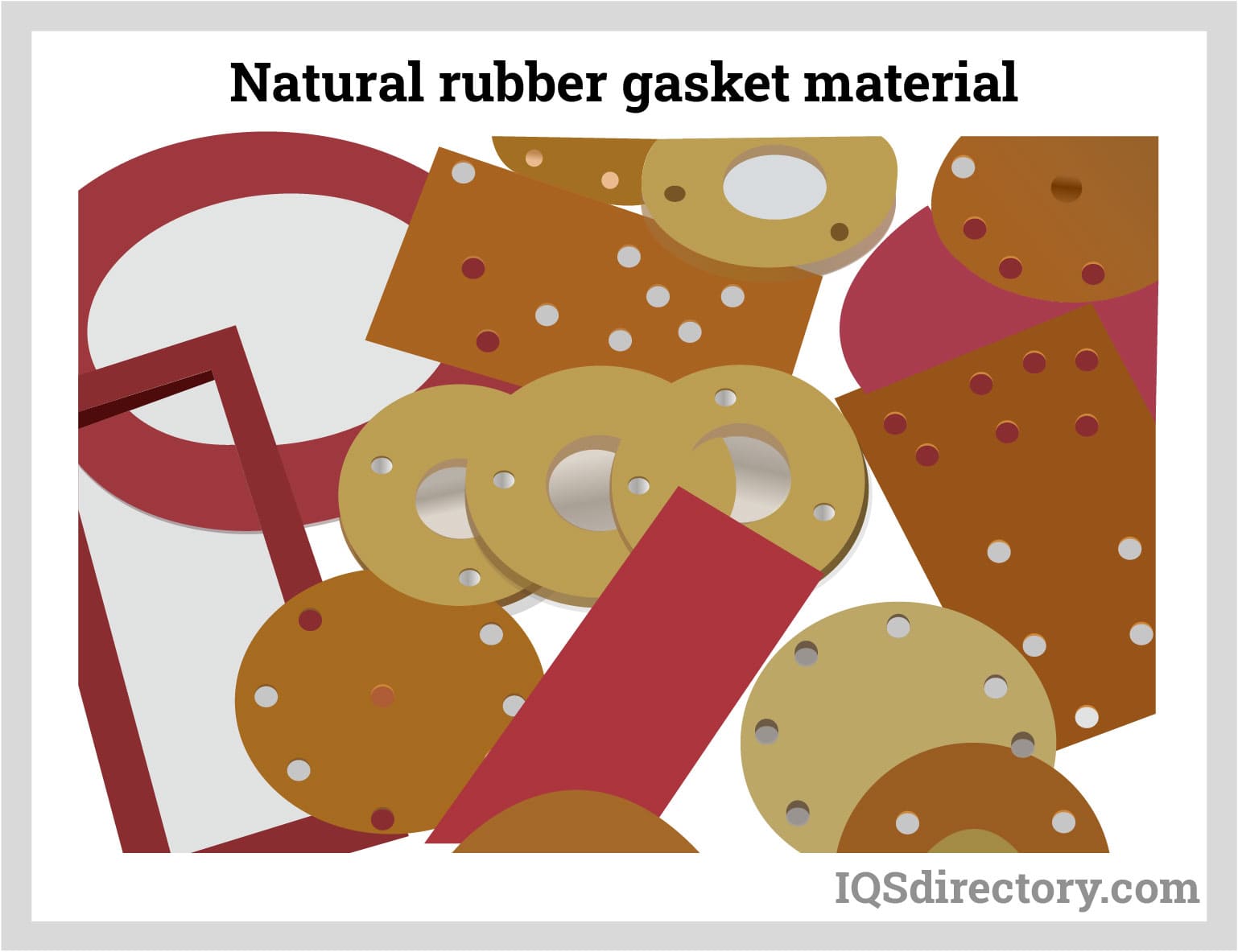
Gaskets are seals that are mechanically made to prevent either process fluids from escaping or contaminants from entering the delicate areas. Each given system has its best suited gasket, and it is critical to make the right...
