Fiberglass Molding
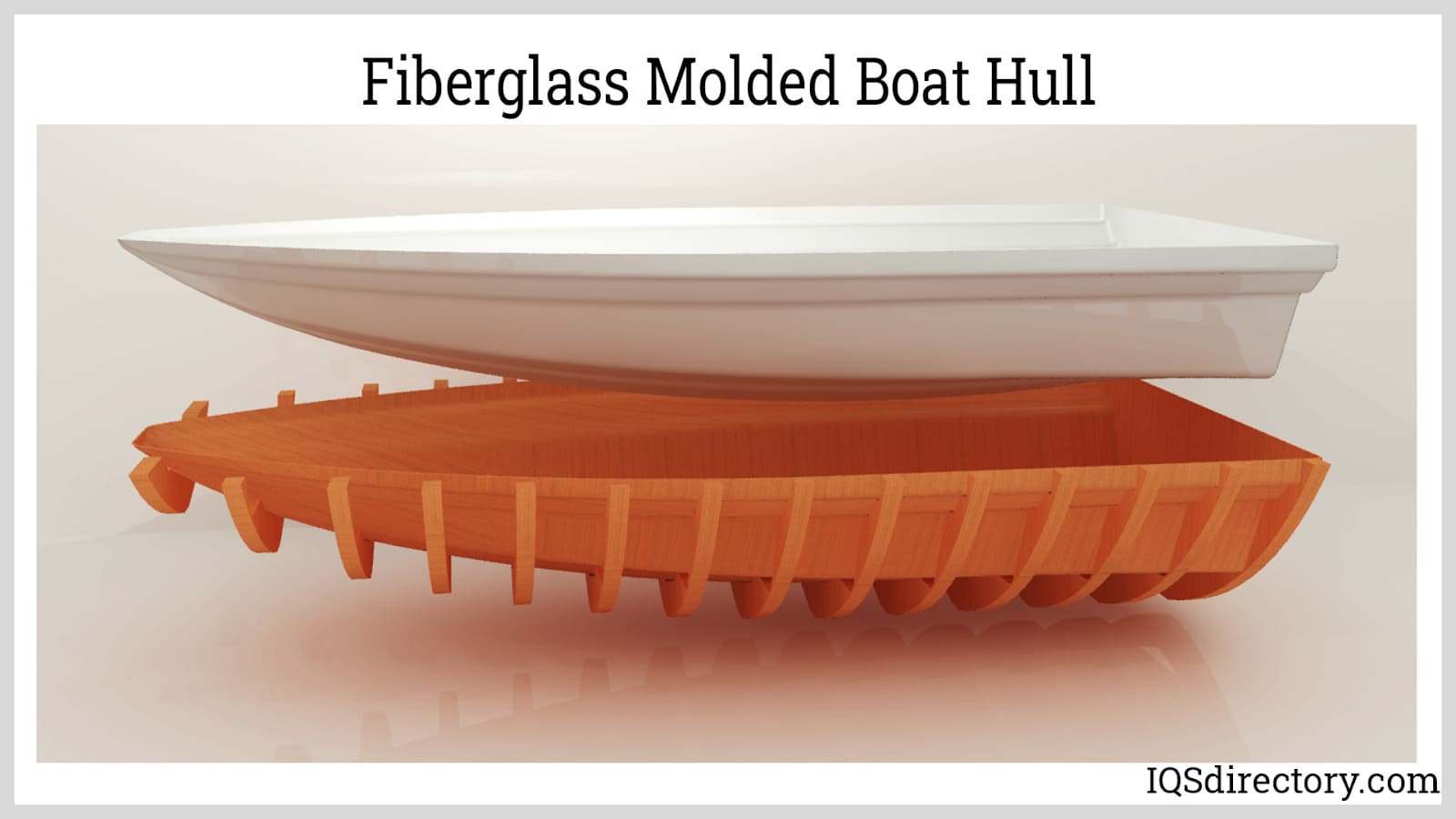
Fiberglass molding is a method for forming complex and intricate parts using fiberglass resin. Though there are several reasons for producing parts and components from fiberglass, the most pressing reasons are the...
