Deburring
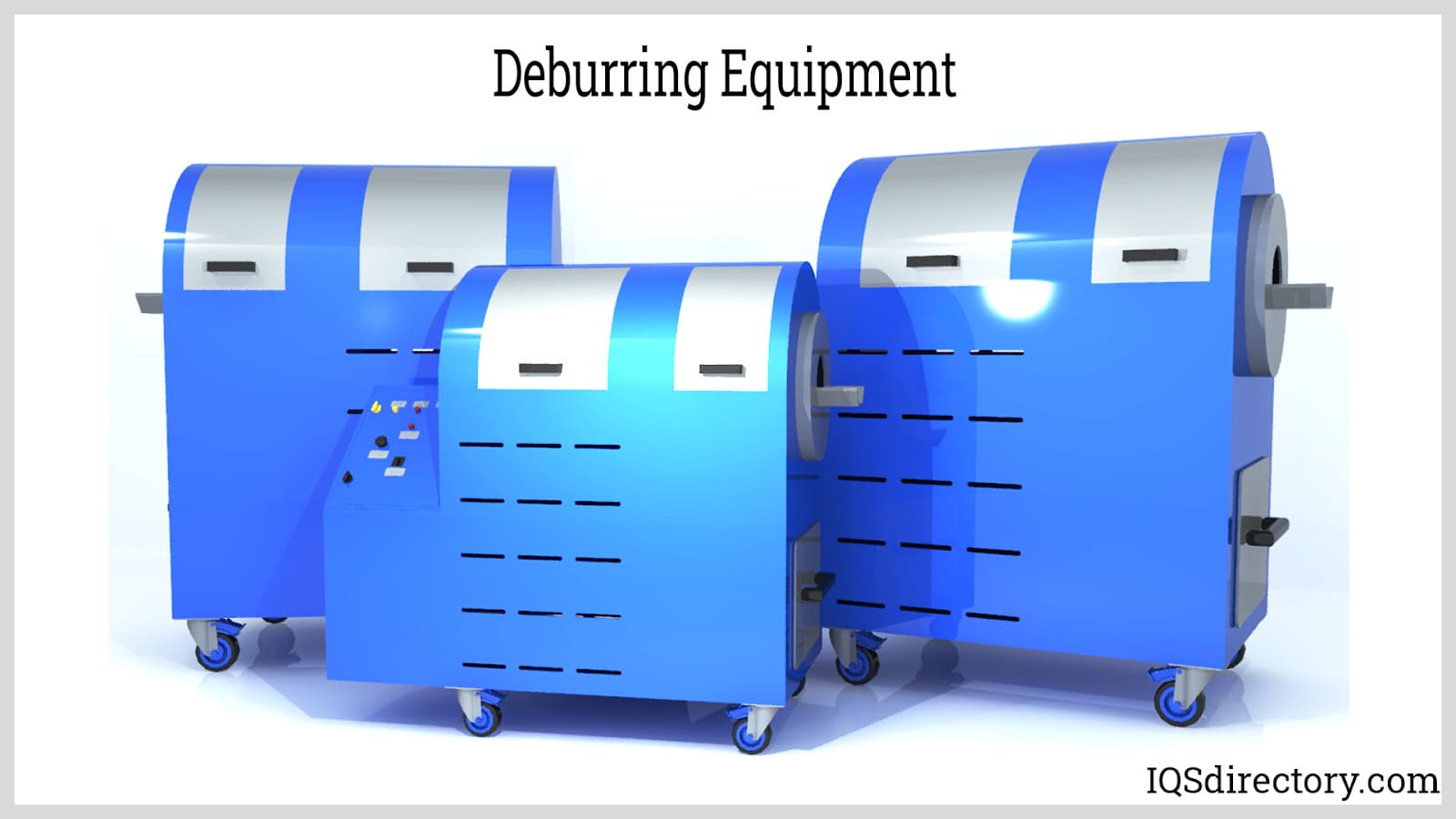
Deburring is a secondary operation of a machining process that enhances the final quality of the product by removing raised edges and unwanted pieces of material, known as burrs, left by the initial...