Please fill out the following form to submit a Request for Quote to any of the following companies listed on
This article presents information about the various categories, properties, and applications of gaskets. Read further to learn more about:
Gaskets are mechanical seals that inhibit leakage by filling the gaps between static mating surfaces. Both polished and unpolished surfaces, particularly metal surfaces, have an inherent roughness or microscopic asperity that creates spaces where fluids can pass through. As a compressive force deforms the gasket, it conforms to the profile of the surface and fills the gaps between its peaks and troughs.
Gaskets are extensively utilized in every industry with either pressurized or non-pressurized liquids and gasses. They can be seen in most fluid-containing equipment such as pipes, tanks, heat exchangers, combustion engines, etc. Gaskets vary in form and rating to suit a particular application.
Gaskets and O-rings are both sealing components used in various mechanical and engineering applications to prevent the leakage of fluids or gases. However, they have several differences in terms of their design, shape, and applications. Here are some key differences between gaskets and O-rings:
A gasket and a seal are similar in that they both serve the crucial purpose of preventing leaks in various mechanical systems, such as engines, pipes, and containers. However, they are not the same thing.
A gasket is a mechanical component, typically made of materials like rubber, metal, or composite materials, designed to create a barrier between two mating surfaces, filling irregularities and providing a tight seal when compressed. Gaskets are often used in static applications, where the parts they seal remain relatively stationary.
A seal is a broader term that encompasses various devices, including gaskets, but also includes O-rings, lip seals, and more. Seals can be dynamic, meaning they are used in applications where one of the mating parts moves, such as in hydraulic cylinders or rotating shafts.
While both gaskets and seals are essential for preventing leaks, they differ in terms of their design, function, and the types of applications they are best suited for.
Seals, O-rings, and gaskets are all types of mechanical seals used to prevent leakage of fluids or gases in various applications. While they serve a similar fundamental purpose, they have some key differences in terms of design, shape, and applications. Here are the similarities and differences between them:
The manufacturer of gaskets covers a full spectrum of techniques, methods, and processes that include cutting, dies, and punches. The choice of method depends on the materials being processed and the strength and final use of the completed product. In all cases, the process begins with choosing a material, which is crucial to the performance of a gasket.
With rotary die cutting, a cylindrical die attached to a rotary press is used to cut and shape non-metallic material. The material is fed into the cutting station with an anvil cylinder and the rotary die. The anvil and cylinder die move in opposite directions along their horizontal axis. The cylinder die cuts out the gaskets as it presses against the anvil. It is an efficient method for producing large quantities of gaskets with consistent shapes.
Kiss cutting also uses a rotary cylinder to cut gaskets from non-metallic material. In kiss cutting, the die does not cut completely through the material and leaves a backing that can be of an adhesive material, making installing the gasket more secure.
Press die cutting is the most popular method for manufacturing gaskets and uses traditional presses for cutting metal and other more rigid non-metallic materials. The die is attached to the ram of the press, which lowers against the workpiece to cut out the gasket. The amount of force required to produce the gasket varies depending on the type of material. The types of presses include hydraulic, pneumatic, and electrical, with more precision cuts being completed manually.
Flatbed die cutting is simpler than press die cutting but has a flat fixed base and movable head that moves across the material. The cutting die is made of strips of sharp steel referred to as steel rule that has been shaped to take the form of the gasket. Dies for flatbed die cutting have a foam surface that is forced back during the cutting process but protects the sharp strips of steel when not in use. The nature of the process makes it ideal for short production runs.
In knifeless cutting, a blade is used to cut the shape of the gasket. It is a computer numeric control (CNC) process that uses computer-aided design (CAD) programming to guide the cutting of the material. The dimensions of the gasket are created in CAD and downloaded into the CNC machine that completes the process.
Waterjet cutting is a slower process than die cutting but does not involve tools such as dies and die shaping. The cutting process is completed using pressurized water that removes the substrate without waste or fumes. The only byproduct of the process is a light mist of water. Waterjet cutting has gained increasing popularity due to its being environmentally friendly.