Please fill out the following form to submit a Request for Quote to any of the following companies listed on
This article will take an in-depth look at fiberglass sheets.
You will understand more about topics such as:
Fiberglass sheets are sheets made of thin, small diameter superfine glass reinforced with plastic. The sheets have exceptional tensile strength with resistance to corrosion, fire and chemicals, such as organic solvents, bleach, and acids. The most valued aspect of fiberglass sheets is their strength-to-weight ratio, which is due to the fibers carrying the load while the plastic distributes the weight. Fiberglass sheets are available in thicknesses that range from 1.5 mm up to 75 mm.
Fiberglass is composed of glass fibers interwoven in a resin matrix. Although all fiberglass is basically the same, there are differences in the quantities of raw materials and their proportions. The basic raw materials are silica sand, soda ash, and limestone with differing amounts of borax, calcined alumina, magnesite, kaolin clay, and feldspar. Silica sand forms the glass portion of fiberglass filaments while soda ash and limestone lower the melting point of the glass. Additional ingredients, such as borax, change the properties and characteristics of fiberglass.
The manufacture of fiberglass sheets and panels begins with the manufacture of fiberglass. Although there are certain proprietary methods for the production of fiberglass, the basics of the process remain the same, which begins with the making of glass fibers.
Extrusion is used to manufacture fiberglass, a process that forces the molten material through a bushing. The manufacturing process begins with the melting of the raw materials, which are extruded through bushings or spinnerets with 200 to 3000 superfine orifices. As the filaments leave the extruder, they are combined with a resin that is used to shape and form them.
The two types of filaments are continuous filaments and staple filaments. The filaments are sized (coated in a chemical finish) and bundled into rovings. The number and quantity of the filaments in a roving and how thick the individual filaments are determines the weight of the glass fibers, which is expressed in yield.
The initial stage of fiberglass manufacture is called batching. This is when raw materials are prepared to be fed into the furnace. In this stage, raw materials must be carefully weighed in exact quantities and thoroughly mixed (batched). Due to increased technology batching has become automated, using computerized weighing units and enclosed material transport systems.
The batch is fed into the furnace, after it is prepared, where it will melt. The raw materials are fed into the furnace to begin the melting process. Electricity, fossil fuel, or a combination of the two can be used to heat the furnace. The temperature must be precisely controlled to maintain a smooth, steady flow of the molten glass.
The furnace is typically divided into three sections, with channels and aid glass flow. The furnace’s first section is where the batch is first fed, melted, increased in uniformity and removal of bubbles. The molten glass then flows into the refiner, where it is cooled, and its temperature is reduced. The final section is the fire hearth, beneath which is located a series of four to seven bushings used to extrude the molten glass into fibers.
After melting, the next stage is fiberization. In this stage the molten glass forms into fibers. Glass fiber formation or fiberization involves a combination of extrusion and attenuation. In extrusion, the molten glass passes out of the fire hearth through a bushing made of an erosion-resistant platinum/rhodium alloy with very fine orifices. The filaments are cooled by water jets as they exit.
The extruded streams are drawn through attenuation into filaments with diameters that range from 4-34 micrometers (µ). A high-speed winder catches the molten streams and applies tension that produces thin filaments. Different processes are used to form fibers with the main types being continuous filament and staple fiber processes.
With the continuous process, fiberglass filaments of indefinite lengths are produced. As the molten glass flows through the bushing, high-speed winders catch the strands and wind them at a very high rate of speed. The process produces fiberglass yarn.
With the staple fiber process, the molten material passes through small openings after which a jet of compressed air converts the streams of molten material into long, thin fibers that form slivers that are woven into yarn.
Chemical coating is the final stage where a chemical coating or sizing is applied. The sizing can range between 0.5 to 2.0% by weight, including binders, lubricants and coupling agents. Abrading filaments can be mitigated by using lubricants, which minimize breaking at the collection and wounding into forming packages.
