Door Latches
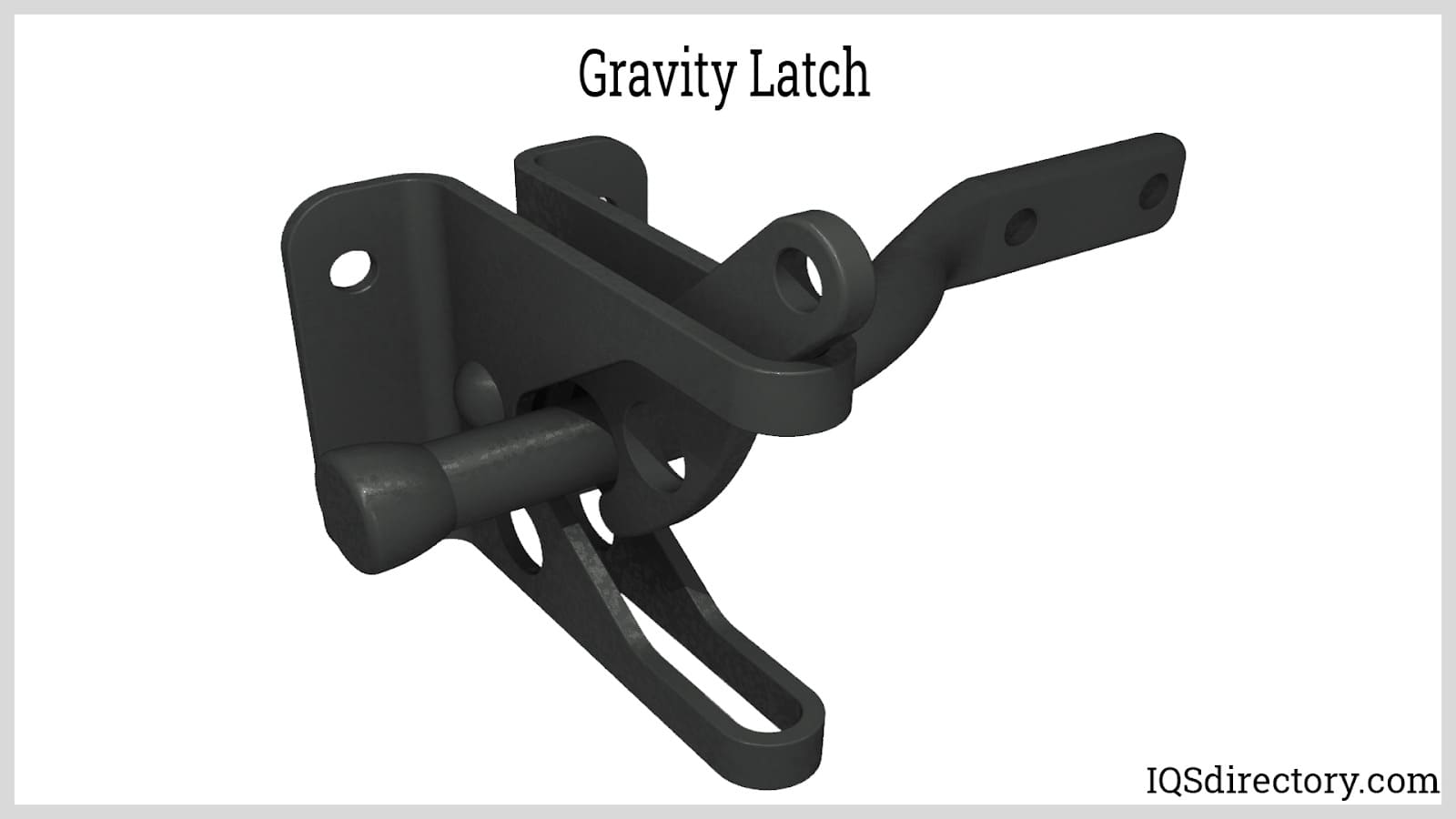
A door latch is a mechanical fastener that connects two surfaces or objects and provides a secure, safe, and strong connection. The latch portion of the mechanism is mounted on a flat surface such that when it meets a...
Please fill out the following form to submit a Request for Quote to any of the following companies listed on
This article contains everything you need to know about rubber latches and their use.
