Aqueous Part Washers
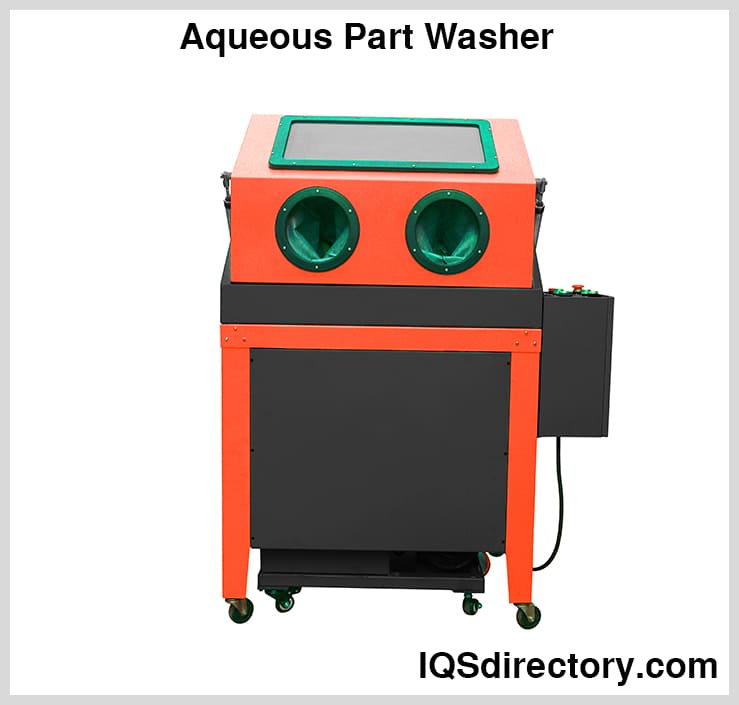
An aqueous part washer is an automated or semi-automated machine manufactured to clean, remove tough grease, and dry large or small parts before distribution or surface treatment. The washing is necessary since...
Please fill out the following form to submit a Request for Quote to any of the following companies listed on
This article explores all of the basics of Parts Cleaners.
You will learn more about topics such as:
A parts cleaner is a cleaning device that uses various types of solvents, cleaning agents, and processes to remove grease, grime, and contaminating materials from manufactured parts prior to shipment or movement for further processing. The process of parts cleaning is a means of further examination of parts for quality control and determination of possible flaws, imperfections, or deformities.
The parts washing process is capable of cleaning and decontaminating any number of parts quickly and efficiently. It is an environmentally safe process that uses chemicals that are eco-friendly and biodegradable.
The first consideration when looking at the parts cleaning process is to determine the number of parts to be cleaned. Though the volume does not affect the steps of the process, it does affect the type of process chosen. Hand cleaning or brushing may be an option for a few parts, whereas huge volumes of parts will require the use of parts cleaning equipment.
Regardless of which method of cleaning is chosen, some type of solvent, cleaner, or chemical will be necessary to ensure the best possible results. Every parts cleaner manufacturer has a wide selection of cleaning materials designed to completely sanitize and cleanse any type of part.
In the case of hand cleaning, all of the steps can be completed at one time. With parts cleaning equipment, there are various steps, the first of which is pre-cleaning. On a parts cleaner, there is a zone of the machine that prepares and pre-cleans the part before it enters the bath. This may consist of a light spray or drenching to remove dust and other loose material that sets on the surface of parts.
The cleaning stage is when the part is placed in the cleaning equipment. There are several types of part cleaning methods that range from small units about four feet high to larger, conveyor units for production lines. In the smaller units, the precleaning is one step in the machine's operation. Larger conveyor units have sections where each stage of the process is completed. These sections are referred to as zones; the zones have access doors for cleaning or repair.
The rinsing process ensures that the parts are completely clean. The requirements established for the parts cleaning process determine the type of rinse necessary. In the majority of cases, city water is used to rinse parts using some form of deionization, reverse osmosis, or purified water to remove the cleaning chemicals or solvents.
Parts are only as clean as the rinse cycle is effective. The purpose of rinsing is not to rewash the cleaned parts but to remove any cleaning agent that may remain on the parts. Multiple rinses improve the quality of the parts cleaning, though it does increase cost.
