Aqueous Part Washers
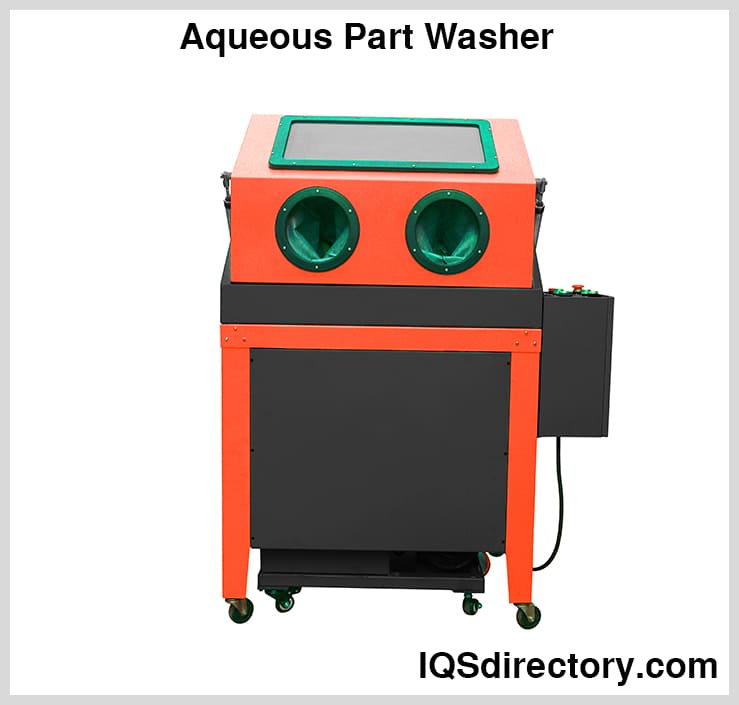
An aqueous part washer is an automated or semi-automated machine manufactured to clean, remove tough grease, and dry large or small parts before distribution or surface treatment. The washing is necessary since...
Please fill out the following form to submit a Request for Quote to any of the following companies listed on
This Article takes an In-depth look at Types of Parts Washers
You will learn more about topics such as:
Parts washers are industrial cleaning equipment that are used to remove grit, dirt, oil, paint, grease, and contaminants from several types of small and large parts. The types of parts washers are divided by the types of parts to be cleaned and their sizes, which can vary from a few millimeters or inches up to very large and complex instruments. They can clean, degrease, and dry high volumes of parts in preparation for surface treatments, assembly, inspection, or shipment.
Machined, forged, or fabricated parts are coated in oils, chemicals, burrs, abrasive dust, debris, paint, and residue left from their processing. For a part to be coated or inserted into an assembly, its surface has to be free of any contaminants that may make it difficult for the application of any treatment. Parts washers provide a high quality surface cleaning such that a part can easily fit into an assembly or have its surface treated.
Using solvents, motion, and chemicals, parts washers remove debris that can prevent a part from being used for other operations. The application of coatings using electroplating requires that the surface of a part be clean and dry for the coating to adhere effectively. Parts washers wash away any potential problems to ensure the coating process can be completed easily and smoothly.
The basic principle regarding the design of a parts washer is in regard to the size, shape, and configuration of the parts to be cleaned. The term parts covers a wide spectrum of different types that range from simple nuts and bolts to complex and intricate shapes with differing weights, part angles, blind holes, and closed off sections. As parts get more complicated, the cleaning process requires specialized equipment with unique cleaning processes.
Every parts cleaner manufacturer has a team of experts that provide solutions for a wide variety of cleaning problems. The many types of methods include parts cleaners with baskets, CNC programming, back and front loading, trays, conveyors, rack systems, and rotary tables. The basic types of parts washers are water or aqueous, which are separated by the types of solutions they use for the cleaning process.
Regardless of the many varieties of parts washers, there are certain elements of parts washers that are the same and include a water heater, filtration system, pumps, scrubbers, brushes, power nozzles, and an enclosure for cleaning process containment.
Water heaters for a parts washer can be heated by gas, electricity, or steam. It assists in increasing the chemical reaction between the detergent, chemicals, and solvents. Timing is a critical part of parts washing especially in industrial production, which requires that the parts washing process blend with the other aspects of production. This requirement necessitates that the parts cleaning process be completed quickly and efficiently. The water heater assists by increasing the speed of the chemical reaction of the solvent or cleaner with water.
The filtration unit is placed between the cleaning tank where the parts to be cleaned are located and the storage tank where the cleaning substances are stored for reuse. During the cleaning process, burrs, particles, and dirt are removed from parts and absorbed in the cleaning solution. In order for the cleaning process to be efficient and productive, the absorbed contaminants have to be removed from the cleaning solution, which is completed by the filtration unit or system.
As with all forms of parts cleaners, there are several different forms of filtration systems that can include a single filter or multiple filters depending on the design. Additionally, the individual filters placed in the units take different forms to meet the needs of the parts cleaner’s process.
The pump moves the cleaning solution from the storage tank to the cleaning tank. They work continuously and are constantly circulating the cleaning solution. Due to the nature of the cleaning process, parts washer pumps are made of resilient materials capable of operating in all types of environments and able to handle harsh chemicals. They operate at extreme temperatures with high flow rates to ensure an efficient cleaning process. In most cases, parts cleaner pumps move 115 gallons per minute (GPM) at a PSI of 65, which is critical to the successful operation of a parts cleaner.
Scrubbers can take the form of spray nozzles or sets of brushes depending on the design of the parts washer and the types of parts. As the pump circulates the cleaning solution between the storage tank and cleaning tank, part of the solution can be diverted to spray nozzles that forcefully apply the solution to the parts. Scrubbers are an essential part of parts cleaners that are required to remove dirt and grime from difficult to reach angles and blind holes.