You will learn:
Rubber latches are components used by industries to secure and fasten objects, surfaces, and openings. Their flexibility and durability coupled with their ability to provide a secure grip, make them valuable for a wide range of applications. Made of rubber or composed of rubber components, they are used in the automotive, aerospace, and medical equipment industries due to their strength and longevity. Rubber latches provide secure and tight closure of doors and lids where surfaces connect.
The structure of a rubber latch includes a flexible rubber strap, attached to a frame, that is stretched to secure and close an opening. The key feature of a rubber latch is its elasticity and stretchability such that it can be pulled over a hook, knob, or some form of anchor point. The placement of the strap creates tension that keeps the latch securely closed and in place.
Rubber latches are indispensable fastening solutions, offering versatility, durability, and ease of use. Their flexible design and secure grip make them ideal for keeping objects and equipment firmly in place, under demanding conditions. As technology advances and new materials emerge, the design and functionality of rubber latches will continue to evolve, ensuring their relevance and adaptability in the ever changing landscape of fastening systems.
There are different classifications of rubber latches, including latches which may be made from rubber or other materials, latches with both rubber and metal components, and latches made from just rubber. The various types are designed to meet the needs of an application or set of conditions.
These latches use a metal toggle that engages with a rubber catch, providing a secure closure for cabinets, boxes, and other objects. They are commonly used in the marine industry, as they are resistant to saltwater and corrosion.
Magnetic latches use a magnet and a rubber catch to create a secure closure. They are commonly used in cabinets, doors, and enclosures, where a quick-release mechanism is required.
These latches use a rubber handle and catch to provide a secure closure for doors, cabinets, and other objects. They are commonly used in the automotive industry, where they can provide a tight and secure closure.
Snap latches use a rubber catch and metal spring to create a secure closure for doors, cabinets, and other objects. They are commonly used in the medical equipment industry, where they can provide a tight and secure closure for cabinets and carts.
These latches use a rubber catch and metal spring to create a secure closure for doors, cabinets, and other objects. They are commonly used in the transportation and industrial equipment industries.
Rubber draw latches are similar to draw latches, but they use rubber instead of metal components. They are commonly used in the automotive and marine industries, where they can provide a secure and weather-resistant closure.
These latches use a rubber handle and catch to provide a secure closure for doors, cabinets, and other objects. They are commonly used in the automotive and transportation industries.
These latches use a rubber handle and catch to provide a secure closure for doors, cabinets, and other objects. They are commonly used in the automotive industry, where they can provide a tight and secure closure.
Regardless of which classification it may fall into, each type of rubber latch offers different benefits, such as weather resistance, durability, and ease of use. The specific type of rubber latch used depends on the application and requirements.
As with the manufacture of other rubber products, the manufacture of rubber latches takes several forms with each method designed to produce a latch to fit specific conditions and environments. Additionally, the method of production is dictated by the types of materials, the composition of the latch, and if any coated metals are used.
The process for the production of latches made from solid rubber varies from processes where metal will be coated with rubber or metal components are attached to rubber. It is for these reasons that there are so many different manufacturing and production methods.
Rubber injection molding is a popular method for creating rubber latches because it allows for the production of complex shapes and features. The process involves injecting molten rubber material into a mold, where it cools and solidifies to form the desired shape. The resulting part can then be trimmed, cleaned, and assembled into a complete latch.
This process is similar to compression molding, but allows for greater control over the flow of material, making it well-suited for more complex designs. It can be used with a variety of rubber materials, including silicone, EPDM, and neoprene.
Compression molding is another common method for creating rubber latches. It involves placing a pre-cut piece of rubber material, referred to as the charge, into a heated mold cavity and then applying pressure to compress the material into the desired shape. The part is then allowed to cool and solidify before being removed from the mold.
Liquid injection molding is a process that can create highly precise and detailed rubber components, which could potentially be used for creating rubber latches. The process involves injecting liquid rubber material into a heated mold cavity under high pressure, where it solidifies into the desired shape. This method is best suited for high-volume production runs.
While extrusion is not typically used for creating complete rubber latches, it can be used to create certain components of a latch, such as a seal or gasket. Extrusion involves pushing rubber material through a die to create a continuous length of material with a uniform cross-section.