Please fill out the following form to submit a Request for Quote to any of the following companies listed on
This article takes an in-depth look at vibratory tumblers.
Read further and learn more about topics such as:
Vibratory tumbler is the equipment used in a vibratory finishing process, one of the most common methods in mass finishing. But how does a vibratory tumbler work?
The operation of vibratory tumblers involves placing the workpieces and parts inside a tub filled with specially shaped pellets of media then applying vibration force to all the tub’s contents. The motor of the vibratory tumbler applies sufficient vibration force. Strong springs are placed at the bottom of the tub to support it during motion. The finishing process may be aided by a specialty finishing chemical that is poured and maintained in the tub.
The vibration will cause the media and the workpieces to rub and grind against each other, resulting in polished workpieces. The tumbler and its contents remain stationary as it is being shaken. A vibratory tumbler can operate in either batch or continuous mode.
A vibratory finishing process is used to clean, deburr, deflash, descale, and polish workpieces. It can be used as a surface preparation step to enhance the bonding of coating, plating, and adhesive materials to the workpiece. It is typically performed after a machining process. It can also be used in slightly reducing the size or radiusing of irregularly shaped materials, and the workpiece maintains its original shape after the process. The results of this finishing method cannot be achieved using manual polishing and deburring.
Vibratory tumblers have high throughput and are suitable for manufacturing high volumes of parts. They provide finished parts faster than rotary tumblers, but it is relative to the nature and dimensions of the parts that will be processed. They can safely finish the surface of plastic, metal, and ceramic workpieces provided that the appropriate media, vibratory action, and type of vibratory finishing are used.
Vibratory tumblers are available in a variety of capacities, shapes, and dimensions. They can be highly automated to provide better control of the finishing process. They may even be equipped with a drying feature.
Products of vibratory finishing are commonly used as aerospace, firearms, and equipment parts, and orthopedic implants.
The finishing media, or grit materials, are the materials responsible for polishing the parts as they are being shaken during the finishing process. As the surface of the media rubs on the parts, the rough edges and surfaces of the parts become smooth and clean. The finishing media come in a variety of materials, grades, and shapes. Choosing the best material type, grade, and shape of the media will provide the best quality for your finished parts.
The types of finishing media in vibratory finishing based on material type are the following:
Ceramic media is the most common vibratory finishing media that has high density, tough, and durable; hence, they are ideal for deburring, edge radiusing, burnishing, and polishing hard metals such as steel, stainless steel, and titanium. They can be used in removing rust on metal parts. They are used in general-purpose finishing, though they are preferred if heavy or fast grinding is to be performed. However, ceramic media can chip due to wear and exposure to excessive forces, and loose ceramic particles can be embedded in the small holes of a part.
Ceramic media is typically made of porcelain, aluminum oxide, silicon carbide, and silica. Aluminum oxide and silicon carbide are used in harder metals, while silica works on softer metals.
Steel media are made from hardened carbon and stainless steel that also has high density. Their high strength and durability prolong their service life and enhance their wear resistance. They can apply large pressure during vibration with the workpieces; hence, these media are used in heavy-duty burnishing and polishing. They can be used in aluminum, brass, steel, stainless steel, and plastic parts. The result of the finishing process using steel media is a bright, burr-free, and smooth surface.
Plastic media are suitable for polishing, deburring, burnishing, and cleaning softer metals such as brass, aluminum, and zinc. Since these media generally are less dense compared to ceramic and steel media, they can perform vibratory finishing safely on threaded and fragile parts. Plastic media are used in mild cutting and less abrasive finishing. The result of finishing on the workpieces is soft and bright surfaces and edges.
Plastic media are commonly made of polymers based on polyester, urea, and formaldehyde.
There are several formulations of plastic media for a specific result and to finish various workpieces made from different types of materials:
Organic media are lightweight media that are typically made of walnut shells and crushed corn cobs. They are environmentally friendly, biodegradable, and durable. They are suitable for light to medium deburring. They are mostly used to dry parts after vibratory finishing. They can be used to produce a glossy surface on metal parts when used with polishing paste. They can also finish pieces of jewelry safely. Crushed corn cobs as organic finishing media have the advantage of absorbing oils and moisture from the surface of the workpiece, thereby imparting enhanced corrosion resistance.