Nozzles are part of the scrubbing aspect of a parts washer but come in different forms depending on the design of a parts washer. They apply the solvent or detergent to parts under pressure and are designed to forcefully remove any contaminants. Nozzles maintain back pressure on the pump and create an efficient pattern for part cleaning. The use of nozzles as parts of parts washers is excluded to spray parts washers. They spray water and water solutions at temperatures of 130°F up to 200°F (54°C up to 93°C).
Parts washers have tanks for storing the cleaning solution and tanks for the parts that are being cleaned. The cleaning tank is an enclosed area that takes different forms depending on the design of the parts washer, with some parts washers having multiple tanks for various stages of the cleaning process. The design of cabinet models requires the use of a single enclosed tank for cleaning and rinsing.
The sizes of parts washer tanks vary in accordance with the types of parts to be cleaned and the capacity of the parts washer. In most cases, the washing tank is larger than any other tank connected to the process. The variety of tanks also determines the type of parts washer with manual parts washers having dipping tanks while cabinet parts washers tanks open like a wardrobe.
Cabinets or enclosures for parts washers vary from a single manually filled parts washers to a long conveyor parts washer. The enclosure for a parts washer is a space that is designed to contain the chemicals and cleaning solutions used to complete the parts washing process. They can be as simple as a wash tub that sits in the corner to a long assembly line through which parts travel through zones to be cleaned. The key principle is that the enclosure provides containment and protection from the cleaning process.
A key feature of parts cleaners is the low water shut off valve that is a safety device that protects a parts washer. The water heater for a parts washer can be damaged if the water level gets too low in the storage tank. A low water shut off valve has a probe that shuts off a parts washer when the water level becomes critical. It prevents the parts washer from restarting until the storage tank is properly filled.
The types of parts washers are determined by the type of cleaning agent, which can be aqueous or solvent. Aqueous cleaners are water based cleaners that combine water and detergent with mechanical and heat energy. Solvents include some form of petroleum compound, which can be mixed with a water based cleaner. The type of cleaning solution that is used for parts cleaning determines the type of equipment that will be used.
Mineral spirits are a traditional type of cleaning solvent that is made of distilled petroleum. They are ideal for dissolving oils and grease and clean very efficiently. Mineral spirit solvents complete the cleaning process without the use of heat, ultrasounds, or sprays and are most commonly used in immersion parts cleaning. They work fast, easily clean holes, blind holes, and grooves, do not require rinsing, and dry quickly.
There are several downsides to the use of mineral spirit solvents, the most important of which is their combustibility and high flammability due to being a petroleum product. The wide variety of mineral spirit solvents on the market makes it possible to choose the perfect solvent to fit the needs of a cleaning process. Testing various types for their effectiveness is a necessity.
Mineral spirits are not environmentally friendly and require exceptionally careful handling. The parts cleaners where they are used have to be frequently cleaned, drained, and refilled on a monthly cycle. Many companies do not want to deal with the problems involved with mineral spirit parts solvents.
Fluorinated solvents are non-flammable, stable, and sustainable solvents that can be reused multiple times. They work well with a wide variety of materials for efficient cleaning and evaporate quickly without leaving a residue. Fluorinated solvents are high performance solvents for removing dirt, oil, solder residue, electronic flux, and various other contaminants.
The low surface tension of fluorosolvents enables them to penetrate contaminants while being gentle on the substrate surface. Parts that can be cleaned by fluorinated solvents include metals, plastics, polyurethane, and fluoroelastomers. Of the different cleaning products, fluorinated solvents are the most expensive, which is made up by their shorter cleaning and drying cycle and reusability.
Water based solutions have grown in popularity due to the concerns of businesses regarding the environment. Unlike mineral solvents that dissolve oil and grease, aqueous based solvents emulsify oil and grease using a surfactant that bonds with the water and oil and lifts contaminants away. Aqueous based parts cleaners are pH-neutral or water-based solutions that are environmentally friendly. To increase efficiency, semi-aqueous cleaning solutions have small amounts of solvents. They use jet sprays or a power washing approach.
Parts cleaners using aqueous based cleaners can have heat added and agitation with low and high pressure sprays. The various types of aqueous based cleaners can remove light dirt, oil, cured ink, and many other difficult to remove substances. Additionally, additives can be mixed with aqueous based solvents for the removal of rust and for the brightening of surfaces.
As with fluorinated solvents, aqueous based cleaners are more expensive and rely on a high pH to clean properly. In most cases, once the cleaning process is completed, secondary steps may be required for rinsing and drying. Unlike mineral spirits solvents, aqueous parts cleaners do not require frequent maintenance and can go for long periods without needing to be cleaned.
Biological parts cleaners are an environmentally friendly cleaner used in parts washing systems. They use microorganisms to remove dirt, grime, and contaminants from the surface of parts. Biological cleaners are an aqueous based method for parts cleaning that involves the use of a nontoxic and nonflammable surfactant that contains microorganisms that continually clean the cleaning water and break down oil, grease, and hydrocarbon based contaminants, which increases the life of the cleaning mechanism. They are a natural cleaning solution that is self cleaning, biodegradable, and safe for users and the environment.
The cleaning agents for biological parts cleaning solutions use water based cleaning liquids that are combined with natural microorganism tablets to remediate hydrocarbons for degrading power. The construction of biological parts washers can include the use of non ferrous metals, plastics, and lightweight materials that are used for heat retention and minimal liquid evaporation.