Laser cutting produces gaskets with tolerances of ±0.0005. Several types of lasers are used to produce gaskets, including CO2 and ultraviolet lasers. More and more gasket producers are finding that there isn’t one standard size of gasket since technology and new designs are continually being implemented. These factors make laser cutting the ideal process for producing custom gaskets. As with knifeless die cutting and waterjet cutting, laser cutting uses CAD designs programmed into CNC machines.
Compression molding involves the use of a heated mold where the gasket material is placed in the heated mold and compressed. The compressed material is allowed to cure prior to being released from the mold. It is the perfect process for short low production runs and less intricate gaskets. The process of compression molding is ideal for manufacturers with limited space since the compression mold equipment has a small footprint. The compression molding process is ideal for the fabrication of flexible rubber materials.
The rubber to metal bonding process has several factors that have to be considered prior to the production of the gasket. A critical aspect of the process is the type of metal, which is usually steel but may also be aluminum. The metal to rubber bonding process is a complex chemical procedure that involves the interaction between the metal and the rubber.
At the beginning of the process, the metal gasket is treated mechanically or chemically to prepare
its surface for the application of the rubber compound. The mixture for the bonding includes a carefully measured combination of the bonding agent and solvent that can be dipped or sprayed onto the surface of the metal.
To ensure a tight seal between the bonding agent and the metal, the metal rubber gasket is compressed. This aspect of the process prevents any possibility of the rubber being removed or peeling.
Material and form are important gasket specifications, as they govern the gasket’s properties against corrosive attacks, extreme temperatures and pressures, mechanical loading imparted by the mating surfaces, and dynamic operating conditions. Depending on the type of material and construction, gaskets are divided into non-metallic, semi-metallic, and metallic gaskets.
Non-metallic gaskets are typically used for low to medium fluid pressures. In terms of temperature, they can handle both low and high ranges depending on the material used. Non-metallic gaskets can easily be manufactured and supplied in the form of sheets that are cut to shape through die-cutting, kiss cutting, and die pressing. Suppliers and parts storage do not have to stock particular forms since the gaskets can easily be cut to the requirements.
Some of the positive features of non-metallic gaskets include their ability to be easily compressed and have excellent scalability with low torque to seal. The liability of non-metallic gaskets makes it possible for them to conform to the desired shape of the application that they are sealing.
Non-metallic gaskets are made of homogeneous materials such as flexible graphite sheets and virgin PTFE or composite fibers and granules embedded in an elastomer resin. As technology progresses, more advanced materials are being developed that are proprietary to manufacturers. Common non-metallic gaskets include:
Of the various non-metallic gasket materials, PTFE is the most widely used due to its many positive properties: it has a high melting point, is hydrophobic, is chemically inert, has a low friction coefficient, and has exceptional flexural strength. PTFE is used in chemical processing because its high bonding energy makes it resistant to chemical reactions, particularly corrosion. The few chemicals that can degrade PTFE include fluorinating agents, magnesium, and molten alkali metals.
Although PTFE is a very strong material, various materials are added as fillers to reinforce its natural mechanical properties and enhance its strength. Some fillers include glass fibers, carbon, bronze, graphite, and molybdenum sulfide. The additional fillers improve PTFE’s wear, deformation strength, electrical properties, thermal conductivity, and friction coefficient.
Aside from its high chemical resistance, PTFE also has excellent insulating properties, toughness, and impact strength. The four forms of PTFE are virgin PTFE, filled PTFE, biaxially oriented PTFE, and expanded PTFE.
Plastics are low-cost, adaptable materials made from a wide range of plastic compounds. They are lightweight and low-friction materials with sealing and insulation properties. As an alternative to metal gaskets, plastics have high durability and can withstand a broad range of temperatures.
Aside from PTFE, plastics used to make gaskets include ABS, Acetal, Nylon, various polyethylenes, and polypropylene. The wide variety of plastics makes it possible to select the ideal sealability, pressure rating, and temperature to fit any application.