Overmolding is a process where rubber material is molded over an existing part or substrate to create a rubber coating. This process can be used to create rubber latches that have a hard plastic or metal core for added strength and durability.
Injection molding is used for small, intricate parts, while compression molding is used to create large parts with simple shapes. Transfer molding is used for complex parts that require precise tolerances. Liquid injection molding is ideal for creating parts with high clarity, while extrusion is used for continuous profiles with uniform cross sections. The choice of manufacturing process is very dependent on the use and type of rubber latch.
The term rubber covers a wide range of materials that include natural rubber that is extracted from the rubber tree to synthetic rubbers made from polymers combined with other materials. In the case of rubber latches, the choice of rubber can determine the lifespan of a latch and its strength since the various forms of rubber have different tensile strengths and wear properties.
Natural rubber is an elastic material that has tear resistance, durability, and low compression set. It has exceptional tensile strength with resistance to fatigue and wear from chipping, cutting, or tearing but can be damaged by heat, light, and ozone. It is used in applications such as seals, gaskets, and shock absorbers. Natural rubber is molded using injection and compression molding.
This synthetic rubber material is highly resistant to weathering, ozone, and aging, making it ideal for outdoor applications. It is often used in automotive and marine applications, as well as in electrical insulation. Neoprene can be molded using methods such as injection molding or compression molding.
This rubber material is highly resistant to heat, cold, and UV radiation, making it ideal for high-temperature applications. It is often used in applications such as gaskets, seals, and medical devices. Silicone rubber can be molded using methods such as liquid injection molding or compression molding.
This is a synthetic rubber material that is highly resistant to weathering, ozone, and UV radiation, as well as a wide range of chemicals. It is often used in automotive and construction applications, as well as in seals and gaskets. EPDM can be molded using methods such as injection molding, compression molding, and transfer molding.
This synthetic rubber material is highly resistant to oil, fuel, and other chemicals, making it ideal for automotive and industrial applications. It is often used in seals, gaskets, and hoses. Nitrile rubber can be molded using methods such as injection molding, compression molding, and transfer molding.
Rubber materials can be used with multiple molding methods, depending on the application and desired properties. Natural rubber can be molded using injection molding, compression molding, or transfer molding, depending on factors such as the size and complexity of the part, the desired level of precision, and the production volume. Similarly, silicone rubber can be molded using liquid injection molding or compression molding, depending on factors such as the geometry of the part and the desired level of precision. The choice of rubber latch production process depends on properties of the rubber, the complexity of the part, the required volume, and the level of precision.
There are very few restrictions in regard to rubber latch design since rubber is a highly adaptable material that can be shaped and configured to fit any set of design parameters. The key to designing rubber latches is an in depth understanding of the rubber material that is being used.
Although there are a wide array of standard rubber latches, manufacturers provide custom designs to meet the needs of special and unique circumstances. In most cases, these unusual designs require a great amount of craftsmanship and engineering know how that rubber latch manufacturers provide.
The choice of rubber material will depend on the specific application and desired properties such as hardness, temperature resistance, and chemical resistance. For example, silicone rubber may be chosen for its high temperature resistance while EPDM rubber may be chosen for its excellent weather resistance.
The complexity of the design will determine the best process for manufacturing the rubber latch. Injection molding may be used for complex designs with fine details, while compression molding may be used for simpler designs with larger dimensions.
The tolerance requirements for the rubber latch will impact the choice of process and material. For example, liquid injection molding may be used for parts with tight tolerances, while extrusion may be used for larger parts with looser tolerances.
The design must be engineered to provide sufficient strength and durability for the intended use. This may involve selecting a thicker or more robust design, or choosing a stronger material such as neoprene or natural rubber.
The design must also take into account any environmental factors that may impact the performance of the rubber latch, such as exposure to extreme temperatures, UV light, or chemicals. The material and design must be able to withstand these conditions to ensure reliable performance over time.
Now that we’ve discussed the basic design and engineering considerations regarding rubber latches in general, let’s tie this information in with our previous discussions of the types of rubbers used and the processes used to create these various types of rubber material into rubber latches. For example:
For silicone rubber, the design and engineering considerations may include the need to accommodate its high durometer and low tear strength. The compression molding process may be a good choice for creating silicone rubber latches because it can handle high-durometer materials.
