Aqueous Part Washers
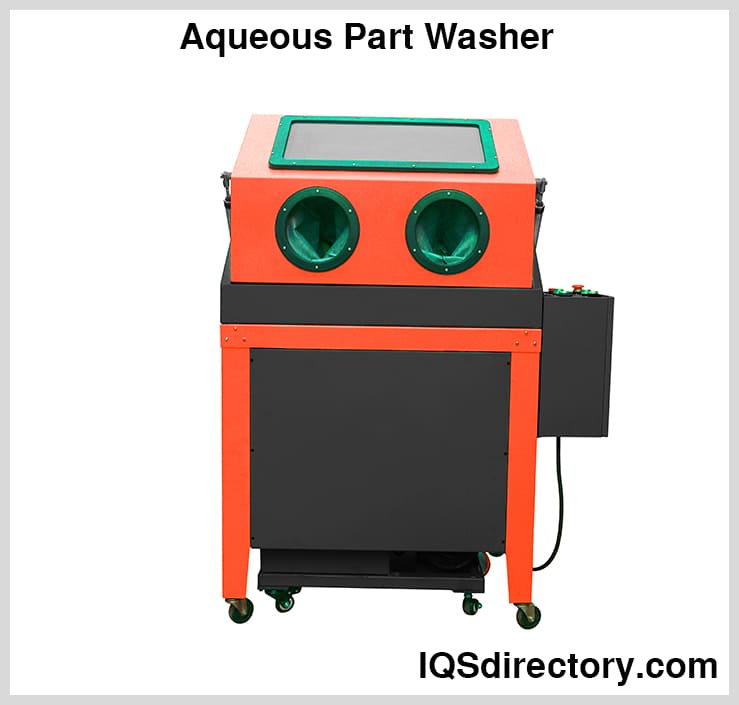
An aqueous part washer is an automated or semi-automated machine manufactured to clean, remove tough grease, and dry large or small parts before distribution or surface treatment. The washing is necessary since...
Please fill out the following form to submit a Request for Quote to any of the following companies listed on
This article takes an in depth look at Tube Fabricating Machinery.
Read further to learn more about topics such as:
Tube fabricating machinery refers to machinery that either bends, cuts, or forms tubes and pipes into various shapes and sizes permanently. These machines work tubes constructed from materials with high ductility and malleability such as stainless steel, aluminum, bronze, brass, and titanium. Most tube forming techniques are metal coldworking processes.
There are several types of machines that transform blank straight tubes into more useful tubes. Each type modifies the geometry of a straight tube differently and typically involves material deformation. There are countless applications of formed tubes; some of them will be discussed in the next chapters.
Tube bending is the process of making an angular bend with the tube by inducing deformation The tube encounters a combination of tensile and compressive forces during this process. The outer side of the bend is stretched and elongated due to tensile forces, while the inner side is thickened due to compressive forces.
There are several notable applications of tube bending. Tube bending is used to fabricate pipe elbows to divert the flowing media in another direction in a piping system. Bent tubes may be an integral part of structural pieces and furniture. They are also seen in air conditioning equipment, musical instruments, and automotive parts.
Tube bending techniques are divided into two categories. In form-bound tube bending, the bend produced on the tube is dependent on the geometry of the tooling. Meanwhile, in freeform tube bending, the tube is formed by moving through dies, and the resulting bend is not affected by its geometry.
The following are the types of tube benders. Tube benders can either be semi-automatic or CNC-controlled.
Rotary draw benders are equipped with a set of interlocking dies for computer numeric control (CNC) tube bending. The tooling protects the tube from collapsing, wrinkling, ovality, and wall thinning during the process. The dies involved in rotary draw bending are the following:
A mandrel bender has the same set-up as the rotary draw bender. This tube bending machinery uses additional tooling called a mandrel. The mandrel is inserted into the tube and offers internal support to prevent wrinkling and collapsing and to reduce ovalization. It helps achieve quality bend for thin-walled tubes, especially if a sharp bend is to be formed.
The types of mandrels are the plug mandrel, formed end plug mandrel, standard mandrel, thin-wall mandrel, and ultra-thin wall mandrel; they are selected according to wall thickness and tightness of the bend radius.
