Fiberglass Molding
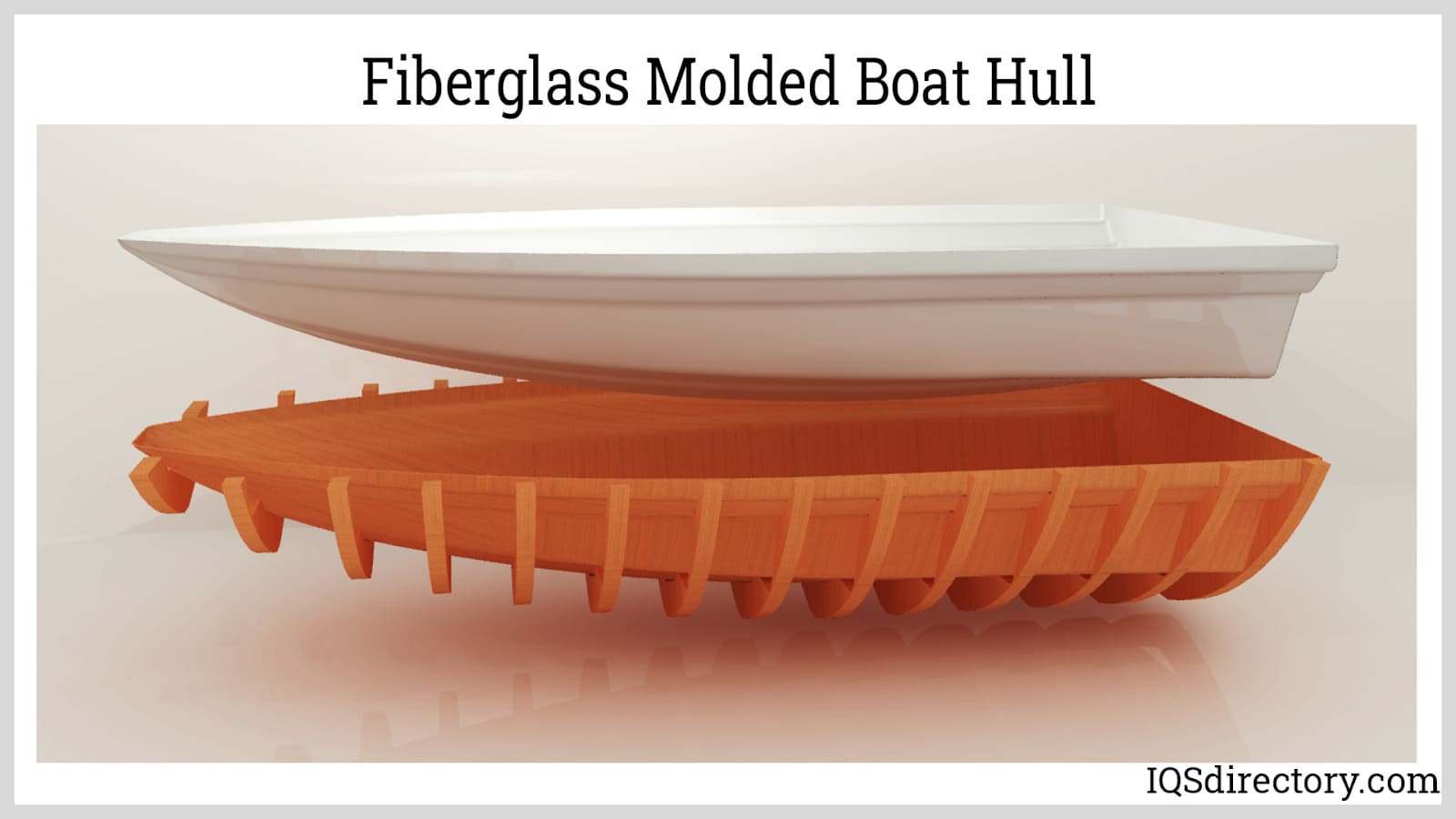
Plastic molding is one of the most successful forms of manufacturing and a vital part of nearly every product that is on the market. The many varied ways that plastic molding is completed adds to the uniqueness of its products. The ability of plastic molding to create any type of shape, design, or configuration, regardless of its complexity, is the main reason for its success and growth.
A major benefit of plastic molding is the wide range of materials that can be used in the plastic molding process, which include fiberglass supported plastics, polyurethane, polypropylene, polyvinyl, and various forms of acrylics. Each of these materials is heated and shaped using different processes depending on the form of the final product, the products required strength, and the intricacy of the part‘s design.
