Compression Molding
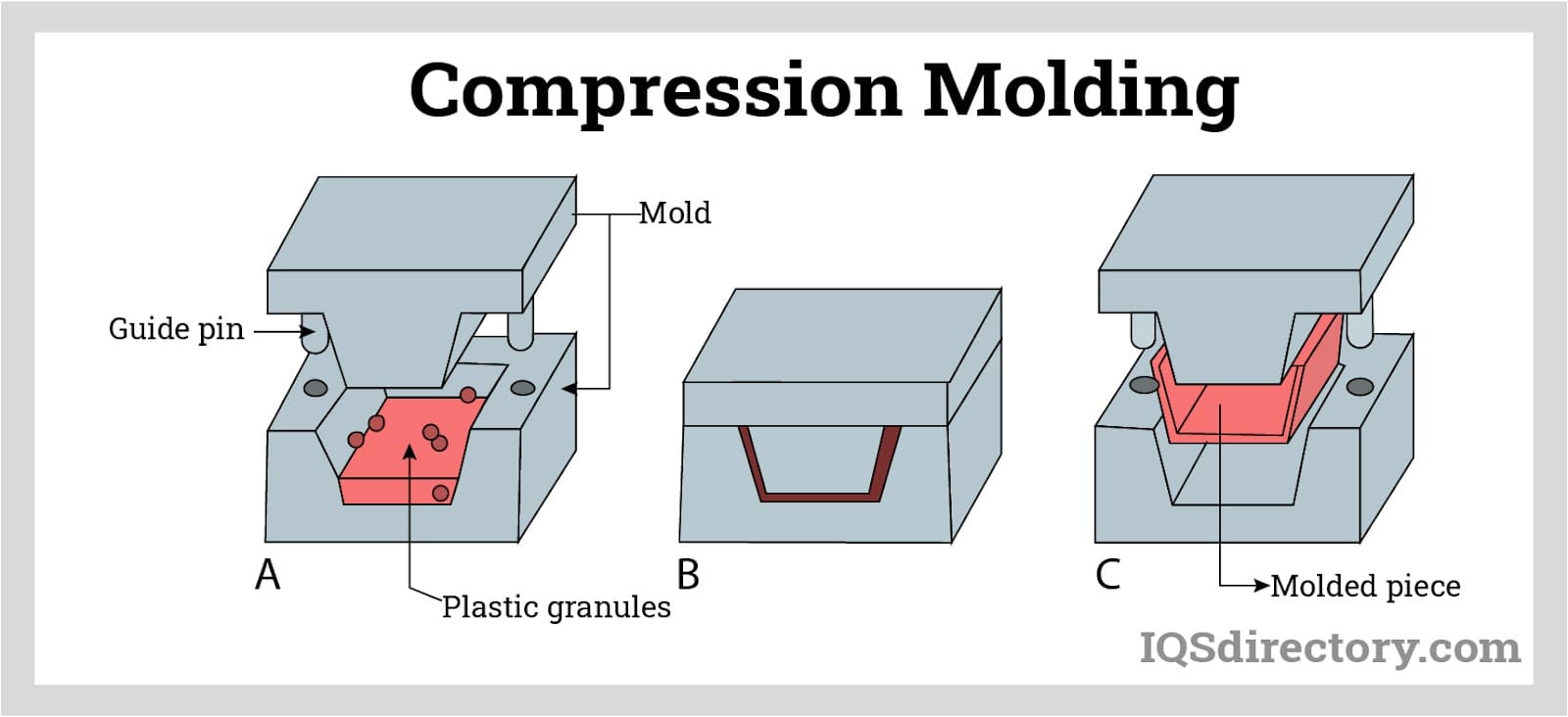
Molding is a manufacturing process that uses a mold - the latter being a solid container used to give shape to a piece of material. It is a forming process. The form is transferred from the mold to the material by...
Please fill out the following form to submit a Request for Quote to any of the following companies listed on
From this article, you will learn what silicone rubber molding is, its products, and their uses.
