Nylon Tubing
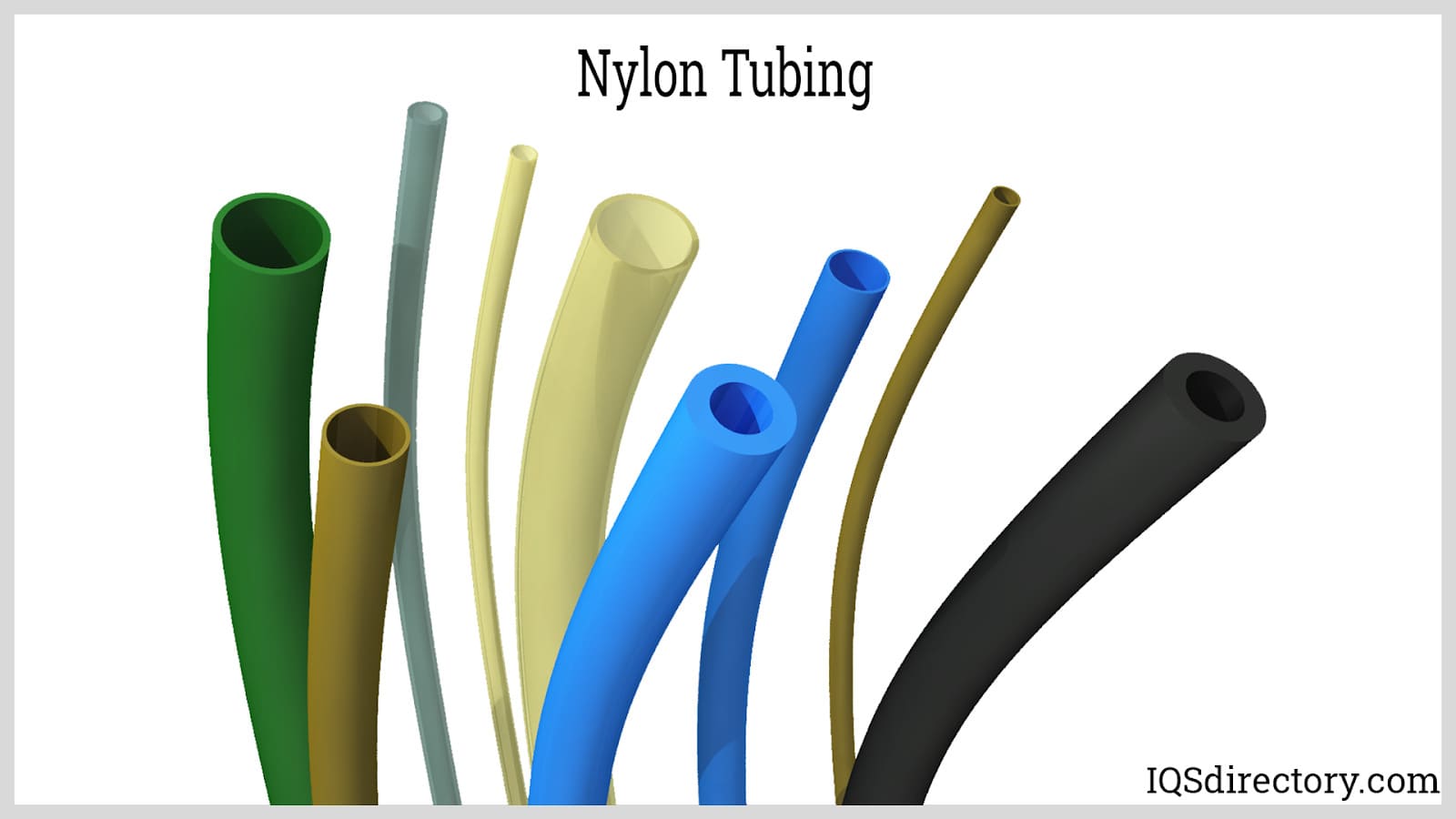
Nylon tubing, also known as polyamide tubing, is a type of tubing made from polyamide resin, which has a strong resistance to abrasion. It is used in high-pressure and high-temperature applications...