A hairpin bender is a type of rotary draw bender that is used to make a 1800 bend (hairpin bend) from a coiled bundle of copper and aluminum tubes. Multiple coils of tubes are uncoiled in the unwinding system of the hairpin bender and fed to its tracks. Unbent tubes are transported to the bending section through a conveyor belt. Guides are present in the conveying system to align and straighten the tubes before bending. The unbent tubes are then clamped and mandrels are inserted in the tubes once it reaches the bending section. The clamping die at one end, housed in a robotic arm, rotates 1800 from the axis to bend the tube over a bending die. This mechanism creates a hairpin bend. Once the bend has been made, the mandrels are pulled out of the tubes. The bent tubes are finally cut to their desired length and collected.
Hairpin benders are high-speed and highly automated machines that can create multiple hairpin tubes per cycle. Some hairpin benders feature a chip-less cutting mechanism that reduces material scrap.
Return benders work similarly to the hairpin bender. They are used to produce "return bends," a U-tube-shaped fitting that alters the direction of the fluid flow by 1800. The spooled tubes are uncoiled and fed to the multiple tracks of the return bender. As with hairpin benders, bending is limited to 1800, and the tube is internally supported by a mandrel.
Crossover benders have the same operating mechanism present in hairpin benders and return benders. However, they are not limited to producing 1800 bends; they can bend tubes in a wide variety of bend angles by tooling change and set-up. This makes crossover benders more versatile. They are used in manufacturing products such as crossover bends, return bends, elbow bends, and short straight tubes. The following are the equipment used in modifying the dimensions of these products:
Press benders consist of two dies that fix and support the tube during bending and a ram that descends and applies the bending force. The ram acts as the bend die; it possesses the contour of the bend to be made. Press benders are quick in producing symmetrical bends and usually do not require lubrication.
Angle rollers, or roll benders, consist of three rollers arranged like a pyramid. An adjustable working roller is positioned in the middle of the two bottom rollers, and its position determines the bend radius. The working roller rotates in the counter direction of the two bottom rollers. The slow-rotating rollers compress the tube as it passes through them. The process is repeated multiple times until the desired bend is achieved. The tube may be adjusted arbitrarily after each repetition as the bend angle is formed gradually.
Angle rollers are freeform rollers. They produce bends with a large centerline radius. They can also form tubes with different cross-sectional shapes and create spirals from tubes.
Tube spinning is a flow forming process used to elongate tubing and change tubing wall thicknesses. After being mounted and clamped to the mandrel, the tube is drawn over the length of the mandrel by a set of rollers that are spaced equidistant around the tube. The axial flow is in the direction of the movement of the rollers.
Tube spinning is performed externally or internally on the mandrel. With external tube spinning, the tube is stretched over the outer surface of the mandrel while internal tube spinning spins and stretches the tubing inside a hollow mandrel.
Tube spinning is used to fabricate tubes with multiple diameters when the wall thickness is not a concern. It requires intricate tooling design and enhances the mechanical properties of a tube.
Shear spinning places downward force on the tubing while stretching it over the contour of the mandrel. The thickness of the finished tubing is less than that of its original form but has the same diameter. The compressive forces acting on the tubing improves its mechanical properties as its depth increases.
Shear spinning requires a more robust tooling design and precise machine control due to the fact that it affects the dimensional accuracy and surface finish of the tubing. There is an increase of friction on the tubing as well as more wear to the mandrel, which requires the use of coolant due to the heat that is generated.
There are four different deep drawing processes, which are tube sinking, floating mandrel, fixed mandrel, and moving mandrel. The four processes are similar in that the tubing is drawn or pulled through a die. For three of the processes, the mandrel is placed in a different position inside the tubing and has a different shape.
With tube sinking, also known as tube drawing, the tube is pulled through the die with the outer diameter (OD) of the tubing determined by the diameter of the die without any regulation of the inner diameter or tube thickness. The process of tube sinking alters the thickness of the tube walls.
In the floating mandrel deep drawing process, the mandrel is pulled into the die by frictional forces while normal forces try to push it out. The mandrel takes a position where there is a balance between the forces. As the frictional forces change, the mandrel changes its position, which results in changes in the tube thickness.
With fixed mandrel deep drawing, the mandrel is pulled into the die with the tubing, a process that is used to change the thickness of tubing. On the entry side, the area of the cross section of the tubing increases and its speed decreases. The mandrel moves at the same speed as the tubing at the exit side while the deformation zone of the mandrel moves faster than the tubing. Frictional forces pull the tubing into the die.
The mandrel for moving mandrel deep drawing is a cylinder that is pulled with the tubing through the die. It is another process used to reduce the thickness of tubing. The area cross section of the tubing increases at the entry, which reduces its speed. The mandrel moves at the same speed as the tubing at the exit side with the mandrel deformation zone moving faster than the tubing.