For EPDM rubber, the design and engineering considerations may include the need to account for its low compression set and good weatherability. The extrusion process may be a good choice for creating EPDM rubber latches because it can create long lengths of uniform cross-section, which is useful for sealing applications.
For natural rubber, the design and engineering considerations may include the need to account for its high elongation and tear strength. The compression molding process may be a good choice for creating natural rubber latches because it can handle materials with high elongation and tear strength.
For neoprene rubber, the design and engineering considerations may include the need to account for its good resistance to oils, chemicals, and weathering. The injection molding process may be a good choice for creating neoprene rubber latches because it can produce complex shapes and small parts with tight tolerances.
For nitrile rubber, the design and engineering considerations may include the need to account for its good resistance to oils, fuels, and chemicals. The transfer molding process may be a good choice for creating nitrile rubber latches because it can handle materials with good flow properties and produce parts with good dimensional stability.
As with rubber materials, the number of applications where rubber latches can be used includes a wide range of industrial, commercial, and residential uses with marine applications being the most common. The durability of the various types of rubber make it the ideal choice for permanently securing doors and preventing panels from shifting.
Rubber latches are used in doors, hatches, and various compartments to ensure a secure closure and to prevent rattling and noise due to their durability and ability to withstand vibration and impact.
Rubber latches are used in aircraft doors, panels, and hatches to provide a secure closure and to reduce cabin noise.
Rubber latches are used in medical equipment, including medical cabinets and carts, to ensure a secure closure and to prevent the entry of contaminants.
Rubber latches are used in industrial equipment, including machinery and tools, to ensure a secure closure and to reduce noise and vibration.
Rubber latches are commonly used in outdoor applications, such as on enclosures, sheds, and cabinets, due to their weather-resistant properties.
Rubber latches are used in electronics applications, such as on equipment enclosures, due to their ability to protect against dust, moisture, and other environmental factors.
Rubber latches are used in sports equipment, such as on backpacks and bags, due to their flexibility and ability to securely fasten items.
Rubber latches are used in military applications, such as on cases and containers, due to their durability, weather resistance, and ability to withstand extreme conditions.
The non-conductive nature of rubber makes it an ideal choice for electrical applications where component conductivity can be adversely problematic. The strength, durability, and impact resistance of rubber latches allows them to maintain their hold in the most extreme conditions. In outdoor applications, such as control and electrical panels, rubber latches are the perfect solution due to their rust, corrosion, and UV resistance.
Civilization has depended on rubber as a strong and durable material for thousands of years. It advanced into the modern realm when Charles Goodyear introduced the vulcanization process at the beginning of the first industrial revolution. From that time forward, manufacturers have been intrigued with the many positive properties of rubber and all it can do.
The main benefit of rubber latches is their flexibility, which allows them to conform to irregular shapes and sizes. This makes rubber latches ideal for applications where a tight seal is needed, such as on enclosures or containers. Rubber latches can also absorb shock and vibration, making them ideal for use in applications that require a secure hold even in dynamic environments.
Additionally, rubber latches are resistant to many types of chemicals and weather conditions, making them suitable for use in a wide range of industries, including automotive, marine, and aerospace. Overall, the flexibility of rubber latches makes them a versatile and reliable choice for applications that require a secure and tight hold.
Rubber latches are known for their durability, as rubber is a resilient material that can withstand significant wear and tear. This makes them suitable for use in applications where the latch may be subjected to repeated use or where there may be a need for a tight seal, such as in automotive, marine, or industrial settings.
Rubber latches are often designed to be weather-resistant, which means they can withstand exposure to various weather conditions such as extreme temperatures, rain, snow, and sunlight. This makes them suitable for use in outdoor applications where other materials may be susceptible to weather-related damage.
Rubber latches can provide a noise reduction benefit compared to other latch materials, such as metal or plastic. This is because rubber has a natural dampening effect, which can help to reduce the noise generated by the latch when it is engaged or disengaged.
Rubber latches are also corrosion-resistant, which means they can withstand exposure to corrosive materials such as saltwater or chemicals. This makes them suitable for use in marine, industrial, or chemical processing applications where other materials may corrode or degrade over time.
