Aqueous Part Washers
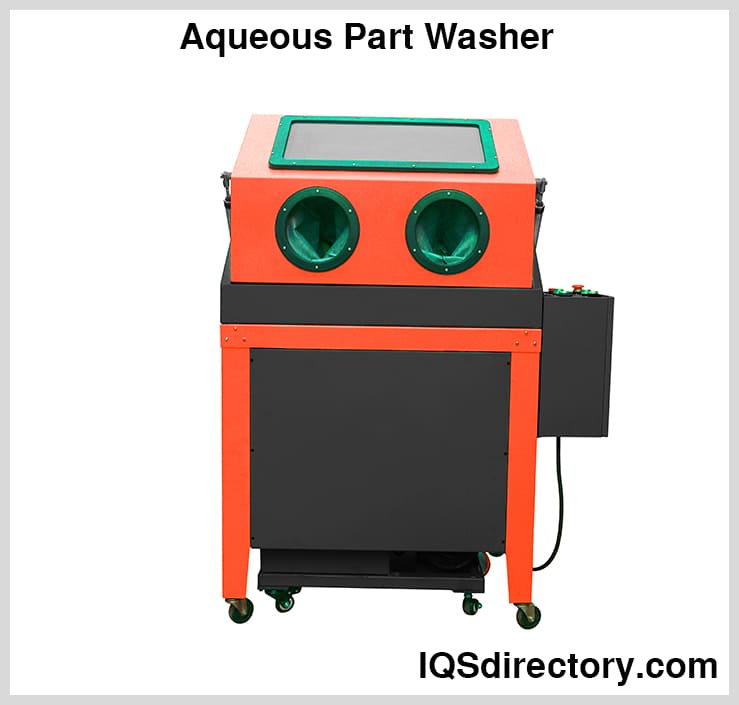
An aqueous part washer is an automated or semi-automated machine manufactured to clean, remove tough grease, and dry large or small parts before distribution or surface treatment. The washing is necessary since...
Please fill out the following form to submit a Request for Quote to any of the following companies listed on
This is the most complete informational guide to parts washers on the internet.
You will learn:
A parts washer is a mechanical device designed to remove grit, grime, oil, miscellaneous debris, dirt, paint, and other contaminating substances from parts in preparation for their use in assembly operations, packaging, or coating. The basic function of a parts washer is to clean and prepare parts. The types of parts washers vary depending on their industrial use and include high pressure washers, washer cabinets, rotary basket washers, deburring, and several other varieties.
Newly produced parts, that have been machined, forged, or fabricated, are coated in oil, chemicals, have burrs, abrasive dust, debris, paint, and various forms of residue left over from the manufacturing process. Before they can move on to the next operation, they need to have a surface cleaning and decontamination, which is the purpose of a parts washer.
In the design of a parts washer, the first consideration is the size, shape, and configuration of the parts to be cleaned. Added to these basic concerns are special aspects in a parts design, which include weight, surface area, angles, closed sections, and blind holes. For efficient and complete cleaning of parts, all of these factors have to be considered during the purchasing process.
There are many options that manufacturers consider when developing parts washers. They include CNC programming, back or front loading, baskets, trays, or rack systems, a rotary table, and conveyor belts. Most parts washers are aqueous with a water solvent or cleaner, which is used to boil, blast, or soak dirty parts. In most cases, producers design parts washer to meet the needs of the customer since every customer has unique part designs and requirements.
The basic components of a parts washer are a water heater, filtration system, pump or pumps, scrubbers, brushes or power nozzle, and a cabinet or enclosure.
The purpose of the heating unit, which can be gas, electric, or steam, is to quickly raise the temperature of the cleaning solution to save time in the cleaning process. When solvents, detergents, and chemicals are used in the washing process, the heating unit speeds up the chemical reaction.
When a parts washer is activated, the cleaning solution or water flows from the cleaning tank to the storage tank. As it passes from the cleaning tank back to the storage tank, it passes through two filters. The first filter is a large grid that catches large particles. The second filter is finer and designed to catch smaller particles that were not caught by the larger filter.
