Rubber Bushings
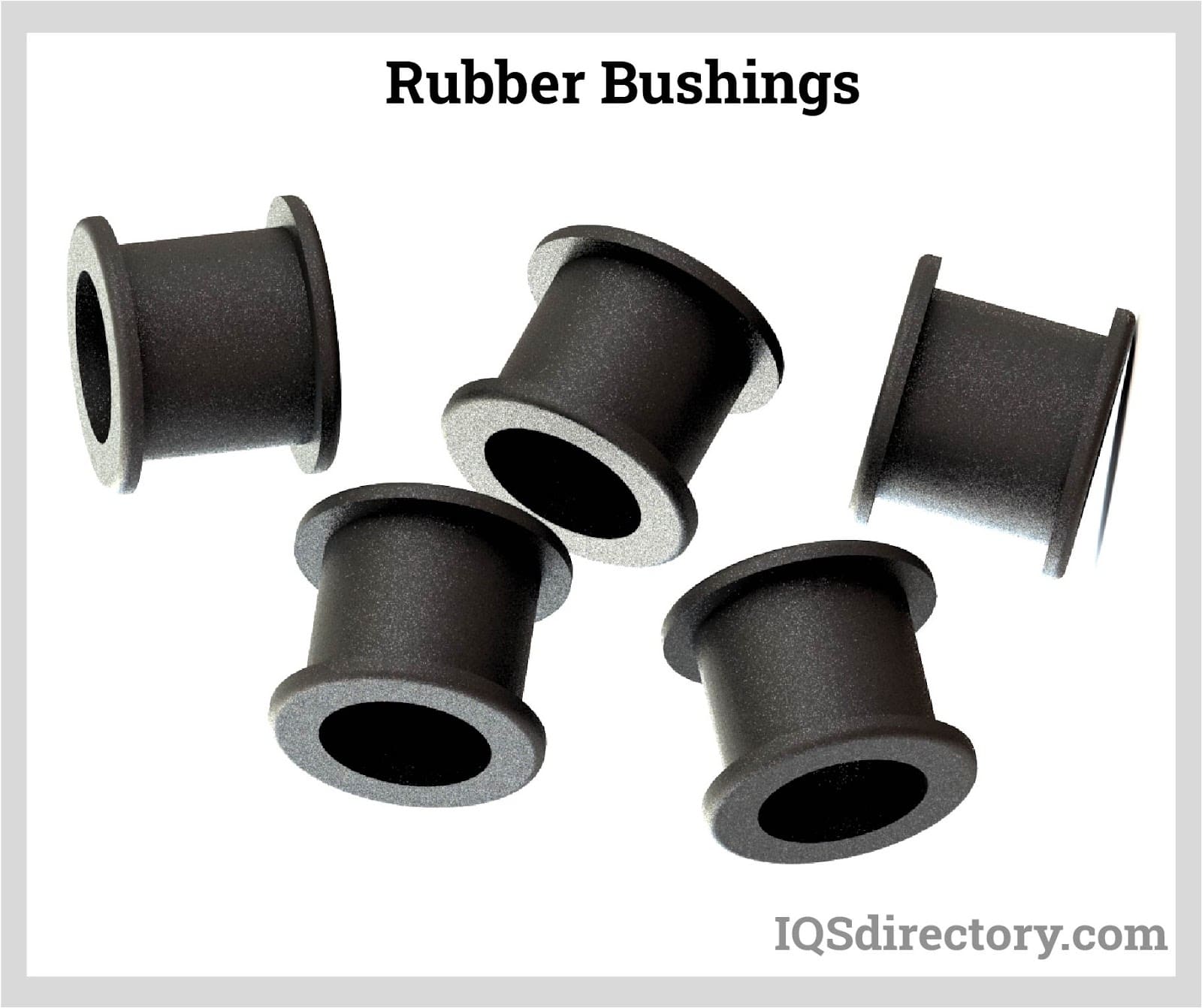
A rubber bushing is a form of vibration isolator that is placed between two parts to limit the motion between them and absorb, mollify, and buffer the energy produced by their interaction. They are very...