Rubber latches are often a cost-effective alternative to other latch materials such as metal or plastic. This is because rubber is relatively inexpensive to produce and can be molded into various shapes and sizes, making it suitable for a wide range of applications.
There have been specific incidences where rubber designs and concepts have changed the approach to a manufacturing problem. These advancements have altered the interpretation of rubber and its use. What has been discovered by designers, engineers, and developers is that rubber can be configured to fit conditions that are beyond the scope of other materials.
A major automobile manufacturer used rubber latches for one of their new designs. The vehicle featured a motorized arm that extended to open the door, and a rubber latch that secured the door in place when closed. The rubber latch was designed to provide a tight seal and absorb shock and vibration, helping to create a comfortable and secure ride for passengers.
This use of rubber latches in the automotive industry highlights their flexibility, which allows them to provide a secure hold, absorb shock and vibration, and create a tight seal, even in dynamic environments.
A manufacturer of off-road vehicles needed a durable latch for the doors of their vehicles that could withstand the harsh conditions of off-road use. They switched to rubber latches, which proved to be more durable and long-lasting than the previous metal latches, as the rubber material was able to withstand impacts and vibrations without breaking.
A company that manufactures enclosures for outdoor electronics needed a latch that could withstand exposure to extreme weather conditions, including high winds and heavy rain. They switched to rubber latches, which proved to be highly resistant to weather-related damage, as the rubber material was able to withstand exposure to moisture and temperature fluctuations without degrading.
A manufacturer of automotive parts needed a latch that could reduce noise and vibration in the interior of a vehicle. They switched to rubber latches, which proved to be effective at reducing noise and vibration, as the rubber material was able to dampen the impact of the latch when it engaged or disengaged.
A manufacturer of marine equipment needed a latch that could withstand exposure to saltwater and other corrosive elements. They switched to rubber latches, which proved to be highly corrosion-resistant, as the rubber material was able to withstand exposure to saltwater and other corrosive elements without degrading.
A manufacturer of industrial equipment needed a latch that was both durable and cost-effective. They switched to rubber latches, which proved to be a cost-effective alternative to metal latches, as the rubber material was less expensive to produce and could be molded into various shapes and sizes, reducing the need for costly machining and fabrication.
Manufacturers and users of rubber latches have been made aware of laws, regulations, and agencies that ensure compliance with safety and environmental standards. The oversight of industrial products is a necessity for the safety of rubber latch users and manufacturers. Compliance with these regulations ensures the safety and efficacy of rubber latches and minimizes their impact on the environment.
The CPSC is an independent federal agency that oversees the safety of consumer products sold in the United States. The CPSC has the authority to issue recalls, ban products, and establish safety standards for consumer products, including rubber latches.
OSHA is a federal agency that governs the use, production, and disposal of chemicals and other substances that may impact the environment. This includes the regulation of chemical substances used in the production of rubber latches, as well as the disposal of waste products generated during the manufacturing process.
The EPA is responsible for enforcing federal environmental laws and regulations that govern the use, production, and disposal of chemicals and other substances that may impact the environment. This includes the regulation of chemical substances used in the production of rubber latches, as well as the disposal of waste products generated during the manufacturing process.
The FDA is a federal agency responsible for regulating food, drugs, medical devices, and other products. Rubber latches used in medical devices or food packaging may be subject to FDA regulations.
The NHTSA is a federal agency that regulates motor vehicle safety in the United States. Rubber latches used in automotive applications, such as car trunks or hoods, may be subject to NHTSA regulations.
The Federal Aviation Administration regulates the use of rubber latches in aircraft to ensure they meet specific safety requirements.
The TSCA is a federal law that regulates the production, importation, and use of chemicals in the United States. Rubber materials used in the production of rubber latches may be subject to TSCA regulations.
The CAA is a federal law that regulates air emissions from industrial sources. Rubber production facilities may be subject to CAA regulations.
The RCRA is a federal law that regulates the disposal of hazardous waste. Rubber production facilities may be subject to RCRA regulations for the disposal of rubber waste.
As with any industrial material, there are drawbacks to the use of rubber latches, each of which can be overcome with proper precautions and adherence to established standards and regulations. The negative aspects of rubber are dependent on the type of rubber, its use, and the conditions to which it is exposed.