You will learn:
Silicone rubber molding is a technique for creating silicone rubber components by using a heated mold. This process involves either compressing or injecting silicone rubber into a mold, allowing it to conform to the shape of the mold cavity. The primary methods for producing silicone rubber molded parts include injection molding, compression molding, and transfer molding, each utilizing molds typically made from steel or cast iron.
The various forms of silicone rubber vary in their hardness and pliability, which makes the material an ideal choice for applications that require durability and flexibility with resistance to high and low temperatures and wear. In many applications, silicone rubber is used in place of other forms of rubber due to its ability to withstand temperatures above 100°C (212°F), a characteristic that makes it ideal for use as medical instruments and seals and gaskets for engines.
Silicone rubber was initially developed to provide insulation for electric generators and motors. As its numerous beneficial properties became apparent, silicone rubber transitioned into a versatile material widely used in both household and industrial applications. Selecting the appropriate type of silicone rubber can significantly improve the efficiency of a product or component. Its notable heat resistance stems from its unique composition, which includes silicone, hydrogen, carbon, and oxygen.
As a contemporary elastomer, silicone rubber possesses characteristics that set it apart from other organic elastomers like natural rubber, latex, and polyurethane. It is primarily composed of silicone and oxygen, two abundant elements found on Earth in forms such as silica and silicate. Although the silicon base for silicone rubber was identified in the early 1800s, it did not gain commercial significance until the mid-20th century.
At the time of its initial synthesis, silicone rubber was not considered to have any practical or marketable applications. During the 20th century, electric motors and generators were integral to industrial processes, and these machines required heat-resistant materials due to the substantial heat they produced. Initially, resin-coated glass fibers were thought to be a viable solution, but they ultimately proved inadequate as they could not withstand the high temperatures generated by smaller motors.
The quest for a material that could resist heat led scientists to create the first silicone polymer capable of enduring the intense heat from motors and generators. This breakthrough in 1943 paved the way for the mass production of silicone rubber, spearheaded by Dow Chemical and Dow Corning. As engineers continued to explore its properties, they uncovered a wide range of additional uses for silicone rubber in various products.
Silicone rubber is classified, in part, using the Shore hardness scale, a method that assesses how resistant a material is to deformation under pressure, utilizing a device called a durometer. Higher durometer readings correspond to greater resistance to indentation. The Shore scales include Shore A, Shore D, and Shore 00, with Shore 00 specifically designed to gauge the softness of extremely pliable materials. Each scale spans from 0 to 100, where 0 denotes very soft, non-metallic substances, and 100 signifies the hardest materials.
By modifying the base polymer with reinforcing fillers and additives, the properties of silicone rubber, such as thermal conductivity, fire resistance, chemical stability, flame retardancy, and resistance to extreme temperatures, can be tailored to suit specific applications. These adjustments are made to enhance the durability and performance of silicone rubber, ensuring it meets the requirements of its intended use. The classification of silicone rubbers is ultimately determined by these properties.
Standard silicone rubber typically exhibits a Shore hardness ranging from A 30 to A 70, making it suitable for everyday items like kitchen utensils and cookware. This versatile material is also ideal for various manufacturing processes, such as compression molding and extrusion, and is commonly used to produce products like tubing and automotive components.
Low hardness silicone rubber, the softest among its classifications, features a Shore hardness between A 5 and A 20. This material is commonly used in the production of baby bottle nipples, food storage wraps, anti-slip mats, and shoe insoles. Its extensive applications are largely attributed to its exceptional elasticity, allowing it to be stretched and reshaped to multiple times its original size without tearing.
Once cured, high hardness silicone rubber reaches a Shore hardness of up to A 90. This type of silicone rubber is characterized by its excellent elongation and tear strength, making it ideal for molding, extrusion, and calendaring processes. It is often used to create products that require high abrasion and fatigue resistance. Items made from high hardness silicone rubber can be either transparent or translucent and possess remarkably high tensile strength.