The main types of plastics are thermoplastics and thermosetting polymers, which are produced using different production processes and have different properties depending on production methods and materials.
Flexible graphite gaskets are made by expanding graphite flakes through intercalation, heating, and compression processes. High-quality particulate graphite flakes are mixed with nitric, phosphoric, and sulfuric acids. This chemical treatment creates graphite intercalation compounds that tend to exfoliate upon heating. The exfoliation process involves the expansion of the graphite by several magnitudes. The intercalated compounds diffused within the graphite tend to vaporize, forming gas pockets. After exfoliation, worm-like or vermiform structures with highly active, dendritic-like rough surfaces are produced. Compression results in a mechanical interlocking of these worm-like structures. After compression, a flexible graphite sheet is formed. Compared to other non-metallic gaskets, flexible graphite has poorer tensile strength. Reinforcements, laminates, and inserts are added to create a composite material that combines their strength with the pliability of graphite.
Flexible graphite is normally manufactured with some form of filler, such as foils and tang inserts. In most cases, the inserted foil or tang is stainless steel with other materials used as well.
Phyllosilicates are a group of minerals from the mica family used to make non-oxidizing, high-temperature gasket materials. As non-oxidizing properties, they solve the problem with graphite gaskets, which is their tendency to oxidize, or “coke,” at high temperatures in environments containing oxygen or other oxidizing agents.
The main classifications of phyllosilicates used in gasket production are mica and vermiculite, which have the same temperature and chemical resistance properties. Mica gaskets are formed from sheets that are created by combining the mica mineral with polymer and subjecting them to high heat. Vermiculite is mica that is capable of expansion. It is formed from the flash conversion of the water molecules between the layers of the crystal structure.
Mica material has excellent resistance to temperatures over 900°F (482°C), where flexible graphite cannot be used. As a gasket, mica is capable of sealing high-temperature applications and will not fail in the presence of oxygen. It comes in multiple forms, such as laminated, flexible, or rigid. It can be tanged with stainless steel to withstand higher pressures. It can be combined with polymers by heat treatment to increase its flexibility, which improves mica’s poor sealability.
Vermiculite gaskets have exceptional heat and chemical resistance, capable of enduring temperatures of 1832°F (1000°C). When vermiculite gaskets are tanged with stainless steel, they have sufficient strength to withstand 740 psi with exceptional sealability. The extraordinary strength of vermiculite makes it possible for vermiculite gaskets to survive and withstand the types of oxidation that graphite and other gasket materials cannot survive. Since it is thermally insulated, vermiculite gaskets are used in exhaust gas recirculation (EGR) applications where blockage of heat flow is necessary.
Elastomers are polymers with a highly elastic nature created by cross-linking long polymer chains into amorphous structures. The intermolecular forces between the polymer chains are relatively weak, allowing them to be reconfigured upon application of stress. Because of this property, elastomer gaskets can easily conform to the profile of the surfaces, creating a tight seal.
There is a wide range of elastomers on the market to meet specific requirements. Their chemical and temperature resistance, however, is inferior to PTFE. Depending on the type of curing reaction or vulcanization, elastomers can degrade under the presence of water, ultraviolet light, oils, and certain solvents. High temperatures can easily expand and melt elastomers, while low temperatures can make them brittle. Types of elastomers used for gasket manufacture are nitrile (NBR), ethylene propylene diene monomer (EPDM), neoprene, silicone, and fluoroelastomer (FKM).
Extruded rubber gaskets are flexible, lightweight, long-lasting, and exceptionally durable. They are made to endure hostile, harsh, and extreme environments, such as applications that involve exposure to chemicals or extremely high temperatures. Extruded rubber gaskets are manufactured using the extrusion process, where the softened rubber is forced through a die and comes in hollow sections, cord shapes, and squares. The properties of hollow cross-sections have exceptional sealing compression.