Over time, rubber latches can experience degradation due to environmental factors such as temperature, humidity, and exposure to UV light. This can result in loss of elasticity and ultimately, failure of the latch.
Rubber latches may not be resistant to certain chemicals, which can cause the latch to weaken or fail. It is important to select a rubber material that is appropriate for the environment in which the latch will be used.
Rubber latches may not be compatible with the material of the component it is latching onto. This can result in the latch failing to provide the necessary retention force or causing damage to the component.
Rubber latches may have limited temperature ranges in which they can function properly, as excessive heat or cold can cause the rubber to lose its elasticity or even crack.
Rubber latches may not be able to withstand heavy use or abrasion, causing them to wear down or fail prematurely.
Rubber latches, like all rubber products, have an environmental impact during production and disposal. Rubber production can be resource-intensive and may contribute to deforestation and habitat destruction, while disposal can result in rubber waste that takes a long time to decompose.
It is important to carefully consider these negative factors when selecting a rubber latch for a particular application. While rubber latches can offer certain advantages such as flexibility and durability, these negative factors can affect their performance and longevity. Other factors to consider include the size and shape of the latch, the material it will be latching onto, and the expected conditions in which it will be used.
The future of rubber latches looks promising due to a number of exciting trends. These trends, along with other factors, point to an increased use of rubber latches in the future. The exact path and growth of rubber can only be imagined based on present day data. The major influence on its future use is the various technological advances that can impact designs and applications.
As new technologies and materials are developed, the properties and capabilities of rubber latches are expected to continue to improve. For example, advancements in 3D printing and additive manufacturing techniques are making it possible to produce more complex and customized rubber latch designs. Additionally, new rubber materials are being developed that offer improved strength, durability, and flexibility.
The automotive, aerospace, and medical equipment industries are all expected to continue to grow in the coming years, which will likely lead to an increased demand for rubber latches.
With increasing concerns about the environmental impact of manufacturing and production processes, there is a growing demand for more sustainable and eco-friendly products. Rubber latches, which can be recycled and are often made from renewable resources, are well positioned to meet this demand. Additionally, the development of new sustainable materials and manufacturing processes is expected to further enhance the eco-friendliness of rubber latches.
As the versatility and durability of rubber latches continues to be recognized, they are expected to expand into new applications and industries. For example, rubber latches could be used in home appliances, such as refrigerators and washing machines, to provide a secure and durable latch. Additionally, the growth of the e-commerce industry is creating new opportunities for rubber latches to be used in packaging and shipping applications.
A door latch is a mechanical fastener that connects two surfaces or objects and provides a secure, safe, and strong connection. The latch portion of the mechanism is mounted on a flat surface such that when it meets a...
A gate latch is a locking mechanism that is used to secure gates on fences or stakes on truck beds using a metal bar and lever that is raised to open the latch and lowered to close it. Although they do not have...
Latches are mechanical components that allow the temporary joining of parts that are moving relative to each other. They are actuated to release the coupling and allow the two parts to separate. Latches are mostly seen on doors and enclosure...
A magnetic door latch is a type of latch that consists of a striking pad and a magnet and is used to keep doors and gates closed. Magnetic door latches are also known as magnetic door stops, magnetic door catches, and door magnets...
A rotary latch is a locking mechanism that secures openings such as doors, enclosures, cabinets, and panels so that they are locked and unable to accidentally open. They are referred to as slam latches since...
A spring latch is a mechanical device that is utilized in the joining of two separate components in order to prevent movement or opening. A spring latch is locked with a spring compression so that it will not be released...
A hinge is a movable joint or mechanism that joins two items together. The hinge is one of the most popular categories of mechanical bearings. Butt hinges are a particular kind of hinge that have rectangular pieces that...
A concealed hinge, also known as a hidden or European hinge, is a type of hinge that has parts invisible to the onlooker when the door is closed. They are commonly used in cabinet doors to add an aesthetically pleasing and...
A continuous hinge is an extended single unit hinge that spans the full length of a door, cabinet, lid, or enclosure entrance. They are made of lightweight metals and can be cut to fit the size of any opening...
An eyelet is a metal, rubber, or plastic ring with flanges are used to strengthen or reinforce holes punched in thin fabrics. It is a smaller counterpart of a grommet that is bigger in size and used for more heavy duty materials...