High strength silicone rubber is engineered to endure significant elongation and tearing, offering exceptional resistance to abrasion and fatigue. Similar to high hardness silicone rubber, it is widely utilized in molding, extrusion, and calendaring processes. With a tear strength ranging from 29 to 49 kN/m, high strength silicone rubber far surpasses the general silicone rubber, which typically has a tear strength of 9.8 kN/m.
Silicone rubber is commonly available in red, black, or gray, and comes in various forms and shapes. Additionally, transparent silicone rubber sheets are used in liquid injection molding. This type of silicone rubber has a Shore hardness range from A 10 to A 70, with Shore A 40 being the most frequently used. Its transparency allows it to function as an unobtrusive gasket in cosmetic products, preserving their aesthetic appeal. Transparent silicone rubber is often employed as air flow diaphragms in ventilators and respirators.
Flame retardant silicone rubber is engineered to offer superior thermal conductivity and heat resistance, making it suitable for use in environments exposed to fire or direct heat. It possesses self-extinguishing properties. To produce flame-retardant silicone rubber, a specific blend of compounds is mixed in precise amounts and subjected to special curing processes. While all silicone rubbers inherently have some degree of flame resistance, this characteristic is significantly enhanced in flame retardant silicone rubber through the incorporation of additional blockers.
Thermal conductive silicone rubber effectively transfers heat away from delicate components and is commonly used in applications involving CPUs and electronic enclosures. As electronic components become increasingly compact, it has become crucial to manage the excess heat they produce to prevent damage to their electrical functions. Silicone rubber’s versatility in thickness and form makes it an optimal material for heat dissipation in small electronic devices.
Electrically conductive silicone rubber has all of the normal properties of silicone rubber but is compounded with carbon and other materials that are electrically conductive. It is used to reduce or eliminate electromagnetic interference (EMI) and radio frequency interference (RFI) noise that is found in various electronics. Electrically conductive silicone rubber is referred to as metallized silicone, which refers to the various metals that are placed in the rubber such as Monel or aluminum wire.
Silicone rubber’s heat resistance is attributed to its low thermal conductivity, which allows it to transfer heat minimally. It maintains its properties even at temperatures up to 150°C (302°F). This heat resistance stems from the stability of its chemical structure, characterized by tightly bound and exceptionally stable siloxane bonds.
Oil resistant silicone rubber retains its structural integrity when exposed to oils. Its high temperature resistance, combined with its oil resistance, makes it particularly suitable for applications involving oil exposure.
Fluorosilicone rubber features a similar structure to standard silicone rubber but includes fluorine in its polymer chain. It combines the advantageous properties of both fluorocarbons and silicones, offering resistance to solvents and oils, exceptional stability at both low and high temperatures, and resistance to deformation under pressure. Fluorosilicone rubber can be molded, extruded, and calendered like other silicone types and is extensively used in aerospace and automotive sectors. Its standout feature is its superior resistance to fuels, oils, and chemicals, making it a more costly option compared to regular silicone rubber.
The organic groups in silicone rubber include materials such as methyl, vinyl, phenyl, and fluorine. The terminology for these classifications is outlined in ASTM D1418 standards.
Silicone, or polysiloxane, is a polymer characterized by its rubber-like texture, with molecular chains composed of silicon and oxygen atoms. Unlike many other polymers, silicone does not have a carbon-based backbone. Its main component is silica, commonly sourced from sand. Unlike silicon, silicone is more flexible, softer, and can withstand extreme temperatures without degradation.
Silicone production starts with extracting silicon from silica or silicates by heating quartz sand to 1800°C (3272°F). This sand is prepared by crushing, grinding, and washing sandstone or quartzite to ensure a fine grain distribution. The resulting pure silicon is then reacted with methyl chloride to produce dimethyldichlorosilane (DMDCS), which is hydrolyzed and stirred to create polydimethylsiloxane (PDMS) chains.
Cross-linking of PDMS is achieved through heat or radiation, forming bonds between the PDMS chains and resulting in a three-dimensional network structure. Different types of silicone are created by incorporating phenyl, methyl, fluorine, or vinyl groups into the PDMS chains during synthesis. These additional groups impart unique properties and characteristics to the silicone rubber. The final compound can be molded or extruded into various shapes.
