Aqueous Part Washers
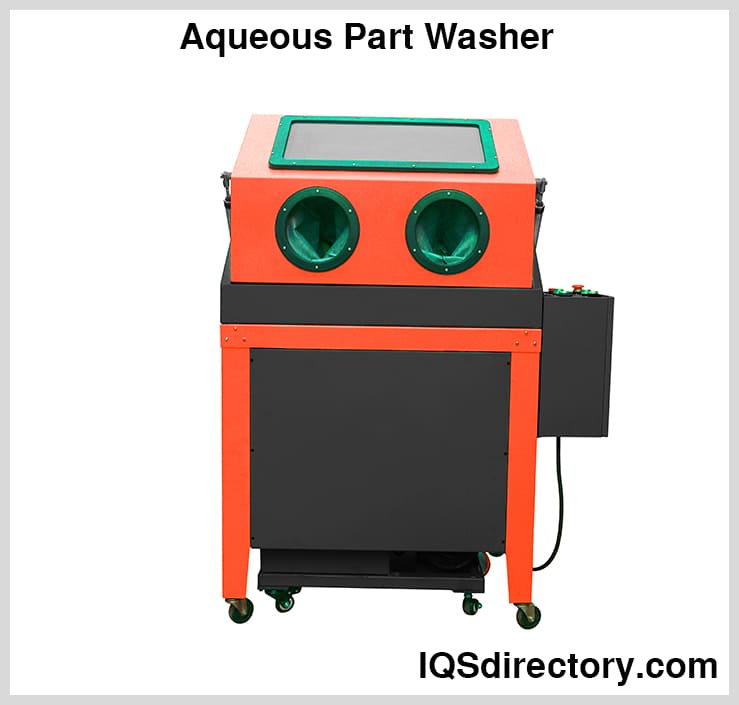
An aqueous part washer is an automated or semi-automated machine manufactured to clean, remove tough grease, and dry large or small parts before distribution or surface treatment. The washing is necessary since...
Please fill out the following form to submit a Request for Quote to any of the following companies listed on
This article will take an in-depth look at automated parts washers.
The article will look at topics such as:
This chapter will discuss the definition of automated parts washers.
Automated parts washers are cleaning systems designed to remove grit, oil, grime, dirt, paint and contaminated substances from parts with minimum manual involvement. During the processing of parts and components, lubricants, oils, and chemicals are used to improve efficiency and eliminate potential damage. As necessary as these substances are during production, they have to be removed prior to being placed in an assembly, packaged, or sent on to a coating process.
Since their introduction, parts washers have been perfected, improved, and engineered to operate automatically using different forms of software that sends commands for the completion of automated tasks such as loading, unloading, washing, rinsing, and drying of assemblies and parts. The use of automated parts washers reduces labor costs, increases efficiency, radically improves the quality of the cleaning process, and is able to clean high volumes of parts in less time.
Automated parts washers include high-pressure washers, washer cabinets, rotary basket washers, deburring washers, and several other types. These robust machines are capable of cleaning a wide range of parts in great detail, regardless of the size or design of the parts or assemblies. Manufacturers depend on automated parts washers to provide a high quality cleaning, which greatly improves the quality of their final product.
As part of the cleaning process, automated parts washers use solvents and chemicals that are added to water to remove any form of dirt or grime that is accumulated during manufacturing. The nature of the cleaning process prepares parts for further processing such as coating and finishing, which require that surfaces be properly prepared by being cleaned and dried such that coatings can adhere effectively. Contaminants are removed using different cleaning media.
Newly produced parts have burrs, abrasive dust, paint, and other residue left over from the manufacturing process. One of the challenges of cleaning freshly produced parts is their designs, which may include unique shapes, grooves, blind spots, holes, passageways, and other unusual features. Automated parts washers are engineered to meet the requirements of cleaning any type of part regardless of how intricate or complex they may be.
The first options to consider in the design process are the size, shape, and configuration of the parts to be cleaned. Additional elements include the parts’ weight, closed sections, surface area, angles, and blind holes. For the development of parts washers, options like CNC programming, back or front loading, baskets, trays, a rotary table, and conveyor belts are considered. Parts washers are commonly aqueous, meaning they use water solvents to boil and soak dirty parts. Parts washers are designed to meet customers' requirements since every customer has unique part designs in mind.