Parts washer pumps are designed to operate submerged in solvents, water, and detergents. The purpose of the pump is to pump cleaning solutions to the cleaning tank. They are made to work continuously and pass water from the storage tank to the cleaning tank.They operate at 185° F and move 115 gallons per minute (GPM) at a psi of 65. GPM and PSI are critical for the pump. When those factors are low, the parts washer may not completely remove the cleaning solution.
The scrubber on a parts washer can be a sprayer or a set of brushes. The pump circulates the cleaning solution from the storage tank to the scrubber, which cleans the parts. In the heated parts washer below the spray nozzle can be seen in the back and on the side of the cabinet.
The size and capabilities of parts washer cabinets are wide and varied. Parts washing involves high pressure application of a cleaning solution, which can take place in a cabinet or on a conveyor belt. Water pressure for cleaning parts has to have enough force to remove contaminants. The cabinet has to be designed to be able to withstand that force but not be harmed by constant exposure to water or solvents. The cabinet below is a spray wash cabinet from BendPak.
One of the concerns for the cleaner storage tank is the water level. If the level of the water gets too low, the heater can be damaged by being exposed. An automatic low water shutoff valve automatically turns the parts washer off and will prevent the parts washer from restarting until the storage tank is at the appropriate level.
The purpose of a parts washer is to help maintain parts in excellent condition for other processing. Though there are a variety of parts cleaning systems, the majority of systems divide into two types – aqueous or water cleaners and solvent cleaners.
Aqueous cleaners have the cleaning power of solvents using cleaning solutions that are biodegradable and water based.
Solvent cleaners dissolve dirt using a chemical process and include mineral spirits, petroleum naphtha, benzene, trichloroethane, and xylenes.
A further division of parts washers is manual, semi-automated, or fully automated.
Sink on a drum is the most common and basic of the types of parts washers and is designed for washing individual or a few parts. It consists of a drum with a sink mounted on it that has a solvent or water supply line. Sink a drum models come with a pump and brushes.
Immersion parts washers use a system of agitation or oscillation to clean parts in a bath of a cleaning solvent. Once the parts are coated with the solvent, a vibrating action creates turbulence in the solution to clean parts.
An important part of parts washers is the sprayers. Keeping them clean is an essential for parts washer maintenance.
Cabinet parts washers use a high pressure, heated, aqueous spray in a cabinet to clean any size parts, which includes heavy oversized ones. Parts are loaded through a door at the front of the cabinet into a basket. The parts are rotated in the cabinet and subjected to high powered spray that contains water, cleaning chemicals, or detergent.
The multi-purpose spray cabinet parts washer offers an efficient and convenient method for washing low volume loads of a variety of parts.
Conveyor parts washing systems have an enclosed automated transport system that moves baskets or fixtures of parts through each phase of the cleaning process. The designs of conveying systems differ depending on the functions of each stage of cleaning. In an immersion conveyor system, baskets or fixtures of parts are sent to the washing station, rinsed, and put through a series of drying cycles.
The process of a conveyor parts washer has many features that streamline parts washing. Incorporated in the process are stages, which is similar to robotic fed parts washers. Certain conveyor washers have variable speed stainless steel belts, filtration units, moisture blow off, heaters, and exhaust ducts. These systems provide continuous in line flow with heated wash zones, rinse zones, and air dry finishing zones that differ depending on part parameters.
The idea behind conveyorized continuous flow systems is throughput continuous flow of parts with minimal handling. The differentiation between the systems is dependent on whether the system has a fixed or variable speed and the products that can be processed. The main benefit of continuous in line parts washing is their efficiency and speed of processing.
Rotary drum parts washers are used for high volume cleaning of small parts. As with a conveyor parts washer, cleaning, rinsing, and drying happen automatically and a high pressure sprayer is used for the cleaning process. Added to the high pressure spray is immersion agitation to reach inside tubes and hollows.
In the manufacturing of parts, most of the burrs are removed in the finishing process. Though finishing is efficient, very small burrs remain attached to the part, which have to be removed. Thermal deburring uses a flammable gas, usually methane or hydrogen, to clean the final small burrs. Parts are placed in a chamber that fills with gas, where the gas is pressurized. Once the appropriate temperature and pressure is reached, the gas is ignited for a few milliseconds at a temperature that removes burrs but does not damage the part.