The last stage in silicone rubber production involves shaping the material for different rubber products. This is done by incorporating fillers and additives to improve specific properties and introduce color. The manipulation processes are tailored to achieve the desired characteristics for the intended industry application.
Silicone rubber additives:
Silicone rubber is shaped and configured using various techniques tailored to the specific product or component being produced. After shaping, the rubber undergoes vulcanization, where a curing agent is used to heat the material and cross-link the polymer chains. High temperature vulcanization (HTV) occurs at temperatures between 150°C and 200°C (302°F to 392°F), whereas room temperature vulcanization (RTV) is performed at ambient temperature.
HTV vulcanization, conducted in a heat press for several minutes, is utilized to produce high-strength silicone rubbers suitable for industrial applications. RTV curing is a slower process, using a platinum catalyst and typically taking around 24 hours, to create soft and pliable silicone rubber products, ranging from very soft to medium soft.
Silicone rubber is often used to create silicone molds for various applications, including mold making with materials like resins, gypsum, wax, and more. These silicone molds are valued for their durability, longevity, and exceptional repeatability, making them ideal for producing custom products and designs. The inorganic properties of silicone rubber help it withstand temperature fluctuations, chemical exposure, and natural contaminants such as bacteria and fungi.
Silicone molds are frequently employed for prototype creation to evaluate product designs. Metal molds, which are time-consuming, labor-intensive, and expensive to produce, can be substituted with silicone molds for a more cost-effective solution. Beyond prototyping, silicone molds are used to create beta units for market testing and gathering consumer feedback. While 3D printing is suitable for quickly producing one-off samples, silicone molds are effective for short production runs used in testing phases.
Manufacturers often opt for silicone molding because it allows for the rapid and straightforward creation of molds without the need for complex machining or specialized tools. The first decision in the process is whether to use a single-piece or a two-piece mold. This choice depends on the design of the master model, with two-piece molds generally requiring more time to produce.
The one-part open face mold is the most basic type of silicone rubber mold. It is best suited for flat-backed masters that do not have undercuts and works well for molding rigid materials such as ceramics and silicone rubber.
The initial steps for making a two-part silicone mold are similar to those for a one-part mold, starting with the creation and selection of the master model.
Silicone rubber is an excellent choice for mold making due to its durability and strength. Silicone rubber molds can be reused multiple times to produce various parts, components, and decorative items. The mold-making process with silicone is efficient and straightforward, allowing for quick adjustments to meet customer specifications, which is crucial in today’s industry.
In two-part silicone rubber molds, the precise fit between the mold halves helps minimize the formation of a parting line during the casting process. In contrast, one-part silicone molds, because of their design, inherently avoid the creation of any parting lines. Regardless of the mold type, silicone molds offer the necessary properties to produce high-quality castings.
Silicone rubber is an essential part of a wide range of products and is manufactured using a variety of methods, each of which is capable of producing parts that meet the expectations and requirements of an application. The choice of fabrication method varies between molding processes, extrusion, and calendaring with each method able to produce parts with the correct hardness, heat resistance, and electrical conductivity.
The extrusion process for silicone rubber parts involves heating and compressing raw silicone through a die that defines the cross-sectional shape of the finished product. Raw silicone rubber is fed into a hopper connected to the extruder's barrel. Inside the barrel, one or more screws move the material toward the die, where it is heated, melted, and compressed. As the silicone is pushed through the die, it assumes the desired shape, then it is cooled, cured, and cut to the required lengths.
Extrusion can be carried out in various forms, such as film and sheet extrusion, each offering specific advantages. This process is cost-effective, supports high-volume production, and is well-suited for creating items like tubing, gaskets, seals, and wire insulation.
Calendaring is a method used to produce thin silicone rubber sheets using rollers or bowls, where each roller turns in the opposite direction to its counterpart at a consistent and controlled speed. In a pair of rollers, one has a nip adjustment that regulates the thickness of the silicone rubber. A silicone rubber calendar may have two or more rollers. The silicone material is heated and introduced into the rollers in strip or pig form on one side of the nip, where it is compressed to create sheets of silicone rubber.