Please fill out the following form to submit a Request for Quote to any of the following companies listed on
This article will take an in-depth look at Polyvinyl Chloride (PVC)
The article will take a look at topics such as:
This chapter will discuss Polyvinyl Chloride (PVC) and how it is made.
Polyvinyl Chloride, popularly known as PVC, is a high strength white, brittle solid thermoplastic that is lightweight, durable, low cost, and easy to process. PVC was accidentally discovered by German scientist Eugen Baumann in 1872 when he placed a tube of vinyl chloride gas in direct sunlight, which produced the white solid material PVC. It did not become widely used until 1913 when it was produced as a corrosion resistant material for piping.
There are several versions of polyvinyl chloride, which include plasticized or flexible, unplasticized, perchloro vinyl, molecular oriented, and modified. The key properties of the PVC polymer are dielectric strength, durability, flame resistant, low cost, and abrasion and chemical resistance.
Since PVC resin made from polymerization is unstable because of its low thermal stability and high melt viscosity, its properties are modified by additives during processing. Heat additives, UV stabilizers, plasticizers, impact modifiers, fillers, and flame retardants, and pigments are some of the additives used to enhance PVC’s stability.
It is made by polymerizing vinyl chloride, and its properties depend on the plasticizer that is added. The plasticizer is a low molecular weight substance that is added to the polymer (PVC) to increase its plasticity and flexibility. Therefore the purpose of the plasticizers is to make the polymer (PVC) more suitable for the required specific applications. The plasticizers must have chemical similarities with the polymers.
This section details how Polyvinyl Chloride is made.
Unlike other thermoplastics that are completely derived from oil, PVC is made from two starting materials (i.e. raw materials). This in turn will reduce the amount of non-renewable fossil fuel that PVC will use in its manufacturing process. The two raw materials that are used to make PVC are: 57% of the molecular weight that is derived from common salt; 43% derived from the feedstocks of hydrocarbons.
Ethylene from sugar crops is now increasingly being used for producing PVC as an alternative to ethylene derived from natural gas or oil. While PVC is most often manufactured from oil and salt, in some parts of the world PVC is manufactured without using oil feedstock at all, but the oil-derived hydrocarbon is substituted with bio-derived hydrocarbon feedstock. This makes PVC way less oil-dependent than other thermoplastics.
PVC has a very high durability and is energy efficient across a broad range of applications. The reserves for the raw materials are abundant since there are over trillions of tons of salt that exist in the sea and are available underground.
The production process of PVC involves the following five steps:
The petrochemical industries supply ethylene derived from natural gas. During a process known as cracking, ethylene is captured. The liquid petroleum is heated in furnaces containing steam and put under high pressure. Consequently, the molecular weight of the chemicals found in feedstocks of petroleum changes. This change in molecular weight allows ethylene to be identified, separated, and captured. It is then liquified by cooling it down.
Chlorine, which is found from the seawater extracted from salt, gains an additional electron when the process of electrolysis takes place. Chlorine is separated and then extracted from the mixture by sending a strong electric current through the salt water solution. The electric current will be strong enough to change the molecular structure of the solution. When ethylene and chlorine react together, ethylene dichloride (EDC) is formed. This is then passed through another thermal cracking process, which produces the monomer called vinyl chloride (VCM).
VCM is sent through a reactor containing a catalyst, where polymerization occurs. The chemicals cause the vinyl chloride monomers to react until links are formed between them. The linking of VCM molecules forms PVC resin, which is the beginning of all vinyl compounds. The structure of PVC is hazy and it inherently exhibits properties that are chemical resistant and fire retardant.
PVC is mixed with various types of plasticizers, stabilizers, and modifiers to formulate vinyl compounds that are rigid and flexible. This in turn will promote the achievement of certain properties that include UV resistance, color considerations, scuff and mar resistance, weatherability, texturing capability, etc.
This section details the emulsion process used in the making of PVC.
In this type of process, the monomer droplets are dispersed in water and act as separate microreactors. The polymerization is started by an organic initiator and proceeds as a bulk polymerization that is miniature. As the monomer is converted into a polymer, the droplets transform into monomer/polymer particles that are sticky and viscous.