Complex parts can have contaminants and oxidation that cannot be cleaned by normal high pressure sprays or immersion. Ultrasonic systems use ultrasound at single or multiple frequencies, of 20 to 400 kHz, and a cleaning solution. The cleaning process uses cavitation bubbles produced by high frequency sound to agitate the cleaning liquid and heat. The force of the agitation goes deep into the holes, cracks, and crevices of the part to remove contaminants. Ultrasonic parts washers can be bench top or high volume large capacity.
Green parts washers, also known as biomatic parts washers, are an environmentally and eco friendly method for parts cleaning. Parts are placed in a heated washer that contains a pH neutral solution with a microbe colony. The microorganisms break down the grime on parts and transform the hydrocarbons into carbon dioxide and water.
The removal of the contaminants is helped by aeration and filtration, where the aeration system adds oxygen to increase microbe activity and the filtration system cleans the solution. The cleaning solution, from the biometric process, seldom needs to be replaced saving on the cost of the system.
Tunnel parts washers are designed for linear parts washing. Parts are placed on a conveying system that takes them through treatment phases. They are designed according to parts dimensions and shapes, hourly productivity, and washing process type, which are degreasing, phosphating, rinsing, rust prevention, drying, or cooling.
The carousel parts washer has a similar design as the conveyor models and is designed for high volume operations. The convenience of a carousel design is its smaller footprint and ability to interface with automated load and unload operations. Parts are loaded and unloaded at the same location, which allows for single operator control.
Depending on the types of solvents used in the parts washing application, certain types of parts washers may need to be classified as explosion proof. For a machine to be classified as explosion proof by the National Fire Protection Agency (NFPA), it must be able to withstand an explosion from vapors or gases and prevent igniting the surrounding atmosphere.
Acid parts washers are made with special components using materials that are specifically designed to withstand the harmful effects of caustic substances. The unique design of acid parts washers allows them to withstand the cleaning of harsh corrosive materials, acids, and alkali materials.
As with any form of industrial equipment, maintenance is key to its longevity, which includes regular cleaning. In many cases, this is difficult because of the solid construction of a parts washer. A design from Alliance Manufacturing, for top load parts washers, is a removal canopy that allows access to the interior of the parts washer without the need for disassembly. The lightweight removal fiberglass canopy can be easily lifted providing full access to the workings of the parts washer.
Vibratory parts washers are a form of immersion parts washer. Parts are placed in large batches in the cleaning container with a solution. At the bottom of the container is a motor that creates the vibrations that agitates and cleans the parts. The constant motion of the vibrations scrubs them and removes any surface residue or particulate material. Vibratory parts cleaners can be automated for flow through operation, have continuous operation, or do basic batch operation.
Robot fed parts washers incorporate multiple washing functions into one machine, which makes them capable of prewashing, high pressure washing, and drying with deburring. The high pressure nozzles deep clean cross, tap, and bore holes as well as tapers and cavities. Robot fed cleaners have stages where parts are moved robotically between chambers. Other forms of robotic parts cleaners include pick and place with grippers for part movement.
Parts washers are a significant necessary investment that has to be maintained and require a regular maintenance cycle. Heavily used parts washers may require being checked weekly to ensure proper performance and operation. Listed below are a few steps to be taken when examining the condition of a parts washer.
The first step in proper maintenance is to become familiar with its working components. Advanced knowledge will assist in determining possible problem areas and ones that need close examination. Tanks, heaters, pumps, nozzles, filters, and turntables can malfunction or not perform up to specifications.
The filter is a critical part of the parts washer unit and needs to be checked for buildup that can clog it. A normal practice is to change the filter monthly or more frequently depending on the parts washer‘s use. To help in extending the life of the filtration system, stored parts may need to be pre-cleaned before being placed in the washer.
In spray types of parts washers, spraying is the simplest and least expensive method for parts cleaning. Spray patterns should be checked to ensure complete coverage and to be sure there is sufficient water pressure.