There are a wide variety of applications that use extruded gaskets, including sunroofs, garage doors, windows, windshields, and boat hatches. The tensile and sealing strength of extruded gaskets blocks noise and protects against moisture and extreme weather. The extrusion process has been used for years to produce cost-effective and high-quality products, which is one of the reasons it is used to manufacture gaskets.
As the name suggests, this type comprises naturally occurring mineral or synthetic polymer fibers. The asbestos gasket is one of the earliest known compressed fiber gaskets used for industrial applications. Asbestos is a naturally occurring silicate mineral with long and thin fibrous crystals. However, the manufacturing of asbestos gaskets is now being discontinued due to associated health hazards such as asbestosis and cancer. Substitutes for asbestos are carbon, graphite, glass, aramid, and other fibers.
Compressed fiber gaskets are produced by a process called beater addition. Beater addition is generally a proprietary process. In this process, the minerals are beaten, fibrillating the main fiber into tiny fibrils. This causes the fibers to spread; elastomer resins are added to bind the fibers together. Typical elastomers are styrene-butadiene rubber (SBR), NBR, neoprene, and EPDM.
Cork is a viable material for low-temperature and low-pressure applications. A gasket is made by compressing granulated cork bark and binding it with an elastomer resin. Cork gaskets are lightweight, flexible, and impermeable to water, oil, and other petrochemicals.
Poron Gaskets: Poron is a patented gasket material made from multicellular polyurethane. Its porous structure makes it well suited for thermal insulation, vibration dampening, acoustic dampening, and shock absorption. Polyurethane's inherent resilience and rebound properties make it suitable for sealing because of its reduced creep relaxation.
These types of gaskets are composites of metallic and non-metallic materials. The metallic component provides structural strength and increased toughness, while the non-metallic part offers enhanced sealing. The myriad of possible metal and non-metal component combinations and the different styles available enable semi-metallic gaskets to be suitable in almost every condition. The downside of using semi-metallic gaskets is that they are supplied in distinct sizes and shapes. They cannot be cut and shaped the same way as non-metallic gaskets. Semi-metallic gaskets must be dimensionally suitable with the mating surfaces, usually flange faces for piping. The different types of semi-metallic gaskets are as follows.
This type of semi-metallic gasket is composed of V-shaped metal strips wound alternately with a filler material. An inner and outer ring supports the winding. The inner ring is the part in contact with the process liquid, apart from the windings. Thus, its material has higher requirements than the outer ring, which is typically made of carbon steel. The inner ring and metal windings are usually made from stainless steel, while the filler can be PTFE, non-asbestos fibers, or graphite.
In this type, the filler material is partially or entirely enclosed in a metal jacket. There are several forms and configurations available such as single, double, and corrugated jackets. Sealing is achieved by deformation of the metal overlap, which is thicker than the rest of the envelope. This thicker section bears more of the compressive load creating the seal.
Corrugated metal gaskets are composed of a thin metal ring with a wave or corrugated pattern. They are coated with a soft layer of a non-metallic material such as graphite, PTFE, and ceramic layers. Their working principle is based on the conformity of the soft layer to the surface irregularities. Corrugated gaskets are suitable for uneven flanges or flanges with surface imperfections.
CMG gaskets are used with specialty flanges and are not designed to be used with piping. As a specialty gasket, they have a limited range of uses, which needs to be carefully considered when applying them to an application. The best use for CMG gaskets is heat exchangers and expansion joints for petrochemical applications. They are ideal for resisting radical shearing with slight compressibility and recovery.
This type of semi-metallic gasket is composed of a grooved metal ring with a non-metallic facing material covering the grooves. Sealing is achieved in a similar way as corrugated gaskets. Compressing the gaskets forces the soft material to conform to the surface of the flange, while the grooved metal faces create concentric rings that further stress the soft material. The grooves enhance the sealing capabilities and provide structural support to the gasket. The facings on Camprofile gaskets are very thin at ~ 0.020” (0.50 mm) and do a poor job of conforming to flange surfaces, which is why flanges must be flat and have no surface irregularities.