The most common form of plastic molding is injection molding, which involves the heating of resin pellets and injecting them into a closed mold. There is an endless array of products that are produced using injection molding, which include encapsulated electric coils, protective helmets, car bumpers, syringes for medical use, and several types and kinds of toys. This perfected and reliable process has become an essential part of the manufacturing of many items for daily use.
Blow molding is another widely used process that creates everything from plastic bags to plastic bottles. Items produced by blow molding can be designed to hold several types of products such as make up, chemicals, and soft drinks. As the name implies, blow molding involves taking heated resin and forcing air into it until it takes the shape of the mold. The efficiency and speed of blow molding is one of the reasons that it has become such a popular form of plastic manufacturing.
Many products need to have some form of coating to give them extra strength and provide a protective covering. The dip molding process involves taking a completed product and having it immersed in a resin bath. Once the coated product is removed from the bath, it is put through a drying process to cure the plastic coating and harden it. This particular process is one of the ways that plastic dip molding is used to perfect and improve products.
One of the more popular and widely used forms of molding is plastic extrusion, a process that can produce a wide array of flexible, sturdy, and durable products. As with all forms of plastic molding, extrusion begins with heated resin. Unlike the other processes that place the resin in a mold, extrusion forces it through a die that has a profile of the shape of the final product. Extrusion is a fast and efficient process that produces products to fit a variety of applications.
A plastic processing technique that is used to produce individual and large plastic products is rotational molding that is able to produce large bins, high quality auto parts, boats, and sports equipment. The process involves the use of a heated hollow mold that is filled with a shot weight of plastic material. The mold is slowly rotated to evenly distribute the plastic to the walls of the mold. The advantage of using rotational molding is the exceptional strength and structural complexity of the final product.
Vacuum forming is a method of plastic molding that does not involve the use of heated resin pellets but takes sheets of plastic and forces them into the mold. It is an open mold process, which means that there are not two halves to the mold and involves the thermoforming of the plastic sheets. The thermoforming process of vacuum forming is used to make the walls of spacecraft and hot tubes.
Plastic molding is an ever growing industry that has become an essential part of the design and production of many of the products used in the home and by industry.
In the creation of fiberglass-reinforced plastic products, fiberglass molding is the most frequently used process. Fiberglass is made when molten glass is extruded through very fine openings in a tool. This extrusion process produces threadlike formations in the glass that are later put through heat treatment or pressing and mixed with plastic resin.
Fiberglass molding is used to fabricate a multitude of products such as machinery support products, electric circuit boards, shells of racing cars, and panels. This process is used extensively because fiberglass does not shrink or expand with changes in temperature. Furthermore, it does not absorb water, is resistant to chemicals, has high strength-to-weight ratio, is not flammable, and can function as an insulator from electricity. Learn more about fiberglass fabrication.
This is one of the most common forms of plastic molding, and the process can range widely in cost, depending on the complexity of the part being molded and the materials which are used. Injection molding produces three dimensional, solid parts with mid to high strength and is unique in plastic molding processes, as it can produce relatively complex shapes. Advanced injection molding techniques include insert molding and reaction injection molding (RIM); insert molding dies contain a solid object, such as an electric coil, around which the molten plastic is injected, creating an encapsulated object. Reaction injection molding combines a liquid resin thermoset polymer (typically polyurethane) with liquid polyisocyanate, which acts as a reagent within the mold, causing the polymers to expand and form bubbles (either open or closed cell foam), filling the mold.
Injection molding machines consist of three main sections: the hopper, where plastic resin pellets are fed into the machines; the extruding barrel, containing a small screw conveyor which simultaneously "plasticizes", or melts, the plastic resin while moving it towards the die; and the die, or closed mold, into which the melted plastic is injected under pressure. The plasticizing of the resin is often assisted by electric band heaters and cartridge heaters wrapped around the extruding barrel. Learn more about injection molded plastics.
Numerous products are made from blow molding. Any consumer item that has a three-dimensional shape and is hollow, such as tanks and CD cases, is manufactured using the blow molding process. Blow molded products are capable of holding a variety of substances such as herbicides, pesticides, cosmetics, and automotive oil. The plastic utilized for these processes are all thermoplastic resins. They include acetal, polysulfone, polyamide, polystyrene, butadiene styrene, Barex, polyvinyl chrloride (PVC), and high and low density polycarbonate.
Plastic blow molding can be categorized into three types: injection blow molding, extrusion blow molding, and stretch blow molding. All of these processes consist of two steps, which vary the most in the early stages. The ultimate shape of the blow molded plastic depends on the shape of the mold cavity. While blow molded products come in an assortment of standard shapes and sizes, there are some products that can be made using custom blow molding, and are thus used for special applications. Learn more about blow molding.