A significant element of the cleaning process is water, which is 95% of the cleaning solution. Though water out of a tap is safe for drinking, it is not clean enough to clean parts since it contains calcium and magnesium that leave water spots and gather on heated surfaces. The rinse system attached to a parts cleaner purifies the water such that it is ideal for parts cleaning.
After the cleaning process, portions of a part may have an exposed surface that could be subject to corrosion. To prevent corrosion, an extra stage of the parts cleaning process is a corrosion rinse that does not contaminate the surface but provides corrosion protection before going on to further processing.
Though cleaning using solvents and chemicals is a common process for parts cleaning, other solid cleaning processes that do not include chemicals are also used for parts cleaning and may not include all of the steps used in liquid or wet processes. One method uses pellets that pummel the part to beat off grime and dirt. The dry ice, or CO2 process, is used for sensitive and fragile part cleaning.
Included in the numerous ways for cleaning parts are ultrasonic cleaners, vibration cleaners, lasers, brushes, and blow systems. These processes are less intrusive than solvent chemical cleaning or dry ice methods.
The selection of the cleaning process, in addition to volume, depends on the part to be cleaned and if it requires special measures to clean fragile, technical parts requiring a more gentle but efficient approach. Regardless, parts cleaning is an essential part of product production and is included in every manufactured product.
While choosing parts washers, a main consideration is how effective the cleaning process is. One of the factors that determines the quality of the cleaning is the power density, which is used to measure the power of a device or power supply unit. It is especially important regarding the internal capacity of an engine.
In the case of part cleaners, power density is the amount of cleaning energy in horsepower per cubic foot of the cabinet volume. As the size of the part cleaner increases, in reference to the diameter and height, the power density drops at an exponential rate.
When examining various parts cleaners, it is important to examine the amount of horsepower from the pump in relation to the work volume of the parts cleaner, which can be seen in the image below.
Four of the factors that need to be considered when determining the performance of an aqueous based parts washer are mechanical energy, temperature, detergent, and time. When a cleaner has exceptional mechanical energy at high temperatures, it delivers shorter cycles and excellent performance. The motor of the pump and quality nozzles are essential aspects in determining how well the parts cleaner will perform. An additional factor is the power density.
As the size and volume of a parts cleaner changes, the power density changes. For optimum performance, the power density must match the volume of the parts cleaner. As the volume increases, the horsepower of the pump and pump motor have to change inaccordance with the increase in volume to maintain the power density.
The power density of parts cleaners is the single factor regarding the performance of the cleaner. A parts cleaner with a low horsepower motor will not provide sufficient power to do a quality job of cleaning parts if the volume of the cleaner is beyond the pump's capacity. Parts cleaner manufacturers supply data regarding the horsepower of the pump motor in relation to the power density. It is one of the factors that engineers plan into their designs.
There is an endless variety of parts cleaners with new ones being developed to meet the demands of manufacturers. Many types are necessary to meet the need to clean and prepare unusual and unique parts. When a part has intricate details and designs, it will require a cleaning process capable of removing contaminants from hard to reach areas.
There is a specific type of parts cleaner for every operation regardless of size or volume. The types of parts cleaners for auto repair shops are smaller and less expensive than ones that have been designed to clean parts as part of manufacturing assembly. Regardless of size, each type has the efficiency and effectiveness necessary to meet the conditions.
Spray parts cleaners are the most common form of parts cleaner. The cleaning process is performed by nozzles placed at varying angles that apply a cleaner and water to parts with high pressure. The pressurized stream from the nozzles cleans away soil, grime, grease, oil, coolants, and other contaminants. The spray washing technique is found in conveyor systems and cabinets.
Spray cleaning is automated. Once the parts are loaded into the mechanism, the cleaner automatically goes through each step of the cleaning process.
Immersion parts cleaners use tubs or containers that are filled with water and a cleaning solution. The process is designed for disassembled parts that need to soak in a cleaning solvent for an extended period. An added feature for immersion parts cleaners is agitation that is similar to the family washing machine. Another version combines immersion with ultrasonic cleaning, which is designed to be used in biotech and pharmaceutical industries with transducers to create high frequency vibrations.