Biological parts cleaners are capable of removing the toughest carbon, grease, gunk, and oils safely without any vapors or toxic effects. The use of biological parts cleaners has been found to exceed the performance of manual solvents and aqueous parts washers. The bioremediation process keeps the equipment and fluids clean, always ready to use.
All parts require some form of washing and cleaning for the removal of oil, grease, dirt, smut, and contaminants on their surface. In most cases, this is done to prepare a part for further finishing such as the application of coatings, painting, and processes for preparation for assembly. Since most components are susceptible to secondary processes, the removal of various contaminants is essential for the adhesion of coatings and quality welding.
The washing and cleaning processes for parts take several forms and include manual washing in a specially designed drum and long conveyors with baskets filled with parts. The three commonly used methods in modern parts washing are auger, ultrasonic, and conveyor. Each of these methods is chosen in accordance with the volume of parts and the types of parts since complex parts require greater attention and more aggressive cleaning.
Auger or rotary drum parts washers are the most economical and cost effective types of parts washers. They are ideal for high volume parts washing, rinsing, and drying. The three aspects of auger parts washing involves spray cleaning and immersion. Spray cleaning scrubs the exterior surface of a part and removes any surface contaminants. The total immersion of a part in a cleaning solution flushes out contaminants trapped in corners, angles, hollowed sections, and tubes. It is an aqueous process for efficient and quick cleaning.
The process for an auger parts washer includes loading parts into the drum, which is followed by the addition of solvents. The auger is activated and the parts spiral as they are washed and rinsed. The process is ideal for washing high volumes of small components and is not suited for intricate or delicate parts.
Ultrasonic parts washing has become a very common modern method for washing parts since it does not involve aggressive agitation or motion to remove dirt from parts. Components are placed in baskets and lowered into a transducer that creates ultrasonic waves. Cavitation bubbles are created by high frequency sound water pressure that agitates a liquid solution. The force of the agitation and the cleaning agent creates pressure that forces oil, grease, and dirt from parts.
During the process ultrasonic waves penetrate the cracks, hollow, angles, and recesses of parts to clean every one of their facets. The lack of aggressive action makes the ultrasonic cleaning method ideal for delicate and fragile parts since sound waves do not damage or harm a part.
Conveyor parts washers are inline pass through washers that consist of a conveyor belt and tunnel. They are a continuous cleaning method with tunnels that are divided into sections that perform various parts of the cleaning process. The use of the conveyor method for parts washing is for high volume production operations where the cleaned and dried parts move from the conveyor washer to other operations such as assembly or welding.
The various types of conveyor washers are automated, which reduces labor costs, increases efficiency, and produces consistent results. They are designed to handle large volumes of all forms of parts and have to be designed to fit specific types of cleaning for an operation. A major benefit of the conveying method is its ability to clean any form of parts, a factor that makes them adaptable to any industry.
The manual method for washing parts involves the use of a vat or drum where individual parts are cleaned using various tools. Workers are required to wear protective clothing and gloves when performing manual washing. It is a labor intensive and taxing process that requires a great deal of time to complete and is very expensive. The inconsistency of the process makes manual cleaning unreliable and inefficient. In most cases, it is limited to auto shops and specialized cleaning of delicate parts.
Solution tribulation washing is a spray washing method that moves a solvent over, under, around, and through parts as they are immersed in the solution. The turbulence is created by a pump that agitates the solution and turbulates it. The turbulent flow is directed by manifolds that have educators or jets. The process for solution turbulation washing has higher impingement and greater cleaning power. The spray, turbulence, and agitation constantly change the flow for more efficient and effective cleaning. Although it can be defined as an immersion method of cleaning, the multiple facets of the process defies categorization and definition.
As technology and new methods have developed, parts washers have been enhanced and improved. Although the manual operation of parts washing is still prevalent, most parts washing has become automated or semi-automated to improve efficiency. The different techniques and methods for parts cleaning are endless with new methods being perfected every day. Many of these changes are connected to new products with stringent requirements.
The use of industrial parts washers includes manufacturing, remanufacturing, assembly, maintenance, and repair operations. The list of contaminants that industrial parts washers remove include dirt, grime, dust, carbon, oil, grease, metal chips, chemicals, ink, paint, residue, burrs, and corrosion. Industrial parts washers are a heavy duty piece of equipment designed for continuous use in all types of environments. Their cleaning mechanism is enhanced with the use of various cleaners, solvents, cleaning solutions, and methods.
The wide variety of parts washers and their different configurations require research and study before purchasing the correct industrial parts washer for an application. In many instances, when people hear the word parts washer, they think of a tub or barrel in a repair shop where a mechanic manually cleans a part before installing it or repairing it. Industrial parts washers go far beyond the typical image of a parts washer and include massive machines capable of cleaning thousands of parts per hour.
Manufacturers work with their customers to provide the necessary details regarding their products such that the customer can choose the correct industrial parts washer for their industry, parts, and location. Careful study is necessary since there are a group of industrial parts washers that require careful handling and special precautions. Such machines can be toxic, flammable, and dangerous.
Parts washer cabinets are designed for low volume batch processing of parts. They are sufficiently small to fit into any type of manufacturing process but provide a cost effective method for cleaning parts. They avoid the need for the use of volatile organic compounds (VOCs) by using water under pressure that removes contaminants that collect on the surface of parts and are designed to properly dispose of the removed materials.
Spray angles ensure that every crevice, corner, and hole is reached and cleaned. Parts washer cabinets can have a fixed, nonmoving platform for placing parts inside the cleaning chamber or have a rotating platform. The fixed form of the platform is similar to the traditional dishwasher found in homes. The rotational version has a platform that rotates and moves parts past a set of pipe sprayers. In either case, water is applied at high pressure. The compact and enclosed design of parts washer cabinets makes them economical by controlling the use of water, which is substantially lower than other forms of parts washers.