Please fill out the following form to submit a Request for Quote to any of the following companies listed on
This article provides comprehensive information about rubber trims and their production process. Read further to learn more about:
Rubber trim is an extruded, sometimes molded, elastomer used to protect the edges or surfaces of objects from sudden impacts. It can be found on panels, windows, doors, removable covers, and hatches. Additionally, rubber trims provide sealing for the edges of mating parts, acting like rubber gaskets or O-rings. Rubber trim is an exceptionally flexible protective material made of dense rubber that has excellent wear and ozone resistance and fits snug and tight.
In some instances, rubber trim is manufactured with a pre-applied hot melt adhesive or butyl adhesive to further enhance its tight fit and avoid slippage. Rubber trim is popular due to its resistance to abrasion caused by frequent bumps and scrapes.
Rubber trims are made with different profiles and are often times customized for a specific application. The profiles are engineered and milled onto a die, then installed onto an extrusion machine where the rubber product is created. The most common is a U-channel used for edge protection. The edge of the part or substrate is inserted into the channel's open side and is locked in place by fasteners or adhesives. Other designs have protrusions or tongues along the inside of the channel to lock the rubber trim in place without the need for a permanent fastening.
For applications requiring a reliable seal, a solid or hollow cord or profile is integrated into the channel. The combined channel (edge trim) and the cord (seal) is produced through a co-extrusion process where two different types of rubber are extruded with different sets of properties. When compressed, the cord deforms and flows along the mating surfaces while the edge trim provides the structural stability of the seal. Rubber trims are preferred due to the broad range of hardness that can be obtained, along with their inherent resistance to chemicals, moisture, and heat.
Rubbers are a class of polymers (elastomers) that have a highly elastic nature created by the cross-linking of long polymer chains into amorphous structures. In elastomers, the intermolecular forces between the polymer chains are relatively weak, allowing them to be reconfigured upon application of stress. This property allows elastomeric materials to easily conform to the profile of the adjacent surfaces.
Depending on the type of curing reaction or vulcanization, elastomers can degrade under the presence of water, ultraviolet light, oils, and certain solvents. High temperatures can easily expand and oxidize or age elastomers, while low temperatures can make them brittle. Typical elastomers used for the manufacturing of rubber trims are nitrile (NBR), ethylene propylene diene monomer (EPDM), neoprene, silicone, and natural rubber.
Polybutadiene Rubber (BR):Polybutadiene rubber is produced from the polymerization of butadiene monomers containing four carbon atoms and six hydrogen atoms (C4H6). The three types of polybutadiene rubber are high Cis polybutadiene, lithium-based polybutadiene, and high trans polybutadiene, which have different isomers of butadiene.
The types of polybutadiene rubbers are made using a solution process that includes transition metals like neodymium, nickel, or copper complexes or an alkyl metal like butyllithium as catalysts. Generally, butadiene rubber has good cracking, abrasion, and rolling resistance but is prone to ozone degradation.
Butyl Rubber (IIR): This is a copolymer of isobutylene and isoprene; hence, the abbreviation IIR. Isoprene only consists of around 3% of the copolymer which gives the required unsaturation for vulcanization. The low unsaturation of IIR enables it to repel most chemicals (gas and liquids) and is highly resistant to aging when vulcanized properly.
The structure of butyl rubber is similar to polyethylene and polypropylene, with every other carbon atom being substituted with two methyl groups instead of one. It is the only elastomer that is resistant to gasses and is biocompatible with resistance to acidic or alkaline chemicals, ozone, heat, and weather and includes good aging properties. Butyl rubber does not perform well in the presence of petroleum-based fluids, hydrocarbons, or flames.