The rotary drum process can be a drum that is perforated with spray nozzles or the drum can be solid in the form of an immersion parts cleaner. As the drum rotates, the parts are in constant motion to facilitate the cleaning process. Drums can vary by height, speed, width, and the aggressiveness of the cleaning process. A rotary drum cleaner is designed to combine a gentle tumbling action with the immersion or spray processes to provide a thorough cleaning.
The typical cycle of a rotary drum cleaner is agitation to clean blind holes, hollows, and tubes. Once parts are cleaned, they are rinsed and dried. A major benefit of rotary drum parts cleaners is their longevity, which is mainly due to the stainless steel construction of the drum.
Of the many varieties of parts cleaning equipment, the one type that seems to be overlooked is part tumblers, which are a highly efficient and well-designed parts cleaning option. The main industrial use for parts tumblers is in the auto industry. As with all parts cleaning equipment, parts tumblers are relied on to remove burrs and polish parts. The two main types of parts tumblers are vibratory and rotary.
Vibratory and rotary tumblers have similar construction with a barrel, base, drive, motor, and gear assembly. The distinction between the two types is the type of motion they create as part of their cleaning process. They can both be used for wet or dry deburring and include a speed motion control.
Rotary tumblers have a hexagonal or cylindrical barrel, base, drive, motor, and gear assembly. The cleaning process for a rotary tumbler includes rotational movement with an abrasive media that creates a sliding action in the tumbler. Rotary tumblers are fast and aggressive methods for deburring and polishing parts.
Unlike a rotary tumbler that uses rotary motion, a vibratory tumbler has a side to side agitating motion at an extremely high rate. The rapid back and forth movement produces friction that continuously grinds the parts against each other to clean their surfaces. Vibratory tumblers are ideal for small and medium sized parts.
Conveyor parts cleaners are designed for high volume cleaning of numerous parts in a continuous flow. Though there are established conveying systems, many conveying systems are specially designed to fit into a specific assembly operation. Some of the common types of conveying systems are u-bend, monorail, and in-line.
Conveyor systems can be integrated into an assembly line or be stand alone depending on the needs of the operation. The benefit of conveyor parts cleaners is their ability to fit into any type of application or process.
In a u-bend system, the part is loaded into the washing system processed, and returned to the operator. The u-bend system is similar to the conveying system used by dishwashers.
A monorail system has all of the characteristics of a traditional conveyor system with the exception that the parts are conveyed by an overhead monorail. The parts are positioned on a specially designed support that takes them through each of the cleaning zones. Each monorail system is built to the specific needs of the parts and application.
In an in-line conveying parts cleaner, also referred to as a tunnel parts cleaner, parts are placed on a conveyor at the entrance and come out completely clean at the exit. Between the insertion and removal, the part passes through various zones or stations where it receives a cleaning treatment.
An ultrasonic parts cleaner removes dirt, grime, contamination, and other materials through the use of high frequency sound at or above 20 kHz. Ultrasonic cavitation produces intensely strong wave bubbles that hit the surface of a part and implode, creating heat and energy. The process of implosion removes particulates from the surface of the part. The use of ultrasound enhances and intensifies the cleaning process using sound frequencies that are above the level of human hearing.
The flexibility of ultrasonic parts cleaning allows it to be adjusted and programmed to fit any type of cleaning need, from technical aircraft parts to medical instruments, by adjusting the temperature, cleaning solution, time, and the frequency of the ultrasonic sound waves.
Agitating parts cleaners are a version of the immersion method of parts cleaning. Parts are immersed in a tank with a cleaning solution and vibration and mixing are applied. The vibrations are produced by impellers that create cavitation, much like what is found in the ultrasonic method at a lower level of implosion. The agitation process is assisted by high pressure spray nozzles for cleaning of blind holes and part intricacies.