The standard components of a parts washer are the filtration system, pumps, scrubbers, brushes, a water heater, power nozzle, and a cabinet. These are detailed below:
The function of the heating unit is to quickly raise the temperature of the cleaning solution, saving time in the cleaning process. The water heater is powered by various sources such as gas, electricity, or steam. The heating assembly accelerates the chemical reactions when solvents, detergents, and chemicals are used in the washing process.
When the parts washer is turned on, the cleaning water flows from the cleaning tank to the storage tank. The water passes through two filters. The first filter catches large particles, whereas the second one catches smaller particles missed by the larger filter.
Pumps in the parts washers are made to be used while submerged in solvents, water, and detergents. The function of the pump is to supply cleaning solutions to the cleaning tank. Pumps work continuously as they transfer water from the storage tank to the cleaning tank. Pumps operate at 185 °F (85 °C) and can transport 115 gallons per minute (GPM) at a psi of 65. These two elements, GPM and PSI, are essential for the working principle of the pump.
When the GPM and PSI are low, the parts washer may have challenges completely removing the cleaning solution.
The scrubber can be found in two forms: a sprayer or a set of brushes. The pump transports the cleaning solution from the storage tank to the scrubber; then, the scrubber cleans the parts.
Parts washer cabinets come in various sizes, all having unique capabilities. The washing process involves applying a cleaning solution under higher pressure in a cabinet or on a conveyor belt. The water pressure provided must be efficient enough to remove contaminants.
The cabinet is made in a manner that enables it to withstand water pressure, enabling them not to be harmed by constant exposure to water or solvents.
The water level works in hand with the cleaner storage tank. The heater can be damaged by being exposed if the water level gets too low. An automatic low or high water probe shuts off the parts washer when critical levels are reached. The process prevents the parts washer from restarting until the storage tank reflects the appropriate level.
The type of cleaning agent can determine the function of various parts washers. These can be found as either aqueous or solvent. Aqueous cleaners are water-based cleaners that unite water and detergent using mechanical and heat energy. Solvent cleaners refer to some form of petroleum compound, which can be mixed with water-based cleaners.
Solvent-based cleaners can clean metal pieces by dissolving dirt and scum. The parts cleaners must be environmentally friendly and meet some of the required standards.
Aqueous-based cleaners use a pH found at a neutral level or water-based solutions. Semi-aqueous cleaning solutions have small amounts of solvents to increase efficiency. Aqueous-based cleaners use jet sprays.
Parts washers have been enhanced and improved due to the advancement in technology. Most parts washers have now become automated and semi-automated to improve efficiency in carrying out assigned work.
Parts washer cabinets are made for processing parts under a low-volume batch. Parts washer cabinets are small enough to fit into any manufacturing process. Therefore, they provide a cost-effective method for cleaning parts. In addition, the use of volatile organic compounds (VOCs) is avoided by such parts washers because they use water under pressure to remove contaminants. Such contaminants group on the surface parts, and the washers are machined to remove the materials properly.
Spray angles are made to correctly reach every crevice, corner, and hole. Some parts washer cabinets have a fixed, nonmoving platform for placing parts inside the cleaning chamber, while some have a rotating platform. The fixed form resembles the traditional dishwasher found in homes. The rotational version of the machine is assembled with a platform that rotates and transports parts past a set of pipe sprayers. Water is applied at high pressure during all procedures. This type is economical as it controls the amount of water inside the compact and enclosed cabinet design.
Manual work or the use of a robot or conveyor can be used to load a parts washer cabinet. Baskets, holders, and turntables can also be used to hold parts depending on the part washer's design. When the automated parts washer is turned on, water is transported from pipes at pressures of 100 to 3500 psi. On the surface of the items, material is forcibly removed using the combination of the force of the spray and the heated water. These washers save money, are eco-friendly, and result in less water use.
Ultrasonic parts cleaners make use of the cavitation effect. In an ultrasonic cleaning tank, vibrating power is generated by transducers and transferred to liquids in the tank to form billions of imploding microscopic bubbles. The process forms a scrubbing action on the surface of parts, crevices, holes, and indentations. The nature of this process cleans the most complex and intricate parts and devices.
The mechanisms of an ultrasonic parts cleaner include a bath, transducers, and heaters, all aligned with a power source. The transducers and heaters are placed on the bottom and sides of the cleaner for the most efficient operation. The size of the bath has to be large enough to efficiently receive all the parts to be cleaned. Different grades of steel are used to make the tanks, such as 316L and 304 stainless steel.