The transformed droplets will gradually become solid spherical polymer particles. There is a need for vigorous agitation and steric stabilizers. The polymer particles that are produced have sizes in hundreds of micrometers and as soon as the agitation stops, they settle out. Suspension polymerization is particularly useful in manufacturing polymers from monomers that are highly reactive via radical polymerization.
Water facilitates agitation and promotes the transfer of heat during the process. With monomer conversion, the viscosity of the suspension remains relatively constant. The polymer product and the water must be separated so that the polymer product can be used. In suspension polymerization, where agglomeration is not controlled, the distribution of the size of the monomer droplet is the final PSD (polymer particle size distribution), except for some shrinkage of volume. The mass transfer between particles is little.
The type and amount of steric stabilizer determine the PSD. The PSD is dependent on the agitation and vessel design also. To maintain stable suspension, controlled agitation and different types of stabilizers, both organic and inorganic, are made use of to obtain the desired bulk density, size, and the particles’ porosity. There are two types of suspension polymerization. Beads are polymer particles that are nonporous and formed where the polymer is soluble in monomers like PMMA and PS.
Powders are polymer particles that are porous and they are formed where the polymer is insoluble in monomer and during polymerization, they precipitate. The powders of the polymer are composed of many primary particles that are small in size. The powder particles are opaque and contain internal porosities that are substantial. Controlling the porosity of the particles is very important because it controls the absorption rate of plasticizers such as PVC.
In this process, both the monomers solution and the initiator are fed into the reactor continuously. As an oil phase, the monomer feed can be, or it can be pre-emulsified in water using surfactants and then fed as an emulsion. The emulsification of monomers in water can be carried out in a separate or inline vessel with static mixers, ultrasonic devices, stator/rotor units, or high pressure mixing systems.
To achieve improved temperature control and a safer process, a monomer emulsion feed is used. To add on top, emulsion feed reduces reactor fouling. If the instantaneous conversions at which the reaction is carried out are very high (greater than 95%), polymerization parameters for copolymerization will not be able to play a significant role. As observed, the polymers formed correlate closely to the added monomer ratio. Feeding monomers also ensures particle composition control and morphology by changing the rates of addition of different monomers. In many cases, a seed of miniature particles is used for controlling the particle number and therefore control the final size of the particle.
To create a second particle generation, a second quantity of seed is added, or of surfactant at a concentration that is sufficiently high for the formation of micelles in the mixture. This in turn will give rise to a particle size distribution with a bimodal structure. This bimodal size distribution will ensure the reaching of high solids content at a relatively low viscosity. The other route to multimodal PSD is the addition of agglomeration agents during the process of emulsion.
The morphologies of the particles can also be modified by the stepwise addition of cross-linking monomers. For particle stability and heat transfer, industrial reactors and hydrodynamic flow conditions are of great importance. Therefore the shape and type of the stirrer, and the reactor’s shape are important as well.
This type of process may also be referred to as mass polymerization. Bulk polymerization does not use a solvent but has an initiator and a monomer as the main components. When solidification takes place, the polymerization conforms to the fixed shape of the reaction vessel. The dissipation of heat produced during polymerization is the real challenge.
This type of process benefits the production of cast-molded products that include polystyrene scintillators. According to research, to promote the rate of polymerization, the distillation of the monomer must be done before the reaction and where this is impracticable, an appropriate solution must be used to rinse the product.
Bulk polymerization is the simplest in terms of formulation since it is carried out in the absence of any solvent or dispersant. It is mostly used for many types of chain-growth polymers and most step-growth polymers. In the case of chain-growth reactions that are exothermic generally, the heat that is emitted may cause the reaction to become too vigorous and difficult to control unless there are cooling coils that are efficient and installed in the reaction vessel.
Bulk polymerizations are also hard to stir because of the viscosity of the high-molecular-weight polymers that is high.
There are numerous machines available to produce PVC tubing in the United States and Canada. These machines are important in today's society because they enable the efficient and cost-effective manufacturing of PVC tubing, which is widely used for various uses such as construction, electronic, and automotive applications. Many of these leading machines are discussed below.
Features: The Conical Twin Screw Extruder is widely used for PVC tubing production due to its ability to efficiently process PVC compounds, achieve high output rates, and offer excellent melt homogeneity for consistent tubing quality.