Certain types of surfaces require a less aggressive cleaning process that uses a media that is softer but capable. The shot blasting process that uses shards or beads to prepare a surface is too aggressive and changes the structure of the surface. A compromise between shot blasting and other cleaning methods is soda blasting
Soda has a Mohs scale rating of 2.5 and won't etch or deform the surface being cleaned. It is an effective method for cleaning softer ductile metals such as aluminum and can remove dirt, grease, grime, paint, and carbon deposits. Soda blasting can be used in slurry form or dry blasting and does not require parts to be prewashed or prepared for the process.
The process of soda blasting requires specialized equipment since soda does not flow like other abrasive materials.
For many years, the process of degreasing a part involved placing the part in an open top vapor degreaser (OTVD), turning it on, letting the solvent complete the process, and removing a cleaned part. Due to the high cost and safety considerations for OTVD parts degreasers, they are being slowly phased out and replaced by vacuum vapor degreasers (VVD), that do the same job with less concern for safety and cost.
The key to VVD success is the removal of air from the cleaning process, which allows pure uncontaminated vapor to rapidly flush the surface of the part. Without any air in the cleaning chamber, there isn't anything to block or slow down the progress of the vapor. The efficiency of a VVD parts degreaser is found in its ability to clean blind holes, tight areas, and complex intricacies. The cleaning solvent is able to reach all surfaces that had been previously occupied by air.
Vacuum degreasing overcomes the many limitations of traditional degreasing equipment that performed adequately for many years but produced high emissions and used exorbitant amounts of energy. All of these factors have been eliminated by vacuum degreasing systems.
Robotic arms with six axis access are a programmable method for parts deburring, flash removal, cleaning, and parting line removal. Pneumatically driven, they can quickly, efficiently, and safely remove defects associated with part production. Robotic arms can be programmed with extended reach for setting up their path with auxiliary axis available from turntables and linear tables, which can further extend their reach.
When the robotic arm is cleaning a workpiece, it is held in place by grippers that position it properly and provide proper access. Additionally, robotic processes can be programmed to clean and dry a workpiece. Dust, oil, and sub micron particles can be cleaned off surfaces using CO2 or dry ice blasting. It is a non-abrasive process that is safer and does not include any secondary waste. CO2 blasting can be used on metals, plastics, and composite materials.
The precision and accuracy requirements of modern manufacturing necessitate that parts be completely cleansed of any contaminants before being placed in the assembly process. Though water cleaning is an acceptable method for cleaning parts, it is unable to clean sufficiently to meet the criteria necessary for the manufacturing process.
In order to meet production specifications and requirements, parts cleaner manufacturers work with chemical companies to develop solvents that are strong enough to clean parts but not contaminate the environment. The requirements for solvents have to be adjusted to meet temperature requirements but include chemical compositions such as chlorinated, brominated, fluorinated, or alcohol.
When making the selection of chemicals, there are several factors to consider, which include health hazards, flammability, and performance. Lower performing chemicals require high heat and additional equipment features. Quick drying chemicals are hazardous and require exceptionally careful handling while slow drying chemicals have excellent performance but need the assistance of a drying mechanism.
Every part that is processed for manufacturing needs to be washed before insertion into a final product. Cutting oil, grease, and grime are part of producing components and parts. To ensure the quality of a product, these unnecessary materials need to be removed. There are several common methods used to clean parts using a solvent.
Solvent based fluids provide lower surface tension and are less viscous than water, allowing them to get into gaps, blind holes, and intricate configurations. Solvents wet the surface of the parts and evaporate out of small tight areas.
Mineral spirits are used for parts cleaning due to their ability to quickly dissolve oil, grease, dirt, grime, burnt carbon, and lubricants. The most common types of mineral spirits used in immersion parts cleaners are petroleum based. They are too volatile and flammable to be used in any of the other parts cleaning devices. Although it is an effective cleaning agent, mineral spirits are toxic and potentially harmful to workers and the environment.
Naphtha is another petroleum cleaner that is used in the immersion method of parts cleaning and is a stronger and more aggressive cleaner than mineral spirits. Regardless of its strength, it is capable of cleaning parts without damaging the surface of the parts. It has a stronger odor than mineral spirits, which is a major deterrent to its use.
In the parts cleaning process, naphtha is stored in a tank beneath the parts cleaning unit. Clean solvent is extracted from the tank at low pressure and applied to parts by a spray nozzle.