Acrylonitrile Butadiene (Nitrile) Rubber (NBR): This rubber is a copolymer of acrylonitrile and butadiene. They are polymerized in an emulsion similar to SBR polymerization systems. NBR is widely used due to its resistance to oils and petroleum-based solvents. However, they have low tensile strength and poor low-temperature performance. Reinforcing fillers are added to solve these problems.
Polyisoprene Rubber (IR): Isoprene rubbers are general-purpose rubbers created from the polymerization of isoprene monomers. The polymer chain is similar to that of natural rubber. Because IR is synthesized in a controlled environment, it is chemically purer than natural rubber with similar or more superior characteristics.
Silicone Rubber: These polymers, instead of having a carbon backbone, have a silicon-oxygen chain with groups of methyl, vinyl, and phenyl. Silicone rubbers have good oxygen, ozone, heat, light, and moisture resistance. However, they are more expensive and have poorer mechanical properties than organic rubber.
The manufacturing of extruded rubber is a very complicated process. The processes can be divided into two: the production of the raw rubber and the downstream processes that mainly involve compounding, forming (extrusion), and curing. The production of raw rubber converts gaseous or liquid petroleum-based compounds into polymers. This process is usually done in petrochemical plants. The rest is done in the rubber manufacturing plant, where the raw rubber and other materials are combined and formed to create the final product.
Rubbers are made by polymerizing organic compounds into long chains and cross-linking them to give them an elastomeric structure. Polymerization is achieved by either step-growth polymerization or chain-growth polymerization.
Step-growth polymerization, or polyaddition polymerization, is a reaction mechanism that involves a monomer with at least two active sites or functional groups that can bind with other monomers, forming an oligomer. The oligomers join to form longer chains until the polymer is formed. Polymerization is controlled by adding monomers with only one functional group, which consumes an active site of the oligomer. This process was one of the earliest methods of polymerization because of its simplicity. Popular elastomers produced through step-growth polymerization are polysiloxane (silicone) and polyurethane.
Chain-growth polymerization or chain polymerization involves the continuous addition of monomers one at a time to a growing chain which is initiated by some reactive species or intermediates. These reactive species initiate the reaction by opening a bond of a monomer which becomes an active site for binding with other monomers. They can be free radicals, cations, anions, or organometallic catalysts.
The polymer chain grows through chain propagation, where the newly added monomers to the chain open one of its bonds which becomes an active site. The chain propagation ends when one chain binds with another chain or with a terminating agent. This is known as chain termination.
Another type of reaction, known as chain transfer, is used to control the average molecular weight of the polymer. Common organic compounds used for rubber production synthesized through chain polymerization are butadiene, isoprene, and chloroprene. Aside from creating homopolymers (a polymer composed of only one monomer), copolymers can also be synthesized. Popular copolymers are styrene-butadiene (SBR), nitrile butadiene (NBR), and ethylene propylene diene monomer (EPDM).
Compounding is the formulation process where certain chemicals are added to the raw rubber to modify its final mechanical and chemical properties, to lower its cost, and aid its processability and vulcanization. Compounding optimizes the properties of the rubber to meet the requirements of its intended application. Aside from the raw rubber (natural or synthetic), typical compounding ingredients are:
Filler Systems: Filler systems include carbon blacks, clays, silica, and calcium carbonate, which are added to reinforce the elastomer structure to meet the required tensile strength and impact and abrasive resistance.
Carbon black is the most widely used reinforcing filler, which is produced from the incomplete combustion of heavy petroleum-based compounds, such as oil and tar. There are different types of carbon blacks, including super abrasion furnace (SAF), high abrasion furnace (HAF), fast extruding furnace (FEF), and semi-reinforcing furnace (SRF). Carbon black reinforces the elastomer by entangling the elastomer molecules on the porous surface of the filler. The deposition of carbon black particles into the elastomer matrix creates a composite with improved mechanical properties.
Non-carbon-based fillers, such as silica, clay, and calcium carbonate, are added to improve tear strength, reduce heat buildup, and create better compound adhesion for multicomponent products. These fillers do not bind well with elastomers in comparison with carbon blacks, resulting in a lower level of reinforcement, a problem that is solved by adding a silane coupling agent.