Features: The Single Screw Extruder is popular for PVC tubing production because of its versatility, cost-effectiveness, and the ability to handle various PVC formulations with ease.
Features: Davis-Standard offers a range of downstream equipment designed specifically for PVC tubing production, including vacuum sizing tanks, haul-off machines, and cutting systems, ensuring accurate dimensions and smooth surface finish.
Features: Bausano Twin Screw Extruders are widely used in PVC tubing production due to their advanced design, precision control, and high output capacity. These extruders are capable of processing various PVC formulations efficiently and ensuring consistent tubing quality.
Manufacturer: American Kuhne (a division of Graham Engineering Corporation)
Features: American Kuhne offers various extrusion equipment options suitable for PVC tubing production, including extruders, crossheads, and downstream equipment, known for their precision and reliability.
Please note that the information provided is based on information provided based on the posting date of this article and newer models or manufacturers may have emerged after that time. For the most up-to-date information, it is recommended you check with industry-specific sources or directly contact manufacturers, suppliers, and other experts in the industry.
This section will detail the types of PVC pipes, characteristics and additives applied in PVC.
The various types of PVC pipes include:
When a pipe comes with an additional letter ‘U’ at the end, it means that the pipe is made from unplasticized PVC (PVC-U). This means that this type of PVC does not contain any plasticizer, which is the solvent that is added to the PVC material to promote its plasticity and flexibility, and reduce its brittleness. Since it does not contain this substance, PVC-U is often known as rigid PVC.
It is the most famous type of PVC used for pipes and fittings. It is utilized in the transportation of water for drinking and also wastewater. These types of pipes are easy to handle, light, affordable, durable, and because of the absence of a plasticizer in them, they are 100% recyclable.
PVC-O is a polymer that is molecular oriented. When PVC undergoes this production process, PVC-U is turned into a layered structure, which makes it more corrosion resistant.
PVC-O is the perfect blend of stiffness, strength, and flexibility. Their hydraulic capacity and durability are high, making them more suitable for pressure pipes for irrigation, drinking water, and sewer pumping mains.
C-PVC stands for chlorinated PVC. Its characteristics are the same as PVC-U. It is manufactured for the transportation of drinking water and exhibits an excellent corrosion resistant property.
The chlorination process of this type of polymer pipe differentiates because it is capable of withstanding a broader range of temperatures than other PVC. Due to this, C-PVC is mostly utilized in residential and commercial construction.
PVC-Hi or Hi Impact pipes are PVC pipes that are conventional, having a modifier that makes them very resistant to external blows. To improve its durability, its composition is a mixture of compounds, including PVC. It needs to have the ability to be effective under high pressure and have long term strength.
Before it can be considered as PVC-Hi, this type of pipe has many standards and regulations it must comply with. Many requirements must be met by this pipe as it is utilized for the transport of natural gas, a volatile substance.
PVC cables are a durable, thinner, and eco friendly type of cable. They are designed to withstand extreme weather and are fire retardant. PVC cables have a useful life of over twenty years and are widely used as part of construction projects. Since they are thinner with smaller diameters, PVC cables and wires are installed as indoor wiring since they allow more wires to be added to a conduit.
The high quality construction of PVC cables makes them a very safe choice since they are not affected by weather, chemicals, and the passage of time. As a versatile and pliable form of cable, PVC cables can be adapted to fit any application.
PVC cables are any electrical wire cable that uses PVC as its insulation. It has become the insulation material for cables because of its many positive properties that makes it a resilient material regardless of the conditions. PVC cables are used for domestic appliance wiring, internal circuit wiring, and home wiring. Part of the flexibility of PVC cables is having a type to fit every application. What is important is to choose the right cable to fit the conditions where it is needed.
PVC siding is a form of protective covering used as siding on a house and window frames. As with all PVC, siding and window PVC is durable, affordable, and helps conserve energy as an airtight insulation material with sealing abilities that are several times greater than other construction materials. PVC siding prevents the problems associated with wood siding and has become the traditional way to protect homes. It never needs to be repainted and can be easily cleaned with soap and water or other forms of cleaners.