Extremely high temperatures and pressure cause non-metallic gaskets and filler sealing materials to fail. In this case, solid metallic gaskets are the only option. They are normally used in boiler and heat exchanger sealing. Similar to semi-metallic gaskets, metallic gaskets are supplied in standard shapes and sizes and must be dimensionally compatible with the mating surfaces. The types of metallic gaskets are ring-joint, flat metal, and grooved metal gaskets.
These are gaskets with thick cross-sections suitable for high-temperature and high-pressure applications. This gasket works by tightly compressing and crushing it between the mating surfaces. This forcefully flows the metal into the surface imperfections and leak paths. The materials used are softer than the flange material. Examples of RTJ gasket materials are soft iron, low carbon steel, stainless steel, and special alloys such as Inconel and Hastelloy.
Unlike the RTJ, this metal gasket has a thinner cross-section. These gaskets are cut from sheet metal; thus, they can be made to match any surface’s shape and size. They operate the same way as non-metallic gaskets but are more suitable for higher temperature applications. Also, they can only be used for applications with high bolt loads.
Grooved metal gaskets are similar to the flat metal gasket; however, serrations or grooves are present on the surface. The peaks of the concentric rings experience higher stresses when loaded. Sealing is achieved by creating a labyrinth seal effect along the grooved surface. Grooved metal gaskets are often made from materials like stainless steel or other alloys.
This type of gasket does not primarily rely on the compression of the gasket along the mating surfaces. Rather, they achieve sealing by having a permanent welded connection between the surfaces. Welded gaskets are often made from materials such as stainless steel, carbon steel, or other metals with good resistance to corrosion and high-temperature conditions.
When selecting a gasket for an application, it is crucial that all of the application parameters be explored in detail to make the proper selection. To simplify the process and orient customer thinking, manufacturers have developed an acronym that represents the essential factors to be consider: S. T. A. M. P. or "size, temperature, application, media, and pressure."
Most gaskets are used in standard ANSI flange connections. In the case of non-standard flanges, it is important to take detailed dimensions of the connection and any bolts or fasteners used. The provided information determines the contact area and assembly stress, which are key factors for producing tightly sealed connections.
Temperature affects the mechanical and chemical properties of the gasket. Two mechanical properties are affected by temperature—creep and relaxation. Creep is the loss of gasket thickness when subjected to a constant load, while relaxation is the loss of compressive stress under constant deformation. Both of these effects are augmented by rising temperatures, resulting in a decreased sealing characteristic of the gasket. Regarding the chemical properties, the effects are particularly evident in graphite gaskets and gaskets with elastomer resins. Graphite tends to oxidize at high temperatures. As oxidation consumes the graphite material, the gasket loses its sealing potential. For elastomer resins present in full elastomer gaskets or elastomer binders, high temperatures can further cure or vulcanize the gasket, making it more brittle and reducing tensile strength. When purchasing gaskets, always look for the pressure-temperature curves or the maximum operating limits of the gaskets and verify if it suits the intended application.
Determining the size or dimensions relates to the application and the type of equipment where the gasket will be used. Additionally, the application aspect of the selection process concerns the end use of the gasket and where it will be installed. The type of application is the guiding factor as to what materials will be used to manufacture the gasket.
The process fluid determines the pressure and temperature, wherein the effects of the external environment are almost negligible. The process fluid also has other properties that can dictate the compatibility of the gasket. The presence of oxidizing agents, acids, alkalis, oil, water, and abrasive media can degrade the material directly in contact with the fluid. That is why composites are widely popular since a highly chemical-resistant inner ring can be used to absorb the attacks of the process fluid while maintaining the desired sealing and structural characteristics of the other components.
In normal operation, a gasket experiences three forces or loads. These are the bolt or flange load, the hydrostatic end force, and the blowout or the force from the internal pressure. The pressure inside the vessel or pipe directly affects the hydrostatic end and blowout force. When these forces exceed the tensile strength of the gasket, rupture of leakage will occur. The gasket must be able to resist the maximum internal pressure that can occur within the vessel. This is typically the test pressure, or the pressure used to check the integrity of the equipment. The test pressure is commonly 1.5 times the working pressure. Gaskets are usually specified with a pressure rating or a pressure class number standardized by engineering associations such as the ASME and DIN.