Bromide is used for cleaning light metals and alloys with exceptional cleaning power and rapid evaporation for faster cleaning. A mid-range temperature setting is sufficient, and this reduces energy costs. Bromide has a faster cleaning cycle that further adds to energy and cost savings. Unlike petroleum based solvents, bromides are non-flammable and do not have a flash point.
Oxygenated solvents have oxygen as a part of their molecular structure and have low toxicity but high solvent cleaning power. An important requirement for oxygenated solvents is purity, which necessitates the purification of solvents during processing. Though they have high purity standards, they tend to be inexpensive.
Halogenated solvents have halogen atoms such as fluorine, bromine, iodine, or chlorine. They are non-flammable and evaporate quickly and have been widely used as cleaners for many years. Recently, they have been deemed an unacceptable method for parts cleaning because of their environmental impact.
Alkaline is highly effective when dissolved in water. When combined with mechanical action and the correct temperature, it easily removes contaminants and particulate matter. Its effectiveness varies depending on the contaminant that needs to be removed, the number of parts, and how automated the cleaning process is.
The contents of alkaline cleaners include alkaline salts, a wetting agent, and a sequestrant agent. They rapidly clean contaminants from metal parts and are easily rinsed from the parts. As a solvent, alkaline dissolves oil on metal surfaces. Alkaline is used in immersion tanks, spray cabinets, conveyorized systems, and ultrasonic systems.
Fluorinated solvents, or fluorosolvents, are chemicals capable of cleaning oil, residue, flux, and contaminants from high volume part operations. Of the various solvents, fluorinated solvents are considered to be an environmentally friendly option due to their lack of flash point or ozone depletion potential. They have low global warming potential or possible surface tension potential. They penetrate the surface of a contaminant without damaging the substrates.
The essential difference between aqueous parts cleaners and solvent parts cleaners is the types of cleaners being used. Cleaning agents for solvent cleaning are based on some form of manufactured petroleum cleaning chemical that includes alcohol, chlorinated hydrocarbons, and terpenes. These types of chemicals are flammable and reactive, which makes them unsafe under certain conditions.
As the name aqueous implies, aqueous cleaners are made from water based natural chemicals that are inserted into the mechanical process for parts cleaning. They have additives such as surfactants, solvents, acids, alkaline building agents, and inhibitors that enhance their performance and assist them in meeting special needs.
Aqueous cleaners are rated as having no volatile organic compounds, hazardous pollutants, flammable materials, or global warming potential. They easily dilute in water and rinse completely after cleaning. There are several types of aqueous cleaners on the market that work efficiently with spray, immersion, ultrasonic, and other forms of mechanical cleaners.
The aqueous cleaning cycle is quick and efficient. Parts can be loaded into the cleaning mechanism without the need for pre-washing, soaking, or scrubbing. Their ease of use makes them cost effective and labor saving.
Aqueous cleaners use hot water, a cleaner, and mechanical energy to remove dirt, grime, contaminants, and soil from parts. Their main benefit is their safety since they do not use any form of petroleum or flammable products that can produce harmful odors and be environmentally unsafe.
A major concern for society is the amount of industrial waste that is produced during manufacturing. A major benefit of aqueous cleaners is the extremely limited amount of waste the process produces.
Aqueous cleaners have the additional benefit of limiting scrap and material waste. Since they are less aggressive cleaners, they do not harm or damage the materials they are cleaning, which eliminates the need to dispose of scratched or marred parts.
A concern regarding the use of mineral solvents and other petroleum based solvents is the amount of air pollution they produce; this is a danger to the workers and the community. The use of aqueous parts cleaners eliminates that concern.
One aspect of the parts cleaning process is the filtration and cleaning of the water to remove residual cleaners. This is necessary for safety and environmental concerns. In the case of aqueous cleaners, the cleaning solution can be extracted and reused without concern for contamination.
As with every aspect of manufacturing, cost is always a concern and major factor. The set up and footprint of aqueous cleaners, since they do not have the pollution potential, is less expensive and more efficient.