The wide use of PVC siding is due to the seamless finished look it provides. Each piece locks together to form a tight and secure seal. PVC siding has a longer useful life than would and is maintenance free with an outstanding appearance that never fades, cracks, or peals.
PVC packaging is flexible, lightweight, cost effective, transparent, tough, and safe with properties that do not affect the taste of a product. Its tight seal protects against contaminants, dirt, dust, and microorganisms. Since PVC is impervious to water and oxygen, it prevents foods from spoiling and keeps products on the shelf longer.
One of the provisions of the medical field is the immediate disposal of medical equipment and devices such as syringes, gloves, and anything that comes in contact with the patient. PVC packaging is used to collect medical devices for radiation sterilization. As an additional safety measure, blister packages for pills and capsules are made of PVC to ensure that they have not been tampered with.
There is a wide assortment of products for the home that are made of PVC such as protective clothing, shower curtains, tents, flooring, and tarps, to name a few. The versatility and adaptability of PVC makes it an ideal material for a wide array of applications and functions. Its stability and durability ensures that products remain useful for years with very little wear.
The number of household uses for PVC are endless. Using the various plastic manufacturing processes, engineers design and develop chairs, bowls, trash cans, mixing bowls, and high chairs using PVC as the main structural element. It is one of the most prevalent and widely used plastic vinyl products on the market today.
The brief list of PVC products presented here are only a sampling of the many products produced using this useful and necessary material. Due to its excellent strength and dependability, new PVC products are constantly being developed and created.
Clear PVC allows for the monitoring of the functions of a system as the system is in operation, which is necessary in laboratories, product production, and manufacturing. A crucial area where clear PVC is essential is clean room applications where there is a need for constant and continuous monitoring of the processes of the room in order to maintain its integrity.
As with all forms of PVC, clear PVC is corrosion resistant, which makes it capable of handling acids, bases, and corrosive chemicals. The smooth interior surfaces of its walls allows for the free flow of transported materials without sediment buildup. Clear PVC is ideal for use in medical applications and sterile environments since it resists bacterial and biological growth.
Normal PVC is a transparent amorphous thermoplastic. CPVC has excellent mechanical properties and impact resistance with water clear clarity. It can be used for exterior applications since it is formulated to block the effects of UV rays.
Clear PVC is made by the chlorination of a PVC polymer that raises the chlorine content to 66%. Chlorination reduces the attraction of the molecular chains, which makes CPVC easy to stretch. In CPVC, 40% of the bonding sites are filled with chlorine atoms, which are large and protect the chain from attack.
Batching is a critical part of the manufacturing of clear PVC since it involves the proper formulation of the PVC resin, plasticizers, stabilizers and additives. In order to achieve the desired results, the various components have to be precision measured, monitored, and controlled. Any slight variation can negatively affect the final CPVC. The final result of the batching process is pellets or a powder, which are used for further processing.
The chlorination process is used to change the properties of PVC, in this case clear PVC. It involves exposing PVC material to a measured and controlled quantity of chlorine gas. With clear PVC, chlorination enhances the PVC’s ability to withstand the effects of high temperatures and chemicals. During the process, the chlorine gas reacts with the PVC material to combine chlorine atoms with the polymer chain of the PVC.
The powder or pellets from the chlorination process are poured into a hopper that feeds into the barrel of an extruder. As the powder or pellets are moved by the screw along the barrel toward the CPVC die, it is heated and melted then forced under pressure through the die. The extrusion process is used to produce clear profiles and tubing.
Extrusion is used to make profiles and tubing while calendaring is used to produce sheets of clear PVC, a process that involves heating of the PVC powder such that it becomes soft and pliable. Once the material is sufficiently heated, it is passed through rollers that flatten, compress, and shape the material into sheets of various thicknesses, which can be from a fraction of an inch up to several inches.
The strength and durability of clear PVC makes it an essential part of several applications, above and beyond its traditional use for medical purposes and research. Since the chlorination process radically increases the strength of clear PVC, it has become an important component for several industrial applications.
Clear PVC has become increasingly popular as more and more uses for it have been discovered. There are several properties and characteristics of clear PVC that make it the perfect choice for replacing metal in critical applications.