The contained transducers can create strong vibrations with frequencies of 20 KHz, 80 KHz, 100 KHz, or 120 KHz. The lower the frequency, the more powerful the vibrations. Large-capacity ultrasonic parts washers have a frequency of 28 KHz. Generally, ultrasonic parts washers work with frequencies of ranges from 35 KHz to 45 KHz. High-frequency ultrasonic parts cleaners have bubbles that release large amounts of cleaning energy. This energy is capable of removing abrasives and polishing paste.
The transducers need electrical energy for the production of the required vibrations. Sufficient power is needed for the proper cleaning processes. Parts to be cleaned can be loaded with baskets hung from the top of the cleaner. Parts to be cleaned must be fully placed in the tank for proper cleaning. These parts should not be in contact with each other.
Biocycle parts cleaning systems are used to remove unsafe chemicals and solvents. Biocycle systems are water-based immersion systems that use bio-safe chemical solutions as parts cleaning agents. These mechanisms use a mixture of biological factors and scientific research. Biocycle parts use microbes, or living microscopic organisms, to break down grease, oil, and contaminants.
A biocycle system is self-cleaning with the use of biodegradable formulas. Developing a biocycle system is centered on creating a natural and safe method for cleaning parts. After the microbes are used to clean the parts, the remaining hydrocarbons are transformed into carbon dioxide and water, which are later filtered and reused. To keep the microbes alive, oxygen is supplied into the solution.
The biocycle system benefits the environment and can be reused indefinitely. Other advantages include being cost-effective and eco-friendly. Biocycle systems have a big advantage in lowering costs and eliminating waste. The cleaning solution in the biocycle system has lasting stability over time. A control box placed on the system works to monitor the cleaning level, and oxygen levels supplied to the microorganisms.
These parts washers are aqueous cabinet parts that spray heated water and solutions on parts. This is done at highly increased pressure. Nozzles in the cabinet can spray a jet of washing solution onto parts. Spray parts washers are found in a stainless steel cabinet. Depending on their design, these can have a fixed table or turntable. The cleaning solution is injected through oscillating nozzles that spray the part's load continuously at different angles. Various components are managed from a control panel. Rinse, steam exhaust, and blow-off cycles are there for efficient results.
The pumping system of the spray washer has to be perfectly aligned and be able to perform properly without the need for adjustments. The spray manifold reaches the surface of parts from several directions: the top-down, bottom-up, and across from the sides. The oscillating motion of the spray manifold creates room for the spray to reach every aspect of a part's surface.
All nozzles are designed in a form that enables them to aim, spray, and offer complete coverage without intersecting spray. Each nozzle blast is directed straight on its own plane. Spray parts washers have different types, with some having a turntable with a turntable drive while others have a fixed table that does not move around in the spray. The effectiveness and efficiency of the spraying system are the basic relations between the types of nozzles.
In mass production sectors, spray parts washers have a conveying system that transports batches of parts through spraying chambers. There is the use of a CNC system due to the complexity of the system. Spray pressures can be set between 30 psi to 70 psi and temperatures reaching between 130 °F to 200 °F (54 °C to 93 °C).
Carousel parts washers are a form of conveyor parts washer with multiple cleaning stages. They are normally used for like parts that require precise, accurate, and complete cleaning. The carousel design is ideal for high production operations that demand rapid cleaning and a small footprint.
With an automated design of carousel parts washers, parts are loaded and unloaded at the same location on the machine using a robotic mechanism. Dirty parts travel along a conveyor path that takes them through the cleaning stages and returns the parts to where they were loaded. The central point of a carousel parts washer is efficiency and speed.
Rotary drum parts washers are cost-effective for high-volume parts cleaning. In this washer, parts are washed using spray and immersion. In this process, the spray cleans the surface of parts as immersion flushes and cleans the insides. Rotary drum parts cleaners are machined to handle small parts in volume.
Rotary drum washers contain a rotating internal helix that tumbles and conveys parts through various stages of the cleaning process. The drum of a rotary drum parts washer performs like an agitator in moving parts to cleaning stations. During the washing and rinsing cycles, parts are tumbled to expose surfaces, edges, and crevices.