The loading of a cabinet parts washer can be done manually or through the use of a robot or powered conveyor. Parts are placed in baskets, on holders, or on turntables depending on the parts washer’s design. When the washer is activated, water is sprayed from pipes at pressures of 100 psi up to 3500 psi. The force of the spray combined with the heated water forcibly removes material on the surface of the items to be cleaned.
Cabinet parts washers are an aqueous form of parts washer that uses aqueous chemicals that are a combination of detergent, hot water, and alkaline. The solutions used in cabinet parts washers are environmentally safe, biodegradable, and economical. They assist in saving water and enhance the efficiency of the parts washer.
Ultrasonic parts cleaning is based on the cavitation effect. Transducers in an ultrasonic cleaning tank generate vibrating power that is transferred to liquids in the tank to form billions of microscopic bubbles that implode. The process creates a scrubbing action on the surface of parts and any crevices, holes, or indentations. The all inclusive nature of the process makes it possible to clean the most complex and intricate aspects of parts and devices.
The components of an ultrasonic parts cleaner include a bath, transducers, and heaters in different sectors with a source of power. The transducers and heaters are positioned strategically on the bottom and sides of the cleaner for the most efficient operation. The size of the bath or tank has to be large enough to accommodate the parts to be cleaned and is determined early in the selection process. Tanks are normally made of various grades of steel or 316L or 304 stainless steel grades.
Transducers can generate extremely strong vibrating power with common kilohertz per second frequencies of 20KHz, 80KHz, 100KHz, and 120KHz. The lower the frequency, the more powerful the vibrations are. Large capacity ultrasonic parts washers have a frequency of 28KHz with most ultrasonic parts washers operating between 35KHz and 45Khz. The bubbles from high frequency ultrasonic parts cleaners implode large amounts of cleaning energy capable of removing abrasives and polishing paste.
The various transducers require electrical energy to produce the necessary vibrations. How power is supplied is determined by the design of the parts cleaner and the manufacturer, with producers having their own proprietary methods. The necessary and required factor is sufficient power to complete the cleaning process.
Parts to be cleaned by an ultrasonic parts cleaner can be loaded in various ways. The most common methods are baskets suspended from the top of the cleaner or placed on racks. In all cases, they must be able to be totally immersed in the tank for proper cleaning and should not be in contact with each other.
Ultrasonic parts cleaner features:
The development of biocycle parts cleaning systems is based on the desire to remove the use of unsafe chemicals and solvents. It is a water based immersion, spray, or turbo system that uses bio safe chemical solutions as parts cleaning agents. It uses a mixture of biological factors and scientific research. Microbes are used to break down grease, oil, and contaminants. The key to the process is living microscopic organisms that break down oil, grease, and hydrocarbon materials.
A biocycle system is self-cleaning using biodegradable formulas. Its development is based on creating a natural and safe method for parts cleaning. After materials are cleaned by the microbes, the remaining hydrocarbons are converted into carbon dioxide and water, which is filtered and reused. Oxygen is pumped into the solution to keep the microbes alive. This form of system is beneficial for the environment, can be reused indefinitely, is cost-effective, and is eco-friendly.
The major benefit of biocycle systems is the lowering of cost and the elimination of waste. The cleaning solution has lasting stability over time and allows for all aspects of the process to be reused. A control box mounted on the system monitors the cleaning level and oxygen supplied to the microorganisms.
There is a wide array of biocycle parts cleaning systems ranging from tubs for hand cleaning of parts up to large and sophisticated spray designs. The critical element of the process is the biochemical cleaner and its application.
Spray parts washers are cabinet aqueous parts washers that spray heated water and solutions on parts at highly increased pressure. Nozzles in the cabinet spray a jet or swirl of washing solution onto parts. As with other forms of parts washers, spray parts washers are enclosed in a steel or stainless steel cabinet. They can have a fixed table or turntable, depending on their design.
The cleaning solution is pumped through oscillating nozzles that blast the part’s load continuously from various angles. The solution level, temperature, suction pump filter, various safety devices, and electrical connection are managed from a sophisticated control panel. For best results, spray parts washers have rinse, steam exhaust, and blow off cycles.
The key to the efficiency of a spray parts water is its pumping system that has to be perfectly aligned and capable of performing without the need for adjustments. The spray manifold attacks the surface of parts from several directions including top down, bottom up, and across from the sides. The oscillating motion of the spray manifold makes it possible for the spray to reach every aspect of a part’s surface.
There are several designs of nozzles for spray parts washers. Regardless of the different types, all nozzles are made to aim, spray, and offer complete coverage without intersecting spray. Each nozzle blast is on its own plane straight at the surface of the batch of parts. When selecting a spray parts washer, assessment of nozzle spray is a necessity.
Spray parts washers come in several varieties, with ones that have a turntable with a turntable drive while others have a fixed table and do not move in relation to the spray. The common factor between the different types is the effectiveness and efficiency of the spraying system.
In mass production facilities, spray parts washers may have a conveying system that sends batches of parts through spraying chambers. They are inline systems that are combined with other industrial and assembly processes. The complexity of conveyor spray washers requires the use of a CNC system, software, or some other form of automation. The sprayed solution is set at temperatures between 130°F up to 200°F with spray pressures that reach between 30 psi up to 70 psi.