Injection molding is the most common process for forming silicone rubber parts that vary in size, complexity, and final application. The process involves the use of a screw type plunger that is similar to that of an extruder. As with an extruder, the raw silicone material is loaded into a hopper connected to the barrel and screw. The material is heated as it moves along the barrel toward a tightly sealed die that has the shape of the final part. The pressure created by the movement of the screw forces the raw material into every portion of the die.
As the pressure of the injection machine increases, the density of the shot, or the amount of material injected into the die, also rises, filling the die cavity. Maintaining a slow, steady movement of the screw is crucial for ensuring continuous and uniform pressure. During the injection process, the silicone rubber cools, which speeds up solidification and accounts for approximately 80% of the molding cycle.
Liquid injection molding utilizes liquid silicone rubber, which is injected into the mold cavity through a nozzle. Unlike standard injection molding, liquid injection molding involves mechanically mixing the silicone rubber before injection using two plungers. One plunger holds the base material along with additives and fibers, while the other contains the catalyst compound that initiates the mixing process.
Liquid injection molding offers several benefits, including reduced curing time, the capability to create intricate and precise designs with tight tolerances, high-volume production, automated process control, and the use of thermal imaging to minimize molding defects.
Compression molding includes the use of heated molds that contain the precise amount of silicone rubber, referred to as the charge, to form the final product. A heated plunger that has the upper half of the mold attached to it applies 15,000 psi to 20,000 psi of pressure to drive the silicone material to every corner of the upper and lower halves of the mold cavity. The pressure is maintained until the silicone rubber component completely cures.
The primary advantage of compression molding is its cost-effectiveness, making it well-suited for low-volume production runs. This process can handle the production of both small, detailed parts and larger, complex components with minimal setup time.
Transfer molding employs a mold, a plunger injection machine, and silicone rubber material. The process starts by loading the raw silicone rubber into a transfer pot positioned below the plunger and above the mold. Under high hydraulic pressure, the plunger pushes the silicone rubber through a small sprue at the top of the mold into the cavity, where it is securely held and allowed to cure.
Transfer molding is known for its precision, resulting in components with minimal flash and waste. It excels at producing parts with tight tolerances and complex shapes, offering better control over dimensional accuracy. Although it shares similarities with compression molding, such as using compression to form parts, transfer molding differs in that the mold cavity is not split into two halves, and the raw silicone rubber is placed in the pot rather than in the lower half of the mold.
Silicone rubber is highly versatile and easy to work with, making it one of the most popular materials in both industrial and commercial applications. Its numerous beneficial properties, combined with its durability and long lifespan, mean it rarely needs replacement. Silicone rubber is commonly used in products such as kitchen utensils, toys, gaskets, seals, and automotive components.
Silicone rubber is frequently used for insulating wires and cables, as well as for applications such as connector seals and switch boots. Its resistance to high temperatures and harsh weather conditions makes it an excellent choice for insulation. Even after extended use, silicone rubber insulation remains flexible, waterproof, and resistant to arcing and cracking. Its strength and durability ensure the protection of even the most sensitive components.
Hoses, gaskets, seals, and other vehicle components are essential for the safe and continued performance of a vehicle. They have to be able to endure the harsh treatment they have to withstand during the operation of a vehicle’s engine. It is for these reasons that silicone rubber is the material that is used to produce the most critical components of an engine. It has the strength, toughness, and impact resistance required and is long lasting.
Parts and components used in aerospace applications must be highly durable and able to endure continuous stress. Key considerations in aerospace manufacturing include resistance to extreme temperature fluctuations, radiation, and regular exposure to various chemicals. Silicone rubber's high performance and resilience make it ideal for meeting the demanding conditions of aerospace environments.
The Food and Drug Administration has set strict standards for materials used in medical equipment due to the critical nature of patient care. These regulations require materials to be chemically inert, biocompatible, and capable of being sterilized. Unlike materials for aerospace or automotive applications, medical devices must function under sanitary conditions and withstand continuous use, such as with catheters and tubing.