The process of pilgering is used to reduce the diameter and wall thicknesses of tubing and is capable of achieving cross sectional reductions of more than 90% in a single cycle. Pilgering involves the use of a pair of ring dies and a mandrel. The mandrel is placed inside the tubing in a fixed position similar to tube drawing with a moving mandrel.
In the rolling section of pilgering, the mandrel is tapered. The pair of dies have matching grooves around their circumferences. The pilgering machine moves the tubing forward and backward such that the dies can reduce its OD. The grooves in the dies decrease along their circumference such that they take a semi-circular shape. During the process, the dies disengage at the center position, at which time, the tube advances and rotates. The disengaging and turning ensures consistent wall thicknesses.
The purpose of autofrettage is to use pressure to improve the durability of tubing and increase its resistance to stress corrosion cracking. Intense pressure is applied to the tubing to expand its bore and stretch its inner layers beyond their elastic limits such that the tubing will not be able to return to its normal shape.
The outer layers of the tubing in autofrettage processing are not stretched beyond their elastic limit because the stress distribution is not uniform. Since the external layers are not stretched, they tend to return to their original shape but are prevented from doing so because of the stretched inner layers.
During the autofrettage process, the inner layers are subjected to a low temperature heat treatment that causes further expansion beyond the elastic limits.
Tube end formers, or end formers, are machines used in shaping the tube typically on or near its end. End formers create an installation port on the tube for other media (e.g., hoses, blocks, or another tube). Formed ends enable tubes to fit with other mechanical parts. For fluid conveying applications, it ensures that no fluid will leak from the connection. It also changes the fluid velocity by increasing or decreasing the flow area.
The axis of the tube is not diverted after the process. End formers can perform a variety of changes in the geometry of the tube end:
Reduction and expansion refer to the increase or decrease of the tube end‘s cross-sectional area respectively.
Beading is the process of creating protruded "beads" near the tube end. Beads serve many purposes. They act as a mechanical stopper when the tube is fitted with other parts and increase the effectiveness of seals. They enable the connection of a tube to a hose and strengthen its end. They also dampen vibration in solid lines.
Flaring is the process of forming joints on two tubes, so they produce a leak-proof seal when fitted to each other. Double-lap flared tubes have thicker material on their inner diameter; this offers additional strength and fatigue resistance and reduced variation in the flow area. Special types of flared joints include Marmon bead flares and spherical ball flares.
Flanging refers to the flattening of the material at the end of the tube to form a flange that is seamlessly connected to the tube.
The types of end forming machinery are ram formers, segmented end forming machines, and rotary forming machines:
Ram end formers work the tube end by applying an axial force to induce material deformation. These machines consist of vise jaws and a ram nose. A pair of vise jaws clamp and support the tube while forming one of its ends. The ram nose, which contains the final shape of the tube end, is situated next to the unsupported tube end. The ram nose strikes the unsupported end of the workpiece to induce deformation. The process is repeated for several strokes using different ram noses; the final shape is gradually achieved after each stroke. Due to heat and friction generated with each stroke, lubrication and coolant are usually applied.
Ram end formers can form a tube end in a variety of shapes; they can be symmetrical or asymmetrical, depending on the geometry of the tooling. These machines are preferred when there is a large amount of expansion or reduction to be induced.
In a beading operation, the tube is placed in a clamp that has a gap between the clamp halves. The clamp halves have a space for the formation of the tube bead. The tube bead is formed as the clamp halves push each side of the tube against each other in the axial direction. Beading performed in a ram former is called compression beading.
Segmented end formers work through the application of radial force to the circumference of the tube to induce material deformation. These machines have a circular die divided into segments that apply radial force. Unlike ram forming, segmented end forming rarely requires a clamping mechanism.
A compressive radial force from the outside of the tube is applied to squeeze the tube and decrease its cross-sectional area. During expansion, on the other hand, a tensile radial force from the inside of the tube is applied to stretch the tube and augment its cross-sectional area. The application of radial force is repeated for a specific number of strokes; the segments slightly rotate to induce uniform deformation in the workpiece.
The common types of tooling in segmented end formers are C tooling and inside/outside (I/O) tooling. C tooling is capable of either expansion or reduction operation. The I/O tooling is more flexible; I/O tooling has two concentric circular segmented dies wherein the tube is fed between the inner and outer die; this enables it to perform both functions.