Rotary drum parts washers are a very economical method for high volume parts cleaning. Parts are washed using spray and immersion, where the spray cleans the surface of parts while immersion flushes and cleans the insides. Rotary drum parts cleaners are designed to clean small parts in volume. They have a rotating internal helix to tumble and convey parts through various stages of the cleaning process.
The drum of a rotary drum parts washer acts like an agitator to move parts to cleaning stations. Although rotary drum parts washers are designed to clean small parts, they can continuously clean parts as they move along the long, cylindrical drum of the washer. The screw-like helix is the part of the mechanism that moves parts along the process. During the washing and rinsing cycles, parts are gently tumbled to expose all of their surfaces, edges, and crevices.
The combination of rotation and spraying enhances the efficiency of the cleaning process of rotary drum parts washers and removes grime, chemicals, dirt, and debris from the exterior and interior of parts. The force of the spray removes surface oils, dust, and contaminants while the immersion in the tumbling process flushes out holes, deep indentations, hollow areas, and blind holes.
Different sizes of rotary drum parts washers:
Conveyor parts washers use an inline parts conveying system and are designed to have parts fed directly from stamping presses, CNC machines, and other forms of manufacturing processes. They have a variety of belt sizes that can meet the needs of any number or size of parts.
In a standard conveying parts cleaning system, the different cycles are designed to wash, rinse, blow off, and dry parts as they move along the conveying system. Additional stages can include more rinsing, rust inhibiting, phosphate applications, and sealing.
As with many other parts cleaning equipment, high efficiency maintenance free pumping systems are used to ensure a steady flow of water and cleaning solutions. The drying cycle is engineered to provide spot free flawless drying application.
Monorail parts washers have a similar function as conveyor systems. Unlike conveyor systems that have a metal mesh belt to move parts through the various cycles, monorail systems have an overhead conveying system where parts are hung or placed in baskets to pass through the cleaning cycles.
The method of conveyance is ideal for use with ultrasonic cleaning of small and large parts. For the ultrasonic method to be successful, parts pass through a pre-wash prior to being exposed to the ultrasonic process.
Monorail systems are normally a part of continuous processes where parts are cleaned, prepared, and sent on for further processing. Much like conveying systems, monorail systems can have multiple stages that are closed looped or inline. A closed looped system allows the operator to load and unload the system at the same station.
Spray nozzles are attached to headers that spray pressurized cleaning solution onto the parts. Monorail systems have multiple access panels for maintenance, monitoring, and service access. A variety of methods are used to prevent parts from falling into collecting tanks. With very large monorail systems, catwalk style gratings allow personnel to walk through the monorail tunnel.
Since most monorail systems are part of ongoing production, they are customized to fit seamlessly into the production process. Hooks, hangers, fixtures, and other movement devices are matched to the existing customer’s system.
Agitating parts washers are an aqueous immersion method of parts cleaning that uses energy to create vibrations and mixing action to clean surface dirt from parts. The vibrating motion is produced by impellers or paddles that cause cavitation on part surfaces. The agitation method is designed for parts that can withstand being shaken, rapidly moved, and bounced without being damaged.
The agitation process is excellent for placing the cleaning agent in contact with the surfaces of parts and depends on the chemical action of the surfactant. The drawback of agitation cleaning is the amount of time necessary to remove grime and contaminants. Parts that are delicate, complex, or intricate do not fare well in agitation parts washers.
Agitation parts washers require more time of operation that can slow down other processes in an assembly operation. Additionally, they need loading and monitoring while processing but cost less and use less energy.
Immersion parts washers clean parts by submerging them in a cleaning solution. They are known as dip tank parts washers and expose items to be cleaned to a mixture of solvents, detergents, and various types of cleaners. Much like agitator parts washers, immersion parts washers are a cost effective method for cleaning parts and are energy efficient. Immersion parts washers are a flexible cleaning method that is capable of cleaning large bulky parts and very small parts in batches with odd shapes, grooves, holes, and blind spots.
There are several varieties of immersion methods, but all types have certain basic features, including a large washing tank or series of tanks that churn the cleaning solution. Parts are placed in baskets and put through one or more of the following cleaning steps:
Small parts washers are specially designed for washing very small parts such as screws, bolts, nuts, bullets, pipe fittings, scrap metal, castings, and stampings. Much like larger parts, small parts have blind holes, complex configurations, and interior and exterior threads that must be cleaned and decontaminated.
Part of the manufacturing of small parts involves using various types of oils, lubricants, and solutions designed to make the shaping and forming of them smoother and more efficient. The lubricating materials must be removed before passing the parts on to other processes. Although large parts cleaners can be the cleaning solution, their use can be time consuming and costly. To meet the needs of manufacturers, parts washer producers have developed small parts washers that are the right size and have the efficiency that small parts cleaning requires.
Two common methods used to clean small parts are immersion and rotation each of which can be designed with small tanks or helixes. In the case of small parts rotary washers, the rotating system gently tumbles the parts in a basket. Like large parts cleaners, small parts washers can be made of metal such as steel and stainless steel. Due to the size of small parts, small parts washers can also be made of plastic.
There are a wide variety of tasks that a small parts parts washer can perform, aside from its function as a small parts washer. Small repair shops use several tools in the completion of projects. In the majority of cases, the tools get covered in grease, oil, lubricants, and dirt. The traditional method of cleaning tools has been rubbing them down by hand with a cleaner. This can be acceptable for a few tools but can become labor intensive for large numbers of tools.
Small parts washers are designed to clean tools as well as parts. Washers include a basket or tank where tools can be immersed in a solvent for cleaning. Helix rotation, agitation, or sprayers release solvents and detergents that clean substances off tools efficiently with little effort. Small parts washers provide far superior cleaning of tools than can be accomplished by manual cleaning.