Stabilizer Systems: Stabilizer systems include antioxidants and antiozonants, which are added to prevent the degradation of rubber. Polymers, especially elastomers, tend to degrade due to the presence of carbon-to-carbon double bonds that can easily be broken and bonded onto by oxygen in the presence of ultraviolet light (photochemical reaction). The result is a broken polymer chain and a decrease in cross-linking density of the elastomer.
A broken polymer chain softens the elastomer, which decreases its abrasion resistance, while the decrease in cross-linking reduces the elastic property of the rubber and makes it stiff and prone to fatigue failure. Adding stabilizers helps limit the rate of oxidation by scavenging free radicals that can break the bonds of the polymer chain and prevents compounds, such as peroxides and hydroperoxides, from producing more free radicals by decomposing them.
Common antioxidants are phosphites, phenols, and hydroquinones. For the antiozonant, PPDs or paraphenylene diamines are the only classes used in significant quantities due to their potency and ability to further improve the fatigue and heat resistance of the rubber.
Vulcanizing or Curing Agents: Curing or vulcanizing agents are sulfur, peroxides, accelerators, activators, and retarders. The process of vulcanizing is where elastomers react with a system of compounds that inserts cross-links between the elastomer chains. It is often associated with sulfur systems, which are the most common method.
Sulfur curing systems consist of three main components: the vulcanizing agent (sulfur), the accelerators, and the activators. Accelerators act as catalysts that promote the vulcanization process by increasing the rate of the cross-linking process resulting in faster curing time and lower reaction temperatures. Accelerators increase the degree of cross-linking, resulting in a rubber matrix with better mechanical properties. Each type of accelerator works through different reaction mechanisms. Common accelerators are benzothiazoles, thiocarbamates, and amines.
Activators enable the efficient use of sulfur to increase the density of cross-links. The most common activator is zinc oxide combined with stearic acid. Zinc, when compared to other metal oxides, is most suited to forming sulfurating intermediates.
Adding the vulcanizing agents, accelerators, and activators to the elastomer prepares it for curing, which can occur prematurely during processing, making it harder to form. Premature vulcanization is termed as scorching. Retarders or inhibitors are added to prevent scorching without affecting the rate of vulcanization. The most popular rubber retarder is cyclohexylthiophthalimide (CTP), which is simply termed PVI or pre-vulcanization inhibitor.
Special Ingredients: Colorants, process oils, resins, and fibers are special ingredients used to give specific properties to the rubber. Colorants and pigments are supported by various compounds such as silica and titanium dioxide. Rubber is usually black due to the addition of carbon black.
Process oils are added to improve the processability of rubber. They can be paraffinic, naphthenic, and aromatic. Process oils also act as an extender to lower the cost of the rubber bulk. The type of process must be compatible with the elastomer to prevent it from migrating out of the compound.
Resins and fibers are added to improve the mechanical properties of the rubber. Hydrocarbon resins increase the viscosity of the compound when heated to achieve better flow, while fibers increase tensile strength and chipping resistance.
Mastication is integrated with compounding, wherein the polymer chain is subjected to high shearing forces that mechanically break down the molecule to create smaller chains. This makes the polymer receptive to the compounding ingredients. Not all polymers require mastication, especially for those with uniform chemistry and high stability. The addition of chemical plasticizers or peptizers improves the mastication process by serving as oxidation catalysts. They prevent the recombination of broken polymer chains by removing the free radicals formed during mixing.
Mastication is usually done in open roll mills or internal mixers. Open mills consist of two rollers heated for temperature control. The rubber compound is sheared as it passes through the fixed clearance between the rollers. Internal mixers are high shear mixers that can either be a tangential rotor type or an intermeshing rotor type. The tangential rotor design shears the rubber between the clearance of the rotor and the walls or stator parts of the mixer. The intermeshing rotor design performs shearing by impinging the rubber between two rotors.