The grades of vibratory finishing media are as follows:
Light cutting media is the most common finishing media that produces a small amount of abrasion and provides a softer finishing action to deburr, deflash, and burnish workpieces. These media can make a smooth and bright surface on the workpiece.
Non-abrasive or polishing media are intended to polish parts, thus making a smooth and lustrous surface.
Medium cutting media are used for fast general-purpose deburr and when both surface brightness on the part and faster cutting are desired.
Fast cutting media are used in heavy-duty finishing. They exert a large amount of abrasive force, which can deburr, grind, and burnish workpieces quickly.
The geometry of the media affects the finishing process done on the workpiece. The commonly available shapes and sizes and the applications in which they are suitable are the following:
Rounded Media (spheres, oval, and cylinders) are used for light deburring and provide delicate finishing action. Since they have no sharp edges, the chances of rounded media getting stuck on parts are low. They also have low chipping rates.
Sharp Media (triangles, wedges, and arrowheads) are used for polishing and deburring hard-to-reach sections (e.g holes) and are suitable for complex parts. Their flat edges enable them to finish the sharp corners that are present on the parts which cannot be reached by rounded media. However, these media have higher chipping and wearing rates compared to rounded media.
Before we move to the types of vibratory tumblers, let us tackle first dry and wet vibratory finishing:
In a dry vibratory finishing process, the finishing process is performed without using specialty chemicals and is carried out by the finishing media alone. Non-abrasive finishing media such as organic media is typically used. This process is used in drying and polishing to reveal a bright and lustrous finish on the surface of the part.
Dry vibratory finishing is less expensive than wet vibratory finishing. However, the dry media can be loaded with dirt, oils, and metal oxides after several cycles, which decreases the performance of the finishing process and contaminates the part. Harder and denser media such as ceramic media might scratch the workpiece. The dry media wear after several finishing batches. Thus, a dust or particle collector must be installed. The dry finishing operation can also generate noise.
In a wet vibratory finishing, the finishing process is aided with a fluid such as water or specialty chemicals. The fluid acts as lubricant and coolant and the heat generated from the rubbing of the workpiece. Then the media is absorbed by the liquid, thereby minimizing the distortion of the part. The fluid helps in removing the oxides and contamination present on the surface of the workpiece. Hence, the part appears cleaner and more polished after a wet finishing process. Less debris is also generated and deposited on the media. However, it is apparent that wet vibratory finishing is a more expensive process than dry finishing. This process also generates waste from the spent specialty chemicals that need to be treated.
A wet vibratory finishing process is carried out using media of almost all material types, except for organic finishing media.
Wet vibratory finishing has a wider range of finishing capabilities than dry finishing, making them the more popular type.
The types of vibratory tumblers are the following:
A continuous vibratory finisher is a kind of vibratory through a finishing machine. The parts are placed at one end of the machine and are conveyed together ith the media while the finishing process is being performed. The finished parts are continuously received at the other end at a constant rate.
Continuous vibratory finishers offer excellent productivity as the parts are finished and conveyed to a location or downstream equipment simultaneously. The cycle time of the combined tasks is considerably reduced.
The vibratory bowl is the simplest configuration of vibratory finishing equipment. It is composed of a bowl lined with polyurethane. The lining reduces the coefficient of friction between the bowl and the media, thus protecting them from wear. The bowl can be equipped with adjustable and removable dividers to process small and sensitive parts separately, which prevents part-to-part friction.
Vibratory bowls are available in a variety of tub shapes and dimensions. Rectangular and bowl-shaped tubs are commercially available. There are tubs with narrow central sections to accommodate large products. The variations in bowl geometry enable you to choose the best vibratory bowl that suits your application.
They can support both small and large production batches. For small capacity finishing, portable and bench or table-mounted vibratory bowls are available.