The majority of parts washers are automatic or semi-automatic and are controlled by computers for loading, washing, rinsing, drying, and unloading. The convenience and efficiency of automatic parts loaders leave personnel and workers available to perform other tasks while parts are being cleaned.
There are several varieties of automatic parts washers, with ones that are connected to assembly processes while others are stand alone. Production line parts washers vary in size according to how clean parts have to be and the number of stations that are included in the parts washer. Parts are fed into the system using metal mesh conveyors or monorail systems where parts are in baskets, hung from hooks, or conveyed using some other system.
All forms of parts washers are used in automatic parts washers including immersion, agitation, rotary, and spray with spray being the most common and widely used. The configuration of automated systems makes it possible for parts to be mechanically machined and passed directly through an automated system into the parts washer without the need for manual transfer. The design of such processes improves efficiency and decreases the time of production.
The advent of computer numerical controlled (CNC) systems and PC software has further increased the efficiency of production and made it possible to time machining and cleaning such that they work together in unison. Cleaning specifications for certain parts require the parts to be subjected to several processes. Formally, each of the cleaning procedures had to be completed independently. With the development of automated parts washing systems, parts washers can be designed, engineered, and configured to complete all of the required processes in one parts washing system with multiple stations.
There are a few limitations to the sizes of parts that can be washed using an automated system. Using gantry or robotic delivery methods, parts are placed directly into the automated parts washer, which moves them by a conveying system through the computer controlled stations. As with the loading process, unloading is completed by a computer controlled mechanism that passes parts on to their next processing location.
As antiquated as manual parts washing may seem, it is still necessary in special circumstances. The standing rule for manual parts washing is safety since the chemicals necessary to complete the task can be harmful to humans and cause serious injury. Regarding that aspect of the process, the first steps in manual parts washing are the use of safety equipment, which involves safety glasses that completely enclose the eyes and very sturdy durable rubber gloves.
Modern manual parts washing has moved beyond the basin and drum method but still requires concern for safety and protection. At the center of modern manual parts washing processes are high pressure sprayers that significantly decrease the time required to clean parts. In most cases, a cabinet, enclosure, or special area is set aside for cleaning with devices to protect against overspray.
Most chemicals used in manual parts washing are water based and biodegradable. They are designed not to pollute the environment or cause damage. Regardless of the design of these cleaning materials, it is still wise to take safety precautions. Whether using a spray, immersion, or agitation, it is important to be properly trained and prepared for the process.
Manual parts washers are the lowest priced form of parts washing devices and are used for sporadic cleaning for more complex or intricate part designs. Manual parts washing includes soaking, brushing, heated fluids, spraying, directed streams, and fluid agitation. In most cases, manual parts washing includes immersion.
Aqueous parts washers use water as their primary cleaning agent that is combined with various types of water soluble cleaners. They are one of the most prevalent methods of parts washing due to their environmentally safe cleaning method. Unlike petroleum based parts washer cleaners, aqueous parts washers use non-flammable washing solutions that makes their washing process safe and hazard free. Using heat agitation and pressurized water, an aqueous parts washer breaks down dirt and contaminants into small particles for easy removal.
The types of aqueous parts washers include all of the different kinds of parts washers and include immersion, spray, conveyor belt, and ultrasonic parts washers. Each type has a filtration system for removing the dirt particles that have been broken down by the process. In the case of oil removal, oil skimmers remove free floating oil from the cleaning solution, which increases the usefulness of the solution and the longevity of the parts washer.
Carousel parts washers have the same type of cleaning system that is used by conveyor parts washers but with a smaller footprint. They are used for production operations that require precision cleaning at a higher production rate. Parts for a carousel parts washer are loaded and unloaded at the same location, which is unlike a conveyor system where parts are loaded at one end and unloaded at the opposite end.
The concept of carousel parts washers is based on the idea of a barrel that is the enclosure for the parts washing system. One side of the barrel is open such that parts for cleaning can be loaded. Inside the barrel is the rotating carousel that carries the parts through each step of the cleaning process. The number of steps can vary from 3 or 4 up to 16 depending on the design of the carousel. Each of the steps are indexed to perform in order for quality cleaning and drying. The rotation speed, timing, number of steps, and treatment times can be easily set to meet the cleaning needs of the loaded parts.
One of the designs of carousel parts washers combines the conveyor design with the carousel process. The enclosure still has the barrel shape but parts are loaded and unloaded on a conveyor that travels through each of the carousel cleaning stages.
A chain mesh parts washer is a form of conveyor parts washer that continuously washes parts as they travel through a set of stages. As the parts move along with the chain, they are cleaned by jet sprayers that have a cleaning solution that forcefully removes dirt and grime from the parts. Chain mesh parts washers are normally used as part of an assembly process and are engineered for the parts that are being cleaned. The chain mesh is ideal for aqueous cleaning of parts since the cleaning solution can flow through the chain mesh for recirculation and retrieval. They are designed for high volume parts washing like conveyor systems and can be easily customized to fit a variety of parts and cleaning mechanisms.
There are several styles of chain mesh parts washers that include ones with fixtures and ones capable of transporting pallets through the cleaning process. The use of pallet chain mesh parts washers enhances the efficiency of assembly operations and are part of the shuttling of pallets of parts between workstations. The system can be integrated for cleaning palletized parts and for the flushing of empty pallets.
The planning of a chain mesh parts washing system includes cell layout, cycle times, and methods for transferring pallets, which can be by forklift or automated system. The success of a chain mesh parts washer is dependent on proper transfer of parts and line speed that has to be set to match production operations.