Masterbatching means the addition of the compounding ingredients into the masticated polymer except for the vulcanizing system. Masterbatching can induce premature vulcanization due to the heat generated by the mixing action. Masterbatching homogenizes the rubber blend to accomplish the maximum carbon black dispersion and the final viscosity.
Final mixing involves the addition of the vulcanizing system. Final mixing is usually done on separate mixers that operate at slower speeds. The required distribution of the final mix must be achieved before premature vulcanization occurs. After mixing, the final blend is cooled and formed into slabs or bales, ready for the subsequent forming operations.
In most manufacturing systems, the product of the mastication and mixing processes goes directly into an extrusion machine with a single-screw or twin screws that further mixes the rubber compound, compresses it, and forces it to flow against a die.
The die has a cross-section of an engineered part that is milled according to the dimensions of the final product with added compensation for any change in dimension after die swelling and vulcanization. Steam jackets, water jackets, or electric heaters are traced along the barrels (screw enclosures) that control the temperature in the extruder.
Other configurations of extrusion machines combine the compounding, masticating, and mixing processes. For these types of machines, the extruder uses screw elements with different profiles. One set of screw elements is for mastication (kneading) while another is for mixing, with the last one being for compressing. The extrudate then goes through a heater or oven to initiate the vulcanization process.
As mentioned earlier, curing or vulcanization is the process of creating cross-links between elastomer chains. This makes the rubber more stable, enabling it to resist the effects of heat, cold, and solvents. Curing was the general term used for the cross-linking process, while vulcanization was originally the term used for curing rubber with sulfur. The earliest curing agent used to cross-link natural rubber or latex was sulfur. Today, other curing processes do not use sulfur as the main curing system. These curing processes use agents such as peroxides, and rarely, phenols and metal oxides.
Vulcanization occurs when the rubber compound containing the curing additives is heated, which breaks the bonds of the sulfur molecules (S8) or sulfur donors, freeing up sites for binding. Cross-links are created when elemental sulfur or sulfur donors bind with the functional groups or on the unsaturated bonds of two elastomer chains. Initially, vulcanization is done with elemental sulfur, which requires temperatures of around 284 °F (140 °C) for five hours. The result is rubber with good physical properties that degrades easily through aging. The introduction of activators, particularly zinc oxide, decreases the time to about three hours. Activators coupled with accelerators further reduce the curing time to several minutes. Activators and accelerators reduce the curing time of the rubber and improve its aging properties.
Peroxide curing agents work almost the same as sulfur curing agents. Heating splits the peroxide into free radicals that remove a hydrogen atom from the polymer chain, freeing up a bond for cross-linking. Generally, peroxide curing is better than sulfur curing in terms of temperature resistance, aging properties, solvent resistance, compression set, and odor. It is a process that does not require activators and accelerators that can potentially form carcinogens known as nitrosamines.
Secondary processes are additional processes done on the product to suit a particular application. This can include cutting, drilling, notching, splicing, coating, and so on. For rubber trims, aside from cutting, typical secondary processes are splicing, slip-coating, sealant injection, and adhesive taping.