The filaments are processed into fabrics using weavers and other converters. The coupling agent aids in attracting the fibers to specific resin chemistry. This strengthens the interface of the fiber and matrix adhesive bond and improves the resin wet out. Depending on the sizing chemistries, fibers can be more compatible with epoxy and some with polyester resin. Fiber abrasion can be reduced by applying lubricants by either adding them into the binder or spraying directly on the fiber.
The treated fibers are used to begin the process of producing fiberglass mats that can be used to make fiberglass sheets and are a nonwoven, high quality material. The fiberglass fibers come in a wide variety of lengths and diameters, which influences the performance of the nonwoven fiberglass. Large diameter, long fibers produce a completely different form of mat from small diameter, short fibers.
The fibers are broken apart and suspended in a pulping system to create a homogeneous mixture where whitewater chemistry is used to keep the fibers suspended. Without the aid of processing chemicals, the fibers would clump together. This aspect of the process is critical for the quality of the fiberglass matting.
Mat forming is a closed loop process that uses, in this case, a water system. After the pulping process, the fibers are distributed evenly across the full width of the mat forming machine. Adjustments to the machine determine the properties of the mat and its performance. During the matting process, the orientation and direction of the fibers changes. Fiber orientation determines the properties of a fiberglass mat in regard to its surface quality and strength.
Once the mat has been formed and the direction of the fibers has been achieved, the strength of the mat is low, which requires the use of a binder. There have been various types of binders produced over the years with modern binders being formaldehyde free and bio based. At this stage, mats can be soft as cloth or stiff for use as laminate.
During the drying process, water is removed from the nonwoven mats and the binder is cured. Drying conditions have to be carefully controlled to ensure the quality of the mats.
Woven fiberglass is a heavy fiberglass cloth with a high fiber content. It is created much like fabric cloth where the warp and fill threads cross alternately at right angles. Two types of weaving processes are twill and satin.
With a satin weave, one fill yarn passes over three to seven warp threads before reaching another warp. The straighter threads make the weave stronger by its strengthening of the fibers. A twill weave is a combination of a plain weave and satin weave.
Woven roving fiberglass has an increased fiber content produced by continuous filaments, is extremely strong, and is used for added thickness to laminates. It has a rough texture, which makes it difficult to combine with other woven roving materials. To overcome this difficulty and to produce layers of woven roving fiberglass, layers of mat fiberglass are placed between the woven roving sheets.
The production of fiberglass fibers is the beginning of the production of a wide assortment of fiberglass products, including fiberglass sheets and panels. The type of fiberglass material, such as woven roving, mat, and the various types of woven fiberglass, are the initial materials for different types of large flat fiberglass. The combined fiberglass, depending on the thickness of the fibers, can be thick and heavy or light like fine cloth.
The process for the formation of panels and sheets of fiberglass is called pultrusion, which is different from extrusion. With pultrusion, a pulling system pulls the combined materials through the pultrusion machine. The process includes a resin mixture of resin, such as polyester, epoxy, or vinylester, fillers, and additives and reinforcing fibers in the form of rolled fiberglass mats or rovings. Pultrusion is a continuous process that produces different lengths of fiberglass parts and materials. .
The pultrusion process begins with the mat or roving being saturated with the resin mixture, or wet out, and pulled through the heated forming die. The hardening of the resin begins with heat from the die where a cured rigid profile is formed. This basic process varies according to the geometry of the final fiberglass panel or sheet.
When the reinforcement material, mat or roving, leaves the resin impregnator, it is positioned to be formed. A preformer squeezes out excess resin before the material enters the die. In the die, a thermosetting reaction is activated to cure the composite of material. After the panels or sheets have been cured, they are cut to specific lengths after which they are allowed to cool to avoid cracking and deformation.
An aspect of the panel and sheet manufacturing process is the addition of a surface veil on the top and bottom of the panel or sheet. Surface veil material is added before the thermoset resin is impregnated into the fiberglass mat or roving. It provides a smooth even surface to the completed sheets or panels. Surface veils are made of dispersed glass or polyester fibers that offer protective properties.