The physical properties, characteristics, and specifications of clear PVC make it the first choice for applications involving chemical processing, mineral processing, and the handling of toxic materials. It is a long lasting, unfailing method for dealing with harsh and hazardous industrial conditions.
PVC is produced in two general forms which are: a rigid or unplasticized polymer (RPVC or uPVC) and flexible plastic polymer. In its base form, PVC has a rigid and brittle structure and has to be enhanced by various additives and stabilizers.
Rigid PVC is used as part of sewage disposal, agriculture, and plumbing. Plasticized PVC is flexible, softer and amenable to bending because of the addition of plasticizers like phthalates (e.g. diisononyl phthalate or DINP). Plasticized PVC is used for the insulation of electrical wires or in flooring of hospitals, homes, schools, and other areas where a sterile environment is necessary. In some cases, it is used as an alternative to rubber. Unplasticized PVC is used in construction as a pipe for plumbing and siding.
Rigid PVC does not contain phthalates, a group of plasticizers that add flexibility to PVC. Phthalates is a group of chemicals that can be found in hundreds of household products. When a PVC product does not have phthalates, it is known as uPVC or rigid PVC. This type of PVC is used as water containers and building materials. uPVC is fade resistant with the color going throughout its thickness.
As with all forms of PVC, uPVC has a wide assortment of uses and is commonly found as a building material and replacement for copper and aluminum piping for waste lines, irrigation systems, and pool circulation systems. It is an ideal replacement for metal products since it is easy to form and cut.
PVC and CPVC differ in the temperature range that each type of polymer can withstand. CPVC is capable of handling temperatures of up to 200 degrees Fahrenheit, while PVC peaks at 140 degrees Fahrenheit.
If the temperatures rise above the maximum acceptable temperature, both PVC and CPVC start to soften. This increases the risk of joints and the failing of pipes, and falling of the plumbing system. Due to the differences in the material’s chemical composition, the bonding agents, solvent cements, and primers are different for CPVC and PVC.
PVC has a high density compared to most plastics. It is also readily available and cheap. Unplasticised rigid PVC ranks well for hardness and durability. Rigid PVC exhibits excellent tensile strength. PVC is a thermoplastic material, which reacts in almost the same way plastic reacts to heat. At their melting point, thermoplastics turn into liquid.
PVC has a range of melting points from 100 degrees Celsius to higher values like 260 degrees Celsius depending on the types of additives. Thermoplastics can be heated until they reach their melting point, cooled, and reheated again without any significant degradation. Instead of burning, thermoplastics such as propylene liquefy allows them to be injection molded in an easy way and then recycled subsequently.
In contrast, thermoset plastics can be heated only once, typically during the injection molding process. During the first heating, thermoset materials set, resulting in an irreversible chemical change. If a thermoplastic material is heated for the second time, it only burns. This characteristic makes thermoset materials poor materials for recycling.
The basic chemical structure of PVC is detailed below.
PVC is a plastic with the following chemical formula (C2H3Cl)n. The content of chlorine by weight is more than half.
The various additives applied in PVC include:
Lubricants are utilized for the reduction of friction during processing. External lubricants can reduce friction between the polymer and the equipment for processing, whereas internal lubricants work on the granules of the polymer (PVC).
Several PVC flexible applications like extruded profiles, injection molded soles and footwear; calendered films make use of liquid mixed metal stabilizers. Liquid mixed metal stabilizer systems are mainly based on zinc, barium, and carboxylates.
Generally, the requirement of co-stabilizers, antioxidants and organophosphates is essential in liquid mixed metals like CaZn and BaZn for the provision of optimum performance. Cadmium-based stabilizers have been successfully replaced by BaZn stabilizers.
Heat stabilizers are necessary in every PVC formulation to prevent the decomposition of the PVC by heat and shear during processing. They can also improve the resistance of PVC to daylight, heat aging, and weathering. To add on top, heat stabilizers influence the physical properties of the PVC importantly and they also influence the cost of the formulation. The choice of heat stabilizer is dependent on a number of factors such as technical requirements of the polymer product, cost, and regulatory approval requirements.