Tumble parts washers are ideal for washing high volumes of very small parts that can be easily loaded into the wash chamber. As the machine tumbles the parts, jet sprayers blast them with tempered water to loosen dirt, remove grime, and clean hollow areas and hidden corners. Although the process for tumble parts washers includes tumbling parts, their design makes it possible to include parts that don’t need to be tumbled that are locked in covered racks and specialized fixtures, a design that makes tumble parts cleaners more flexible and adaptable.
The mechanism of tumble parts washers includes the same features as other types of parts washers with storage tanks for recirculating water and rinse tanks. Some designs include a third tank for heavily soiled parts that require extra cleaning. The stages of tumble parts washers can include sprayers, immersion,and ultrasonic cleaning, which can be run in any order.
Metal parts washers are a necessity for industries that work with metal parts. They provide an easy and convenient method for cleaning parts, which improves the appearance of parts and protects them from degradation from environmental factors. The number of metal parts washers is endless and includes cabinet size parts washers and long conveyor style parts washers. Each type and category provides an economical and efficient method for cleaning metal parts.
Petroleum based solvent parts washers are very common forms of metal parts washers. They provide exceptional cleaning and are capable of removing the most difficult forms of grease, grime, dirt, and contaminants. Unfortunately, regardless of their excellent cleaning record, petroleum based solvent parts washers are hazardous and toxic, which requires that their use be very cautiously considered.
What has rapidly risen as a very popular method of metal parts cleaning is water based cleaners that can perform the same types of cleaning but are safer, nontoxic and nonflammable. There are several varieties of water based parts washers and include ultrasonic parts washers that are ideal for delicate or fragile parts.
In essence, there is a type of metal parts cleaner for every application. It is essential that the choice of a metal parts cleaner be carefully considered such that the correct type of metal parts washer be chosen. The factors that have to be considered when selecting a metal parts washer is the type of parts to be cleaned, the available space for the parts cleaner, the required quality of the cleaning, and how a metal parts cleaner will fit into an operation or process.
Any industry that deals with different types of parts makes use of a parts washer. This is especially true for industries that require the use of metal parts that can get fouled during the various fabrication processes where parts washers are used to clean fasteners, bolts, nuts, screws, bearings, gear boxes, and assemblies.
The automotive industry depends on parts washers for a variety of reasons due to the nature of the mechanism that powers their products. Essential aspects of every automobile are oil, gas, grease, and various lubricants that can contaminate, foul, and dirty components. To be able to effectively assemble and repair automobiles, parts washers are a necessity for cleaning parts during assembly and diagnosing difficulties during repair.
Depending on the industry, industrial environments are not always the cleanest places for equipment. Part of the successful operation of an industry is regular maintenance where parts, components, and assemblies are examined, checked, and cleaned. An essential part of the process is parts washers that make it possible to check a defective part to determine if it needs to be replaced or repaired. Efficient parts washers assist in the proper performance of repairs and getting equipment up and running.
The effectiveness of an army depends on rapid and reliable movement of troops, which requires a fleet of vehicles capable of leaping into action at a moment's notice. Every motor vehicle in the motor pool has to be operational and requires the use of parts washers to ensure every truck, humvee, troop carrier, and jeep is in peak condition.
Cabinet parts washers are commonly used in the food industry to clean equipment, dishes, tools, and bowls. The process of a parts washer makes it possible to load a wide array of cooking equipment into a parts washer and have it cleaned in a single cycle. Since cabinet parts washers are low volume parts washers, they are ideal for use by the food industry.
The efficiency of parts washers is ideal for the medical instrument industry that has high standards and regulations regarding the cleaning of instruments and devices. Several forms of parts washers are used in the medical equipment industry and include immersion, spray cabinets, and ultrasonic parts washers, each of which is ideal for the cleaning of delicate medical devices.
There are many accessories for parts washers that are designed to enhance and provide additional benefits for various types of parts washers. The four listed below are common types of accessories that are readily available from parts washer manufacturers. The initial investment in a parts washer may not require any accessories, which can become necessary after extended use.
Solvent filters help save money by making solvents reusable after completing a cleaning process. They are designed to filter out oil, grease, and other materials that are removed during cleaning. Solvent filters provide a continuous supply of filtered solvents that can be used multiple times.
Parts washers come equipped with containers designed to organize and separate parts during cleaning. Over time and multiple uses, these sturdy containers can wear out or be damaged. All manufacturers have a readily available supply of baskets and racks as replacements.
Work shelves have several uses that include storage of parts, providing additional space in certain types of washers, and replacements for worm shelves. They are made of heavy gauge steel and have a durable metal frame.
As grime, oil, and grease are removed from parts, their residue settles at the bottom of the washing tank. Sludge trays are designed to collect the sludge and keep it away from cleaned parts.
A degreaser is a super solvent cleaning system that cuts through grease and built up oil and is commonly used with parts washers. The term degreaser is a generic term that covers a wide assortment of products that include precision cleaners, maintenance cleaners, and carb cleaners. They are designed to quickly and efficiently remove soil without the need of mechanical devices or scrubbing. Although petroleum degreasers are commonly used, water based degreasers are preferred for their safety and easy use. For parts washers, degreasers are used with immersion cleaning systems and batch cleaners. Specialized degreasers include the use of ultrasonic and vapor degreasers for more automated degreasing. Ultrasonic and vapor degreasing is repeatable and ideal for highly critical cleaning processes for medical equipment and aerospace.
A wastewater evaporator converts water into a vapor and leaves behind contaminants. The process uses thermodynamics, which involves heating the wastewater to turn it into a vapor. The droplets from the vapor are removed from the process by a blower as water vapor. The process is used with parts washers to separate water from the contaminants collected by the process.