There are many machines available to produce fiberglass sheets, and they are important in today's society because fiberglass sheets are widely used in various industries such as construction, automotive, and aerospace for their lightweight, strong, and insulating properties. Below we examine many notable manufacturers of machines used for fiberglass sheet production:
This series of machines by MFG (Molded Fiber Glass Companies) is designed for fiberglass sheet production, offering capabilities such as continuous filament winding, precise resin application, and curing systems.The MFG-FLS Series of machines by Molded Fiberglass Companies is known for its precise resin application, continuous filament winding capabilities, and advanced curing systems, enabling efficient and high-quality production of fiberglass sheets.
MVP's Patriot™ Filament Winding System is a versatile machine that enables the production of fiberglass sheets using the filament winding process, allowing for automated placement of continuous fibers onto rotating mandrels.The Model Patriot™ Filament Winding System by Magnum Venus Products stands out for its versatility and automated filament winding process, allowing for precise placement of continuous fibers onto rotating mandrels during fiberglass sheet production.
RIMSTAR offers a range of filament winding machines suitable for fiberglass sheet production, featuring advanced controls, programmable winding patterns, and multi-axis motion systems for precise fiber placement.The filament winding machines by RIMSTAR offer advanced controls, programmable winding patterns, and multi-axis motion systems, providing the ability to produce fiberglass sheets with precise fiber placement and customizable winding configurations
Cannon SpA provides complete production lines for fiberglass sheet manufacturing, including machines for resin impregnation, curing ovens, and cutting systems, enabling high-quality and efficient production processes.The Fiberglass Sheet Production Line by Cannon SpA is known for offering comprehensive solutions, enabling efficient and integrated production processes for high-quality fiberglass sheets.
Ashland offers equipment and systems for fiberglass sheet production, including resin impregnation lines, curing equipment, and finishing systems. The fiberglass sheet production equipment offered by Ashland provides a complete package for manufacturing fiberglass sheets with optimal quality and efficiency.
Please note that specific models and features may have evolved since my last update, and it is advisable to consult the respective manufacturers or industry resources for the most up-to-date information on the latest models and capabilities of machines used for fiberglass sheet production.
Fiberglass has properties that make it a good choice for various applications. It has additional benefits when reinforced with composites added to the glass strands.
Fiberglass sheets are reinforced with fibers that give the sheets varying degrees of flexibility and strength. The sheets are lightweight with a strong and resistant structure. They have a non-porous surface with a high resin content that does not retain moisture, which makes them useful in a wide variety of environments.
Fiberglass is an excellent insulation material, even in thinner layers. The combination of low moisture absorption, high dielectric strength and a low dielectric constant makes it the ideal material.
Fiberglass is not combustible since it is a mineral material. It has high heat resistance. Fiberglass does not support or propagate flames and if exposed to heat, it does not emit toxic products or smoke. It does not burn and is basically unaffected by curing temperatures used in industrial processing. Fiberglass will retain approximately 50% of its strength at extremely high temperatures.
Fiberglass is highly resistant to the attack of most chemicals and is resistant to corrosion.
Fiberglass is a dimensionally stable engineering material. It has no sensitivity to changes in temperature and hygrometry, making it very stable. It does not warp, bend, distort or shrink after exposure to extremely high or low temperatures as it has a low coefficient of linear expansion.
Fiberglass can have different types of sizes, which creates a bond between the glass and the matrix and can combine with many synthetic resins and certain mineral matrices like cement and plaster.
The use of glass strands composites eliminates thermal bridging, enabling considerable heat savings compared to asbestos and organic fibers. Fiberglass is a great thermal insulator because of its high ratio of surface area to weight.
Fiberglass maintains its form and is not impacted by the action of rodents and insects. It also does not rot, and it is not affected by most chemicals and weather because it does not decompose.
When exposed to water, fiberglass does not change in form. It does not absorb moisture hence it will remain unchanged physically and chemically.