A plasticizer is a substance added to the polymer to improve its flexibility, make it resilient, and easier to handle. The choice of plasticizers depends on the final properties required by the final product, and the application of the product. There are many different types of plasticizers (more than 300), of which about 50 to 100 are used commercially. The most commonly used plasticizers are phthalates which can be separated into two distinct groups with applications and classes that are very different.
Phthalates of low molecular weight contain eight or fewer carbon atoms in their chemical structure. These include DBP, BBP, DIBP, and DEHP. These phthalates have very limited uses in specific applications.
Phthalates of high molecular weight have 7 to 13 carbon atoms in their chemical structure. These include DPHP, DTDP, DIUP, DIDP, and DINP. In many everyday uses, including cables and flooring, HMW phthalates are safely used.
Special plasticizers like adipates, benzoates, citrates, and trimellitates are utilized where special physical properties are required, such as the ability to withstand very low temperatures or the importance of increased flexibility.
Many of the PVC products that are used everyday but tend to be taken for granted consist of phthalate plasticizers. They include blood bags, electrical cables, footwear, stationery, toys, and medical tubing. Phthalates are utilized in other non-PVC applications like rubber products, paints, adhesives, and some cosmetics.
These are not strictly necessary for the plastic’s integrity but are used to add other properties. Optional additives include impact modifiers, processing aids, nitrile rubbers, filters, flame retardants, pigments, and colorants.
This chapter will detail the benefits of PVC, including its applications and the recycling of PVC.
As much as PVC may have drawbacks such as:
However, the benefits of using PVC far outweigh the drawbacks. These benefits will be discussed and detailed below.
PVC has remarkable electrical insulation properties, making it ideal for use in cabling applications. It has a good impact strength and weather-proof attributes that make it ideal for construction products. PVC has extensive medical approvals and food contact.
The processing of PVC is easy. It is a long lasting material that is tough and lightweight. The production of PVC requires very little energy, which is unlike the production of other plastics.
Outstanding characteristics of PVC is its clarity and being organoleptic where it does not influence the taste or flavor of foods making PVC an ideal packaging material.
Its carbon footprint is relatively small. PVC windows help to cut energy bills. It is fully recyclable. It reprocesses well and can be recycled into second or third life applications with ease due to its properties.
PVC pipes have many benefits, such as durability and cost-effectiveness, which makes them highly favorable. The other benefits of using PVC pipes are explained below.
PVC pipes are safe to use in the transport of water for drinking. Due to the high resistance to corrosion property of PVC, it is harder for bacteria to breed on it, therefore making it an asset that is more valuable to the public. To add on top, the makeup of PVC turns into a sort of barrier from contaminants to make their way into the drinking water.
PVC is a plastic with low carbon content, meaning it needs fewer resources and less energy to manufacture. Since PVC is lightweight and uses less energy during production, it is easy to package and ship. Pumping costs are reduced by the smooth surfaces of pipes made using PVC, which further reduces energy costs of manufacturing processes. PVC pipes are recyclable and sustainable.
PVC can be recycled up to seven times and still retain its properties. Natural resources are preserved by recycling PVC. With each kg of recycled PVC, 2 kg of CO2 is saved. In this age of sustainability and environmental preservation, PVC is one of the most environmentally friendly materials on the market and can benefit the local economies by protecting landfills and waste dumps.
One of the key factors of modern industry is the production of products with longevity without the need for replacement. PVC pipes are both lightweight and durable with the ability to last for decades due to their high resistance to stressful conditions. It is this strength and durability that has led to PVC’s popularity and multiple uses. Added to these positive properties, PVC costs less, is easy to install, has lower operating costs, and requires very little maintenance.
The applications of PVC include:
PVC is used in a broad range of construction products. PVC is ideal for window profiles due to its strong, durable, lightweight, and versatile characteristics. It is also ideal for cabling applications because of its excellent insulation and inherent flame retardant properties.
Examples of PVC construction products are listed below:
PVC is used in many life saving and healthcare products. It is used in surgery, drug delivery, pharmaceuticals, and medical packaging because of its cost efficiency and unrivaled performance characteristics.
Examples of PVC healthcare products are listed below:
PVC is used as insulation for cables due to its ease of handling in installation, flexibility and inherent flame retardation. PVC cables are very strong and long lasting; they do not harden and crack over time and are used in many applications that include telecommunications and electric blankets.