Silicone rubber is well-suited for medical applications because of its flexibility, transparency, and lubricating properties. It is used not only for tubing and wound protection but also for orthopedic padding and other body-contact devices. Due to its durability and biocompatibility, silicone rubber is also used for implants and body part replacements.
Silicone rubber is commonly used in food and cookware production due to its non-toxic and food-safe properties. It meets the standards set by the Food and Drug Administration (FDA) and can be manufactured in a variety of appealing colors. Silicone rubber is especially popular in bakeware because it does not leach or affect the taste or smell of the food being prepared.
Silicone rubber utensils are non-stick and easy to clean. They require less oil during food preparation, contributing to healthier and more nutritious meals. Available in various shapes, such as baking pans and mixing bowls, silicone cookware is dishwasher safe and can be washed by hand without scratching or damaging.
The unique molecular structure of silicone allows it to exist in various forms, including liquid, solid, semi-viscous paste, oil, grease, and rubber. Its versatility makes silicone rubber suitable for a wide range of applications, including those that require both functional and aesthetic considerations.
Silicone rubber is renowned for its exceptional resistance to high temperatures, making it a preferred choice for industrial applications such as gaskets, seals, and plugs. It can maintain its properties across a broad temperature range, enduring up to 200°C (392°F) for extended periods and withstanding temperatures above 350°C (662°F) briefly.
In addition to its high-temperature resistance, silicone rubber remains flexible and crack-resistant in cold temperatures, retaining its elasticity down to -70°C (-94°F), where other organic rubbers may become brittle. Its ability to maintain performance over a wide temperature range makes it highly reliable in various conditions.
Silicone rubber is non-toxic and easy to sterilize. It is non-porous, which makes it impossible for bacteria or viruses to build up and grow. This aspect of silicone rubber makes it ideal for the manufacture of medical equipment, food processing devices, and cookware. When silicone items are cleaned, solvents easily remove any surface contamination. Additionally, the sanitary property of silicone rubber makes it the ideal material for use in cleanrooms and environments that require a high standard of cleanliness.
Silicone rubber retains its properties when exposed to oils, solvents, and various chemicals. Even when submerged in water, it maintains its mechanical strength and electrical characteristics. Its resistance to high temperatures and oil makes it a valuable material in motors, and it is unaffected by polar organic compounds and dilute acids.
UL 94 HB is a classification by Underwriters Laboratories (UL) that measures the horizontal burning rate of materials. It categorizes materials based on their burning rate under different conditions, with HB representing the slowest rate. Silicone rubber is rated UL 94 HB, indicating limited black smoke production and no release of toxic gases when burned.
Materials that are chemically or physiologically inert do not react with other substances and are characterized by their stable electron arrangement. Referred to as group 0 for their zero reactivity, silicone rubber belongs to this category due to its non-reactivity with other materials, making it suitable for use with living tissue and ensuring its biocompatibility.
The greatest advantage of silicone rubber is its versatility. By altering the manufacturing elements or curing agents, silicone rubber can be customized to exhibit lower compression set, improved resistance to flames, water, steam, and temperature variations. It can be produced in translucent or colored forms, and its durability ensures it remains reliable and effective for decades.
As with many types of industrial equipment, the leading suppliers of silicone molding machines are primarily located in Asia. These manufacturers offer a diverse range of silicone manufacturing equipment, including both injection and compression molding designs.
The JD-RL Series is an injection molding machine designed to handle all types of rubber, whether synthetic or organic, utilizing a low bed structure. It comes standard with a PLC, with microcomputers available as an optional upgrade. JD-RL machines feature both direct and indirect clamping and include a specialized nozzle design that prevents overflow. While many features are standard, the JD-RL Series can be customized and configured to meet specific and unique requirements.
The KTVK 85-300T is engineered for flexible and adaptive production, specifically designed for silicone injection molding in large, high-volume operations. It functions as a compression injection molding machine and is equipped with all the necessary features to manufacture HTV silicone through compression. The machine also includes an LSR dosing system, allowing HTV molds to be used with LSR for enhanced efficiency.