The elimination of petroleum based cleaners significantly reduces the potential damage to parts cleaning equipment. The chemical base of petroleum solvents cleans the surface of parts but also produces wear on the parts cleaner, leading to repairs and longevity limits.
Ultrasonic parts cleaners break down contaminants with ultrasonic vibrations at the molecular level through the use of cavitation bubbles produced by high frequency sound waves. The speed of the cleaning process is enhanced and magnified with the use of an aqueous cleaning solution.
Parts cleaner manufacturers have turned to aqueous parts cleaners as an alternative to harmful parts cleaning solvents. This has led to the rapid rise in aqueous cleaners being combined with ultrasonic cleaning as well as spray and immersion methods.
Manufacturing has become more dependent on technology to produce products and components at a faster rate. The increasing demands to be efficient and reach perfection requires that every step of the process be completed without the need for reprocessing and without increased waste. Critical to these factors are parts cleaners that prepare parts and components for insertion into finished products.
The efficiency and effectiveness of parts cleaners ensure that the components used to produce marketable products meet necessary quality and customer expectations. Unclean and defective parts can cause delays and increase costs.
The traditional method of cleaning parts by hand is time consuming and inefficient. With the increased pressure on time, it is ineffective to waste manpower on cleaning parts by hand, a process that does not have the capacity or ability of parts cleaners. Pressure washing and agitating parts washers free up labor to be repurposed for more urgent projects.
The types of lubricants, oils, grease, and other materials that get embedded on the surface of parts are extremely challenging to remove. The efficiency of parts cleaners removes the grime safely and effectively.
The cleaners and solvents that are necessary to attack and remove contaminants from parts are aggressive and can be harmful. The use of parts cleaners eliminates any potential danger and creates a safe working environment.
Parts cleaners rapidly and efficiently clean parts and have them readily available. In today's competitive market, speed of processing assists in increasing productivity and allows for better use of time and assets.
Aside from the reduced labor costs, the parts cleaning process uses less power and water as a result of the technically advanced design of parts cleaning equipment. Additionally, parts cleaning equipment has a longer sustained work life, which reduces equipment costs. Parts cleaners seldom need repair and are capable of working continuously.
There is a parts cleaner that is designed to fit every manufacturing operation. From small parts cleaners for auto repair to large conveyor units for assembly operations, parts cleaners can be designed and engineered to fit any space or configuration.
Efficient operations and time savings have become the central issue for manufacturing operations. Being able to produce high quality products in a short span of time is a necessity to be able to keep up with a competitive market. Parts cleaners fulfill the objectives of part preparation without increasing costs or involving the use of other assets.
The rising concern for the safety of the environment has raised the consciousness of all producers, especially those involved in the use of solvents and chemicals. Modern parts cleaner manufacturers are very aware of the need to produce equipment that completes the process of cleaning parts without making an impact on the environment. This has led to a trend in parts cleaner equipment that does not produce an environmental footprint and has recyclable and reusable materials.
Efficiency is a requirement of every industrial operation. It is the cornerstone of successful production and the ability to meet the demands of customers. For this reason, parts cleaners have become a necessary part of several industries, from small toy manufacturers to large automobile producers.
The differentiation in the modern market is the quality of the final product. Customers have become more demanding in regards to the value of the products they purchase. This concern has led producers at all levels to develop processes that ensure the quality of their products, which has led to the use of parts cleaners as a central part of production.
Medical instruments must be flawless and exceptionally clean. The production of medical equipment uses a closed loop cleaning system that washes, rinses, and dries components in one simple operation. Enhanced cleaning involves cleaning, rinsing, passivation, rinsing, and drying through the use of an ultrasonic process. Parts cleaning equipment for the medical instrument industry uses precision designed and engineered cleaning equipment.
There are a wide range of sensitive parts and aircraft sensors that require precision engineering and machining that necessitate exceptional cleaning. The key factor for the aerospace industry is the quality of parts due to the need for accuracy for the safety of aircraft. This requirement places greater demand on parts cleaners to provide high quality cleaning and the removal of all possible contaminants and particulate matter.