Automotive applications are listed below:
Because PVC is environmentally friendly and also because of its highly versatile property, it is used as a construction material that is extensively utilized in the construction of sporting venues. This includes use in roofing, seating, floorings, and electrical wiring and piping. In addition, PVC is used by athletes from the shoes and clothes they wear to equipment they use and the surfaces they compete on.
The structure of PVC, together with its composition, lends itself to being recycled mechanically, with reasonable ease, to produce recycling material of good quality. It is important to sort PVC materials when recycling. The PVC industry invested greatly to develop sophisticated recycling schemes to ensure the reuse of large amounts of PVC in a new generation of products that are advanced, energy efficient, and sustainable.
This investment has meant not only the recycling of production off cuts, but also products like PVC-U windows and doors are recycled on a large global scale. The process of recycling old windows is far more complex than off-cuts due to contamination like building debris need to be removed before re-processing.
Polyvinyl chloride (PVC) is a tough synthetic polymer that exists in two forms which are plasticized and unplasticized PVC. Plasticized PVC has more plasticity, flexibility, and it’s softer due to the presence of a plasticizer. Many types of plasticizers are available that result in the polymer (PVC) having a variety of properties when added to it. Different PVC products are available with different properties depending on the type of PVC used. It is important to take note of the properties of the type of PVC used in the product that one can purchase for a certain application. To add on, PVC is a material that is long lasting, cheap and it can be applied with greater ease, for example in the electrical field where it is used as insulation for cables. PVC has a great diversity of applications, including floor and wall covering, making doors and windows, sewer pipes, water transport pipes, and natural gas transport pipes.
Nylon tubing, also known as polyamide tubing, is a type of tubing made from polyamide resin, which has a strong resistance to abrasion. It is used in high-pressure and high-temperature applications...
Plastic tubing is a form of tubing that is manufactured from a mixture of a polymer with a variety of chemicals to form a material that can be solid or flexible. Since its first use in the 1950‘s, plastic tubing has revolutionized industrial processes and has found a use in a wide variety of applications...
Poly tubing is a highly flexible, lightweight, and durable tubing that is produced from polyethylene, a polymer that is made from the polymerization of ethylene. It is a very versatile form of tubing that has break and crack resistant walls...
Silicone tubing is a very tough elastomer that exhibits high strength, flexibility, and resistance. Silicone tubing can be stretched without tearing and is highly versatile. It cannot be weakened with repeated bending and twisting due to...
Plastic channels are plastic products that have linear extruded profiles. They have a constant cross-sectional shape across their axis. They are long and narrow structures, and their depth is relatively short. These products serve a variety of functions and uses...
Plastic extrusion, also known as plasticating extrusion, is a continuous high volume manufacturing process in which a thermoplastic material -- in a form of powder, pellets or granulates -- is homogeneously melted and then forced out of the shaping die by means of pressure...
Plastic materials are objects artificially made from organic compounds called polymers along with other additive components. They possess excellent formability, making them extremely versatile for many different fabrication and manufacturing processes...
A plastic tank is a large capacity liquid or granular storage unit that can be vertical, horizontal, below or above ground, as well as movable. They are designed to hold several gallons of a variety of substances for long periods without experiencing wear, weathering, or deterioration...
A plastic rod is a solid plastic shape made by the process of plastic extrusion or plastic co-extrusion. These have a contrast of plastic tubing and hollow plastic profiles. Plastic rods are found in various industries, including...
Plastic trim products are extruded linear profiles that can be made to any length. Because of its ability to attach, hold, and seal, plastic trim has many applications. Plastic, HDPE, LDPE, butyrate, PVC, acrylic, and...
A plastic water tank is a large capacity container designed to store water for household, agricultural, irrigation, and industrial manufacturing use. There are various types of water tanks produced to meet the needs of specific applications, with...
A poly tank is a plastic storage tank used to store, transport, and collect water, other liquids, and granular or powder materials. They are made of polyethylene or polypropylene and are a cost effective, lightweight, and easy to handle...
A coupling is a device that is used to transmit power between two shafts connected together at their ends. Couplings serve one primary purpose: to join two pieces of rotating equipment together, while...