Various proportions of different raw materials can be used to form fiberglass. The fiberglass formed can be categorized into the following types:
A-glass is also known as alkali glass or soda-lime glass and is resistant to chemicals. It is the most commonly available type of fiberglass and mostly It is used in making glass containers like jars and bottles for food and beverages and window panes. Soda-lime is much cheaper, chemically stable, hard, and workable. Soda-lime can be remelted and softened and thus best suited for glass recycling.
The A-glass type is made primarily from lime, soda, alumina, dolomite, silica, and finishing agents like sodium sulfate. A-glass fiber can be found as:
Flat glass - is used to make windows. A float process is used in forming flat glass. It has a higher quantity of magnesium oxide and sodium oxide and a lower quantity of silica, aluminum oxide, and calcium oxide as compared to container glass.
Container glass - is typically used to make containers. It is manufactured by blowing and pressing. Container glass is more chemically durable in containers used for food and beverage storage due to its low content of water-soluble ions such as sodium and magnesium.
Advantex glass is acid corrosion resistant. It can be used in applications where thermal fluctuation is greater due to its higher melting point. Advantex fiberglass contains calcium oxide in high quantities and is typically used in structures that are corrosion prone. Moreover, Advantex glass can be applied in the oil industry, mining industry, sewage systems, and power plants.
This is alkali resistant glass.
AR-glass is also known as alkali resistant glass. It is specifically designed for use in concrete. This is enabled by Zirconia which is added into the AR-glass structure and thus the fiberglass can be applied in concrete. When used in concrete, AR-glass prevents cracking thereby providing flexibility and strength to the concrete. AR-glass is not easily dissolvable in water and is generally unaffected by pH changes. AR-glass does not rust and can be easily added to steel mixtures and concrete.
The C-glass type is also called chemical glass and has good chemical impact resistance. The C-glass gives structural equilibrium when subjected to corrosive environments. This is facilitated by calcium borosilicate in high quantities. A-glass type chemicals used in its manufacturing have pH values that give high resistance to C-glass regardless of whether the environment is alkaline or acidic. The C-glass can thus be applied as surface tissue in the outer layer laminates of tanks and pipes used to hold chemicals and water.
Ingredient | % Composition |
---|---|
Silica | 62 to 65 |
Soda, Potash | 1.0 |
Lime | 6 |
Boric Oxide | 3 to 4 |
Magnesia | 1.0 to 3.0 |
Alumina | 11 to 15 |
D-glass is popular for being a low dielectric constant. This is facilitated by boron trioxide presence in its structure. The D-glass type of fiberglass is typically used in optical cables, cookware, and electrical appliances.
E-glass is also known as electrical glass and has good electrical insulation properties. It is an alkali glass. It is susceptible to chloride ion and cannot be used for marine applications. It is a lightweight composite material that is used in aerospace and industrial applications. E-glass is much cleaner to work with due to its draping characteristic. It was originally developed to be used in electrical applications, but it is now used in numerous other areas as well. Glass reinforced plastic can also be made with a combination of thermosetting resins. The glass reinforced plastic can then be used to make panels and sheets, which are applied in a wide range of industries. Structural integrity can be protected against any mechanical impact.
E-glass is very popular across industries because it has high strength, is cheaper, nonflammable, high stiffness, is not moisture sensitive, low density, electrical insulation, resistant to heat, and can maintain strength in various conditions.
Ingredient | % Composition |
---|---|
Silica | 52.5 to 53.5 |
Soda, Potash | Less than 1.0 |
Lime | 16.5 to 17.5 |
Boric Oxide | 10.0 to 10.6 |
Magnesia | 4.5 to 5.5 |
Alumina | 14.5 |
ECR glass fiber is also known as electronic glass fiber. It has acid and alkali resistance, waterproof properties, high heat resistance, lower electrical leakage, higher surface resistance, and mechanical strength when compared to E-glass. Its properties are generally better than E-glass properties. Unlike many other types of fiberglass, the ECR glass manufacturing process is environmentally friendly. ECR glass fiber is used to make transparent fiberglass reinforced panels with a longer service life. ECR glass has superior resistance to acid, water, and alkali and thus is more durable.