Rotary end formers have a rotary head that expands or reduces the tube‘s cross-sectional area by applying tensile or compressive radial force respectively. The rotary head has three to four cylinders that traverse through the tube, either on the inside or outside, axially while applying radial force. Rotary end formers can create flaring ranging from 200-900.
Tube hydroforming and tube swaging machines modify the cross-section of the tube at any point on the tube.
Tube hydroforming is the process of expanding metal tubes into the inner walls of a mold with a highly pressurized fluid to change their cross-sectional shape. This tube forming technique is a versatile method that accommodates tubes and hollow sections of all shapes. Tube hydroforming machines can transform stock tubes into complex and irregularly shaped sections.
To begin the tube hydroforming process, the stock tube is placed between the mold halves of the hydroforming machine, which will be closed afterward by a sufficient clamping force. The length of the stock tube must be slightly greater than the length of the cavity. Sealing rods equipped with an internal press are inserted on both ends of the tube. The rods will then fill the tube with water. The press, powered by thrust actuators, compresses the fluid inside the tube; the elevated internal pressure will cause the metal tube to expand into the cavities of the mold. Finally, the hydroformed tube is ejected from the mold.
Hydroformed tubes have high stiffness and seamless connections; this increases their strength. The cost-effectiveness of the tube hydroforming process is greater when used to form large tubes.
Tube swaging is a tube forming process that aims to reduce and form the cross-section of a tube. It can also change the cross-sectional shape of the tube. Tube swaging is essentially a forging process. The tube is forced through and compressed by a confining die to the desired shape. The types of tube swagers are the following:
In rotary swagers, a motorized spindle with a set of reciprocating dies is housed inside a cage containing a set of pressure rollers that surround the spindle. As the spindle rotates, the dies are pushed against the pressure rollers by centrifugal force. The dies are then pushed inward; this closes the die. The alternating open and closed position of the dies compresses the tube into the desired shape as it passes through the cavity of the rotating dies. A mandrel can be inserted to support and assist in shaping the tube.
A rotary swager can be a two-die or a four-die swager. Two-die swagers are used for smaller parts and provide a better surface finish. Four-die swagers, on the other hand, are used if there are large initial reductions to be made in larger parts.
Long die swagers are a type of rotary swager; they are used to produce long, shallow tapers.
In stationary spindle swagers, the dies have a similar reciprocating action to rotary swagers. However, the spindle and the forming dies are stationary. The head rotates and drives the pressure rollers. Since the forming dies are fixed, stationary spindle swagers can transform a tube‘s cross-section into a different or asymmetrical shape.
In die-closing swagers, a certain length of the tube to be swaged is inserted through a set of closed reciprocating dies before the swager starts rotating. The wedges then advance and compress the die. A radial compressive force is applied every time the die strikes the tube for a fixed amount of time. Once the swaging is finished, the dies retract and the swaged part is finally removed.
Tube cutting machinery is a category of tube forming machines that either reduce or divide the length of the tube or remove some of the tubing material by cutting. Tube cutting is usually an intermediate step for other fabrication processes.
Some tube cutting machinery is listed below:
Tube threading is the process of creating helical ribs on the end of a tube or pipe for assembly with other tubes or parts with threaded ends. It does not affect the tube‘s cross-section and axis; it is not an end forming process.
The tube stock is inserted and clamped by the jaws present on the center of the tube threader‘s wheel. The jaws are locked to prevent the tube from slipping. Before threading, burrs on the tube end are removed; this stage of tube threading is called reaming. Reaming is performed by a separate deburring machine in case the tube threader is not equipped with a reaming tool.
To create the thread, the material is cut away from the tube end through a stationary universal die head that contains a set of sharp teeth. The universal die head is adjusted according to the outer diameter of the tube. Once set-up is completed, the wheel rotates the tube and the universal die head is placed on the tube end. Cutting starts as soon as the sharp teeth are engaged on the tube. Liquid coolant is poured on the cutting area and the chips generated from cutting are collected on the bed of the tube threader.
Tube and pipe notchers are used to reshape the ends by removing a portion of the tubing material to enable mounting on other tubes and mechanical parts. Notched tube ends are welded to create joints used in structural applications. Side notched pipes enable fabrication of tee fittings used in fluid flow branching.
There are many types of tube and pipe notchers; some of them are end mill notchers, punch-type notchers, and plasma notchers. End mill notchers strip material from the tube by engaging a sharp rotating mill perpendicularly placed at its end. Punch-type notchers apply a shear force to cut the tube end using a punch. Lastly, plasma notchers use a jet of ionized gas to melt and cut the tube end. Plasma notchers are more practical than the latter tube notchers in cutting large sections.