Gasket thickness is not critical for metal and semi-metallic gaskets, as the thickness is already standardized for a given pressure rating. The effect of gasket thickness is only evident on non-metallic gaskets. Thicker non-metallic gaskets generally have lower pressure and temperature ratings. In order to achieve the required sealing, thicker gaskets must be compressed with greater force. Thinner gaskets offer better blowout resistance, lower creep relaxation properties, and better compressive strength. It is best to select the thinnest non-metallic gasket material that can conform to the flange irregularities.
Gaskets are mechanical seals that are used to fill the gap or space between two mating surfaces in order to prevent leakage of fluids, gases, or other substances. They offer several benefits in various industrial and mechanical applications:
Gaskets are widely used in a number of industries. Here are some common applications and uses of gaskets:
The system safety safeguards are intentionally designed to fail during process abnormalities. The next weakest point in the system is the gaskets. Gaskets are usually the first to burst during the overpressure of pipes or pressure vessels. Even if the gasket has the right specifications, there is still plenty of reason for these components to fail. Enumerated below are the most common causes of gasket failures.
Over Compression: Over compression can lead to permanent gasket failure. Signs of over-compression are bulging or extrusion of the gasket material, or inward buckling for spiral wound gaskets. Non-metallic gaskets are typically limited to 15,000 psi. Metallic gaskets are designed to be crushed at higher pressures up to 30,000 psi.
Gaskets are seals that are mechanically made to prevent either process fluids from escaping or contaminants from entering the delicate areas. Each given system has its best suited gasket, and it is critical to make the right...
The head gasket is a motor engine component that seals the combustion part of the engine so that oil and the motor coolant circulate. The head gasket also seals the combustion chamber inside the engine...
Rubber gaskets are elastic components used for mechanically sealing the microscopic gap between two mating surfaces or joints. Examples of these surfaces are flange faces of piping and fittings, mating surfaces of an...
Molding is a manufacturing process that uses a mold - the latter being a solid container used to give shape to a piece of material. It is a forming process. The form is transferred from the mold to the material by...
Die cutting is the mass fabrication of cut-out shapes by shearing a stock material such as paper and chipboard using tooling called a die. A die is a specialized tool used in manufacturing to cut or shape a material fitted into a press...
Hydraulic seals are a form of gasket-like rings that are used to fill gaps between hydraulic cylinder components. Many different components are found in hydraulic cylinders, some of which get in...
Kiss cutting is a method for cutting into a material where the upper layers are pierced, but the back layer is left intact. The term "kiss" refers to the way the blade touches the upper layers of the material and leaves a pattern...
An O-ring is a round elastic loop that is used as a seal for static and dynamic applications. Their main purpose is to serve as a seal between structures such as pipes, tubes, in pistons, and cylinders. O-rings are made of...
Rubber injection molding is when uncured rubber is transformed into a usable product by injecting raw rubber material into a mold cavity made of metal. The applied pressure produces a chemical reaction like...
Rubber molding is a process of transforming uncured rubber or an elastomer into a usable product by transferring, compressing, or injecting raw rubber material into a metal mold cavity...
A rubber O ring is a mechanical gasket in the shape of a torus or donut and is used for static and dynamic applications where there is relative motion between parts and the possibility of friction. Some of the benefits of rubber O rings are...
There are several methods to perform rubber overmolding, and each method has its own unique advantages and disadvantages. The choice of method typically depends on the design and material requirements of the product being...
Silicone rubber molding is a method for shaping, forming, and fabricating silicone rubber parts and products using a heated mold. The process involves compressing or injecting silicone rubber into a mold...
A grommet edging is a flexible rubber or plastic strip that covers rough and sharp surfaces found in openings and edges of panel walls to protect the passing electrical cables, wires, and other sensitive components...