The green washer uses bio-matic, a mixture of biology and scientific research, as a method for cleaning. Parts are immersed in a heated washer containing a pH-neutral solution. This solution is combined with a microbe colony. The microbes work in an environmentally safe manner. The efficiency of the cleaning process of rotary drum parts washers is enhanced by the combination of rotation and spraying, which removes chemicals, dirt, and grime from the exterior and interior of parts. The force supplied by the spray can remove surface oils, dust, and contaminants. The immersion in the tumbling process works to flush out holes, hollow areas, and blind holes.
They are in different sizes, including minis, large versions, and dual types. Minis are used for small parts, and other die components. Large versions have a higher cleaning power and can be used for high-volume cleaning. Dual types have drums that function at different rates and can clean separate parts. They are made efficient as they take up small floor space.
This type of automated parts washer uses an inline parts conveying system. The system is machined to allow it to have parts brought in directly from stamping presses, CNC machines, and other manufacturing processes. Various belt sizes are contained, and these can meet the needs of any number and size of parts. The different cycles are programmed to wash, rinse, blow off, and dry parts as they move along the conveying system. As with other washers, a steady flow of water has to be ensured.
These washers are similar to conveyor systems; however, monorail systems have an overhead conveying system to move parts, unlike conveyor systems with a metal mesh belt. Monorail systems are a part of continuous processes where parts are brought for cleaning, prepared, and then sent for further processing. Monorail systems can have closed-loop multiple stages and also inline stages. The closed-loop is used for the operator to load and unload the system at the same station. Spray nozzles on headers spray pressurized cleaning solution onto the parts. Several control panels are contained for maintenance, monitoring, and service access.
These refer to an aqueous immersion method of parts cleaning that prefers energy for creating vibrations and mixing action that cleans surface dirt from parts. The resulting vibration is due to impellers and paddles that cause cavitation on part surfaces. The agitation method is machined for parts that can withstand being shaken rapidly and bounced without experiencing any damage.
The agitation process depends on the chemical action of the surfactant. This process is ideal for bringing the cleaning agent in contact with the surfaces of parts. The amount of time required to remove grime and contaminants is a disadvantage of the agitation process. Simple parts are required for the agitation process. The agitation parts washers are cost-effective and use less energy. However, the agitation process takes more time.
Immersion parts washers submerge parts in a cleaning solution. Immersion parts washers are also referred to as dip tank parts washers. These reveal items to be cleaned with a mixture of solvents, detergents, and other cleaners. Immersion parts washers are a cost-effective method for cleaning parts and saving energy. These washers can cater to large bulky parts and very small parts in batches with odd shapes, grooves, and blind spots.
To be cleaned, parts are placed in baskets and passed through processes that include soaking, ultrasonic cleaning, heat immersion, and agitation. Soaking is applied for easy-to-clean parts that will be transferred to other cleaning processes. This process prepares parts for an intensive cleaning process. Agitation in these processes takes two forms: lift platform agitation and turbo agitation.
In platform agitation, parts are lifted up and down in the cleaning solution with a motion to scrub and agitate the parts' surfaces. In turbo agitation, a pump continuously circulates the cleaning solution. For highly effective cleaning, these two processes are used together. Heat immersion imposes the principle of using water heated to high temperatures in line with water-based cleaners. This heat immersion is an excellent eco-friendly alternative to parts washing.
These types of washers are assigned and machined for washing very small parts such as screws, bullets, pipe fittings, scrap metal, castings and bolts. Small parts washers have blind holes, complex configurations, and interior and exterior threads that must be cleaned and decontaminated. Various types of oils, lubricants, and solutions are used to make the small parts. These are designed to make the shaping and forming of them smoother and more efficient. There is a removal of the materials used for lubrication before proceeding to the next process. As compared to large parts, these are less costly and time efficient.
Immersion and rotation are two common methods used to clean small parts. In the case of small parts rotary washers, the rotating system gently tumbles the parts in a basket. Small parts washers can be made of metal such as stainless steel. Beside the stainless steel, plastic can also be used for their formation. Small parts washers are machined to clean tools as well as parts. Washers are incorporated with a basket or using a tank. The basket can be used for tools to be immersed in a solvent for cleaning. Solvents and detergents that clean substances off tools efficiently with little effort can be released using helix rotation, agitation and sprayers. Small parts washers can work in hand with manual cleaning to provide efficient cleaning tools.
This chapter will discuss the applications and benefits of automated parts washers.