A fastener is a non-permanent or permanent mechanical tool that rigidly connects or affixes two surfaces or objects together. Non-permanent fasteners can easily be removed without damaging the joined materials...
A hinge is a machine element that connects two bodies allowing angular movement about a fixed axis of rotation, all the while preventing translations and rotations on the remaining two axes. A hinge can be...
A friction hinge works by creating a specific tolerance in between the mechanical components. It works based on the principle of torque that can be achieved by applying a desired amount of force. Some other additions to these hinges such as...
A lock is a mechanism designed to connect an opening to its frame using a latch, solid cylinder, bolt, or some other form of a solid metal plunger that extends into the strike. They are metal devices that prevent entry or access for privacy, security, or...
A metal washer is a small flat piece of metal that has a hole in the center and is used as a spacer, a method for absorbing shock, or distributing the load of a fastener. The hole in the middle of a metal washer allows for a bolt or screw to pass through...
A self-drilling screw is a type of tool that has the same design features as a drill bit or cutting tool. As the name implies, self-drilling screws do not require a pilot hole in order to perform as a fastener...
A spring hinge is a self-closing hinge that automatically closes two connected workpieces using the action of a spring that is loaded into the hinge's barrel. They can be found in a wide variety of products such as...
Stainless steel hinges connect two components while allowing them to move in relation to one another. They can have various leafs shaped like rectangles and other forms depending on the type of stainless steel hinge. Stainless steel hinge leafs are...
Molding is a manufacturing process that uses a mold - the latter being a solid container used to give shape to a piece of material. It is a forming process. The form is transferred from the mold to the material by...
Rubber injection molding is when uncured rubber is transformed into a usable product by injecting raw rubber material into a mold cavity made of metal. The applied pressure produces a chemical reaction like...
Rubber latches are latches made of rubber or are composed of rubber components. They are used in the automotive, aerospace, and medical equipment industries due to their flexibility, durability, and non-abrasive properties...
Rubber molding is a process of transforming uncured rubber or an elastomer into a usable product by transferring, compressing, or injecting raw rubber material into a metal mold cavity...
There are several methods to perform rubber overmolding, and each method has its own unique advantages and disadvantages. The choice of method typically depends on the design and material requirements of the product being...
Silicone rubber molding is a method for shaping, forming, and fabricating silicone rubber parts and products using a heated mold. The process involves compressing or injecting silicone rubber into a mold...
A rubber bushing is a form of vibration isolator that is placed between two parts to limit the motion between them and absorb, mollify, and buffer the energy produced by their interaction. They are very...
Extruded rubber is a group of products made by softening and pressurizing an elastomeric compound and forcing it to flow through a hard tool called a die. The resulting product is a continuous piece of material that has the same cross-section throughout its length...
Rubber gaskets are elastic components used for mechanically sealing the microscopic gap between two mating surfaces or joints. Examples of these surfaces are flange faces of piping and fittings, mating surfaces of an...
A rubber O ring is a mechanical gasket in the shape of a torus or donut and is used for static and dynamic applications where there is relative motion between parts and the possibility of friction. Some of the benefits of rubber O rings are...
A rubber roller is a machine part that is composed of an inner round shaft or tube covered by an outer layer of elastomer compounds. The inner shaft is made of steel, aluminum alloys, or other strong and rigid material composites...
Rubber sheets are basically sheets made of rubber or cloth that are coated with rubber to improve the mechanical properties of rubber sheeting such as increased tensile strength and reduced elongation...
Rubber to metal bonding is when a rubber part has to be adhered to a metal part, a metal component is chemically prepared and is attached or encapsulated as part of the process to become a bonded rubber part...
Rubber trim is an extruded, sometimes molded, elastomer that is used to protect the edges or surfaces of objects from sudden impacts. They are usually found on panels, windows, doors, removable covers, and hatches...
Rubber tubing, also known as rubber hose or rubber piping, is made of natural and synthetic rubber and is used to circulate and transport liquids and gases for household and industrial uses. The natural or synthetic rubber materials used for the manufacture of rubber tubing...
Urethane casting is the process of injecting polyurethane and additive resins into a soft mold usually made of silicone elastomer. The casting process is similar to injection molding; injection molding differs by using hard, metal molds...