The vibratory dual finishing machine consists of an inner chamber and an outer chamber, which are used for wet and dry vibratory finishing steps, respectively. The heavier duty finishing steps such as deburring, radiusing, and polishing are performed in the inner chamber. These steps are commonly aided with finishing chemicals. The inner chamber has a polyurethane lining to reduce wear and friction. The drying and cleaning steps are performed in the heated outer chamber. Both chambers are separated with a stable partition to ensure the contents of each chamber will not be transferred to the other.
After the wet finishing is completed in the inner chamber, the media is screened and retained in the bowl while the parts are discharged to the outer chamber.
A vibratory dual finishing machine is an economical option as the wet and dry processes are combined in a single unit.
Vibratory dryers consist of an elliptically shaped tub filled with heated drying media used in drying the part after a wet finishing process. This equipment also gives additional polishing to the part.
Vibratory dryers can process small and large volumes of parts and are commercially available in batch and continuous modes. Vibratory dryers can be used in in-line manufacturing in which the finished parts are received by downstream equipment.
A vibratory trough finishing machine is composed of an enclosed, long U-shaped tub lined with polyurethane with divider plates inside the tub, which can be removed and adjusted manually. This machine is used in vibratory finishing of long, large, irregularly shaped parts and of delicate parts. The divider plates create compartments inside the tub that separate each delicate part in order to prevent the rubbing contact of each part during finishing.
Vibratory trough finishing machines can perform almost all finishing operations. They can process large quantities of products. They are highly versatile finishing machines and come in standard sizes and various combinations of lengths, widths, and capacities. Batch and continuous vibratory troughs are commercially available to support your production needs.
The following are additional considerations in selecting and operating vibratory tumblers:
The media-to-parts ratio refers to the volume of finishing media per total part volume. If the part to be finished is sensitive or soft, a higher media-to-parts ratio is more desirable to minimize scratching due to part-to-part contact. When finishing sensitive products, the use of a divider plate is always recommended. The media-to-parts ratio is used to determine the volume appropriate for your application. The total part and media volume must occupy 90% of the tub volume. The characteristics of the part influence the media-to-parts ratio. The table below shows the different media-to-parts ratio and their specific application:
Media-to-Parts Ratio | Application |
---|---|
0:1 | Part-to-part finishing. No media is present. |
1:1 | Equal volumes of media and parts. Produces rough surface finish on forgings, castings, and stampings. |
2:1 | Still produces rough surface finish on forgings, castings, and stampings. Finishing of very small parts. |
3:1 | Ideal ratio for moderate deburring and surface finishing |
4:1 | Good ratio for ferrous metals. Sufficient ratio for non-ferrous parts. |
5:1 | Minimal part-to-part interaction. Suitable for soft and non-ferrous parts. |
6:1 | Finishing non-ferrous and fragile parts for pre-plate and decorative finish. |
8:1 | Bright burnished finish and high quality pre-plate finish. |
10:1 | Finishing fragile, sensitive, and irregularly shaped parts. |
Frequency and amplitude are properties that characterize the vibration intensity. The frequency refers to the rate of the number of vibration cycles per unit time, measured in cycles per minute (CPM), while the amplitude is the maximum distance reached by the vibrating object from the stationary position to the extreme position (measured in millimeters). Frequencies of vibratory tumblers can vary from 900-3600 CPMs, while amplitudes range from 1-8 mm. The amplitude can be adjusted using the controls of the motor.
The surface finishing of delicate and fragile parts can be carried out using a high frequency but low amplitude vibration. Meanwhile, burnishing, deburring, and radiusing require large amplitudes.
A Barrel tumbler is another type of tumble mass finishing equipment. It works by rotating the parts, the media, and the finishing chemical inside a barrel. The rotational movement causes the parts and the workpiece to rub against each other. Like vibratory tumblers, barrel tumblers also perform a variety of finishing processes, from heavy cutting actions like burnishing, deburring, radiusing, and deflashing to surface improvement such as polishing, cleaning, and drying. Barrel tumblers typically operate in a batch production mode, though continuous or in-line configurations are less commonly found.
We will now compare vibratory and barrel tumblers based on different aspects.