Automotive manufacturing industries run both new vehicle parts formed from forming processes and used parts with grease, road dirt, and grime collected through automatic parts washers. Automated parts washers are also found in hardware factories. Here, small tools like fasteners are produced. They run their newly formed products through parts washers in high volumes. In the medical sector, some medical facilities use automated parts washers to sanitize large amounts of reusable instruments and supplies. Recycling facilities also use automated parts washers; before a used item like a plastic bottle or drum can be melted down and formed into a new product, it must be fully cleaned and sanitized.
Parts washers offer a safe and efficient method for parts washing through the use of elements such as water, heat, agitation, and other environmentally safe chemicals. Parts washers are cost-effective as they remove the need for labor in the parts cleaning process. Some cleaning processes do not require human intervention, thus saving labor costs. Parts washers can clean any form of parts regardless of size or complexity, and they can reach complex and isolated parts to remove contaminants effectively. The parts washer can be efficiently controlled by the manufacturer with automated control panels, enabling the production of desired results.
Automated parts washers are mechanical devices designed to efficiently remove grit, oil, grime, dirt, paint, and other contaminating substances with minimum manual supervision. In short, the common use of an automated parts washer is to clean and prepare parts. Certain computer software is used to control the parts. In this design process, the first option to consider is the size, shape, and configuration of the parts to be cleaned. Some elements include weight, closed sections, surface area, angles, and blind holes. The standard components of a parts washer are the filtration system, pumps, scrubbers, brushes, a water heater, power nozzle, and cabinet. Types of automated parts washers include small parts washers, agitation parts washers, immersion parts washers, and conveyors parts washers. They can be used in the automotive, medical, and recycling sectors.
An aqueous part washer is an automated or semi-automated machine manufactured to clean, remove tough grease, and dry large or small parts before distribution or surface treatment. The washing is necessary since...
A parts cleaner is a cleaning device that uses various types of solvents, cleaning agents, and processes to remove grease, grime, and contaminating materials from manufactured parts prior to shipment or movement for further processing...
A parts washer is a mechanical device designed to remove grit, grime, oil, miscellaneous debris, dirt, paint, and other contaminating substances from parts in preparation for their use in assembly operations, packaging, or coating...
A wastewater evaporator is a method of removing water from water-based waste by converting the water in the waste to a vapor and leaving contaminants. The function of a wastewater evaporator is to reduce the volume of waste materials...
Parts washers are designed for cleaning, degreasing of equipment, and drying of mass quantities of small or large parts in preparation for surface treatment, assembly, inspection, or shipment...
Industries worldwide utilize abrasive blasting for various purposes, including cleaning rust and oil, removing surface coatings like paint and pollutants, preparing surfaces for paint and coatings, reinforcing metal surfaces and...
Deburring is a secondary operation of a machining process that enhances the final quality of the product by removing raised edges and unwanted pieces of material, known as burrs, left by the initial...
Finishing machines are machines used for metal finishing, which is the last stage of the metal fabrication process; the stage encompasses the use of machines in finishing the metal surface...
Sandblast cabinets include systems or machinery and components for projecting blast media against a part‘s surface to abrade, clean, or modify the surface. Sand, abrasive, metal shot, and other blast media are driven or propelled using pressurized water, compressed air, or a blast wheel...
Sandblasting equipment includes systems or machinery, and components for projecting blast media against a part‘s surface to abrade, clean, or modify the surface. Sand, abrasive, metal shot, and other blast media are driven or propelled using pressurized water, compressed air, or a blast wheel...
Shot peening equipment includes systems or machinery and components for projecting shot peening media against a part‘s surface to modify the surface or surface engineer the part...
A tumbling machine is a durable deburring and metal-polishing machine designed for finishing large parts or batches of smaller parts. A tumbling machine is also known as a barreling machine or a mass-finishing...
An ultrasonic cleaner is a type of sonic cleaner or sonic cleaning machine that uses cavitation to remove unwanted material. The cleaning effect is created by the compression and refraction of a cleaning medium. Miniscule vibrations propagate throughout the...
Ultrasonic cleaning is a type of cleaning process which uses cavitation induced by alternating compression and rarefaction cycles at ultrasonic frequencies. Ultrasonic frequencies are sound waves vibrating at 20 kHz or higher...
Vibratory tumbler is the equipment used in a vibratory finishing process, one of the most common methods in mass finishing. But how does a vibratory tumbler work...