Cleaning parts is a necessity for modern industrial processes that rely on lubricants, oil, grease, and other substances during manufacturing. Once production is completed, the unnecessary materials have to be removed. Parts washers offer a safe and efficient method for parts washing through the use of water, heat, agitation, and environmentally safe chemicals.
Parts washers remove the need for labor in the parts cleaning process. In the majority of cases, the parts cleaning process does not necessitate human involvement until the cleaning process is completed. Handling, cleaning, rinsing, and drying are all completed safely and efficiently.
Parts washers can clean any form of parts or components regardless of size or complexity. The various solutions and cleaning systems can reach the most remote and isolated part of a part and remove any contaminants. Parts washers are only limited by the size of the required enclosure.
A parts washer gives a manufacturer total control of the production of a part from machining to completion. This increases quality assurance and guarantees proper production.
Modern production methods require close attention to detail. Having the ability to initiate a process and not necessitate worker oversight increases individual productivity and efficiency. This particular feature for cleaning parts by using a parts washer frees up personnel to perform more critical and necessary tasks.
The purchase of a parts washer may seem to be a simple matter of providing an efficient cleaning process. Although this is a major feature of a parts cleaner, purchasing a parts washer can also lead to improved processing, more efficient operation, and cost savings regarding malfunctioning or damaged parts.
The proper handling of a parts washer is essential to its performance. Any type of neglect can diminish a parts washers ability to properly and precision clean parts. There are several factors that have to be considered when performing maintenance on a parts washer. Each step in the process necessitates careful examination of a parts washer including every one of its components. This process becomes more vital for petroleum based solvent parts washers that require more frequent maintenance.
Parts that need cleaning should be moved from the production line to cleaning. Parts Stored with oil and grease on them accumulate dirt putting extra pressure on parts cleaning equipment, resulting in longer cycle times, increased operating costs, and maintenance and repair issues for parts cleaning equipment.
Metal parts with burrs complicate the cleaning process, making it difficult for detergents or solvents to penetrate areas around burrs. During washing, burrs come off, making it harder on filtration and cleaning systems.
Every parts cleaning system has established parameters regarding loading. These must be adhered to for the proper performance of a parts washer. Excessive overloading and jamming in parts to speed up processes leads to poor quality and performance.
If contaminants are oil-based, like cutting fluids or coolers, a hydrocarbon cleaning process is best. If contaminants are water-based, like grinding or lapping compounds, aqueous is the best choice. The proper selection of cleaning solutions affects cleanliness levels and cycle times.
Humans unknowingly transfer contaminants, such as oils, skin cells, and strands of hair, which complicate a parts washers’ performance. Operators should wear hairnets, lint free gloves, work coats, and bodysuits, which will protect them from potential harm from corrosive wash materials or chemicals and from their interference or contamination of the materials to be cleaned.
An aqueous part washer is an automated or semi-automated machine manufactured to clean, remove tough grease, and dry large or small parts before distribution or surface treatment. The washing is necessary since...
Automated parts washers are mechanical devices designed to efficiently remove grit, oil, grime, dirt, paint and other contaminating substances from parts with minimum manual supervision. These substances are removed...
A parts cleaner is a cleaning device that uses various types of solvents, cleaning agents, and processes to remove grease, grime, and contaminating materials from manufactured parts prior to shipment or movement for further processing...
A parts washer is a mechanical device designed to remove grit, grime, oil, miscellaneous debris, dirt, paint, and other contaminating substances from parts in preparation for their use in assembly operations, packaging, or coating...
A wastewater evaporator is a method of removing water from water-based waste by converting the water in the waste to a vapor and leaving contaminants. The function of a wastewater evaporator is to reduce the volume of waste materials...
Industries worldwide utilize abrasive blasting for various purposes, including cleaning rust and oil, removing surface coatings like paint and pollutants, preparing surfaces for paint and coatings, reinforcing metal surfaces and...
Deburring is a secondary operation of a machining process that enhances the final quality of the product by removing raised edges and unwanted pieces of material, known as burrs, left by the initial...
Finishing machines are machines used for metal finishing, which is the last stage of the metal fabrication process; the stage encompasses the use of machines in finishing the metal surface...
Sandblast cabinets include systems or machinery and components for projecting blast media against a part‘s surface to abrade, clean, or modify the surface. Sand, abrasive, metal shot, and other blast media are driven or propelled using pressurized water, compressed air, or a blast wheel...
Sandblasting equipment includes systems or machinery, and components for projecting blast media against a part‘s surface to abrade, clean, or modify the surface. Sand, abrasive, metal shot, and other blast media are driven or propelled using pressurized water, compressed air, or a blast wheel...
Shot peening equipment includes systems or machinery and components for projecting shot peening media against a part‘s surface to modify the surface or surface engineer the part...
A tumbling machine is a durable deburring and metal-polishing machine designed for finishing large parts or batches of smaller parts. A tumbling machine is also known as a barreling machine or a mass-finishing...
An ultrasonic cleaner is a type of sonic cleaner or sonic cleaning machine that uses cavitation to remove unwanted material. The cleaning effect is created by the compression and refraction of a cleaning medium. Miniscule vibrations propagate throughout the...
Ultrasonic cleaning is a type of cleaning process which uses cavitation induced by alternating compression and rarefaction cycles at ultrasonic frequencies. Ultrasonic frequencies are sound waves vibrating at 20 kHz or higher...
Vibratory tumbler is the equipment used in a vibratory finishing process, one of the most common methods in mass finishing. But how does a vibratory tumbler work...