The same fiberglass can be known as R-glass, S-glass, and T-glass. Their modulus, acidic strength, wetting properties, and tensile strength is superior to that of E-glass. R-glass can be applied in the aerospace and defense industries. It is a high-performance and industry specific fiberglass produced in low volumes.
S-glass is also known as structural glass. It is popular for its mechanical properties, which include stiffness. S-glass is mostly useful when tensile strength is a critical consideration. Thus, S-glass is typically used in aircraft and building epoxies.
This is the best performing fiberglass type available. Silica can be found in higher levels in S2-glass, unlike in other fiberglass types. Thus, S2-glass has improved properties like high compressive strength, high temperature resistance, better cost performance, and high impact resistance. Due to its superiority in properties over conventional fiberglass types, S2-glass is typically used in the textile and composite industry.
Z-glass can be used in various industries, such as the concrete reinforcement industry, where it is used to create transparent products. Z-glass can be used in creating 3D printed fibers. Z-glass is reliable and durable due to its high acid, alkali, UV, mechanical, scratch, salt, and wear resistance.
This chapter will discuss applications and uses of fiberglass.
Fiberglass comes in various forms to suit various applications, the major ones being:
The fiberglass tapes are popular for their thermal insulation properties and are made from glass fiber yarns. The fiberglass tape is applied widely in applications such as hot pipelines, wrapping vessels etc.
The fiberglass cloth can exist as glass filament yarns and glass fiber yarns. Fiberglass cloth is typically used to shield heat in materials such as fire curtains.
The aircraft and aerospace industry require material that is lightweight and stable. S glass fiberglass sheets are the most used in this industry because of their favorable mechanical properties like high strength, high laminate strength to weight ratio. They have the highest retention at high temperatures. They are used to make wings, helicopter rotor blades, aircraft armor, flight deck armor, floors, and seats of aircraft. S-glass fiberglass sheets have no conductivity and offer low radar thermal profiles.
Fiberglass sheets have mechanical properties that are better than those of conventional construction materials making them suitable for the construction industry. They have less weight, are inflammable, have impact resistance, and high strength. Fiberglass sheets are used in the construction of commercial, residential, and industrial constructions, ranging from bathrooms to swimming pools to skylights for industrial buildings.
Fiberglass sheets are used to produce house building components such as roofing laminate, roofing sheets, door surrounds, over-door canopies, window canopies and dormers, chimneys, and windows.
In consumer goods, fiberglass can be used to make furniture frames and/or finished goods such as divider screens, decorative trays, wall plaques, sports equipment, playground equipment, etc. It is used as a primary material in these consumer goods because of its higher strength, lightweight, formability, durability, resistance to wear, and corrosion.
Fiberglass is the best material to make equipment or machinery which has to be resistant to corrosion. Some items have to be resistant to corrosion because they will be exposed to unfavorable and harsh environments. Fiberglass sheets are used in the manufacture of tanks to help them last longer. They are used in the energy production industry to make corrosion resistant equipment like underground petrol tanks, storage tanks, and cooling towers.
Fiberglass is commonly used in the marine industry due to its durability and strength. One of the major pros of using fiberglass in the marine industry is that it can be molded into different shapes easily. Thus, fiberglass can be used widely. It is used to make boats of all sizes and other equipment used in the marine. It is also used in the production of docks. Docks get corroded, rusted, and damaged by the salty seawater, so fiberglass is used here for protection.
Fiberglass sheets are widely used in the auto industry to form panels, sides, covers, and other design factors of automobiles. As the need to lighten the weight of automobiles has risen to lessen gas consumption, fiberglass sheets have become a necessary base material that lightens a cars weight but provides durability and strength. Fiberglass sheets are easy to form and provide engineers with the flexibility to create any design.
The high percentage of resin in fiberglass creates a smooth surface for the manufacture of hoods and helps with low aerodynamic loss. Common automobile parts made of fiberglass are front and rear bumpers, hoods, doors, and castings. It is widely used in sports to lower their weight.