The YL3-V440L is a fully automated molding machine that incorporates new core technology for improved precision and reliability. It features a smart operating system with minimal maintenance requirements and user-friendly design. The YL3-V440L provides extensive data support for modern manufacturing processes and includes an L3R injection system, a D1 clamping structure, and an ID card reader for customizable permission levels.
The L90 – 160T is capable of molding both liquid silicone rubber and standard silicone rubber. It boasts an energy-saving capacity ranging from 58 tons to 3800 tons and a clamping force of 1600 kN. A distinctive feature of the L90 – 160T is its ability to mold LSR materials of varying hardness with consistent efficiency and quality. This machine is used to produce a wide range of products, including toothbrushes, oxygen masks, catheters, mobile phone cases, and valves and seals.
The Allrounder Hidrive hybrid injection molding machines from Arburg offer advanced technology for exceptional performance. Featuring a servo-electric clamping unit and a hydraulic injection unit with hydraulic accumulator technology, these machines automatically adjust pressure levels to meet product requirements. The self-adjusting hydraulic accumulator is designed to save energy while ensuring product quality. In addition to high efficiency, the Allrounder Hidrive injection system is engineered for maximum energy savings, providing a cost-effective production solution.
Molding is a manufacturing process that uses a mold - the latter being a solid container used to give shape to a piece of material. It is a forming process. The form is transferred from the mold to the material by...
Rubber injection molding is when uncured rubber is transformed into a usable product by injecting raw rubber material into a mold cavity made of metal. The applied pressure produces a chemical reaction like...
Rubber latches are latches made of rubber or are composed of rubber components. They are used in the automotive, aerospace, and medical equipment industries due to their flexibility, durability, and non-abrasive properties...
Rubber molding is a process of transforming uncured rubber or an elastomer into a usable product by transferring, compressing, or injecting raw rubber material into a metal mold cavity...
There are several methods to perform rubber overmolding, and each method has its own unique advantages and disadvantages. The choice of method typically depends on the design and material requirements of the product being...
A rubber bushing is a form of vibration isolator that is placed between two parts to limit the motion between them and absorb, mollify, and buffer the energy produced by their interaction. They are very...
Extruded rubber is a group of products made by softening and pressurizing an elastomeric compound and forcing it to flow through a hard tool called a die. The resulting product is a continuous piece of material that has the same cross-section throughout its length...
Rubber gaskets are elastic components used for mechanically sealing the microscopic gap between two mating surfaces or joints. Examples of these surfaces are flange faces of piping and fittings, mating surfaces of an...
A rubber O ring is a mechanical gasket in the shape of a torus or donut and is used for static and dynamic applications where there is relative motion between parts and the possibility of friction. Some of the benefits of rubber O rings are...
A rubber roller is a machine part that is composed of an inner round shaft or tube covered by an outer layer of elastomer compounds. The inner shaft is made of steel, aluminum alloys, or other strong and rigid material composites...
Rubber sheets are basically sheets made of rubber or cloth that are coated with rubber to improve the mechanical properties of rubber sheeting such as increased tensile strength and reduced elongation...
Rubber to metal bonding is when a rubber part has to be adhered to a metal part, a metal component is chemically prepared and is attached or encapsulated as part of the process to become a bonded rubber part...
Rubber trim is an extruded, sometimes molded, elastomer that is used to protect the edges or surfaces of objects from sudden impacts. They are usually found on panels, windows, doors, removable covers, and hatches...
Rubber tubing, also known as rubber hose or rubber piping, is made of natural and synthetic rubber and is used to circulate and transport liquids and gases for household and industrial uses. The natural or synthetic rubber materials used for the manufacture of rubber tubing...
Urethane casting is the process of injecting polyurethane and additive resins into a soft mold usually made of silicone elastomer. The casting process is similar to injection molding; injection molding differs by using hard, metal molds...
A grommet edging is a flexible rubber or plastic strip that covers rough and sharp surfaces found in openings and edges of panel walls to protect the passing electrical cables, wires, and other sensitive components...