Vibratory tumblers are good at finishing almost all types of parts. They are recommended for delicate, soft, and fragile parts since each part can be separated from the others by a divider plate to prevent part-to-part contact. Vibratory tumblers preserve the original shape of the parts being processed as the tub remains stationary during operation. They can also accommodate long parts. Meanwhile, rotary tumblers are suitable for small and hard parts.
The media used in rotary tumblers wear out at a slower rate than vibratory tumbler media. They last twice longer than vibratory tumbler media. However, rotary tumbler media have to work longer to perform the same finishing process done by a vibratory tumbler. Rotary tumblers also consume more media.
Vibratory tumblers provide finished parts faster than rotary tumblers.
Since rotary tumblers deform the loaded parts to a certain extent, they are suitable for heavy deburring, radiusing, and size reduction. They can shape rough, irregularly shaped parts into smooth, rounded ones. Meanwhile, vibratory tumblers are ideal for polishing, cleaning, and drying, though they can also perform heavy finishing tasks.
Vibratory tumblers are generally more expensive compared to rotary tumblers due to their massive construction, versatility, and features. They consume large floor spaces. Rotary tumblers have a lower initial cost.
Vibratory tumblers are quite noisy during operation as the contents oscillate against the tub due to the strong vibration force. However, advanced vibratory tumblers offer noise control. Rotary tumblers, on the other hand, produce less noise.
Deburring is a secondary operation of a machining process that enhances the final quality of the product by removing raised edges and unwanted pieces of material, known as burrs, left by the initial...
Finishing machines are machines used for metal finishing, which is the last stage of the metal fabrication process; the stage encompasses the use of machines in finishing the metal surface...
A tumbling machine is a durable deburring and metal-polishing machine designed for finishing large parts or batches of smaller parts. A tumbling machine is also known as a barreling machine or a mass-finishing...
Industries worldwide utilize abrasive blasting for various purposes, including cleaning rust and oil, removing surface coatings like paint and pollutants, preparing surfaces for paint and coatings, reinforcing metal surfaces and...
An aqueous part washer is an automated or semi-automated machine manufactured to clean, remove tough grease, and dry large or small parts before distribution or surface treatment. The washing is necessary since...
Automated parts washers are mechanical devices designed to efficiently remove grit, oil, grime, dirt, paint and other contaminating substances from parts with minimum manual supervision. These substances are removed...
A parts cleaner is a cleaning device that uses various types of solvents, cleaning agents, and processes to remove grease, grime, and contaminating materials from manufactured parts prior to shipment or movement for further processing...
A parts washer is a mechanical device designed to remove grit, grime, oil, miscellaneous debris, dirt, paint, and other contaminating substances from parts in preparation for their use in assembly operations, packaging, or coating...
Sandblast cabinets include systems or machinery and components for projecting blast media against a part‘s surface to abrade, clean, or modify the surface. Sand, abrasive, metal shot, and other blast media are driven or propelled using pressurized water, compressed air, or a blast wheel...
Sandblasting equipment includes systems or machinery, and components for projecting blast media against a part‘s surface to abrade, clean, or modify the surface. Sand, abrasive, metal shot, and other blast media are driven or propelled using pressurized water, compressed air, or a blast wheel...
Shot peening equipment includes systems or machinery and components for projecting shot peening media against a part‘s surface to modify the surface or surface engineer the part...
An ultrasonic cleaner is a type of sonic cleaner or sonic cleaning machine that uses cavitation to remove unwanted material. The cleaning effect is created by the compression and refraction of a cleaning medium. Miniscule vibrations propagate throughout the...
Ultrasonic cleaning is a type of cleaning process which uses cavitation induced by alternating compression and rarefaction cycles at ultrasonic frequencies. Ultrasonic frequencies are sound waves vibrating at 20 kHz or higher...
A wastewater evaporator is a method of removing water from water-based waste by converting the water in the waste to a vapor and leaving contaminants. The function of a wastewater evaporator is to reduce the volume of waste materials...
Parts washers are designed for cleaning, degreasing of equipment, and drying of mass quantities of small or large parts in preparation for surface treatment, assembly, inspection, or shipment...