Dip molding plastic is one of the simplest means of molding plastic and, like blow molding, is capable of producing a large number of parts or products at low cost. The dip molding process serves in one of two manufacturing capacities: to create whole flexible or rigid products such as rubber gloves, condoms and plastic caps; or to coat pre-manufactured products such as wire racks, wire cable and plastic coated handles.
Both manufacturing methods use the same basic process: a large volume of glass or metal molds are surface prepped, so that the final product may be easily stripped from the mold when dry. Objects which are to be coated in plastic are buffed and prepped so that the plastic coating stays firmly on. The molds are then dipped into a vat of molten polymer or elastomer resin; depending on the desired thickness and the consistency of the polymer material being used, molds are often dipped multiple times, sometimes alternating between cold water or another solidifying reagent and the molten polymer vat. Flexible products with complex layers, such as kitchen gloves, may have other layers, such as a fabric layer, applied in between polymer coats. Once the molten plastic has set, the plastic product is ready to be removed from the mold, trimmed, cleaned and finished. Learn more about dip molding.
Plastic extrusions are formed similarly to the way injection molded plastics are formed, although extrusions are formed through an open die. Plastic resins such as PVC, acrylic, polypropylene or ABS are fed through a hopper into the extruding barrel, which shears and melts the resin, pushing it through the open die to form a profile or shape. This profile is immediately immersed in cold water to set the plastic; the profile is extruded continuously, passing through the die, through cold water tanks and onto a sawing table, where pre-specified lengths are cut.
Extruded plastics may be manufactured to meet the specifications for a broad range of niche applications, including but not limited to building trim, window and door sealants, vinyl siding, PVC pipe and surgical tubing. Plastic sheets and flexible plastic sheet rolls are also formed through extrusion, being pulled and stretched instead of cooled after the melted plastic exits the die; flexible plastic sheets are rolled through a series of large calenders before being rolled onto a tube. Learn more about plastic extrusions.
Plastic tubing refers to any number of tubes and pipes produced using plastic.
The versatility of plastic tubing makes it a presence in countless industries, from the rugged industrial standards of aerospace and industrial applications to the sterile safety standards of medicine and beverage tubing.
Learn more about plastic tubing.
Polyurethane is a material that is valued for its uses in memory foam products due to its flexibility and rigidity. Polyurethane is also a valuable material for products such as solid plastic forms, polyurethane rods, urethane wheels, urethane brushings, and urethane sheets. Polyurethane moldings have an excellent reputation for their high performance. Their longevity is greater than that of plastic, and are more impact-resistant than rubber. It also has elastic memory, reduces noise, and is resistant to heat and chemicals. It possesses many of the good qualities of metal, rubber, and plastics, and is capable of forming strong adhesive bonds with most plastics and metals.
Polyurethane molded parts require little to no additional finishing. This process is used by manufacturers to fabricate a wide array of moldings, parts, bowling balls, urethane bumpers, polyurethane belts, conveyor bushings, electrical potting compounds, press tool blocks, and pneumatic seals. Polyurethane products are used extensively in industries such as athletic equipment, engineering, manufacturing, industrial, food processing, automotive, and construction. Learn more about polyurethane molding.
Rotational plastic molding is capable of achieving plastic parts with more strength and structural complexity than any other plastic molding processes. Unlike other plastic molding methods, rotational molding produces a relatively low volume of parts in what are typically short runs, due to the amount of time and equipment required for rotational molding. Rotationally molded plastics may not be mass produced like blow molded, dip molded or thermoformed parts, and this process is typically reserved for complex or high-performance parts such as plastic figurines and military-spec rackmount carrying cases.
The rotational molding process is unique among plastic molding techniques. A molten polymer - often polyethylene or polycarbonate - is poured into a closed three dimensional mold; the mold is then placed within a gyroscope-like structure which slowly spins, evenly coating the entire interior of the mold with the polymer to form a hollow shape. This process is not only more effective at creating complex three dimensional structures, but it also creates parts with uniform material consistency and, consequently, very high strength. Learn more about rotational molding.
Vacuum formed plastics are used as faceplates and semi-flat components in a wide range of industries, particularly in electronic equipment such as fax machines, keyboards, phones and home appliances. Also known as thermoforming, or pressure forming, the vacuum forming process begins with stock plastic sheets rather than polymer resin pellets; these sheets are heated until the polymer reaches a flexible temperature, then they are vacuumed into an open mold, causing the heated sheets to "thermoform" to the exact shape of the die mold beneath. Twin sheet thermoforming is commonly used to create large and precision application parts such as hot tubs and interior wall panels for aerospace, but thermoforming is also a highly cost-effective means of producing three-dimensional plastic packaging. Blister packs, clamshells, plastic covers, plastic trays and other plastic packaging can be produced for low costs at high runs by vacuum forming.
Learn more about vacuum forming.