The pump supplies the pressure for the system and needs to be checked for proper alignment and any need for adjustments. Checking the pump‘s bearings, depending on their location, needs to be added to the regular maintenance cycle. Part of this process includes checking that the bearings are properly lubricated.
Certain cabinet parts washers have a turntable to rotate parts for a full cleaning. The table is turned by a set of gears. It is important to ensure that the turntable is performing properly, and its bearings are checked for lubrication. The gears should be aligned to avoid slippage. Turntable weight capacity should be carefully monitored regarding the load the turntable can bear. The more parts that are washed at one time reduces cleaning but the pump needs to have a high gallons per minute capacity to be able to sufficiently cover all surfaces.
The turntable method of parts washing can also include indexing where parts are washed one at a time. For indexing, parts can be loaded robotically or by hand on to the rotating fixture that indexes in a timed cycle from three seconds or longer. Parts are indexed into high pressure spray zones to remove chips and oils.
Having the parts washer properly leveled is critical to its performance. Parts washer leveling is a normal part of the installation process. Though it is unlikely, it may be prudent to check the positioning of the parts washer if it is determined there is a malfunction. For small, portable parts washers, making sure the device is level when positioned is essential and a normal part of manufacturer‘s instructions.
All parts washers have waste accumulated during the cleaning process. Proper disposal of the waste is essential. Waste should not be disposed of in onsite septic tanks since it will contaminate the system. In some cases, the amount of waste may be controlled by evaporation from the system. Certain municipalities permit waste to be dumped into the sewer system. To ensure that it is acceptable, local regulatory agencies should be checked for guidance.
When preparing parts for cleaning, it is important to not overfill or pack the cleaning basket, which can lead to unsatisfactory cleaning and the need to repeat the operation. The determination of whether parts are sufficiently clean includes visual inspection, particle count, and other testing methods.
Parts with burrs, cleaned by a solvent or aqueous method, can cause difficulties in the cleaning process. Thermal deburring is the best method to ensure proper removal of burrs.
The parts cleaning solvent or cleaner should match the parts to be cleaned. Parts can be covered in oil based coolants from the machining process, which will require a solvent and process designed to remove the contaminant, such as hydrocarbon cleaning. Parts from grinding or lapping can be cleaned using the aqueous process. A wise choice of cleaner and cleaning process can make the process of parts washing more efficient and less time consuming.
When the cleaning solution is saturated with grime, dirt, and other contaminants, it cannot be filtered or cleaned since the amount of grease and oil in the solution is greater than the grease to be cleaned. A skimmer or sludge scraper can reduce the problem but will not completely remove the need to clean out the parts washer tank.
A main component of a parts washer is the type of chemical or detergent that is used to do the cleaning. Which one is used depends on the parts to be cleaned and the method since chemicals and detergents for immersion cleaners are different from ones for ultrasonic and spray parts washers.
Parts cleaning involves the use of parts cleaning detergents and solvents many of which are hazardous, dangerous, and toxic. A necessary part of parts washer management is monitoring the workplace environment such that there is sufficient control of these toxic materials to prevent injury and illness.
Washing parts is a complex process that uses specially designed materials that can remove the grease, grime, oil, chemicals, and soil from high volume parts production. With the rise in environmental concerns, manufacturers are using biodegradable ingredients, as seen in the image of the detergent below from TEMCO.
Oil eater detergents are an effective method for cleaning industrial parts and acts as a degreaser that does not contain acid.
Water based detergents are pH neutral, nontoxic, non irritating, and nonflammable high quality parts cleaners and can be used with a bioremediating system.
Detergents are for aqueous parts washers and are designed to be used in jet sprayers and power washers. To be the most effective, detergent solvents have a defoamer that floats on top of the washing solution surface to prevent foaming.
There are several different types of cleaning solutions designed to be used with ultrasonic parts cleaners. The different types include acidic solutions, alkaline solutions, high caustic solutions, deionized water, enzymatic solution, neutral solution, and mildly alkaline solutions.
Ultrasonic cleaning solutions are demulsifying or emulsifying. Demulsifying is used to remove oily contaminants but has to be drained from the tank after cleaning. Emulsifying solutions suspend contaminants in the tank. If it is used over several cleaning cycles, the contaminants may cling to parts when they are removed.