The cleaning process for automobile parts breaks into two categories: manufacturing and repair. In the rebuild and repair classification, individuals and repair shops use parts cleaners to remove any built up materials from the use of a part to determine its reusability. In manufacturing, the precision and quality of the final product depends on high quality parts that are capable of withstanding the demanding conditions of vehicle use.
Parts cleaners for the pharmaceutical industry are required to meet the strict standards for clean rooms. The manufacture of labware, instruments, and tools are carefully monitored to ensure the highest quality of cleanliness and hygiene. The processes for pharmaceutical parts manufacturing require precision engineered parts cleaning equipment.
Though the standards for food processing are not as strict as those for medical equipment and the pharmaceutical industry, producers are required to adhere to the regulations of the Food and Drug Administration (FDA), which has comprehensive guidelines regarding the equipment, parts, and machines that can be used for food production. These demanding stipulations make it necessary to have parts cleaning tools that can easily fit into production and provide intensive cleaning.
The main concern for the energy industry tends to overlap with the concerns of aerospace because of the harsh and hazardous conditions that energy production must face. The volatile nature of producing energy and energy products demands that components and parts be flawless and without residue or possibly volatile contaminants. In the production process, parts cleaners ensure that the components being manufactured are cleansed of any potential hazards.
The optics industry requires the pre-sanitization of all of its components, including fiber optic glass, microscope lenses, telescope lenses, and lighting instruments. Parts cleaners remove oil, burrs, fine metal, and soil from the surfaces of glass and quartz. A key is the rinsing process that guarantees that there isn't any residue or product buildup.
An aqueous part washer is an automated or semi-automated machine manufactured to clean, remove tough grease, and dry large or small parts before distribution or surface treatment. The washing is necessary since...
Automated parts washers are mechanical devices designed to efficiently remove grit, oil, grime, dirt, paint and other contaminating substances from parts with minimum manual supervision. These substances are removed...
A parts washer is a mechanical device designed to remove grit, grime, oil, miscellaneous debris, dirt, paint, and other contaminating substances from parts in preparation for their use in assembly operations, packaging, or coating...
A wastewater evaporator is a method of removing water from water-based waste by converting the water in the waste to a vapor and leaving contaminants. The function of a wastewater evaporator is to reduce the volume of waste materials...
Parts washers are designed for cleaning, degreasing of equipment, and drying of mass quantities of small or large parts in preparation for surface treatment, assembly, inspection, or shipment...
Industries worldwide utilize abrasive blasting for various purposes, including cleaning rust and oil, removing surface coatings like paint and pollutants, preparing surfaces for paint and coatings, reinforcing metal surfaces and...
Deburring is a secondary operation of a machining process that enhances the final quality of the product by removing raised edges and unwanted pieces of material, known as burrs, left by the initial...
Finishing machines are machines used for metal finishing, which is the last stage of the metal fabrication process; the stage encompasses the use of machines in finishing the metal surface...
Sandblast cabinets include systems or machinery and components for projecting blast media against a part's surface to abrade, clean, or modify the surface. Sand, abrasive, metal shot, and other blast media are driven or propelled using pressurized water, compressed air, or a blast wheel...
Sandblasting equipment includes systems or machinery, and components for projecting blast media against a part's surface to abrade, clean, or modify the surface. Sand, abrasive, metal shot, and other blast media are driven or propelled using pressurized water, compressed air, or a blast wheel...
Shot peening equipment includes systems or machinery and components for projecting shot peening media against a part's surface to modify the surface or surface engineer the part...
A tumbling machine is a durable deburring and metal-polishing machine designed for finishing large parts or batches of smaller parts. A tumbling machine is also known as a barreling machine or a mass-finishing...
An ultrasonic cleaner is a type of sonic cleaner or sonic cleaning machine that uses cavitation to remove unwanted material. The cleaning effect is created by the compression and refraction of a cleaning medium. Miniscule vibrations propagate throughout the...
Ultrasonic cleaning is a type of cleaning process which uses cavitation induced by alternating compression and rarefaction cycles at ultrasonic frequencies. Ultrasonic frequencies are sound waves vibrating at 20 kHz or higher...
Vibratory tumbler is the equipment used in a vibratory finishing process, one of the most common methods in mass finishing. But how does a vibratory tumbler work...