Testing and quality control are done to determine the final properties of the product and to ensure the uniformity and consistency of the product. Large manufacturing plants with compounding processes usually have an internal testing laboratory. Tests conducted on the final rubber compound may include:
Property |
Method / Standard |
Description / Instrument |
---|---|---|
Cure Quality |
ASTM D2084 |
Oscillating disk cure meter (rheometer) |
Hardness |
ASTM D2240 |
Measurement of indentation using a durometer |
Tensile Strength |
ASTM D412 |
Universal testing machine (tensile test) |
Elongation |
ASTM D412 |
Analysis of stress-strain curve by elongating until rupture |
Compression Set |
ASTM D395 |
Measurement of residual deformation upon compression and deflection |
Heat Resistance (Thermal Aging) |
ASTM D865 / ASTM D572 / ASTM D573 |
Analysis of stress-strain curve or mechanical characteristics before and after heating in air or oxygen-rich atmosphere |
Abrasion Resistance |
ASTM D1630 / ASTM D2228 |
Measurement of material loss using NBS abrader or Pico abrader |
Tear Resistance |
ASTM D624 |
Similar to tensile test until rupture; the difference is the profile of the specimen cut by standard dies |
Resilience |
ASTM D2632 |
Measurement of rebound using vertical rebound tester |
Impact Resistance |
ASTM D256 |
Measurement of load causing permanent deformation using Izod and Charpy impact testers |
Flex Resistance |
ASTM D813 / ASTM D1052 |
Measurement of the number of cycles before failure using DeMattia or Ross flexer |
Heat Buildup |
ASTM D623 |
Measurement of the rise in temperature after rapid cycling using Goodrich flexometer |
Ozone Resistance |
ASTM D1149 / ASTM D3395 |
Analysis of mechanical properties in an ozone-rich atmosphere |
Outdoor Exposure |
ASTM D518 |
Analysis of physical properties when exposed to sunlight, soil, moisture, and bacteria |
Water absorption |
ASTM D570 |
Measurement of tensile properties after aging in humidity or water spray in the presence of ultraviolet light |
Solvent Resistance |
ASTM D471 |
Assessment of volume, weight, and other physical properties upon contact with test liquids |
Brittleness |
ASTM D746 |
Determining the temperature at which brittle fracture occurs |
Low Temperature Stiffness |
ASTM D1053 |
Measurement of modulus of rigidity in low temperatures using Gehman torsion tester |
Note that not all tests must be performed. The required tests depend on the intended customer and the application of the product. After quality inspection, the products are rolled, bundled, or packed preparing them for distribution.
A rubber bushing is a form of vibration isolator that is placed between two parts to limit the motion between them and absorb, mollify, and buffer the energy produced by their interaction. They are very...
Extruded rubber is a group of products made by softening and pressurizing an elastomeric compound and forcing it to flow through a hard tool called a die. The resulting product is a continuous piece of material that has the same cross-section throughout its length...
Rubber sheets are basically sheets made of rubber or cloth that are coated with rubber to improve the mechanical properties of rubber sheeting such as increased tensile strength and reduced elongation...
Molding is a manufacturing process that uses a mold - the latter being a solid container used to give shape to a piece of material. It is a forming process. The form is transferred from the mold to the material by...
Rubber gaskets are elastic components used for mechanically sealing the microscopic gap between two mating surfaces or joints. Examples of these surfaces are flange faces of piping and fittings, mating surfaces of an...
Rubber injection molding is when uncured rubber is transformed into a usable product by injecting raw rubber material into a mold cavity made of metal. The applied pressure produces a chemical reaction like...
Rubber molding is a process of transforming uncured rubber or an elastomer into a usable product by transferring, compressing, or injecting raw rubber material into a metal mold cavity...
There are several methods to perform rubber overmolding, and each method has its own unique advantages and disadvantages. The choice of method typically depends on the design and material requirements of the product being...
A rubber roller is a machine part that is composed of an inner round shaft or tube covered by an outer layer of elastomer compounds. The inner shaft is made of steel, aluminum alloys, or other strong and rigid material composites...
Rubber to metal bonding is when a rubber part has to be adhered to a metal part, a metal component is chemically prepared and is attached or encapsulated as part of the process to become a bonded rubber part...
Rubber tubing, also known as rubber hose or rubber piping, is made of natural and synthetic rubber and is used to circulate and transport liquids and gases for household and industrial uses. The natural or synthetic rubber materials used for the manufacture of rubber tubing...
Silicone rubber molding is a method for shaping, forming, and fabricating silicone rubber parts and products using a heated mold. The process involves compressing or injecting silicone rubber into a mold...
A grommet edging is a flexible rubber or plastic strip that covers rough and sharp surfaces found in openings and edges of panel walls to protect the passing electrical cables, wires, and other sensitive components...