Strong aggressive chemicals are necessary to ensure proper cleaning and exceptional performance of a parts washer. Regardless of the methods used to wash parts, powerful cleaning agents are a necessity and include chemicals such as Trichloroethylene, Butyl Cellosolve, Bacteria, Sodium Hydroxide, Toluene, Benzene, and Acetone to name a few.
Trichloroethylene: Trichloroethylene is a colorless chemical commonly used in cleaners and solvents.
Butyl Cellosolve: Butyl Cellosolve is found in a wide range of cleaners from ones used for industrial cleaning to household cleaners.
Bacteria: Bacteria and enzymes are found in parts washers to provide a natural method for removing soil and stains by a process known as bioremediation.
Sodium Hydroxide: Sodium hydroxide is a caustic cleaning agent that can dissolve grease, oils, fats, and protein deposits.
Toluene: Toluene is half as strong as acetone and butanone and is the primary ingredient in paint thinner. It dissolves adhesives, rubber, and sealants.
Benzene: Benzene is a widely used chemical in manufacturing processes that has to be handled carefully due to its deleterious effects.
Acetone: Acetone has several uses as a cleaner as well as a method to treat metals before they are painted.
The above list are a few of the many chemicals used to treat and clean parts. Each of them has to be handled with great care due to their toxicity. The cleaning of parts requires the use of powerful cleaning agents that can do serious harm to workers and other materials. It is essential that they be stored and managed properly.
There are a wide variety of methods used to determine the cleanliness of parts. The types of test for cleanliness range from wiping the part with a cloth to applying different chemicals and seeing their reaction. The level of cleanliness tends to be subjective since there aren’t written standards. The list of tests below are a few of the cleanliness tests commonly used.
The cotton swab test is very simple and consists of wiping the surface of a part with a white glove or cotton swab. The glove or swab is examined for residuals or contaminants. It is a visual inspection method for determining if a part passes or fails.
The dyne test is a quick method for measuring surface wetness or tension. It is one of the easiest methods for deciding how much contamination there is on the surface of a part. A pen, marker, or ink is used to mark a flat portion of a part. A part fails the test if ink beads up on its surface.
The gravimetric test measures the size of particulate matter on a part. It can be set to measure different levels of microns (μm) from 2 μm up to several microns depending on the level of concern. A part is washed with a solvent before cleaning to establish how dirty it is. A chemical, such as acetone, cleans the part to ensure that all particulate matter is removed. After a part is washed, the cleaning solution is run through a filtering system that separates non-soluble contaminants from the solvent used to wash the part. The contaminants are examined to determine the amount, weight, size, and type.
The FTIR testing method is used for testing organic cleanliness of parts before and after they are cleaned. A part is rinsed in a solvent onto a test surface and then scanned. The FTIR scans the IR infrared spectrum absorption rate of a substrate.
The TOC test looks for total, organic, and inorganic carbon content of dissolved carbon dioxide and carbonic acid salts. The test can be done before and after cleaning to determine part cleanliness efficiency and after cleaning to measure possible alkaline content.
Water break free test is a gross test for part cleanliness for oil and hydrophobic films. It is used on freshly cleaned stainless steel, titanium, steel, aluminum, brass, and other metals. The test consists of immersing a part in a clean water rinse at an angle to look for shedding of water. Droplets that form and do not sheet indicate the presence of oils or residues.
The conductivity rinse test is completed before, during, and after rinsing. The change in the rinse water conductivity will indicate the effectiveness of the rinsing process.
The ROSE test is used to detect the presence of bulk ionics. The process of parts cleaning involves the use of solvent solutions designed to draw ions on the substrate of a part into the solvent solution. The resistivity analyzes before and after cleaning to determine ionic contamination in units per square inch.
The Ion Chromatography Test is similar to the ROSE test and uses thermal extraction to extract ionics into a solution, which is tested using an ion chromatograph. The collected data indicates the ionic species and their level. In addition, the conductivity of the extracted solution is measured.