It is estimated that most of the outer bodies of trains and buses are made of fiberglass sheets. HIgh speed trains rely on fiberglass for its strength to weight ratio and smooth surface due to the importance of aerodynamics. Aside from the use of fiberglass sheets for the manufacture of train and bus exteriors, it is also used for interiors and shields for carriage equipment. Of vital importance to the transportation industry is fire retardant materials, which makes fiberglass sheets perfect for construction of trains and trams.
Fiberglass grating is a composite material that is manufactured by combining resin with fiberglass to produce an architecturally attractive and corrosion resistant grating. It is lightweight, fire retardant, and non conductive, which makes it ideal for industrial structures such as raised floors, fire escapes, and drain covers. A major factor regarding the use of fiberglass grating is how easy it is to install compared to metal grating.
The two types of fiberglass grating are molded and pultruded. Molded fiberglass grating is created in a mold and comes in a variety of thicknesses, patterns, and sizes. Square mesh patterns make it possible to cut it for floor panel layouts. Rectangular shaped molded fiberglass grating is used for trench covers and walkways. Each type, square or rectangular, can be provided with a skid resistant surface.
The pultruded process for the manufacture of fiberglass grating produces profiles that are joined in the shape of a grating. They are highly durable, corrosion resistant, and low maintenance. Pultruded fiberglass gratings are capable of supporting loads over longer spans and are produced by drawing fiberglass rovings and mats through a resin bath and heated dies. The weight bearing bars and cross bars are locked with a recess tie bar.
This chapter will discuss disadvantages and advantages of fiberglass sheet as well as considerations when selecting fiberglass sheet.
Fiberglass sheets may have drawbacks which include:
However, the advantages of fiberglass sheets outweigh the drawbacks. These advantages include:
Before choosing the type of fiberglass, first consider the type of project and the needs of the finished product. Things to consider are damage tolerance, mechanical and physical properties that are favorable for the project in question. Make sure to also consider cost. After this, compare the findings with other alternative materials and select the most suitable one.
Fiberglass molding is a method for forming complex and intricate parts using fiberglass resin. Though there are several reasons for producing parts and components from fiberglass, the most pressing reasons are the...
Many of the products used daily are made possible by producers and suppliers of rubber and plastic. These substances are robust, adaptable, and capable of practically any shape required for various industrial purposes. Several varieties are...
Plastic fabrication is the process of designing, manufacturing, and assembling a product made out of plastic material or composites that contain plastic. There are numerous plastic fabrication methods known today, considering the wide variety of products made out of plastic...
Plastic injection molding, or commonly referred to as injection molding, is a manufacturing process used in the mass fabrication of plastic parts. It involves an injection of molten plastic material into the mold where it cools and...
Plastic materials are objects artificially made from organic compounds called polymers along with other additive components. They possess excellent formability, making them extremely versatile for many different fabrication and manufacturing processes...
Plastic overmolding has a long and interesting history, dating back to the early 1900s. The first overmolding process was developed by German chemist Leo Baekeland, who invented Bakelite, the first synthetic plastic. Baekeland used a...
A polyurethane bushing is a friction reducing component that is placed between moving and stationary components as a replacement for lubricants. The use of polyurethane for the production of bushings is due to...
Polyurethane molding is the process of fabricating or manufacturing plastic parts by introducing a urethane polymer system into a tool or mold and allowing it to cure. Like any other type of plastic, the excellent processability...
Polyurethane rollers are cylindrical rollers covered by a layer of elastomer material called polyurethane. Depending on the application, the inner roller core is prone to scratches, dents, corrosion, and other types of damage...
Thermoplastic molding is a manufacturing process that works to create fully functional parts by injecting plastic resin into a pre-made mold. Thermoplastic polymers are more widely used than thermosetting...
Urethane casting is the process of injecting polyurethane and additive resins into a soft mold usually made of silicone elastomer. The casting process is similar to injection molding; injection molding differs by using hard, metal molds...
Urethane wheels are wheels made of molded urethane, also known as polyurethane. Urethane is an elastomer that comprises urethane carbamate linkages and is a portmanteau phrase for elastic polymer...