Tube slotters are used to remove a portion of tubing material to create slots. Slots may be created by a press; a punch strokes the tube and applies shear force on the tube to cut the material. Mandrels are used to support the tube internally during cutting. Slots may also be created by machining or laser cutting.
Tube deburring removes the excess metal found on the tube end. It also polishes the tube end to achieve a smooth finish and improves the aesthetic quality of the tube.
In a brush deburring machine, the tube end is sanded by a brush with rough and abrasive bristles made from thin metal wires. The brush is attached to a rotating element (e.g., rotating disc or cylinder) which scrapes off the unwanted material on the tube end. The tube remains fixed during the process.
Tube cutting is the process of cutting the tube into its desired length. There are various types of tube cutting machines:
A cold saw machine utilizes a circular toothed blade to cut the tube at a specific length. The blade can be a solid high-speed steel (HSS) or a tungsten carbide-tipped (TCT) blade. It is powered by an electric motor in order for it to rotate. A coolant is sprayed on the cutting section of the tube. Cold saw machines generate minimal friction and heat during cutting; hence, they have longer blade life.
In band saw machines, the toothed blade is made from a band of thin, sharp metal. The blade rotates around two wheels and is continuously cycled in one direction. The arrangement of the wheels determines the orientation of the cutting plane, which can be horizontal or vertical. The tube is placed on the bed of the band saw machine and is fed towards the blade.
Band saw machines are ideal for large volume production. They can cut tubes with different cross-sections. However, they are not suitable for thin-wall tubes.
Supported shear cutting machines use a set of internal punches and external dies. The stationary and movable punches are inserted into the tube. The punches support the tube internally during cutting. The tube is then clamped into the external dies, which are composed of stationary and movable dies. The movable punch and die move to apply shear force and cut on the portion between the stationary and movable punches and dies.
Dual blade shear cutting machines are used to cut carbon steel and alloy steel tubes and eliminate the dimple produced by a single blade cutting machine. In these machines, a horizontal blade produces an initial scarfing cut on the side of the tube then the vertical blade continues the cut from the formed notch. The tube is clamped tightly by a set of tooling during the process.
In rotary cutting machines, the tube rests on two backup rollers, and the rotating blade is fed from the top and descends to cut the tube.
In lathe cutting machines, the tube is fed through a chuck-type clamping mechanism. This mechanism rotates the tube and feeds it to the cutting tools. Another set-up features a stationary tube with the rotating cutting tools surrounding and cutting the tube.
Laser cutting machines use high-energy solid-state or CO2 lasers to melt the tubing material. This cuts the tube into the desired length quickly.
An aqueous part washer is an automated or semi-automated machine manufactured to clean, remove tough grease, and dry large or small parts before distribution or surface treatment. The washing is necessary since...
Automated parts washers are mechanical devices designed to efficiently remove grit, oil, grime, dirt, paint and other contaminating substances from parts with minimum manual supervision. These substances are removed...
Tube bending is one of the fabrication methods used to form tubes permanently by bending them. In many circumstances, bent tubes are more useful than in their straight form. Bent tubes are an integral part of many instruments, such as...
Deburring is a secondary operation of a machining process that enhances the final quality of the product by removing raised edges and unwanted pieces of material, known as burrs, left by the initial...
Finishing machines are machines used for metal finishing, which is the last stage of the metal fabrication process; the stage encompasses the use of machines in finishing the metal surface...
A parts cleaner is a cleaning device that uses various types of solvents, cleaning agents, and processes to remove grease, grime, and contaminating materials from manufactured parts prior to shipment or movement for further processing...
A parts washer is a mechanical device designed to remove grit, grime, oil, miscellaneous debris, dirt, paint, and other contaminating substances from parts in preparation for their use in assembly operations, packaging, or coating...
A tumbling machine is a durable deburring and metal-polishing machine designed for finishing large parts or batches of smaller parts. A tumbling machine is also known as a barreling machine or a mass-finishing...
Vibratory tumbler is the equipment used in a vibratory finishing process, one of the most common methods in mass finishing. But how does a vibratory tumbler work...
A wastewater evaporator is a method of removing water from water-based waste by converting the water in the waste to a vapor and leaving contaminants. The function of a wastewater evaporator is to reduce the volume of waste materials...
Parts washers are designed for cleaning, degreasing of equipment, and drying of mass quantities of small or large parts in preparation for surface treatment, assembly, inspection, or shipment...