An essential and necessary aspect of parts cleaning is precision cleaning that removes contaminants, meets cleanliness parameters, and adheres to industry standards. Though the term clean may seem to be a simple idea, in actuality, every industry has a different interpretation and sets of parameters, requirements, and levels of cleanliness. Additionally, aside from the general industry standards, each company has their cleanliness goals that must be met before a part is approved for use or shipment.
Unlike placing dishes in a dishwasher, parts washer manufacturers produce equipment capable of cleaning parts to the micron (µ) or micrometer level, which are minute units that cannot be measured in inches or millimeters. This type of precision is necessary due to the nature and use of the parts being cleaned. Individual parts washers clean to different micron measurement levels with some capable cleaning down 2 µ while others only need to clean to 50 µ.
Precise, accurate, and precision cleaning keeps parts functioning correctly and prevents damage to equipment and components during the use of a part.
In the modern era, precision cleaning has become a necessity since it increases the usability, safety, and usage life of a component or part. The many manufacturing processes that are used to produce modern equipment add a wide range of contaminants and unnecessary materials to a part that need to be removed. This is achieved through the use of multiple precision cleaning methods to ensure adherence to cleaning requirements.
The two main types of contaminants are solid and residual. Solid contaminants are fibers, particles, chips, fragments, and other small pieces of material that attach to the surface of a part. Residues are substances such as oil or grease that remain on the surface after manufacturing.
The key to ensuring the cleanliness of parts is proper inspection after a part has been cleaned. Included in the process is the use of various testing methods that can highlight any substances or materials that have not been sufficiently removed.
An aqueous part washer is an automated or semi-automated machine manufactured to clean, remove tough grease, and dry large or small parts before distribution or surface treatment. The washing is necessary since...
Automated parts washers are mechanical devices designed to efficiently remove grit, oil, grime, dirt, paint and other contaminating substances from parts with minimum manual supervision. These substances are removed...
A parts cleaner is a cleaning device that uses various types of solvents, cleaning agents, and processes to remove grease, grime, and contaminating materials from manufactured parts prior to shipment or movement for further processing...
A wastewater evaporator is a method of removing water from water-based waste by converting the water in the waste to a vapor and leaving contaminants. The function of a wastewater evaporator is to reduce the volume of waste materials...
Parts washers are designed for cleaning, degreasing of equipment, and drying of mass quantities of small or large parts in preparation for surface treatment, assembly, inspection, or shipment...
Industries worldwide utilize abrasive blasting for various purposes, including cleaning rust and oil, removing surface coatings like paint and pollutants, preparing surfaces for paint and coatings, reinforcing metal surfaces and...
Deburring is a secondary operation of a machining process that enhances the final quality of the product by removing raised edges and unwanted pieces of material, known as burrs, left by the initial...
Finishing machines are machines used for metal finishing, which is the last stage of the metal fabrication process; the stage encompasses the use of machines in finishing the metal surface...
Sandblast cabinets include systems or machinery and components for projecting blast media against a part‘s surface to abrade, clean, or modify the surface. Sand, abrasive, metal shot, and other blast media are driven or propelled using pressurized water, compressed air, or a blast wheel...
Sandblasting equipment includes systems or machinery, and components for projecting blast media against a part‘s surface to abrade, clean, or modify the surface. Sand, abrasive, metal shot, and other blast media are driven or propelled using pressurized water, compressed air, or a blast wheel...
Shot peening equipment includes systems or machinery and components for projecting shot peening media against a part‘s surface to modify the surface or surface engineer the part...
A tumbling machine is a durable deburring and metal-polishing machine designed for finishing large parts or batches of smaller parts. A tumbling machine is also known as a barreling machine or a mass-finishing...
An ultrasonic cleaner is a type of sonic cleaner or sonic cleaning machine that uses cavitation to remove unwanted material. The cleaning effect is created by the compression and refraction of a cleaning medium. Miniscule vibrations propagate throughout the...
Ultrasonic cleaning is a type of cleaning process which uses cavitation induced by alternating compression and rarefaction cycles at ultrasonic frequencies. Ultrasonic frequencies are sound waves vibrating at 20 kHz or higher...
Vibratory tumbler is the equipment used in a vibratory finishing process, one of the most common methods in mass finishing. But how does a vibratory tumbler work...